烧结配料优化熔剂结构的攻关实践
烧结配料的优化控制

烧结配料的优化控制莱钢自动化部 杜春雷[摘 要]莱钢银前配料PL C 系统针对常规控制存在的问题,通过实现料批控制功能和数字变频控制功能动态优化烧结原料的配比,大大提高了烧结矿产品的质量。
[关键词]配料制度 料批控制 数字变频控制 优化控制 1.前言随着工业自动化水平的提高和普及,计算机控制技术逐渐引入到烧结生产中,大多采用了DCS (集散控制系统)或PL C 控制系统,基本实现了烧结生产的自动化控制。
但莱钢在烧结质量控制方面,特别是配料生产中缺乏优化控制手段,主要靠基础自动化及人工经验操作,输送到265m 2烧结机的各种原料难以得到理想化的配比,从而烧结矿的质量也难以保证。
莱钢银前烧结PL C 系统通过实现料批控制功能和数字变频控制功能,从而实现对烧结配料生产的优化控制。
2.莱钢银前烧结配料生产工艺概述莱钢银前烧结配料室共有15个料仓,分别储存参与烧结的各种含铁原料、溶剂和燃料,由13台宽带给料机和两台双螺旋给料机(下生石灰)将原料打到13台配料称和两台螺旋称(称量生石灰),经过称量后按料头料尾对齐的原则配比后进入一混一皮带,再经过两台混合机加水搅拌均匀后,输送到265m 2烧结机。
如下图1。
配料是烧结生产的一个重要环节,它既影响着生产成本,又影响着高炉冶炼指标。
3.配料PL C 系统的硬件配置和组态软件3.1现场控制站选用QUAN TUM 系列PL C 完成基础设备级自动控制。
3.2组态软件采用基于M icrsoft W indow s 2000环境的CON CEPT 2.6编程软件,为整个控制系统提供一个统一的开发环境。
监控软件—652—采用功能强大的M P 7.2软件,可以实现实时过程监控和监督控制,报警和报警管理,历史数据,统计过程控制等。
3.3监控站设置两个客户端,一台服务器。
通过交换机统一挂在工业以太网上。
3.4网络通讯银前烧结整个网络分控制级和监控管理级两级控制。
控制级通过光纤将配料PL C 和熔燃、烧冷、筛分其它3套PL C 系统连接构成工业以太环网,通讯速率100M b s 。
优化烧结配料生产实践及措施

2 0 1 6年 l 2月
优 化 烧 结 配 料 生 产 实 践 及 措 施
秦 书财 ( 型钢 炼铁 厂)
摘 要 : 针对 烧 结配料 生 产 中存 在 的 问题 , 分析 了影 响烧 结 配料 稳 定 性 的 因素 , 并 结合 生产 实
际, 采取 了一 些有 效 的技 术控 制措 施 , 稳定 了配料 工 艺过程 , 进 而稳 定 了烧结 生产 。
加 之称料 过程 盘子 在 皮 带 上 有 一定 的运 行 速度 , 产 生 相 当大 的冲量 , 所 以抓 取盘 子相 当 闲难 , 大 大增加 了职工 劳动强 度 。 1 . 4 存 在诸 全 隐患 ; 另外 自动 配料 过 程 也存 在一 些 问题 , 如 宽 带 出现 问题 以及 料 种 出现 变 化都 不 能及 时发现 , 也不 能作 出及 时处 理 与调整 。
患。
综 合 以上 因素 , 跑 盘 称料 法 配合 电子 称 校称 的 方 式在 实 际的烧 结生 产 中不能很 好 的达到精 确 配料
的 目的 。
1 ) 称 料过 程容 易卡 盘子 , 卡盘 后需 停机 取 出 ; 2 ) 称 料 频 次 影 响。 正 常 情 况 每 两 个 小 时 就 要 进行 一次 全料 种 ( 混匀料、 白云石 、 生石 灰 、 焦分 、 返
2 . 1 . 1 自动配 料 系统工 作原理
41
金工程专业 。工程师 , 从事技术管理工作。
秦 书财 : 优化 烧结 配料 生产 实践及措 施
第 6期 ( 总第 1 8 6期 l 2 . 2 采用双 报警 系统 实时监 测 下料量
自动 配料 每种 料 的下 料 工 艺过 程 为 : 料种 通 过 宽带 给料 机从 料仓 中输 出 , 再 经过 皮 带 电子称 输 送 至输 料大皮 带 , 即采 用 宽 带 给料 机 +电子 皮 带秤 的 给料 方式 。其 工作 原理 为 : 当料仓 料 口大 小一 定时 ,
关于烧结工序调整生石灰等熔剂配比的相关情况分析

关于烧结工序调整生石灰等熔剂配比将产生的相关情况分析2010年11月13日集团公司董荣华副总经理在长寿新区指挥中心组织召开了重钢新区石灰平衡专题会议,会议决定:提高生石灰配比到50kg/t以上,以利于烧结矿质量的稳定,原则上要停止从矿山直供石灰石粉;为确保资源综合利用,矿山可考虑细粒级石灰石的煅烧生产,并提出具体意见供集团决策。
根据会议精神,大宝坡石灰石矿从烧结环节生石灰的需求、矿山资源与粒级平衡、烧结石灰煅烧工艺等方面进行了初步的综合分析,并提出相关的建议。
一、烧结石灰需求及相应的烧结石灰石资源的供应分析1、烧结石灰需求分析目前新区烧结环节所用冶金熔剂消耗水平为:石灰石粉47kg/t、生石灰33 kg/t、白云石21 kg/t、轻烧粉42 kg/t;烧结矿的碱度水平在1.85~1.9;折算到石灰石的消耗总量在110 kg/t 水平。
按此消耗水平,以3台360m2烧结机生产,生石灰配50kg/t,石灰石粉配20kg/t,烧结矿碱度1.85计算,650万吨和800万吨钢规模烧结石灰的需求与可消化的石灰石粉量见下表。
实用文档注:烧结石灰石入窑量=烧结石灰用量*1.82、炼钢环节石灰及石灰石需求分析炼钢环节综合石灰消耗按55kg/t钢,因炼钢石灰石运距远转运环节多,但采用的是竖窑与回转窑的组合窑型,入窑筛下物按10%测算,650万吨和800万吨钢规模炼钢石灰及石灰石资源的需求分析见下表。
注:炼钢石灰石入窑量=炼钢石灰用量*2;炼钢石灰石需求量=炼钢石灰石入窑量/0.9炼钢石灰生产环节在650万吨钢规模时将产生粉料8万吨;在800万吨钢规模时将产生粉料10万吨。
3、石灰石资源的平衡分析经过多年来生产实践,矿山生产的粒级分布比例大体为:大二甲(40~80mm):小二甲(20~40mm):小石末(0~20mm)=5:3:2;而供新区的冶金石灰石因运输环节增加易产生粉料,据初步统计如果全供竖窑料其粉料将达到15%左右,若回转窑与竖窑组合其粉料可控制到10%。
烧结配料结构的研究与实践
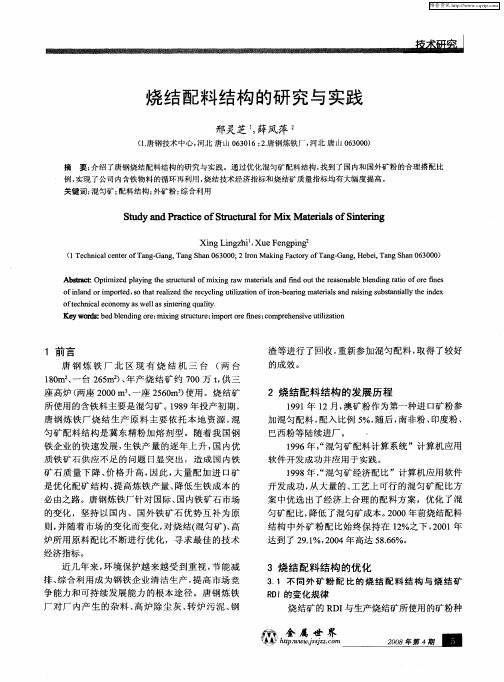
( c n cl e tro Ta gGa g Ta gS a 6 0 0 2Io a igF co yo T n ・ n g He e, n gS a 6 0 0 1 Te h ia ne f n — n , n h n0 3 0 ; nM kn a tr f a gGa , b iTa h 0 3 0 ) c r n
经济 指 标 。
19 9 8年 ,混匀 矿经 济 配 比”计算 机应 用 软件 “
开发成功 , 从大量的、 工艺上可行的混匀矿配 比方 案 中优 选 出 了经 济 上 合 理 的配 料 方 案 ,优 化 了 混
匀矿 配 比, 降低 了混 匀矿 成本 。 0 0年 前烧 结配料 20 结 构 中外矿 粉 配 比始终 保 持在 1%之 下 ,0 1 2 2 0 年 达到 了 2 . 20 91 04年 高达 5.6 %, 86%。
Ke r s b dbe dn r ; xn tu tr ;mp  ̄ oef e ;o rh n ieuiz t n ywod : e ln igo e miigs cu e i o r n sc mpe e sv t iai r i l o
1前言
唐 钢 炼 铁 厂 北 区 现 有 烧 结 机 三 台 ( 台 两
例, 实现 了公司 内含铁物料 的循环再利用 , 结技术经济指标和烧结矿质量指标均有大幅度提高。 烧 关键 词: 混匀矿 ; 配料 结构; 外矿粉 ; 综合利用
Su ya dP a t eo S r cu a rM i aeil f i tr g td r ci f t tr l o x M tras Sn e i n c u f o n
烧结配矿优化及高炉生产应对实践

M etallurgical smelting冶金冶炼烧结配矿优化及高炉生产应对实践张利波摘要:近些年,高炉炼铁一直是冶炼生铁过程中应用的最重要的技术,居于主导地位。
最近几年,全球的学者即使研究出许多高炉炼铁技术,不过在制作成本的经济性方面,依旧不能和以往的高炉制造技术进行比较。
国内,因为历史条件与制造成本的干预,非高炉炼铁技术的发展速度较慢,超过百分之九十五的生铁依旧借助高炉进行制作。
高炉生产期间,入炉原料重点是烧结矿、球团矿和块矿,而且烧结矿的比例高于百分之八十。
所以,烧结矿的品质高低在高炉生产过程中占据着主导作用,提升烧结矿品质对于缩减制作成本、保证高炉良好的运行具备着较高的作用。
关键词:烧结配矿优化;高炉生产;应对实践对策现如今使用的矿粉、矿石以及含铁工业物料等,使得烧结原料逐渐繁杂,如何通过原料的优化搭配实现品质最优、成本最优是钢铁生产重点关注的问题。
烧结矿是高炉的主要“口粮”,其质量的好坏直接影响高炉生产稳定和各项经济技术指标的完成。
为了确保烧结矿质量稳定,工作人员运用智能化手段,提升烧结配料精度,改善烧结矿质量,为高炉高效生产筑牢保障。
1 研究背景1.1 铁矿粉市场行情在我国环保政策高效实施的环境下,钢铁公司开始限制产量,铁矿石的需求数目逐渐下降。
不过在2017年~2018年鉴因为钢铁利润空间的变化,个别产能被释放,导致铁矿石的需求数目逐渐提升。
身为铁矿石的出产地澳大利亚与巴西境内铁矿石的出产量也随之增加,不过市场依然处于供需不平衡的状态,导致铁矿石的流通价格较高。
并且,因为持续的挖掘与应用优质资源,导致地球上的优质铁矿石数量逐步的减少,铁矿石供需框架的调节会是后期国际上需要一起面临与开展的工作。
我国铁矿石的存储数量位于世界前列,大约为整体存储量的百分之十二,整体的应用潜力较高。
由于铁矿的开采、加工工艺的提升,铁矿资源的整体应用会呈现出良好的经济性。
1.2 烧结配矿结构优化的理论基础低品矿粉为减少烧结资金投入最为重要的方式,不过品味下降可能导致非铁元素的高效提升,造成烧结矿品质降低,为后续高炉生产留下隐藏的危害,科学的应用铁矿粉高温特性展开烧结配矿,能够提升烧结配矿的效果。
120t转炉熔剂结构优化实践
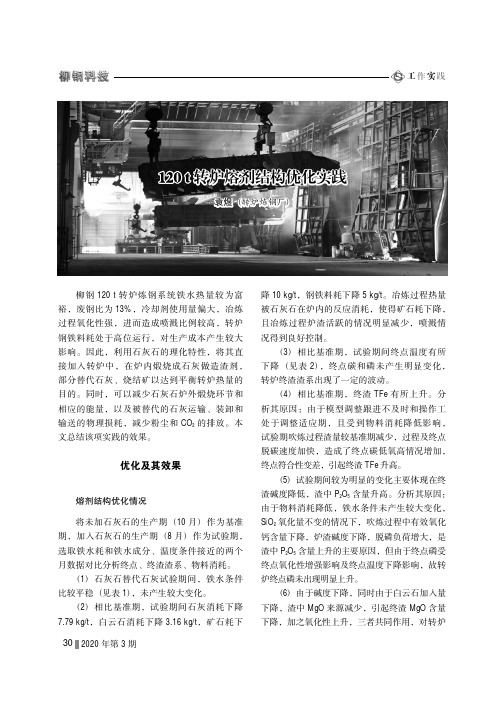
2020年第3期柳钢120t 转炉炼钢系统铁水热量较为富裕,废钢比为13%,冷却剂使用量偏大,冶炼过程氧化性强,进而造成喷溅比例较高,转炉钢铁料耗处于高位运行,对生产成本产生较大影响。
因此,利用石灰石的理化特性,将其直接加入转炉中,在炉内煅烧成石灰做造渣剂,部分替代石灰、烧结矿以达到平衡转炉热量的目的。
同时,可以减少石灰石炉外煅烧环节和相应的能量,以及被替代的石灰运输、装卸和输送的物理损耗,减少粉尘和CO 2的排放。
本文总结该项实践的效果。
优化及其效果熔剂结构优化情况将未加石灰石的生产期(10月)作为基准期,加入石灰石的生产期(8月)作为试验期,选取铁水耗和铁水成分、温度条件接近的两个月数据对比分析终点、终渣渣系、物料消耗。
(1)石灰石替代石灰试验期间,铁水条件比较平稳(见表1),未产生较大变化。
(2)相比基准期,试验期间石灰消耗下降7.79kg/t ,白云石消耗下降3.16kg/t ,矿石耗下降10kg/t ,钢铁料耗下降5kg/t 。
冶炼过程热量被石灰石在炉内的反应消耗,使得矿石耗下降,且冶炼过程炉渣活跃的情况明显减少,喷溅情况得到良好控制。
(3)相比基准期,试验期间终点温度有所下降(见表2),终点碳和磷未产生明显变化,转炉终渣渣系出现了一定的波动。
(4)相比基准期,终渣TFe 有所上升。
分析其原因:由于模型调整跟进不及时和操作工处于调整适应期,且受到物料消耗降低影响,试验期吹炼过程渣量较基准期减少,过程及终点脱碳速度加快,造成了终点碳低氧高情况增加,终点符合性变差,引起终渣TFe 升高。
(5)试验期间较为明显的变化主要体现在终渣碱度降低,渣中P 2O 5含量升高。
分析其原因:由于物料消耗降低,铁水条件未产生较大变化,SiO 2氧化量不变的情况下,吹炼过程中有效氧化钙含量下降,炉渣碱度下降,脱磷负荷增大,是渣中P 2O 5含量上升的主要原因,但由于终点磷受终点氧化性增强影响及终点温度下降影响,故转炉终点磷未出现明显上升。
涟钢二烧配加钢渣熔剂粉的生产实践

按照烧 结矿 碱度 R=17 .5组织 配 矿 , 二
烧 中和粉堆分别配人 O 0 5 、%、 %钢 %、.% l 2 渣熔剂粉后 , 配矿具体见表 2 表 5 一 。
( 碱度 :.5 17 )
表 2 中和粉不配钢渣熔剂粉配矿
・
l ・ 3
表 4 中和粉配用 1 钢渣熔剂粉配矿 %
( 度 :.5 碱 17 )
烧结熔剂用量 的影响 ห้องสมุดไป่ตู้ 将生石灰折 算成石粉 , 则石粉总量用 G折表 示, G折 =石 粉 ( %)+生石灰 ( ){ 6 5 其 中生石 灰 % 7 / 2, 按含 C O 7 %计算 , a 6 石粉按含 C O 5 %计算。 a 2
从 表 8可 以看 出 , 加钢 渣熔 剂粉 之后 , 配 烧结料 层透 气 性得 到改 善 , 间 通过 提 高 料 车 层厚 度及压 料 , 结配 重 、 用系数 均 呈上升 烧 利
一
踮 ; 2 铝
{ 昭 。
o m m = 卯
盯
叭噼
从表 2一表 6可 以看出, 在保证烧结矿 碱度 ( .5 及 其 它物 料 品种 不 变 的情 况 下 , 17 ) 二 烧 随着配 入钢 渣熔 剂 粉 比例 的升 高 ( 高 不
于 2 )烧 结矿 品位不 断下 降 , 5.0 % , 从 68 %下 降到 5 . 8 ;P含量 不 断 上 升 , 0 0 4 64 % 从 . 8 % 升高 到 0 06 ; .9 % 吨烧 结 矿 含 铁 原 料 成 本 下 B一1# C一1# 8、 9J  ̄在相 同的碱 度 R=17 .5下 组织 生产 , 烧结 机运 行参数 情况 如表 7 其 。
12 实际 生产情 况 .
二 烧 (8 m 2 0 烧 结 机 ) B一1 # C一1# 6、 7、
阳春新钢铁超厚料层烧结生产实践

阳春新钢铁超厚料层烧结生产实践摘要:随着高炉精料工作的进步与铁水产能的提升,提高烧结矿入炉量,对保障高炉入炉熟料率、支撑高炉高产低耗体系具有重要意义。
阳春新钢铁180m2烧结机在不进行大量的设备改造前提下,通过改善布料、点火强化、合理分配风量、稳定料温、优化操作等措施,料层厚度由原设计的700 mm逐步提高到了940 mm,烧结矿入炉量显著提高,固体燃耗大幅下降,取得了良好效果。
Production practice of ultra thick layer sintering ofYang Chunxin iron and Steel CompanyChen Fei-long(Yang Chunxin Steel Co.,Ltd.,Guangdong Yangchun 529629)Abstract: as the pellet price continues to rise, the premium of pellets and pulverized coal is expanded, and increasing the sinter entry volume is of great significance for ensuring the rate of clinker in the blast furnace, supporting high and low consumption of blast furnace and reducing the cost of ore matching. Under the premise of no larger equipment transformation,the thickness of the material layer of Yang Chunxin steel 180m2 sintering machine has gradually increased from 700 mm of original design to 940 mm. By improving thedistribution condition, distributing air volume and igniting intensification, sinter entry volume is obviously increased, solidfuel consumption has decreased, and good results have been achieved.引言阳春新钢铁有限责任公司(以下简称新钢铁)炼铁厂共有2台180平米烧结机,分别于2009年12月和2011年1月投产。
- 1、下载文档前请自行甄别文档内容的完整性,平台不提供额外的编辑、内容补充、找答案等附加服务。
- 2、"仅部分预览"的文档,不可在线预览部分如存在完整性等问题,可反馈申请退款(可完整预览的文档不适用该条件!)。
- 3、如文档侵犯您的权益,请联系客服反馈,我们会尽快为您处理(人工客服工作时间:9:00-18:30)。
优化烧结熔剂配料结构
提高烧结产质量攻关实践
1 前言
我厂原15.4m2的烧结机经过三次扩容改造,现烧结机有效面积为25.34m2。
2004年9月30日,作为2#高炉扩容改造最大配套改造项目——烧结系统改造完成,点火生产。
此次改造,烧结机设计台时产量49t,年烧结矿生产能力将达到40万t。
但在实际生产过程中烧结机台时产量从未达到设计能力,平均仅为44.08t/台时,烧结矿合格率为76.76%(2004年10月至2006年6月统计指标,见附表)。
三座高炉因烧结矿比例结构很低,仅维持生产了七个月时间,被迫组织两座高炉生产,而烧结矿配比也在55%以下,高炉炉料结构不合理,严重制约了高炉生产的稳定顺行和经济指标的提高。
因此,如何提高烧结台时产量,提高烧结矿合格率,使烧结矿产质量稳定提高,已成为我厂的迫切要求。
为此,我们从影响烧结矿产质量指标的各个方面(如原料、设备、生产组织)入手,进行了分析和技术攻关,使烧结台时产量大幅度提高,平均为51.02t,超攻关目标3.02t,烧结矿合格率有了进一步稳定和提高,平均达88.92%,比攻关目标提高8.92%。
2 原因分析
2.1烧结铁料粒度:烧结料中烧结矿粉、球团矿粉、原矿粉粒度较粗,﹥8mm平均占36%,最高时﹥8mm占到70%,且粒级差大,
原矿粉粒度波动尤为突出。
2.2 熔剂成份:烧结配料熔剂有石灰石、生石灰、消石灰三种,品种多,CaO含量低,成分波动大。
尤其是消石灰粉由多个厂家提供,CaO在5
3.24-66.67%之间,平均仅为59.53%,SiO2在2.54-12.9%之间,平均约为 6.89%,H2O在10%-20%,平均约为16.11%,水分、化学成分波动极大,且生烧严重,同时多家消石灰不能均衡进货,中和混匀工作难以作为。
2.3 熔剂粒度:石灰石粉﹤3mm达85%以上,生石灰粉﹤3mm 达95%以上,二者相对稳定,能够基本满足生产需要。
消石灰粉﹤3mm在70-75%之间,主要问题有二:一是未完全焙烧的大粒度石灰石,在烧结过程中生成生石灰,进入成品烧结矿,影响烧结产质量指标;二是经过碾压板结的消石灰,在烧结过程中未能发生矿化反应,而以游离CaO的形态存在于烧结矿中(俗称“白点”),在吸收水分时(外喷水和大气湿分中的水)消化,导致烧结矿体积膨胀,引起烧结矿粉化。
2.4操作方面:主要是烧结预配、烧结矿粉、球团矿粉、原矿粉的打水润湿、配料、混合、看火等岗位操作人员的操作水平参差不齐,工作责任性有待加强,尤其是混合加水和看火等岗位。
2.5部分工艺设备的原因:主要表现在大料仓场地狭小、天车能力不够,预配料中和混匀不好。
热返矿不能稳定参与配料。
一二次混合效果差,生球粒度不理想。
烧结布料偏析。
头尾密封板、台车、滑道漏风严重。
烧结矿冷却效果差,成品皮带打水等。
2.6由于烧结成品料仓的先天不足和烧结矿供需矛盾,烧结碱度频繁调整,部分烧结矿要落地露天堆存入炉,致使烧结返矿粉量大幅波动,烧结配料比相应发生变化,给稳定烧结原料结构,提高烧结矿产质量指标带来极大影响。
3 采取的措施
3.1逐步减少熔剂品种,增大生石灰配料量,取消消石灰。
第一步:5月26日,消石灰配料量由6%降低到2%,生石灰配料量增加到6%,6月6日,生石灰配料量固定为6.5%。
第二步:6月22日,消石灰停止配料,烧结配料熔剂为生石灰和石灰石,生石灰配料量固定为6.5%,用石灰石调整烧结碱度。
3.2提高生石灰质量,加强中和混匀工作。
劳动服务公司在努力提高立窑生石灰质量的同时,强化对土窑生石灰的生产管理,下功夫解决土窑生石灰“两高两多一低”的问题,即生过烧率高、SiO2高、煤粉多、煤矸石多、CaO低。
同时,劳动服务公司和原料车间积极配合,按照土窑和立窑生产的生石灰量进行搭配混匀,加强生石灰成份稳定工作。
3.3通过对生石灰破碎设备的改进,生石灰加工能力提高2t/h,为增加生石灰用量创造了良好的条件。
原料车间进一步加强生石灰破碎设备维护保养,提高设备作业率,保证生石灰配料量。
3.4强化岗位工作标准,加强操作制度落实。
生石灰配料量增加后,对烧结加水配碳等操作提出了新的要求,为此采取了以下措施:
①严格按规定对烧结球团返矿粉、原矿粉、除尘灰等进行初步混匀,强化打水润湿和翻倒作业,提高混料作用,稳定返矿和混合矿水份,从而为提高烧结矿的产质量打下基础;
②调整7#精矿粉仓圆盘给料量,适当增加料流量,保证生石灰布在底料上,减少环境污染,减轻工人劳动强度;
③配料室严格操作,提高配比准确性,加强打水工作,提高生石灰消化效果;
④保证热返矿压仓操作,并根据料批大小及时调整配料量,给一次混合水分稳定创造条件;
⑤一次混合及时调整加水量,使水分受配料室变料、返矿量波动的影响减少到最小程度,为二次混合提高成球速度和成球率打好了基础;
⑥加强看火操作,提高岗位工的判断能力,准确反馈水碳信息,及时对布料及点火状况进行检查,发现并处理问题,以保证布料平整和点火质量,稳定烧结过程,保证烧透烧好。
⑦加强交接班制度,严肃生产工艺纪律,减少或消除交接班引起的烧结产质量波动。
3.5加强组织管理,稳定生产。
①烧结工长努力发挥当班生产组织第一责任人的作用,加强生产的组织与协调,强化对配料、混合、烧结等关键工序的控制,保证操作制度较好地贯彻落实。
②攻关组加强对烧结各岗位技术规程的执行情况进行检查,
对发现的问题及时提出整改要求。
重点对生石灰的生产和混匀、焦粉粒度组成、混合料水分、返矿粉润湿、烧结配料、看火操作等工艺环节加大了检查力度。
③各部门密切配合,加强信息沟通,强化对烧结熔剂质量的管理,为烧结生产创造了有利的条件。
4 提高烧结产质量攻关所取得的成果和经济效益
经济效益计算:
⑴熔剂采购成本降低
价差:148.49元/t(1—6月份消石灰平均结算价)-120元/t (生石灰结算价)=28.49元/t
月降低成本:1535×28.49=4.37万元
年降低成本:18420×28.49=52.479万元
⑵可比烧结矿成本效益
6、7月份
增产使烧结矿工资及附加、制造费用分别下降 2.53元/t和2.41元/t;
在烧结矿碱度不变的情况下,用生石灰取代消石灰后,熔剂中有效CaO含量升高,烧结配料熔剂单耗下降,费用分别降低2.02元/t和2.41元/t;
6月份经济效益为:23624.02×4.55=10.75万元。
7月份经济效益为:23492.32×4.82=11.32万元。
两月平均效益为:11.04万元。
年效益为:11.04×12=132.48万元。
⑶合计年经济效益为:132.18+52.479=184.959万元
用生石灰取代消石灰后,烧结配料焦粉单耗下降、以及动力费等因无可比性产生的经济效益忽略。
从高炉生产来看,入炉烧结矿比例升高5个百分点以上,高炉炉料结构有了新的改善,炉况顺行程度显著提高,焦比降低,产生的间接效益未计。
5 结语
通过分析我厂烧结生产现状,采取一系列行之有效的措施,开展工艺技术攻关,使烧结台时产量大幅度提高,烧结矿合格率有了进一步稳定和明显提高,实践证明是成功的,达到了预期的效果。
从这两个月烧结攻关实践看,有些问题还有待于进一步加强和改进,如:争取更加合理的铁料组成,确立一个比较稳定的返矿粉配比;严格控制进厂原矿粉的粒度;稳定熔剂质量;加强焦粉破碎、配料、混合、烧结等关键工序生产管理,推行标准化作业,保证操作制度得以较好地贯彻落实等。
在今后的烧结生产中,要继续巩固攻关所取得的成果,不断加强生产组织管理,烧结矿的产质量指标将会更上一层楼。
攻关组
二〇〇六年八月三日。