大客车车身结构强度及刚度分析
某全铝车身客车结构强度与抗扭刚度分析

0 前言
随着城市汽车保有量的增加,汽车尾气对城市 环境的污染越来越严重,降低汽车尾气对城市环境 的污染已刻不容缓[1]。
对电动客车而言,与传统的柴油车相比,目前 仍存在一系列的问题,如续航里程不足等。而汽车 轻量化不仅可以有效缓解 污染问题,还可以很好 地降低行驶过程中的能量消耗,充分利用电池的能 量利用率。对于汽车轻量化,汽车车身的五大片所 承受的载荷较小,采用全铝车身来替代汽车的钢车 身是一种行而有效的方法。众所周知,铝的力学性 能较钢的力学性能而言,其强度和刚度都略有偏 弱。针对钢车的整车分析,目前已经有了大量的文 章[2-5],而对全铝车身结构的分析,目前相对偏少。 因此本文以某全铝车身客车为例,分别从结构的强 度和刚度两个方面进行了分析,以确保全铝车身结 构的安全性与可靠性。
对于该工况,限制左后轮所有的平动自由度,限制 左前轮横向及垂向的自由度,限制右后轮纵向及垂 向的自由度,限制右前轮垂向自由度。将上述载荷 施加到车体对应的节点上,得到的整车以及车身的 应力分布如图 2、图 3 所示。
图 4 转向工况整车应力云图
· 58 ·
Copyright©博看网 . All Rights Reserved.
《铝加工》
2019 年第 4 期总第 249 期
技术工程
节点上,得到的整车以及车身的应力分布如图 8、 图 9 所示。
图 5 转向工况全铝车身应力云图
从云图分布可以看出,在转向工况时,应力最 大值出现在底架后车桥右侧的小立柱与纵梁的焊接 部位,最大值为 112MPa;铝制车身部分最大应力 为 79MPa,出现在右侧围后部立柱铆接孔附近的加 强筋部位,小于材料的屈服强度,满足强度要求。 2.3 制动工况
表 2 有限元模型参数
车载测试中的车身结构强度与刚度测试技术

车载测试中的车身结构强度与刚度测试技术随着汽车工业的快速发展和技术的不断进步,车辆的安全性能及各种性能指标的测试已成为汽车制造商和消费者重视的焦点。
而车身结构强度与刚度是衡量汽车安全性能的重要指标之一。
本文将介绍车载测试中的车身结构强度与刚度测试技术,并探讨其在汽车设计与制造中的应用。
一、背景介绍车身结构强度与刚度是指汽车车身在受到外部载荷作用时的抗变形与抗破坏能力。
它们直接关系到车辆的安全性能和乘客的生命安全。
因此,对车身结构的强度与刚度进行准确的测试和评估是非常重要的。
二、测试方法1. 静态弯曲测试静态弯曲测试是一种常用的测试方法,通过在汽车车身上施加静载来评估车身的强度与刚度。
这种测试方法可以模拟车辆行驶过程中受到的不同载荷,如悬架系统的压力、载荷和冲击力。
通过测量汽车车身的形变和应力分布,可以评估车身的强度和刚度。
2. 动态碰撞测试动态碰撞测试是一种用来评估车身结构强度和刚度的重要测试方法。
在这种测试中,使用碰撞试验装置模拟不同方向和速度的碰撞情况,以评估车身在碰撞时的变形和损坏情况。
这种测试方法可以帮助设计师改进车辆的结构,提高碰撞时的安全性能。
3. 模态测试模态测试用于评估车身结构的固有振动特性,包括固有频率、固有振型和振动模态等信息。
通过模态测试可以了解车身结构的刚度及其在不同频率下的振动特性,以及确定设计中可能存在的问题。
这对于优化车身结构以提高刚度和减少振动有很重要的意义。
三、技术应用车身结构强度与刚度测试技术在汽车设计与制造中有着广泛的应用。
首先,它可以帮助汽车制造商评估和改进车辆结构,确保车辆在日常使用和不同情况下具备足够的强度和刚度。
其次,这些测试结果还可以为汽车工程师提供重要的数据,用于优化车身结构,提高车辆的性能和安全性。
此外,现代汽车制造业中还出现了车载测试设备的发展,这些设备可以模拟不同的驾驶条件和道路状况,以评估车辆在不同环境下的结构强度和刚度。
这为汽车设计和制造提供了更加准确和全面的数据支持。
客车车身结构强度分析
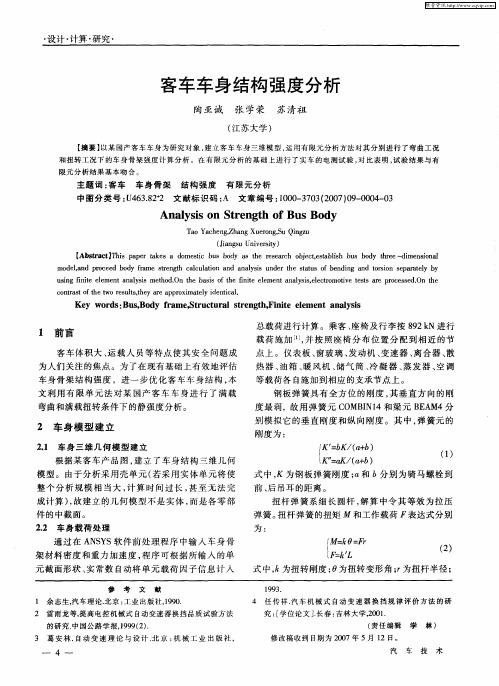
通过 在 AN Y S S软 件 前 处理 程 序 中输 入 车 身 骨
架 材 料 密度 和 重力 加 速 度 , 序 可根 据 所 输入 的单 程 元 截 面形 状 、 常数 自动 将 单元 载荷 因子信 息 计 入 实
参 考 文 献
{ 0r fk F = M =
1 3. 99
钢板 弹 簧具 有 全 方位 的 刚度 , 垂 直 方 向 的刚 其
度 最 弱 ,故 用 弹簧 元 C MB N1 O I 4和梁 元 B A E M4分 别模 拟 它 的垂 直 刚 度 和纵 向刚度 。其 中 , 弹簧 元 的
刚度 为 :
叶
弯 曲和满 载扭 转条 件 下 的静 强度 分 析 。
2 车 身 模 型 建 立
21 车 身三维 几 何模型 建 立 .
根 据某 客 车产 品 图 , 立 了车 身 结 构三 维 几 何 建
【 ” 、 K = (+b a /a K
㈩
模 型 。 由于分 析 采用 壳 单 元 ( 采用 实体 单 元将 使 若
整 个 分 析 规模 相 当 大 , 算 时 间 过 长 , 至 无 法 完 计 甚 成计 算 ) 故 建 立 的几 何模 型不 是 实 体 , 是各 零 部 , 而
主题 词 : 车 车 身 骨架 结构 强度 有 限元分 析 客 中图分类 号 : 4 38 U 6 .2 文 献标 识码 : A 文章 编号 :0 0 3 0 (0 7 0 — 0 4 O 10— 7 3 20 9 0O 一 3 J
An l sso t e g h o sBo y a y i n S r n t fBu d
c n r s ft wo r s lst y a ea r xi tl de tc 1 o ta to he t e ut , he r pp o ma ey i n ia .
客车车身结构及其设计

客车车身结构及其设计引言客车是一种用于运输大量乘客的交通工具,其车身结构的设计和构造对于乘客的安全性和乘坐舒适度至关重要。
本文将介绍客车车身结构的主要组成部分以及设计考虑因素,以帮助读者更好地了解客车的设计原理和相关技术。
车身结构的主要组成部分客车车身是由多个部分组成的,每个部分都有其特定的功能。
以下是客车车身结构的主要组成部分:车身骨架是客车车身的主要支撑结构,其目的是提供车身的刚性和稳定性。
通常采用钢材或铝合金等高强度材料制成,通过焊接和螺栓连接等方式组装。
车身壳体车身壳体是客车车身的外部覆盖部分,其主要功能是保护乘客和货物免受外部环境的侵害。
车身壳体通常由钢板或铝板等材料制成,并覆盖在车身骨架上。
车门和窗户车门和窗户是客车车身的出入口和通风窗口,其设计需要考虑开关方便、密封性好和安全性高等因素。
车门通常采用滑动门或旋转门,而窗户则通常采用拉伸式或推拉式设计。
车顶和地板是客车车身的顶部和底部部分,其设计需要考虑防水、保温、隔音和抗震等要求。
车顶通常采用弯曲或平坦的设计,而地板则采用防滑和吸音材料,并配有通风孔和排水系统。
车身设计考虑因素在客车车身的设计过程中,有几个关键因素需要考虑,以确保车身的性能和安全性。
结构强度和刚度客车车身必须具有足够的强度和刚度,以承受行驶过程中的各种静态和动态载荷。
这可通过合理选取材料和设计结构来实现,例如在关键部位添加加强筋或采用抗弯设计。
客舱空间和布局客车车身的设计应考虑乘客的舒适感和空间利用效率。
合理的客舱布局可以提供舒适的乘坐体验,并且最大程度地利用车身空间,例如通过座椅折叠和储物空间设计等。
安全性和碰撞防护客车车身的设计应考虑乘客和驾驶员的安全。
这包括提供较好的防撞能力和抗侧滑能力,以及采用合适的安全气囊和安全带等被动安全装置。
节能和环保客车车身的设计应尽量减少空气动力阻力和重量,以降低燃油消耗和减少尾气排放。
这可以通过优化车身外形和材料选择来实现,例如采用流线型外观和轻量化材料。
基于有限元的全承载式客车车身强度刚度分析

模 工作量 大。综合两 种情况 ,本文 以壳单元 为主 ,辅 以必要 的梁 单元和 弹簧单元 。全承载 式客车有 限元 分 析按 以下步骤进行 。 1 )掌握所研 究对象的结构特点 :车身骨架 由六 部
载式车身骨架 与其他两 种车身结 构相 比 ,其突 出特 点 是 没有相对独立 的底盘 车架 ,客 车载荷 主要 靠 由小截
面 型材 焊接而成 的封 闭骨架承受 。所 以全 承载式客 车
分组 成 :前 、后 围,左 、右侧 围 ,顶盖 和底 架 。其 多
数是 由几种矩形钢 管焊接而成 ,如3 X5 1 、4 0 0 . 0X X 5 5 ×1 、5 5 ×2 等 ,顶盖有安装空调和 内行李架 0 . 0 0 . 5 X 0 的埋块 。侧 围设计 有连接 座椅 的带 凹槽铝板 。底架行 李舱等处设计有增强作用 的三角板 。
sr n t n r in l t n s ft emo o o u usb d a nb n n n r in o r t g c n iins te gh a dt so a i e so h n c q eb o yf mei e dig a dt so pe ai o d to o sf l o n
2)利用 C E 析软 件 与 三维 建模 软 件 的接 口技 A分 术 ,将 客 车车 身 骨 架 三维 几 何模 型 的I E 格 式导 人 GS
H P R EH Y E M S 软件 中。HY E ME H P R S 模块最显著 的特点 是 具有强大 的有 限元 网格前 、后处理 功能 ,以不同截
车身必 须具有足 够的强度 ,保证其使 用寿命 和足够 的 刚度 ,以保证其使用要求 。
汽车车身强度与刚度分析与优化
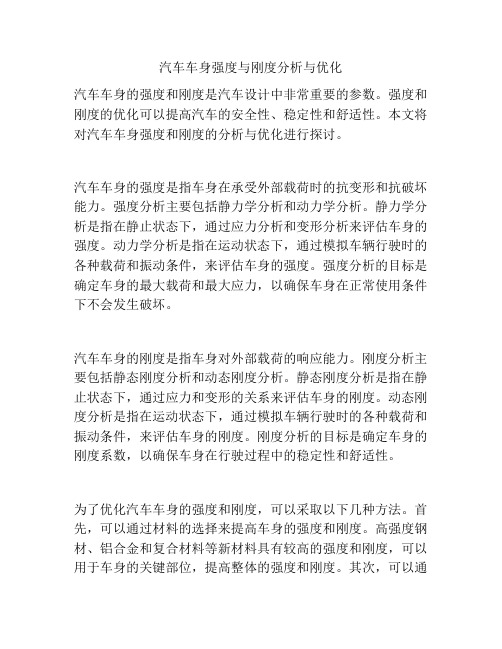
汽车车身强度与刚度分析与优化汽车车身的强度和刚度是汽车设计中非常重要的参数。
强度和刚度的优化可以提高汽车的安全性、稳定性和舒适性。
本文将对汽车车身强度和刚度的分析与优化进行探讨。
汽车车身的强度是指车身在承受外部载荷时的抗变形和抗破坏能力。
强度分析主要包括静力学分析和动力学分析。
静力学分析是指在静止状态下,通过应力分析和变形分析来评估车身的强度。
动力学分析是指在运动状态下,通过模拟车辆行驶时的各种载荷和振动条件,来评估车身的强度。
强度分析的目标是确定车身的最大载荷和最大应力,以确保车身在正常使用条件下不会发生破坏。
汽车车身的刚度是指车身对外部载荷的响应能力。
刚度分析主要包括静态刚度分析和动态刚度分析。
静态刚度分析是指在静止状态下,通过应力和变形的关系来评估车身的刚度。
动态刚度分析是指在运动状态下,通过模拟车辆行驶时的各种载荷和振动条件,来评估车身的刚度。
刚度分析的目标是确定车身的刚度系数,以确保车身在行驶过程中的稳定性和舒适性。
为了优化汽车车身的强度和刚度,可以采取以下几种方法。
首先,可以通过材料的选择来提高车身的强度和刚度。
高强度钢材、铝合金和复合材料等新材料具有较高的强度和刚度,可以用于车身的关键部位,提高整体的强度和刚度。
其次,可以通过优化车身结构来提高强度和刚度。
例如,增加加强筋和支撑结构,提高车身的整体刚度。
此外,还可以通过优化焊接和连接工艺,减少焊接接头的应力集中,提高车身的强度和刚度。
最后,可以通过模拟和仿真分析来优化车身的强度和刚度。
利用计算机辅助设计软件,可以对车身进行各种载荷和振动条件的仿真分析,以评估车身的强度和刚度,并进行优化设计。
总之,汽车车身的强度和刚度是汽车设计中非常重要的参数。
通过强度和刚度的分析与优化,可以提高汽车的安全性、稳定性和舒适性。
材料的选择、结构的优化和仿真分析等方法可以用于优化车身的强度和刚度。
随着科技的不断进步,汽车车身的强度和刚度将不断提高,为用户提供更加安全和舒适的驾驶体验。
客车车身骨架结构分析冯伟佳

客车车身骨架结构分析冯伟佳发布时间:2021-10-01T08:25:16.934Z 来源:《基层建设》2021年第18期作者:冯伟佳[导读] 客车车身的产品开发设计是一个周期较长、复杂程度高的系统工程,需要造型、结构、材料、制造等方面的技术工程师共同参与开发佛山市飞驰汽车科技有限公司 528031摘要:客车车身的产品开发设计是一个周期较长、复杂程度高的系统工程,需要造型、结构、材料、制造等方面的技术工程师共同参与开发,最终实现外观造型、满足空气动学、人机工程学、国家安全法规的要求。
随着汽车产品竞争日趋剧烈,为了快速响应市场及用户的需求,就必须缩短整车的开发周期。
客车车身骨架作为主要承载结构,其重量约占大客车总重量的30%~40%,合理的结构分析可有效地实现节能减排,在一定程度上改善汽车性能。
关键词:客车车身;骨架;结构分析一、研究目的及意义客车车身结构比较复杂,是由许多杆件通过焊接连在一起,主要构件有车身骨架、车身壳体、抗弯薄板以及覆盖件。
车身作为一个受力的整体,由于结构强度和刚度的需要,组成车身的各杆件的截面形状不同,杆件间的连接方式也是各种各样的。
其中车身骨架是客车的主要承载构件,因此,为了提高整车的性能和使用寿命,对车身骨架的性能要求比较高。
首先,在结构方面,车身骨架的布置要结合整车的布置来考虑:其次,在使用过程中,车身骨架不仅要承受各种静载荷,并且还要能够承受各种动载荷,承受的载荷有拉、压、弯曲、扭转、剪切等各种形式,而且它还必须具有足够的扭转和弯曲刚度,为确保客车在各种工况下运行时,客车车身骨架包括装于其上的其它总成及部件均不会出现疲劳破坏或是产生超出允许范围的变形,故设计人员在设计过程中需进行强度、刚度的静动态分析计算,并对其进行优化,这是非常必要的旧车身结构按承载方式可分为三类:(1)非承载式车身,这种车身结构的特点是汽车车身本体悬置于车架上,通过弹性元件与车架连接。
在这种情况下,用车架来支承整车,它承受着车身各部分总成的各种形式载荷,而车身只起到辅助承载的作用而已。
汽车车身结构的强度与刚度优化

汽车车身结构的强度与刚度优化汽车的车身结构对于汽车的强度和刚度有着至关重要的作用。
强度和刚度是指汽车车身在受力情况下抵抗外界力量的能力和保持形状稳定度的能力。
为了提高汽车的安全性和乘坐舒适度,汽车制造商在设计和制造过程中注重对车身结构的强度和刚度进行优化。
本文将就汽车车身结构的强度与刚度优化进行探讨。
一、汽车车身的强度优化汽车车身作为汽车的主要承载部件之一,其强度优化是保证汽车在受到碰撞等外部力量时保持结构完整的关键因素。
强度优化主要涉及以下几个方面:1. 材料选择与设计:汽车车身主要采用高强度钢材料,例如高强度钢板和高强度铝合金等,以提高车身的抗拉强度和抗压强度。
同时,结构设计上考虑到不同部位的应力分布情况,合理选择截面形状和连接方式,以增加车身整体的强度。
2. 刚性车身框架:刚性车身框架是汽车车身结构的基础,通过合理设计框架的形状和加强梁的设置,可以提高车身的整体刚度和强度。
此外,采用焊接、胶接等粘接技术可以增加零件之间的接触面积和接触强度,提高整体结构的刚性。
3. 正确的加强部位:在车身结构中,对于承受较大载荷的部位,如前后防撞梁、侧门梁等,在设计中应给予特别加强,以增加这些部位的强度和刚度,保护乘客在碰撞时能够得到更好的保护。
二、汽车车身的刚度优化刚度优化是指汽车车身在受到力量作用时保持形状稳定度的能力。
刚度优化能够提高汽车的操控性能和乘坐舒适度,有利于车辆稳定行驶。
以下是刚度优化的主要方面:1. 车身阻尼控制:通过在车身结构中增加阻尼材料或减振器等装置,可以有效减少车身在行驶过程中的振动和共振现象,提高车身的刚度。
这样可以有效降低噪音和震动,提高乘坐舒适度。
2. 车身加强件设置:在车身结构中适当设置加强件,如抗扭转梁、加强筋等,可以增加车身整体的刚度。
这样有利于提高车辆的操控性能,并降低车身变形的可能性。
3. 材料选择与设计:合理选择材料和结构设计,以提高车身的刚度。
比如,在车身设计中采用单体式设计,将车身各部分有机地组合在一起,可以增加车身的整体刚度。
- 1、下载文档前请自行甄别文档内容的完整性,平台不提供额外的编辑、内容补充、找答案等附加服务。
- 2、"仅部分预览"的文档,不可在线预览部分如存在完整性等问题,可反馈申请退款(可完整预览的文档不适用该条件!)。
- 3、如文档侵犯您的权益,请联系客服反馈,我们会尽快为您处理(人工客服工作时间:9:00-18:30)。
xx彩霞xx
近年来,随着城市公共交通的不断发展,在经济发达、城市化水平高的大型及特大型城市对大型城市公交客车提出了更高的要求。
对于国内的大客车而言,道路行驶条件较为严峻,通常为B级或C级路面。
客车在高低不平、崎岖起伏的道路上行驶时,整个车身骨架会产生成为车架强度主要问题的反复约束扭转应力。
因大客车车身是由空间骨架、抗弯薄板、壳体和应力蒙皮等构成的空间高次超静定结构。
各杆件结构形状各异,而且杆件之间的连接也是多种多样,骨架受力情况比较复杂,难以用经典的理论方法进行研究。
本文运用有限元方法和电测量技术对某白车身结构进行了研究,并对构件的形状、布置以及板材厚度等影响进行了分析,通过反复模拟计算,设计出满足车身刚度和强度等性能要求的轻量化结构。
1模型的建立
1.1车身骨架模型
(1)整体坐标系的建立,以通过前轴中心线的垂直平面与客车纵向对称面的交线与车架上平面的交点为坐标原点;以客车前进的反方向为X轴的正方向;以从原
点垂直向上的直线为Z轴的正方向;由右手定则确定Y轴。
(2)本文应用ANSY&S序及车身结构模型化方面成功的经验,选取某半承载框
架式结构的大客车为研究对象,该车整个骨架由矩形钢管以及钢板冲压件
通过焊接而成。
建立模型时取各构件之间的连接点、集中载荷的作用点作为有限元计算模型的节点。
根据模型的简化原则,样车车身骨架被划分为1281个长
度不等,截面形状各异的单元和783个节点,见图1。
1.2车身有限元计算时载荷的处理
(1)对于车身骨架的白重,在软件前处理程序中输入骨架材料密度和重力加速度,程序便根据所输入的单元截面形状、实常数白动将单元载荷因子的信息计入总载荷,进行计算。
(2)对乘客和座椅质量分别在相应受力点上施力。
对于车窗玻璃质量,考虑窗框质量,取系数k=
1.2,以均布载荷的形式加到车身骨架腰梁的相应单元(构件)上。
对于底盘各总成质量,以静力等效的原则按实际位置以集中载荷施加。
(3)车架的两根纵梁均为开口薄壁结构,截面形心和弯曲中心不相重合。
如图2所示,取弯心轴OL为X轴,按右手坐标系建立单元局部坐标系OXYZ 形心坐标系C,这时单元杆的轴线即为截面弯心的连线,而杆单元上的作用载荷
P
1、P2等在向节点处的简化时,有一个对纵梁产生扭转的附加局部扭矩。
1.3车身有限元计算时工况的选取
1.3.1弯曲工况
整车处于水平满载状态,施加垂直方向上的载荷,模拟客车正常行驶情况。
1.3.2弯扭工况
对于弯扭工况的选取有以下几种方案:
(1)选取一前轮上升200mm,并且一后轮下沉200mm;
(2)选取两前轮或两后轮上升或下降240mm;
(3)选取一车轮下降240mm或完全悬空。
对于方案
(1),由于实验条件所限,难以实现,方案
(2)没有第一种和第三种恶劣。
所以在实验和模型计算过程中均采用方案
(3),由于样车发动机后置,后轮悬空比前轮悬空工况恶劣得多,取左后轮悬空为弯扭工况。
2计算结果及分析
弯曲工况下车身骨架的应力水平较小,应力值大于50MPa的单元数目为49个,仅占单元总数的
3.66%。
最大应力为
101.4MPa,其位于中门后第一级台阶横梁。
同时整车应力集中区域主要有:
(1)前门xx上半部的附近区域;
(2)xxxx上半部的附近区域;
(3)前后悬架与车架和底架相连处的附近区域。
整车平均应力水平由计算结果估计大约在18MPa左右。
在满载左轮悬空的弯扭联合工况下,车身骨架的应力水平比弯曲工况下的
应力水平要高得多。
但是应力值大于50MPa的单元为116个,仅占单元总数的
8.66%。
最大应力为
122.49MPa,其位置位于中门门楣的上一根门楣梁。
整车平均应力水平由计算结果估计大约在30MPa左右。
应力集中区域主要有:
(1)xxxx附近区域;
(2)车身左侧围上与中门相对的立柱、上边梁区域;
(3)车身左右侧围上的各窗xx。
考虑到客车行驶过程中的动载荷、疲劳及材料缺陷引起的应力集中等问题,取安全系数为
1.5,则对于骨架材料Q215A钢而言,许用屈服应力[o]=
143.3MPa。
可以看出,在弯扭工况下,即使是最大应力也未超过许用应力。
左后轮悬空是最恶劣的工况,但在汽车实际行驶过程中很难遇到。
剔除由于悬架的变形而造成刚体平移的因素,总体上车身骨架的变形量相对较小。
对于车身刚度而言,从整体结构考虑,门窗对角线变形大小尤为重要。
从整理的弯曲工况下车身骨架变形网格图和计算结果可以看出,弯曲工况下各门窗对角线位移均较小,其对角线的变形量最大绝对变形量为
4.65mm,位置在前门。
最大相对变形量为
0.2%,其位置亦在前门。
从弯扭工况下车身骨架变形网格图和计算结果中可以看出在弯扭工况下,各门窗对角线位移明显增加,其对角线最大绝对变形量为
22.8mm,位于后围挡风玻璃窗。
最大相对变形量为
1.1%,其位置亦在后围挡风玻璃窗。
左侧围的窗对角线变形量均明显大于右侧围相应的窗对角线变化量。
但总体而言,本模型车身骨架的刚度较好,对角线的变形程度尚不会影响门的开启及损坏风窗玻璃。
3实验结果及分析
本次实验测试了车身满载弯曲工况、左后轮悬空扭转工况,以验证计算模型的可行性。
实验过程严格按照国家客车车身应力测试标准。
现对实验测得的结果分析如下。
3.1刚度分析
弯曲工况下车身骨架各开口处对角线的相对变形量较小,其中右三窗的窗对角线长度的长度变化量最大,前乘客门和左六窗的对角线长度变化量次之。
弯扭工况下开口比较大的区域依次排列如下:
前后风窗结构、车门结构、司机窗结构、左右侧围结构。
前后风窗开口大且只靠左右立柱加强,显然是薄弱之处。
3.2强度分析
在弯曲工况下,应力较大的部位位于中门后柱及右四窗前后立柱上以及中门附近
底架上。
最大应力值为-
41.07MPa,位于右上边梁与右四窗前柱相连处下表面。
在扭转工况下,应力集中的地方主要在中门立柱、门楣,还有中门附近的窗柱与上边梁和腰梁的连接处,以及其左侧围相应的窗立柱的上下端,其总体应力水平有所偏大。
满载扭转工况,左后轮下沉情况,最大应力位于右上边梁与中门后立柱相连处下表面,为-
118.9MPa。
应力值超过50MPa处有15处。
4结束语
采用有限元分析结合试验研究分析车身结构,是一种行之有效的方法,它能提供足够准确的车身刚度特性以及整车结构应力分布的大致规律,为设计工作提供了有价值的结构整体分析数据。
从原模型计算结果和试验结果都可以看出:
该车身骨架的高应力区共有3个部位:
(1)xxxx附近区域;
(2)车身左侧围上与中门相对的立柱、上边梁区域;
(3)车身左右侧围上各窗xx。
计算出的结果、趋势和试验所测的结果、趋势基本一致。
由计算结果知,该车在弯曲和弯扭工况下,骨架的变形和应力均较小,表明该车在静载下满足强度和刚度要求;在弯扭两种工况下,车身骨架的各单元的应力也未超过许用应力,表明该车车身结构能满足使用要求。
但与以往大客车车身骨架应力水平值相比较而言,该车的最大应力仍偏高,若考虑超载等因素,会使车身骨架结构最大使用寿命缩短,出现结构的早期破坏。
该车车身骨架主要承载构件没有形成封闭抗剪环,是车身骨架结构的主要缺点之一。
由计算结果可以看出,在弯曲和弯扭两种工况下,应力主要集中在中门附近的左右侧围的窗立柱上。
但若将车窗立柱的截面沿X方向的尺寸加大,
其应力水平明显下降。
这表明中门附近两侧是整个车身骨架中比较薄弱的部位。
新
车型加大了门立柱的尺寸,使中门附近的应力有所改善。
但是单纯用加强立柱的方法虽能使该区域的应力下降,却使别的地方的应力增大,产生负面影响。
而且,计算结果表明,加大了立柱尺寸后,车型车门和车窗立柱上应力应变仍居高不下。
因此通过改进模型计算所得到的结果表明:
根本解决方法是从整体考虑,重新构造剪力封闭环;仔细调整前后围与车身骨架其他各片之间的连接方式;增大上边梁、腰梁的尺寸;实现整体承载,增加车身骨架的刚度和强度。