低碳钢高速线材的表面缺陷及冷镦开裂原因分析
低碳冷镦钢冷镦开裂原因分析
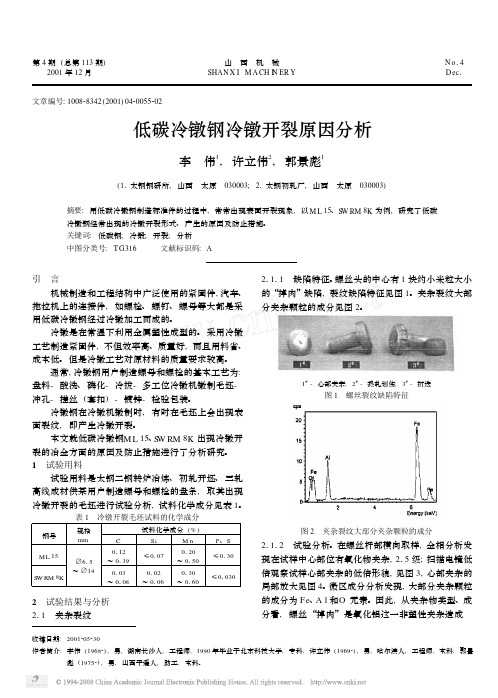
冲孔- 搓丝 (套扣) - 镀锌- 检验包装。
冷镦钢在冷镦机镦制时, 有时在毛坯上会出现表
面裂纹, 即产生冷镦开裂。
本文就低碳冷镦钢M L 15、SW RM 8K 出现冷镦开
裂的冶金方面的原因及防止措施进行了分析研究。
1 试验用料
试验用料是太钢二钢转炉冶炼、 初轧开坯、 三轧
高线成材供某用户制造螺母和螺栓的盘条, 取其出现
折迭裂纹在试样横断面对称的两侧, 各为 2 条平 行的纵向裂纹, 镦制后裂纹张开 (如螺丝头部的外缘 和冷顶锻试样的外侧) , 且裂纹内壁有轻微氧化, 每侧 裂纹的裂纹源均向 2 条裂纹中间延伸。
折迭裂纹产生的原因是, 轧制时孔型或张力等调 整、控制不当, 造成辊缝处“制耳”, 耳子轧后即为折 迭。 3 结论 311 低碳冷镦钢冷顶锻开裂主要有 3 种类型: 夹杂裂 纹、 划伤裂纹和折迭裂纹。 312 夹杂裂纹的特征是在钢材或零件表面有小米粒 大小的 “掉肉”, 留下小坑, 显微镜下为氧化物夹杂。 它是由于炼钢注温高、 注速快、 镇静时间短所致。 313 划伤裂纹的特征是沿纵向较深, 裂纹深处无氧 化、 脱碳, 是由钢材生产和吊运时表面划伤所致。 314 折迭裂纹在钢材或零件两侧对称出现, 且多为纵 向裂纹, 裂纹内壁有轻微氧化。 轧钢时应防止出现 “耳子”, 以避免出现此类裂纹。
图 4 图 3 的局部放大
212 划伤裂纹 21211 划伤裂纹特征: 螺丝头的外缘及杆部有一条纵 向裂纹, 裂纹较深, 裂纹深度的方向约沿着试样直径 方向, 裂纹内未露出内部的 “新金属” (见图 1)。 21212 划伤裂纹的金相分析: 在螺丝杆部横向取样, 观察发现, 在裂纹源处无金属夹杂, 裂纹源延伸处的 钢材组织中也无氧化、 脱碳现象。 21213 综合分析, 缺陷为热轧划伤, 原因是, ①材料 表面缺陷。常见的缺陷特征有材料 45°剪裂、炼钢夹杂
高速线材表面质量缺陷的产生原因及排除方法

高速线材表面质量缺陷的产生原因及排除方法摘要:对高速线材常见表面质量缺陷裂纹、折叠、耳子、划痕等进行了原因分析,并提出了相应排除方法。
关键词:高速线材、表面质量缺陷、原因分析、排除方法。
概述:在高速线材的生产中,成品的表面缺陷是影响产品质量的一个重要因素,其大致有以下几种:裂纹、折叠、耳子、划痕、碳化钨辊环的破裂和掉肉、麻面、结疤(翘皮或鳞皮)。
2原因分析及排除方法2.1裂纹裂纹是指线材表面沿轧制方向有平直或弯曲、折曲,或以一定角度向线材内部渗透的缺陷。
裂纹长度和深度不同,在线材的长度方向上都能发现。
有的裂纹内有夹杂物,两侧也有脱碳现象。
2.1.1线材表面产生裂纹的主要原因在于钢坯上未消除的裂纹(无论纵向或横向)、皮下气泡及非金属夹杂物都会在线材表面造成裂纹。
连铸坯上的针孔如不消除,经轧制被延伸、氧化、溶解就会造成成品的线状发纹。
针孔是连铸坯的重要缺陷之一,不显露时很难检查出来,应特别予以注意。
高碳钢线材轧制后冷却速度过快,也可能造成成品裂纹,后者还能出现横向裂纹。
轧后控冷不当形成的裂纹无脱碳现象伴生,裂纹中一般无氧化铁皮。
另外坯料清理不好也会产生此类问题。
轧制过程中形成裂纹的原因主要有以下几点:(1)轧槽不合适,主要是尖角和轧槽尺寸有问题。
(2)轧槽表面太粗糙或损坏。
(3)粗轧前几道导卫的划伤。
(4)粗大的氧化铁皮轧进轧件表面及内部,而且这通常在粗轧前几道产生。
(5)导卫使用不当主要是尺寸太大。
2.1.2若产生裂纹,应从以下几方面进行检查,排除故障:(1)高压水除鳞是否正常工作,是否某架轧机轧辊的冷却水路被堵塞或偏离轧槽。
(2)导卫是否偏离轧制线,有无氧化铁皮堵塞在某个导卫中。
(3)轧槽是否过度磨损或因处理堆钢事故时损伤了轧槽。
(4)精轧机是否有错辊,导卫是否对中及尺寸是否对应于所轧的规格。
2.2折叠线材表面沿轧制方向平直或弯曲的细线,以任意角度渗入线材的表面内,在横断面上与表面呈小角度交角状的缺陷多为折叠,通常折叠较长,但亦有间断的不连续的,并在线材的长度方向上都有分布,折处的两侧伴有脱碳层或部分脱碳层,折叠中间常存在氧化铁夹杂。
冷镦钢开裂成因分析及质量改进

冷镦钢开裂成因分析及质量改进冷镦钢是一种用途广泛的金属材料,常常用于制作螺栓、螺母等零部件。
在生产过程中,冷镦钢有时会出现开裂的情况,这不仅影响了产品的质量,也增加了生产成本。
对冷镦钢开裂的成因进行分析,并提出质量改进的措施,对于企业的生产和发展具有重要意义。
冷镦钢开裂的成因分析主要包括以下几个方面:原材料质量、冷加工工艺、设备状况、操作技术以及质量控制等方面。
首先是原材料质量。
冷镦钢的开裂与原材料质量有着密切的关系,如果原材料中含有过多的夹杂物、气孔等缺陷,或者材料的组织不均匀,都会导致冷镦钢在冷加工过程中出现开裂的情况。
其次是冷加工工艺。
冷加工工艺的参数设置不当、过程控制不严等因素都可能导致冷镦钢开裂。
冷加工时温度过低或者过高、冷加工过程中受力不均匀等,都会对冷镦钢的质量产生不利影响。
再者是设备状况。
设备的磨损、老化或者不合理的设计都可能导致冷加工过程中对冷镦钢造成损伤,从而引起开裂。
操作技术也是一个重要的因素。
冷加工过程中操作者的技术熟练程度、操作规范程度等都会影响冷镦钢的开裂情况。
如果操作不当、经验不足,都会加剧冷镦钢开裂的风险。
最后是质量控制。
如果生产过程中的质量控制不严格、产品检验不到位,都会让质量不合格的冷镦钢流入市场,增加了产品开裂的风险。
针对以上分析的成因,我们公司提出了以下质量改进措施。
首先是加强原材料的质量控制。
在原材料采购环节,加强对原材料的检验,确保原材料的质量符合要求。
对有质量问题的原材料,及时进行退货处理,避免不良原材料影响产品质量。
其次是优化冷加工工艺。
通过对冷加工工艺参数的优化调整,确保冷加工过程中的温度、压力、速度等参数在合理范围内,减少冷镦钢在冷加工过程中的应力集聚,降低开裂的风险。
再者是加强设备维护和更新。
定期对冷加工设备进行检查、维护和更新,确保设备处于良好的工作状态,避免设备老化和磨损给冷镦钢的质量带来影响。
加强操作技术培训。
对操作者进行系统的技术培训,提高操作者对冷加工过程的理解和技术水平,降低操作不当造成的产品质量问题。
冷镦钢开裂成因分析及质量改进

冷镦钢开裂成因分析及质量改进【摘要】冷镦钢在生产过程中容易出现开裂问题,影响产品质量和生产效率。
本文通过分析冷加工工艺、开裂原因,探讨质量改进策略和监控方法,提出改进生产工艺的建议。
总结认为,冷镦钢开裂问题可通过调整工艺参数和提高生产控制水平来解决,未来可深入研究开裂机理、优化材料配方等方面。
希望通过本文的研究,能够为解决冷镦钢开裂问题提供有效的参考,推动行业质量水平的提升。
【关键词】冷镦钢、开裂成因、质量改进、冷加工工艺、性能影响、质量监控、生产工艺、根本解决方法、研究方向、总结、展望。
1. 引言1.1 冷镦钢开裂成因分析及质量改进冷镦钢是一种常用的金属材料,广泛应用于汽车、机械制造等领域。
冷镦钢在生产过程中经常出现开裂现象,严重影响产品质量和生产效率。
对冷镦钢开裂成因进行分析,并提出质量改进方案至关重要。
本文旨在对冷镦钢开裂成因进行深入分析,探讨影响冷镦钢性能的冷加工工艺因素,并从根本上解决冷镦钢开裂问题。
通过对冷镦钢开裂原因的探讨和质量改进策略的提出,希望能够引起相关行业的重视,提升产品质量和企业生产效率。
在本文中,我们将首先分析冷加工工艺对冷镦钢性能的影响,探讨冷镦钢开裂的根本原因,并提出质量改进策略。
接着,我们将介绍冷镦钢质量监控方法,以及改进冷镦钢生产工艺的具体措施。
我们将总结冷镦钢开裂的根本解决方法,并提出未来研究方向,展望冷镦钢质量改进的发展方向。
希望通过本文的研究,能够为相关行业提供参考,促进冷镦钢质量的提升和行业的发展。
2. 正文2.1 冷加工工艺对冷镦钢性能影响分析冷加工工艺是冷镦钢生产过程中至关重要的环节,其对冷镦钢的性能影响非常显著。
在冷加工工艺中,冷镦钢的变形应力和应变量会大大增加,这会导致冷镦钢的晶粒变形和排列发生变化,从而影响其力学性能。
冷加工过程中会产生大量的加工硬化作用,使得冷镦钢的硬度和强度明显提高,但同时也容易导致其脆性增加,从而增加冷镦钢开裂的风险。
在冷加工工艺中,温度、速度、压力等参数的控制也对冷镦钢的性能有着直接的影响。
冷镦钢开裂成因分析及质量改进
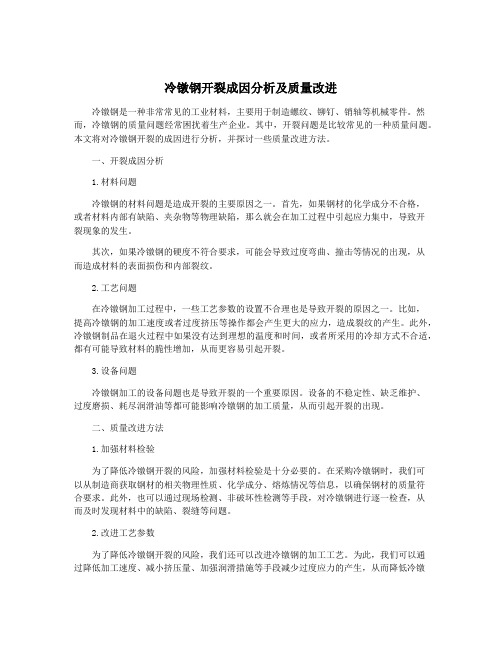
冷镦钢开裂成因分析及质量改进冷镦钢是一种非常常见的工业材料,主要用于制造螺纹、铆钉、销轴等机械零件。
然而,冷镦钢的质量问题经常困扰着生产企业。
其中,开裂问题是比较常见的一种质量问题。
本文将对冷镦钢开裂的成因进行分析,并探讨一些质量改进方法。
一、开裂成因分析1.材料问题冷镦钢的材料问题是造成开裂的主要原因之一。
首先,如果钢材的化学成分不合格,或者材料内部有缺陷、夹杂物等物理缺陷,那么就会在加工过程中引起应力集中,导致开裂现象的发生。
其次,如果冷镦钢的硬度不符合要求,可能会导致过度弯曲、撞击等情况的出现,从而造成材料的表面损伤和内部裂纹。
2.工艺问题在冷镦钢加工过程中,一些工艺参数的设置不合理也是导致开裂的原因之一。
比如,提高冷镦钢的加工速度或者过度挤压等操作都会产生更大的应力,造成裂纹的产生。
此外,冷镦钢制品在退火过程中如果没有达到理想的温度和时间,或者所采用的冷却方式不合适,都有可能导致材料的脆性增加,从而更容易引起开裂。
3.设备问题冷镦钢加工的设备问题也是导致开裂的一个重要原因。
设备的不稳定性、缺乏维护、过度磨损、耗尽润滑油等都可能影响冷镦钢的加工质量,从而引起开裂的出现。
二、质量改进方法1.加强材料检验为了降低冷镦钢开裂的风险,加强材料检验是十分必要的。
在采购冷镦钢时,我们可以从制造商获取钢材的相关物理性质、化学成分、熔炼情况等信息,以确保钢材的质量符合要求。
此外,也可以通过现场检测、非破坏性检测等手段,对冷镦钢进行逐一检查,从而及时发现材料中的缺陷、裂缝等问题。
2.改进工艺参数为了降低冷镦钢开裂的风险,我们还可以改进冷镦钢的加工工艺。
为此,我们可以通过降低加工速度、减小挤压量、加强润滑措施等手段减少过度应力的产生,从而降低冷镦钢开裂的风险。
如果需要进行退火处理,我们也可以控制退火温度和时间,同时改变冷却方式,从而降低材料的脆性。
设备维护是保证生产质量的重要环节,因此,我们应该定期对冷镦机进行保养和检修。
冷镦开裂

冷镦钢开裂原因分析及预防摘要介绍国内冷镦钢的生产概况,从钢坯加热、表面质量、脱碳、冷镦性能、工艺调整等方面指出冷镦钢生产的技术要求,探讨冷镦钢成品中所存在的质量问题,同时提出提高冷镦钢质量的措施。
关键词冷镦钢;表面质量;开裂;黑线前言冷镦钢盘条主要用于制作标准件螺钉,用户加工过程为:除鳞→拉拔→退火→冷镦→搓丝→热处理→电镀→入库。
预计每年全国需冷镦钢盘条约达500万吨,如此大的市场空间还吸引着国内外其他厂家的目光,因此,冷镦钢盘条具有很大的潜力市场。
由于冷镦下游产品是由线材经过多道次拉拔,热处理等工艺生产出来的,因此对冷镦钢线材的质量控制提出了很高的要求,无论是成分组织、表面质量、尺寸精度还是通条性能等方面均要求严格。
1 冷镦开裂原因在2006年9、10月份,由于高线设备改造后工艺调整不当及存在的相关问题,用户反馈在加工过程中冷镦开裂,由此产生的质量异议占异议总量的95%占以上。
我厂通过近几年的不懈努力,使冷礅钢线材实现了稳定的批量生产。
在生产实践中我们发现表面质量缺陷是导致冷镦开裂最直接的原因。
主要分三种:(1)线材表面折叠,主要是由于压下量过大、孔型过充满或导卫开口度过大,轧件尺寸过小而倒坯形成耳子,在随后的轧制过程中产生折叠。
(2)导槽、导辊、活套轮以及轧线上所有与轧件有直接接触的物体被磨损或存在棱角与毛刺,都有可能使轧件划伤而最终导致裂纹。
(3)孔型、导卫磨损严重、轧线不对中、错辊、导卫安装不当或对中不好,以及进钢时导卫晃动等,使轧件在孔型内变形不均匀,形成耳子、棱子、轧痕也是造成其后镦裂的隐患。
1.1 对称双裂纹产生原因根据以上成因,可以把镦裂分为平行双面连续裂纹、单条单面连续裂纹、断续裂纹等3种。
如图(1)和图(2)中所示为平行双面连续裂纹。
是在生产过程中轧件产生双边耳子,在后续道次图(1)图(2)轧制中形成折叠而产生。
双边耳子的产生多是由于压下调整不当、孔型过充满、各机架断面尺寸控制不合理、张力控制不稳定等引起。
冷镦钢开裂成因分析及质量改进

冷镦钢开裂成因分析及质量改进首先,冷镦钢的开裂与材料本身的内部结构有着密切的关系。
一般来说,冷镦钢的主要组成成分是铁和碳,有些低合金钢还会加入一些其他的合金元素,例如锰、钼、铬等。
这些元素在钢材中形成了各种固相与溶相,并形成了相互之间的复杂的相变关系。
在加工过程中,由于变形强度过大,致使钢材发生了位错等缺陷,造成了材料的内应力增大。
随着内应力的不断积累,最终导致了冷镦钢的开裂。
除此之外,冷镦钢的开裂现象还与外部的工艺条件有着密切的关系。
在冷镦钢的加工过程中,传统的工艺一般采用了多道工序,如毛坯加工、共轭滚后、粗拉削、精拉削等,其中每道工序都有可能引起材料的开裂,特别是在共轭滚后和粗拉削工序中更为常见。
这是因为这两个工序的加工过程都会增加钢材的塑性变形程度,导致材料的内应力增加,从而引起冷镦钢的开裂。
针对这些问题,我们可以采用以下一些措施来改进冷镦钢的质量。
首先,我们可以对冷镦钢的加工条件进行适当的优化。
例如,在毛坯加工、共轭滚后、粗拉削等工序中,应该控制变形度、速度、温度等条件,严格遵守工艺参数。
其次,我们可以采用一些新的成型工艺来降低材料的内应力。
例如,现代的冷镦钢加工工艺已经开始采用单锤冷锻、多锤冷锻等技术,这些技术都能够有效地控制变形程度,降低材料的内应力,从而减少冷镦钢的开裂。
最后,我们可以加强冷镦钢材料的质量控制,从原材料的选择、配料环节开始,大力优化生产工艺,并对检验人员进行严格的培训,确保每个生产环节都能够有效地管理和控制,从而保证冷镦钢材料的质量。
综上所述,冷镦钢的开裂现象是由许多因素引起的,其中材料本身的内部结构和外部工艺条件是主要的原因。
通过优化生产工艺、采用新的冷锻工艺等方式来降低材料的内应力,可以有效地减少冷镦钢的开裂,提高冷镦钢的质量和性能。
冷镦钢开裂成因分析及质量改进

冷镦钢开裂成因分析及质量改进冷镦钢开裂是指在冷镦加工过程中,钢材出现裂纹现象,这种现象严重影响了产品的使用性能和质量,也给生产制造过程带来了一定的损失。
深入分析冷镦钢开裂的成因并进行质量改进非常重要。
一、冷镦钢开裂的成因分析1.原材料质量不合格冷镦钢的原材料主要是钢坯,如果钢坯的质量不合格,如夹杂物含量过高、组织不均匀等,都会导致冷镦钢在加工过程中容易产生开裂现象。
2.冷加工参数设置不合理冷镦是一种冷加工工艺,如果冷加工参数设置不合理,如温度、速度、力度等方面没有精确控制,就会导致钢材变形过大、应力过大,从而引起开裂。
3.模具磨损严重冷镦加工需要使用模具,如果模具磨损严重,就会导致钢材在加工过程中受到不均匀的力度作用,从而导致开裂。
4.加工环境不合理如果冷镦加工的环境温度、湿度等因素不合理,就会导致钢材在加工过程中受到外部环境的影响,从而引起开裂。
二、冷镦钢开裂的质量改进1.严格控制原材料质量从源头上保证原材料的质量,选择质量合格的钢坯,并严格对其进行质量检测,确保原材料质量的稳定性。
3.加强模具维护及时对冷镦加工所使用的模具进行检查和保养,发现磨损严重的模具及时更换,确保模具的使用状态良好,减少对钢材的不良影响。
4.改善加工环境优化冷镦加工的环境,控制好温湿度等因素,营造一个适合冷镦加工的环境条件,减少外部环境对钢材的影响,降低开裂的风险。
5.加强质量控制在冷镦加工过程中,加强对产品质量的检测和控制,对一旦发现开裂等质量问题,及时进行处理和改进,确保产品质量符合要求。
冷镦钢开裂是一个需要认真对待并加以解决的问题,只有深入分析其成因,并从原材料质量、加工参数、模具维护、加工环境和质量控制等方面进行全面改进,才能有效预防和减少冷镦钢的开裂现象,提高产品质量和生产效率。
- 1、下载文档前请自行甄别文档内容的完整性,平台不提供额外的编辑、内容补充、找答案等附加服务。
- 2、"仅部分预览"的文档,不可在线预览部分如存在完整性等问题,可反馈申请退款(可完整预览的文档不适用该条件!)。
- 3、如文档侵犯您的权益,请联系客服反馈,我们会尽快为您处理(人工客服工作时间:9:00-18:30)。
理化检验 - 物理分册
杨卓青等 :一种新的钝化线形式
出了一种新的钝化 线形 式 ———J = 2 K ( 0. 5εF ) n · Δa ,该方程与材料的实测钝化线吻合较好 。
参考文献 :
[ 1 ] Begley J A , Landes J D. The J2Integral as a Fract ure Criterion[ A ] . Fract ure To ughness Proceeding of t he 1971 National Sympo sium o n Fract ure Mechanics , Part Ⅱ[ C ] . U SA : ASTM STP 514 , 1972. 1 - 20.
near cracks
图 5 线材表面平行裂纹形貌 Fig. 5 Parallel cracks appearance o n wire surface
图 3 线材表面单道线缺陷形貌 Fig. 3 Single liner defect s appearance o n wire surface
理化检验 - 物理分册
曾强国 :低碳钢高速线材的表面缺陷及冷镦开裂原因分析
样品
图2 图4 图6 图7 图8 图 10
Fe 29. 7 61. 8 92. 5 37. 6 11. 7 82. 0
表 1 各样品能谱微区成分分析结果
Tab. 1 Chemical compo sitio n of EDS micro2zone analyzing of each sample
关键词 : 低碳钢 ; 线材 ; 冷镦 ; 开裂
中图分类号 : T G356. 4 文献标识码 : A 文章编号 : 100124012 (2005) 0220069203
ANAL YSIS O F SU R FACE D EF EC TS AND COLD2H EAD IN G CRAC KS O F L O W CA RBON S T EEL H IGH SP EED WIR ES
ZENG Qiang2guo
(Quality Supervisio n Depart ment of Anyang Iro n & Steel Group , Co . L td. , Anyang 455004 , China)
Abstract : In t his paper , typical surface defect s of low carbo n steel high speed wires fo r cold2heading have been examined by using SEM and EDS. Co mparing t he defect s of semi2p roduct during rolling , wit h cold2heading
图 9 冷镦开裂的标准件 1 × Fig. 9 Break part s after cold2heading
图 10 冷镦开裂裂纹微观形貌 Fig. 10 Micro2appearance of cold2heading cracking
面与中间料有类似缺陷 ,见图 8 。其中白色夹杂物 的微区成分见表 1 。可以认为其与中间料的缺陷有 密切联系 。 2. 3 冷镦产品的缺陷分析
(2) 表面单道长裂纹 裂纹沿线材纵向分布 , 有的裂纹长达 30mm 以上 ,见图 3 。现场认为是轧
·69 ·
理化检验 - 物理分册
曾强国 :低碳钢高速线材的表面缺陷及冷镦开裂原因分析
图 1 线材表面裂纹簇形貌 Fig. 1 Cracks cluster appearance o n wire surface
[ 4 ] 刘永明. 焊缝热影响区断裂性能试验研究 [J ] . 力学季 刊 , 2002 ,23 (2) :157 - 163.
[ 5 ] To sal L . Comparison of t he Static and Dynamic Frac2 t ure Behavio ur of an A E2460 St ruct ural Steel [J ] . En2 gineering Fract ure Mechanics , 2000 ,66 :537 - 549.
cracks on part s , it was found t hat slag was included into steel during tapping and continuous casting and p roduced surface cracks o n wire p roduct s , which lead to cold2heading cracks.
高速线材在制作标准件时的开裂形貌 ,见图 9 。 对于没有完全贯穿的裂纹 ,在显微镜下可以看到由 外向里的裂纹扩展情形 ,裂纹尖端可见少量夹杂物 , 裂口处已成空缝见图 10 。夹杂物成分见表 1 ,杂质 元素基本上同中间料和成品材相符 ,属连铸过程中 保护渣卷入所造成 。
3 分析与讨论
通过上述对高速线材产品酸洗后表面缺陷的微 观分析 ,主要典型缺陷为表面细小裂纹簇 、单道长条 裂纹 、平行裂纹和划伤等 。其中表面微裂纹簇在宏 观上观察往往被认为是点缺陷 ,而且可见非金属夹 杂物 ;而从显微分析来看 ,其为含有夹杂的许多小裂 纹 。从成分上分析 ,主要是硅 、钙等元素 。这是在炼 钢过程中钢液没有得到净化 ,造成连铸坯生产过程 中较大夹杂物上浮被坯壳截获 ,形成皮下夹杂[2] 。 在轧制前的加热过程中 ,铸坯表层被氧化及其表层 下的夹杂物逐渐裸露 。在随后的轧制过程中 ,这种
制折叠 ,但在显微镜下观察 ,缺陷内部存在大量的混 合型复合夹杂或夹渣 ,见图 4 ,其微区成分见表 1 。
(3) 平行裂纹 线材表面另一类较典型的缺 陷 ,宏观上呈现纵向平行 、间距约 1~2mm 的两条 或两条以上的黑线 ,见图 5 。内有异物呈断续分布 , 能谱成分分析结果为单一的硅酸盐脆性夹杂物 ,它 的存在往往也导致冷镦标准件细小开裂 。
[ 8 ] 陈 篪 ,姚 蘅. 论 J 积分和裂纹顶端张开位移间的关系 [ A ] . 金属断裂研究文集 [ C ] . 北京 :冶金工业出版社 , 1978. 64 - 76.
[ 9 ] Gregory P , Gibson. Some Observatio n on J2R Curves [ D ] . U SA : ASTM STP 856. 1985. 166 - 182.
线材取样酸洗后 ,对其中具有典型特征的缺陷用扫 描电子显微镜观察[1] ,并进行微区能谱成分分析 。 通过观察 ,缺陷大致有以下几类 :
(1) 表面细小裂纹簇 宏观下 ,在线材长度方 向上裂纹呈簇状分散分布 ;在显微镜下呈分离的细 裂纹 (见图 1) ,且裂纹附近有白色片状硅质为主的 复合夹杂 (见图 2) 。微区能谱半定量分析结果 (质 量分数 ,下同) 见表 1 ,其中所含氯元素主要由于酸 洗液中盐酸引起 ,不予考虑 。
(4) 表面划伤 图 6 是典型的划伤形貌 ,划伤方 向沿轧制方向 ,缺陷较直 ,其深度浅且底部圆滑 ,缺陷
·70 ·
图 6 线材表面通长划伤形貌 Fig. 6 Scratch appearance o n wire surface
内较洁净 ,有极少数夹杂物。成分 (质量分数) 见表 1 。从成分上看 ,该类钢种成分基本上是正常的 。 2. 2 轧制中间料表面缺陷和成品缺陷的对照分析
图 4 线材表面单道线缺陷内夹杂形貌 Fig. 4 Inclusions appearance in single liner surface defect s
图 2 裂纹附近少量片状白色夹杂形貌 Fig. 2 Little lamellate white inclusio n appearance
[ 6 ] 江志业. 16MnR 钢焊缝及热影响区断裂性能的研究 [J ] . 压力容器 , 1995 ,12 (6) :464 - 468.
[ 7 ] Landes J D , Begley J A. Recent Develop ment s in J IC Testing [ A ] . Develop ment s in Fract ure Mechanics Test Met hods Standardizatio n [ C ] . U SA : ASTM STP , 632. 1977. 57 - 81.
由于冷镦成型时变形量一般在 70 %以上 ,产品 很容易产生裂纹 ,因而对用材的选择和质量都有严 格要求 。不仅要求钢材具有较高的强度和塑性指 标 ,而且还要求其具有精确的尺寸和良好的表面质 量 。安阳钢铁集团公司的高速线材机组自投产以 来 ,先后多次试制了 Q195L 钢和 C7D 钢等系列冷 镦用盘条 。该类钢种的碳含量低塑性好 ,但在加工
为了确定成品材料上的缺陷来源 ,对连铸坯轧 制成材过程中的中间道次即精轧前的中间料进行了 取样分析 。酸洗后的中间料表面在显微镜下观察 , 在其横截面上可见裂纹底部存在大量异物 ,个别地 方已经脱落 ,见图 7 。成分见表 1 ,其中含有钾 、钠等 元素 ,这是连铸过程中卷入的保护渣 。
对该炉次的成品材进行取样 ,酸洗后发现其表
Na 19. 6 8. 31 1. 85
Ti 5. 66 -
%
Zn 3. 98 -
图 7 中间料裂纹的横截面形貌 Fig. 7 Carcks apperanace on cro ss sectio n wit h
intermediat material
图 8 成品表面含异物的线缺陷形貌 Fig. 8 Liner inclusio n apperanace o n surface of p roduct
收稿日期 :2003204222 作者简介 :曾强国 (1970 - ) ,男 ,高级工程师 ,硕士 。