(完整版)电弧炉冶炼浇注工艺规程(LB)
电弧炉炼铁工艺流程

电弧炉炼铁工艺流程今天咱们来聊一聊电弧炉炼铁是怎么一回事儿。
想象一下,有一个超级大的炉子,这个炉子就像一个神奇的大盒子。
这个大盒子就是电弧炉啦。
那这个电弧炉炼铁,得先把一些东西放进去,就像我们做饭要先把食材放进锅里一样。
放进去的东西呢,有铁矿石,还有一些废铁。
比如说,就像我们玩搭积木,那些废铁就像之前搭好的小积木块,而铁矿石就像是还没加工过的新积木材料。
然后呀,这个电弧炉里会有电弧产生。
电弧是什么呢?就像我们在黑夜里看到的闪电一样,不过这个闪电是在炉子里的。
这个电弧可厉害了,它能产生特别特别高的温度。
这个温度高到什么程度呢?就好像是夏天最热的时候,你站在太阳底下,感觉都要被烤化了,但是电弧炉里的温度比那还要热好多好多倍。
这么高的温度有什么用呢?它能把放进去的铁矿石和废铁慢慢熔化掉。
就像我们把冰块放在火旁边,冰块会慢慢变成水一样,只不过这里是铁变成了铁水。
在铁熔化的过程中,会有一些杂质。
这就好比我们淘米的时候,米里面会有一些小沙子。
那怎么把这些杂质去掉呢?在电弧炉里,会有一些特殊的办法。
比如说,会有一些气体吹进铁水里,这些气体就像小扫帚一样,把杂质给扫走。
当铁水里面的杂质被去除得差不多了,铁水就变得很纯净了。
这时候的铁水就可以被倒出来,做成各种各样的东西啦。
比如说,可以做成我们家里炒菜用的铁锅,还可以做成汽车的一些零件呢。
有一个叔叔,他就在一个有电弧炉的工厂里工作。
他给我讲过一个很有趣的事情。
有一次,他们在电弧炉炼铁的时候,发现炼出来的铁水颜色不太对。
这可把大家急坏了,就像我们发现自己画的画颜色涂错了一样。
后来他们仔细检查,才发现原来是有一些特殊的杂质混进去了。
于是他们赶紧调整了炼铁的过程,最后又炼出了合格的铁水。
电弧炉炼铁就是这样一个很有趣的过程,它就像一场神奇的魔法,把铁矿石和废铁变成了有用的铁水,然后这些铁水又能变成我们生活中各种各样离不开的东西呢。
电弧炉冶炼工艺规程2013-11

山西国瑞轨道车辆装备有限公司碱性电弧炉冶炼操作工艺规程1.适用范围1.1 本规程适用于冶炼和在此环境中从事其他作业的人员。
1.2 本规程为3T碱性电弧炉冶炼操作、技术检查、工艺指导的依据。
2.使用的装备、检具、工具、材料2.1装备:3T电弧炉、6T钢水包、10T桥吊、烤包器、喂丝机、装料装备等。
2.2检具、仪器:直读光谱仪、热态电子吊秤、磅秤、快速智能测温仪。
2.3材料:废钢、铁合金、纯铝(线)、铁矿、石灰、萤石、碳化硅粉、焦炭粉、耐火材料、保温材料等。
3.冶炼前装备、检具、工具准备3.1 检查电气设备、机械传动、水冷系统、三相电极升降系统有无异常。
3.2 检查操作室内配电柜、操作平台指示灯是否正常。
3.3 检查检斤电子称、磅秤、测温仪、喂丝机、烤包器、10T桥吊工作状态是否良好。
3.4 检查直读光谱仪、送氧系统工作状态是否良好。
4.材料准备4.1铁合金材料分类存放,块度超出规定上限的要粉碎至规定范围。
4.2 造渣材料石灰要求新烧干燥,使用块度为20~80mm,粉末状石灰严禁使用;萤石必须烘烤,使用块度为20~80mm。
4.3 铁矿石必须烘烤,块度在30~100mm之间,碳化硅应干燥,使用粒度为0~3mm。
4.4铁合金料使用前必须烘烤,烘烤温度≥450℃,烘烤时间≥2小时。
5.补炉每炉钢水出炉后,应迅速扒除残钢和残渣,并用卤水镁砂修补炉内需补部位,要求高温、快补和薄补。
当炉体大修和中修后,要烘烤炉体,在炉体良好时方可冶炼生产。
6.配料及装料6.1 按生产要求钢种及吨位进行配料,配料应大小块度合适,大中小料搭配以减少加料次数6.2 配碳量:要求炉料熔清后碳量≥0.50%。
6.3 装料前在炉底铺炉料2~7%左右的石灰。
6.4 废钢应清洁、少锈,装料时尽可能密实,下部先装一斗小料,大料装在中部高温区,其次装中块或小块料,最上面装钢屑,二次加料只需加小块料。
7.熔化7.1 送电10~15分钟电极穿井后,调整电流采用最大功率送电。
电炉浇注工安全操作规程模版
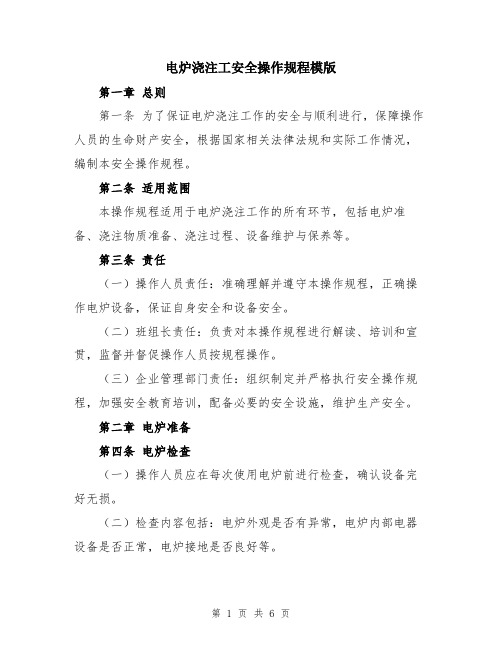
电炉浇注工安全操作规程模版第一章总则第一条为了保证电炉浇注工作的安全与顺利进行,保障操作人员的生命财产安全,根据国家相关法律法规和实际工作情况,编制本安全操作规程。
第二条适用范围本操作规程适用于电炉浇注工作的所有环节,包括电炉准备、浇注物质准备、浇注过程、设备维护与保养等。
第三条责任(一)操作人员责任:准确理解并遵守本操作规程,正确操作电炉设备,保证自身安全和设备安全。
(二)班组长责任:负责对本操作规程进行解读、培训和宣贯,监督并督促操作人员按规程操作。
(三)企业管理部门责任:组织制定并严格执行安全操作规程,加强安全教育培训,配备必要的安全设施,维护生产安全。
第二章电炉准备第四条电炉检查(一)操作人员应在每次使用电炉前进行检查,确认设备完好无损。
(二)检查内容包括:电炉外观是否有异常,电炉内部电器设备是否正常,电炉接地是否良好等。
(三)如发现设备有问题,应立即报告班组长,并由维修人员进行维修或更换设备。
第五条电源接通与断开(一)操作人员在接通电源前,应先检查电炉设备及所有电源插座、电缆的连接是否牢固,确保接线正确。
(二)接通电源时应轻按开关,确保设备启动正常;断开电源时应先关闭设备,再拔掉电源插头。
(三)不得将电炉长时间放置在开着电源的状态下。
第三章浇注物质准备第六条浇注物质的选择(一)浇注物质应符合相关标准和规定,不得使用已过期或变质的物质。
(二)不得将易燃、易爆、有毒或刺激性的物质用于电炉浇注。
(三)标明了浇注工作所需物质的容器上,必须注明物质的名称、性质、用途、生产日期和有效期限。
第七条浇注物质的储存(一)浇注物质在储存过程中应避免阳光直射、高温、潮湿等情况,确保储存环境干燥通风。
(二)浇注物质容器要放置牢靠,标示完整,不得堆放过高,防止倾倒。
(三)不得将不同性质的浇注物质存放在同一储物柜中。
第八条浇注物质的配制(一)对于需要配制的浇注物质,应根据配方要求按比例准确称量、搅拌,注意个人防护措施。
电弧炉冶炼工艺流程

电弧炉冶炼工艺流程一、原材料准备电弧炉冶炼工艺的起点是原材料的准备。
这一阶段包括将原材料(如生铁、废钢、矿石等)按照一定的比例和规格进行分类、筛选、清洗和处理,以确保其满足冶炼工艺的要求。
二、配料与投料配料是根据冶炼所需的化学成分和温度,将各种原材料按照一定的比例和顺序加入到电弧炉中。
投料过程中需注意避免不同原材料的交叉污染,确保原料的纯度和质量。
三、熔化与氧化在电弧炉中,通过电弧产生的热量将原材料熔化为钢水。
熔化过程中,通过吹氧或加入氧化剂对钢水进行氧化,以去除钢水中的杂质和气体,同时调整钢水的化学成分。
四、还原与合金化在熔化和氧化的基础上,通过加入还原剂和合金元素,对钢水进行进一步的合金化和还原处理。
这一步骤可以提高钢的力学性能和耐腐蚀性,以满足不同产品的需求。
五、钢水搅拌与成分调整通过搅拌装置对钢水进行搅拌,使钢水中的化学成分均匀分布。
同时,根据产品要求对钢水的化学成分进行微调,以确保其符合质量标准。
六、钢水温度调整与控制通过对钢水温度的监测和调整,确保钢水在浇注和连铸过程中的温度稳定和可控。
温度过高可能导致钢水氧化和吸气,温度过低则可能导致浇注困难和铸坯裂纹。
七、钢水去杂与精炼通过真空处理、喷吹氩气等手段,去除钢水中的杂质和气体,同时对钢水进行精炼,提高其纯净度和质量。
八、钢水浇注与连铸将经过处理的钢水浇注入连铸机中,通过连续铸造的过程生产出一定形状和质量的钢坯。
浇注和连铸过程中需严格控制浇注速度、冷却强度等参数,以确保铸坯的质量和性能。
九、钢坯冷却与矫直钢坯从连铸机出来后,需要进行冷却处理。
根据不同的钢种和规格,采用不同的冷却方式和设备,使钢坯逐渐降温并达到一定的硬度。
随后,通过矫直机对钢坯进行矫直处理,以消除铸造过程中产生的内应力。
十、成品检验与入库经过冷却和矫直处理后的钢坯需进行严格的检验,以确保其满足产品质量标准。
对于合格的成品,将其运输到仓库进行分类存放和标识,以备后续加工和使用。
电弧炉冶炼操作规程
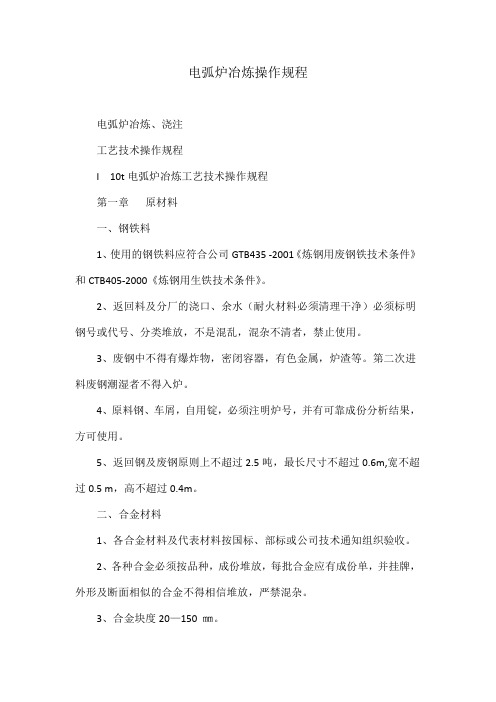
电弧炉冶炼操作规程电弧炉冶炼、浇注工艺技术操作规程I 10t电弧炉冶炼工艺技术操作规程第一章原材料一、钢铁料1、使用的钢铁料应符合公司GTB435 -2001《炼钢用废钢铁技术条件》和CTB405-2000《炼钢用生铁技术条件》。
2、返回料及分厂的浇口、余水(耐火材料必须清理干净)必须标明钢号或代号、分类堆放,不是混乱,混杂不清者,禁止使用。
3、废钢中不得有爆炸物,密闭容器,有色金属,炉渣等。
第二次进料废钢潮湿者不得入炉。
4、原料钢、车屑,自用锭,必须注明炉号,并有可靠成份分析结果,方可使用。
5、返回钢及废钢原则上不超过2.5吨,最长尺寸不超过0.6m,宽不超过0.5 m,高不超过0.4m。
二、合金材料1、各合金材料及代表材料按国标、部标或公司技术通知组织验收。
2、各种合金必须按品种,成份堆放,每批合金应有成份单,并挂牌,外形及断面相似的合金不得相信堆放,严禁混杂。
3、合金块度20—150 ㎜。
4、铁合金应保持干燥,不露天堆放,除进炉冷装外必须烘干或烘红。
5、合金必须有专用烘灶,不得混装,专用灶必须挂牌,标明合金名称及主要成份,上灶时间。
6、合金送料员按照电炉要求进行过磅后,再送电炉复磅。
7、出钢后半小时内必须收回炉前剩余合金,进入原合金灶烘烤或归于同种合金存放点。
三、造渣材料、氧化材料、脱氧材料1、石灰(1)化学成分:CaO≥88%,SiO2≤5%, S≤0.20%,P≤0.05%,MgO≤3%。
(2)使用石灰水份≤0.50%,块度30—100 ㎜,粉末及夹渣不得使用。
2、萤石(1)化学成份:CaF2≥85%, SiO2≤14.3%,S≤0.15%.(2)使用前水份≤0.10%,块度10—60 ㎜,应清洁干净。
3、白泡石(1)化学成份:SiO2≥80%,Al2O3≤18%。
(2)使用前水份≤0.30%,块度20—50 ㎜,应清洁干净,不能有粉末。
4、耐火砖块水份≤0.30%,块度≤50 ㎜。
5、铁矿(1)化学成份:Fe≥56%,SiO2≤12%,P≤0.10%, S≤0.10%。
电炉浇注工安全操作规程范本

电炉浇注工安全操作规程范本第一章总则第一条为了规范电炉浇注工安全操作,提高工作效率,保障人身和财产安全,特制定本规程。
第二条适用范围:本规程适用于电炉浇注工作,包括电炉设备的操作、维护以及与其相关的安全措施。
第三条运行原制定本规程的企业,应把本规程作为电炉浇注工作的基本规范,认真执行。
第四条所有从业人员参加工作前,必须接受相关安全操作培训,了解并遵守本规程。
第二章作业第五条电炉浇注工作必须由经过培训并持有相关证书的人员操作。
第六条在电炉操作过程中,参与浇注工作的人员必须戴上防护眼镜、防护帽、防护服、防护手套等个人防护装备。
第七条操作人员必须熟悉电炉设备的结构和主要工作原理,了解操作程序和注意事项。
第八条在操作前,必须仔细检查和保养电炉设备,保证其完好无损,确保安全。
第九条电炉浇注工作必须在安全区域进行,确保周围环境安全整洁,严禁乱堆乱放物品。
第十条在电炉设备上属于禁区的人员,必须离开工作现场。
第三章安全第十一条电炉浇注工作必须按照规定程序进行,严禁擅自进行违规操作。
第十二条按照规定操作程序进行浇注时,必须注意无尘室空气中的温度和湿度,严禁使用开火和明火。
第十三条浇注过程中,严禁穿戴松散的衣物和饰物,以免被卷入设备造成伤害。
第十四条在浇注过程中,禁止将手臂或头部靠近设备内部,以免发生意外伤害。
第十五条浇注完成后,必须立即进行设备的清理,确保设备内部干净整洁。
第十六条严禁在设备上随意搬动和更换零部件,如遇到问题,应及时通知维修人员进行处理。
第四章应急措施第十七条在电炉浇注过程中,如发生紧急情况,必须立即按照应急预案采取相应措施,并向公司相关人员汇报。
第十八条在设备发生故障或异常情况时,操作人员应立即停止工作,向维修人员反映情况,并等待维修人员进行处理。
第十九条在浇注过程中,如发现漏电、电压异常等情况,应立即切断电源,并通知维修人员进行处理。
第五章管理第二十条电炉设备必须按照相关规定进行工作记录,包括设备运行情况、维修记录、事故情况等,必要时应向相关部门汇报报告。
电弧炉冶炼浇注工艺规程(LB)
电弧炉冶炼、浇注工艺规程1.0 目的规范公司电炉熔炼操作,确保冶炼出合格钢水。
2.0 范围适用于公司电炉的熔炼。
3.0 职责3.1 技术部负责制定本规程;3.2中检站、技术部负责熔炼过程的检验。
4.0 熔炼、浇注工艺规程4.1 总则1.1本工艺系电弧炉炼钢基本操作工艺,除专用工艺另行规定外,均须按本工艺执行。
1.2本工艺为操作人员、检查人员、工程技术人员工作中的主要依据。
1.3本工艺规程适用于理邦精工10T电弧炉熔炼、浇注工序。
4.2 原材料的准备4.2.1废钢4.2.1.1大型废钢(大型机器零部件等):块重<500kg,块度<700×500×500。
4.2.1.2中小废钢(钢材及切头、锻铆件等):块重<200kg,块度<600×500×400。
4.2.1.3钢屑、轻薄料压块:块度<700×400×4004.2.1.4回炉料(浇冒口、废铸件等):块重<500kg,块度<700×500×400。
4.2.1.5废钢应按成分、块度分类存放。
不应带有冰块、砂块、有色金属等,严禁封闭容器、易爆炸物等物品入炉。
4.2.1.6炉料应无油、干燥。
油污料和严重锈蚀的炉料应清除污、锈4.2.1.7严禁装入油漆桶、涂料桶类物品入炉。
4.2.2合金及辅助材料4.2.2.1所用各种合金材料和辅助材料应保持干燥、洁净。
4.2.2.2各种材料的主要成份、块度,必须符合原材料技术要求,使用前必须清楚成份含量,并经烘烤使用。
4.2.2.3各种合金辅料使用条件及干燥温度如下表:4.2.2.4严禁使用粉化石灰造渣。
4.2.2.5电极必须存放于干燥地方,搬运时严禁破损。
4.2.2.6认真填写原材料烘干记录。
4.3 补炉与烘炉4.3.1补炉材料:补炉材料必须提前半小时混合均匀。
干式捣打料(XYD--2):含MgO>80%,堆积密度2.45-2.6;卤水(比重1:3)。
电弧炉冶炼操作(铸钢王继朋)
电弧炉冶炼操作冶炼前的准备工作原材料的准备1. 废钢的要求1)废钢根据化学成分不同分类堆放(主要是高合金钢与普通碳素钢、高合金钢与不同种类的高合金钢)。
1)废钢应清洁,少锈,少油污及无泥砂,有色金属及爆炸物禁止入炉。
废钢尺寸应适合与装料,就我车间实际操作。
细长料长度应不大于1.2mm块状炉料边长不大于800mm重型废钢单重不大于3吨为宜,过大的炉料应先切割后入炉。
1)浇冒口及废铸件上的粘砂及浇汤道需清理砂子及砖块后入炉,以免不导电而致石墨电极折断及炉衬的侵蚀。
1)增碳(炼钢)生铁必须有详细化学成分,以便还原期增碳使用。
2. 对合金的要求1)熟知各种合金的化学成分及含量,加入方法和加入时间。
注:常用合金材料性能及加入。
硅铁:主要用于脱碳剂及合金化。
硅铁中的杂质为P, Al等。
力叭时间一般为还原期稀薄渣形成后加入,含量一般75%,回收率95%左右。
锰铁:主要钢液的脱氧及合金化。
锰铁中含P量比较高(炼氧化法Mn 13寸往往P过高即此原因)。
力叭时间扒渣后随同造渣材料一起加入炉内。
含量70-78%回收率98%右。
铬铁:合金化,可分为高碳铬铁,中碳铬铁,低碳铬铁及微碳铬铁。
含量55^65%)回收率98%右。
P、S含量不高。
钼铁:合金化,钼铁属难熔合金,力叭时间在装料时同炉料一起装入或在熔化期及氧化前期力叭。
为节约用量,一般在熔毕样分析成分结果出来后按计算加入,并及时吹氧,使其完全熔化。
钼铁加入时会产生沸腾现象(称为钼沸腾)。
力口料时应将炉体向后摇起,加料人员站在路门侧面。
含量50-58%回收率98%上(按100% 计算)。
镍:还原期(后期)力叭,含量99%以上,回收率100%2)铁合金加入炉中以前需要烘烤(以除去水分及部分合金所含氢较高),块度适中。
3、造渣材料1)石灰(见表)块度要求20-80m。
粉末原则上不超过5%(S<0.15%2)萤石。
是由萤石矿直接开采而得。
改善炉渣流动性而不降低碱度,可增强渣钢面反应能力,对脱去钢液中的PS有利。
电弧炉炼钢工艺流程
电弧炉炼钢工艺流程1.准备工作:首先,需要准备好所需的废钢或生铁作为原料。
同时,还需准备好电弧炉、电源设备、废气处理系统等辅助设备。
另外,还需安排好工作人员及其岗位,以确保整个工艺流程的顺利进行。
2.上料:将准备好的废钢或生铁装入电弧炉的炉腔中。
为了确保炉料的均匀加热,需要合理布置炉料,并根据炉型的不同选择适当的上料方式。
3.加热:当上料完成后,开始对电弧炉进行加热。
通过电源设备产生电能,将电能转化为热能,使炉料快速加热。
一般情况下,电弧炉的加热温度可达到数千摄氏度,能够将炉料完全熔化。
4.合金调整:在炉料熔化的过程中,根据需要,向炉内加入适量的合金元素,以调整钢材的成分和性能。
加入的合金元素可以是合金块或合金粉末,通过电弧炉的高温将其熔化后与炉料充分混合。
5.温度控制:为了确保炉内温度的稳定,需要对电弧炉进行温度控制。
利用温度计等仪器检测炉内温度,并通过电源设备对电弧炉的功率进行调节,以维持所需的炉温。
6.炉脱硫:在炼钢过程中,废钢或生铁中含有大量杂质,其中最常见的是硫。
通过炉脱硫装置,可以将炉内硫化物与氧反应生成二氧化硫(SO2),然后通过废气处理系统排出。
7.炉脱磷:除了硫以外,废钢或生铁中还含有磷等杂质。
通过加入含氧化钙(CaO)的熔剂,使炉内的磷发生反应生成磷酸钙(Ca3(PO4)2),随后通过废渣排除。
8.合金调整:根据需要,可以在炉脱磷的过程中或炼钢结束后再次对钢水进行合金调整,以细调钢材的成分和性能。
9.出钢:当钢水炼制完成后,通过倾吊机将炉内的钢水倾出,将其倒入铸钢机进行连铸或铸坯待用,或直接进行浇注成型。
10.重复循环:一次炼钢过程结束后,可以继续进行下一次的炼钢,以提高炼钢效率。
总结:。
电炉冶炼作业指导书
电弧炉冶炼作业指导书电弧炉炼钢力求时间短、质量高、耗电少、充分利用原材料的合金元素和降低辅助的消耗,以达到冶炼出高质量、低消耗的合格钢水。
一、原材料的准备1.1原材料应少锈、少砂,防止雨水淋湿,入炉料不得含有有色金属及爆炸物。
1.2 废钢应避免油污。
对于空心物(管、盒和罐)应仔细检查出来,经开口处理后方可使用。
1.3在冶炼每一炉钢前,冶炼班应将配料单送给选料操作工,以便按炉配料,并送往炉前。
1.4入炉的铁合金必须附有成分单,成批进公司的金属料应进行主要元素的分析,并附有成分单。
合金废钢应另加分类保管,并标出合金钢牌号。
1.5入炉的石灰与萤石以及所有附加材料应是干净和烘烤过的。
石灰水分每天分析一次,水分不得大于1%,粉末状石灰严禁入炉。
二、补炉2.1保证补炉质量,以利于补炉材料能与原炉衬紧密地烧结,热补时强调高温、快速、薄补炉。
先补出钢口和炉两侧,再补渣线,厚度25~30mm为宜。
2.2 应由专人负责准备足够数量的铁耙等扒补炉工具。
出钢后应迅速清除炉门坎上的残渣和残钢。
如炉门坎烧结较好而又干净,在不影响补炉操作时可不必除掉。
2.3 补炉材料和粘结剂应由专人准备。
力求数量足,补炉材料不得附有其它杂物。
根据公司的实际情况,补炉材料:70~80% 1~3mm和20~30% 0~1mm镁砂粉及比重1.1~1.3g/cm3MgCl2≥30%的卤水,比例为镁砂:卤水≈8~10:1;也可用镁砂7~8%沥青焦油代替卤水镁砂进行补炉。
2.4 出钢后炉子复位后应迅速扒除残渣残钢,随即投补损坏严重的地方。
一般先补炉门两侧和炉门坎下的炉坡,当炉温很高,难以观察炉体损坏情况时,应根据上一炉出钢的炉体情况分析判断,立即向损坏严重处投补,然后补出钢口两侧。
2.5 若出钢口堤坡处浸蚀严重时,可用耙子推挡进行阶梯修补,并保证有良好的烧结。
2.6 评定烧结好与坏,即看新补的材料和原有炉衬一样发红时,证明烧结良好。
2.7 若需补得厚些,则应通电进行烧结。
- 1、下载文档前请自行甄别文档内容的完整性,平台不提供额外的编辑、内容补充、找答案等附加服务。
- 2、"仅部分预览"的文档,不可在线预览部分如存在完整性等问题,可反馈申请退款(可完整预览的文档不适用该条件!)。
- 3、如文档侵犯您的权益,请联系客服反馈,我们会尽快为您处理(人工客服工作时间:9:00-18:30)。
电弧炉冶炼、浇注工艺规程1.0 目的规范公司电炉熔炼操作,确保冶炼出合格钢水。
2.0 范围适用于公司电炉的熔炼。
3.0 职责3.1 技术部负责制定本规程;3.2中检站、技术部负责熔炼过程的检验。
4.0 熔炼、浇注工艺规程4.1 总则1.1本工艺系电弧炉炼钢基本操作工艺,除专用工艺另行规定外,均须按本工艺执行。
1.2本工艺为操作人员、检查人员、工程技术人员工作中的主要依据。
1.3本工艺规程适用于理邦精工10T电弧炉熔炼、浇注工序。
4.2 原材料的准备4.2.1废钢4.2.1.1大型废钢(大型机器零部件等):块重<500kg,块度<700×500×500。
4.2.1.2中小废钢(钢材及切头、锻铆件等):块重<200kg,块度<600×500×400。
4.2.1.3钢屑、轻薄料压块:块度<700×400×4004.2.1.4回炉料(浇冒口、废铸件等):块重<500kg,块度<700×500×400。
4.2.1.5废钢应按成分、块度分类存放。
不应带有冰块、砂块、有色金属等,严禁封闭容器、易爆炸物等物品入炉。
4.2.1.6炉料应无油、干燥。
油污料和严重锈蚀的炉料应清除污、锈4.2.1.7严禁装入油漆桶、涂料桶类物品入炉。
4.2.2合金及辅助材料4.2.2.1所用各种合金材料和辅助材料应保持干燥、洁净。
4.2.2.2各种材料的主要成份、块度,必须符合原材料技术要求,使用前必须清楚成份含量,并经烘烤使用。
4.2.2.3各种合金辅料使用条件及干燥温度如下表:4.2.2.4严禁使用粉化石灰造渣。
4.2.2.5电极必须存放于干燥地方,搬运时严禁破损。
4.2.2.6认真填写原材料烘干记录。
4.3 补炉与烘炉4.3.1补炉材料:补炉材料必须提前半小时混合均匀。
干式捣打料(XYD--2):含MgO>80%,堆积密度2.45-2.6;卤水(比重1:3)。
4.3.2出钢后立即检查炉况,需要补炉时,应先将炉底之剩钢、残渣全部扒出,然后进行修补。
4.3.3对炉底和炉壁被侵蚀及破坏部位进行修补,侵蚀严重处要少量多次重复补炉。
补炉的原则是“高温、快补、薄补”,维护炉膛原状。
4.3.4炉体损坏严重时,若补炉材料用量在500-700kg时,补炉后应用电极烘烤30min;若补炉材料用量超过700kg,应酌情延长烘烤时间。
4.3.5出钢槽用整体浇制特种耐火材料。
修补时不得采用水玻璃砂修补,出钢槽应干燥,流畅;更换新出钢槽时,应用木柴彻底烘烤。
4.3.6当炉体大修或中修后,或停炉时间较长时,开炉前应按要求烘烤炉衬和出钢槽,氧化期宜采用矿石脱碳,以便进一步加强炉衬的烘烤烧结。
4.3.7补炉后应认真检查炉体水冷系统,发现渗漏及时联系处理。
4.4 配料4.4.1配料前根据所炼钢种确定氧化期脱碳量,配碳量=钢种规格中限+氧化期脱碳量。
4.4.2氧化期脱碳量的确定,一般碳钢件脱碳量为0.2-0.3%,一般合金钢铸件脱碳量为:0.3-0.4%,重要合金钢铸件脱碳量为:0.4-0.5%。
大修炉后第一炉的脱碳量应在0.5%以上,中修炉后第一炉的脱碳量应在0.4%以上。
4.4.3熔清碳上、下偏差不得超过配碳量的+0.05%,若下偏差低于规格要求0.05%时,必须做增碳处理,二次化验合格后,方能进行氧化。
4.5 装料4.5.1装料前再次检查电路设备完好情况,如有故障及时修理或更新4.5.2超装量大于25%时,应与技术部门协商,方可进行。
4.5.3检查电极有无损坏,以及是否足够一炉使用,否则要及时接好,避免在冶炼过程中接放电极。
4.5.4装炉料前炉底必须先铺石灰一层,重量为炉料重的1%左右,以利于提前造渣和减轻装料对炉底的冲击,并减少热损失。
4.5.5装料应按大、中、小、轻,适当比例配加,以保证装料紧密。
装料次序为:薄铁皮或长钢屑铺底—大料—中料—小料或钢屑,高硫及大块料应放在料斗中心,以利于去硫和熔化。
渣铁避免装在电极位置,防止不导电,配加的生铁应在料斗的下中层。
4.5.6炉料入炉时,不得碰撞炉墙,如有炉料接触水冷炉盖时,一定要排除,避免起弧烧坏炉盖。
4.5.7装二次料时,要求小料和轻薄炉料,入炉速度要求快,减少热损失。
加料次数应在2次以内,不宜超过3次。
4.5.8所有入炉材料均需准确称重,并做好记录。
4.6 熔化期4.6.1在熔化初期(穿井和电极回升阶段),应满负荷送电(电压240V、电流10000-12500A),快速熔料。
4.6.2为了节约电能和提高冶炼速度,通电后45分钟—1小时后,当炉内形成钢水熔池时(炉料熔化70%左右),就开始吹氧助熔,氧压力为0.5Mpa,吹氧管插入的深度为钢渣的交界面上,吹氧管与钢水面夹角为15°,当大块炉料难于熔化时,采用吹氧切割帮助熔化,为了防止搭桥,配合吹氧进行捣料,加快熔化速度,防止搭桥塌料砸断电极。
4.6.3炉料熔化过程中,应根据炉料情况适当补加渣料。
4.6.4炉料全部熔清后,搅拌取熔清样分析C、P、S、Cu、Mn、Mo,取样应具有代表性。
4.6.5熔清碳应保证氧化期脱碳量。
碳量不足时应用生铁增碳至符合要求,并搅拌均匀,再取样分析。
4.6.6熔化末期加入适量的石灰及碎矿石,提前造好碱度与FeO含量适当且流动性良好的泡沫渣,保持渣量在3%左右。
4.6.7 熔化末期若磷含量较高,应流掉部分炉渣,做好前期去鳞操作。
4.7 氧化期:氧化期的任务是去鳞,除气和夹杂物,提高钢水的温度。
因此在低温下,提前去鳞,在高温下,借助于氧化去碳,造成熔池钢水沸腾,促使钢水中气体溢出和夹杂物上浮。
去碳只是手段,而不是目的,所以为了完成氧化期的任务,就必须有足够的温度,一定的脱碳量和脱碳时间。
吹氧氧化是提高温度,加快反应速度行之有效的方法。
4.7.1开始氧化的条件:4.7.1.1炉料全部熔清后取样化验。
4.7.1.2碳符合所炼钢种熔清碳要求。
4.7.1.3炉渣流动性良好。
7.1.4钢水温度达到1570℃以上。
4.7.2吹氧氧化的氧压为0.7—1.0Mpa,氧枪插入深度距炉渣面200mm左右,氧枪和钢水面的夹角为15°,并进行移动吹氧。
4.7.3用矿石和氧气进行综合氧化沸腾时,矿石的烘烤,块度应符合工艺要求,矿石分批加入,每吨钢水降低0.01%碳,加矿为1.2kg,矿石加入的间隔时间为5分钟4.7.4吹氧氧化用氧量为每吨钢水每脱0.10%的碳约耗氧15m³左右4.7.5在氧化期中,要保持高温沸腾均匀,自动流渣,当补加渣料时应去氧化渣,严禁产生大沸腾和抛钢现象。
4.7.6如起镁砂,应扒除部分或全部渣子,重造新渣。
4.7.7最后一批矿加工完或吹氧后,静沸腾5分钟后进行搅拌,取样分析C、P,如达到工艺要求,加锰铁进行预脱氧,锰铁的加入量为配锰量的0.20% 4.7.8氧化期总渣量为炉料重的3—3.5%左右。
4.7.9扒渣条件:4.7.9.1含碳量、含磷量符合工艺要求。
4.7.9.2钢水温度不应低于出钢温度。
4.7.9.3钢水沸腾静止。
4.7.9.4炉渣流动性良好,进行扒渣。
4.7.10扒渣应迅速、干净、以免钢水降温,吸气和回磷,同时要尽量不带出钢水。
4.7.11氧化期注意事项:4.7.11.1磷高时,自动流渣,扒去部分渣子重新造渣,保持一定的碱度。
4.7.11.2脱碳速度,每分钟脱碳0.02—0.04%。
4.7.11.3取样要有代表性,样勺插入炉内中心。
4.7.12氧化期的电力要求,按附表进行配电操作。
4.8 还原期还原期主要任务是脱氧、脱硫,获得合适的化学成份和适宜的出钢温度。
温度是完成上述任务的主要因素。
4.8.1扒渣后迅速加入锰铁(配Mn达规格中限)和稀薄渣料,薄渣料占炉料重量的0.8—1%,其配比为石灰:萤石=5:2.加完后进行搅拌,并开始封闭出钢口和电极孔。
4.8.2稀薄渣形成后,加还原造渣,其配比为石灰:萤石:碳粉:电石=3:1:1:1,重量为炉料重的1.2—1.5%,一次加完,封闭炉门,保持还原气氛20—30分钟左右,时刻注意炉内还原性气氛的良好性,及时用碳粉或碳化硅粉调节,对硫要求不高的钢种可以不加电石。
4.8.3还原期任务完成后,出钢前必须加硅铁粉破坏电石渣,用量为料重的0.08—0.09%,分批加入,渣好后(渣白)取样分析钢水成份,根据分析结果调整各元素含量。
4.8.4良好的白渣形成后加入硅铁,配硅达到规格中限,加完硅铁后,要充分搅拌,经常看温度。
4.8.5加完硅铁到出钢的时间不大于15分钟。
4.8.6还原期渣量为3—3.5%。
4.8.7还原期要确保钢水的脱氧去气含量,严禁吹氧提温及使用大电压4.8.8还原期电力曲线根据附表进行。
4.9 出钢出钢是电炉炼钢的最后一环,出钢过程中操作的好坏,直接影响到钢的质量。
4.9.1出钢应具有以下条件4.9.1.1白渣流动性良好。
4.9.1.2化学成份调整合适,达到规格要求,加入的铁合金已全部熔化4.9.1.3温度达到出钢温度(各钢种规定的浇注温度)。
4.9.1.4加硅铁后,取潮模样,收缩良好。
4.9.1.5出钢槽干燥清洁,出钢口放大,以使钢渣混出。
4.9.2出钢前,加铝量1.1—1.5kg/吨钢水(湿雨季可以加1.5kg/吨钢)加入包内预热,等待出炉。
4.9.3炉后取潮模样,收缩良好,方可浇注,并保存好备查。
4.9.4取样或测温前一定要进行搅拌,后方可进行。
4.9.5钢包充分烘烤,温度达到750℃以上(颜色暗红色)。
4.9.6钢包从停止烘烤到出钢的时间间隔<5min。
4.9.7出钢过程中应达到如下要求:4.9.7.1出钢槽平整、清洁、干燥,保持钢水流畅通,不准散流翻花。
4.9.7.2钢水流不得直接冲包壁,包柱。
4.9.7.3大口喷吐,钢渣混冲,防止钢水氧化,以利脱硫。
4.9.8出钢后在钢包内测温,并做好记录。
4.10浇注4.10.1浇注前的准备4.10.1.1浇注工必须熟悉本炉钢水材质、重量以及所浇铸件的数量、重量;4.10.1.2清除浇注通道的不安全因素;4.10.1.3检查砂箱卡子、锁箱螺栓是否紧固牢实;4.10.1.4备好草灰、发热剂、干砂、引气材料、铁锨。
水管等用具;4.10.1.5备好倒剩余钢水和渣子的地坑。
4.10.2操作要求4.10.2.1钢水出炉后要在钢包中镇静5—10分钟再浇注(重要的合金钢铸件出钢后要吹氩精炼5分钟左右,吹氩压力为0.2—0.3Mpa),具体镇静时间长短应根据出钢温度、出钢降温、钢水在钢包中的降温以及要浇注的砂箱数来决定;参见下表4.10.2.2浇注时钢包不能摆动,必须对正浇口杯,钢包底距浇口杯不得高于150—200mm;4.10.2.3按浇注顺序、工艺要求进行浇注;4.10.2.4开始浇注后的第一个铸件应是较大的铸件,以便将包底部温度较低的钢水及时放出,以保证能够关严注口,再浇小铸件,薄壁铸件和结构复杂的铸件,最后浇厚壁及结构简单铸件;4.10.2.5浇注时,浇口杯应保持充满,并不得引起钢水飞溅或漩涡;4.10.2.6浇注开始后应立即引火;4.10.2.7浇注时若发生跑火,应将大流改为小流,但不能停流,当跑火不能封堵时,应停止浇注;4.10.2.8浇注时如发生钢水猛烈沸腾,并从冒口连续喷出钢夜时,应立即停止浇注;4.10.2.9浇注剩余钢水要返回炉内或倒入专门地坑中;4.10.2.10浇注完毕,在砂箱上标注铸件名称、浇注时间、开箱时间;4.10.2.11专人记录浇注情况。