无损检测方案汇总
无损探伤方案

无损探伤方案无损探伤是一种非破坏性检测方法,通过使用物理学的原理和科学的仪器设备来检测物体的内部或表面缺陷、杂质、裂纹等。
它广泛应用于航空、航天、核能、军工、建筑、交通等领域。
本文将介绍无损探伤方案的几种常见方法。
一、磁粉探伤法磁粉探伤法是一种适用于铁、钢等金属表面、近表面缺陷的无损探伤方法。
其原理是在被检测物体表面均匀涂有铁磁性粉末,利用外加磁场引导粉末在裂纹、缺陷处留下磁纹,从而发现该处的缺陷。
磁粉探伤法灵敏度高、速度快、成本低,但只适用于铁、钢等铁磁性材料。
二、涡流探伤法涡流探伤法是一种适用于金属、导体等导电材料表面或近表面缺陷的无损探伤方法。
其原理是将交流电源通入探测器,电流在待检测金属或导体中产生涡流,从而形成磁场,利用磁场对探测器产生的信号进行检测,可以发现缺陷。
涡流探伤法灵敏度高、速度快、适用于各种导电材料。
三、超声波探伤法超声波探伤法是一种适用于大多数材料内部缺陷的无损探伤方法。
其原理是利用超声波在材料内部的传播和反射来检测材料内部缺陷。
可以通过探头的不同位置、不同方向进行检测,对材料内部的缺陷、尺寸、定位等都可以进行准确的检测。
超声波探伤法灵敏度高、适用范围广,但在检测厚度较大、表面不平整、材料吸音性较强时可能存在一定的局限性。
四、射线探伤法射线探伤法是一种适用于金属、非金属等大多数材料内部缺陷的无损探伤方法。
其原理是利用电磁波的作用直接透射材料,得到材料内部组织、缺陷等信息来实现无损检测。
射线探伤法灵敏度高、适用范围广,但需要射线源,且辐射可能对人体和环境造成危害,需要进行详细的安全措施。
五、热波探伤法热波探伤法是一种利用材料吸收热能散热规律来检测缺陷的无损探伤方法。
其原理是利用探测器对材料表面施加热源,通过测量热能的传播和分布情况来检测材料内部的缺陷。
热波探伤法适用范围广,可以检测小到几毫米的缺陷,但需要加热、冷却,操作比较繁琐。
综上所述,无损探伤方案是通过选择不同的探测方法和仪器设备,根据被检材料的不同特性来进行无损检测。
无损检测施工方案
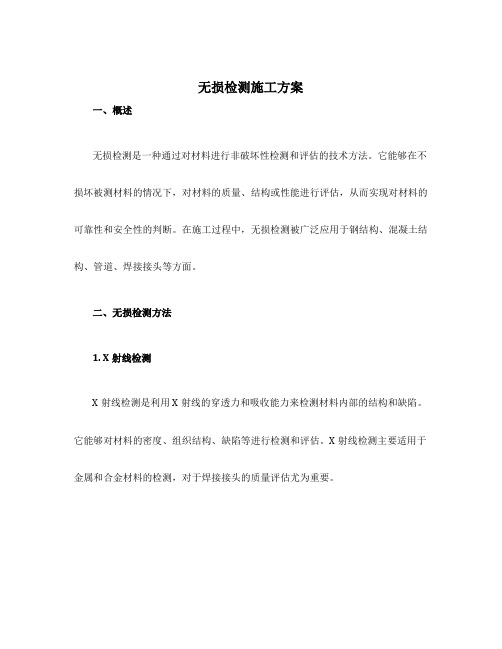
无损检测施工方案一、概述无损检测是一种通过对材料进行非破坏性检测和评估的技术方法。
它能够在不损坏被测材料的情况下,对材料的质量、结构或性能进行评估,从而实现对材料的可靠性和安全性的判断。
在施工过程中,无损检测被广泛应用于钢结构、混凝土结构、管道、焊接接头等方面。
二、无损检测方法1. X射线检测X射线检测是利用X射线的穿透力和吸收能力来检测材料内部的结构和缺陷。
它能够对材料的密度、组织结构、缺陷等进行检测和评估。
X射线检测主要适用于金属和合金材料的检测,对于焊接接头的质量评估尤为重要。
2. 超声波检测超声波检测是利用超声波在材料中的传播和反射特性来检测材料内部的结构和缺陷。
它能够对材料的厚度、波速、声阻抗等进行检测和评估,并能够定位和测量缺陷的尺寸。
超声波检测主要适用于金属和非金属材料的检测,对于混凝土结构和管道的检测具有重要意义。
3. 磁粉检测磁粉检测是利用外加磁场和磁粉的磁化作用来检测材料表面和近表层的结构和缺陷。
它能够对材料的表面裂纹、缺陷和疲劳裂纹进行检测和评估,并能够定位和测量缺陷的尺寸和形态。
磁粉检测主要适用于金属材料的表面检测,对于焊接接头和表面裂纹的检测具有重要意义。
4. 热红外检测热红外检测是利用物体的热辐射特性来检测物体的缺陷和异常情况。
它能够通过红外相机对物体的温度分布进行测量和分析,从而判断物体内部的结构和材料的性能状况。
热红外检测主要适用于建筑物、电力设备和输电线路等方面的检测,对于温度异常、能量损失等问题具有重要意义。
三、无损检测施工流程无损检测施工包括前期准备、检测方案制定、实施检测和结果分析报告等环节。
1. 前期准备在进行无损检测之前,需要对被测物体进行准备工作。
首先,要清理被测物体的表面,确保无杂质和污染物。
其次,要研究被测物体的结构和材料特性,了解其内部结构和缺陷的可能性。
2. 检测方案制定根据被测物体的特点和检测要求,制定适合的检测方案。
选择合适的无损检测方法,并确定检测仪器和设备的使用参数。
无损检测施工方案
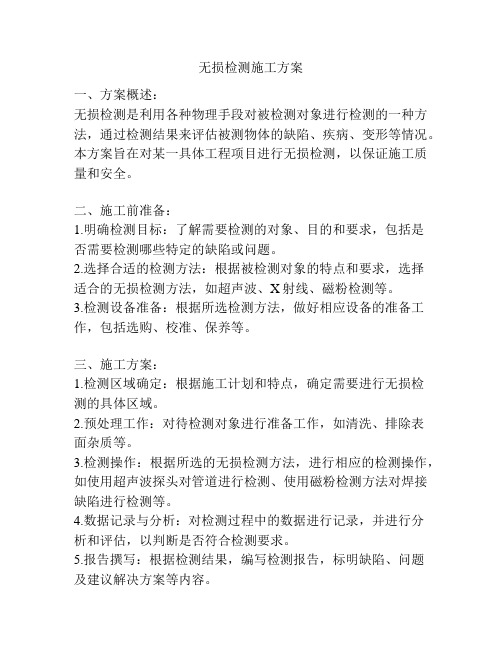
无损检测施工方案一、方案概述:无损检测是利用各种物理手段对被检测对象进行检测的一种方法,通过检测结果来评估被测物体的缺陷、疾病、变形等情况。
本方案旨在对某一具体工程项目进行无损检测,以保证施工质量和安全。
二、施工前准备:1.明确检测目标:了解需要检测的对象、目的和要求,包括是否需要检测哪些特定的缺陷或问题。
2.选择合适的检测方法:根据被检测对象的特点和要求,选择适合的无损检测方法,如超声波、X射线、磁粉检测等。
3.检测设备准备:根据所选检测方法,做好相应设备的准备工作,包括选购、校准、保养等。
三、施工方案:1.检测区域确定:根据施工计划和特点,确定需要进行无损检测的具体区域。
2.预处理工作:对待检测对象进行准备工作,如清洗、排除表面杂质等。
3.检测操作:根据所选的无损检测方法,进行相应的检测操作,如使用超声波探头对管道进行检测、使用磁粉检测方法对焊接缺陷进行检测等。
4.数据记录与分析:对检测过程中的数据进行记录,并进行分析和评估,以判断是否符合检测要求。
5.报告撰写:根据检测结果,编写检测报告,标明缺陷、问题及建议解决方案等内容。
四、施工要求:1.施工人员:由经过专业培训的无损检测人员进行,确保操作规范、准确性和安全性。
2.操作环境:提供适合的操作环境,如保持室温、降低干扰等,以确保检测过程的准确性。
3.保养维护:保养和维护无损检测设备,确保设备的正常运行。
4.安全防护:在无损检测过程中,使用符合要求的个人防护设备,确保施工人员的安全。
五、质量控制:1.制定质量控制计划:在施工前制定无损检测质量控制计划,包括检测要求、检测方法、操作标准等内容。
2.质量检查:在施工过程中进行质量检查,确保操作符合要求,并及时纠正不合格操作。
3.重要数据备份:对重要数据进行备份,以防止数据丢失造成损失。
六、施工管理:1.组织施工人员:组织好无损检测人员的工作安排和任务分配,确保施工进度和质量。
2.施工进度控制:配合工程进度安排,合理安排无损检测施工时间,确保无损检测工作的顺利进行。
无损检测方案

无损检测方案无损检测是一种通过对材料或构件进行检测,不会对其使用性能产生永久性影响的检测方法。
无损检测可以检测出材料或构件内部的缺陷,并能够识别其位置、形状和大小,帮助判断材料或构件的可靠性和使用寿命。
本文将介绍几种常用的无损检测方法及其检测方案。
1.超声波检测(UT)超声波检测是一种利用超声波在材料或构件内部传播的特性来检测其缺陷的方法。
其检测方案一般包括以下几个步骤:1)选择适当的超声波探头和频率;2)设置超声波发射和接收参数,如工作频率、发射和接收幅度、时间增益等;3)对材料或构件进行扫描,记录超声波的传播时间及幅度;4)对测得的数据进行分析,判断缺陷的位置、形状和大小。
2.射线检测(RT)射线检测是一种利用射线的穿透性来检测材料或构件内部缺陷的方法。
其检测方案一般包括以下几个步骤:1)选择适当的射线源和探测器;2)设置射线源和探测器的参数,如电流、电压、曝光时间等;3)将射线源和探测器对准待检测区域,进行曝光;4)对曝光的胶片或探测器图像进行观察和分析,判断缺陷的位置、形状和大小。
3.磁粉检测(MT)磁粉检测是一种利用磁场和磁粉的性质来检测材料或构件表面和近表面缺陷的方法。
其检测方案一般包括以下几个步骤:1)选择适当的磁场源和磁粉;2)在待检测区域施加磁场,并撒布磁粉;3)观察磁粉在缺陷处的聚集情况,判断缺陷的位置、形状和大小。
4.涡流检测(ET)涡流检测是一种利用交变磁场在导电材料中产生涡流而检测材料或构件表面缺陷的方法。
其检测方案一般包括以下几个步骤:1)选择适当的涡流探头和频率;2)设置涡流探头的参数,如工作频率、发射幅度等;3)将涡流探头对准待检测区域,进行扫描;4)观察涡流信号的变化,判断缺陷的位置、形状和大小。
以上是常用的几种无损检测方法及其检测方案的简要介绍。
在实际应用中,根据材料或构件的特点和具体要求,可以根据这些方法的优缺点选择合适的方法,并制定相应的检测方案来进行无损检测。
无损检测项目实施方案
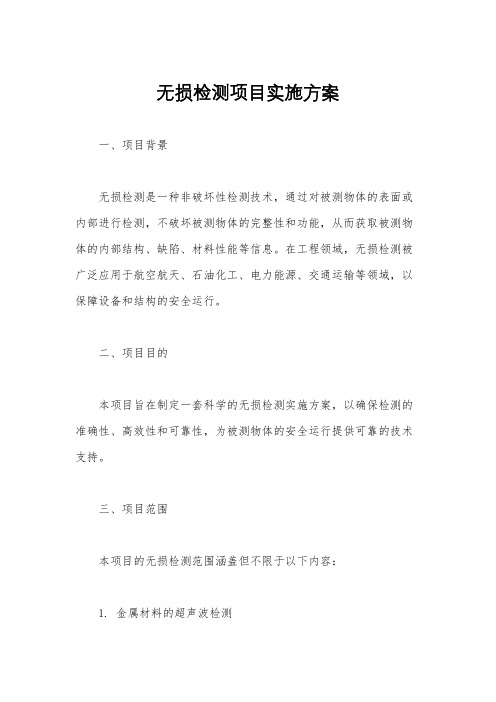
无损检测项目实施方案一、项目背景无损检测是一种非破坏性检测技术,通过对被测物体的表面或内部进行检测,不破坏被测物体的完整性和功能,从而获取被测物体的内部结构、缺陷、材料性能等信息。
在工程领域,无损检测被广泛应用于航空航天、石油化工、电力能源、交通运输等领域,以保障设备和结构的安全运行。
二、项目目的本项目旨在制定一套科学的无损检测实施方案,以确保检测的准确性、高效性和可靠性,为被测物体的安全运行提供可靠的技术支持。
三、项目范围本项目的无损检测范围涵盖但不限于以下内容:1. 金属材料的超声波检测2. 焊接接头的射线检测3. 压力容器的磁粉检测4. 电力设备的红外热像检测5. 建筑结构的声发射检测四、实施方案1. 确定检测方法:根据被测物体的材料、形状、缺陷类型等因素,选择合适的无损检测方法,如超声波检测、射线检测、磁粉检测、红外热像检测等。
2. 确定检测设备:选用符合国家标准和行业标准的无损检测设备,确保设备的性能稳定、精度高、操作简便。
3. 制定检测方案:根据被测物体的具体情况,制定详细的无损检测方案,包括检测位置、检测参数、检测步骤等内容。
4. 进行检测操作:由经过专业培训的无损检测人员,按照制定的检测方案进行实际操作,确保检测的准确性和可靠性。
5. 分析检测结果:对检测所得数据进行分析和评估,判断被测物体的安全状况,提出相应的建议和处理方案。
五、质量控制1. 严格遵守国家标准和行业标准,确保无损检测的准确性和可靠性。
2. 对无损检测设备进行定期维护和校准,保证设备的正常运行。
3. 对无损检测人员进行定期培训和考核,提高其专业技能和操作水平。
4. 对检测结果进行审查和复核,确保检测数据的准确性和可靠性。
六、安全措施1. 严格遵守无损检测操作规程,确保检测人员的人身安全和设备的安全运行。
2. 对检测现场进行安全评估,采取必要的安全防护措施,确保检测作业的安全进行。
七、项目成果1. 完成无损检测报告,对被测物体的安全状况进行评估和分析,提出相应的建议和处理方案。
无损检测方案

船舶无损检测方案一.总则例如:X-射线(RT)、超声波(UT)、磁粉(MT)、渗透(PT).无损检测数量、试验程序满足规范要求。
1.无损检测的认可标准:(1)RT:Ⅲ-Part3-CB/T 3558-94;(2)UT: Ⅲ-Part3-CB/T 3559-94;(3)MT: Ⅱ-Part3-JB/T 6061-92;(4)PT: Ⅱ-Part3-JB/T 6062-92;验收标准:CB/T3177-94二.焊缝区域等级划分1.一级焊缝在船中0.6L区, 外板横向对接缝、内底板横向对接缝;以及上甲板、纵舱壁,舭龙骨,纵桁的对接缝2.二级焊缝在船中0.6L范围外,外板横接缝;在船中0.6L范围内,外板纵接缝。
三.无损检测数量和范围1.一级焊缝(1)射线(RT)根据CCS材料与焊接规范对舯部0.6L区域内强力甲板和外板的射线拍片数量N=0.25(i+0.1Wt+0.1Wl).=0.25(644+0.1*1572+0.1*879)=222.25≈223i~~0.6L范围内纵、横向对接焊缝交叉处的总和Wt~~0.6L范围内横向对接焊缝的总长mWl~~0.6L范围内分段合拢的纵向对接焊缝的总长m具体位置见片位图纵横向对接焊缝交叉处的布片方向应平行于横向对接焊缝(2)超声波(UT)船底、舷侧和甲板纵骨的对接接头,在船中0.6L范围内每10个检查1个,0.6L范围内超声波检测位置范围见表1。
表一区域结构焊缝名称UT数量双层底纵骨HB02P/S~HB03C;HB03C~HB04C;HB04C~HB05C;HB05C~HB06C;HB06C~HB07C;HB07C~HB08C;HB08C~HB09C;HB09C~HB10C;HB10C~HB11C;HB11C~HB12C;HB12C~HB13C;HB13C~HB14C;HB14C-HB15C;4*13=52 纵桁HB02P/S~HB03C;HB03C~HB04C;HB04C~HB05C;HB05C~HB06C;HB06C~HB07C;HB07C~HB08C;HB08C~HB09C;HB09C~HB10C;HB10C~HB11C;HB11C~HB12C;HB12C~HB13C;HB13C~HB14C;HB14C-HB15C;2*13=26底边舱纵骨HS12DP/S~HB03P/S;HB03P/S~HB04P/S;HB04P/S~HB05P/S;HB05P/S~HB06P/S;HB06P/S~HB07P/S;HB07P/S~HB08P/S;HB08P/S~HB09P/S;HB09P/S~HB10P/S;HB10P/S~HB11P/S;HB11P/S~HB12P/S;HB12P/S~HB13P/S;HB13P/S~HB14P/S;HB14P/S~HB15P/S2*13*2=52 斜板HS12DP/S~HB03P/S;HB03P/S~HB04P/S;HB04P/S~HB05P/S;HB05P/S~HB06P/S;HB06P/S~HB07P/S;HB07P/S~HB08P/S;HB08P/S~HB09P/S;HB09P/S~HB10P/S;HB10P/S~HB11P/S;HB11P/S~HB12P/S;HB12P/S~HB13P/S;HB13P/S~HB14P/S;HB14P/S~HB15P/S2*13*2=52顶边舱纵骨HS12UP/S~HS13P/S;HS13P/S~HS14P/S;HS14P/S~HS15P/S;HS15P/S~HS16P/S;HS16P/S~HS17P/S;HS17P/S~HS18P/S;HS18P/S~HS19P/S;HS19P/S~HS20P/S;HS20P/S~HS21P/S;HS21P/S~HS22P/S;HS22P/S~HS23P/S;HS23P/S~HS24P/S;HS24P/S-HS25P/S2*13*2=52 斜板HS12UP/S~HS13P/S;HS13P/S~HS14P/S;HS14P/S~HS15P/S;HS15P/S~HS16P/S;HS16P/S~HS17P/S;HS17P/S~HS18P/S;HS18P/S~HS19P/S;HS19P/S~HS20P/S;HS20P/S~HS21P/S;HS21P/S~HS22P/S;HS22P/S~HS23P/S;HS23P/S~HS24P/S;HS24P/S-HS25P/S2*13*2=52UT数量总计:286舭龙骨对接焊缝100%UT.2.二级焊缝(1)射线(RT)0.6L以外的射线数量为0.6L范围呢的10%即23张,具体见片位图(2)超声波(UT)船底、舷侧和甲板纵骨的对接接头,在船中0.6L范围以外每20个检查1个.其他:1,波形壁分段焊缝10%UT,合拢焊缝10%UT2,海水箱周界100%UT3,分段内纵骨接头50%UT4,起重柱与甲板角焊缝100%UT5,顶边舱竖板与主甲板,底边舱斜板与内地板、外板100%UT6,水密与非水密肋板与舱壁内底板全焊透位置100%UT7,波形壁与底墩角焊缝100%UT,底墩侧板与底墩顶板100%UT8, 底墩侧板与底边舱斜板100%UT9, 直径大于75的一级管对接焊缝100%RT10, 直径大于100的二级管对接焊缝10%RT.11, 主基座对接接头100%用超声波(UT)检查,角接头10-20%用超声波(UT)检查12, 尾柱(铸钢件)和钢板之间的接头用超声波或者着色探伤,检测点根据CCS 验船师指定。
无损检测施工方案
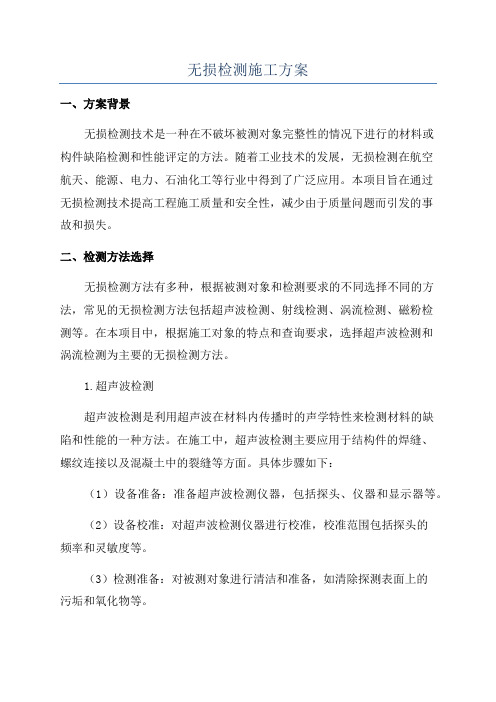
无损检测施工方案一、方案背景无损检测技术是一种在不破坏被测对象完整性的情况下进行的材料或构件缺陷检测和性能评定的方法。
随着工业技术的发展,无损检测在航空航天、能源、电力、石油化工等行业中得到了广泛应用。
本项目旨在通过无损检测技术提高工程施工质量和安全性,减少由于质量问题而引发的事故和损失。
二、检测方法选择无损检测方法有多种,根据被测对象和检测要求的不同选择不同的方法,常见的无损检测方法包括超声波检测、射线检测、涡流检测、磁粉检测等。
在本项目中,根据施工对象的特点和查询要求,选择超声波检测和涡流检测为主要的无损检测方法。
1.超声波检测超声波检测是利用超声波在材料内传播时的声学特性来检测材料的缺陷和性能的一种方法。
在施工中,超声波检测主要应用于结构件的焊缝、螺纹连接以及混凝土中的裂缝等方面。
具体步骤如下:(1)设备准备:准备超声波检测仪器,包括探头、仪器和显示器等。
(2)设备校准:对超声波检测仪器进行校准,校准范围包括探头的频率和灵敏度等。
(3)检测准备:对被测对象进行清洁和准备,如清除探测表面上的污垢和氧化物等。
(4)检测操作:将超声波探头放置在被测对象上,并通过仪器观察显示器上的信号波形。
(5)数据分析:根据显示器上的信号波形,判断被测对象是否存在缺陷。
2.涡流检测涡流检测是一种通过利用涡流感应的原理,检测材料内或表面缺陷的方法。
施工中涡流检测主要应用于管道和金属构件的检测。
具体步骤如下:(1)设备准备:准备涡流检测仪器,包括探头、仪器和显示器等。
(2)设备校准:对涡流检测仪器进行校准,校准范围包括探头的频率和灵敏度等。
(3)检测准备:对被测对象进行清洁和准备,如清除探测表面上的污垢和氧化物等。
(4)检测操作:将涡流探头放置在被测对象上,并通过仪器观察显示器上的信号波形。
(5)数据分析:根据显示器上的信号波形,判断被测对象是否存在缺陷。
三、检测操作规范在实施无损检测时,需要严格按照操作规范进行操作,以确保检测结果的准确性和可靠性。
无损检测项目实施方案

无损检测项目实施方案一、项目背景及目的无损检测是指在不破坏被测物的完整性和功能的情况下,通过对其进行各种试验和观察,利用各种物理原理的检测方法来识别和评估被测物的质量和完整性。
本项目的目的是通过无损检测手段对被测物进行评估和测试,发现和预防可能存在的问题,并提供解决方案,确保被测物的质量和安全性。
二、项目范围本项目的检测对象为被测物在制造、加工、装配、维护、运行等各个环节中可能存在的缺陷和问题,包括但不限于材料缺陷、结构缺陷、尺寸偏差、内部缺陷等。
三、项目方法和流程1.无损检测方法选择:根据被测物的具体情况和需要检测的问题,选择合适的无损检测方法,如超声波检测、磁粉检测、涡流检测、X射线检测等。
2.设备准备:根据所选无损检测方法的要求,准备相应的检测设备和仪器,并进行调试和校准。
3.检测准备:对被测物进行清洁和预处理,确保表面的平整和干净,以及对可能干扰检测结果的因素进行排除。
4.检测操作:按照所选检测方法的要求,进行相应的检测操作,如用超声波探头对被测物进行扫描、用磁粉对被测物进行喷洒和观察等。
5.数据分析和评估:根据检测结果,对数据进行分析和评估,判断被测物是否存在缺陷和问题,并进行定量评估和分类。
6.缺陷识别和定位:对检测到的缺陷进行识别和定位,包括确定缺陷类型、位置、大小等。
7.结果报告和建议:根据检测结果,撰写出具体的检测报告,包括被测物的基本信息、检测结果、缺陷类型和位置、评估和建议等。
四、项目实施计划1.项目启动和准备阶段:制定项目计划和方案,明确项目的目标、方法、范围等。
2.设备准备和调试阶段:购买或租赁所需的检测设备和仪器,并进行调试和校准。
3.检测方案准备阶段:根据被测物的具体情况和问题,制定检测方案,包括选择无损检测方法、确定检测参数等。
4.检测操作阶段:按照检测方案进行相应的操作,对被测物进行检测。
5.数据分析和结果报告阶段:根据检测结果进行数据分析和评估,并撰写检测报告,提供问题和解决方案的建议。
- 1、下载文档前请自行甄别文档内容的完整性,平台不提供额外的编辑、内容补充、找答案等附加服务。
- 2、"仅部分预览"的文档,不可在线预览部分如存在完整性等问题,可反馈申请退款(可完整预览的文档不适用该条件!)。
- 3、如文档侵犯您的权益,请联系客服反馈,我们会尽快为您处理(人工客服工作时间:9:00-18:30)。
目录1.委托单位…………………………………...........................................……………………1.2.工程名称………………………………..................................................................………1.3.检测内容………………………………………..............................................................…1.4.检测依据…………………………………………………......................................…….…1.5.检测内容及数量……………………………………………...................................………1.6.参加作业人员的资格和要求………………………………...................................………1.7.设备…………………………………………….....…..…................................................…1.8.检测……………………………………...................................................................………2.无损检测方案1、委托单位:2、工程名称:3、检测内容:4、检测依据:4.1、《钢制承压管道对接焊接接头射线检验技术规程》DL/T821-20024.2、《承压设备无损检测》NB/T47013.2&3-2015图纸设计技术要求。
5、检测内容及数量:5.1、按图纸技术及委托方要求6、参加作业人员的资格和要求6.1检测人员为国家质量监督检验检疫总局颁发的射线Ⅱ级、超声Ⅱ级及Ⅱ级以上资格的人员,并有检查对象焊缝特性有足够的认识。
具有良好的职业道德、高度的工作责任心。
具有良好的视力。
7、设备7.1射线检测7.1.1 X射线应有相应的曝光曲线图,工作中应根据实际情况进行校验和修正,设备性能应满足管道检测范围的需要。
7.1.2观片灯的主要性能要符合JB/T7903的有关规定,最大亮度应能满足评片的要求。
7.1.3黑度计可测的最大黑度不小于4.5,测量值的误差应不超过±0.05。
7.1.4胶片选用中细粒度类胶片,确保射线透照的底片质量。
7.1.5采用铅屏增感,增感屏应经常擦试,以保证表面清洁和平整。
7.1.6像质计的型号和规格应符合JB/T7902有规定。
7.1.7按工程要求配备XXG—2505探伤机一台和及探伤附件一套,如胶片、增光屏、铅字、磁铁、象质计、黑度计、卷尺、暗袋、红灯、暗室、显影液、停影液、定影液等器材。
7.2超声检测7.2.1所用探伤仪应满足所用探头应满足NB/T47013.3-2015标准中的规定。
7.2.2所用试块应满足NB/T47013.3-2015标准中关于试块的要求。
7.2.3耦合剂为化学浆糊或洗洁精等。
7.2.4按工程要求配备PXUT-350+超声波探伤机一台。
8、检测 8.1.X 射线检测8.1.1检测时机—根据无损检测委托单, 15CrMoG 及12Cr1MoVG 应按排焊后24小时进行 8.1.2透照方法:a)外透法:单壁透照法、双壁单投影法,双壁双投影法 8.1.3定位标记和识别标记a)定位标记:对接接头透照部位一般应有中心标记、分段透照或抽查时还应有搭接标记。
当抽查时称为有效区段透照标记。
采用中心全周透照法时,可用铅质标尺替代搭接定位标记。
b)识别标记:①被检的每段焊缝附件均应有下列铅质识别标记:工件编号、对接接头编号、部位编号、焊工代号和透照日期。
②外径≤89的管子被检焊缝附近,至少应有工件编号。
对接接头编号和焊工代号,加倍抽检的对接接头还应有“JB ”标记,返修后的对接接头透照部位还应有返修标记R1,R2(其数码1,2…指返修次数)③定位标记和识别标记应距焊缝边缘≥5mm ,并在底片上显示。
④透照检验过的工件应作出永久性标识或采用详细的透照部位草图,以作为底片位置对照的依据。
8.1.4像质计1)外径大于89mm 的管子,采用JB/T7902是规定的R ′系列象质计 2)外径小于89mm 的管子采用等径丝系列象质计3)除双壁双影透照外,透照厚度应根据透照方法,按下表确定4)外径小于89mm 透照厚度用以下公式计算T A =0。
8×T T D ⨯-)(+T5)象质指数应根据透照厚度按下表确定6)象质计的摆放,R ′系列应放在射线源侧的工件表面上被检焊缝区一端(被检长度1/4区)金属丝应横跨焊缝并与焊缝垂直,细丝置于外侧,对于双壁单透影法可放置于胶片侧,采用等径丝应放在射源侧管子正中的表面上,金属丝应横跨焊缝并与焊烽垂直。
8.1.5X 射线能量的选择:射线能量的选择取决于透照工件的材料种类、透照方式和透照厚度(T A )。
在保证穿透力和检测范围的前提下,应尽量采用较低的射线能量。
使用管电压为400kV 以下的X 射线透照对接接头时,应根据透照厚度(T A )选取管电压值,一般不应超过TL/T821-2002图6的规定。
8.1.6散射线的屏蔽a)为尽可能减少散射线的影响,应采用适当的方法限制和缩小照射场面积并采取屏蔽措施。
b)当透照成排管子时,因管子间散射线影响大,通常可在管子间用夹板来屏蔽散射线。
8.1.7分段透照的数量a)采用双壁单投影法透照时,射线源至管子外表面的距离,当≤15mm 时,至少分3段透照,即每段对应的中心角应≤120°,当>15mm 时,至少分4段透照,即每段对应的中心角≤90°。
b)对外径大于76mm 且小于89的管子,其焊缝采用双壁双投影法透照时,至少分两次透照,透照角度每次偏转≤90°。
c)对外径≤76mm 的管子,其焊缝采用双壁双投影法透照时,允许一次透照并应选择较高电压,曝光量宜控制在7.5m A ·min 以内,管子内壁轮廓应清晰地显现在底片上。
8.1.8透照的几何条件 射线源至工件表面距离L 1可由下式确定:L 1≥L2:射线源侧工件表面至胶片的距离 d:焦点尺寸8.1.9胶片的暗室处理a)胶片的暗室处理应按胶片的使用说明或公认的有效方法处理b)胶片的自动冲洗应严格控制胶片显影、定影、水洗和干燥等工序的温度、传送速度和药液量。
c)胶片手工冲洗宜采用槽浸方式,在规定的温度(20°左右)和时间内进行显影、定影等操作。
定影后的底片应充分水洗和除污,以保证底片的质量。
d)可采用定期添加补充液的方法来保持显影性能的稳定,但添加补充液的总量不允许超过原显影液体积的三倍。
8.1.10底片质量和观察8.1.10.1底片上必须显示出与象质指数对应的最小钢丝线径,等径丝应显示三根及以上。
8.1.10.2底片上应清晰显示出象质计、深度对比块、定位标记和识别标记,位置正确且不掩盖被检焊缝影像,此外能清晰地年到长度不小于10mm的象质钢丝影像。
8.1.10.3底片有效评定范围的黑度,应1.5-3.5(包括固有灰雾度)的范围内。
8.1.10.4评片应在专用评片室内进行,评片室内光线应暗淡,室内照明用光不得在底片表面产生反射。
8.1.10.5评片时允许使用放大倍数小于或等于5的放大镜辅助观察底片的局部细微部分。
8.1.11对接接头质量分级8.1.11.1圆形缺陷的评级表3缺陷评定区表4 缺陷点数换算表表5 不计点数的缺陷尺寸表6 圆形缺陷的分级8.1.11.2条状缺陷的评级长宽比大于3的缺陷定义为条状缺陷,包括气孔、夹钨、夹渣。
表7 条状缺陷的分级8.1.11.3未焊透的分级a)不加垫板单面焊的未焊透缺陷的质量分级管外径Do>100 mm时,不加垫板单面焊的未焊透缺陷按表14的规定进行分级评定;管外径≤100 mm的小径管不加垫板单面焊的未焊透缺陷按表15的规定进行分级评定。
未焊透缺陷的深度用对比试块测定。
b)根部内凹和根部咬边的质量分级管外径Do>100 mm时,不加垫板单面焊的根部内凹和根部咬边缺陷按表16的规定进行分级评定;管外径≤100 mm的小径管不加垫板单面焊的根部内凹和根部咬边缺陷按表17的规定进行分级评定。
根部内凹和根部咬边缺陷的深度用对比试块测定。
表8 管外径Do>100 mm时不加垫板单面焊的未焊透的分级表9 管外径Do≤100 mm时不加垫板单面焊的未焊透的分级8.1.11.4根部内凹和咬边的分级表10 管外径Do>100 mm时根部内凹和根部咬边的分级表11 管外径Do≤100 mm时根部内凹和根部咬边的分级8.1.12焊口返修在接到委托指令后,根据现场情况及时进行检测。
返修复探时,根据返修部位的长度再扩大延伸,防止未返修位置受返修影响新产生缺欠。
复检记录应详细记录复检的部位、次数,同一部位返修超过2次时,及时通知施工单位处理。
8.1.13射线辐射防护a)放射卫生防护应符合GB18871、GB16357和GB18465的有关规定。
b)现场进行X射线检测时,应按GB18465的规定划定控制区和监督区、设置警告标志,检测工作人员应佩带个人剂量计,并携带剂量报警仪。
RT 检测过程控制程序图检测任务委托受理/工程部底片评定底片像质控制/RT Ⅱ级评片人员缺陷记录控制/RT Ⅱ级评片人员复评记录控制/RT Ⅱ级复评人员与顾客沟通检测技术要求工程部确认现场检测条件检测部位状况存档文件资料编制检测方案、专用工艺(工艺卡)编制RT Ⅲ级审核:RT 检测责任师检测作业准备检测部位条件控制/项目负责人检测人员条件控制/项目负责人仪器试块器材控制/RT Ⅱ级人员安全设施条件控制/项目负责人工艺技术交底控制/检测责任师检测作业实施作业工艺纪律控制/检测责任师作业过程记录控制/RT Ⅱ级人员检测部位标识控制/RT Ⅱ级人员安全作业实施控制/RT Ⅱ级人员编制检测报告/RT Ⅱ级人员检测报告审核/检测责任师检测报告签发/技术负责人检测报告印章/综合办存档/档案室用户RT 责任师分析原因,制定纠正措施8.2超声检测8.2 .1检测设备8.2.1.1使用的检测仪器性能必须满足检测灵敏度要求,每隔三个月至少对仪器的水平线性和垂直线性测定一次。
8.2.1.2超声波探伤仪:采用A型脉冲反射式超声波探伤仪,其工作频率范围为0.5MHz~10MHz,仪器至少在荧光屏满刻度的80%范围内呈线性显示。
探伤仪应具有80dB以上的连续可调衰减器(增益),步进级每档不大于2dB,其精度为任意相邻12dB误差在±1dB以内,最大累计误差不超过1dB。