关于无损检测方案
无损检测实施方案

无损检测实施方案一、背景介绍无损检测是一种通过对被检测物体进行表面和内部缺陷的检测,而不破坏被检测物体的方法。
在工业生产和科学研究中,无损检测被广泛应用于材料、零部件、设备等领域,以确保产品质量和安全性。
本文将就无损检测的实施方案进行详细介绍。
二、无损检测的原理和方法无损检测的原理是利用各种物理学原理和技术手段,如超声波、X射线、磁粉、涡流等,对被检测物体进行全面、准确的检测。
其中,超声波检测是最常用的方法之一,通过超声波的传播和反射来检测材料内部的缺陷;X射线检测则是利用X射线的透射性质,对材料进行内部缺陷的检测;磁粉和涡流检测则是利用材料对磁场的响应来检测材料表面和近表面的缺陷。
这些方法各有特点,可以根据被检测物体的特点和要求来选择合适的方法进行检测。
三、无损检测的实施步骤1. 制定检测计划:在进行无损检测之前,需要制定详细的检测计划,包括被检测物体的材料、结构、尺寸等信息,以及检测的要求和标准。
2. 选择检测方法:根据被检测物体的特点和要求,选择合适的无损检测方法,如超声波、X射线、磁粉、涡流等。
3. 准备检测设备:根据选择的检测方法,准备相应的检测设备和工具,包括超声波探头、X射线发射器、磁粉液、涡流探头等。
4. 进行检测操作:按照检测计划和方法,进行无损检测操作,对被检测物体进行全面、细致的检测。
5. 分析和评定检测结果:根据检测数据和图像,对检测结果进行分析和评定,判断被检测物体是否存在缺陷,以及缺陷的类型和程度。
6. 编制检测报告:根据检测结果,编制详细的检测报告,包括被检测物体的信息、检测方法和过程、检测结果和评定等内容。
四、无损检测的应用领域无损检测广泛应用于航空航天、汽车制造、铁路运输、石油化工、电力能源、建筑结构、核工业等领域。
在航空航天领域,无损检测可以用于飞机结构、发动机零部件、液压系统等的检测;在汽车制造领域,无损检测可以用于车身、发动机、变速箱等零部件的质量检测;在石油化工领域,无损检测可以用于管道、储罐、压力容器等设备的安全检测。
无损检测施工方案
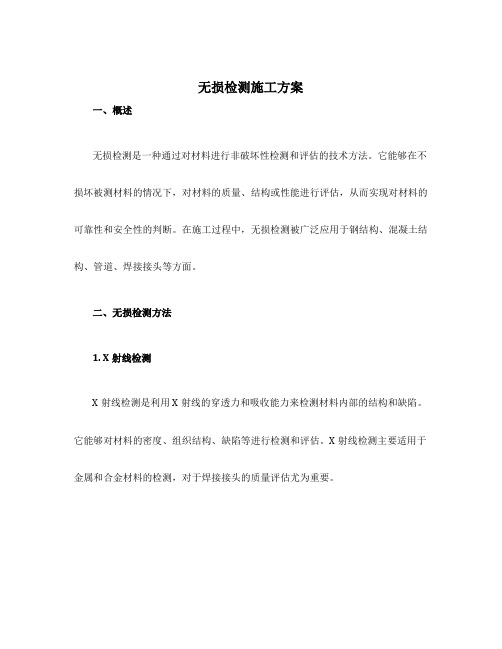
无损检测施工方案一、概述无损检测是一种通过对材料进行非破坏性检测和评估的技术方法。
它能够在不损坏被测材料的情况下,对材料的质量、结构或性能进行评估,从而实现对材料的可靠性和安全性的判断。
在施工过程中,无损检测被广泛应用于钢结构、混凝土结构、管道、焊接接头等方面。
二、无损检测方法1. X射线检测X射线检测是利用X射线的穿透力和吸收能力来检测材料内部的结构和缺陷。
它能够对材料的密度、组织结构、缺陷等进行检测和评估。
X射线检测主要适用于金属和合金材料的检测,对于焊接接头的质量评估尤为重要。
2. 超声波检测超声波检测是利用超声波在材料中的传播和反射特性来检测材料内部的结构和缺陷。
它能够对材料的厚度、波速、声阻抗等进行检测和评估,并能够定位和测量缺陷的尺寸。
超声波检测主要适用于金属和非金属材料的检测,对于混凝土结构和管道的检测具有重要意义。
3. 磁粉检测磁粉检测是利用外加磁场和磁粉的磁化作用来检测材料表面和近表层的结构和缺陷。
它能够对材料的表面裂纹、缺陷和疲劳裂纹进行检测和评估,并能够定位和测量缺陷的尺寸和形态。
磁粉检测主要适用于金属材料的表面检测,对于焊接接头和表面裂纹的检测具有重要意义。
4. 热红外检测热红外检测是利用物体的热辐射特性来检测物体的缺陷和异常情况。
它能够通过红外相机对物体的温度分布进行测量和分析,从而判断物体内部的结构和材料的性能状况。
热红外检测主要适用于建筑物、电力设备和输电线路等方面的检测,对于温度异常、能量损失等问题具有重要意义。
三、无损检测施工流程无损检测施工包括前期准备、检测方案制定、实施检测和结果分析报告等环节。
1. 前期准备在进行无损检测之前,需要对被测物体进行准备工作。
首先,要清理被测物体的表面,确保无杂质和污染物。
其次,要研究被测物体的结构和材料特性,了解其内部结构和缺陷的可能性。
2. 检测方案制定根据被测物体的特点和检测要求,制定适合的检测方案。
选择合适的无损检测方法,并确定检测仪器和设备的使用参数。
无损检测作业实施方案

无损检测作业实施方案一、前言。
无损检测是一种非破坏性检测方法,可以在不破坏被测物体的情况下,通过各种检测技术手段获取被测物体内部的缺陷信息,对被测物体的完整性和可靠性进行评估。
本文档旨在制定一套无损检测作业实施方案,以确保无损检测工作的准确性和高效性。
二、作业准备。
1. 设备准备,确保无损检测设备处于良好状态,检查设备的电源、传感器、探头等部件是否完好,必要时进行校准和调试工作。
2. 人员准备,安排有经验的无损检测人员进行作业,确保其具备相关的资质和证书,并了解被测物体的特性和检测要求。
3. 环境准备,选择适宜的环境进行无损检测作业,确保作业场所的温度、湿度等环境因素符合检测要求。
三、作业实施。
1. 检测方案制定,根据被测物体的特性和检测要求,制定相应的无损检测方案,包括选择合适的检测技术和方法,确定检测位置和方向等。
2. 作业流程安排,按照检测方案制定作业流程,明确各项作业步骤和责任人,确保每个环节的顺利进行和无差错。
3. 检测数据采集,严格按照检测方案和流程进行数据采集工作,确保数据的准确性和完整性,避免漏检和误检情况的发生。
4. 检测结果分析,对采集到的数据进行分析和评估,判断被测物体的完整性和可靠性,及时发现并记录缺陷信息。
5. 报告编制,根据检测结果编制检测报告,清晰地呈现检测数据和分析结论,提出相应的建议和措施。
四、作业总结。
1. 检测记录保存,将检测过程中采集到的数据和检测报告进行保存,建立完整的档案记录,为后续的评估和跟踪提供依据。
2. 作业经验总结,对本次无损检测作业进行总结和经验归纳,发现存在的问题和不足之处,并提出改进措施。
3. 资料交接和归档,将作业相关资料进行交接和归档,确保资料的完整性和安全性,为后续的工作提供支持。
五、作业安全。
1. 作业人员安全,无损检测作业人员要严格遵守相关的安全操作规程,正确使用检测设备,确保个人安全和设备完好。
2. 环境安全,作业场所要符合安全要求,确保无损检测作业不会对周围环境和人员造成影响。
无损检测施工方案
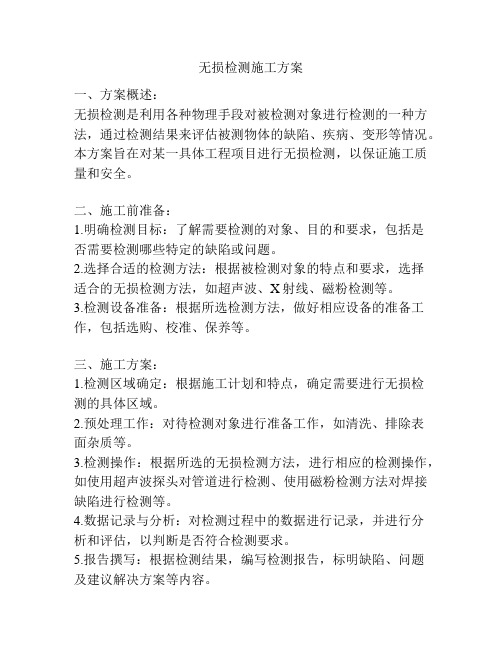
无损检测施工方案一、方案概述:无损检测是利用各种物理手段对被检测对象进行检测的一种方法,通过检测结果来评估被测物体的缺陷、疾病、变形等情况。
本方案旨在对某一具体工程项目进行无损检测,以保证施工质量和安全。
二、施工前准备:1.明确检测目标:了解需要检测的对象、目的和要求,包括是否需要检测哪些特定的缺陷或问题。
2.选择合适的检测方法:根据被检测对象的特点和要求,选择适合的无损检测方法,如超声波、X射线、磁粉检测等。
3.检测设备准备:根据所选检测方法,做好相应设备的准备工作,包括选购、校准、保养等。
三、施工方案:1.检测区域确定:根据施工计划和特点,确定需要进行无损检测的具体区域。
2.预处理工作:对待检测对象进行准备工作,如清洗、排除表面杂质等。
3.检测操作:根据所选的无损检测方法,进行相应的检测操作,如使用超声波探头对管道进行检测、使用磁粉检测方法对焊接缺陷进行检测等。
4.数据记录与分析:对检测过程中的数据进行记录,并进行分析和评估,以判断是否符合检测要求。
5.报告撰写:根据检测结果,编写检测报告,标明缺陷、问题及建议解决方案等内容。
四、施工要求:1.施工人员:由经过专业培训的无损检测人员进行,确保操作规范、准确性和安全性。
2.操作环境:提供适合的操作环境,如保持室温、降低干扰等,以确保检测过程的准确性。
3.保养维护:保养和维护无损检测设备,确保设备的正常运行。
4.安全防护:在无损检测过程中,使用符合要求的个人防护设备,确保施工人员的安全。
五、质量控制:1.制定质量控制计划:在施工前制定无损检测质量控制计划,包括检测要求、检测方法、操作标准等内容。
2.质量检查:在施工过程中进行质量检查,确保操作符合要求,并及时纠正不合格操作。
3.重要数据备份:对重要数据进行备份,以防止数据丢失造成损失。
六、施工管理:1.组织施工人员:组织好无损检测人员的工作安排和任务分配,确保施工进度和质量。
2.施工进度控制:配合工程进度安排,合理安排无损检测施工时间,确保无损检测工作的顺利进行。
无损检测方案

无损检测方案无损检测是一种通过对材料或构件进行检测,不会对其使用性能产生永久性影响的检测方法。
无损检测可以检测出材料或构件内部的缺陷,并能够识别其位置、形状和大小,帮助判断材料或构件的可靠性和使用寿命。
本文将介绍几种常用的无损检测方法及其检测方案。
1.超声波检测(UT)超声波检测是一种利用超声波在材料或构件内部传播的特性来检测其缺陷的方法。
其检测方案一般包括以下几个步骤:1)选择适当的超声波探头和频率;2)设置超声波发射和接收参数,如工作频率、发射和接收幅度、时间增益等;3)对材料或构件进行扫描,记录超声波的传播时间及幅度;4)对测得的数据进行分析,判断缺陷的位置、形状和大小。
2.射线检测(RT)射线检测是一种利用射线的穿透性来检测材料或构件内部缺陷的方法。
其检测方案一般包括以下几个步骤:1)选择适当的射线源和探测器;2)设置射线源和探测器的参数,如电流、电压、曝光时间等;3)将射线源和探测器对准待检测区域,进行曝光;4)对曝光的胶片或探测器图像进行观察和分析,判断缺陷的位置、形状和大小。
3.磁粉检测(MT)磁粉检测是一种利用磁场和磁粉的性质来检测材料或构件表面和近表面缺陷的方法。
其检测方案一般包括以下几个步骤:1)选择适当的磁场源和磁粉;2)在待检测区域施加磁场,并撒布磁粉;3)观察磁粉在缺陷处的聚集情况,判断缺陷的位置、形状和大小。
4.涡流检测(ET)涡流检测是一种利用交变磁场在导电材料中产生涡流而检测材料或构件表面缺陷的方法。
其检测方案一般包括以下几个步骤:1)选择适当的涡流探头和频率;2)设置涡流探头的参数,如工作频率、发射幅度等;3)将涡流探头对准待检测区域,进行扫描;4)观察涡流信号的变化,判断缺陷的位置、形状和大小。
以上是常用的几种无损检测方法及其检测方案的简要介绍。
在实际应用中,根据材料或构件的特点和具体要求,可以根据这些方法的优缺点选择合适的方法,并制定相应的检测方案来进行无损检测。
无损检测项目实施方案
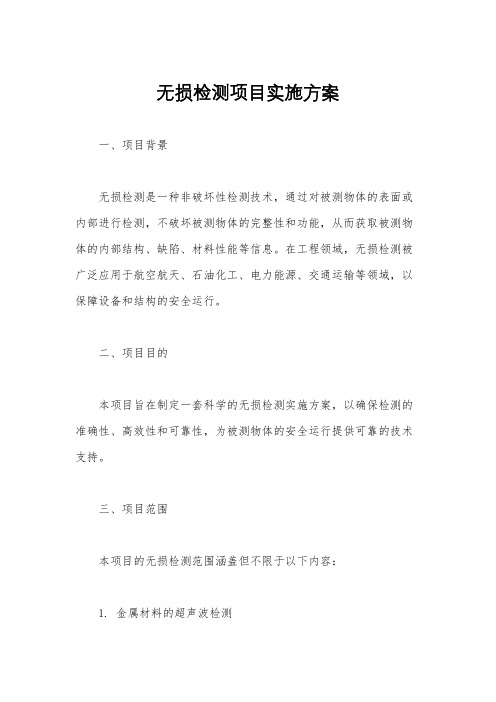
无损检测项目实施方案一、项目背景无损检测是一种非破坏性检测技术,通过对被测物体的表面或内部进行检测,不破坏被测物体的完整性和功能,从而获取被测物体的内部结构、缺陷、材料性能等信息。
在工程领域,无损检测被广泛应用于航空航天、石油化工、电力能源、交通运输等领域,以保障设备和结构的安全运行。
二、项目目的本项目旨在制定一套科学的无损检测实施方案,以确保检测的准确性、高效性和可靠性,为被测物体的安全运行提供可靠的技术支持。
三、项目范围本项目的无损检测范围涵盖但不限于以下内容:1. 金属材料的超声波检测2. 焊接接头的射线检测3. 压力容器的磁粉检测4. 电力设备的红外热像检测5. 建筑结构的声发射检测四、实施方案1. 确定检测方法:根据被测物体的材料、形状、缺陷类型等因素,选择合适的无损检测方法,如超声波检测、射线检测、磁粉检测、红外热像检测等。
2. 确定检测设备:选用符合国家标准和行业标准的无损检测设备,确保设备的性能稳定、精度高、操作简便。
3. 制定检测方案:根据被测物体的具体情况,制定详细的无损检测方案,包括检测位置、检测参数、检测步骤等内容。
4. 进行检测操作:由经过专业培训的无损检测人员,按照制定的检测方案进行实际操作,确保检测的准确性和可靠性。
5. 分析检测结果:对检测所得数据进行分析和评估,判断被测物体的安全状况,提出相应的建议和处理方案。
五、质量控制1. 严格遵守国家标准和行业标准,确保无损检测的准确性和可靠性。
2. 对无损检测设备进行定期维护和校准,保证设备的正常运行。
3. 对无损检测人员进行定期培训和考核,提高其专业技能和操作水平。
4. 对检测结果进行审查和复核,确保检测数据的准确性和可靠性。
六、安全措施1. 严格遵守无损检测操作规程,确保检测人员的人身安全和设备的安全运行。
2. 对检测现场进行安全评估,采取必要的安全防护措施,确保检测作业的安全进行。
七、项目成果1. 完成无损检测报告,对被测物体的安全状况进行评估和分析,提出相应的建议和处理方案。
无损检测方案范文

无损检测方案范文无损检测(Non-Destructive Testing,简称NDT)是指在不破坏被测对象的前提下,利用光、电、声、磁等物理原理和方法对被测对象进行检测、测量和评定的一种技术手段。
无损检测广泛应用于各个行业领域,如航空航天、能源、化工、电力、建筑、交通、机械等,其重要性和作用日益凸显。
1.检测方法的选择:根据被测对象的特点和检测目的,选择最适合的无损检测方法。
常用的无损检测方法包括:超声波检测、射线检测、涡流检测、磁粉检测、红外热像检测等。
不同的方法适用于不同的被测对象和缺陷类型。
2.仪器设备的准备和操作:根据选择的无损检测方法,准备相应的仪器设备,并对其进行校准和检验,确保其工作稳定和准确。
对于一些特殊的仪器设备,如X射线机、涡流探头等,需要对操作人员进行专门的培训,确保其掌握正确的操作方法和安全注意事项。
3.测量参数的设置和数据采集:根据被测对象的要求和检测目的,确定相应的测量参数,如超声波的频率和幅值、射线的曝光时间和电流等。
在进行数据采集时,需要按照标准要求进行多次重复测量,并保证数据的准确性和可靠性。
4.数据分析和处理:对采集到的数据进行分析和处理,提取有效信息,判断是否存在缺陷。
常用的分析方法包括信号处理、图像处理、图像增强等。
对于一些大规模的数据,如声场数据、热图数据等,可以利用计算机辅助分析方法,加快数据处理速度和提高分析精度。
5.结果评定和记录:根据数据分析的结果,对被测对象进行评定和判定,判断其是否合格。
评定的标准可以是技术标准、规范文件等。
对于发现的缺陷,需要进行相应的描述和记录,包括缺陷类型、尺寸、位置等信息,以便后续进行修复或控制。
6.报告撰写和归档:根据检测结果和记录,撰写相应的检测报告,包括被测对象的基本信息、检测方法、仪器设备、测量参数、数据分析结果、评定结论等。
检测报告应具备完整性、可读性和可追溯性。
同时,将检测报告进行归档保存,以备后续需要。
以上就是一个完整的无损检测方案的主要内容。
无损检测施工方案
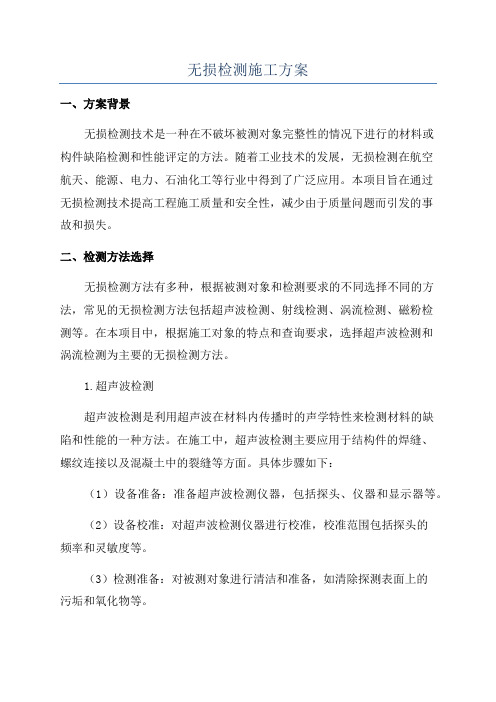
无损检测施工方案一、方案背景无损检测技术是一种在不破坏被测对象完整性的情况下进行的材料或构件缺陷检测和性能评定的方法。
随着工业技术的发展,无损检测在航空航天、能源、电力、石油化工等行业中得到了广泛应用。
本项目旨在通过无损检测技术提高工程施工质量和安全性,减少由于质量问题而引发的事故和损失。
二、检测方法选择无损检测方法有多种,根据被测对象和检测要求的不同选择不同的方法,常见的无损检测方法包括超声波检测、射线检测、涡流检测、磁粉检测等。
在本项目中,根据施工对象的特点和查询要求,选择超声波检测和涡流检测为主要的无损检测方法。
1.超声波检测超声波检测是利用超声波在材料内传播时的声学特性来检测材料的缺陷和性能的一种方法。
在施工中,超声波检测主要应用于结构件的焊缝、螺纹连接以及混凝土中的裂缝等方面。
具体步骤如下:(1)设备准备:准备超声波检测仪器,包括探头、仪器和显示器等。
(2)设备校准:对超声波检测仪器进行校准,校准范围包括探头的频率和灵敏度等。
(3)检测准备:对被测对象进行清洁和准备,如清除探测表面上的污垢和氧化物等。
(4)检测操作:将超声波探头放置在被测对象上,并通过仪器观察显示器上的信号波形。
(5)数据分析:根据显示器上的信号波形,判断被测对象是否存在缺陷。
2.涡流检测涡流检测是一种通过利用涡流感应的原理,检测材料内或表面缺陷的方法。
施工中涡流检测主要应用于管道和金属构件的检测。
具体步骤如下:(1)设备准备:准备涡流检测仪器,包括探头、仪器和显示器等。
(2)设备校准:对涡流检测仪器进行校准,校准范围包括探头的频率和灵敏度等。
(3)检测准备:对被测对象进行清洁和准备,如清除探测表面上的污垢和氧化物等。
(4)检测操作:将涡流探头放置在被测对象上,并通过仪器观察显示器上的信号波形。
(5)数据分析:根据显示器上的信号波形,判断被测对象是否存在缺陷。
三、检测操作规范在实施无损检测时,需要严格按照操作规范进行操作,以确保检测结果的准确性和可靠性。
- 1、下载文档前请自行甄别文档内容的完整性,平台不提供额外的编辑、内容补充、找答案等附加服务。
- 2、"仅部分预览"的文档,不可在线预览部分如存在完整性等问题,可反馈申请退款(可完整预览的文档不适用该条件!)。
- 3、如文档侵犯您的权益,请联系客服反馈,我们会尽快为您处理(人工客服工作时间:9:00-18:30)。
中粮生物化学(安徽)股份有限公司改造项目(燃料乙醇)无损检测方案编制:审核:批准:中国三冶集团有限公司二〇一七年三月六日目录一、工程概述 (1)1.1工程概况 (1)1.2编制依据及验收规范 (1)1.3检测工程要求 (1)二、主要检测项目的保证措施 (1)2.1概述 (1)2.2射线检测方案 (1)2.3超声检测方案 (6)2.4渗透检测方案 (7)2.5磁粉检测方案 (10)2.6保证措施 (13)三、安全技术措施 (16)3.1人员要求 (16)3.2设备要求 (16)3.3人员防护 (16)3.4现场防护 (16)四、应急预案 (17)五、无损探伤JSA分析及防护方法 (18)无损检测方案一、工程概述:1.1工程概况中粮生物化学(安徽)股份有限公司(燃料乙醇)项目共有三十台储罐,依据相关规范及标准,对罐体进行无损检测工作。
1.2 编制依据及验收规范1.2.1 GB50128-2005《立式圆筒形钢制焊接储罐施工及验收规范》;1.2.2 NB/T47013.1~6-2015《承压设备无损检测》;1.2.3 GB50341-2014 《立式圆筒型钢制焊接油罐设计规范》;1.2.4 SH/T3167-2012 《钢制焊接低压储罐》;1.2.5 NB/T47015-2011 《压力容器焊接规程》;1.2.6 HG/T20569-2013 《机械搅拌设备》;1.2.7计图纸文件要求的其他规范、规程;1.2.8 GB18871-2005《射线卫生防护基本标准》。
1.3 检测工作要求1.3.1 发酵区储罐探伤要求:底及次圈罐壁纵焊缝100%射线探伤,Ⅲ级合格;底及次圈罐壁环焊缝和其余各圈纵焊缝20%射线探伤,Ⅲ级合格;其余各圈环焊缝2%探伤,Ⅱ级合格;罐壁所有丁字焊缝100%射线探伤,Ⅱ级合格;底圈壁板与罐底内外角焊缝100%磁粉探伤,Ⅰ级合格;罐底边缘板(外缘300mm)对接焊缝100%射线探伤,Ⅱ级合格;罐底板T型焊缝根部和表面100%磁粉探伤。
1.3.2乙醇成品罐区及乙醇中间罐区储罐探伤要求:按GB50341-2014中的第12.2条及GB50128-2014中的第7.2条相关条款规定进行探伤。
二、主要检测项目的保证措施2.1概述1无损检测指令由本工程的无损检测业主工程师下达;2无损检测依据《承压设备无损检测》(NB/T 47013.147013.6-2015)~为此,我公司制定了以下检测方案:射线检测采用以X射线探伤机检测法为主,对不适合射线检测的部位采用超声检测;对于表面及近表面缺陷的检测:铁磁性的材料采用磁粉检测;非铁磁性的材料采用渗透检测。
针对既定无损检测方案,我公司对人员、设备、材料、工艺、设施等各个方面进行了周密的安排,并在本施工组织设计中编制了详细的措施。
2.2射线检测方案1.总则1.1适用范围:本规程适用中粮生物化学(安徽)股份有限公司(燃料乙醇)项目。
1.2依据:GB5O128-2005《立式圆筒形钢制焊接储罐施工及验收规范》NB/T47013.2-2015《承压设备无损检测》1.3检测人员:必须由取得锅炉压力容器无损检测人员资格考核委员会颁发的射线Ⅰ级及Ⅰ级以上人员担任操作,Ⅱ级及Ⅱ级以上人员审核并签发报告。
1.4评片人员的视力应每年检查一次,校正视力不得低于5.0。
1.5 射线防护应符合GB 18871-2002 《电离辐射防护与辐射源安全基本标准》的规定。
2表面要求2.1焊缝的表面质量(包括焊缝余高)应由焊接检验人员经外观检验合格后出具《射线探伤委托通知单》委托探伤。
2.2表面的不规则状态在底片上的影象应不掩盖焊缝中的缺陷,否则应作适当的修理。
3仪器、设备和器材3.1选用设备:a)定向X射线机:规格型号:XXG-25053.2 胶片和增感屏3.3 胶片a)射线胶片分为T1、T2、T3、T4四类,T1为最高类别,T4为最低类别。
b) 在满足灵敏度要求的情况下,根据本工程无损检测要求选用T3类型胶片,AGFA-C7胶片,胶片规格:300×80mm3.4 增感屏a) 采用铅增感屏,增感屏的表面应保持洁净和平整。
b) 在透照过程中胶片和增感屏应始终紧密接触。
c) 规格:300×80mm;厚度:0.03~0.1/0。
1mm(前后屏)3.5 像质计3.5.1 像质计的选用:应根据透照方式、检测技术级别(本工程为AB级)、像质计放置方式及公称厚度(或透照厚度)确定像质计灵敏度,选用符合NB/T47013.2-2015《承压设备无损检测》规定的Ⅱ型、Ⅲ型像质计Fe10/16、Fe6/12及小径管专用像质计。
3.5.2 透照厚度:射线照射方向上工件的公称厚度,多层透照时,应为通过的各层材料工程厚度之和。
3.5.3径管≤100mm时,选用NB/T 47013.2-2015附录F规定的专用(等径金属丝)像质计。
3.5.2像质计灵敏度应符合NB/T 47013.2-2015《承压设备无损检测》表5、表6、表7的规定。
3.5.2线型像质计的放置:应符合NB/T 47013.2-2015《承压设备无损检测》第4.7.2条的规定。
3.5.3黑度计和比较黑度片采用数字显示型式的黑度计(TD-210),黑度计误差不超过±0.05,所使用的标准黑度片应在计量检定有效期内。
3.5.4观片灯:观片灯的亮度至少应观察到黑度为4.0的底片,且观察的慢射光亮度可调,对于需要观察或透光量过强的部分应采用滤光板以屏蔽强光。
3.5.5评片室:评片一般应在专用评片室进行,室内的光线暗且柔和。
4底片标记及布片方法4.1 底片标记:底片标记放置见<图1>。
4.1.1 定位标记和识别标记应放在胶片的适当位置,并距焊缝边缘至少5mm。
4.1.2 象质计的放置应放在射线源一侧的工件表面上被检焊缝区的一端(被检区长度的1/4部位)。
当射线源一侧无法放置象质计时,也可放在胶片一侧,但应附加“F”标记以示区别。
4.1.3 采用射线源置于中心位置的周向曝光时,象质计应在内壁,每间隔90度放一个。
4.1.4 搭接标记(抽查时为有效区段透照标记)应距离底片两端至少10mm,用(↑)标记。
搭接标记的摆放位置应符合《NB/T 47013.2-2015》标准(附录G)的要求。
4.2 布片4.2.1 按焊缝布置图绘制出焊缝编号,顺时方向布片,环缝从以纵缝丁字口为中心,顺时方向布片。
4.2.2 工件上必须标明定位标记和识别标记,做永久标记和作为重复探伤的依据。
4.2.3 布片位置要详细的标记在原始记录简图上,标注记录与标记相符。
5 拍片,5.1曝光条件X射线机应定期制作曝光曲线,供合理选择曝光工艺参数。
5.1.2 管电压在保证穿透的情况下,尽量采用低电压、长时间,在焦距F≥700mm时,曝光量推荐不低于15mA.min. 当焦距改变时可按平方反比定律对曝光量的推荐值进行换算,采用r射线透照时,总的曝光时间应不小于输送源往返所需时间的10倍。
5.1.3 允许使用的高管电压应控制在不同透照厚度允许X 射线最高透照管电压(图1)范围内。
用γ射线透照,当采用内透法(中心法或偏心法)时,在保证像质计灵敏度达到NB/T 47013.2-2015要求时,透照厚度下限减半。
不同透照厚度允许的X射线最高透照管电压图(1)5.2 几何条件5.2.1 L2与L1/d的关系应满足JB/T4730.2-2005标准图2、图3、 AB级要求,或按下式计算:L1≥10d·L22/3式中:L1—源至被检部位工件上表面的距离,(或称透照距离)。
d—焦点尺寸(方焦点尺寸取边长,长焦点取长短边只和的1/2)。
L2—被检部件工件表面至胶片的距离。
推荐焦距(F)一般选用F≥700mm(满足L3≤L1/2)。
5.3透照次数5.3.1环向对接焊接接头透照次数应满足NB/T 47013.2-2015标准附录D的要求。
AB级的K≤1.03(纵缝)K≤1.1(环缝)5.3.2小径管环向对接焊接接头检测a) 小径管环向对接焊缝采用双壁双影透照,当同时满足下列条件时应采用倾斜透照方式椭圆成像:1)T(壁厚)≤8mm;2)g(焊缝宽度)≤D/4。
射线束的方向应满足上下焊缝的影像在底片上呈椭圆形显示,焊缝投影间距以1倍焊缝宽度为宜,只有当不能满足上述条件或上下焊缝椭圆形显示有困难时,可采用做垂直透照方式重叠成像。
5.3.3小径管环向对接焊接头100%检测的透照次数,采用倾斜透照椭圆成像时,当T/D0≤0.12时,相隔90°透照2次;当T/D>0.12时,相隔120°或60°透照3次。
垂直透照重叠成像时,一般应相隔120°或60°透照3次。
5.3.4 本工程小径管直径<32mm的管子采用垂直透照重叠成像时,一般应相隔90°透照2次。
5.4 切片、装片、拍片过程中要注意保护胶片,防止胶片及增感屏折叠、挤压、污染。
5.5 透照前应对工件进行编号和标记,并画布片示意图。
5.6透照时为防止漏检,底片有效长度和划线长度必须按标准并满足K值要求。
5.5 透照方式按射线源、工件和胶片之间的相互关系,□纵、环缝源在外单壁透照□纵、环缝源在内单壁透照□纵缝源在外双壁单影透照□小径管环缝双壁双影椭圆成像□小径管环缝垂重叠成像6.暗室处理底片处理及要求按“暗室处理工艺守则”进行,底片晾干应用白纸隔开。
7 底片的质量7.1.1 底片黑度(包括胶片本身的灰雾度)底片有效评定区域内的黑度AB级时,2.0≤D≤4.5。
注:底片有效评定区域内的黑度,指搭接标记之间焊缝和热影响区的黑度。
7.1.2 底片上的像质计和识别系统齐全,位置准确,且不得掩盖受检焊缝的影像。
透照布置示意图和说明□环缝中心周向透照□环缝双壁单影透照(1)□环缝双壁单影透照(2)7.1.3 底片上至少应识别出NB/T 47013.2-2015标准表3规定得像质指数,且长度不少于10mm。
7.1.4 底片有效评定区域内不得有胶片处理不当或妨碍底片准确评定的伪像。
8. 评片8.1 质量分级及评定必须严格按照NB/T 47013.2-2015《承压设备无损检测》中相关要求评定。
8.2 验收级别应符合本工程技术条件及图纸要求。
8.2 评片执行初评与复评制度,对难于评定的缺陷应采取会诊或其它探伤方法进行综合判定。
8.3 评片中发现焊缝有超标缺陷,要及时发出“焊缝返修通知单”待返修完后,重新委托拍片、评判。
8.4 评片中要及时填好“射线评片原始记录”,探伤完毕以后,应及时鉴发探伤报告,并经探伤负责工程师签字。
9. 返修与扩探9.1 评片中发现有超过规定缺陷时,要及时制定切实可行的返修方案进行返修,待返修完毕24小时后重新进行射线探伤。