油脂脱酸工艺中影响碱炼的因素
油脂精炼车间工艺概述

脱色、脱臭常见问题处理
? 1、脱色塔控制温度和压力
? 1)吸附脱色中的操作温度决定于油脂品种操作压力及吸附剂品种及特性 脱色温度超高后会因新生色素而回升变色 2)压力是(—0.9)bar 温度应控制在90℃—130℃
? 2 B2610液位高报的原因
Ab 油中含皂较高
(1) 酸碱量不正确较多。
(2) 离心机碟片较脏或转鼓较脏。
(3) 背压调的过低。
(4) 向心泵开度较小。
(5) 油分离温度不正确,分离效果较差。
(6) 排渣量较小或间隔时间较长。
(7) 油出现乳化现象。
B:白土残油较高
1、 白土质量较差(粒度较小、水分较高、黏度较大)。
2、 白土添加量较多。
3、 过滤饼厚度较厚。
4、 过滤板较脏。
5、 蒸汽质量较差(带水分高)。
6、 蒸汽吹扫压力低。
7、 蒸汽吹扫时间短(质量较好的蒸汽)。
8、 过滤机设备本身因素。
9、 中和油质量较差(磷、皂含量较高)。
C:成品油FFA偏高
1、 汽提效果不佳。
2、 真空度不好。
2 白土用量要合适,满足生产需求即可.
3.过滤机使用要调整好,压力在3.0bar以下
4 过滤器要用规定的过滤袋
5 D2770真空在200 torr以下
6 E2701温度在120 ~130 ℃,E2702温度在180 ~200 ℃,VHE2704的温度在230 ~270℃
7 VHE2703将脱臭油冷却至150 ℃左右,E2600将脱臭油冷却至100 ℃左右,E2706冷却至45 ℃以下
3、 直接汽质量较差(带水多)。
4、 直接汽压力低。
油脂精炼中常见的生产技术问题及对策

油脂精炼中常见的生产技术问题及对策随着人们消费水平的不断提高和油脂精炼技术的迅速发展,高档精炼油脂已成为我国食用油市场上主要的供应品种。
作为食用油加工的最后一个工段—-—油脂精炼,其主要任务是生产出高质量的精炼油,怎样提高油脂精炼率与降低消耗是矛盾的两个方面,也是精煤生产技术的关键所在.对大多数的油品而言,其精炼的过程通常包括脱胶、脱酸、脱色及脱臭等工序,各工序的目的及操作要求各不相同,生产中遇到的技术问题也不一样,现就这些工序中几个常见的技术问题作简要的分析,供同行参考.1 脱胶脱胶被认为是精炼工艺中最重要的环节之一,有效的脱胶操作将有利于保证成品油的质量,减少损耗。
因为胶质的存在会使成品油的食用品质降低,并会使油脂在脱色时白土用量增多,如果脱臭前还有胶质存在,油脂将会产生严重异味并影响成品油的稳定性。
水化是常用的脱胶方法。
一般将约2 %左右的略高于油温的水加入到70 ℃左右的毛油中,使磷脂水化。
磷脂吸水后,溶解性发生了变化,并从油中析出,可通过沉淀或离心的方法,使之与油分离,采用这种方法可以除去大部分胶质。
在实际生产中,用新收获油料(如新上市的油菜籽)或用储藏条件不大好的原料制得的毛油,经脱胶后通常仍残余一些胶质,表现为水化油280 ℃加热试验经常不合格,即使重新加水处理,也没有明显效果。
究其原因,主要是油中存在着较多的非水化磷脂之故。
要脱除这部分胶质,目前比较行之有效的方法是在待处理油中先加入约011 %左右的无机酸(通常用磷酸) ,并使之与油充分混合,让其中的非水化磷脂转化为水化磷脂,然后按正常的脱胶方法进行即可。
值得注意的是:间歇水化时,油中加入磷酸后需快速搅拌充分,然后才能加水水化,否则,因磷酸数量太少而未能与油充分接触,脱胶仍然不彻底;而连续工艺采用的是专用混合设备,混合效果一般没有问题,但同样因为磷酸的加入量太少,需要控制磷酸和油的流量之间的平衡,以达到预期的效果。
2 脱酸脱酸也是油脂精炼的主要工序,脱除油脂中的游离脂肪酸可用化学或物理的方法。
精炼控制关键点

精炼工艺控制关键点一、脱胶工序胶溶性杂质:毛油中含的磷脂、蛋白质、黏液质和糖基甘油二酯等杂质,因与油脂组成溶胶体系而称之为胶溶性杂质。
胶溶性杂质的不良影响:1、碱炼影响:胶质使碱炼时产生过度的乳化作用,使油、皂不能很好地分离,即皂脚夹带中性油增加,导致炼耗增加,同时使油中含皂增加,增加水洗的次数及水洗引起的油脂损失;2、脱色影响:脱色时,胶质会覆盖脱色剂的部分活性表面,使脱色效率降低;3、脱臭影响:脱臭时温度较高,胶质会发生碳化,增加油脂的色泽;4、氢化影响:降低氢化速率。
脱胶:脱除毛油中的胶溶性杂质的工艺叫做脱胶,因毛油中的胶溶性杂质主要是磷脂,所以工业生产中常把脱胶称为脱磷。
在碱炼前先脱除胶溶性杂质,可以减少中性油的损耗,提高碱炼油质量,可以节约用碱量,并能获得有价值的副产品——磷脂。
脱胶方法:1、水化脱胶:对于磷脂含量多或希望磷脂做为副产品提取的毛油,通常采用水化脱胶;2、酸炼脱胶:达到较高的脱酸要求,可能需要采用酸脱胶,主要采用磷酸、柠檬酸等弱酸,硫酸很少用于食用油的脱胶。
一般酸脱胶得到的油脚色深,且部分磷脂变质,不能作为制取食用磷脂的原料。
3、吸附脱胶4、热聚脱胶5、化学试剂脱胶水化脱胶水化脱胶是利用磷脂等胶溶性杂质的亲水性,把一定数量的水或电解质稀溶液在搅拌下加入毛油中,使毛油中的胶溶性杂质吸水膨胀,凝聚并分离除去的一种脱胶方法。
影响水化脱胶的因素1、操作温度胶体分散相在一定条件下开始凝聚时的温度,称为胶体分散相凝聚的临界温度,只有等于或低于该温度,胶体才能凝聚。
胶体分散相吸水越多,凝聚临界温度也就越高。
温度高,油脂的黏度低,水化后油脂和磷脂油脚分离效果好;温度高,磷脂吸水能力强,吸水多,水化速度也快,磷脂膨胀的充分,有些夹持在磷脂疏水基团间的油被迫排出,因而水化温度高,有利于提高精炼率。
加入水的温度要与油温基本相同或略高于油温,以免油水温差悬殊,产生局部吸水不均匀而造成局部乳化。
终温不要太高,终温最好不要超过85℃。
油脂提炼技术资料 第三节 油脂脱酸.ppt

6、杂质的影响
胶溶性杂质、羟基化合物、色素等,对碱炼效果有 重要影响,促使碱炼产生持久乳化;其他色素增加用 碱量,造成中性油皂化机率。
碱液中的杂质影响碱的准确用量,其中的钙、镁盐 在中和时产生水不溶性的钙皂或镁皂,给洗涤操作增 加困难。配制碱溶液应使用软水。
7、分离
油-皂分离效果取决于皂脚的絮凝情况、皂脚稠度、 分离温度和沉降时间等。在连续式工艺中,油-皂分离 效果还受分离机性能、物料流量、进料压力以及轻相 (油)出口压力或重相出口口径等影响。
在碱滴的表面,进行界面反应。
(2)扩散作用:
界面反应使油-碱滴界面形成皂膜。皂膜里的碱滴 由于浓度差,不断扩散到皂膜外层,逐渐形成较稳 定的胶态离子膜。 (3)皂膜絮凝:
结构松散的皂粒吸附粗油中的胶质色素等杂质, 并在电解质、温度及搅拌作用下,相互吸引絮凝成 大的胶团即“皂脚”。
图6-10 碱炼脱酸过程示意图
吸附其他杂质形成皂脚与油脂分离。 (3)磷脂、棉酚与烧碱中和皂化反应形成皂脚。 (4)少量中性油皂化:
引起油脂精炼损耗增加。
O
‖
CH2─O─C—R1
│
O
│
‖
CH ─O─C─R2 + 3NaOH ======
│
O
│
‖
CH2─O─C─R3
CH2─OH │
│
R1COONa
CH ─OH + R2COONa │
(二)影响碱炼效果的因素
1、碱及其用量
(1)碱的种类: A、苛性钾(KOH):钾皂软,且苛性钾较贵,少用; B、氢氧化钙(Ca(OH)2):容易皂化中性油,脱色 能力差,且钙皂不便利用,少用; C、纯碱(Na2CO3):纯碱的碱性适宜,不易皂化中性油, 但反应过程中产生碳酸气,使皂脚松散而上浮于油面, 造成分离时的困难。 D、烧碱(NaOH):市售氢氧化钠有两种制品:隔膜法 制品;水银电解法制品。应选购隔膜法制品。
油脂的精炼——精选推荐
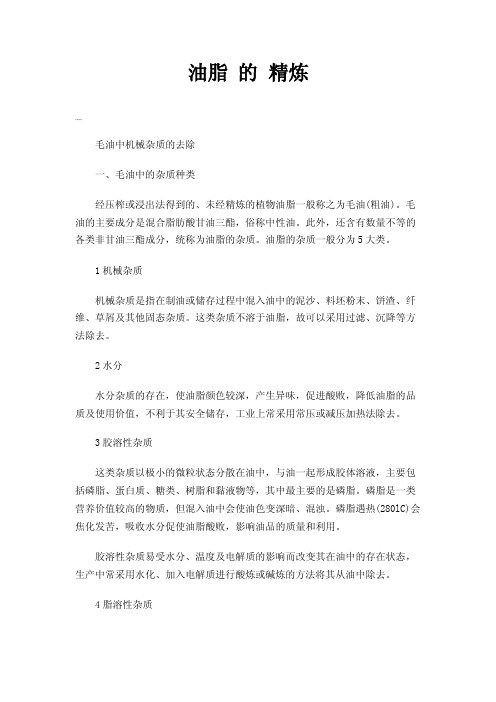
油脂的精炼毛油中机械杂质的去除一、毛油中的杂质种类经压榨或浸出法得到的、未经精炼的植物油脂一般称之为毛油(粗油)。
毛油的主要成分是混合脂肪酸甘油三酯,俗称中性油。
此外,还含有数量不等的各类非甘油三酯成分,统称为油脂的杂质。
油脂的杂质一般分为5大类。
1机械杂质机械杂质是指在制油或储存过程中混入油中的泥沙、料坯粉末、饼渣、纤维、草屑及其他固态杂质。
这类杂质不溶于油脂,故可以采用过滤、沉降等方法除去。
2水分水分杂质的存在,使油脂颜色较深,产生异味,促进酸败,降低油脂的品质及使用价值,不利于其安全储存,工业上常采用常压或减压加热法除去。
3胶溶性杂质这类杂质以极小的微粒状态分散在油中,与油一起形成胶体溶液,主要包括磷脂、蛋白质、糖类、树脂和黏液物等,其中最主要的是磷脂。
磷脂是一类营养价值较高的物质,但混入油中会使油色变深暗、混浊。
磷脂遇热(280lC)会焦化发苦,吸收水分促使油脂酸败,影响油品的质量和利用。
胶溶性杂质易受水分、温度及电解质的影响而改变其在油中的存在状态,生产中常采用水化、加入电解质进行酸炼或碱炼的方法将其从油中除去。
4脂溶性杂质主要有游离脂肪酸、色素、甾醇、生育酚、烃类、蜡、酮,还有微量金属和由于环境污染带来的有机磷、汞、多环芳烃、曲霉毒素等。
油脂中游离脂肪酸的存在,会影响油品的风味和食用价值,促使油脂酸败。
生产上常采用碱炼、蒸馏的方法将其从油脂中除去。
色素能使油脂带较深的颜色,影响油的外观,可采用吸附脱色的方法将其从油中除去。
某些油脂中还含有一些特殊成分,如棉子油中含棉酚,菜子油中含芥子甙分解产物等,它们不仅影响油品质量,还危害人体健康,也须在精炼过程中除去。
5微量杂质这类杂质主要包括微量金属、农药、多环芳烃、黄曲霉毒素等,虽然它们在油中的含量极微,但对人体有一定毒性,因此须从油中除去。
油脂中的杂质并非对人体都有害,如生育酚和甾醇都是营养价值很高的物质。
生育酚是合成生理激素的母体,有延迟人体细胞衰老、保持青春等作用,它还是很好的天然抗氧化剂。
油脂精炼技术与工艺
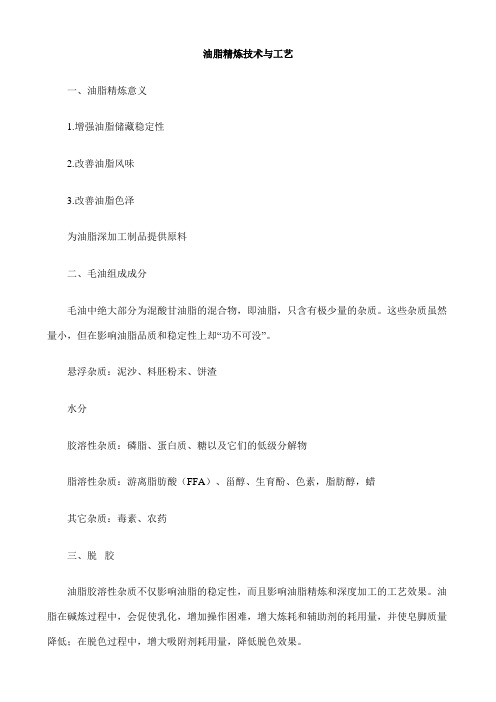
油脂精炼技术与工艺一、油脂精炼意义1.增强油脂储藏稳定性2.改善油脂风味3.改善油脂色泽为油脂深加工制品提供原料二、毛油组成成分毛油中绝大部分为混酸甘油脂的混合物,即油脂,只含有极少量的杂质。
这些杂质虽然量小,但在影响油脂品质和稳定性上却“功不可没”。
悬浮杂质:泥沙、料胚粉末、饼渣水分胶溶性杂质:磷脂、蛋白质、糖以及它们的低级分解物脂溶性杂质:游离脂肪酸(FFA)、甾醇、生育酚、色素,脂肪醇,蜡其它杂质:毒素、农药三、脱胶油脂胶溶性杂质不仅影响油脂的稳定性,而且影响油脂精炼和深度加工的工艺效果。
油脂在碱炼过程中,会促使乳化,增加操作困难,增大炼耗和辅助剂的耗用量,并使皂脚质量降低;在脱色过程中,增大吸附剂耗用量,降低脱色效果。
脱除毛油中胶溶性杂质的过程称为脱胶。
我们在实际生产中使用的方法是特殊湿法脱胶,是水化脱胶方法的一种。
油脂水化脱胶的基本原理是利用磷脂等胶溶性杂质的亲水性,将一定量电解质溶液加入油中,使胶体杂质吸水、凝聚后与油脂分离。
其中胶质中以磷脂为主。
在水分很少的情况下,油中的磷脂以内盐结构形式溶解并分散于油中,当水分增多时,它便吸收水分,体积增大,胶体粒子相互吸引,形成较大的胶团,由于比重的差异,从油中可分离出来。
影响水化脱胶的因素水量操作温度混合强度与作用时间电解质电解质在脱胶过程中的主要作用中和胶体分散相质点的表面电荷,促使胶体质点凝聚。
磷酸和柠檬酸可促使非水化磷脂转化为水化磷脂。
磷酸、柠檬酸螯合、钝化并脱除与胶体分散相结合在一起的微量金属离子,有利于精炼油气、滋味和氧化稳定性的提高。
使胶粒絮凝紧密,降低絮团含油,加速沉降。
四、脱酸植物油脂中总是有一定数量的游离脂肪酸,其量取决于油料的质量。
种籽的不成熟性,种籽的高破损性等,乃是造成高酸值油脂的原因,尤其在高水分条件下,对油脂保存十分不利,这样会使得游离酸含量升高,并降低了油脂的质量,使油脂的食用品质恶化。
脱酸的主要方法为碱炼和蒸馏法。
油脂精炼工段常见技术问题及解决办法探析_涂向辉 (1)

3 AND OILS PROCESSING
为此, 在间歇式碱炼操作时, 要注意: ①在加碱 中和时要用较强的搅拌强度(搅拌速度为 60~70r / min), 以增大碱液与游离脂肪酸的接触面积, 缩短中性油与 碱液的接触时间, 从而提高中和速率和降低中性油的 皂化损失; ②中和后要控制一定的搅拌强度(搅拌速度 为 30~15r / min), 以调节碱滴在油中的下降速度, 控制 胶膜结构, 避免生成厚的胶态离子膜, 并使胶膜易于 絮凝。 另外, 待碱炼的油最好先经过脱胶, 使其中胶 质含量减少, 才能保证良好的碱炼效果。
triacetin with methanol on Nafion acid resins [ J]. Journal of Catalysis, 2007 (245): 381~391. [8] Jaturong Jitputti, Boonyarach Kitiyanan, Pramoch Rangsunvigit, et al. Transesterification of crude palm kernel oil and crude coconut oil by different solid catalysts [J] . Chemical Engineering. 2006 (116): 61~66. [9] 张 敬 畅 , 孟 秀 娟 , 曹 维 良. 新 型 疏 水 性 固 体 酸 Zr (SO4)2 / AC 催 化 剂 的 制 备 及 其 催 化 性 能 [ J] . 催 化 学 报 , 2006, 27 ( 2) : 135~138. [10] Isa K. Mbaraka, Daniela R. Radu, Victor S.-Y. Lin, Brent H. Shanks. Organosulfonic acid-functionalized mesoporous silicas for the esterification of fatty acid [J] . Journal of Catalysis, 2003 ,
油脂精炼工艺与技术

2、操作温度
毛油中胶体分散相在一定条件下,开始凝聚时的温度, 称其为凝聚临界温度。
临界温度随分散相质点粒度而升高;而质点粒度又随
水化程度及胶体分散相吸水量而增大。因此,加水量 越大,质点粒度越大,凝聚临界温度就越高。
3、混合强度与作用时间
相界面上进行的非均态反应。机械混合使水滴形成足 够的分散度,又不能形成稳定的油/水或水/油乳化状 态。
对原油的适应性强。但中性油皂化及皂脚中夹带油造成精炼损 耗较高,耗碱,碱炼后水洗产生废水。
图3-1 碱炼脱酸过程示意图
界面反应使油-碱滴界面形成皂膜;皂膜里的碱滴扩散到皂膜 外层,继续与游离脂肪酸反应;胶态离子膜吸附粗油中的胶 质色素等杂质,并相互吸引絮凝成大的胶团即“皂脚”。
二、影响碱炼效果的因素
图2-1 磷脂分子与水作用时的排列
二、影响水化脱胶的因素
水化脱胶效果很大程度上取决于形成磷脂胶团的稳 定性。
1、加水量 适量的加水量才能形成稳定的多层脂质体结构。水
量不足,水化不完全,胶粒絮凝不好;水量过多, 容易形成水/油或油/水乳化现象,难以分离。 加水量与胶质含量和操作温度有关。 低温水化(20~30℃) W=(0.5~1)X; 中温水化(60~65℃) W=(2~3)X; 高温水化(85~95℃) W=(3~3.5)X; 水化时添加水温应与油温相等或略高
硫酸使蛋白质、粘液质等胶杂变性和树脂化,从油中析出;硫 酸使胶质发生水解;硫酸使色素发生磺化或酯化对油脂脱色; 硫酸作为强电解质,中和乳浊状和胶质的电荷,使它们发生凝 聚或絮凝。
二、碱炼法脱胶
碱性条件下,胶溶性杂质发生水解作用继而发生中和、凝聚、 吸附等作用而脱除。
三、吸附法脱胶
利用吸附剂的表面吸附作用将油中胶杂脱除。
- 1、下载文档前请自行甄别文档内容的完整性,平台不提供额外的编辑、内容补充、找答案等附加服务。
- 2、"仅部分预览"的文档,不可在线预览部分如存在完整性等问题,可反馈申请退款(可完整预览的文档不适用该条件!)。
- 3、如文档侵犯您的权益,请联系客服反馈,我们会尽快为您处理(人工客服工作时间:9:00-18:30)。
油脂脱酸工艺中影响碱炼的因素查考:中国榨油机网 油脂碱炼是一个相当复杂的过程。
为了选择最适宜的操作条件,获得良好的碱炼效果,现将碱炼时应掌握的一些主要影响因素讨论如下。
1、碱及其用量⑴碱油脂脱酸可供应用的中和剂较多,大多数碱金属的氢氧化物或碳酸盐。
常见的有烧碱(NaOH)、苛性钾(KOH)、氢氧化钙(Ca(OH)2)以及纯碱(Na2CO3)等。
各种碱在碱炼中呈现出不同的工艺效果。
烧碱和苛性钾的碱性强,反应所生成的皂能与油脂较好地分离,脱酸效果好,并且对油脂有较高的脱色能力,但存在皂化中性油的缺点。
尤其是当碱液浓度高时,皂化更甚。
钾皂性软,由于苛性钾价昂,因此,在工业生产上不及烧碱应用广。
市售氢氧化钠有两种工艺制品,一为隔膜法制品,另一为水银电解法制品。
为避免残存水银污染,应尽可能选购隔膜法生产的氢氧化钠。
氢氧化钙的碱性较强,反应所生成的钙皂重,很容易与油分离,来源也很广,但它很容易皂化中性油,脱色能力差;且钙皂不便利用,因此,除非当烧碱无来源时,一般很少用它来脱酸。
纯碱的碱性适宜,具有易与游离脂肪酸中和而不皂化中性油的特点。
但反应过程中所产生的碳酸气,会使皂脚松散而上浮于油面,造成分离时的困难。
此外,它与油中其他杂质的作用很弱,脱色能力差,因此,很少单独应用于工业生产。
一般多与烧碱配合使用,以克服两者单独使用的缺点。
⑵碱的用量碱的用量直接影响碱炼效果。
碱量不足,游离脂肪酸中和不完全,其他杂质也不能被充分作用,皂膜不能很好地絮凝,致使分离困难,碱炼成品油质量差,得率低。
用碱过多,中性油被皂化而引起精炼损耗会增大。
因此,正确掌握用碱量尤为重要。
碱炼时,耗用的总碱量包括两个部分,一是用于中和游离脂肪酸的碱,通常称为理论碱,可通过计算求得。
另一部分则是为了满足工艺要求而额外添加的碱,称之为超量碱。
超量碱需综合平衡诸影响因素,通过小样试验来确定。
①理论碱量。
理论碱量可按粗油的酸值或游离脂肪酸的百分含量进行计算。
当粗油的游离脂肪酸以酸值表示时,则中和所需理论NaOH量为:M NaOH 1GNaOH理=G油× AV ×———— ×———=7.13×10-4×G油× AV(6-5)M KOH1000式中:GNaOH理—氢氧化钠的理论添加量(kg);G油—粗油脂的重量(kg);AV—粗油脂的酸值(mgKOH / g 油);M NaOH—氢氧化钠的分子量,40.0;M KOH—氢氧化钾的分子量,56.1;当粗油的游离脂肪酸以百分含量给出时,则可按公式(6-6)确定理论NaOH量:40.0GNaOH理=G油× FFA% ×————(6-6)M式中:GNaOH理—氢氧化钠的理论添加量(kg);G油—粗油脂的重量(kg);FFA%—粗油脂中游离脂肪酸百分含量;M—脂肪酸的平均分子量;一般取粗油中的主要脂肪酸的平均分子量。
例如,棉籽油的主要脂肪酸为油酸和亚油酸,其平均分子量为281.46,则式(6-6)可导成:GNaOH理=0.1421 ×G油× FFA%(6-7)②超量碱。
碱炼操作中,为了阻止逆向反应弥补理论碱量在分解和凝聚其他杂质、皂化中性油以及被皂膜包容所引起的消耗,需要超出理论碱量而额外增加一些碱量,这部分超加的碱称为超量碱。
超量碱的确定直接影响碱炼效果。
同一批粗油,用同一浓度的碱液碱炼时,所得精炼油的色泽和皂脚中的含油量随超量碱的增加而降低。
中性油被皂化的量随超量碱的增加而增大。
超量碱增大,皂脚絮凝好,沉降分离的速度也会加快。
图6-10示出了超量碱与炼耗之间的关系。
不同油品和不同的精炼工艺,有不同的曲线,可由试验求得。
曲线Ⅲ的最低点示出最合适的超碱量。
图中的数值为全封闭快混合连续碱炼工艺的最适超碱量。
由此可见,超量碱的确定,必须根据粗油品质、精油质量、精炼工艺和损耗等综合进行平衡。
当粗油品质较好(酸值低、胶质少、色泽浅),精炼油色泽要求不严时,超量碱可偏低选择,反之则应选择高些。
连续式的碱炼工艺,油、碱接触时间短,为了加速皂膜絮凝,超量碱一般较间歇式碱炼工艺高。
超量碱的计算有两种方式,对于间歇式碱炼工艺,通常以纯氢氧化钠占粗油量的百分数表示。
选择范围一般为油量的0.05%~0.25%,质量劣变的粗油可控制在0.5%以内。
对于连续式的碱炼工艺,超量碱则以占理论碱的百分数表示。
选择范围一般为10%~50%。
油、碱接触时间长的工艺应偏低选取。
③碱量换算。
一般市售的工业用固体烧碱,因有杂质存在,NaOH含量通常只有94%~98%,故总的用碱量(包括理论碱和超量碱)换算成工业用固体烧碱量时,需考虑NaOH纯度的因素。
当总碱量欲换算成某种浓度的碱溶液时,则可按式(6.3-8)来确定碱液量:GNaOH理+GNaOH超(7.13×10-4 ×AV +B)×G油GNaOH =————————=——————————————(6-8)CC式中:GNaOH—氢氧化钠的总添加量(kg);GNaOH里—氢氧化钠超量碱(kg);GNaOH 超—氢氧化钠的总添加量(kg);G油—粗油脂的重量(kg);AV—粗油脂的酸值(mgKOH / g 油);B—超量碱占油重的百分数;C— NaOH溶液的百分比浓度(W/W)。
油脂工业生产中,大多数企业使用碱溶液时,习惯采用波美度(°Bé)。
各种常用烧碱溶液的重量百分比浓度与波美浓度的关系见表6-8。
表6-8烧碱溶液波美度与比重及其他浓度的关系(15℃)波美度(°Be′)比重(d)百分浓度(%)当量浓度(N)波美度(°Be′)比重(d)百分浓度(%)当量浓度(N)4 1.029 2.50 0.65 19 1.15 13.50 3.896 1.043 3.65 0.95 20 1.161 14.24 4.138 1.059 5.11 0.33 21 1.170 15.06 4.4110 1.075 6.58 1.77 22 1.180 16.00 4.7211 1.083 7.30 1.98 23 1.190 16.91 5.0312 1.091 8.07 2.20 24 1.200 17.81 5.3413 1.099 8.71 2.39 25 1.210 18.71 5.6614 1.107 9.42 2.61 26 1.220 19.65 5.9915 1.116 10.30 2.87 27 12.30 20.60 6.3316 1.125 11.06 3.11 28 1.241 21.55 63.6917 1.134 11.90 3.37 29 1.252 22.50 7.0418 1.143 12.59 3.60 30 1.263 23.50 7.42例:某油脂加工企业,精炼一批酸值为7的毛棉油,超量碱选用0.2%,试求碱炼每吨油所需工业固体碱(纯度为95%)、16°Be′及20°Be′烧碱溶液的重量。
解:GNaOH理=7.13×10-4×G油× AV =7.13×10-4×1000× 7 =5(kg)GNaOH超=0.2%×G油=0.2%× 1000 =2(kg)固体烧碱重量=(5+2)÷95% =7.37(kg)查表6-3,16°Be′及20°Be′烧碱溶液的百分比浓度分别为11.06%和14.24%。
依据式(6-8)则:16°Be′烧碱溶液的重量:GNaOH理+GNaOH超 5 +2GNaOH =————————=——————=63.29(kg)C11.06%20°Be′烧碱溶液的重量:GNaOH理+GNaOH超 5 +2GNaOH =————————=——————=49.09(kg)C14.24%2、碱液浓度⑴碱液浓度的确定原则。
碱炼时碱液浓度的选择,必须满足:①碱滴与游离脂肪酸有较大的接触面积,能保证碱滴在油中有适宜的降速;②有一定的脱色能力;③使油-皂分离操作方便。
适宜的碱液浓度是碱炼获得较好效果的重要因素之一。
碱炼前进行小样试验时,应该用各种浓度不同的碱液作比较试验,以优选最适宜的碱液浓度。
(2)碱液浓度的选择依据。
选择碱液渡的依据如下:①粗油的酸值与脂肪酸组成。
粗油的酸值是决定碱液浓度的最主要的依据。
粗油酸值高的应选用浓碱,酸值低的选用淡碱。
碱炼粗棉油通常采用12~22°Bé碱液。
长碳链饱和脂肪酸皂对油脂的增溶损耗,较之短碳链饱和脂肪酸皂或不饱和长碳链脂肪酸皂大,因此,大豆油、亚麻油、菜籽油和鱼油宜采用较高浓度的碱液,椰子油、棕榈油等则宜采用较低的碱液浓度。
②制油方法。
油脂制取的工艺及工艺条件影响粗油的品质。
在粗油酸值相同的情况下,用碱浓度按制油工艺统计的规律为:浸出>动力榨机压榨>动力榨机预榨>液压机榨>冷榨。
但此规律仅能供作选择碱液浓度时参考,并不能作为确定碱液浓度的依据。
因为粗油的品质还决定于制油工艺条件以及粗油的保质处理。
因此,当考虑制油工艺对碱液浓度选择的影响时,须根据粗油的质量具体分析。
③中性油皂化损失。
当含有游离脂肪酸的粗油与碱液接触时,由于酸碱中和反应比油碱皂化反应速度快,故中性油的皂化损失一般是以碱炼副反应呈现的。
皂化反应的程度决定于油溶性皂量和碱液浓度。
当碱炼的其他操作条件相同时,中性油被皂化的机率随碱液浓度的增高而增加。
④皂脚的稠度。
皂脚的稠度影响分离操作。
稠度过大的皂脚易引起分离机转鼓及出皂口(或精炼罐出皂截门)堵塞。
在总碱量(纯NaOH)给定的情况下,皂脚的稠度随碱液浓度的稀释而降低。
此外,据研究,皂脚包容的中性油,其油珠粒度取决于皂脚中水和中性油的含量,即油珠粒度与皂脚的稠度有密切关系,随着皂脚的稀释,皂脚中包含的油珠粒度将增大。
油珠粒度增大即可提高油珠脱离皂脚的速度,从而有利于皂脚含油量的降低。
⑤皂脚含油损耗。
碱炼时,反应生成的皂膜具有很强的吸收能力,能吸收碱液中的水和反应生成的水。
当采用过稀的碱处理高酸值粗油时,所生成的水皂溶胶,受到的碱析作用弱,皂膜絮凝不好,从而增加了皂脚乳化油的损耗。
甚至会在不恰当的搅拌下形成水/油持久乳化现象,给分离操作增加困难。
皂脚乳化包容中型油一般与碱液浓度呈反比关系。
选择适宜的碱液浓度,才能使皂脚乳化包容的中性油降至最低水平。
⑥操作温度。
温度是酸碱中和反应及油碱皂化反应的动力之一。
由阿仑尼乌斯(Arrhenius)方程:lgK = A – B/T可知,反应速度常数K的对数与绝对温度T的倒数呈直线关系,即反应速度常数随操作温度的升高而增大。