轴系安装工艺新
轴系安装工艺
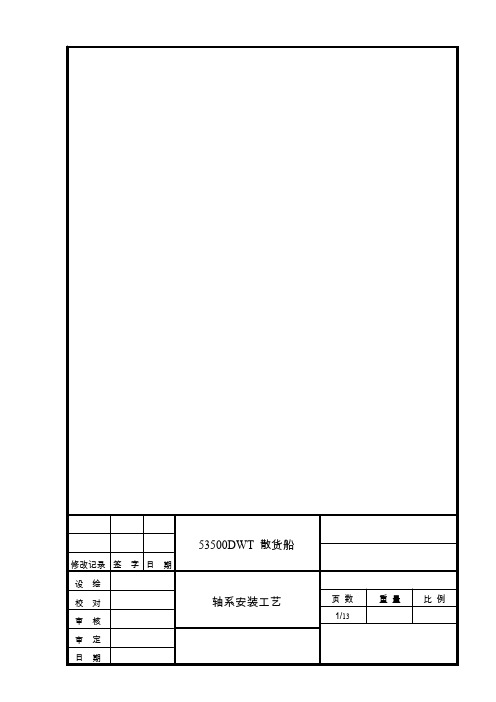
2/13
53500DWT 轴系安装工艺
3/13
1. 预拉线 1.1. 准备好φ0.5(或φ0.8)的钢线两根,一根长约 40m(用于轴系拉线) ,一 根长约 20m(用于舵系拉线) 。 1.2. 在机舱后舱壁(Fr12)或 Fr31 前 1m 处和 Fr0 后 1m 处分别设立拉线架。 1.3. 在机舱后舱壁(Fr12)相应位置(X=Fr12,Y=0,Z=3300)等处开φ200 的孔,以便钢线通过。 1.4. 拉好钢线,并在艏拉线架端进行可靠的固定,在艉拉线架端挂上重物,以 保持钢线张紧。 1.5. 对钢线进行调整,使钢线分别通过点 1(X=0,Y=0,Z=3300)和点 2(X=0, Y=Fr12 或 Fr31,Z=3300) 。 1.6. 检查轴系中心线和舵系中心线的相互位置的偏差,偏差值δ≤3mm。 1.7. 检查舵系中心线与基线的垂直度,偏差应≤1mm/m。 1.8. 检查舵系中心线与轴系中心线交点至艉柱端面的垂直距离,应为 4300mm (在镗孔前此距离为 4290mm) 。 1.9. 在机舱后舱壁(Fr12)及艉柱端面处划好检验圆线,重新校核检验圆线, 并打上样冲眼。 1.10. 不同直径钢线所挂重物重量(表 1 或表 3)及相应位置挠度值表(表 2 或 表 4) (仅适用预拉线) 。 表1 钢线直径(mm) φ0.5 φ0.8 所挂重物重量(N) 200 550 表 2(单位 mm) 钢线直径 φ0.5 φ0.8 2.
艉柱端面处钢线挠度 0.005 0.004
机舱后舱壁处钢线挠度 0 0
艉管安装(见船体工艺部分)
3. 轴系拉线 3.1. 拉线前的准备工作 3.1.1. 船体装配工作,从艉端算起在船长的 85%内的必须完成,在高度上必须 装到上甲板。 3.1.2. 主机及轴系的安装区域内,所有的舱室及水舱(柜) 、油舱(柜)都应经 过焊缝检验及水密试验并合格。 3.1.3. 在轴系校中前,船上所有重量较大的设备都应安放到位,或用相当重量 的物件放在相应的位置上代替,不允许在轴系安装过程中有重量较大的 物件放入、取出或移动位置。 3.1.4. 全船有冲击性和振动性的工作全部停止。
轴系安装及主机定位工艺规程
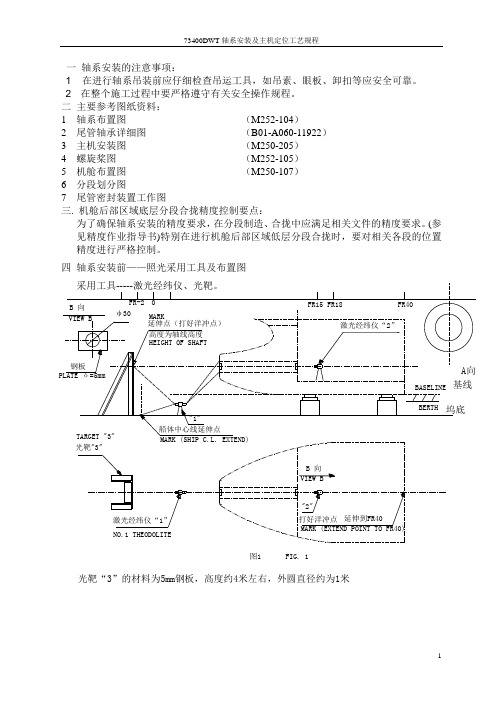
一轴系安装的注意事项:1 在进行轴系吊装前应仔细检查吊运工具,如吊素、眼板、卸扣等应安全可靠。
2 在整个施工过程中要严格遵守有关安全操作规程。
二主要参考图纸资料:1 轴系布置图(M252-104)2 尾管轴承详细图(B01-A060-11922)3 主机安装图(M250-205)4 螺旋桨图(M252-105)5 机舱布置图(M250-107)6 分段划分图7 尾管密封装置工作图三. 机舱后部区域底层分段合拢精度控制要点:为了确保轴系安装的精度要求,在分段制造、合拢中应满足相关文件的精度要求。
(参见精度作业指导书)特别在进行机舱后部区域低层分段合拢时,要对相关各段的位置精度进行严格控制。
四轴系安装前——照光采用工具及布置图图1FIG. 1光靶“3”的材料为5mm钢板,高度约4米左右,外圆直径约为1米五轴系中心线确定的条件:1 机舱前壁以后,主甲板以下主船体成型。
2 舵机平台以下焊接完。
3 轴系区域内主要辅机机座装焊完成,除主机以外的一般设备就位。
4 船体垫墩、支柱受力均匀、稳定牢固,不允许随意移动。
5 照光所用的仪器及测量工具应校验合格。
六轴系中心线的确定轴系中心线的确定应根据季节温度变化来进行,夏天一般在晚上8-9点进行,冬天一般在下午5点左右进行, 或在阴天进行,在轴系中心线的确定过程中,船上不应有能够导致船体变形的工作在进行。
1 船体尾部理论轴中心面的确定。
①以坞底平面上船体中心线的延伸点为基准,调整激光经纬仪“1”的轴线直至与船中心线重合。
②将激光经纬仪“1”射出的光点延伸到船坞尾部光靶“3”上,根据机舱区域舱底龙骨平整度数据平均值为基线高度并在垂直方向向上平移轴系高度+船体板厚,则此点为轴系轴线上一点。
以此点作为基点并打好样冲点,同时将激光经纬仪旋转180°将光点投射到尾柱平面上,并打好样冲,这样就可初步确定轴系尾部理论垂线。
2 机舱内轴系中心线的确定在机舱与尾管前平面适当位置设立一激光经纬仪“2”,将光点延伸到船体外部的光靶“3”,使之与光靶“3”上的样冲点重合。
船舶轴系安装及校中工艺

船舶轴系安装及校中工艺摘要按校中计算的要求和方法将轴系装成某种状态(直线或曲线),处于这种状态的轴系,其各轴段上内力和各轴承上的负荷均应处在允许范围之内,或具有最佳的数值,以保证轴系和与之相连的机械(如主机曲轴、齿轮箱等)能持续正常的运转,这部分工作称为轴系校中。
本文船舶轴系安装及校中工艺进行了论述。
关键词轴系校中;主机安装;机座扭曲度;机座下沉量;主机曲轴拐挡差;轴承间隙;轴承负荷中图分类号u66 文献标识码a 文章编号 1674-6708(2011)56-0115-031 概述按校中计算的要求和方法将轴系装成某种状态(直线或曲线),处于这种状态的轴系,其各轴段上内力和各轴承上的负荷均应处在允许范围之内,或具有最佳的数值,以保证轴系和与之相连的机械(如主机曲轴、齿轮箱等)能持续正常的运转,这部分工作称为轴系校中。
校中安装顺序一般有两种,一种是在尾轴和主机均已安装完毕,此时的中间轴及轴承须根据尾轴及主机的实际位置进行校正安装,另一种是在尾轴安装完毕后,自艉至艏逐节校中安装中间轴及其轴承,主机在中间轴安装后再进行校正定位。
江苏省重工有限公司采用的校中顺序是后者。
但不论采用哪种安装方法,轴系校中的结果,都应保证各轴段上内力和各轴承上的负荷均应处在允许范围之内。
现根据江苏省重工有限公司多年建造万吨船的实践经验,结合校中计算书和主机厂的规范要求和方法,就江苏省重工有限公司建造的11.4万吨油轮船舶螺旋桨处于70%浸没状态下校中的方法介绍如下。
2 轴系校中前的准备工作1)尾轴及螺旋桨根据轴系布置图安装并已交验结束;2)根据本船轴系布置图(参见附图2)及主机安装图要求主机及中间轴承已初步定位;3)在中间轴距其端法兰端面某处安装临时支撑。
本船按校中计算书要求在中轴距其艏端法兰2528位置安装临时支撑,本船参见附图2;4)刮拂中间轴承座上平面的固定垫块,用平板检验接触点应均匀分布,每25mm2不少于2-4点,固定垫块上平面按图纸要求加工成倾斜度1/100;5)调整船舶浮态,使螺旋桨处于70%浸没状态下校中。
尾轴系安装工艺(11000DWT)

11000DWT成品油/化学品船工艺文件标记数量修改单号签字日期尾轴系安装工艺VZJ527-403-01ZG编制打字校对审核总面积m2共5页第1页标检乐清市长虹船舶制造有限公司审定日期1、总则1.1 本工艺规定的各道工序均应在下列工作完成后进行。
(1)船体大合拢(焊接)完毕并经检验合格。
(2)主甲板以下全部装焊完毕并经水火矫正(含主机座、齿轮箱座)。
(3)轴系布置区域内各密性舱柜的气(水)密试验收合格。
(4)拉线工作不受阳光爆晒或大风影响下进行,同时应停止各种强烈的振动与敲击及移动重物工作。
2、拉线工作2.1 根据下列图纸(1)VZJ527-400-02 机舱布置图(2)VZJ527-425-01 轴系布置图(3)VZJ527-420-01 主机及齿轮箱安装图(4)VZJ527-425-02-00 尾轴尾管总图(5)VZJ527-230-02 舵系布置图2.2 设立拉线架2.2.1 在27#肋位+300船中处距基线2700mm处设第一拉线架。
2.2.2 在-2#肋位+200船中处距基线2700mm处设第二拉线架。
2.2.3 在0#肋位靠近船台船中处(基线以下)设第三拉线架。
2.2.4 在0#肋位主甲板上船中处设第四拉线架。
2.3 拉线2.3.1 在舵系,艉轴系拉线所通过的舱壁开设相应小孔。
2.3.2 选用Ф0. 6mmⅡ组碳素弹簧钢丝二根分别按装在第一、第二拉线架及第三、第四拉线架间,并在第二拉线架钢丝尾端悬挂36kg重铁锤。
(钢丝与钢锤面积:0.0625m2必须用较软绳丝相联)。
2.3.3 拉紧二根钢丝。
2.3.4 用铅锤线找出船中线,并将轴系之钢丝左、右调正到位。
相应考虑主机,齿轮箱机坐的左、右对称,以免影响主机,齿轮箱正确安装。
2.3.5 用钢尺将轴线钢丝调至距基线2700mm处,兼顾艉柱中尾管孔位置。
2.3.6 将舵系钢线下部调正在舵销承的中点处,上部调正至主甲板相对应肋位船中处。
2.3.7 检查两根钢丝的准确位置,两钢丝相交不相碰,间隙以0.2mm至5mm间隙的允许,偏差δ≤0.001 √L m=0.001 √132 m=0.00509 m=5.09mm。
船舶轴系的安装

2.5.2 加工工具
由于镗孔工作经常在船台上进行,无法使用固 定的镗床.因此各船场根据需要设计镗孔专用工具,称 镗排。
图2-26一种典型结构的镗杆 1-进给箱;2-传动机构;3-推力轴承;4-支承轴承;5-轴承支架;6-平面刀架; 7-尾柱轴毂;8-刀架;9-中间轴承;10-尾隔舱壁;11-电动机;12、13-皮带轮
第二节 船舶轴系安装工艺的一般过 程
轴系安装的基本工作内容:轴系位于主机和 螺旋浆之间,担负着把主机的扭矩传给螺旋浆, 同时又把螺旋浆的作用力通过轴系中的推力 轴传给船体,使船舶根据驾使指令航行. 轴系安装任务是完成主机到螺旋浆的整个 轴系中的尾管及尾管轴承,螺旋浆与浆轴的安 装,中间轴及中间轴承,推力轴及推力轴承等部 件的安装任务.同时还涉及到主机的安装过程.
不柱度 0.02 椭圆度 0.01
0.02 0.01 0.015
0.03 0.02 0.02
0.03 0.02 0.02
螺栓
不柱度 0.015
椭圆度 0.01
0.01
0.15
0.15
2.3.2 尾轴的装配 一 尾轴红套
采用水润滑的尾轴,工作条件恶劣,且
与海水接触,因此需要有轴颈表面的铜包覆 层,主要起防腐作用,兼有改善轴与尾管轴承 之间的摩擦作用力。
第三节 轴系主要零部件的内场装配
2.3.1 轴的配对
船舶轴系是由尾轴,中间轴,推力轴等分别加 工,然后通过螺栓组合而成。 轴系配对是指各轴段置于同一直线上,保证其 同轴度要求,然后铰镗法兰上的螺栓孔,并配置相应的 螺栓,固紧等一系列工作的总称。 轴系的配对工作可以在平台上或长台车床上 进行,如下图2-3所示。
为了进行轴系安装工程,机电车间要进行内 场(车间内)加工装配和外场(一般在船台)加工 和安装. 内场(车间内)主要完成轴系零件的加工装配 外场(一般在船台)主要完成船体加工和安装,
艉轴安装工艺

艉轴安装工艺1、零部件验收要求2、艉轴管安装操作程序3、艉轴承安装操作程序4、艉轴安装操作程序轴系安装(艉轴系)须在艉柱壳和隔舱艉管孔镗削完毕后,经验收合格方可进行,在安装前须作充分准备,具体程序:1、零部件验收要求(由检验员验收)对轴系所有重要零部件须在车间验收合格方可上船。
a、艉轴管:已消除在粗车后发现的疏松、冷隔、浇铸偏缺或液压试验渗漏等缺陷后,且要求艉轴管首法兰面与轴心线垂直度每米不超过0.15毫米,艉轴管各内外圆应同心,同轴度不大于0.10毫米。
外圆不同轴颈或内圆不同孔径的轴心线应位于同一轴心线上,同轴度不超过0.025毫米。
尾管与艉柱毂孔配合的要求见表1。
b、艉轴承衬套外圆加工的尺寸与艉轴管孔的配合标准见表2,对小型船舶允许采用复套和环氧树脂定位。
对白合金艉轴承衬套外圆与艉管孔配合可按表2放松0.01~0.03毫米。
c、艉轴精加工后的检查应参照图纸,并以实际尺寸为基准,按验收标准表3、表4、表5选配艉轴与轴承的间隙,工作轴颈锥体的加工技术要求须符合验收标准表3、表4、表5值同时对法兰面及定位凸肩作验收测量须符合验收标准,验收完毕后须对工作轴颈锥体以及两端曼纹上好油脂,做好保证工作。
d、螺旋桨的材料、加工,静平衡试验按验收标准(螺旋桨制造及修理),并在车间内作一次予装试拆,测量防蚀套与密圆到位情况,以及螺旋桨锥面到位,并作记号(此项工作须在艉轴和螺旋桨单件验收合格后进行)。
其次外购件须有合格证书,经检验后方可安装,零件的验收工作必须按交验项目、内容验收,按验收阶段,验收单位进行验收,特别是对船检师,船东验收的项目应多加注意,并事先做好充分准备,不得有遗漏,以免影响生产顺利进行。
2、艉轴管安装:a、艉轴管衬套一般都须在车间内压入,压入采用液压拉伸器如图1或螺旋拉伸图2。
操作程序1) 压板与拉杆螺栓安装前,将艉轴管内径及轴承外径的油槽油孔位置复查一遍。
油槽相位:一般根据轴承直径拉有3~5条且油槽拉在轴承上部,同时复查其过盈量是否在验收标准表2规定内。
轴系安装原则工艺

1.概述1.1轴系安装工作是船舶建造中重点控制的工作程序,为此特制订本原则工艺。
1.2本工艺主要阐述轴系拉线安装原则工艺,本工艺在实施过程中,轴系的零部件和轴系的拉线、安装工作需按“船舶交验项目表”(由检验部编制)要求及时向有关部门报检,经检验合格后方可移交下道工序安装制作。
2.艉柱定位2.1 挂舵臂预先在分段中拉线定位焊接,要求其与理论中心线偏差小于3mm,上船台大合拢时,其与理论中心线的偏差应不大于12mm,保证环氧浇注所需的最小厚度13mm。
挂舵臂前端面至主机输出端法兰面的距离,其误差为士10mm,以保证主机的安装位置。
3.艉管拉线和照光3.1 拉线前应具备的条件a. 对船体建造进度的要求最末货舱往后和主甲板以下的主要船体结构的焊接及火工矫正工作结束。
上述区域的双层底、艉尖舱,机舱内与船体连接的舱室和箱柜的密性试验工作应结束。
发电机等大型设备进舱。
船体艉部的临时支撑应处于松开状态。
船体基线经检查,符合公差标准,画出船体基线与船体中心线并做出明显标志。
除上述要求外,其他船体施工仍可按船厂建造进度进行,但在轴系找中时,凡影响轴系找中的所有吊装工作应停止。
b. 对周围环境的要求要求在不受阳光曝晒及温度无急剧变化的情况下(船体左右舷的温差应该控制在2℃以内),即在晚间或阴雨天时进行,以避免船体的温差变形。
震动作业和有严重噪音干扰的作业必须停止。
3.2 艉管定位3.2.1 艉管已在承包商工厂拼装,焊接,加工结束。
前后轴承按压入计算书的要求压装到位,并经检验合格。
3.2.2 加强板在内场按放样长度要求进行焊接。
需以适当的间隔分步对称进行焊接,使得在下一焊接开始前,前一焊缝己经冷却。
3.2.3 清洁艉柱内孔经检验合格后,从机舱内缓慢吊艉管进入艉柱中并定位,没有加强板的艉管从外往机舱内吊入,艉管前后各用四根顶升螺栓(成45度方向)初调艉管后拉钢线(见下述)。
3.3 拉线3.3.1 初拉线的任务a. 确定轴系中心线距船体基线和船体舯线的正确位置。
船舶轴系的加工与安装工艺流程中心线与舵系中心线的指交度

目录1、船舶轴系的加工与安装工艺流程----------------22、船舶轴系找中----------------------------------------43、轴系安装工艺----------------------------------------64、舵系及螺旋桨安装工艺----------------------------75、主机安装工艺----------------------------------------8船舶轴系的加工与安装工艺流程1.配合船体在后分段焊接艉柱时的拉线,(由船体拉线),目的复核尾轴管长度,以及控制轴系中心线与舵系中心线的指交度。
2.初步拉线、船体建造后的第一次拉线,目的(1)检查轴系中心线与舵系中心线的相交度;(2)检查确定主机座、齿轮箱座位置;(3)确定重磅厚度估计中间轴承座高度;(4)估计垫块厚度,主机齿轮箱等底脚螺丝的预制尺寸与基线偏差。
3.找中复核,(由轮机拉线、质管部、船研所到场)目的决定尾管中心线镗削位置,安排镗排的基准。
4、镗孔5.复线:镗孔后的拉线,目的(1)向船检师及船主提交轴系与舵系的相交度;(2)制定尾轴系样棒;(3)提供尾轴管的具体尺寸。
6.复测:在复线基础上较为准确地测量,目的是正确决定主机在机座上的左右、前后位置。
7.艉轴管安装。
8.尾轴安装步骤:a.尾轴安装b.装尾轴油封(检查渗漏)c.安装螺旋桨及舵系d.安装中间轴9.机座重磅板定位焊接、拂磨10.离合器、主机进舱,临时固定11.下水后,按平轴法安装中间轴12.齿轮箱定位13.主机定位14.拂垫块15.钻孔16.非定位螺钉紧固17.绞定位螺栓孔配置定位螺栓18.安装完毕检验,向船验师提交轴系安装数据船舶轴系找中轴系是船舶动力装置重要组成部分,轴系的好坏直接关系到船舶航行安全及使用寿命,船舶的建造对轴系的要求提高到特别重要地位。
一.目前我公司采用拉钢丝线找中定位二.找中工艺(拉钢丝线)(一)新造船舶轴系,拉钢丝线找中心前,船舶建造工程应完成下列工作:1.船舶主甲板以下船体结构及设在该区内的第一层上层结构全部焊接及火工校正工作全部结束。
- 1、下载文档前请自行甄别文档内容的完整性,平台不提供额外的编辑、内容补充、找答案等附加服务。
- 2、"仅部分预览"的文档,不可在线预览部分如存在完整性等问题,可反馈申请退款(可完整预览的文档不适用该条件!)。
- 3、如文档侵犯您的权益,请联系客服反馈,我们会尽快为您处理(人工客服工作时间:9:00-18:30)。
轴系安装工艺新一、概述:本工艺的制定是根据《中国造船质量标准》(2005)及相关规范、标准制定的。
本工艺包括的 工作内容:轴系、舵系放线、艉轴管及密封装置的安装、螺旋桨安装、中间轴安装、齿轮箱 安装、主柴油机安装;艉柱、吊舵臂、挂舵臂的安装,吊舵臂镗孔,下舵承、舵销承装配, 舵叶拂配,舵系装配等等;本工艺文件规定了上述内容的施工方法和技术要求。
1、基本工艺流程轴系、舵系理论中前支撑定位f 艉管定位f 艉轴承安装f 艉轴及密封装置安装 > 螺旋桨安装 中舵系装配十 间轴对中安装f 齿轮箱对中安装f 主柴油机对中安装 2、 放轴系中心线和舵系中心线3. 1拉线前船台施工应具备的条件:3. 1. 1拉线前应完成的工作主船体机舱段主甲板下全部完工及密性试验完成,尾部油、水 舱、柜密性试验完成,相关构件及外板装焊完工后,机舱前壁向船首的一条环形大接缝焊装 结束,大型机器设备预定位,船体基线以及横倾由船体部门确定并验收合格。
3. 1. 2主机及轴系的基座都已焊好,并交验合格。
3. 1. 3在确定轴系理论中心线、主机定位及校中轴系时,船上应停止冲击或振动作业。
3. 1. 4轴系校中安装应考虑和排除阳光照射引起船体变形的影响。
一般在早晚或阴雨天进 行。
3. 2轴系和舵系理论中心线基准点的确定、检查:编 制描 打校 对描 校审 核标 检审疋日 期 2011 -2-9挂舵臂安装焊 接工艺总面积 m 2 共12页 第1页湖北江润造船有限公司心线的确定挂舵臂定位f 舵销套定位 吊舵臂镗孔 f 舵杆与舵叶拂配 f下舵承、舵销承装配吊舵臂、3. 2. 1按船体提供的最终的基线标,用激光经纬仪测出轴线高度(本船轴线与基线平行,轴线距基线高度为2200 mm),并从艉部引向机舱内按图纸要求确定32#舱壁处轴线离基线高度为2200 mm,确定轴线首靶点。
3. 2. 2同理,按图在4#肋位垂直于船肿中纵线,高度值为2200 mm,确定轴线艉靶点。
3. 2. 3连接两靶点,用© 0.8mm钢丝挂重量约为75Kg,分别延长至-5#检查,-5#距基线高度应为2200mm,以检查船体焊接试水后变形数据,检查主机座安装误差情况。
按理论值,也可检查轴线挠度。
(如图1)I3、钢丝自重及挠度修正值如下:Y=g*x(l-x)/0.99*2G式中Y—挠度修正值(m);g—钢丝线单位重量(N/ m);L —钢丝两基准点间的距离(m);X—所求挠度到基点距离(m);G —钢丝拉紧力(N);5、理论轴线确定后,检查主机座位置及高度尺寸是否满足要求。
主机座满足要求后,将首靶点移至13#肋位处,13#肋位距轴线高度按理论计算为2200 mm。
6、靶点用大于100X100X 8角钢制作固定。
7、轴系理论中心线的要求:轴系理论中心线与船体纵中心线的不平行度误差不大于0.3mm/m ;轴线与基线平行,且只允许后端向下倾斜。
8、舵系拉线与轴系拉线同时进行。
舵系则在0#肋位处按船体中心线向上与轴线重合并沿伸至舵机平台甲板上,并做好标记(注意:在舵系放线之前,需要检查船舶的横倾,如有则需要调整下基准点)。
用一根© 0.8mm钢丝连接上下两基点并在钢丝下端挂一重~50 Kg的重物, 此钢丝即为舵系理论中心线,并在主甲板及艉楼甲板倒龙骨上用样冲做好标记。
该线同时引到艉封板上做好标记,为舵叶吊中的基准线。
上述拉线基准点需经检验员确认,施工人员按此基准点进行轴系与舵系的拉线。
9、舵系中心的误差应符合表1的要求:表9.1轴系理论中心距基线的高度应根据主船体的变形情况而作适当调整,但调整方法和调整数值应同设计院和船东代表协商。
9、2报船东代表和船检验船师检验,若没有达到上述规定的指标应调整。
10、艉柱、吊舵臂的安装:10.1安装艉柱,以轴系理论轴线为基线,根据图纸指定的位置,将艉柱安装到主船体上(注意,安装艉柱前需要将艉管及艉管前支撑从尾部往机舱装进去,并往机舱多拉一些,以不影响安装艉柱为原则);10.2安装吊舵臂,以舵系理论轴线为基线,根据图纸指定的位置,将吊舵臂安装到主船体上,然后将艉柱与吊舵臂之间的船体构件安装到船体上。
10.3艉柱、吊舵臂的焊接要求是有经验的持证焊工,严格按如下焊接顺序施焊:10. 3. 1先焊吊舵臂,焊接顺序为先焊接船体构件与构件之间的焊缝,再焊吊舵臂与船体构件之间的焊缝,焊接采用对称和跳焊的方法,严格控制变形,注意在焊接过程中,钳工要不断地测量吊舵臂下舵承外壳、舵销承外壳中心线与舵系中心线是否重合,根据变形情况调整焊接方向。
10.3. 2再焊艉柱,焊接顺序为先焊接船体构件与构件之间的焊缝,再焊艉柱与船体构件之间的焊缝,焊接采用对称和跳焊的方法,严格控制变形,注意在焊接过程中,钳工要不断地测量艉柱内孔中心线与轴系中心线是否重合,根据变形情况调整焊接方向。
11、艉管前支撑的安装11.1安装艉管前支撑,根据轴系理论中心线调整艉管前支撑使其内孔中心线与轴系理论中心线相吻合,并根据图纸指定的位置固定艉管前支撑。
钢丝挠度按第4条计算。
11.2艉轴管前支撑的焊接要求是有经验的持证焊工;用CO2气体保护焊,焊接采用对称和跳焊的方法;并在对称接头处留~6 mm的气孔,等冷却后再填平气孔。
11.3注意在焊接过程中,钳工要不断地测量艉管及艉轴前轴承支撑中心线是否与轴系理论中心线重合,根据变形情况可调整焊接方向。
冷却后检查艉轴管前支撑中心线与轴系理论中心线是否有偏差并做好记录。
12、艉轴管的安装12.1艉柱和艉管前支撑安装好后,以理论轴线为基准,根据图纸指定位置,用设在艉柱和艉管前支撑上的调节螺栓将艉轴套管调节好,使艉轴套管的中心线与理论轴线相吻合。
钢丝挠度按第4条计算。
12. 2艉轴套管调节好后,开始装配浇注环氧树脂的挡板。
12. 3浇注环氧树脂的挡板装好后,由宁波北伦科技有限公司的专业技术人员开始浇注环氧树脂,以定位艉轴套管。
12. 4轴系中心线误差应符合表2的要求:表212.艉管环氧浇注定位以后,用磁力座钻配钻和攻艉管固定螺纹孔,同时安装固定双头螺栓。
13镗削吊舵臂下舵承外壳孔及舵销承外壳孔:13 . 1舵系理论中心线为基准划镗孔检验圆和加工圆线,(检验圆线比加工圆线约大20~30mm),并在圆线上打上样冲眼。
注意,加工圆线和检验圆线是个同心圆,而且,在镗孔前及在画镗孔加工圆线时,应检查轴毂孔能否按图纸要求镗出规定的尺寸,现时使轴毂的最小厚度(一般为舵杆直径的30%)不小于规定的数值。
13.2镗杆定中时,在舵承外壳孔及上舵承座前后左右焊接四只M14 X 50螺栓,以舵系理论中心线调节四个螺栓使前后左右距离相等(距离约比镗杆直径大0.10 mm)放入镗杆调节使镗杆与四棵螺栓距离相等。
13.3镗削舵臂下舵承外壳孔和舵销承外壳孔。
13.4注意镗孔时进刀量不要太大,分几次镗削13. 5镗孔技术要求按表3表314挂舵臂的安装14.1在舵叶上安装挂舵臂之前,舵已基本成型,舵叶的构件与构件间的焊缝焊已经全部焊接完工,板缝焊已基本焊完(与挂舵臂之间的焊缝除外)舵叶上下封板用样冲作出舵叶纵向和横向中心线,以便以后舵叶对中做准备。
14.2根据舵叶施工图纸将挂舵臂固定到要求的位置,注意定位挂舵臂时,一定要保证挂舵臂的中心线与舵叶的中心线一致性,且注意键槽的方向。
14. 3挂舵臂找中定位完工后,用L100 X 100X 10或工字钢临时固定牢,防止焊接变形。
然后,开始焊接舵叶构件与挂舵臂之间的焊缝,注意焊接采用跳焊的方法,严格控制变形。
在施焊过程中,钳工要不时地测量挂舵臂内孔中心尺寸,根据变形情况调整焊接方向和速度。
14.4舵叶施焊完工后(焊缝已冷却),将舵叶及挂舵臂所有临时加强支撑拆除,让舵叶充分释放应力。
14.5舵叶锥孔与舵杆的拂配,用吊车垂直吊舵杆,将舵杆与舵叶锥孔进行拂配,使舵杆锥度与舵叶舵杆套接触面积达到75%,并且用色油检查,25X 25 mm2的面积达到3~4点。
15舵叶舵销套定位安装:15.1将舵叶水平放置在平台上并调平。
15.2根据舵叶舵杆套部分的内孔中心线拉一根© 1mm钢丝,此钢丝穿过舵销套座内孔,此钢丝即为舵叶中心线。
要考虑钢丝的挠度,钢丝挠度按第4条计算。
15.3根据舵叶舵杆套部份的内孔中心线为基准定位舵销套(注意:定位舵销套之前,需要将舵销套座内孔及舵销套外园用丙酮清洗干净),通过八个M20调节螺栓调整,使舵销套内孔与舵杆套内孔同心,如图3所示。
tri15.4舵销套环氧树脂定位;15. 4. 1舵销套调整好后,焊接挡板,准备浇注环氧树脂。
15.4. 2浇注环氧树脂,该工作由宁波北伦科技有限公司的专业技术人员完成。
16.吊舵臂下舵承孔及舵销承孔镗削完工后,仔细测量内径,参照图纸装配要求加工下舵承及舵销承外径,外圆加工要求如表4表4艉轴承的安装仃.1艉轴承的安装:仃.1. 1压缩空气将艉轴管内的铁屑、杂物清除干净,艉轴承表面擦洗干净。
17.1. 2用带表的油压千顶将前后轴承装入艉轴艉管中,记录装配时压力表的读数,计算轴承装配压力。
注意:装轴承时要注意轴承油槽方向向上。
18.艉轴及前密封装置的安装18.1艉轴的安装:18. 1. 1安装艉轴前应按技术要求检查合格,艉轴与螺旋桨和联轴节锥孔拂括配合质量及与传动键括配质量应合格,艉轴表面擦洗干净。
(以上产品应有船检证书)18. 1. 2在艉轴的工作轴颈部分和艉轴承内圆表面上涂上润滑剂。
18. 1. 3用桁车和手拉葫芦或推车将艉轴从船外向船内送入艉轴管轴承内。
(所用的起吊工具不得损伤艉轴)18. 1. 4按图纸要求调整好艉轴前后尺寸后用长塞尺测量艉轴与艉轴承左右及上下部的安装间隙,要求如下:上部间隙满足技术要求;下部接触处间隙为零,用0.05 mm塞尺检查插不进;左右两边的间隙应均匀。
检查完工后做好支撑。
18. 1. 5将前密封装置的内外检查,看密封装置是否有毛刺、裂纹等缺陷,然后再安装密封装置。
18. 1. 6前密封装置安装完工之后,进行密封装置的密封压力试验并报船检。
佃.螺旋桨和可拆联轴节安装佃.1螺旋桨的锥孔和艉轴配合面擦拭干净,转动艉轴使键朝上,把螺旋桨安装到艉轴上再安装导流帽,在机舱内艉轴前端用槽钢档住,后端用带压力表的液压顶顶螺旋桨,在顶的过程中记录压力及进入量。
(要求设计院提供螺旋桨压入力的数据)19.2安装艉轴前端的可拆联轴节,用专用扳手使劲拧紧螺帽,使联轴节紧配在艉轴前端锥孔上。
佃.3轴承内加入润滑剂,转动艉轴用百分表检查艉轴端面及外圆跳动情况,并做好记录。
19.4可拆联轴节安装完工后,用大角钢或工字钢、工艺螺栓等将可拆联轴节连同艉轴牢靠的一起固定在船体上,为船舶下水做准备。
注意,固定联轴节时,应使螺旋桨成顺八字。