管道腐蚀机理的分析
国内外管道腐蚀与防护研究进展
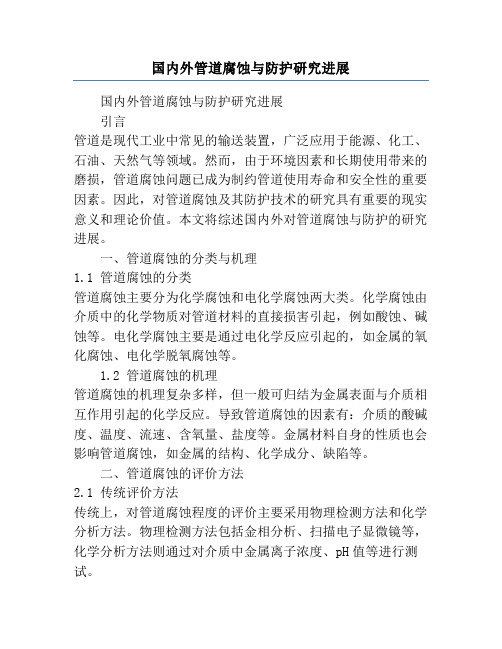
国内外管道腐蚀与防护研究进展国内外管道腐蚀与防护研究进展引言管道是现代工业中常见的输送装置,广泛应用于能源、化工、石油、天然气等领域。
然而,由于环境因素和长期使用带来的磨损,管道腐蚀问题已成为制约管道使用寿命和安全性的重要因素。
因此,对管道腐蚀及其防护技术的研究具有重要的现实意义和理论价值。
本文将综述国内外对管道腐蚀与防护的研究进展。
一、管道腐蚀的分类与机理1.1 管道腐蚀的分类管道腐蚀主要分为化学腐蚀和电化学腐蚀两大类。
化学腐蚀由介质中的化学物质对管道材料的直接损害引起,例如酸蚀、碱蚀等。
电化学腐蚀主要是通过电化学反应引起的,如金属的氧化腐蚀、电化学脱氧腐蚀等。
1.2 管道腐蚀的机理管道腐蚀的机理复杂多样,但一般可归结为金属表面与介质相互作用引起的化学反应。
导致管道腐蚀的因素有:介质的酸碱度、温度、流速、含氧量、盐度等。
金属材料自身的性质也会影响管道腐蚀,如金属的结构、化学成分、缺陷等。
二、管道腐蚀的评价方法2.1 传统评价方法传统上,对管道腐蚀程度的评价主要采用物理检测方法和化学分析方法。
物理检测方法包括金相分析、扫描电子显微镜等,化学分析方法则通过对介质中金属离子浓度、pH值等进行测试。
2.2 非破坏性评价方法近年来,非破坏性评价方法在管道腐蚀检测中得到了广泛应用。
例如,超声波检测技术可以通过测量超声波在材料中的传播时间和幅度来评估金属材料的腐蚀程度。
磁粉探伤技术则利用磁场特性检测金属材料中的缺陷或腐蚀情况。
三、管道腐蚀防护技术研究3.1 传统防护技术传统上,常用的管道腐蚀防护技术包括阴极保护、涂层防护和材料选择。
阴极保护通过引入外部电流或材料使金属处于负电位,从而减少电化学反应的发生。
涂层防护则是在金属表面涂覆一层能耐腐蚀介质的材料,以提供保护层。
材料选择则是选择对特定工况下介质具有良好抗腐蚀性能的金属材料。
3.2 新型防护技术随着科技的进步,新型管道腐蚀防护技术不断涌现。
例如,纳米涂层技术可以通过在传统涂层中添加纳米颗粒,增强涂层的抗腐蚀性能。
管道腐蚀总结汇报怎么写

管道腐蚀总结汇报怎么写标题:管道腐蚀总结汇报一、引言管道腐蚀是目前工业领域面临的严重问题之一。
为了解决管道腐蚀对工业生产和设备运行的不良影响,我们开展了一系列的研究和实践,总结了一些经验和教训。
本文旨在对我们的工作进行总结和汇报,以期为相关领域的研究和应用提供参考。
二、研究目的与方法我们的研究旨在探索管道腐蚀的机理和防控方法,并验证其有效性。
通过实验室模拟和实地观察,我们深入研究了管道材料的腐蚀机理、腐蚀诱因、腐蚀检测方法和防腐措施。
同时,我们还对不同腐蚀环境下不同材料的耐腐蚀性能进行了比较研究。
三、管道腐蚀机理分析我们发现,管道腐蚀是多种因素综合作用的结果。
主要腐蚀机理包括化学侵蚀、电化学腐蚀、微生物腐蚀等。
其中,电化学腐蚀是较为普遍和影响较大的一种腐蚀形式。
我们详细研究了电化学腐蚀的过程和影响因素,探究了电化学腐蚀速率的评价方法以及对策。
四、腐蚀诱因与检测方法我们分析了腐蚀诱因与管道腐蚀的关系,发现腐蚀环境的酸碱度、温度、湿度、氧气含量等因素对腐蚀程度有着重要影响。
同时,我们也介绍了常见的管道腐蚀检测方法,如传统的腐蚀率测定法、电化学方法、无损检测方法等,并对这些方法的优缺点进行了分析。
五、腐蚀防控措施为了有效防止管道腐蚀,我们探索了多种腐蚀防控措施。
包括材料选择、涂层防护、电化学保护、缓蚀剂应用等。
我们对这些措施进行了实验验证,结果表明这些方法在不同环境和使用条件下均能有一定的腐蚀防控效果。
六、案例分析与实践经验我们通过实地观察和研究案例,总结了一些实践经验。
例如,通过对一家化工厂的管道腐蚀问题进行实地调查,我们发现管道的材料选择与工艺条件的匹配程度对腐蚀的影响较大。
此外,我们还分析了一些典型故障案例,并总结了相应的教训和解决方法。
七、结论与展望在对管道腐蚀的研究和实践中,我们对腐蚀机理、诱因、检测方法和防控措施等方面取得了一定的成果。
但仍然存在一些问题和待解决的挑战,如新型材料的应用、腐蚀防护技术的研发等。
输油管道腐蚀机理与防护措施

输油管道腐蚀机理与防护措施【摘要】输油管道的腐蚀问题是原油长距离运输中的重要问题。
由于输油管道距离长、经过的地区地址环境复杂,管道运行中出现的腐蚀问题不易准确监测和定位,因此一直都是一个比较困难的问题。
本文分析了输油管道中的常见腐蚀类型,以及其发生的原因,简述了在工程中常用的输油管道腐蚀防护技术。
最后以某地并行输油管道的防腐蚀防护为例对其应用做了说明。
标签输油管道;腐蚀;防护措施1、输油管道的常见腐蚀类型输油管道长期处于原油浸泡之中,原油中的腐蚀介质是输油管道腐蚀的直接诱因。
目前输油管道的材质一般都是碳钢或合金钢,含有多种化学活性不一的金属元素(铁、锰等)和非金属元素(硫、磷等)。
这些不同化学活性的元素可在输油管道内因为电极电位之间的差异,加上管道内原油的流动,会在管道内形成完整的化学腐蚀电池。
只要时间允许,这种局部的腐蚀电池可沿着管道大量出现,时间一长会对管道形成严重的腐蚀后果。
除了这类最常见的管道腐蚀类型外,还存在其他多种腐蚀方式,如氧化反应、微生物腐蚀、二氧化碳腐蚀、硫化氢腐蚀等多种类型。
在原油中存在一定数量的微生物,这些微生物中对金属输油管道危害最大的是厌氧性腐蚀细菌硫酸盐还原菌(SRB),STB的存在会加速腐蚀电化学动力学过程,在腐蚀部位形成点腐蚀,增加管道氢脆破坏的危险性。
除了SRB之外,铁细菌也会对金属管道的腐蚀造成危害,在管道内部形成锈瘤和局部浓度差腐蚀电池,并会给SRB的繁殖创造条件。
氧气腐蚀一般发生在输油管道的外部,由于金属输油管道的化学成分主要是铁,加上存在的水分,会在管道表面形成二氧化三铁的松散水合物,发展到后期会在管道壁上形成坑蚀,当腐蚀面积较大时通常在腐蚀面上形成蜂窝状的腐蚀坑。
二氧化碳腐蚀也是常见的管道腐蚀类型,这是由于原油中的二氧化碳含量较高,在油管中的腐蚀机理为二氧化碳、铁、水共同反应形成碳酸铁,其中的碳酸根会结合钙离子而形成碳酸钙沉积。
这类腐蚀在油水井的输油管腐蚀中较为常见。
腐蚀的机理及其控制措施
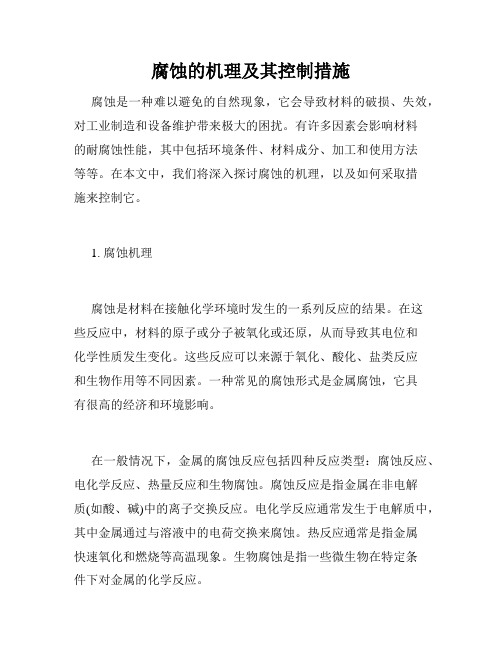
腐蚀的机理及其控制措施腐蚀是一种难以避免的自然现象,它会导致材料的破损、失效,对工业制造和设备维护带来极大的困扰。
有许多因素会影响材料的耐腐蚀性能,其中包括环境条件、材料成分、加工和使用方法等等。
在本文中,我们将深入探讨腐蚀的机理,以及如何采取措施来控制它。
1. 腐蚀机理腐蚀是材料在接触化学环境时发生的一系列反应的结果。
在这些反应中,材料的原子或分子被氧化或还原,从而导致其电位和化学性质发生变化。
这些反应可以来源于氧化、酸化、盐类反应和生物作用等不同因素。
一种常见的腐蚀形式是金属腐蚀,它具有很高的经济和环境影响。
在一般情况下,金属的腐蚀反应包括四种反应类型:腐蚀反应、电化学反应、热量反应和生物腐蚀。
腐蚀反应是指金属在非电解质(如酸、碱)中的离子交换反应。
电化学反应通常发生于电解质中,其中金属通过与溶液中的电荷交换来腐蚀。
热反应通常是指金属快速氧化和燃烧等高温现象。
生物腐蚀是指一些微生物在特定条件下对金属的化学反应。
除此之外,在腐蚀机理的研究中,需要探讨腐蚀的成因,包括干燥腐蚀、隐蔽腐蚀和应力腐蚀等等,因为它们都会成为影响腐蚀的因素。
干燥腐蚀是指材料在干燥的环境中产生氧化物而腐蚀,在一些研究中可以通过控制清洁度来避免。
隐蔽腐蚀是指在材料内部发生的腐蚀过程,难以发现和处理。
应力腐蚀则是指金属在受到外界应力和化学环境共同影响下的腐蚀过程。
2. 腐蚀控制措施腐蚀虽然不可避免,但可以通过多种措施来降低腐蚀的风险和减缓腐蚀速度。
以下是几种常见的腐蚀控制措施:2.1 材料选择选用合适的耐腐蚀材料是一种很有效的腐蚀控制措施。
例如,在重化工行业中,选用防腐钢材料可以有效地降低设备和管道的腐蚀风险,从而延长使用寿命。
而在食品加工业中,采用不锈钢、铸铁等材料也可以有效地降低食品中的有害物质含量,提高食品的质量和安全性。
2.2 防腐涂料防腐涂料是一种常见的腐蚀控制方式。
涂料中含有具有防腐性能的化学物质,能够形成一层保护膜,保护金属材料不被化学环境侵蚀。
管道腐蚀机理

管道腐蚀机理全文共四篇示例,供读者参考第一篇示例:管道腐蚀是管道工程中常见的问题,它会降低管道的使用寿命,甚至导致管道破裂造成事故。
管道腐蚀的机理复杂,主要包括电化学腐蚀、化学腐蚀和微生物腐蚀等多种方式。
了解管道腐蚀的机理对于有效预防和控制管道腐蚀至关重要。
电化学腐蚀是管道腐蚀的一种主要形式。
在含水介质中,金属管道表面会形成电化学电池。
管道金属处于不同电位的部位之间形成阳极和阴极。
阳极在电化学反应中被氧化产生金属离子,而阴极则在电化学反应中充当还原剂。
在电解质溶液中,阴极和阳极之间的电流流动促使阳极金属的溶解,产生腐蚀现象。
电化学腐蚀通常受到外界因素如温度、湿度、PH值等的影响,因此管道在设计和使用中需要考虑这些因素以避免腐蚀的发生。
化学腐蚀是另一种常见的管道腐蚀形式。
化学腐蚀是指金属与环境中的化学物质直接发生反应而导致金属腐蚀。
当氧气、水、有机物和酸碱等物质与金属表面接触时,会产生氧化、还原和形成酸碱等化学反应,加速金属表面的腐蚀。
氧气是导致管道腐蚀的主要因素之一,因此在设计和使用管道时需要注意通风和防潮,减少氧气和水接触金属表面的机会。
微生物腐蚀是一种特殊的管道腐蚀形式。
微生物腐蚀是由微生物在管道表面形成生物膜,并产生特定的代谢产物导致金属腐蚀。
微生物腐蚀通常发生在含有微生物的介质中,如水、土壤等。
微生物腐蚀对管道的腐蚀速度较慢,但会在管道内壁形成微小的腐蚀斑点,逐渐加剧管道的腐蚀。
在设计和使用管道时需要定期清洗和消毒,防止微生物生长和腐蚀。
除了以上几种腐蚀机理外,还有一些其他因素也会对管道的腐蚀产生影响,如温度、压力、流速等。
温度会影响金属的热化学性质,而压力和流速则会影响管道内介质的腐蚀速度。
在高温和高压下,金属会更容易受到腐蚀,因此在设计和使用管道时需要考虑这些因素并采取相应的保护措施。
为了有效预防和控制管道腐蚀,可以采取一些常见的防腐措施,如涂层保护、阳极保护、防腐看管等。
涂层保护是在管道表面涂覆防腐材料,形成一层保护层以阻止金属与环境接触。
燃气管道腐蚀的原因

燃气管道腐蚀的原因一、电化学腐蚀燃气钢管的管壁与作为电解质的土壤或水相接触,产生电化学反应,使阳极区的金属离子不断电离而受到腐蚀,即为电化学腐蚀。
电化学腐蚀既可腐蚀内壁,也可以腐蚀外壁。
通常埋地钢管的外壁腐蚀是以电化学腐蚀为主的。
(一)基本原理任何金属沉浸在电解液中都会向溶液释放正离子。
当某种金属沉浸在该种金属盐的标准溶液中时,即得到该金属的标准溶液电位,其值与假定等于零的标准氢电极的电位之间的电位差即为标准电极电位。
各种金属按其标准电极电位的顺序排列成电化学次序,如表10-4所示。
假设将电极电位不同的两种金属(锌和铜)浸入水和硫酸组成的电解质中,既成原电池。
如图10-2所示。
用外部电池将两极连通时,电子就会从锌电极流向铜电极,即由负电位流向正电位,电流方向则从阴极(铜)流向极(锌)。
阳极锌离子Zn++不断离开金属,与电解质中硫酸根离子SO--4结合;在阴极聚集的电子与氢离子H+结合,在阴极表面释出氢气。
这个过程的结果是阴极(铜)被极化,阳极(锌)被腐蚀。
表10-4 常用金属标准电极电位锂Li+-3.03V镍Ni++-0.23V钾K+-2.925V锡Sn++-0.14V钠Na+-2.713V铅Pb++-0.126V镁Mg++-2.371V氢H+0铝Al+++-1.66V铜Cu+++0.337V锌Zn++-0.762V汞Hg+++0.792V铬Cr++-0.74V银Ag++0.7994V铁Fe++-0.44V铂Pt+++1.2V镉Cd++-0.402V金Au++++1.45V埋地钢管由于金属本身结构的不均匀,表面粗糙度不同,以及作为电解质的土壤物理化学性质不均匀,含氧量不同,pH值不同等因素,因而产生电化学反应,使阳极区的金属离子不断电离而受到腐蚀。
图10-3说明组成电解质的土壤性质不同,会引起电化学腐蚀。
图10-2 原电池工作原理图10-3 土壤不均匀性引起的腐蚀由于砾石和砂子透气性好。
而粘土透气性差,埋在不同地段的钢管将产生电位差,管道在阳极区受到腐蚀。
海底管道气体运输的管道腐蚀研究与防护技术
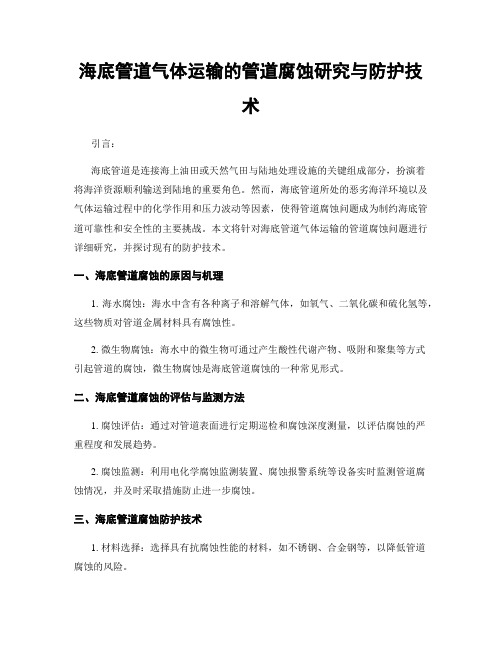
海底管道气体运输的管道腐蚀研究与防护技术引言:海底管道是连接海上油田或天然气田与陆地处理设施的关键组成部分,扮演着将海洋资源顺利输送到陆地的重要角色。
然而,海底管道所处的恶劣海洋环境以及气体运输过程中的化学作用和压力波动等因素,使得管道腐蚀问题成为制约海底管道可靠性和安全性的主要挑战。
本文将针对海底管道气体运输的管道腐蚀问题进行详细研究,并探讨现有的防护技术。
一、海底管道腐蚀的原因与机理1. 海水腐蚀:海水中含有各种离子和溶解气体,如氧气、二氧化碳和硫化氢等,这些物质对管道金属材料具有腐蚀性。
2. 微生物腐蚀:海水中的微生物可通过产生酸性代谢产物、吸附和聚集等方式引起管道的腐蚀,微生物腐蚀是海底管道腐蚀的一种常见形式。
二、海底管道腐蚀的评估与监测方法1. 腐蚀评估:通过对管道表面进行定期巡检和腐蚀深度测量,以评估腐蚀的严重程度和发展趋势。
2. 腐蚀监测:利用电化学腐蚀监测装置、腐蚀报警系统等设备实时监测管道腐蚀情况,并及时采取措施防止进一步腐蚀。
三、海底管道腐蚀防护技术1. 材料选择:选择具有抗腐蚀性能的材料,如不锈钢、合金钢等,以降低管道腐蚀的风险。
2. 防蚀涂层:在管道表面涂覆高性能的防蚀涂层,能够形成一层保护膜,有效隔离管道与外界环境接触,减缓腐蚀速度。
3. 防护层:在防蚀涂层上加装聚乙烯或聚丙烯等防护层,以进一步提高管道的防蚀性能和耐磨性能。
4. 阳极保护:通过在海底管道上安装阳极,使管道表面形成电场,从而防止腐蚀物质对管道金属的进一步腐蚀。
5. 隔离套管:在管道外壁加装隔离套管,形成一层防护壳,提供额外的保护层以防止管道腐蚀。
四、海底管道腐蚀防护技术的挑战与前景1. 深水环境:随着海底油气开发向深海扩展,深水环境带来了更加复杂的腐蚀问题,如高压、高温和高浓度的盐度等。
2. 可持续发展:在防护技术的选择和设计中,需考虑环境友好型,提高能源利用效率,减少对环境的影响。
3. 新材料:开发新的高性能材料,如纳米涂层、新型复合材料等,以提高防蚀性能和延长管道寿命。
油气管道腐蚀控制研究

油气管道腐蚀控制研究1.引言在现代工业化社会中,油气管道是不可或缺的能源运输渠道。
不过,由于其长期受到高浓度的腐蚀性介质侵蚀,其供能及安全性常常受到威胁。
因此,开展油气管道腐蚀控制研究,对于提升其安全性和可靠性具有重大意义。
2.腐蚀机理及对管道的影响管道腐蚀是指管道在使用过程中遭到腐蚀性介质的侵蚀而损坏。
其主要机理是化学腐蚀和电化学腐蚀。
化学腐蚀是指管道材料与介质直接发生化学反应,如钢管与硫酸的反应生成的铁硫酸盐。
电化学腐蚀则是在液体介质中形成电池,其阳极是钢管表面,阴极则是输入管表面或其他金属外膜,由此引发腐蚀反应。
管道腐蚀的影响主要表现在以下几个方面:(1)降低其结构强度和稳定性,导致泄漏和事故的发生。
(2)降低输送能力,增加能源运输成本。
(3)影响油气质量和品质,降低使用价值。
综上所述,管道腐蚀控制对于保障油气采掘和输送的安全以及提高质量和效益有着极为重要的意义。
3.管道腐蚀控制措施为了控制管道腐蚀,我们可以从以下几个方面入手:(1)选择合适的材料选用常见的镀锌钢、不锈钢、铜等材料,或者使用具有抗腐蚀性能的耐蚀合金。
(2)利用防腐涂层防腐涂层是一种把防腐剂涂刷在管道表面的防护措施。
一般来说,防腐涂层对于防止管道腐蚀性环境的侵蚀是比较有效的。
不过,由于防腐涂层随着使用时间的推移会逐渐失效,因此需要定期检查、保养和更换。
(3)采用电化学保护电化学保护是在管道表面施加电流,使其成为电化学电池的阴极而达到保护钢管的目的。
其优点是成本较低,但需要定期进行检查和维护,否则会影响有效性。
(4)减少腐蚀环境减少腐蚀环境是对减少管道腐蚀最为直接的措施。
如清除管道中的水分、减少盐分、降低硫和氧化铁等等。
同时,将管道置于合理的运输条件下,如控制介质流速和温度、防止过量压缩等措施也可以降低管道腐蚀。
4.管道腐蚀控制的技术研究在上述腐蚀控制措施中,防腐涂层是应用较为广泛的一种,目前市面上涂层种类众多,但涂层性能参差不齐。
- 1、下载文档前请自行甄别文档内容的完整性,平台不提供额外的编辑、内容补充、找答案等附加服务。
- 2、"仅部分预览"的文档,不可在线预览部分如存在完整性等问题,可反馈申请退款(可完整预览的文档不适用该条件!)。
- 3、如文档侵犯您的权益,请联系客服反馈,我们会尽快为您处理(人工客服工作时间:9:00-18:30)。
管道腐蚀机理的分析
【摘要】某油田自投产以来,输送油、气、水的管道大都处于复杂的土壤环境中,所输送的介质也都具有腐蚀性,一旦管道被腐蚀穿孔,就会造成油、气、水漏失,污染环境,其间接造成的经济损失更是难以估计,所以如何预防埋地管道的腐蚀损坏,长期以来就是地面工程工作中的重要环节。
【主题词】土壤;腐蚀
引言
为了降低土壤对管线外部的腐蚀,针对不同的地理环境,采取不同的埋藏方法,以及对管线除锈、刷漆、增加保护膜;为了缓解管道内壁的防腐程度,在掺水管道中加入原油流动改进剂。
通过以上做法,控制了腐蚀灾难的发生,消除腐蚀事故和环境污染,使管道腐蚀减少到最低。
1、基本概况
某采油矿共有各类管道1689条,其中金属管道有1496条,非金属管道193条,某矿驱油以水驱和聚驱为主,随着地下形势的变化,地面管网腐蚀穿孔严重,仅2010年全矿有1400多处管线穿孔,腐蚀管线占全矿总管线数量的17.6%(见表1)。
表1 某采油矿管线基础数据统计表
序号管线名称管线材质管线长度(Km)使用年限在用数量(条)
10年以下(条)10-20年(条)20-25年(条)25年以上(条)
1 集输管道20#C钢373.057 698 246 120 27 1091
2 集输管道钢骨架塑料复合管26.29
3 90 90
3 集输管道20#C钢内衬玻璃钢 5.256 10 10
4 集输管道玻璃钢0.69 2 2
5 注水管道20#C钢94.659 83 11
6 2
7 15 241
6 注水管道玻璃钢33.955 99 99
7 站间管道20#C钢232.16 61 47 108
8 注水支干线管道20#C钢57.554 7 20 14 7 48
合计823.624 978 391 208 49 1689
某采油矿某队位于某区东部,地理位置多为低洼地。
油水井管线90%以上埋藏于低洼地带,该地区土壤是由多相物质组成的复杂混合物,颗粒间充满空气、水和各种盐类,土壤具有电解质的特性,致使地下管道裸露的金属部分在土壤中构成了腐蚀电池,特定的潮湿环境加剧了管线的腐蚀速度。
因此在近几年的时间里,管线穿孔严重,更换频繁,全队89口油井,2010年全井更换管线18口,占某队总井数的20.4%,造成了巨大的经济损失。
为了节约生产成本,延长管线使用寿命,减少工人的劳动强度,我们对出现这种情况的原因进行了分析。
2、管线腐蚀穿孔的研究
管道的腐蚀分外壁腐蚀和内壁腐蚀,而影响埋地管道腐蚀速度的因素是多方面的,主要取决于土壤的性质。
实践证明,当土壤温度不同时,两部分地下钢管间的电位差可达0.3伏左右。
对于大口径的地下管道,与管顶相接触的土壤可能较干和透气性好,而与管底部相接触的就可能较潮湿和透气性差。
因而在管底部的钢即土壤电位低于管顶部的电位,管底部形成阳极区而发生腐蚀。
一般说,土壤电阻率在几十欧.米以上的,对钢铁的腐蚀性比较轻微。
在海水渗透的低洼地和盐碱地,电阻率很低,多在5欧.米以下,其腐蚀性相当强。
而某区某队队所处的位置正是低洼地,腐蚀性相当强。
油气管道的防腐方法各有特点,一条管道防腐措施的优劣,不是某项防腐技术的结果,而是上述方法的综合效益。
将涂层均匀致密地涂敷在金属管道表面上,使管道金属与大气、土壤、水等腐蚀介质隔离,这是管道防腐最基本的措施。
其防腐原理是高电阻的涂层隔离了管道金属与腐蚀介质的接触,切断了腐蚀电池的通路,使腐蚀电流趋于零,从而阻止管道腐蚀。
在对管道腐蚀穿孔方面,做了以下工作:一是在2010年年底,我队申请更换了一部分油井的管线。
采用泡沫黄夹克管,这种管道的防腐,强调了涂层具有良好的介电性能、物理性能、稳定的化学性能和较宽的温度适应性能,达到了防腐、绝缘、保温、增加强度等各种功能兼收并蓄。
更换管道半年多来,未发生一次穿孔事故,收到了较好的效果。
二是2010年与设计院专业人员配合在某区一队开展管道腐蚀的研究工作。
(1)分析试验站点介质成分,通过化验数据表明化学元素对管道腐蚀,金属腐蚀是在周围介质作用下,由于化学变化、电化学变化或物理溶解而产生的破坏或变质。
影响金属腐蚀的原因很多,如环境、土壤、细菌、杂散电流、管线材质等。
(2)我们把腐蚀严重的管段送到设计院分析腐蚀严重管段内表面形貌与成份。
观察表明,断口表面附着大量的腐蚀产物,已看不到管道基体,腐蚀产物分布杂乱无章,大小不一,形状不规则;其上有裂纹存在,表明存在应力,或者多项产物共存,而且存在可溶性、形核、生长等各方面的差异性。
3、现场试验应用情况
试验应用环保低表面能涂层在现场的应用:针对现场掺水、回油管线多发腐蚀穿孔、严重结垢的情况,经多方对比选用了性能较好的环保低表面能陶瓷减阻耐磨涂料及环氧粉末两种涂层进行现场试验。
在某计量间到某单井管线及聚某号计量间的站间管线上各安装了一组低表面能陶瓷减阻耐磨涂料-裸管-环氧粉末试验管,其中计量间到单井的管线为Φ48×3.5mm,站间管线为Φ89×4.0mm,目前已试验8个月。
4、认识
(1)在施工过程中,针对不同的地理环境,采用不同的埋藏起点。
对于干燥地带,加强管道的埋藏深度,在1.5至2.0米之间;对于潮湿地带,降低管道的埋藏深度,选择相对干燥的地带,增加地面覆土。
经过这样防腐后,埋地管道在土壤中的透气性增强,从而降低土壤对管道的腐蚀。
四是对在生产中发现穿孔的问题井,建议加强防腐。
应采取对焊接后的腐蚀部位除锈,然后刷一层底漆,缠二至四层胶带,外包一层保护带,组成总厚度在1-4毫米左右的防腐层,然后再下沟回填土。
这样就提高了受损部位焊接后的抗腐蚀能力;
(2)在对管道的内壁防腐方面,在掺水管道中加入原油流动改进剂的方法。
原油流动改进剂是一种水溶性表面活性剂,具有防蜡、降粘、破乳的功能。
流动改进剂在原油集输过程中,表面活性剂吸附在管壁上,形成亲水膜,降低了沿程摩阻,并将金属管壁的亲油性转变亲水性,防止在管壁上结蜡和挂油,抑制了石蜡的沉积;当流动改进剂与含水油混合后,就形成一种水包油型的原油假乳状液,表面活性剂吸附在油珠表面,使原油小颗粒均匀地分布在水中,对油珠的聚并有抑制作用,有效地起到降粘作用;流动改进剂又有破乳功能,当假乳状液静止后,油水很快破乳,实现油水分离,从而达到防蜡、降粘、降低摩阻的功能。
原油流动改进剂投用后,有效地缓解了因自产天然气不够烧而造成掺水温度低的不利局面,更对管道的内壁防腐起到了一定的作用。
参考文献
[1]《管道阴极保护》。