按分析方法计算换热器强度
工程热力学与传热学 第十八章 传热过程分析与换热器计算
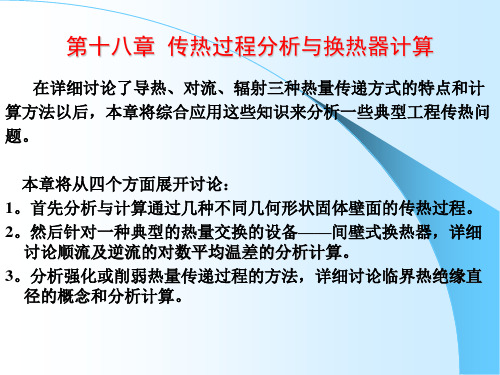
Q = kA(t1 − t 2 ) = kA∆t m
热流体放出的热量 冷流体吸收的热量
′ ′ Q1 = q m1c1 (t1 − t1′) ′ ′ Q2 = q m c 2 (t 2′ − t 2 )
′ ′ ′ ′ q m1c1 (t1 − t1′) = q m 2 c 2 (t 2′ − t 2 )
A2 β = A1
肋片越高,肋距越小,肋化系 数就越大。
' 肋片与流体的换热量 α 2 (t w 2 − t f 2 ) A2 ' α 2 (t w 2 − t f 2 ) A2η f
ηf 为肋片效率 加肋侧与流体的换热量
' ' Q = α 2 (t w 2 − t f 2 ) A2' +α 2 (t w 2 − t f 2 2) A2η f ' ' A2' A2 = α 2 (t w 2 − t f 2 ) A2 ( + η f ) A2 A2
图9-6 交叉流换热器示意图
4)板式换热器。板式换热器由一组几何结构相同的平行薄平板叠加所 组成,两相邻平板之间用特殊设计的密封垫片隔开,形成一个通道,冷、 热流体间隔地在每个通道中流动。为强化换热并增加板片的刚度,常在平 板上压制出各种波纹。板式换热器中冷、热流体的流动有多种布置方式, 图9-7所示为1-1型板式换热器的逆流布置,这里的1-1型表示冷、热流体 都只流过一个通道。板式换热器拆卸清洗方便,故适合于含有易污染物的 流体(如牛奶等有机流体)的换热。
图9-4 简单的壳管式换热器示意图
为了提高管程流体的流速,在图9-4所示的换热器中,一端的封头里 加了 一块隔板,构成了两管程的结构,称为l-2型换热器(此处l表示壳程 数,2表示管程数)。图9-5所示是一个1-2型换热器的剖面图。
固定管板式换热器管板的应力分析和强度评定

������ 16 ������
石 油 化 工 设 备 技 术
2018 年
如图2所示.
图 1 管 板 结 构 示 意
表 2 材 料 特 性
部件 管板 壳体 换热管
部件
管板 壳体 换热管
材质 Q345R Q345R 00Cr17Ni14Mo2 弹 性 模 量/
MPa 1.83×105 1.83×105 1.78×105
目前,对换热 器 管 板 结 构 进 行 应 力 分 析 的 研 究已有较多成果.李子林等 应 【6】 用 ANSYS 软 件 对固定管板式换热器在机械载荷和温度载荷共同 作用下的应力强 度 进 行 分 析,并 对 危 险 截 面 进 行 强 度 校 核 ,得 出 应 在 不 同 危 险 工 况 下 ,对 换 热 器 不 同部位进行分析和评定才能保证其安全可靠运行 的结论;杨宏 悦 分 【7】 析 了 不 同 操 作 工 况 下 管 板 模 型的应力场,得出 除 了 筒 体 上 的 一 次 薄 膜 应 力 起 控制作用外,管板 的 强 度 控 制 因 素 是 位 于 管 板 与 筒体连接圆角过 渡 处 的 一 次 应 力 加 二 次 应 力,且 最大值发生在热载荷和壳程压力同时作用的操作 工况下的结论;季维英 通 【8】 过建立包括壳体、管 束 在内的管板三维 实 体 有 限 元 模 型,将 法 兰 垫 片 用 等 效 的 均 布 比 压 来 代 替 ,分 析 了 管 板 在 包 括 开 工 、 正常工作和停车等过程中可能出现的七种瞬态和 稳态操作工 况 下 的 强 度 状 况.强 度 分 析 表 明,在 温度载荷及压力 载 荷 共 同 作 用 的 工 况 下,热 应 力 决定了整个管板系统的应力分布.根据分析结果
收 稿 日 期 :2018G04G18. 作者简介:陈一鸣,女,2017 年 毕 业 于 青 岛 科 技 大 学 过 程 装 备与控制工 程 专 业,现 为 该 校 动 力 工 程 专 业 在 读 硕 士 研 究 生 ,主 要 从 事 化 工 机 械 设 备 方 面 的 研 究 工 作 . Email:qdcym09@163.com. 基金项目:山 东 省 自 然 科 学 基 金 项 目 (NO.ZR2018LE015): 错位桨搅拌假塑性流体流场混沌特性及其表征.
固定管板式换热器管板的应力分析和强度评定

固定管板式换热器管板的应力分析和强度评定作者:杨翠娟来源:《名城绘》2019年第04期摘要:换热器设备在化工、石油、食品等多种工业生产中应用广泛。
在换热器制造过程中,管板与换热管之间的连接结构和连接质量一定程度上决定了换热器的质量优劣和使用寿命。
由于管板与换热管连接区域结构不连续,从而易产生各种连接质量问题,因此在危险工况下对管板与换热管连接部位进行应力分析和强度校核是十分必要的。
关键词:固定管板式换热器;管板;应力分析;强度评定目前,对换热器管板结构进行应力分析的研究已有较多成果。
应用ANSYS软件对固定管板式换热器在机械载荷和温度载荷共同作用下的应力强度进行分析,并对危险截面进行强度校核,得出应在不同危险工况下,对换热器不同部位进行分析和评定才能保证其安全可靠运行的结论;分析了不同操作工况下管板模型的应力场,得出除了筒体上的一次薄膜应力起控制作用外,管板的强度控制因素是位于管板与筒体连接圆角过渡处的一次应力加二次应力,且最大值发生在热载荷和壳程压力同时作用的操作工况下的结论;通过建立包括壳体、管束在内的管板三维实体有限元模型,将法兰垫片用等效的均布比压来代替,分析了管板在包括开工、正常工作和停车等过程中可能出现的七种瞬态和稳态操作工况下的强度状况。
1管板结构的静力分析在反映结构力学特性的前提下,模拟时进行以下简化:1)不考虑管板与换热管焊接热应力影响;2)不考虑管板与壳体的连接焊缝;3)不考虑管板兼做法兰螺栓对其的受力。
选择管板一侧面与所有换热管孔面施加450℃的温度载荷,并在该侧面施加2MPa的压力载荷;在管板另一侧面施加147℃的温度载荷和0.6MPa的压力载荷;沿半径方向,对换热器管板最外边缘施加全约束。
分析应力发现,该工况下管板结构的最大应力为46.9MPa,管板最大应力发生外侧管孔局部区域,其他区域应力值并不大。
采用管板材料为Q345R,450℃板厚为80mm的钢板许用应力为66MPa。
第7章 传热过程的分析和计算
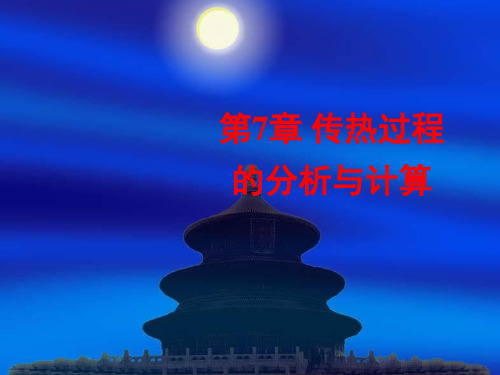
Rk
1
d1lh1
1
21l
ln
d2 d1
1
2xl
ln
dx d2
1
dxlh2
dRk ddx
1
2x d x
1
d
2 x
h2
0
dc
2x
h2
临界绝缘直径与保温材料有关、与所处环境有关
dc
2x
h2
(1)当dx<dc时,随保温层厚度的增加,总热阻 减小,传热量增大,此时对管道敷设保温层反而
7.4.2 换热器热计算的基本方程
约定: 下标 1 —— 热流体 下标 2 —— 冷流体 上标 ’ —— 进口参数 上标 ’’ —— 出口参数 以热流体进口作为计算起点
1 换热器中流体的温度分布 因变量—冷、热流体的温度 自变量—?
换热面积 —热流体入口,Ax=0 —热流体出口,Ax=At —在换热器内的不同位置,Ax不同,流体温
★如何提高传热系数?
1
1
K
1 h1
1 h2
1 h1
1 h2
数学上可以证明
K min h1, h2
提高较小的表面传热系数值,强化薄弱环节, 效果最好
h1=103,h2=10,没有强化前:K=9.90 W/(m2.K)
❖ 措施1: h1=2000,h2=10: K’=9.95 W/(m2.K)
7.2.1 通过平壁的传热过程 导热中—只关注平板的导热过程,计算了各类边
界条件下的温度分布、通过平板的导热量 传热过程中—壁面两侧流体间的热量传递过程
1 h1 A(t f 1 tW1)
2
换热器计算
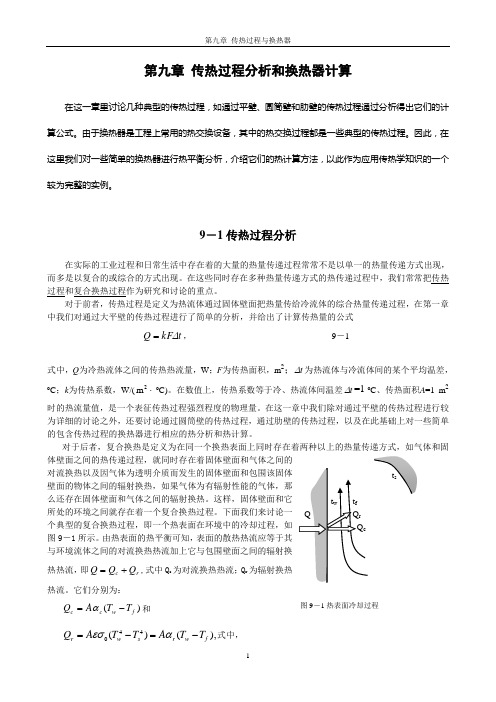
第九章 传热过程分析和换热器计算在这一章里讨论几种典型的传热过程,如通过平壁、圆筒壁和肋壁的传热过程通过分析得出它们的计算公式。
由于换热器是工程上常用的热交换设备,其中的热交换过程都是一些典型的传热过程。
因此,在这里我们对一些简单的换热器进行热平衡分析,介绍它们的热计算方法,以此作为应用传热学知识的一个较为完整的实例。
9-1传热过程分析在实际的工业过程和日常生活中存在着的大量的热量传递过程常常不是以单一的热量传递方式出现,而多是以复合的或综合的方式出现。
在这些同时存在多种热量传递方式的热传递过程中,我们常常把传热过程和复合换热过程作为研究和讨论的重点。
对于前者,传热过程是定义为热流体通过固体壁面把热量传给冷流体的综合热量传递过程,在第一章中我们对通过大平壁的传热过程进行了简单的分析,并给出了计算传热量的公式 t kF Q ∆=, 9-1式中,Q 为冷热流体之间的传热热流量,W ;F 为传热面积,m 2;t ∆为热流体与冷流体间的某个平均温差,oC ;k 为传热系数,W/(⋅2m o C)。
在数值上,传热系数等于冷、热流体间温差t ∆=1 o C 、传热面积A =1 m2时的热流量值,是一个表征传热过程强烈程度的物理量。
在这一章中我们除对通过平壁的传热过程进行较为详细的讨论之外,还要讨论通过圆筒壁的传热过程,通过肋壁的传热过程,以及在此基础上对一些简单的包含传热过程的换热器进行相应的热分析和热计算。
对于后者,复合换热是定义为在同一个换热表面上同时存在着两种以上的热量传递方式,如气体和固体壁面之间的热传递过程,就同时存在着固体壁面和气体之间的对流换热以及因气体为透明介质而发生的固体壁面和包围该固体壁面的物体之间的辐射换热,如果气体为有辐射性能的气体,那么还存在固体壁面和气体之间的辐射换热。
这样,固体壁面和它所处的环境之间就存在着一个复合换热过程。
下面我们来讨论一个典型的复合换热过程,即一个热表面在环境中的冷却过程,如图9-1所示。
换热器的热力学性能分析及优化

换热器的热力学性能分析及优化热力学性能是一个换热器最基本的特征之一。
换热器是在化工、锅炉、发电等工业领域中广泛应用的设备,其热力学性能的良好或否决定着生产和制造的成本和效益。
本文将从流体动力学、传热学和流体力学等角度,对换热器的热力学性能进行分析和探讨,并提出一些优化方案,以提高其效率和性能。
一、换热器的流体动力学分析滑板换热器和管壳式换热器是工业应用中较为常见的换热器类型。
换热器在使用过程中,流体的流动状态会对其热力学性能产生很大的影响。
因此,首先需要对其流体动力学进行分析。
1.1 流体的流动方式换热器中流体的流动方式可根据其物理特性和流路结构分为多种类型,如层流、紊流、混合流等。
其中,在翅片换热器中,流动一般是层流型的,层流状态下流体的流动需要满足雷诺数小于2100的条件,而在管壳式换热器中,流动一般是混合流型的,流体的流动通常在管侧是紊流,在壳侧是层流或混合流。
1.2 流体的速度和流量流体在换热器中的速度和流量也会对其热力学性能产生影响。
在流速过高的情况下,容易产生压力损失和泄漏现象,从而影响换热器的效率和使用寿命,而低流速则会导致传热不充分,影响换热器的热力学性能。
因此,需要在流体流量和速度之间寻求平衡,以达到最佳的换热效果和热力学性能。
二、换热器的传热学分析换热器的传热性能是换热器的另一个重要特征。
换热器的传热效率直接影响其热力学性能和效益。
因此,在换热器的设计和制造中,传热学的分析与优化非常关键。
2.1 热传导的特性热传导是换热器传热的基本方式,也是最常见的传热方式之一。
对于不同的材料,其热传导的特性不同,如金属的热传导率相对比较高,而非金属的热传导率相对较低。
因此,在换热器的制造中,需要根据不同的材料特性和使用要求进行选择,以达到最佳的传热效果和热力学性能。
2.2 湍流传热的影响湍流传热是一种非线性的、复杂的传热方式,其传热效率相对于层流传热更高。
然而,湍流传热所需的能量消耗也更大,从而会产生较大的热损失。
传热学 第9章-传热过程分析和换热器计算
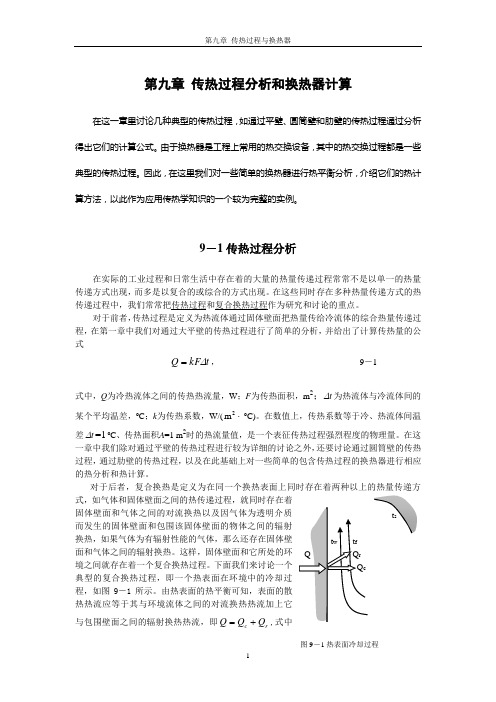
第九章 传热过程分析和换热器计算在这一章里讨论几种典型的传热过程,如通过平壁、圆筒壁和肋壁的传热过程通过分析得出它们的计算公式。
由于换热器是工程上常用的热交换设备,其中的热交换过程都是一些典型的传热过程。
因此,在这里我们对一些简单的换热器进行热平衡分析,介绍它们的热计算方法,以此作为应用传热学知识的一个较为完整的实例。
9-1传热过程分析在实际的工业过程和日常生活中存在着的大量的热量传递过程常常不是以单一的热量传递方式出现,而多是以复合的或综合的方式出现。
在这些同时存在多种热量传递方式的热传递过程中,我们常常把传热过程和复合换热过程作为研究和讨论的重点。
对于前者,传热过程是定义为热流体通过固体壁面把热量传给冷流体的综合热量传递过程,在第一章中我们对通过大平壁的传热过程进行了简单的分析,并给出了计算传热量的公式 t kF Q ∆=, 9-1式中,Q 为冷热流体之间的传热热流量,W ;F 为传热面积,m 2;t ∆为热流体与冷流体间的某个平均温差,o C ;k 为传热系数,W/(⋅2m o C)。
在数值上,传热系数等于冷、热流体间温差t ∆=1 o C 、传热面积A =1 m 2时的热流量值,是一个表征传热过程强烈程度的物理量。
在这一章中我们除对通过平壁的传热过程进行较为详细的讨论之外,还要讨论通过圆筒壁的传热过程,通过肋壁的传热过程,以及在此基础上对一些简单的包含传热过程的换热器进行相应的热分析和热计算。
对于后者,复合换热是定义为在同一个换热表面上同时存在着两种以上的热量传递方式,如气体和固体壁面之间的热传递过程,就同时存在着固体壁面和气体之间的对流换热以及因气体为透明介质而发生的固体壁面和包围该固体壁面的物体之间的辐射换热,如果气体为有辐射性能的气体,那么还存在固体壁面和气体之间的辐射换热。
这样,固体壁面和它所处的环境之间就存在着一个复合换热过程。
下面我们来讨论一个典型的复合换热过程,即一个热表面在环境中的冷却过程,如图9-1所示。
换热器设计及性能分析总结二版
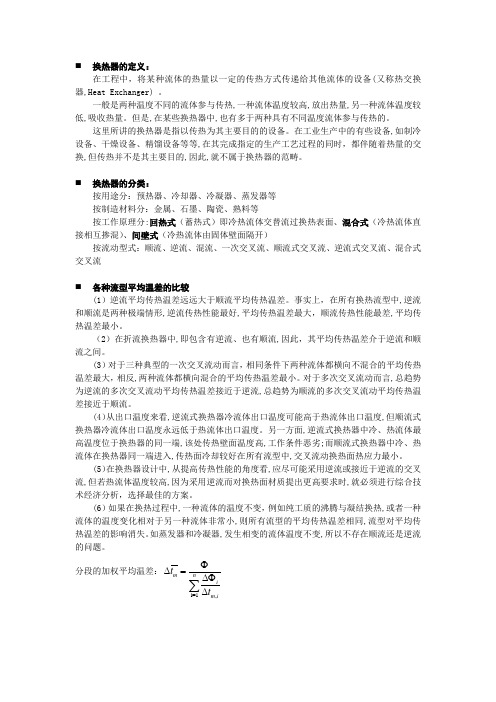
⏹ 换热器的定义:在工程中,将某种流体的热量以一定的传热方式传递给其他流体的设备(又称热交换器,Heat Exchanger) 。
一般是两种温度不同的流体参与传热,一种流体温度较高,放出热量,另一种流体温度较低,吸收热量。
但是,在某些换热器中,也有多于两种具有不同温度流体参与传热的。
这里所讲的换热器是指以传热为其主要目的的设备。
在工业生产中的有些设备,如制冷设备、干燥设备、精馏设备等等,在其完成指定的生产工艺过程的同时,都伴随着热量的交换,但传热并不是其主要目的,因此,就不属于换热器的范畴。
⏹ 换热器的分类:按用途分:预热器、冷却器、冷凝器、蒸发器等按制造材料分:金属、石墨、陶瓷、熟料等按工作原理分:回热式(蓄热式)即冷热流体交替流过换热表面、混合式(冷热流体直接相互掺混)、间壁式(冷热流体由固体壁面隔开)按流动型式:顺流、逆流、混流、一次交叉流、顺流式交叉流、逆流式交叉流、混合式交叉流⏹ 各种流型平均温差的比较(1)逆流平均传热温差远远大于顺流平均传热温差。
事实上,在所有换热流型中,逆流和顺流是两种极端情形,逆流传热性能最好,平均传热温差最大,顺流传热性能最差,平均传热温差最小。
(2)在折流换热器中,即包含有逆流、也有顺流,因此,其平均传热温差介于逆流和顺流之间。
(3)对于三种典型的一次交叉流动而言,相同条件下两种流体都横向不混合的平均传热温差最大,相反,两种流体都横向混合的平均传热温差最小。
对于多次交叉流动而言,总趋势为逆流的多次交叉流动平均传热温差接近于逆流,总趋势为顺流的多次交叉流动平均传热温差接近于顺流。
(4)从出口温度来看,逆流式换热器冷流体出口温度可能高于热流体出口温度,但顺流式换热器冷流体出口温度永远低于热流体出口温度。
另一方面,逆流式换热器中冷、热流体最高温度位于换热器的同一端,该处传热壁面温度高,工作条件恶劣;而顺流式换热器中冷、热流体在换热器同一端进入,传热面冷却较好在所有流型中,交叉流动换热面热应力最小。
- 1、下载文档前请自行甄别文档内容的完整性,平台不提供额外的编辑、内容补充、找答案等附加服务。
- 2、"仅部分预览"的文档,不可在线预览部分如存在完整性等问题,可反馈申请退款(可完整预览的文档不适用该条件!)。
- 3、如文档侵犯您的权益,请联系客服反馈,我们会尽快为您处理(人工客服工作时间:9:00-18:30)。
软件批准号:CSBTS/TC40/SC5-D01-1999
DATA SHEET OF PROCESS EQUIPMENT DESIGN
工程名:
PROJECT
设备位号:
ITEM
设备名称:
EQUIPMENT
图 号:
DWG NO。
设计单位:压力容器专用计算软件
DESIGNER
设 计 Designed by 日期Date
校 核 Checked by 日期Date
审 核 Verified by 日期Date
批 准 Approved by 日期Date
固定管板换热器设计计算 计算单位压力容器专用计算软件
设 计 计 算 条 件
壳 程 管 程
设计压力 p
1 MPa设计压力 p t 1.5 MPa
s
设计温度 t
80 °C设计温度 t t150 °C
s
壳程圆筒外径Do 377 mm 管箱圆筒外径Do 377 mm 材料名称 20(GB9948) 材料名称 20(GB8163)
简 图
计 算 内 容
壳程圆筒校核计算
前端管箱圆筒校核计算
前端管箱封头(平盖)校核计算
后端管箱圆筒校核计算
后端管箱封头(平盖)校核计算
管箱法兰校核计算
开孔补强设计计算
管板校核计算
腐蚀后带法兰固定式管板计算 设计单位 压力容器专用计算软件
设 计 计 算 条 件 简 图 设计压力 p
s 1 MPa
设计温度 T s80 C°
平均金属温度 t s 0 °C
装配温度 t0 15 °C
壳 材料名称 20(GB9948)
设计温度下许用应力[σ]t 148.2 MPa
程 平均金属温度下弹性模量 E s 2.023e+05 MPa
平均金属温度下热膨胀系数αs 1.076e-05 mm/mm°C
圆 壳程圆筒内径 D i359 mm 壳程圆筒名义厚度(高颈法兰取法兰颈部大小端平均值)δs9 mm 壳程圆筒有效厚度
se
δ8 mm
筒 壳体法兰设计温度下弹性模量 E
f
' 1.94e+05 MPa 壳程圆筒内直径横截面积 A=0.25πD i2 1.012e+05 mm2 壳程圆筒金属横截面积 A s=πδs (D i+δs) 9224 mm2管 设计压力p t 1.5 MPa 箱 材料名称: 20(GB8163)设计温度T t 150°C 圆 设计温度下弹性模量 E h 2.01e+05 MPa 筒 管箱圆筒名义厚度(高颈法兰取法兰颈部大小端平均值)δh 9 mm 管箱圆筒有效厚度δhe 9mm 管箱法兰设计温度下弹性模量 E f" 1.94e+05 MPa 材料名称: T2管子平均温度 t t 0 °C 换 设计温度下管子材料许用应力[]σt t23 MPa 设计温度下管子材料屈服应力σs t35 MPa
设计温度下管子材料弹性模量 t
t
E 1.124e+05 MPa 热 平均金属温度下管子材料弹性模量 E t 1.18e+05 MPa
平均金属温度下管子材料热膨胀系数αt 1.623e-05 mm/mm °C
管子外径 d12 mm 管 管子壁厚δt 1 mm 管子根数 n241
注:。