刀具路径.ppt
二维刀具路径参考PPT
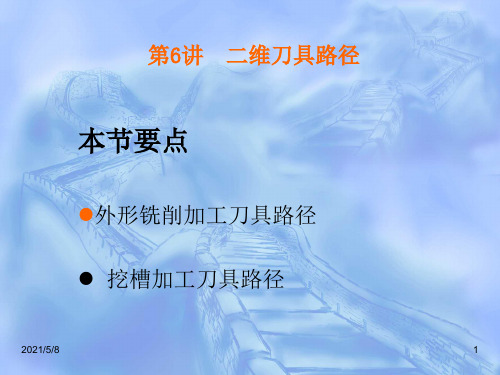
2021/5/8
4
在主菜单中顺序选择刀具路径(Tool paths)
外形铣削(Contour)
(选择图素) 执行(Done)
点选外形铣削参数项。弹出如下图所示的外形铣削对话
框。
2021/5/8
5
▪ 每种加工模组都需要设置一组刀具参数, 可以在“刀具参数(Tool parameters)”对话框中进行 设置。如果已设置刀具,将在对话框中显示出 刀具列表,可以直接在刀具列表中选择已设置 的刀具。如列表中没有设置刀具,可在刀具列 表中单击鼠标右键,通过快捷菜单来添加新刀 具。
进行加工的几何模型和参数各不相同。本章将分别介绍各模
组的功能及使用方法。
2021/5/8
2
第二节 外形铣削模组
外形铣削模组可以由工件的外形轮廓产生加工路 径,一般用于二维工件轮廓的加工。其切削深度是固 定不变的。
外形加工是一种常用的,实用又简单的加工方式 ,一般用平底锣刀,圆鼻刀,斜度刀,不用球刀,开 粗时平面进刀量可以用到刀具直径的三分之二至四分 之三左右,深度进刀见下表:
4、设定进刀/退刀长度为0.5in,进刀/退刀
弧的半径为1in,角度为90°。
5、刀具补正为左补正。
2021/5/8
9
外形切削实例
步骤三:设置毛坯尺寸、工件材料。选择主功能表
刀具路径
工作设定,弹出“工作设定”对话框,
如下图所示。该对话框主要是设置毛坯尺寸、工件材
料,因为要有工件材料才能计算主轴的速度和进给参
2021/5/8
7
外形切削实例
3、铣削刀具路径都是由定义外形时选择的 第一个几何图素的端点开始。
4、使用< 135°,作为刀具转角设定。
第一节刀具路径1(Toolpath)
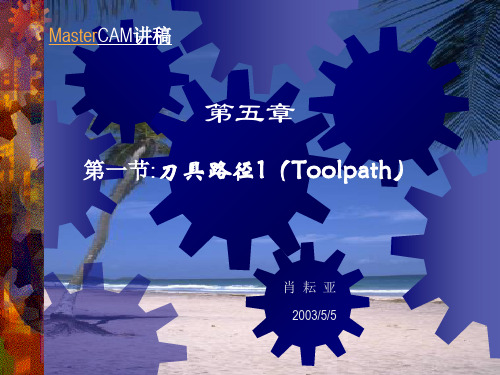
第五章
第一节:刀具路径1(Toolpath)
肖 耘 亚 2003/5/5
CAM的概念
以数控机床为基础(自动加工) 由计算机实现编程和机床控制 不可替代的几个因素:
机床调整 工件装卸 工艺知识 加工经验
MasterCAM在CAM环节的内容
取档(CAD模型) Toolpath(生成刀具路径/NCI)
取档(CAD模型) 从主菜单Toolpath进入刀具路径功
能
取Surface:曲面加工
先作Drive/check干涉检查,取两个面 再选Rough粗加工,进一步操作如下:
以鼠标为例的刀路编制与操作
选Pocket:挖槽式粗加工
系统提示:Select
drive…Surface
在Tool
Feed
parameters页填空:
rate=800(进给速度),
Plunge=500(Z向速度), retract=700(Z向退刀速度), Spindle=1200(主轴转速), coolant(冷却)选Floot
以鼠标为例的刀路编制与操作
在Surface parameters页填空:
选All~Surf标右键打开随动菜单,
选Get tool from library…,进入刀具 管理器,选8mm的平铣刀,确定后 返回参数对话框
以鼠标为例的刀路编制与操作
在Tool
Feed
parameters页填空:
rate=1000(进给速度),
Drill:钻孔
Pocket:投影加工 Face:面铣
串连图素再执行
Toolpath菜单介绍
Surface:曲面加工
画刀具工作图PPT文档资料

•.
•7
4 画切削面
垂直主切削刃,S向。刃倾角λs
延长主切削刃垂直线,画其垂直线副后角αo’(注意正负)
S向
•.
•8
第1章重点
刀具工作图、参数标注: p6图1-7
•.
•9
刀具切削部分的结构要素
刀具切削部分结构: 一尖:刀尖 二刃:主刀刃和副刀 刃 三刀面:前刀面、主 后刀面和副后刀面。
•.
•1
主刃
副刃Βιβλιοθήκη •.•2应该在这 前刀面
后刀面
•.
•3
画刀具工作图
车刀前角几何参数为:主偏角Kr=45 , 副 偏 角 Kr ˊ =35 , 前 角 γ0=10 , 后 角 α0=8 ,副后角α0ˊ =6 ,刃倾角λs=5 ,刀尖半径ε=1mm。刀杆横截面积为 25 X 25 mm
•.
•4
1 画基面 主运动方向,进给方向 Kr, Kr’
1)先画进给方向。 2 Kr 主切削刃 (注意反方向)
3 Kr’ 副切削刃
•.
•5
2 画主剖面
垂直主切削刃,剖。 前角γo : 主后角αo
延长主切削刃,画垂直线。 垂线前角γo
•.
•6
3 画副刃主剖面 垂直副刃,剖 副后角αo’
延长副切削刃,画垂直线。 延长线副后角αo’
第五章 刀具路径切入切出和连接
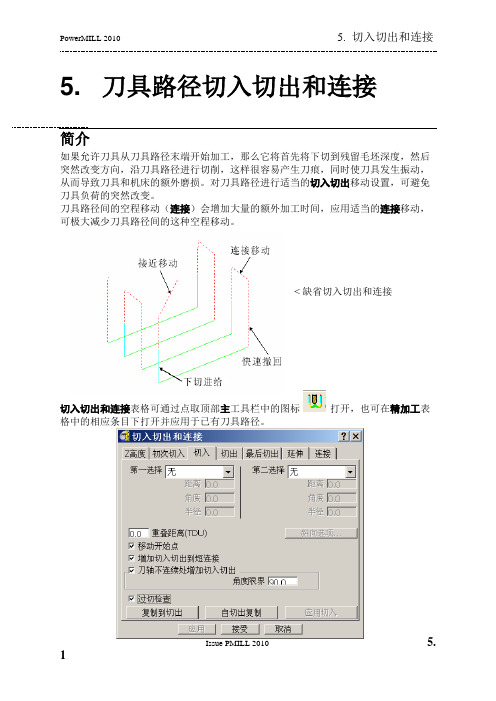
Issue PMILL 2010 5.15. 刀具路径切入切出和连接简介如果允许刀具从刀具路径末端开始加工,那么它将首先将下切到残留毛坯深度,然后突然改变方向,沿刀具路径进行切削,这样很容易产生刀痕,同时使刀具发生振动,从而导致刀具和机床的额外磨损。
对刀具路径进行适当的切入切出移动设置,可避免刀具负荷的突然改变。
刀具路径间的空程移动(连接)会增加大量的额外加工时间,应用适当的连接移动,可极大减少刀具路径间的这种空程移动。
< 缺省切入切出和连接切入切出和连接表格可通过点取顶部主工具栏中的图标 打开,也可在精加工表格中的相应条目下打开并应用于已有刀具路径。
掠过距离和下切距离用来控制刀具在零件之上快速移动的高度。
通过设置适当的安全Z高度和开始Z高度,可最大限度减小加工过程中刀具低速移动和不必要的空程移动。
掠过距离–刀具在模型之上从一条刀具路径末端提刀到下一刀具路径始端进行快速移动的相对高度。
刀具在掠过距离所设定的高度之上做快进移动,快速跨过模型,到达下一下切位置。
下切距离–工件表面之上的一相对距离,刀具下切到此距离值后将由快进速率下切改变为以下切速率下切。
切入/切出运动切入控制刀具在切削路径开始前的运动;切出控制切削路径末端离开刀具路径时的运动。
可使用的切入选项有:无,垂直圆弧,水平圆弧,左水平圆弧,右水平圆弧,延伸移动,加框和斜向。
切出可使用的选项和切入可使用的选项除没有斜向选项外,其它部分完全相同。
左图所示:切入/切出–垂直圆弧和相对 - 掠过 - 连接运动。
刀具路径颜色代码:紫色–快进掠过进给率 G1浅蓝色–下切进给率 G1绿色/橙色–切削进给率 G1红色虚线–全速快进 G0切入切出和连接是刀具路径的有效延伸,因此必须对其进行过切保护处理。
为此一定要设置刀具路径切入切出和连接表格中的过切检查选项(缺省设置为已勾取),以免发生过切。
点取此选项后,将不产生任何可能导致过切的切入切出。
下面以图解方式解释不同的切入切出和连接设置,在此,除非特别指出,过切检查选项始终呈勾取状态。
第6章 二维刀具路径
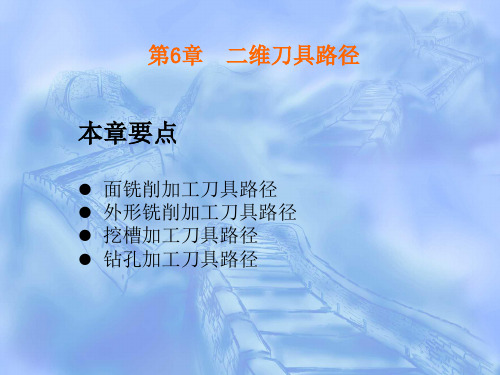
第六章
▪ 钻削参数选项卡
二维刀具路径
首次钻孔深度 以后各次钻孔深度
钻孔循环
刀具暂留孔底时间 让刀距离(只用于精镗孔)
第6章 二维刀具路径
▪ Cycle(钻孔循环)
深孔钻:一般钻孔和镗孔,孔深小于三倍刀具 直径,孔底要求平整,可在孔底暂停;
深孔啄钻:用于钻深孔,孔深大于三倍刀具直径; 断削式:用于钻深孔,孔深大于三倍刀具直径; 攻牙:加工内裂纹; 镗孔#1:用进给速度进刀和退刀进行镗孔; 镗孔#2:用进给进刀、主轴停止、快速退刀进行
▪ 输入点子菜单
手动选点:手动选择钻孔点,选取该命令后,打开抓点方式菜单; 自动选点:自动选择加工点,依次选择三个点为一组,系统自动选
择一系列已存在的点作为钻孔中心点; 图素选点:选择所有图素的端点定位钻孔点,包括线的端点、圆弧
的端点、聚合线端点和封闭圆的中心点; 窗口选点:用光标构建一个窗口,系统用窗口范围内的一系列点产
镗孔; 精镗孔(刀具偏移):在孔深处停转,将刀旋转
角度后退刀。
第6章 二维刀具路径
▪ 6.5 二维加工综合实训
生钻削刀具路径; 前一刀具路径的点:选择上一次钻削操作的点; 限定圆弧选点:用一个指定的半径(在一公差值内)选择开放的或
封闭的圆弧的中心点钻孔; 样板选点:根据样板定义钻削点,指定一系列矩形排列或环形排列
的点; 选项:选取该命令弹出图6-55所示点的排序对话框,用以设置点的
排序方式—17种2D排序、12种圆周排序、16种交叉排序方式; 子程式:选取该命令可重复钻孔的位置,构建一个子程式,每个钻
第6章 二维刀具路径
本章要点
面铣削加工刀具路径 外形铣削加工刀具路径 挖槽加工刀具路径 钻孔加工刀具路径
铣削刀具走刀路线的最基本原则 优质课件

从零件方面的影响或从刀具路径的观点来看,铣削主要的工序类型包括:8.切断9.高进给铣削 10. 插铣 11. 坡走铣12. 螺旋插补铣 13.圆弧插补铣 14. 摆线铣削1.面铣2.方肩铣3.仿形铣削4.型腔铣削5.槽铣6.车铣7.螺纹铣削7.4 铣刀的主偏角铣刀的主偏角是指刀片刃口和工件的加工表面之间的夹角。
主偏角会影响切屑的厚度、切削力的大小和方向,从而影响刀具寿命。
在相同的进给速度下,减小主偏角,则切屑厚度变薄,切屑与切削刃的接触长度更长,较小的主偏角也可使刀具更为平缓地进入切口,这有助于减小径向压力和保护切削刃口。
但是轴向力太大,会增加对工件和锥孔的压力。
现在铣刀常用的主偏角是:45º、90º、10º以及圆刀片90度主偏角可以铣削具有台肩要求的工件,可以获得直角边。
但是会产生绝大部分的径向力,同时也意味着被切的表面承受的轴向压力较小。
这对于低强度结构的工件、薄壁工件的加工很有积极意义。
45度主偏角的刀具,加工时同存在大小值接近的轴向和径向力,这会产生更为平稳的压力,并且对机床功率的要求相对较小。
为平面铣削的首选刀具。
10度主偏角铣刀,主要用于插铣,并且也是小切深,大走刀量面铣刀。
常用于模具宽大型腔加工时,大量快速去除余量。
因为径向切削力很小,因而可以降低因刀杆悬伸过长而产生的振动趋势。
69度、75度主偏角铣刀,主要用于冷硬铸铁和铸钢的表面粗加工。
圆刀片刀具意味着连续可变的主偏角,范围从0~90度,其具体值取决于切深的情况。
此刀片半径具有非常坚固的切削刃,并且由于产生薄屑,切削力会顺着长长的切削刃均匀分布。
因而适合于高进给速率的加工。
常用于模具型腔的快速去除余量。
薄切屑效应,适合加工耐热合金和钛合金。
因为其具有平稳切削、对机床功率、稳定性的要求低。
如今,它已不是非标准刀具,而是作为高效且具有高金属去除率的粗加工刀具。
7.3 面铣刀的直径和位置R aF Fnnv fa e a ea eDHSM铣刀直径比切削宽度大很多,并且刀具中心完全在工件宽度之外,此情形多发生在三面刃铣、卡刀铣和立铣。
《铣工的顺铣与逆铣》课件
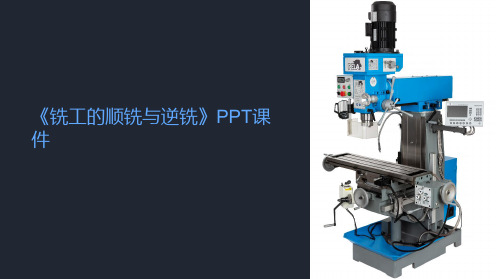
广泛应用于扁平面铣削、开槽、平面等加工。
2 逆铣
常用于钢材的高效粗铣、粗加工表面铣削等工艺。
刀具选择和参数调整
1
调整切削参数
2
合理设置进给速度、进给量、切削深度
等参数。
3
选择合适的刀具
考虑刀具类型、刀杆材料、刀具齿数等 因素。
定期检查刀具状态
确保刀具的磨损程度和刀面质量。
小结和要点
• 顺铣和逆铣是铣工常用的两种铣削方式。 • 它们在刀具路径、优缺点和应用领域等方面有一些区别。 • 选择合适的刀具和调整切削参数是确保加工质量的关键。
逆铣的刀具路径
逆铣中,铣刀从工件的一端开始,顺时针绕着工件移动,完成铣削加工。刀具路径在工件表面形成交错的切削 轨迹,提高表面质量。
顺铣和逆铣的优缺点
顺铣
优点:切削稳定,加工效率高。 缺点:切削力大,对刀具耐用性要求高。
逆铣
优点:表面质量好,切削《铣工的顺铣与逆铣》PPT课 件
铣工顺铣与逆铣的定义
顺铣是指铣刀逆时针旋转、工件相对铣刀静止或移动的铣削方式。逆铣则是 指铣刀顺时针旋转、工件相对铣刀静止或移动的铣削方式。
顺铣的刀具路径
顺铣中,铣刀从工件的一端开始,逆时针绕着工件移动,完成铣削加工。刀 具路径可形成连续的切削轨迹,提高加工效率。
第六章 二维刀具路径
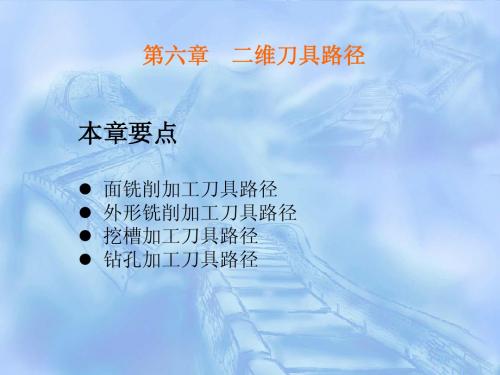
第六章 二维刀具路径
钻削参数选项卡
首次钻孔深度 以后各次钻孔深度
钻孔循环
刀具暂留孔底时间
让刀距离(只用于精镗孔)
第六章 二维刀具路径
Cycle(钻孔循环) Cycle(钻孔循环)
深孔钻:一般钻孔和镗孔,孔深小于三倍刀具 深孔钻 直径,孔底要求平整,可在孔底暂停; 深孔啄钻:用于钻深孔,孔深大于三倍刀具直径; 深孔啄钻 断削式:用于钻深孔,孔深大于三倍刀具直径; 断削式 攻牙:加工内裂纹; 攻牙 镗孔#1 镗孔#1:用进给速度进刀和退刀进行镗孔; #1 镗孔#2 #2:用进给进刀、主轴停止、快速退刀进行 镗孔#2 镗孔; 精镗孔(刀具偏移) 精镗孔(刀具偏移):在孔深处停转,将刀旋转 角度后退刀。
第六章 二维刀具路径
本章要点
面铣削加工刀具路径 外形铣削加工刀具路径 挖槽加工刀具路径 钻孔加工刀具路径
第六章 二维刀具路径
在各类机械零件中,二维板类零件占有很大的比重,利用 Mastercam9.1 软件的Mill模块的Face Face(面铣削加工)、Contour Contour(外形 铣削加工)、Pocket Pocket(挖槽加工)、Drill Drill(钻孔加工)等功能,可以 对绘制的二维轮廓进行直接加工,并编制出相应的二维加工程序。
第六章 二维刀具路径
输入点子菜单
手动选点:手动选择钻孔点,选取该命令后,打开抓点方式菜单; 手动选点 自动选点:自动选择加工点,依次选择三个点为一组,系统自动选 自动选点 择一系列已存在的点作为钻孔中心点; 图素选点:选择所有图素的端点定位钻孔点,包括线的端点、圆弧 图素选点 的端点、聚合线端点和封闭圆的中心点; 窗口选点:用光标构建一个窗口,系统用窗口范围内的一系列点产 窗口选点 生钻削刀具路径; 前一刀具路径的点:选择上一次钻削操作的点; 前一刀具路径的点 限定圆弧选点:用一个指定的半径(在一公差值内)选择开放的或 限定圆弧选点 封闭的圆弧的中心点钻孔; 样板选点:根据样板定义钻削点,指定一系列矩形排列或环形排列 样板选点 的点; 选项:选取该命令弹出图6-55所示点的排序对话框,用以设置点的 选项 排序方式—17种2D排序、12种圆周排序、16种交叉排序方式; 子程式:选取该命令可重复钻孔的位置,构建一个子程式,每个钻 子程式 孔循环在同一个孔执行钻削
- 1、下载文档前请自行甄别文档内容的完整性,平台不提供额外的编辑、内容补充、找答案等附加服务。
- 2、"仅部分预览"的文档,不可在线预览部分如存在完整性等问题,可反馈申请退款(可完整预览的文档不适用该条件!)。
- 3、如文档侵犯您的权益,请联系客服反馈,我们会尽快为您处理(人工客服工作时间:9:00-18:30)。
图6.14阵列图形
4)修剪图形:在主菜单中单击M修整/F倒圆角/R 圆角半径,输入半径为20, 接着分别选择两两相邻的圆弧,如图6.14所示的 1,2圆弧,修剪后的如图6.15。
图6.15修剪图形
5)存档:在主功能表中单击F档案/S存档, 输入文件名为Project.MC8。
2.产生刀具路径及NCI文件
图6.4操作管理对话框
图
图6.7追加文本或注释的后处理程序
6.2 全圆加工 全圆铣削加工的刀具路径能够自动加工整圆,下 面介绍全圆加工的操作步骤。 1.构建图形 在主功能表中单击C绘图/A圆弧/P极坐标/C圆心 点,输入圆心点为(50,0),半径为25,起始 角度为0°,终止角度为360°。
1)设置构图面:T,视角:I。 2)选择加工图形 在主功能表中单击T刀具路径/P挖槽/C串连, 选择图6.15的梅花形状,单击D执行, 系统 跳出刀具参数对话框。
3)刀具参数设置
在刀具参数对话框中的刀具图象显示区点击 鼠标右键,出现菜单,点击从刀库中选取刀具, 进入刀具管理器,选取一把10mm的球头刀, 按 O确定按钮,刀具就显示在刀具参数对话框的 刀具显示处。接着设置刀具参数: 参数设置如图6.16。
6.1菜单
6.1 手动输入 手动输入的功能是将命令、注释或特殊码 插入到NCI和NC文件中。其操作步骤如下: 1.调用手动输入功能: 在主功能表中单击T 刀具路径/N下一页/M手动输入,出现如图6.2 的手动输入对话框 。
图6.2手动输入对话框
2.输入或调用文本:在图6.2对话框中,可 选择文件来源用手动输入,输入的文本 或注释的长度不超过750个字元, 输入的 文本或注释将出现在NC文件中;也可选 择读取文字档,单击图6.2的选取按钮,弹 出如图6.3的对话框,选择所需的路径及 文件名,单击6.3的保存按钮,回到手动输 入对话框,再单击6.2的O确定按钮.
图6.9菜单
2)用鼠标选择刚创建的四个圆形,单击图6.9的 D执行/D执行,弹出图6.10所示对话框。 3)设置刀具参数 在图6.10的刀具参数对话框中的刀具图象显示 区点击鼠标右键,出现菜单,点击从刀库中选取刀 具,进入刀具管理器,选取一把10mm的平铣刀, 按 O确定按钮,刀具就显示在刀具参数对话框的刀 具显示处。接着设置其余刀具参数:
图6.18粗铣/精铣参数对话框
按图6.18中的确定按钮,出现加工路径如图6.19所示。
图6.19加工路径
6)储存NCI文件: 在主菜单中单击T刀具路径 /O操作管理,弹出操作管理对话框如图6.20 所示,选择执行后处理按钮, 弹出后处理程式 对话框如图6.21所示,选择储存NCI档,按O 确定按钮, 弹出图6.22对话框,以 YOUYING1.NCI的文件名保存梅花图形的 NCI刀具路径,单击图6.22保存的按钮,最后 关闭操作管理对话框。
图6.3选择文本对话框
在本例中选择图6.2的手动输入,并在手动输入 对话框中输入:TOOL NUMBER ONE 作为注释文本,以默认的形式存在 D:\MCAM8\MILL\NCI\T.NCI中。
3.将文本加到NC文件中:在主功能表中单击N公用 管理/P后处理/RNCI->NC,出现如图6.4所示的对 话框,单击是按钮,弹出如图6.5所示的对话框, 单击 打开按钮,弹出如图6.6所示的对话框, 单击保存按 钮,弹出追加了文本或注释的后处理程序如图6.7 所示,注释TOOL NUMBER ONE已追加到后处 理程序中。
参数设置后如图6.10所示。
刀具图象显示区
图6.10刀具参数对话框
设置全圆铣削参数:刀具参数设置后,单击全 圆铣削参数,设置参数. 参数设置后如图6.11所示,按确定按钮,出现走 刀路径如图6.12。
图6.11全圆铣削参数对话框
5)加工模拟 单击主功能表的N公用管理/B路径模拟/R自动执 行,重新出现刀具路径如图6.12所示。
图6.12刀具路径
6.3投影加工 投影刀具路径允许任何NCI文件投影至平 面、圆柱、圆锥体、球体或横截面等几何
元素上进行加工,产生新的NCI文件。投影 加工时仅改变NCI文件的深度,而不改变 XY坐标的尺寸。所有的投影都必须采用 球头铣刀进行加工。下面以梅花状图形为 例,介绍投影加工的步骤。
6.3.1.建立投影加工图形产生NCI文件 1.构建图形 1)设置构图面:T,视角:T。 2)绘制圆:在主菜单中单击C绘图/A圆弧/P极坐标/C圆 心点,输入圆心坐标(0,50),半径为20,起始角 度为0°,终止角度为360°。
刀具图象显示区
图6.16刀具参数对话框
4) 设置铣削参数 刀具参数设置完毕后,单击图6.16的挖槽参数按钮,设 置参数,参数,设置后如图6.17所示。
图6.17挖槽参数对话框
5)设置粗铣/精铣 参数,参数设置完毕后,单击图6.17 的粗铣/精铣参数按钮,设置参数,参数设置后如图 6.18所示。
同样再创建其它三个圆:圆心点(0,50)、 半径20;圆心点(-50,0),半径15和圆心 点(0,-50)、半径10,起始角度为0°, 终止角度为360°,如图6.8。
图6.8构建圆形
2.生成加工刀具路径 1)在主菜单中单击T刀具路径/N下一页 /C全圆路径/C全圆铣削,显示点之管理菜 单,如图6.9所示。
3)阵列图形:在主菜单中单击X转换/R旋转/W窗选,选 择刚创建的圆,接着单击D执行,系统提示输入阵列 的中心,单击菜单上O原点(0,0),默认系统原点为阵列 的中心,系统弹出如图6.13的对话框,设置相应的参数 如图示:
图6.13阵列图形对话框
单击图6.13的确定按钮,产生图形如图6.14。
第6章附加刀具路径
本章的学习目标: ·学习Mastercam8.0的附加刀具路径的功能。 ·应用附加刀具路径扩大Mastercam8.0的CAM 功能。 ·应用Mastercam8.0选择附加刀具路径的参数, 进行附加刀具路径编辑。
在主功能表中单击T刀具路径/N下一 页,出现附加刀具路径的菜单如图6.1所 示,现分节介绍如下: