矿物组成、结构及其对烧结矿质量的影响
烧结矿强度和粒级组成影响因素分析

烧结矿强度和粒级组成影响因素分析2008年全国炼铁技术交流会论文集烧结矿强度和粒级组成影响因素分析刘福泉王树立顾爱军(宣钢炼铁厂)摘要:本文结合宣钢炼铁厂及相关单位的研究成果,综合分析了影响烧结矿强度和粒度组成的因素和对策。
关键词:烧结矿强度粒度组成1 前言烧结矿强度及粒级组成是烧结矿质量的重要内容,没有合格的强度和适宜的粒级组成,就很难谈得上烧结矿的质量,烧结矿强度及粒级组成对高炉冶炼有着明显的影响,根据日本、前苏联、首钢、本钢的生产统计,烧结矿-5mm粒级每增加1%,将影响高炉焦比0.5%,影响高炉产量0.5-1.0%。
根据一些专家研究成果表明,烧结矿强度及粒级组成的影响因素是多方面的和复杂的,既有碱度和矿物组成,SiO、MgO和AlO等化学成分方面的影响,又有配碳量和FeO含量,热返矿粒度和返223矿量、熔剂和燃料粒度、配矿及反应性的影响,还有料层厚度、抽风负压和冷却速度等工艺操作参数方面的影响。
2 宣钢炼铁厂烧结矿强度及粒级组成与同类型企业比较表1烧结矿粒级组成 %碱度 2厂家烧结机面积m FeO% 强度% 倍 +40 40-25 25-16 16-10 10-5 -5 柳钢 50 1.70 6.03 20.85 27.51 39.41 12.21 69.5湘钢 50 2.0 6.70 4.46 14.24 17.96 28.63 28.56 6.07三明24×5 8.5 10.72 15.19 4 8.17 22.47 3.45 67.61唐钢60×3 5.6 20.3 56.30 13.70 4.1 78.30济钢36×2 8.03 24.62 52.53 10.34 4.66 85.81 太钢一烧 90 9.54 27.69 28.92 18.61 13.01 12.51 4.06 69.87 太钢二烧 90 9.39 22.50 18.81 11.64 14.47 25.00 9.33 73.058台累 1.90 7.48 13.59 21.78 23.09 17.63 17.68 5.21 77.08 武钢烧结厂入炉粒级 8.69 12.65 50.42 25.81 2.43 首钢二烧 78 1.91 9.12 13.36 21.70 38.23 23.29 3.42 87.37 宣钢一烧86×2 2.30 9.32 7.98 17.95 28.51 28.68 13.13 3.75 78.60 宣钢二烧64×2 2.30 9.28 6.53 15.97 27.15 30.93 15.87 3.55 78.20 宣钢三烧36×4 2.30 7.47 20.71 25.52 22.56 16.81 6.93 80.6 宣钢四烧36×2 24.09 33.22 20.81 12.48 6.85 2.54 81.2说明由于各烧结厂家测定烧结矿强度、粒级的地点、采样方法不统一,数据可比性不强。
烧结原料总结汇报

烧结原料总结汇报烧结原料总结汇报烧结原料是指用于制备烧结矿的各种原材料,包括铁矿石、焦炭、石灰石和配料等。
烧结过程是指将这些烧结原料经过炉内高温煅烧、氧化还原和结晶等反应,形成烧结矿的过程。
烧结原料在烧结过程中起着至关重要的作用,对烧结矿的质量和性能具有直接影响。
下面将对常见的烧结原料进行总结汇报。
1. 铁矿石:铁矿石是制备烧结矿的主要原料,它是由铁矿石矿石和氧化铁矿石组成的。
常见的铁矿石有赤铁矿、磁铁矿和褐铁矿等。
铁矿石的物理性质和化学成分直接影响烧结矿的组成和性能。
2. 焦炭:焦炭是烧结过程中重要的还原剂,它具有高固定碳含量、低灰、低硫和良好的机械强度等特点。
焦炭在高温条件下能够和铁矿石反应产生一系列还原反应,从而促进烧结矿中的铁矿石氧化还原反应的进行。
3. 石灰石:石灰石是烧结矿的主要熔剂,它在高温条件下能够与铁矿石中的硅酸盐和氧化铁石进行反应,生成易熔的矽酸钙和液相。
石灰石的质量和石灰石与铁矿石的配比对烧结矿的熔融性、融化温度和液相组成等有很大影响。
4. 配料:配料是指将各种烧结原料按一定的比例混合制备成的烧结原料混合料。
配料的质量和配比直接影响烧结矿的成分和物理性能。
通过合理的配料,可以在一定程度上改善烧结矿的熔融性、弹性、抗返矿性能等。
综上所述,烧结原料对烧结矿的质量和性能具有重要的影响。
铁矿石是烧结矿的主要原料,其物理性质和化学成分对烧结矿的组成和性能起着决定性作用。
焦炭作为还原剂能够促进烧结矿中的氧化还原反应。
石灰石作为熔剂能够改善烧结矿的熔融性和融化温度。
通过合理的配料,可以改善烧结矿的物理性能和抗返矿性能。
合理选择和使用烧结原料,优化烧结矿的质量和性能,对冶金行业的发展和节能减排具有重要意义。
通过对烧结原料的总结汇报,我们可以更好地理解烧结过程和烧结矿的形成机制,为冶金行业的研究和生产提供技术支持。
同时,我们也要强调烧结原料的合理使用和资源综合利用,提高烧结矿质量,减少能源消耗和环境污染,助力可持续发展的目标实现。
铁矿石碎矿粒度对烧结养分性能影响的研究

铁矿石碎矿粒度对烧结养分性能影响的研究随着全球经济的不断发展,矿山资源的开采和利用也日益受到关注。
铁矿石作为重要的工业原料之一,被广泛运用于水泥、钢铁等行业中。
在铁矿石的加工过程中,碎矿是必不可少的环节,其粒度也对烧结养分性能有重要影响。
本文将探讨铁矿石碎矿粒度对烧结养分性能的影响,并借助相关研究解释其原因。
铁矿石烧结过程中,养分性能表现为烧结矿的质量和机械强度等指标。
烧结矿的质量受到铁矿石粉末矿物成分、颗粒大小和形态、烧结温度、煤粉性质等因素的影响。
其中,铁矿石粉末的粒度是影响烧结养分性能的关键因素之一。
研究表明,铁矿石碎矿粒度对烧结养分性能有重要影响。
在一定范围内,铁矿石粉末的粒度越细,烧结矿的质量和机械强度越高。
这是由于粉末颗粒大小的变化会导致颗粒间的空隙率、表面积和孔隙度发生变化,从而影响到烧结过程中矿石的结合和转化。
粉末颗粒大小越小,其表面积越大,颗粒之间的空隙率也越小,因此,烧结矿的质量和机械强度也就越高。
除了粉末颗粒大小的影响外,铁矿石碎矿粒度对烧结养分性能的影响还与铁矿石的矿物成分和结构有关。
铁矿石的矿物组成复杂,不同矿物对烧结过程中的结合、转化和热分解有不同的影响。
在粒径相同的情况下,矿物成分不同的铁矿石其热分解温度和转化速率也会有较大的差异,进而影响到烧结矿的质量和机械强度。
因此,铁矿石碎矿粒度的作用是与其矿物成分和结构相互交织并共同作用的。
另外,铁矿石的碎矿粒度对于烧结过程中的烧损率也有很大的影响。
烧损率是指烧结过程中铁矿石的挥发分和焦炭的消耗率,其大小直接影响到冶金品质和成本。
一般来说,碎矿粒度较细的铁矿石在烧结过程中,因其表面积大,热传递效率高,所需焦炭量相对较少,从而减小烧损率。
另外,铁矿石粒度过细会导致料层透气性不足,从而增加焦炭的消耗和烧损率。
因此,铁矿石碎矿粒度的选择必须兼顾铁矿石烧结特性和冶金经济成本。
综合来看,铁矿石碎矿粒度直接影响烧结养分性能。
在烧结工程实践中,在保证烧结质量稳定和产品质量的前提下,应该根据铁矿石的矿物成分、结构特点和冶金成本等因素,综合考虑碎矿粒度的选择。
烧结矿的矿物组成和显微结构对其质量的影响

烧结矿的矿物组成和显微结构对其质量的影响这里所说烧结矿的质量,主要指其机械强度和还原性而言。
烧结矿的机械强度和还原性与组成烧结矿的矿物性质、含量、晶粒大小及其相互之间的分布情况有着直接的关系。
一、烧结矿中不同矿物组成和显微结构对其强度的影响1.烧结矿个各种矿物自身强度对烧结矿强度的影响烧结矿中的磁铁矿、赤铁矿、铁酸一钙、铁橄榄石有较高的抗压强度,其次则为钙铁橄榄石及铁酸二钙,在钙铁橄榄石中,当x小于等于1.0时,钙铁橄榄石的抗压性、耐磨性及脆性的指标均与前一类接近或超过,当x=1.5时,钙铁橄榄石强度相当低,而且易产生裂纹,它的晶格常数接近于2Cao·SiO 2。
其中玻璃质具有最低的强度。
因此在烧结矿的结构中应尽量减少玻璃质的形成,这对提高烧结矿强度是非常有利2.冷却结晶过程中产生的内应力对烧结矿强度的影响矿物组成对烧结矿强度的影响不仅仅局限于烧结矿中分离出来的结晶个体和玻璃质的强度作用,在很多情况下它还取决于烧结矿的矿物组成以及它在冷却时产生的内应力。
烧结矿在冷却过程中,产生不同的内应力:(1)由于烧结矿块表面与中心存在温差而产生的热应力。
这种热应力主要取决于冷却条件,可用缓慢冷却或热处理的方法来消除。
(2)烧结矿中各种矿物相具有不同热膨胀系数,因而引起各矿物相之间的应力。
研究防止这种矿物相之间的应力的产生,对提高熔剂性烧结矿的强度具有重要的意义。
(3)硅酸二钙在冷却过程中的多晶转变所引起的相变应力。
通常在烧结矿中主要出现β—C2S和γ—C2S。
当β—C2S在自然冷却转变为γ—C2S时,由于体积膨胀产生根大应力,这是导致高硅磁铁矿精矿烧结熔剂性烧结矿在自然冷却时产生自动粉化的根本原因。
例如,使用迁安高硅磁铁矿精矿(TFe60—62%,SiO2 10—12%)生产碱度为1.15的烧结矿,由于在其中生成少量的C2S ,当此烧结矿在冷却到300度以后时,发生由β—C2S向γ—C2S的相转变,因而导致烧结矿在冷却时产生严重的碎裂和粉化。
烧结矿矿物组成对其强度的影响

烧结矿矿物组成对其强度的影响1.烧结矿的显微结构介绍烧结矿中矿物组成主要有赤铁矿、磁铁矿、铁酸钙、硅酸钙和少量的非晶态的玻璃相。
烧结矿中的矿物组成及其相互间的结构特征,对烧结矿的机械强度有直接的影响。
所以研究烧结矿的质量应与其内部的矿物组成与显微结构特征联系起来。
烧结矿中常见的显微结构:(1)粒状结构:烧结矿中先结晶出的自形晶、半自形晶或其他形晶的磁铁矿,与粘结性矿物晶粒相互组成粒状结构。
(2)斑状结构:烧结矿中自形晶程度较强的磁铁矿斑状晶体与较细的粘结相矿物结合成斑状结构。
(3)骸晶结构:烧结矿中早期结晶的磁铁矿呈骨架状的自形晶中,常有粘结性的矿物填充其内,仍大致保持磁铁矿原来的结晶外形和边缘部分,形成骸晶结构。
(4)共晶结构:在烧结矿中磁铁矿呈圆点状在橄榄石的晶体内,或赤铁矿呈圆点状晶体分布在硅酸盐晶体中。
(5)熔蚀结构:在烧结矿中磁铁矿多为熔蚀残余他形晶,晶粒较小,多为浑圆形状,与铁酸钙形成熔蚀结构。
此种类型在高碱度烧结矿中常见,也是高碱度烧结矿的结构特点。
通过对烧结矿矿物组成和显微结构特征的研究,可以得知烧结矿中出现哪些矿物对提高其质量有利,出现哪些矿物不利。
2.烧结矿矿物组成对其强度的影响烧结矿各种矿物自身的强度对烧结矿强度的影响:烧结矿中的磁铁矿、赤铁矿、铁酸一钙、铁橄榄石有较高强度,其次为钙铁橄榄石及铁酸二钙,玻璃质具有最低的强度。
因此烧结矿的结构中应尽量减少玻璃质的形成,这对提高烧结矿的强度非常有利。
烧结矿中矿物组分对烧结矿强度的影响:(1)非自溶性烧结矿:其显微结构为斑状或共晶结构。
其中大量的磁铁矿斑晶被铁橄榄石和少量玻璃相所胶结,它的主要胶结物铁橄榄石机械强度较大,胶结磁铁矿能力较强,因而具有良好的强度。
(2)自熔性烧结矿:它的显微结构为斑晶或斑晶玻璃状结构。
其中的磁铁矿斑晶或晶粒被玻璃质和钙铁橄榄石所胶结,并且后二者含量居多,强度较差。
(3)高碱度烧结矿:其显微结构为溶蚀或共晶结构,由铁酸钙和磁铁矿构成。
烧结矿中各种矿物的形成
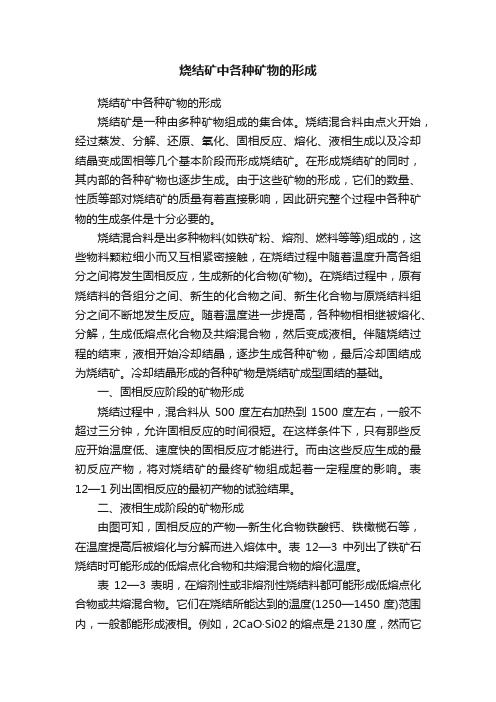
烧结矿中各种矿物的形成烧结矿中各种矿物的形成烧结矿是一种由多种矿物组成的集合体。
烧结混合料由点火开始,经过蒸发、分解、还原、氧化、固相反应、熔化、液相生成以及冷却结晶变成固相等几个基本阶段而形成烧结矿。
在形成烧结矿的同时,其内部的各种矿物也逐步生成。
由于这些矿物的形成,它们的数量、性质等部对烧结矿的质量有着直接影响,因此研究整个过程中各种矿物的生成条件是十分必要的。
烧结混合料是出多种物料(如铁矿粉、熔剂、燃料等等)组成的,这些物料颗粒细小而又互相紧密接触,在烧结过程中随着温度升高各组分之间将发生固相反应,生成新的化合物(矿物)。
在烧结过程中,原有烧结料的各组分之间、新生的化合物之间、新生化合物与原烧结料组分之间不断地发生反应。
随着温度进一步提高,各种物相相继被熔化、分解,生成低熔点化合物及共熔混合物,然后变成液相。
伴随烧结过程的结束,液相开始冷却结晶,逐步生成各种矿物,最后冷却固结成为烧结矿。
冷却结晶形成的各种矿物是烧结矿成型固结的基础。
一、固相反应阶段的矿物形成烧结过程中,混合料从500度左右加热到1500度左右,一般不超过三分钟,允许固相反应的时间很短。
在这样条件下,只有那些反应开始温度低、速度快的固相反应才能进行。
而由这些反应生成的最初反应产物,将对烧结矿的最终矿物组成起着一定程度的影响。
表12—1列出固相反应的最初产物的试验结果。
二、液相生成阶段的矿物形成由图可知,固相反应的产物—新生化合物铁酸钙、铁橄榄石等,在温度提高后被熔化与分解而进入熔体中。
表12—3中列出了铁矿石烧结时可能形成的低熔点化合物和共熔混合物的熔化温度。
表12—3表明,在熔剂性或非熔剂性烧结料都可能形成低熔点化合物或共熔混合物。
它们在烧结所能达到的温度(1250—1450度)范围内,一般都能形成液相。
例如,2CaO·Si02的熔点是2130度,然而它能与FeO组成熔点为1280度的共熔混合物,因而能熔入液相。
高碱度烧结矿的主要矿物结构
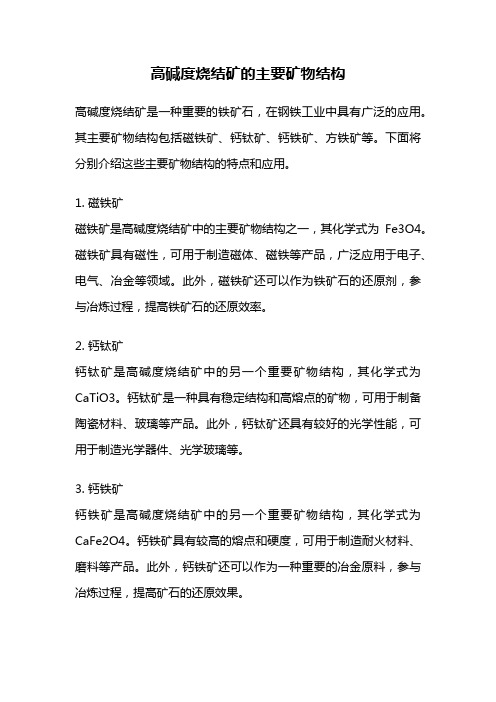
高碱度烧结矿的主要矿物结构高碱度烧结矿是一种重要的铁矿石,在钢铁工业中具有广泛的应用。
其主要矿物结构包括磁铁矿、钙钛矿、钙铁矿、方铁矿等。
下面将分别介绍这些主要矿物结构的特点和应用。
1. 磁铁矿磁铁矿是高碱度烧结矿中的主要矿物结构之一,其化学式为Fe3O4。
磁铁矿具有磁性,可用于制造磁体、磁铁等产品,广泛应用于电子、电气、冶金等领域。
此外,磁铁矿还可以作为铁矿石的还原剂,参与冶炼过程,提高铁矿石的还原效率。
2. 钙钛矿钙钛矿是高碱度烧结矿中的另一个重要矿物结构,其化学式为CaTiO3。
钙钛矿是一种具有稳定结构和高熔点的矿物,可用于制备陶瓷材料、玻璃等产品。
此外,钙钛矿还具有较好的光学性能,可用于制造光学器件、光学玻璃等。
3. 钙铁矿钙铁矿是高碱度烧结矿中的另一个重要矿物结构,其化学式为CaFe2O4。
钙铁矿具有较高的熔点和硬度,可用于制造耐火材料、磨料等产品。
此外,钙铁矿还可以作为一种重要的冶金原料,参与冶炼过程,提高矿石的还原效果。
4. 方铁矿方铁矿是高碱度烧结矿中的另一种常见矿物结构,其化学式为Fe2O3。
方铁矿是一种重要的铁矿石,可用于制造铁和钢等产品。
方铁矿在高温下具有良好的还原性,可以通过冶炼过程将其还原为金属铁。
高碱度烧结矿的主要矿物结构研究对于优化其冶炼过程和提高产品质量具有重要意义。
通过深入了解和研究这些矿物结构的特点和应用,可以更好地利用高碱度烧结矿资源,提高其综合利用效率。
除了上述介绍的几种主要矿物结构外,高碱度烧结矿中还存在着其他一些矿物结构,如锰铁矿、铝铁矿等,这些矿物结构也具有一定的应用价值。
高碱度烧结矿的主要矿物结构包括磁铁矿、钙钛矿、钙铁矿和方铁矿等。
这些矿物结构在钢铁工业中具有广泛的应用,可用于制造磁体、耐火材料、陶瓷、玻璃等产品,并参与冶炼过程,提高矿石的还原效率和产品质量。
对于这些主要矿物结构的深入研究,有助于优化高碱度烧结矿的冶炼工艺,促进钢铁工业的可持续发展。
烧结矿主要成分
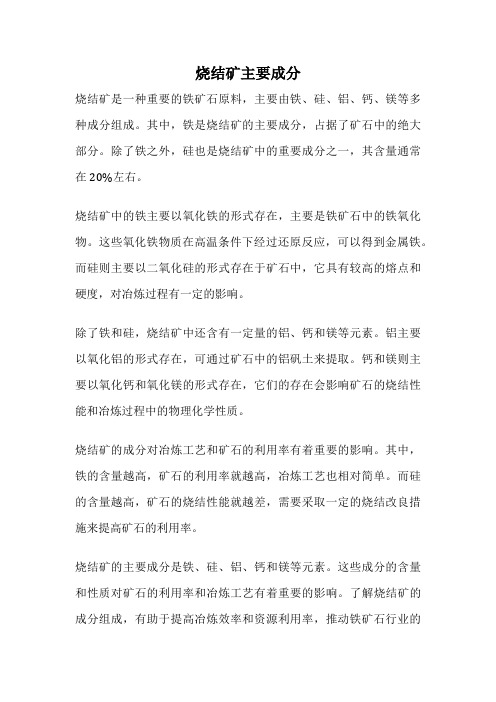
烧结矿主要成分
烧结矿是一种重要的铁矿石原料,主要由铁、硅、铝、钙、镁等多种成分组成。
其中,铁是烧结矿的主要成分,占据了矿石中的绝大部分。
除了铁之外,硅也是烧结矿中的重要成分之一,其含量通常在20%左右。
烧结矿中的铁主要以氧化铁的形式存在,主要是铁矿石中的铁氧化物。
这些氧化铁物质在高温条件下经过还原反应,可以得到金属铁。
而硅则主要以二氧化硅的形式存在于矿石中,它具有较高的熔点和硬度,对冶炼过程有一定的影响。
除了铁和硅,烧结矿中还含有一定量的铝、钙和镁等元素。
铝主要以氧化铝的形式存在,可通过矿石中的铝矾土来提取。
钙和镁则主要以氧化钙和氧化镁的形式存在,它们的存在会影响矿石的烧结性能和冶炼过程中的物理化学性质。
烧结矿的成分对冶炼工艺和矿石的利用率有着重要的影响。
其中,铁的含量越高,矿石的利用率就越高,冶炼工艺也相对简单。
而硅的含量越高,矿石的烧结性能就越差,需要采取一定的烧结改良措施来提高矿石的利用率。
烧结矿的主要成分是铁、硅、铝、钙和镁等元素。
这些成分的含量和性质对矿石的利用率和冶炼工艺有着重要的影响。
了解烧结矿的成分组成,有助于提高冶炼效率和资源利用率,推动铁矿石行业的
可持续发展。
- 1、下载文档前请自行甄别文档内容的完整性,平台不提供额外的编辑、内容补充、找答案等附加服务。
- 2、"仅部分预览"的文档,不可在线预览部分如存在完整性等问题,可反馈申请退款(可完整预览的文档不适用该条件!)。
- 3、如文档侵犯您的权益,请联系客服反馈,我们会尽快为您处理(人工客服工作时间:9:00-18:30)。
烧结矿是烧结过程的最终产物,是许多种矿物的复合体,矿物组成非常复杂。
影响烧结矿矿物组成的因素包括:燃料用量、烧结矿碱度、脉石成分和添加物种类以及操作工艺条件等。
烧结矿中各矿物通过自身的强度和还原性影响烧结矿的强度和还原性。
5.5.4.1 烧结矿的矿物组成由于原料条件和烧结工艺条件不同,烧结矿的矿物组成不尽相同,但是总是由含铁矿物及脉石矿物两大类组成的液相粘结在一起的。
酸性烧结矿矿物主要为磁铁矿、赤铁矿、浮氏体、金属铁、铁橄榄石、钙铁橄榄石、玻璃体、铁酸钙、硅钙石、石英等;主要胶结物为铁橄榄石和少量的钙铁橄榄石、玻璃体等。
自熔性烧结矿矿物主要为磁铁矿、赤铁矿、浮氏体、金属铁、钙铁橄榄石、橄榄石类、铁酸钙、硅酸钙、钙铁辉石、钙铁辉石-钙镁辉石固溶体、石英、石灰等;主要胶质物为钙铁橄榄石、玻璃体等。
高碱度烧结矿的矿物主要是磁铁矿、赤铁矿、钙质浮氏体、铁酸钙和硅酸二钙等;主要胶质物为铁酸二钙。
当烧结矿脉石中含有较多的Al2O3或烧结料中Fe2O3较多时,粘结相还有铝黄长石、铁铝酸四钙、铁黄长石、钙铁榴石(3CaO·Fe2O3·3SiO2)。
MgO含量较多时会出现钙镁橄榄石、镁黄长石、镁蔷薇辉石等。
脉石中含有萤石时,烧结矿中则含有枪晶石。
烧结含钛铁矿时会出现钙钛石(CaO·TiO2,3CaO·2TiO2)、梢石(CaO·TiO2·SiO2)。
对某一烧结矿来说,不一定全部含有上述矿物,而且数量也不相等。
磁铁矿和浮氏体是各种烧结矿的主要含铁矿物,非铁矿物以硅酸盐类矿物为主。
表5-6给出了武钢不同碱度烧结矿的矿物组成。
表5-6 武钢不同碱度烧结矿的矿物组成烧结矿碱度矿物组成,(体积)%磁铁矿赤铁矿铁酸一钙铁酸二钙铁黄长石硅酸钙铁橄榄石浮氏体金属铁玻璃质0.8 57.5 6.2 2.7 - 13.1 - 2.73 0.18 - 17.41.3 48.32.9 14.4 - 15.3 0.92 - - 0.1 18.02.4 34.6 0.2 29.1 4.4 10.9 4.44 - - - 16.23.5 27.6 0.2 39.3 9.3 10.7 7.51 - - 0.3 7.3 5.5.4.2 烧结矿的结构烧结矿的结构包括宏观结构和显微结构。
烧结矿的宏观结构有微孔海绵状、粗孔蜂窝状和石头状。
一般来说微孔海绵状结构的烧结矿,强度和还原性都好,是理想的宏观结构。
燃料用量适中和各种操作条件都合适时,可以得到这种条件的烧结矿。
当燃料用量偏高和液相数量偏多时出现粗孔蜂窝状结构,有熔融而光滑的表面,其还原性和强度都有所降低。
如果燃料用量过多,造成过熔,则出现气孔很少的石头状烧结矿,强度好,但还原性很差。
相同的燃料用量下,液相粘度低时形成微孔结构,粘度高时形成粗孔结构。
显微结构一般是指在显微镜下矿物组成的形状,大小和它们相互结合排列的关系。
从微观上看,烧结矿具有各种不同的结晶形态和单体矿物组成。
烧结矿中的矿物按其结晶程度分为自形晶、半自形晶和他形晶三种。
具有极完好的结晶外形的称为自形晶;部分结晶完好的称为半自形晶;形状不规整且没有任何完好结晶面的称为他形晶。
矿物的结晶程度取决于本身的结晶能力和结晶环境。
烧结矿中最多的含铁矿物磁铁矿往往以自形晶或半自形晶的形态存在,这是因为磁铁矿在升温过程中较早地再结晶长大,有良好的结晶环境,并且具有较强的结晶能力。
其它粘结相在冷却过程中开始结晶,并按其结晶能力的强弱以不同的自形程度充填于磁铁矿中间,来不及结晶的以玻璃体存在。
矿物呈完好的结晶状态时强度好,而呈玻璃态时强度差。
随着生产工艺条件的变化,不同烧结矿在显微结构上也有明显的差异。
由铁矿物和粘结相组成的常见显微结构列于表5-7。
表5-7 烧结矿的常见显微结构5.5.4.3影响烧结矿矿物组成和显微结构的因素影响烧结矿矿物组成和显微结构的因素包括燃料和熔剂用量、烧结原料的矿物组成以及烧结操作工艺条件。
1)燃料用量烧结料中的配碳量决定烧结温度、烧结速度和气氛条件,对烧结矿物组成影响很大。
烧结非熔剂性赤铁矿时,当配碳量过少(3%~4%)则不能保证赤铁矿充分还原和分解,磁铁矿结晶程度差,燃烧层液相数量少,只有少量铁橄榄石和钙铁橄榄石不均匀地分布在磁铁矿和石英接触处,不起粘结作用,粘结相主要是玻璃质,孔洞多,强度差,但还原性好。
在正常燃料用料下,烧结矿矿物主要是磁铁矿和铁橄榄石,还有少量浮士体,磁铁矿结晶程度提高,粘结相主要是铁橄榄石,孔洞少,烧结矿强度提高。
当燃料消耗量过多少时(7%),烧结温度升高,还原气氛增加,生成大量的浮氏体和铁橄榄石,磁铁矿减少,可能出现金属铁,烧结矿因过熔,造成大孔薄壁或气孔度少的烧结矿,使强度和还原性都变坏。
生产熔剂性烧结矿时,随着含碳量增加,磁铁矿结晶程度提高,生成大粒结晶,粘结相主要是钙铁橄榄石代替玻璃质,孔洞少,烧结矿强度提高,还原性有所下降。
但用碳量过多时,浮氏体和钙铁橄榄石增加,磁铁矿减少,易生成过熔烧结矿。
同时,高温下易生成正硅酸钙,在冷却时发生晶型转变,使烧结矿粉化,强度和还原性都变坏。
图5-20给出了国内某钢厂熔剂性烧结矿矿物组成与烧结料含碳量之间的关系。
燃料用量对烧结矿结构的影响是:含碳量低时,烧结矿的微孔结构发达,随着含碳量的增加,烧结矿逐渐发展成为薄壁结构,而且沿料层高度也有变化,上部微孔多,下部则大孔薄壁多。
1-正硅酸钙;2-钙铁橄榄石;3-玻璃质;4-铁酸钙;5-赤铁矿;6-磁铁矿图5-20 含碳量与熔剂性烧结矿矿物组成的关系2)烧结矿碱度在燃料用量一定的条件下,烧结矿的最终矿物组成主要取决于碱度。
a)低碱度烧结矿与高碱度烧结矿搭配使用的低碱度烧结矿,其碱度值一般选择在0.8~1.0之间。
该碱度的烧结矿中铁矿物主要为磁铁矿、少量赤铁矿,粘结相为钙铁橄榄石、铁黄长石、钙铁辉石、硅灰石和玻璃质等硅酸盐,一般不含铁酸钙,总粘结相量为25%~30%,强度好于自熔性烧结矿,但还原性能较差。
在高、低碱度烧结矿搭配冶炼时,由于其配比高而影响冶炼效果。
酸性球团烧结矿的碱度值一般在0.3~0.5之间,克服了普通酸性烧结矿还原性能差、垂直烧结速度慢、燃料消耗高等问题。
两种酸性烧结矿的矿物组成见表5-8。
表5-8 两种酸性烧结矿矿物组成普通酸性烧结矿为典型的熔融型结构。
磁铁矿多为自形晶、半自形晶、颗粒粗大,还有部分骸晶状赤铁矿。
铁矿物被玻璃质、橄榄石胶结,形成斑状结构。
浮氏体与硅酸盐矿物形成共晶结构。
酸性球团烧结矿外观呈葡萄状块、单体球和熔结块。
固结方式为铁矿物再结晶固结和渣相固结。
单球与葡萄状球具有明显的带状构造(即外部带、过渡带和中心带)。
磁铁矿、赤铁矿多为再结晶长大固结,颗粒为细粒扩散型结构。
部分铁矿物与硅酸盐渣相胶结成粒状结构。
介于球团矿与烧结矿两种微观结构之间。
表5-9 自熔性烧结矿的矿物组成b)自熔性烧结矿自熔性烧结矿粘结相量不足,且粘结相主要是质脆且难还原的硅酸盐和玻璃质,故烧结矿强度差,还原性能差,软熔温度低。
当进行冷却和整粒处理时,返矿率高,粉末多,粒度小。
特别是生产高品位烧结矿、钒钛烧结矿和含氟烧结矿时,烧结与炼铁技术经济指标更差。
国内4个钢铁厂的自熔性烧结矿的矿物组成见表5-9。
生产自熔性烧结矿需要在较高的温度条件下才能生成足够的液相,故液相的粘度小,冷却后的烧结矿呈大孔薄壁结构,当采取厚料层低碳操作时,结构有所改善。
铁矿物以磁铁矿为主,有少量的次生赤铁矿,多呈半自形晶,部分自形晶和他形晶,晶粒较小,小于0.01mm晶粒能达20%~40%。
粘结相以硅酸盐为主,只有少量的铁酸钙。
柱状集合体的钙铁橄榄石种有针状和柱状的正硅酸钙,并与铁矿物形成粒状结构。
铁酸一钙多为板状晶体与铁矿石形成熔蚀结构。
c)高碱度烧结矿我国和日本几种高碱度烧结矿的矿物组成见表5-10。
表5-10 高碱度烧结矿矿物组成矿物组成,(体积)%厂别磁铁矿赤铁矿铁酸钙正硅酸钙玻璃质黄长石其它鞍钢新烧35 15 35 3 10 少 2 宝钢25 25 30-35 3 10 3 2首钢35 15 35 3 10 少 2梅山45 15 25 3 12 - -马钢35 20~25 25~30 3 12 少-武钢二烧35 15 30 3 10 - -柳钢40.7 17.7 30.3 5.0 4.5 1.8*-包钢50 10 25 3 10 2 少量枪晶石本钢33 16 44 2 5 - -日本(平均)13.3 30.4 42.4 14(硅酸盐)日本神户**43.2 6.8 44.4 5.8(硅酸盐)*其中黄长石0.2%,钙铁橄榄石1.6%;**该烧结矿FeO含量10.29%。
碱度在2.5以上的高碱度烧结矿,几乎不含钙铁橄榄石和玻璃体,只有铁酸钙、磁铁矿和硅酸钙三种矿物。
随着碱度升高,铁酸钙和硅酸钙明显增加,磁铁矿减少,矿物组成基本不变。
由于作为主要矿物的磁铁矿和铁酸钙,强度和还原性较好。
并且随着硅酸三钙的增加,正硅酸钙明显减少,同时过量的CaO起了稳定β-2CaO·SiO2的作用,所以此类烧结矿不发生粉化现象,强度和还原性较好。
高碱度烧结矿具有上述特点,是由于燃料用量一定时,随着碱度的提高,熔剂量逐渐增多,放出CO2,降低了烧结料层温度和还原气氛,有利于提高烧结矿的氧化度,所以磁铁矿减少,铁橄榄石减少以至消失,而过量的CaO有利于生成CaO·Fe2O3和CaO-SiO2体系矿物。
高碱度烧结矿外观一般呈致密块状,大气孔少,气孔壁厚,熔结较好,断面呈青灰色金属光泽。
高碱度烧结矿的微观结构为:赤铁矿、磁铁矿多呈他形晶和半自形晶,被铁酸钙固结形成板状熔蚀结构、柱状熔蚀结构和针状交织结构,当进行低温烧结时,则以后种结构为主。
局部区域磁铁矿被硅酸盐粘结相固结形成粒状结构和斑状结构,也有周围被粘结相固结的原生赤铁矿颗粒。
显微粒度一般比自熔性和低碱度烧结矿粗,小于0.01mm的晶粒数量较少,大部分在0.01~0.03mm之间。
高碱度混合料中石灰石粉配比较高,如果石灰石粒度粗(+3mm部分大于10%),将使烧结矿中游离氧化钙含量升高,而降低烧结矿的贮存强度。
3)脉石成分及添加物脉石中的SiO2是影响烧结矿矿物组成的重要因素。
只有一定数量的SiO2,才能形成足够数量的铁橄榄石或钙铁橄榄石等粘结相,将分散的磁铁矿晶粒粘结起来,保证烧结矿的强度。
如果烧结料中的SiO2数量太少,则烧结矿矿物只有磁铁矿、赤铁矿和少量玻璃体,烧结矿由大量磁铁矿集合而成,粘结相数量少,只有少量玻璃体充填于磁铁矿晶粒之间,起不到连接作用,烧结矿强度不好。
脉石中含有一定量的Al2O3,烧结过程中进入熔体中,使烧结矿矿物结构大大复杂化。
Al2O3含量大于7%时,形成多种铝铁酸钙和铁酸钙的固熔体(CaO·Al2O3+CaO·Fe2O3),降低烧结料的熔化温度,促进液相生成。