机械专业英语翻译unit12教学文稿
机械工程专业英语课翻译

Unit1Two methods of designating limit dimensions are considered as standard.One method is the maximum material method in which the large dimension is placed above the smaller dimension for male parts, and the reverse is true for female parts.This method is well suited for small lot quantities because it is likely that the machinist himself may check the dimension of the parts .In so doing he will be verifying initially the large dimension of the male parts and the smaller dimension of the female part.other method is the maximum number method and is preferred by production and quality control departments .In this method of designating a dimension , the large number is always placed above the smaller number ,regardless of whether the part is male or female.两种方法都被看作是指定极限尺寸标准。
一种方法是最大的资料法,大尺寸较小的尺寸摆在上面男性部件,事实正相反对女性的部分。
(完整版)机械类专业英语课文参考翻译

第一课Text:It is known that metals are very important in our life. Metals have the greatest importance for industry. All machines and other engineering[7endVi5niEriN] constructions have metal[5metl] parts; some of them consist only of metal parts.众所周知,金属在我们的生活中是非常重要的,金属对于工业而言是有巨大的重要性,所有机器和其他工程构造都有金属零部件,其中一些还只能由金属组成。
There are two large groups of metals:1) Simple metal- more or less pure chemical elements[5elimEnt]2) Alloys[5AlCi]- materials consisting of a simple metal combined with some other elements.有两大类金属:(1)纯金属——或多或少的金属元素(2)合金——组成纯金属的原料结合其他元素。
About two thirds of all elements found in the earth are metals, but not all metals may be used in industry. Those metals which are used in industry are called engineering metals. The most important engineering metalis iron[5aiEn], which in the form of alloys with carbon[5kB:bEn] and other elements, finds greater use than any other metal. Metals consisting of iron combined with some other elements are known as ferrous[5ferEs] metals; all the other metals are called nonferrous[5nCn5ferEs] metals. The most important nonferrous metal arecopper[5kCpE], aluminum[E5lju:minEm], lead[li:d], zinc[ziNk], tin[tin], but all these metals are used muchless than ferrous metals, because the ferrous metals are much cheaper.在地球上发现的所有元素中,大约三分之二是金属元素,但是并不是所有的金属都能够用于工业上。
机械工程英语第二版第二部分完整翻译(叶邦彦、陈统坚主编)教学提纲
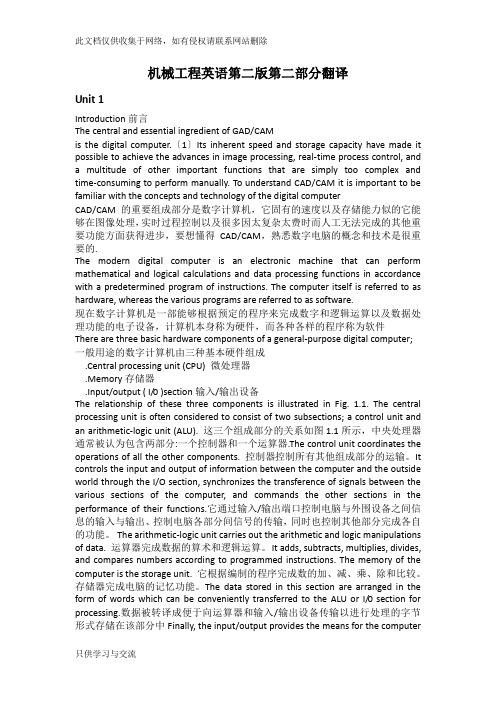
机械工程英语第二版第二部分翻译Unit 1Introduction前言The central and essential ingredient of GAD/CAMis the digital computer.〔1〕Its inherent speed and storage capacity have made it possible to achieve the advances in image processing, real-time process control, and a multitude of other important functions that are simply too complex and time-consuming to perform manually. To understand CAD/CAM it is important to be familiar with the concepts and technology of the digital computerCAD/CAM的重要组成部分是数字计算机,它固有的速度以及存储能力似的它能够在图像处理,实时过程控制以及很多因太复杂太费时而人工无法完成的其他重要功能方面获得进步,要想懂得CAD/CAM,熟悉数字电脑的概念和技术是很重要的.The modern digital computer is an electronic machine that can perform mathematical and logical calculations and data processing functions in accordance with a predetermined program of instructions. The computer itself is referred to as hardware, whereas the various programs are referred to as software.现在数字计算机是一部能够根据预定的程序来完成数字和逻辑运算以及数据处理功能的电子设备,计算机本身称为硬件,而各种各样的程序称为软件There are three basic hardware components of a general-purpose digital computer; 一般用途的数字计算机由三种基本硬件组成.Central processing unit (CPU) 微处理器.Memory存储器.Input/output ( I/0 )section输入/输出设备The relationship of these three components is illustrated in Fig. 1.1. The central processing unit is often considered to consist of two subsections; a control unit and an arithmetic-logic unit (ALU). 这三个组成部分的关系如图1.1所示,中央处理器通常被认为包含两部分:一个控制器和一个运算器.The control unit coordinates the operations of all the other components. 控制器控制所有其他组成部分的运输。
机械工程英语第2版教学课件ppt作者叶邦彦陈统坚华南理工大学主编unit12

Unit 12 Nanomaterial and micro-machine纳米材料与微型机械Nanomaterial [纳米材料]Nanomaterials represent today’s frontier in the development of novel advanced materials and present great promises and opportunities for a new generation of materials with improved and tailorable properties for applications in sensors, optoelectronics, energy storage, separation and catalysis.Applications of NanomaterialsThe first technological uses of these materials were as catalysts [催化剂] and pigments [颜料].In microelectronics, It would be ideal if the switching occurred with the motion of a single electron.In addition to technology, nanomaterials are also interesting systems for basic scientific investigations.Micro-machine1. IntroductionMany people may think that the smaller machines are easier to make. However, it is actually difficult to invent a small machine that will be significant to human beings. Here gives a possible reason.In addition to micro-machining, the development of micro-machines requires a number of technologies including materials, instrumentation, control, energy, information processing, and design.2. Micro-machine as Gentle MachinesThe most unique feature of a micro-machine is its small size. Micro-machines do not affect the object or the environment as much as conventional machines do. They perform their tasks gently.3. Micro-electronics and Mechatronics [机电一体化]The concept of micro-machines and related technologies is still not adequately unified , as these are still at the development stage .The micro-machines and related technologies are currently referred to by a variety of different terms.4. The Evolution of Machines and MicromachinesEver since the Industrial Revolution, machine systems have grown larger and larger in the course of their evolution.Only very recently has evolution in the opposite direction begun, with the appearance of mechatronics.The next target in miniaturization [微型化] of machine systems is miniaturization of the structural parts left untouched by present mechatronics.Notes1. Nanomaterials and nanotechnology have become a magic word in modernsociety. Nanomaterials repres ent today’s frontier in the development of novel advanced materials and present great promises and opportunities for a newgeneration of materials with improved and tailorable properties for applications in sensors, optoelectronics, energy storage, separation and catalysis.纳米材料和纳米技术已成为现代社会一个具有魔幻色彩的词汇。
机械专业英语翻译

Application and evaluation of VR-based CAPP systemQ.Peng *,F.R.Hall,P.M.ListerSchool of Engineering and the Built Environment,University of Wolverhampton,Wolverhampton WV11SB,UKAbstractThis paper proposes an approach to an integrated CAPP/VR system.A desktop VR environment is used to explore the machining process element of CAPP.An architecture of a virtual CAPP system is proposed based on an incorporated VR design interface,which can respond to the dynamic manufacturing process.The key problems under discussion are to ®nd an effective method to quickly capture the 3D information from the manufacturing environment,and to de®ne a uniform and well-organised structure of the program layout for achieving improved sharing of VR resources.Examples of the simulation for cutting process are supplied to demonstrate and verify the proposed CAPP/VR integration system.#2000Published by Elsevier Science B.V .Keywords:CAPP;Virtual reality;CAD/CAM;Engineering simulation1.IntroductionManufacturing competition has acted as a driving force for the application of new technologies in industries.Suc-cessful industrial companies must be able to adapt quickly to fast-changing conditions by the market and competitors within a shorter lead time at a low cost.Although great emphasis has been placed on concurrent engineering,it is still a challenge for engineers to bridge the gap created by the con¯ict between design demands and manufacturing requirements.As a bridge between computer-aided design (CAD)and computer-aided manufacturing (CAM),compu-ter-aided process planning (CAPP)plays an important role in an integrated CAD/CAM system.The aim of process planning is to de®ne in detail the process required for producing a product according to its speci®cations and available manufacturing resources.This can be a very complex process.The selection of a machine tool,cutter,or a material removal process is based on a wide variety of factors,therefore CAPP relies on a good interface between the engineer and the computer system being used.So far,research projects have led to the experimental systems that are strictly limited in their applications.These limitations can be summarised as follows:Failure to process dynamically .Since the manufacturing process is a dynamic system,classical programs are notable to satisfy the demands of current manufacture.Some-times,the new knowledge is required to ensure correct manufacturing,and often time does not allow for this knowledge base to be added to the CAPP system.Separate design and manufacturing process .A process planner receives a design and may complete the process plan separately and remotely from the design engineer.The plan is then sent to the shop floor for manufacturing.Direct communication and interaction between the design and manufacturing process is therefore not encouraged. Poor data collection .As process planning can be highly complex and involves the expertise and intricate relations of knowledge coming from various sources,it is a difficult and time consuming task to represent and formalise the manufacturing knowledge used by a CAPP system.Arti-ficially intelligent (AI)systems,fuzzy logic and neural network technologies have been employed to overcome this difficulty in the following areas [1]:the recognition and processing of machining features; part families,machining cells and group technologies; operation selection and planning;and operation sequence planning.These applications,however,currently work with rather restricted models.They cannot be used without a well formed model.The correct execution of these systems depends on the pre-de®ned knowledge and data provided by human experts.The AI systems readily fail with non-heuristic problems.To overcome these dif®culties,a potential method to assist in the generation of process plans is to supporttheJournal of Materials Processing Technology 107(2000)153±159*Corresponding author.Tel.: 44-1902-322276.E-mail address :pengQ@cc.Umanitoba.CA (Q.Peng).0924-0136/00/$±see front matter #2000Published by Elsevier Science B.V .PII:S 0924-0136(00)00677-4process planner by giving him direct access to the infor-mation about the products,manufacturing resources,and manufacturing methods.A virtual environment is a computer simulator in which the user feels that he or she is immersed within a realistic surroundings and is able to interact with the objects and operations.The virtual environment generated by computer is more affordable and interactive than a traditional simu-lator.Therefore,virtual reality(VR)offers the opportunity to visualise,explore,manipulate,and interact with objects within a computer generated environment,and is a useful tool to enhance CAPP involved in design,development, evaluation,and validation.It is expected that the application of this new technology will bridge the some of the gaps that currently exist.The following parts of this paper evaluate the applications of VR-based CAPP systems,and propose a cost-effective integrated CAPP/VR system aiming towards meeting the current requirement for competitive manufac-turing processes.2.Applications of CAPP and VRCAPP has been a very popular research area for the recent years.Many researches have been working towards the improvement of CAPP systems because of the shortage of experienced process planners and the need for integrated CAD/CAM systems.There are two major traditional approaches to CAPP system:variant and generative methods [2].The variant CAPP system uses an information retrieval procedure based on group technology(GT).All the parts involved in this system are grouped into component families according to their similarity of design and manufacture.This method may be useful for relatively well-established com-panies,since they have relatively stable products.The generative CAPP system uses manufacturing knowledge to generate process plans.This is advantageous for new product development,but it relies on the development of AI, fuzzy logic and neural network technologies as mentioned previously.A conventional CAPP procedure is shown in Fig.1.This process is completed generally by a`serial'approach from the input of part information to the output of the process plan.This procedure cannot meet the needs of concurrent engineering,and will not serve to develop new products within shortened lead times.VR technology has shown its advantages over conven-tional simulation processes where it can aid the understand-ing of sophisticated engineering problems.AVR system can provide not only basic computerised functions,but also an ef®cient way to utilise human sense and interaction to engineering applications in a virtual environment.A number of researchers have employed VR techniques to deal with various aspects and issues in design and manu-facturing.Mine[3]developed a meta-CAD system for virtual environments to take advantage of the natural and intuitive forms of interaction available in a virtual world. Dani and Gadh[4]provided an approach to concept shape designs via a virtual reality interface,whilst Schulz et al.[5] presented their research in developing a virtual environment for car-body engineering applications by creating VRML scenes using the Internet as a communication platform for analysing engineering simulation.The use of VR to support industrial applications is rapidly increasing[6,7].BMW uses VR to explore the visualisation of new car layouts to enhance communication andtheFig.1.An example of a conventional CAPP procedure.154Q.Peng et al./Journal of Materials Processing Technology107(2000)153±159simulation of processes,while Rolls Royce Aeroengines and Associates use VR technology in their early veri®cation of maintenance procedures,training maintenance engineers in these procedures,enhanced visualisation of complex envir-onments and rapid prototyping of plant control and instru-mentation.Several commercial software toolkits,such as dVise [8],Superscape [9],and the Deneb Robotics'package [10]are available to support the creation of virtual environment.These tools provide a VR environment to support existing CAD technology,such as modelling and database construc-tion.A user can generate a synthetic virtual environment which can make the user have the feeling of immersion through a wide variety of VR hardware.Deneb Robotics has developed several VR tools to support machining and robot environments [10].These tools have been used to support this research.Fig.2shows a virtual manufacturing workshop produced by the Deneb Robotics toolkit.Navigation around the VR environment can be performed by using the com-puter mouse and keyboard.A designer can design plan,test and redesign the object and the manufacturing process using VRs specialist input devices.When the design is satisfactory,the information may then be transferred into the CNC machines to generate a real prototype.The applications of VR in process planning can be justi®ed as follows:Process simulation can employ the virtual environment as a real-time,interactive graphical visualisation or inter-face.By using VR,it is hoped that process planners will be able to respond immediately to production demands. Easier user interface.Support via user groups or networks,a very powerful and cost-effective means of process planning will be obtained by combining VR technology and Internet technology.Desktop VR is seen as a tool which can provide ¯exible visualisation and simulation,and provide not only improved design and process planning but also training of engineers and the workforce.3.A virtual CAPP systemA virtual CAPP system can be de®ned as a computer system that can generate the same information about machining process planning as we can observe in a real workshop.A virtual CAPP system has been constructed by the authors based on the Deneb Robotics VR toolkit (see Fig.3).An example of 3D machining simulation of a component is shown in Fig.4.The ®rst step to run the system is to select the machine tool and workpiece blank from the database,and load the blank into the worktable of the machine tool.An interactive process allows the user to either select machine tools from a menu with the mouse button,or to type in or to select an input from data ®les.The position of the machine and blank can be moved or rotated so that the user's viewpoint could be positioned close to the workpiece.The next step is to load the machining process in the form of NC code that is used to machine the workpiece.The machining operations can then be run.The dimensions of the part can be inspected using the system control menu duringoperations.Fig.2.A virtual manufacturing environment produced by Deneb Robotics toolkit [9].Q.Peng et al./Journal of Materials Processing Technology 107(2000)153±159155This system allows the user to create a 3D model of components from an original design,simulate the machining process based on existing NC code,and pass the code to NC machines in the real world to create the real parts.The machining process of a part can be viewed from different directions in a 3D simulation process,such that the user can easily ®nd failures or weaknesses in the process planning.It is therefore a useful tool for either training or for trial run purposes in order to detect any errors that might exist in the process planning.This virtual CAPP system,however,is still a `series'process from top to bottom,as shown in Fig.3,with a VR environment providing a 3D simulator of the existing pro-cess planning.The models of machine tools and workpieces must exist in the database or library,and it cannot support a real-time respond for process planning.A virtual CAPP system ideally would integrate various activities of the manufacturing process,resources,and the virtual environment as shown in Fig.5.It should have the following capabilities:improve the response of real-time process for the CAPP system;enhance the application interface with existing software packages;ease the interaction of user with machines and equipment on the shop floor;flexible control of the shop floor;consider easily uncertainly factors during machining process from multiple viewpoints;bridge the gap between process planning and machining process;andovercome the difficulties of automatic generation of process plan from the component geometric model.Clearly,there are some dif®culties in developing user-based application using existing VR toolkits due to the following reasons:there are obvious differences in the performance of these VR toolkits between their demonstration and the practical applicability,because of the poor capability of integration with other CAD/CAM systems;it takes a time to construct a user-based application because of a relatively inefficient interface for data input and limited modelling capabilities;and it is difficult to support a real-time process.Most existing toolkits,for example,can only simulate pre-de®ned processes,and does not allow the user to interact with the virtual environment in real-time.Issues such as the immediate feedback for the modi®cation of a machining process,and real-time decision making cannot be addressed.Understandably,therefore,research efforts have been made to improve the current CAPP/VRsystem.Fig.3.The process of a virtual CAPP system based on Deneb Robotics VRtoolkit.Fig.4.An example of 3D machining simulation of acomponent.Fig.5.The resources of a virtual CAPP system.156Q.Peng et al./Journal of Materials Processing Technology 107(2000)153±1594.Capturing of user-based environments and modelling of objectsModelling is the most time consuming task in the con-struction of a VR system,and the creation of a virtual environment from separate objects can be daunting.To develop a cost-effective method in building a virtual envi-ronment will save considerable time and allow existing objects to be captured very quickly.Most current VR systems are designed to use CAD modelling tools outside the virtual environment.Feature-based methods are used by most of the current CAD systems.Starting with a simple shape,features are added or modi®ed to re®ne the model.This approach speeds up the model creation process because existing designs can be used as the basis for new models.However,modelling from other CAD tools requires translator programs to convert data from one CAD system to another,because there is not a universal database format available.It therefore takes a signi®cant amount of time to build a new VR environment if an existing CAD database is not available.The3D laser scanner is a popular and accurate tool to recover3D data from an object.However,its capturing process is slow,because it scans the surface line by line, and the high energy light source also has to be treated with care.An alternative tactile approach to3D shape capture measures the surface of an object by the touch of a mechani-cal arm.The relative coordinate positions are determined by the sensors in the joints of the arm,which can be supported by robotic devices.This method is accurate and reliable but the slow speed is a disadvantage.Furthermore,access to all surfaces may be dif®cult.In the electro-magnetic sensor system,a transmitter is driven by a pulsed DC signal.The sensor measures the transmitted magnetic-®eld pulse referenced to the magnetic transmitter.An electronics card controls the transmitting and receiving elements and converts the received signals into3D position and orientation measurements.This method sup-ports real-time measurement with high accuracy,but its disadvantages include the touch tracking process with the wire and sensor,limited captured points from sensors,and the limitation of the magnetic-®eld applied.An image is generally represented in a computer as a 2D array of pixels.Each pixel has a value which represents the image intensity sampled at a point,or a small rectangular picture cell.In a greyscale image,each pixel takes a number of different values,which allows256different intensity levels.Image-based methods are characterised by their non-contact measurement,low energy,and instant capturing of the overall surface data.Therefore,a new method has been used by the authors[11]which integrates the shape from shading and binocular stereo techniques to overcome the weaknesses of the above-mentioned methods.The emphasis of the methodology is to extract the geometric information from a3D object in the mini-mum time and transfer this information into the VR system.It can support the development of the manufacturing environments.5.Manufacturing knowledge representation and acquisitionManufacturing knowledge in process planning is mainly concerned with the machining process of a part,such as the part feature,set-up,tooling,®xture,process de®nition, machining parameter and NC program.It deals with the geometric representation of the parts,form-generating cap-ability of process,and constrained machining knowledge. The feature-based approach can be used to perform the manufacturing knowledge representation.The geometry and topology features of the part are linked by the different machining methods.The system consists of a parametric library of machining features.These features,for example, include:planar,cylinder,hole,slot,pocket,step,notch and ®llet.The hierarchy of the feature-based knowledge model is shown in Fig.6.Cutting parameters can be stored in a database,while the machining process knowledge can be stored in a knowledge base with either the form of the frame, or the rules.A user interface based on the VR environment enables the system to easily acquire,modify or update this knowledge base.The planner can easily construct the shape of the object,position the selected features,generate the operations and arrange the operation sequence.6.De®nition of a uniform and well-organised structure for the virtual environmentA uniform and well-organised structure for the virtual environment can create improved sharing of VR resources. Visualisation of both the product geometry and the physical arrangement of the process planning can help to generate acceptable,accurate and ef®cient process plans.It canalsoFig.6.Hierarchy of the feature-based knowledge model.Q.Peng et al./Journal of Materials Processing Technology107(2000)153±159157increase the degree of customer acceptance and improve the ®nished product.The architecture of an integrated CAPP/VR system is proposed by the authors in Fig.7.It can access directly various resources from a database,a knowledge base,and Internet data during the process planning.The design process of CAPP can be simulated visually and can interact with the designer in real-time.7.Example and discussionFig.8shows an example to simulate a machining process of a part in the system's user interactive ers can operate this window to complete the process plan,for data retrieval,machining simulation and feedback in real-time.The system has the capability to update process data,andtoFig.7.Proposed architecture for an integrated CAPP/VRsystem.Fig.8.An example for simulating a machining process of a part with the system's user interactive window.158Q.Peng et al./Journal of Materials Processing Technology 107(2000)153±159communicate information regarding emergency situations through the user interactive window.This system can overcome many conventional problems that affect the¯exibility and reactivity of the CAPP system. It has the following advantages:it provides the design for manufacturing practice at the early stages of process planning,with immediate feed-back from the integrated CAPP/VR system;dynamic on-line activity reduces the variety of shop floor manufacturing constraints,thereby improving the validity of the process plans;when re-planning,the VR-based tool makes quick deci-sion making possible;andsharing manufacturing resources through Intranet becomes feasible.However,there is clearly still much work required:An evaluation of the method,comparing the output with generalised models derived from industry.Compound features need to be defined in a feature library, including pattern holes,cross-slot,and multi-step.More compound features can be defined by combining primi-tive features through the user interface.Integration of the3D information capturing system and VR environment.Integration of process planning and supply chain issues, which can support order/purchase activities through the Internet.8.ConclusionsVR is becoming an important method to solve engineer-ing problems because of its special simulation features,such as immersion,real-time interaction,and3D graphics.Its further application will not only depend on the development of VR technology,but more on its capability to provide cost-effective solutions to real industrial problems.CAPP normally deals with the complex processes and multi-factors arising from a wide variety of manufacturing environments,and therefore,it relies on a good interface between the engineers and the computer system.The devel-opment and application of VR technology enhances the capability of the engineering simulation process.VR pro-vides a3D virtual environment and can be used in the design and validation of a CAPP system.The VR application of a particular CAPP system will have real potential in the manufacturing environment,however, currently it is dif®cult for user to build using existing VR toolkits,which identi®es the area for future improvements to be made.An integrated CAPP/VR model has been proposed by the authors to improve current CAPP applications. The development of an effective CAPP system will rely upon the application of VR technology and the integration of a wide variety of existing CAD,knowledge base,arti®cial intelligence,optimisation,CAM and internet/network technologies.References[1]L.Monostori,H.Van Brussel,E.Westkampfer,Machine learningapproaches to manufacturing,Ann.CIRP45(2)(1996)675±708.[2]C.McMahon,J.Browne,CAD/CAM Principle,Practice andManufacturing Management,2nd Edition,Addison-Wesley,Reading, MA,1998.[3]M.R.Mine,ISAAC:a meta-CAD system for virtual environments,Computer-Aided Des.29(8)(1997)547±553.[4]T.H.Dani,R.Gadh,Creation of concept shape designs via a virtualreality interface,Computer-Aided Des.29(8)(1997)555±563.[5]M.Schulz,T.Reuding,T.Ertl,Analysing engineering simulations ina virtual environment,IEEE Comput.Graphics Appl.18(6)(November/December1998)46±51.[6]J.R Wilson,S.Cobb,M.D'Cruz,R.Eastgate,Virtual Reality forIndustrial Application:Opportunities and Limitations,Nottingham University Press,1996.ISBN1-897676-573.[7]L.J.Rosenblum,M.R.Macedonia,Projects in VR,IEEE Comput.Graphics Appl.18(6)(November/December1998)6±9.[8]dVise User Manual,Version4.1,Division Ltd.,UK,1997.[9]Superscape web site:///.[10]Deneb Robotics,Inc.,Simulation Software Product,VNC,Quest,Reference Manuals,1998.[11]Q.Peng,M.Loftus,A fast3D modelling approach for virtual realityenvironments,advances in manufacturing technology,in:Proceed-ings of the XII National Conference on Manufacturing Research, Derby,UK,Professional Engineering Publishing Limited,1998, pp.309±314.ISBN1-86058-172-2.Q.Peng et al./Journal of Materials Processing Technology107(2000)153±159159。
新版轮机英语unit12 ME Engines.ppt
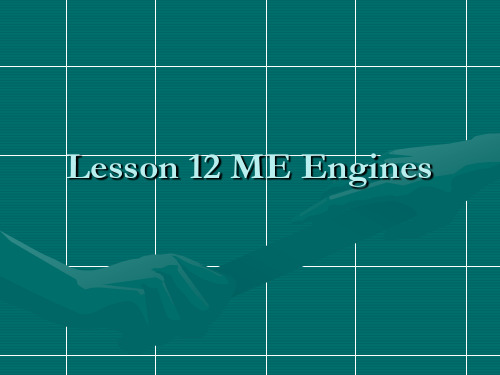
• 电控柴油机的优点 • 电控柴油机的结构 • 电控柴油机工作原理
• The introduction of the electronically controlled camshaft-less low speed diesel engines, which is now gaining momentum, is a milestone(里程碑) in diesel technology that deserves a place in history like Rudolf Diesel’s first engine in Augsburg,
• However, a mechanical cam is fixed once made and, in spite of (不管) various mechanical and hydraulic add-on devices like VIT, etc. , timing control possibilities are limited with mechanical cams .
• without the limitation from the camshaftcontrolled engine , where this would result in too high pressure at high load.
• Both cam angle , inclination(坡度,曲率) and length are electronically variable .
• the 1912 motor vessel Selandia, the introduction of turbocharging on two-stroke diesels in 1954,and the first SCR (Selective Catalytic Nox Reduction) systems on ships in 1989.
机械工程英语第二版(叶邦彦 陈统坚主编)第二部分书后翻译
Unit 1 计算机技术1、The central and essential ingredient of GAD/CAM is the digital computer. CAD/CAM的核心部分是数字计算机。
2、Sinfnal conditioners,which filter random electrical noise and smooth the signal emanating from transducting devices.信号调整器,它可以过滤掉杂乱的电噪声,并可修整、平滑由传感装置送出的模拟信号。
3、A pulse counter is used to convert the pulse trains into a digital representation ,which is then aplied to the computer”s input channel. 脉冲计数器可将脉冲串转换为一种数字代码,以适合于计算机输入通道。
4、This results from the shared nature of the communication lines.这来自通信线的共享特性。
5、messages to a specific computer are usually transmitted to all computers in the network,with the addressee decoding its address and accdot the information.送往某特定计算机的信息,一般都传送到网络中的所有计算机,同时由信息接收计算机译出地址码并接收信息。
6、In a network,all computers are connected and communicated with each other according to some kinds of enacthed regulations or agreement,which are called"network protocols".在网络中,所有计算机都根据一些规则和协议进行连接和通信,规则和协议称为网络协议。
机械工程专业英语教程(第2版)[施平主编][翻译]_lesson12
Spur GearsGears , defined as toothed members transmitting rotary motion from one shaft to another , are among the oldest devices and inventions of man . In about 2600 B.C. , the Chinese are known to have used a chariot incorporating a complex series of gears . Aristotle , in the fourth century B.C. , wrote of gears as if they were commonplace . In the fifteenth century A.D. , Leonardo da Vinci designed a multitude of devices incorporating many kinds of gears .齿轮,在最古老的设备和发明人中,被定义为通过轮齿将旋转运动从一根轴传递到另一根轴,大约在公元前2600年,中国人就知道用战车组成一系列复杂的齿轮系。
西元前四世纪,亚里士多德记述了齿轮就好像是他们司空见惯的一样。
在十五世纪,达芬奇设计了大量的包含各种各样齿轮的设备。
Among the various means of mechanical power transmission (including primarily gears , belts , and chains ) , gears are generally the most rugged and durable . Their power transmission efficiency is as high as 98 percent . On the other hand , gears are usually more costly than chains and belts . As would be expected , gear manufacturing costs increase sharply with increased precision -- as required for the combination of high speeds and heavy loads , and for low noise levels . ( Standard tolerances for various degrees of manufacturing precision have been established by the AGMA , American Gear Manufacturers Association. )在众多的机械传动方式中(包括齿轮传动,带传动,链传动),一般来说,齿轮是最经久耐用的,它的能量传递效率高达98%。
机械专业英语翻译unit12
牛头刨床
金属切削加工设备,利用住复运动的刀具切割已固定在 机床工作平台上的工件〔一般用来加工较小工件)。机床 的刀架似牛头,故名。滑枕带着刨刀,作直线住复运动 的刨床,因滑枕前端的刀架形似牛头而得名。牛头刨床 主要用于单件小批生产中刨削中小型工件上的平面、成 形面和沟槽。 牛头刨床的主运动为电动机→变速机构→ 摇杆机构→滑枕往复运动;牛头刨床的进给运动为电动 机→变速机构→棘轮进给机构→工作台横向进给运动。
Shaper(牛头刨床)( Fig.13-3) The machine tools of this group are generally used
for machining flat surfaces, which is usually performed by a cutter that peels the chip from the work. The main motion is reciprocating and the feed is normal to the direction of the main motion. 译文:通常由一个刀具从工件上切削屑片来完成的这 组的机床通常用于加工平面。它的主运动是往复和进 给是正常的主运动方向。
ratchet棘轮 19.pawl棘爪 20.cross rail横梁
27.internal grinder内圆磨床 28.external grinder 外圆磨床 29.Wheel head 磨头
21.grinding machine 磨床
22.grinding wheel砂轮
The milling machine(铣床) is a machine that
may travel only at right angles to the spindle while the Universal Milling Machine(万能铣床) is provided with a table. 译文:铣床的主轴是由一台安装在立柱上的电动机通 过一系列齿轮传动所驱动的。普通铣床的工作台只能 沿着垂直于主轴的方向运动,而万能铣床(如图12-2) 可以做到。
新版轮机英语unit12 ME Engines
• constitutes a number of mechanical parts made redundant and replaced by hydraulic and mechatronic(机械电子的) mechatronic(机械电子的) part with enhanced functions , as summarised below:
• Governor • Regulating shaft(油门调节轴) shaft(油门调节轴) • Mechanical cylinder lubricator • Local control stand(机旁控制台) stand(机旁控制台)
• The above-mentioned parts are replaced aboveby: • Hydraulic Power Supply (HPS)(液压动 (HPS)(液压动 力单元) • Hydraulic Cylinder Units (HCU)(液压 (HCU)(液压 汽缸单元)
• The necessary power for fuel injection and exhaust valve operation-previously operationprovided via the chain drive-is now driveprovided from a Hydraulic Power Supply (HPS) unit located at the front of the engine at bedplate level.
• With the Alpha Lubrication system, about 0.3 g/bhph cyl. Oil can be saved, compared with engines with mechanical lubricators.
- 1、下载文档前请自行甄别文档内容的完整性,平台不提供额外的编辑、内容补充、找答案等附加服务。
- 2、"仅部分预览"的文档,不可在线预览部分如存在完整性等问题,可反馈申请退款(可完整预览的文档不适用该条件!)。
- 3、如文档侵犯您的权益,请联系客服反馈,我们会尽快为您处理(人工客服工作时间:9:00-18:30)。
磨床
磨床使用磨粒进行切削,磨粒粘接在一起形成 不同形状不同尺寸的砂轮和砂带用于切削。磨 削可以带来高质量的工件表面。另外,工件的 尺寸精度在磨削过程中以0.00025的精度得到提 高。使用不同种类的磨床可以加工工件的内外 表面。相同的加工方法--使用不同形式的研磨 介质诸如粘接剂,粉状颗粒和磨粒--还包括研
The spindle of the milling machine is driven by an
electric motor through a train of gears mounted in
the column.
The table of the plain milling machine(普通铣床)
The tool and the apron(挡板) of a shaper are located on the ram(骨枕). A chip is peeled off the
work on the forward stroke. An adjustable table with
“T” – slots holds work, vise, and other fixtures for
holding the work. 译文:牛头刨床的刀具和挡板位于骨枕。切削片在 前进冲程的过程中被剥落。“T”型的可调节工作台 - 工件槽,台钳,和其他用于固定工件的夹具。
The shaper has a rocker arm(摇臂) which drives the ram, and a mechanism for regulating the length of the stroke(冲程) The ram supports the tool head. The head carries the down-feed (向下进刀) mechanism and will swivel from side to side to permit the cutting of angles. This is generally hand feed, but some shapers are equipped with a power down-feed in addition to the regular hand down-feed.
机械专业英语翻译unit12
牛头刨床
金属切削加工设备,利用住复运动的刀具切割已固定在 机床工作平台上的工件〔一般用来加工较小工件)。机床 的刀架似牛头,故名。滑枕带着刨刀,作直线住复运动 的刨床,因滑枕前端的刀架形似牛头而得名。牛头刨床 主要用于单件小批生产中刨削中小型工件上的平面、成 形面和沟槽。 牛头刨床的主运动为电动机→变速机构→ 摇杆机构→滑枕往复运动;牛头刨床的进给运动为电动 机→变速机构→棘轮进给机构→工作台横向进给运动。
with one end, while the other end of the arbor rotates in the bearing mounted on the arbor yoke(刀杆座). 译文:铣刀安装于刀杆上,通过垫片或者套筒进行定 位。刀杆的一端固定于主轴上,刀杆的另一端则安装 于刀杆座上的回转轴承上。
Shaper(牛头刨床)( Fig.13-3) The machine tools of this group are generally used
for machining flat surfaces, which is usually performed by a cutter that peels the chip from the work. The main motion is reciprocating and the feed is normal to the direction of the main motion. 译文:通常由一个刀具从工件上切削屑片来完成的这 组的机床通常用于加工平面。它的主运动是往复和进 给是正常的主运动方向。
The milling machine(铣床) is a machine that
removes metal from work with a revolving milling cutter(铣刀) as the work is fed against it.
译文:铣床是一种当工件向铣刀进给时,铣刀旋转
23.finish 光洁度 24.Cutter grinder 工具磨床 25.surface grinder平面磨床 26.centreless grinder无心磨 床
27.internal grinder内圆磨床 28.external grinder 外圆磨床 29.Wheel head 磨头
may travel only at right angles to the spindle while the Universal Milling Machine(万能铣床) is
provided with a table. 译文:铣床的主轴是由一台安装在立柱上的电动机通 过一系列齿轮传动所驱动的。普通铣床的工作台只能 沿着垂
12.Universal Milling Machine万能铣床 13.Shaper 牛头刨床 14.planer龙门刨床
8.Knee升降台
15.ram 滑轨 16.vise 台钳 17.fixture 夹具 18.notched wheel or
ratchet棘轮 19.pawl棘爪 20.cross rail横梁 21.grinding machine 磨床 22.grinding wheel砂轮
着从工件上切除金属的机床。
“that”引导定语从句,修饰“machine”;“as” 引导时间状语从句,意为“当……时候”。
The milling cutter is mounted on an arbor(刀杆) where it is held in place(定位) by spacers(垫片) or bushings(套筒). The arbor is fixed in the spindle
专业名词Words and Expressions
ling machines 铣床 ling cutter 铣刀 3.arbor刀杆 4.spacer垫圈、垫片 5.bushing套 6.yoke支座 7.starting lever起动手柄
9.elevating screw升隆丝杆 10.index head 分度头 11.foot stock 分度头支座