内孔数控车削加工(编程)教案
内孔数控车削加工(编程)教案

内孔数控车削加工(编程)教案一、教学目标1. 了解内孔数控车削加工的基本概念和特点。
2. 掌握内孔数控车削加工的编程方法和步骤。
3. 能够独立完成内孔数控车削加工的编程和操作。
二、教学内容1. 内孔数控车削加工概述内孔数控车削加工的定义内孔数控车削加工的应用领域内孔数控车削加工的优势和特点2. 内孔数控车削加工编程基础数控编程的基本概念和原理数控编程的常用指令和功能内孔数控车削加工的编程格式和步骤3. 内孔数控车削加工编程实例内孔数控车削加工的编程实例解析内孔数控车削加工的编程技巧和注意事项内孔数控车削加工的编程练习和操作三、教学方法1. 讲授法:讲解内孔数控车削加工的基本概念、特点和编程方法。
2. 示教法:演示内孔数控车削加工的编程实例和操作步骤。
3. 练习法:学生独立完成内孔数控车削加工的编程练习和操作。
1. 教材:内孔数控车削加工教材或相关数控编程教材。
2. 数控车床:内孔数控车床或其他适用的数控车床。
3. 编程软件:数控编程软件或其他适用的编程工具。
五、教学评价1. 课堂参与度:学生参与课堂讨论和提问的情况。
2. 编程练习:学生完成编程练习的情况和质量。
3. 操作技能:学生独立完成内孔数控车削加工操作的情况和质量。
六、教学环境1. 实验室环境:具备内孔数控车床及相关设备的实验室,保证学生能够进行实际操作。
2. 计算机辅助教学:配备计算机和数控编程软件,以便学生进行编程练习和操作模拟。
3. 安全设施:确保实验室内具备必要的安全设施,如安全眼镜、手套等,以保障学生的安全。
七、教学安排1. 课时:根据教学计划安排,本课程共计课时,其中理论教学课时,实践操作课时。
2. 教学进度:按照教学大纲和教案进行教学,确保学生能够逐步掌握内孔数控车削加工的编程方法和操作技能。
3. 实践操作:安排适量的实践操作时间,让学生能够在实际操作中巩固所学知识和技能。
1. 教师应定期进行教学反思,了解学生的学习情况和进展,及时调整教学方法和策略。
数控车削编程与加工技术(第2版)第1篇

上一页 下一页 返回
任务二 认识车刀
• 钨钛钴类硬质合金(YT):主要用于切削钢材. • 钨钛钽(铌)钴类硬质合金(YW):既能切削钢材,也能切削铸铁,更适于切
削耐热钢、不锈钢、高锰钢等难加工材料. • 碳化钛基类硬质合金(YN):能精车削和半精车削各种钢材,包括淬火钢
、不锈钢、工具钢等.用于加工尺寸较大的工件和表面粗糙度要求较 高的零件,其效果尤为显著. • 3.特殊刀具材料 • 特殊刀具材料主要有陶瓷、人造金刚石、立方氮化硼等.
上一页 下一页 返回
任务二 认识车刀
• 4.涂层刀具 • 涂层刀具是在韧性较好的硬质合金基体上或高速钢刀具基体上,经真
空溅射等方式涂覆一层耐磨性较高的难熔金属化合物而制成.涂层厚 度一般为5~10μm. • 涂层法制造的可转位刀片,耐用度可提高数倍,切削速度可提高约30 %,这种刀片一般用于切削钢材.某些新型涂层刀片,还能切削难加工材 料. • 对于受摩擦剧烈的刀具宜采用TiC(碳化钛)涂层;而在容易产生黏结的 情况下,宜采用TiN(氮化钛)涂层刀具.
上一页
返回
任务一 认识车削加工
• 一、常见的车床及其主要特征和用途
• 1.卧式车床 • 卧式车床外形如图1-1所示. • (1)主要特征:卧式车床主轴水平布置;加工对象广;主轴转速和进给量
的调整范围大;主要由工人手工操作,生产效率不高. • (2)主要用途:用于加工各种轴、套和盘类零件上的回转表面.此外,还
的运动指令. • (5)伺服系统接到执行信息指令后,立即驱动车床进给机构严格按指令
的要求进行位移,以进行工件的自动切削加工.
下一页 返回
任务三 认识数控车床
• 二、数控车床的主要组成部分
数控车削内孔

参考文献:
[1]Mohan D, Singh K P, Sinha S, et. al. Removal of
pyridine derivatives from aqueous solution by activated
carbons developed from agricultural waste materials [J]
便于排屑,刃倾角 λ 取负值(后排屑)。
(3)机夹可转为内孔车刀。数控车床所采用的可转位车刀,
与通用车床相比一般无本质的区别,其基本结构、功能特点是相
同的。但数控车床的加工工序是自动完成的,因此对可转位车
刀的要求又高于通用车床所使用的刀具。
2. 内孔车刀的安装
(1)内孔车刀刀尖应与工件中心等高或稍高。
dihydropyrimidinones [J]Ultrasonics sonochemistry, 2008, 15(6),
1015
[7]Wang Q, Shao Y, Gao N, et al. Degradation kinetics
and mechanism of 2, 4-Di-tert-butylphenol with UV /
(2)内孔车刀
刀柄伸出刀架不宜过长。
(3)内孔车刀刀柄基本平行于工件轴
线。
(4)盲孔车刀装夹时,主刀刃应与孔底平成 3°-5°,在车平面
时要求横向有足够的退刀余量。
3. 刀位点和对刀
刀位点是指在加工程序编制中用以表示刀具特征的点。内
孔车刀的刀尖是刀位点。在执行加工程序前,需调整每把刀的
刀位点,使其尽量与某一理想基准点重合,这一过程称为对刀。
粗糙度和较高的几何精度,在车削安装套类零件时关键的是要
《数控车削编程与加工技术》教学及实训教案
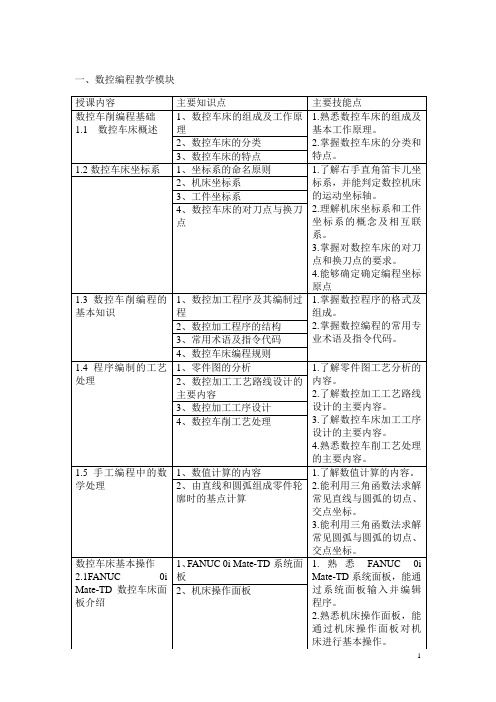
一、数控编程教学模块2、左旋螺纹的车削方法3、被吃刀量的合理选取课题12 外梯形螺纹车削1、梯形螺纹车刀的刃磨2、低速车削梯形螺纹的方法3、梯形螺纹的测量课题13 平底孔及台阶孔车削1、盲孔车刀的选用及刃磨2、平底孔及台阶孔的车削方法3、内孔的测量课题14 通孔及内沟槽车削1、通孔车刀及内沟槽刀的选用及刃磨2、通孔及内沟槽的车削方法3、工件的测量课题15 探测锤头及锤柄的加工1、车刀的选用及刃磨2、加工工艺的设计3、零件表面质量的控制课题16 手柄的加工1、车刀的选择及刃磨2、手柄加工工艺的设计课题17 线垂的加工1、在车床上攻丝、套丝的方法2、小直径钻头的使用方法课题18 国际象棋的加工1、国际象棋棋子的加工工艺2、零件表面质量的控制实训课题主要技能点课题19 配合工件的加工1、刀具的选用及刃磨2、锥体的配合3、三角螺纹配合4、形位公差的保证实训课题参考图纸课题3课题4课题5 课题6课题7课题8课题9次数 D d L1 Ø38±0.20 Ø 18 35.72 Ø 36±0.15 Ø 16 34.13 Ø 34±0.10 Ø 15 32.4 课题10课题11课题12课题13课题14d 总长Φ1 Φ30+0.01 0100+-0.20牙型角:30°螺距:P牙顶间隙:a c螺距1.5~5间隙0.25螺距6~12 间隙0.5大径d 公称直径中径:d2=d-0.5p小径d3=d-2h3 牙高h3=0.5p+ac牙顶宽f=0.366p牙槽底宽w=0.366p-0.536p 三针检测量针检测0.51p (dD)单针测量A=M+d0/2课题15课题16课题172 Φ35+0.05 0100+-0.20 Φ403 Φ40+0.027 0 100+-0.20Φ45课题19。
《数控加工编程及操作》教案

闽北职业技术学院教案2010 ~ 2011 学年第二学期课程名称:数控加工编程及操作授课教师:游年华课程所属系(部):信息与工程系课程名称:机械制造基础授课班级:09机械(1)班课程类型:理论课总学时:64(理论24)学分:4使用教材:《数控加工编程及操作》清华大学出版社刘力健牟盛勇主编教学方法、手段:讲授考核方式:考试主要参考书目:《数控加工编程及操作》中国轻工业出版社郭庆梁浦艳敏主编(教案正文)第1章数控加工系统授课日期:2011年3月7日下午第7、8节标题: 1.1数控加工及其特点;1.2数控机床的工作原理及性能指标;1.3 数控机床的典型机械结构;1.4 数控刀具系统;1.5 夹具及对刀工具简介;1.6 数控加工技术的发展教学目的与要求:1、通过本章的学习,要求读者了解数控加工的优点、数控机床的性能指标、数控机床的组成和一些典型结构、刀具及夹具系统。
2、掌握数控加工的基本过程。
授课时数:2学时教学重点和难点:1、教学重点:数控加工的基本过程。
2、教学难点:数控加工系统。
教学内容及过程:教学内容方法与手段时间分配第一课时引入新课:同学们都十分熟悉普通加工设备,如普通车床、普通铣床等常见的机加工设备,但在实际的生产加工中数控设备的应用是十分广泛的,数控车床、数控铣床就是我们接下来要学习的内容。
第1章数控加工系统1.1 数控加工及其特点PPT 、讲授法5分钟1.2 数控机床的工作原理及性能指标PPT 、讲授法15分钟1.2.1 数控机床组成及工作原理1.2.2 数控机床的分类及性能指标1.3 数控机床的典型机械结构(教学难点)PPT 、讲授法25分钟1.3.1 数控机床主传动系统1.3.2 数控机床的进给传动系统1.3.3 数控机床的自动换刀装置第二课时1.4 数控刀具系统PPT 、讲授法15分钟1.4.1 数控刀具的特点1.4.2 数控刀具的分类1.5 夹具及对刀工具简介(教学重点)PPT 、讲授法15分钟1.5.1 数控机床的夹具1.5.2 数控机床的对刀工具1.6 数控加工技术的发展PPT 、讲授法15分钟1.6.1 数控系统的发展1.6.2 数控机床的发展思考题(作业):1 简述数控加工的优点。
《数控车削编程与操作训练》教案5-6
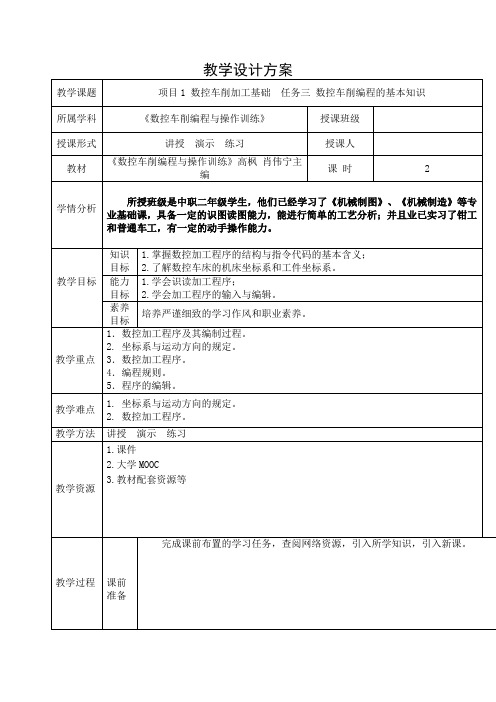
教一、数控车削编程的基本知识1.3.1数控编程的内容及步骤1.数控编程的主要内容:2.数控编程的主要步骤:1.3.2 数控编程的方法:数控编程分为手工编程和自动编程两种。
1.手工编程对于加工形状简单的零件,手工编程比较简单,程序不复杂,而且经济、及时此,在点定位加工及由直线与圆弧组成的轮廓的加工中,手工编程仍广泛应用。
2.自动编程自动缩程就是用计算机及相应编程软件编制数控加工程序的过程。
常见软件MasterCAM、UG、Pro/E、CAXA制造工程师等。
1.3.3 数控编程的基本知识:1.数控车床的坐标系(1)坐标系的建立标准坐标系采用右手直角笛卡儿坐标系,如图1—10所示。
在坐标系中车床主轴纵向方向是z轴,平行于横向运动方向为z轴,车刀远离的方向为正向,接近零件的方向为负向。
卧式车床坐标系如图1—11所示。
(2)编程坐标系与编程原点为了方便编程,首先要在零件图上适当地选定一个编程原点,该点应尽量设置件的工艺基准与设计基准上,并以这个原点作为坐标系的原点,再建立一个新的坐标称编程坐标系或零件坐标系。
编程坐标系用来确定编程和刀具的起点。
在数控车床上,编程原点一般设在右与主轴回转中心线交点0上,如图1—12b所示;也可设在零件的左端面与主轴回心线交点0上,如图1—12a所示。
坐标系以机床主轴线方向为z轴方向,刀具远件的方向为Z轴的正方向。
x轴位于水平面且垂直于零件旋转轴线的方向,刀具远轴轴线的方向为x轴正向,如图1—12所示。
.2.编程方式的选择:(1)绝对坐标方式与增量(相对)坐标方式①绝对坐标系所有坐标点的坐标值均从编程原点计算的坐标系,称为绝对坐标②增量坐标系坐标系中的坐标值是相对于刀具前一位置(或起点)来计算的,称为(相对)坐标。
增量坐标常用£,、形表示,与X、z轴平行且同向。
例1—1如图1—13中,O为坐标原点,A点绝对坐标为(D3,一L2),A点相对点的增量坐标为(U,W),其中U=D3一D2;W=一(L2一L1,)。
内孔数控车削加工(编程)教案
一、教学目标1. 了解内孔数控车削加工的基本概念和特点。
2. 掌握内孔数控车削加工的编程方法和技巧。
3. 能够独立完成内孔数控车削加工的编程和操作。
二、教学内容1. 内孔数控车削加工概述内孔加工的定义和分类内孔数控车削加工的特点和应用范围2. 内孔数控车削加工编程基础内孔加工的数控编程指令内孔加工的编程格式和步骤3. 内孔数控车削加工编程实例简单内孔加工编程实例复杂内孔加工编程实例4. 内孔数控车削加工操作要点内孔加工的刀具选择和安装内孔加工的切削参数设置内孔加工的加工质量和精度控制5. 内孔数控车削加工编程练习完成一定难度的内孔加工编程任务分析和解决内孔加工过程中出现的问题三、教学方法1. 讲授法:讲解内孔数控车削加工的基本概念、编程方法和操作要点。
2. 演示法:展示内孔数控车削加工的编程实例和操作过程。
3. 实践法:让学生亲自动手进行内孔数控车削加工编程和操作,提高实际操作能力。
四、教学资源1. 教材:内孔数控车削加工教材或相关资料。
2. 数控车床:用于实践教学的内孔数控车床。
3. 编程软件:用于编写内孔数控车削加工程序的软件。
五、教学评价1. 课堂问答:评估学生对内孔数控车削加工基本概念和编程方法的理解程度。
2. 编程练习:评估学生对内孔数控车削加工编程的掌握程度。
3. 操作考核:评估学生对内孔数控车削加工操作的熟练程度。
六、教学重点与难点1. 教学重点:内孔数控车削加工的基本概念和特点。
内孔数控车削加工的编程方法和技巧。
内孔数控车削加工操作的要点和注意事项。
2. 教学难点:内孔加工的数控编程指令的理解和运用。
复杂内孔加工编程实例的分析和操作。
内孔加工过程中质量问题和解决问题的方法。
七、教学进程安排1. 课时安排:总共安排15课时,其中包括课堂讲解、编程练习和操作考核。
2. 教学进程:第1-4课时:内孔数控车削加工概述和编程基础。
第5-8课时:内孔数控车削加工编程实例和操作要点。
第9-12课时:内孔数控车削加工编程练习和问题解决。
内孔数控车削加工教案
内孔数控车削加工教案教案:内孔数控车削加工一、教学目标1.了解内孔数控车削加工的基本概念和步骤。
2.学会使用CNC机床进行内孔数控车削加工。
3.培养学生的操作技能和安全意识。
二、教学内容1.内孔数控车削加工的基本概念和步骤。
C机床的操作和编程方法。
三、教学步骤步骤一:导入新课通过讲解内孔数控车削加工的基本概念,引起学生的兴趣和注意力。
步骤二:介绍内孔数控车削加工步骤1.准备工作:检查设备和工具的完好性。
2.选择合适的刀具和夹具,根据工件的要求设置车床参数。
3.安装工件和夹具,进行刀具装夹和刀具长度的调整。
4.进行刀具预调和零点设置,编写和输入数控程序。
5.进行内孔车削加工,控制车床进行车削操作。
6.加工结束后,进行工件的检验和测量。
步骤三:CNC机床的操作和编程方法1.了解CNC机床的基本结构和工作原理。
2.学习CNC机床的操作方法,包括开机、关机、急停等基本操作。
3.学习CNC机床的编程方法,包括手动编程和自动编程。
步骤四:操作实践让学生亲自操作CNC机床进行内孔数控车削加工,通过实践巩固所学内容,并培养学生的实际操作技能。
四、教学评价通过学生的实际操作和工件的质量来评价学生的学习结果,并进行相关的讲解和指导。
五、教学资源C机床2.刀具和夹具3.工件4.教学投影仪和PPT等。
六、教学注意事项1.安全第一,确保学生在操作过程中的安全。
2.严格按照操作步骤进行操作,提前做好准备工作。
3.运用现场演示、实践操作等多种教学方法,提高学生的学习效果。
七、教学延伸1.让学生进一步学习和了解数控技术的发展和应用领域。
2.开设相关的实践课程,提高学生的实际操作能力。
3.组织学生参观和参加相关的行业展览、比赛等活动,拓宽学生的视野和交流机会。
数控车床编程教案
数控车床编程教案教案:数控车床编程一、教学目标1.了解数控车床编程的基本概念和原理。
2.掌握数控车床编程的基本语法和常用指令。
3.能够独立进行简单的数控车床编程。
二、教学内容1.数控车床编程的概念和原理2.数控车床编程的基本语法和常用指令3.数控车床编程实例分析和编写三、教学过程1.导入(10分钟)通过提问和讨论,引导学生了解数控车床编程的概念和作用。
2.数控车床编程的基本语法和常用指令(30分钟)讲解数控车床编程的基本语法和常用指令,包括:-G代码:用于控制运动指令,如G00、G01等。
-M代码:用于控制辅助功能,如M03启动主轴、M05停止主轴等。
-T代码:用于选择刀具号。
-F代码:用于控制进给速度。
-S代码:用于控制主轴转速。
3.数控车床编程实例分析和编写(40分钟)通过实际案例分析和讲解,引导学生学会分析和编写数控车床程序。
实例包括:-面铣:通过分析面铣过程,学习如何编写相应的数控车床程序。
-镗孔:通过分析镗孔过程,学习如何编写相应的数控车床程序。
-外圆车削:通过分析外圆车削过程,学习如何编写相应的数控车床程序。
四、教学总结(10分钟)总结数控车床编程的要点和关键步骤,强调学生应掌握的基本知识和技能。
五、教学反馈通过课堂练习和作业,检查学生对数控车床编程的理解和掌握程度。
六、教学资源1.教学课件和案例分析材料。
2.计算机和数控车床编程软件。
七、教学评价通过对学生的课堂表现、练习和作业的评价,对教学效果进行评估和反思,并做出相应改进。
八、教学延伸1.组织学生进行实际操作,编写和调试数控车床程序。
2.进一步拓展学生对数控车床编程的理论知识和实际应用的学习。
3.组织学生参观数控车床加工现场,了解实际生产中数控车床编程的应用。
以上是关于数控车床编程的教案,希望能够帮助学生掌握数控车床编程的基本知识和技能,为日后的实际应用打下坚实的基础。
《数控车削编程与加工技术》课程标准
《数控车削编程与加工技术》课程标准学时:144学分:8适用专业及学制:三年制、数控技术应用、模具制造技术、全日制审定:机电技术教学部一、制定依据本课程是数控类专业核心课程。
本标准依据《中职国家专业教学标准》而制定。
二、课程性质《数控车削编程与加工技术》课程是以就业为导向,顺应现代职业教育教学制度的改革趋势,在数控技术应用专业开设的必修课。
该专业课程涉及数控车床的加工工艺、编程和操作核心,全面系统介绍车削加工技术基础、内外轮廓的加工、华中系统数车编程操作等方面知识。
三、课程教学目标本课程是中职数控类专业的一门专业课程。
其主要任务是以生产实践中的莞任务为项目构建课程体系,实现理论与实践的紧密结合。
围绕生产实际工作任务的需要,突出工作任务与知识的关联性,让学生在生产实践活动中学习知识,分析问题,增强课程内容与职业岗位能力要求的相关性,提高学生的学习积极性和主动性。
1.知识目标(1)能适应数控车床操作的工作、学习环境;(2)会手工编制加工阶梯轴的规范程序;(3)能较熟练运用数控车仿真系统或机床模拟仿真实现零件的模拟加工;(4)会车削带曲面轴类零件;(5)会数控车削轴上沟槽;(6)会数控车削普通内外螺纹;(7)能完成中等复杂轴套类零件的编程与加工;(8)能达到数控车中级工(国家职业资格四级)资格水平。
2.能力目标(1)本课程是操作性很强的,对于这种类型的课程,必须加强平时的练习,在重复操作练习中提高熟练程序,并掌握其中的操作原理;(2)能读懂零件图、能根据数控车床加工工艺文件选择、安装和调整数控车床常用刀具、能利用数控车床进行轮廓、螺纹、槽及孔的加工、能对数控机床进行日常的维护保养、上网查找相关资料、全面深入地掌握相关方法;(3)学会举一反三的方法,能在课外摸索一些新的加工工艺,并能学习使用。
3.素质目标(1)培养学生认真细致的学习态度和科学的求学态度,注重动手;(2)培养学生强烈的责任心和良好的敬业精神;(3)培养学生具有互助合作的精神。
- 1、下载文档前请自行甄别文档内容的完整性,平台不提供额外的编辑、内容补充、找答案等附加服务。
- 2、"仅部分预览"的文档,不可在线预览部分如存在完整性等问题,可反馈申请退款(可完整预览的文档不适用该条件!)。
- 3、如文档侵犯您的权益,请联系客服反馈,我们会尽快为您处理(人工客服工作时间:9:00-18:30)。
内孔数控车削加工(编程)教案
内孔数控车削加工教案
数控车床上孔加工工艺
很多零件如齿轮、轴套、带轮等,不仅有外圆柱面,而且有内圆柱面,在车床上加工内结构加工方法有钻孔、扩孔、铰孔、车孔等加工方法,其工艺适应性都不尽相同。
应根据零件内结构尺寸以及技术要求的不同,选择相应的工艺方法。
1.麻花钻钻孔
如图8-7-1,钻孔常用的刀具是麻花钻头(用高速钢制造) ,孔的主要工艺特点如下:
钻头的两个主刀刃不易磨得完全对称,切削时受力不均衡;钻头刚性较差,钻孔时钻头容易发生偏斜。
通常麻花钻头钻孔前,用刚性好的钻头,如用中心孔钻钻一个小孔,用于引正麻花钻开始钻孔时的定位和钻削方向。
麻花钻头钻孔时切下的切屑体积大,钻孔时排
屑困难,产生的切削热大而冷却效果差,使得刀
刃容易磨损。
因而限制了钻孔的进给量和切削速度,降低了钻孔的生产率。
可见,钻孔加工精度低(IT2~13)、表面粗糙度值大(Ra12.5),一般只能作粗加工。
钻孔后,可以通过扩孔、铰孔或镗孔等方法来提高孔的加工精度和减小表面粗糙度值。
2.硬质合金可转位刀片钻头钻孔
如图8-7-2,CNC车床通常也使用硬质合金可转位刀片钻头。
可转位刀片的钻孔速度通常要比高速钢麻花钻的钻孔速度高很多。
刀片钻头适用于钻孔直径范围为16~80mm的孔。
刀片钻头需要较高的功率和高压冷却系统。
如果孔的公差要求小于±0.05,则需要增加镗孔或铰孔等第二道孔加工工序,使孔加工到要求的尺寸。
用硬质合金可转位刀片钻头钻孔时不需要钻中心孔。
3.扩孔
扩孔是用扩孔钻对已钻或铸、锻出的孔进行加工,扩孔时的背吃刀量为0.85~4.5mm范围内,切屑体积小,排屑较为方便。
因而扩孔钻的容屑槽较浅而钻心较粗,刀具刚性好;一般有3~4个主刀刃,每个刀刃的切削负荷较小;棱刃多,使得导向性好,切削过程平稳。
扩孔能修正孔轴线的歪斜,扩孔钻无端部横刃,切削时轴向力小,因而可以采用较大的进给量和切削速度。
扩孔的加工质量和生产率比钻孔高,加工精度可达ITl0,表面粗糙度值为Ra6.3~3.2μm。
采用镶有硬质合金刀片的扩孔钻,切削速度可以提高2~3倍,大大地提高了生产率。
扩孔常常用作铰孔等精加工的准备丁序:也可作为要求不高孔的最终加工。
4.铰孔
铰孔是孔的精加工方法之一,铰孔的刀具是
铰刀。
铰孔的加工余量小(粗铰为O.15~0.35mm,精铰为0.05~0.15mm),铰刀的容屑槽浅,刚性好,刀刃数目多(6~12个),导向可靠性好,刀刃的切削负荷均匀。
铰刀制造精度高,其圆柱校准部分具有校准孔径和修光孔壁的作用。
铰孔时排屑和冷却润滑条件好,切削速度低(精铰2~5m /min),切削力、切削热都小,并可避免产生积屑瘤。
因此,铰孔的精度可达IT6~IT8;表面粗糙度值为Ra1.6~0.4μm。
铰孔的进给量一般为0.2~1.2mm/r,约为钻孔进给的3~4倍,可保证有较高的生产率。
铰孔直径一般不大于80 mm。
铰孔不能纠正孔的位置误差,孔与其他表面之间的位置精度,必须由铰孔前的加工工序来保证。
5.镗孔
镗孔一般用于将已有孔扩大到指定的直径,可用于加工精度、直线度及表面精度均要求较高的孔。
镗孔主要优点是工艺灵活、适应性较广。
一把结构简单的单刃镗刀,既可进行孔的粗加工,又可进行半精加工和精加工。
加工精度范围为ITl0以下至IT7~IT6;表面粗糙度值Ra为12.5μm至0.8~0.2μm。
镗孔还可以校正原有孔轴线歪斜或位置偏差。
镗孔可以加工中、小尺寸的孔,更适于加工大直径的孔。
镗孔时,单刃镗刀的刀头截面尺寸要小于被加工的孔径,而刀杆的长度要大于孔深,因而刀具刚性差。
切削时在径向力的作用下,容易产生变形和振动,影响镗孔的质量。
特别是加工孔径小、长度大的孔时,更不如铰孔容易保证质量。
因此,镗孔时多采用较小的切削用量,以减小切削力的影响。
8.7.2 数控车床上孔加工编程
1.中心线上钻、扩、铰孔加工编程
车床上的钻、扩、铰加工时,刀具在车床主轴中心线上加工。
即X值为0。
⑴主运动模式
CNC车床上所有中心线上孔加工的主轴转速都以G97模式,即每分钟的实际转数(r/min)来编写,而不使用恒定表面速度模式(CSS)。
⑵刀具趋近运动工件的程序段
首先将Z轴移动到安全位置,然后移动X轴到主轴中心线,最后将Z轴移动到钻孔的起始位置。
这种方式可以减小钻头趋近工件时发生碰撞的可能性。
N36 T0200 M42;
N37 G97 S700 M03;
N38 G00 Z5 M08;
N39 X0;
N40···
⑶刀具切削和返回运动
N40 G01 Z-30 F30;
图8-7-3工件端面啄式钻孔例图
N41 G00 Z2;
程序段N40为钻头的实际切削运动,切削完成后执行程序段N41,钻头将Z 向退出工件。
刀具的返回运动时,从孔中返回的第一个运动总是沿Z 轴方向的运动。
⑷啄式钻孔循环(深孔钻循环): ①啄式钻孔循环格式 G74 R ~
G74 Z ~ Q ~ F ~;
式中:R ~:每次啄式退刀量; Z ~:向终点坐标值(孔深);Q ~:Z 向每次的切入量。
②啄式钻孔(如图8-7-3所示):
在工件上加工直径为10 mm 的孔,孔的有效深度为60 mm 。
工件端面及中心孔已加工,程序如下:
O8701;
N10 T0505;(φ10麻花钻)
N20 G0 X0 Z3.S700 M3;
N30 G74.R1.; N40
G74.Z-60.Q8000 F0.1;
N50 G0 Z50;
N60 X100;
N70 M05;
N80 M30;
2.数控镗削内孔
数控车削内孔的指令与外圆车削指令基本相
同,但也有区别,编程时应注意以下方面:
①粗车循环指令G71、G73,在加工外径时余
量U为正,但在加工内轮廓时余量U应为负。
②若精车循环指令G70采用半径补偿加工,以刀具从右向左进给为例。
在加工外径时,半径补偿指令用G42,刀具方位编号是“3”。
在加工内轮廓时,半径补偿指令用G41,刀具方位编号是“2”。
③加工内孔轮廓时,切削循环的起点S、切出点Q的位置选择要慎重,要保证刀具在狭小的内结构中移动而不干涉工件。
起点S、切出点Q 的X值一般取与预加工孔直径稍小一点的值。
如图8-7-4,内轮廓加工编程示例:内径粗车循环:半径补偿精加工内形
G0 X19 Z5;(快进到内径粗车循环起刀点)……
G71 U1 R0.5;G0 G41 X19 Z5;(引入半径补偿)
G7l P10 Q20 U-0.5 W0.1 F150;G70 P10 Q20 F80;
N10 Gl X36;G40 G0 Z50 X100;
…………
N20 X19;……
数控车床上孔加工工艺编程实例
加工图8-7-4所示阶梯孔类零件,材料为45钢,材料规格为Ф50×50mm ,设外圆端面已加工完毕,要求按图纸要求加工该零件内结构。
1. 加工方法:
①选用φ3的中心钻钻削中心孔; ②钻φ20的孔; ③粗镗削内孔; ④精镗削内孔。
2. 程序编写:O8702
①φ3的中心钻(T01)G01钻削中心孔 ②φ20钻头(T02)钻削孔
O8702 G98;
G98;
M3 S2000 T0101; M3 S300 T0202; (换1号φ3的中心钻) (换2号φ20的钻头) G0 X0 Z5; G0 X0 Z5; G01 Z -6 F30; G74 R3.;
G04 P1000;
G74 Z-58.Q8000 F60
图8-7-4 孔类零件
G00 Z5;G0 Z50 X100;
G0 Z50 X100;M5;主轴停转
M5;主轴停转M0;程序暂停
M0;程序暂停
③内孔镗刀(T03)G71镗削内孔④内孔镗刀(T04)G70精镗内孔
G98;
M3 S800 T0303;G98;
G0 X19. Z5;M3 S1200 T0303;
G71 U1 R0.5;G0 G41 X19.5 Z5;
G7l P10 Q20 U-0.5 W0.1 F150;(快速进刀,引入半径补偿)
N10 G00 X36;G70 P10 Q20 F80;
G01 Z0;G40 G0 Z50 X100;
X30 Z-10;(快速进刀,引入半径补偿)
Z-32;M5;
G03 X24 Z-35 R3;M30;
N20 X19
G0 Z50 X100;
M5;
M0;。