铸造控制计划范例
铸造产品控制计划

铸造产品控制计划
一、质量管理体系
1.1定义
质量管理体系包括对质量控制和质量保证的系统安排、技术要求和质量保障流程,并且需要确定、持续改进和实施质量管理体系的管理体系。
1.2目的
本质量管理体系旨在建立一个能够确保铸造产品质量的技术体系,遵循相关的质量标准,为铸造产品的客户提供可信赖的质量。
1.3指令
(1)本质量管理体系的内容遵循国家相关的质量管理体系标准;
(2)所有参与铸造产品制造的工作人员都应按照本质量管理体系的规定完成工作,并负责保证质量的控制和保证;
(3)本工厂实施质量管理体系的总体负责人为生产经理,其下设有质量管理部门,责任人为质量管理部经理;
(4)本质量管理体系及其相关文件被包括在本工厂质量手册中。
二、质量控制
2.1原料
(1)实施原料质量检验,确保原料质量符合要求;
(2)设置原料质量检测体系,检测原料的物理化学性能,包括熔点、密度、强度等;
(3)建立原料的检验程序及质量控制计划。
2.2生产
(1)按照生产要求建立质量控制计划;(2)确定检验程序及检。
铸件质量控制计划

铸件质量控制计划引言概述:铸件是工业生产中常见的零部件之一,其质量直接影响到产品的性能和可靠性。
为了保证铸件的质量,制定一套科学合理的铸件质量控制计划是非常重要的。
本文将详细介绍铸件质量控制计划的内容和步骤。
一、材料选择1.1 材料性能要求:根据铸件的使用环境和要求,选择合适的材料。
包括强度、耐热性、耐腐蚀性等指标。
1.2 材料检验标准:制定材料的检验标准,包括化学成分、机械性能、金相组织等方面的检验要求。
1.3 材料供应商评估:对材料供应商进行评估,选择有资质、信誉好的供应商,确保材料的质量可靠。
二、模具设计与制造2.1 模具设计:根据铸件的形状和尺寸要求,进行模具的设计。
确保模具结构合理、易于制造和使用。
2.2 模具制造:制定模具制造的工艺流程,包括材料选择、加工工艺、热处理等环节。
确保模具的质量和寿命。
2.3 模具检验:对制造完成的模具进行检验,包括尺寸精度、表面质量、装配性能等方面的检验。
三、铸造工艺控制3.1 熔炼工艺控制:制定熔炼工艺参数,包括炉温、炉型、熔炼时间等。
确保熔炼过程中合金成分均匀、气体含量低。
3.2 浇注工艺控制:制定浇注工艺参数,包括浇注温度、浇注速度、浇注方式等。
确保铸件充型完整、无缺陷。
3.3 凝固过程控制:控制铸件的凝固过程,包括冷却速度、冷却方式等。
确保铸件的显微组织和性能符合要求。
四、铸件检验与评估4.1 尺寸检验:对铸件的尺寸进行检验,包括长度、宽度、高度等方面的测量。
确保铸件的尺寸精度符合要求。
4.2 表面质量检验:对铸件的表面质量进行检验,包括气孔、夹杂、裂纹等缺陷的检查。
确保铸件表面光洁、无明显缺陷。
4.3 性能评估:对铸件的力学性能、热处理效果等进行评估,确保铸件的性能符合要求。
五、质量记录与改进5.1 质量记录:建立完善的质量记录体系,包括材料检验记录、模具制造记录、铸造工艺参数记录等。
确保质量数据可追溯。
5.2 质量改进:根据铸件的质量问题和不良情况,及时采取措施进行改进,包括调整工艺参数、优化模具设计等。
压铸控制计划范例

压铸控制计划范例【背景】压铸是一种常用于生产大型、复杂零件的加工工艺。
该工艺使用高压将熔化金属注入压铸模具中,然后通过冷却和凝固来形成所需的零件。
为了确保产品质量,减少缺陷和增加生产效率,需要制定一份压铸控制计划。
【目标】该压铸控制计划的目标是确保生产的压铸零件符合规格要求,并提高产品质量和生产效率。
【内容】1.质量控制-制定合格品标准:明确压铸零件的尺寸、表面光洁度、材料硬度等质量要求。
-制定首件检验标准:确保生产出的第一件产品满足质量标准。
-制定过程控制标准:对压铸工艺中的各个步骤、参数进行监控和控制,确保产品质量稳定。
-制定末件检验标准:对生产出的每个压铸零件进行全面检验,确保产品质量符合要求。
2.设备维护-制定设备维护计划:定期对压铸设备进行保养和维护,确保设备正常运行,减少故障发生率。
-制定备用设备准备计划:在设备故障时,及时准备备用设备,避免生产中断。
-建立设备维修记录:记录设备维护和维修情况,为以后的维护提供参考。
3.员工培训-制定员工培训计划:定期培训压铸操作人员,提高其操作技能和质量意识。
-建设员工技能档案:记录员工培训情况和技能水平,为岗位调整和晋升提供依据。
-开展质量安全培训:加强员工的质量和安全意识,确保操作规范和安全生产。
4.数据分析-收集生产数据:定期收集压铸生产的相关数据,如生产数量、不良品数量等。
-进行数据分析:通过对数据的统计和分析,找出生产中的问题和改进措施。
-制定改进措施:根据数据分析结果,制定相应的改进措施,优化生产流程和工艺。
5.过程改进-建立问题反馈机制:鼓励员工提出问题和改进意见,并建立相应的反馈机制。
-进行改进措施评估:对提出的改进措施进行评估和实施,确保改进效果。
-持续改进:不断进行过程改进,提高压铸生产质量和效率。
【执行】该压铸控制计划由相关部门和人员执行,包括质量部、生产部、设备维护人员和培训人员。
各部门和人员要按照计划的要求进行工作,并定期进行评估和改进。
铸件质量控制计划
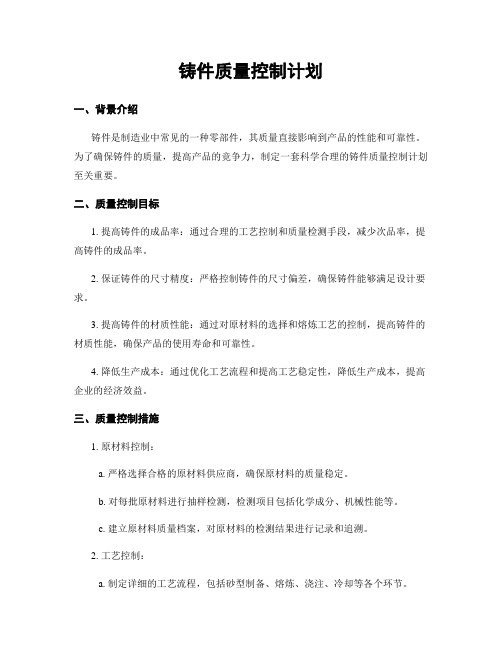
铸件质量控制计划一、背景介绍铸件是制造业中常见的一种零部件,其质量直接影响到产品的性能和可靠性。
为了确保铸件的质量,提高产品的竞争力,制定一套科学合理的铸件质量控制计划至关重要。
二、质量控制目标1. 提高铸件的成品率:通过合理的工艺控制和质量检测手段,减少次品率,提高铸件的成品率。
2. 保证铸件的尺寸精度:严格控制铸件的尺寸偏差,确保铸件能够满足设计要求。
3. 提高铸件的材质性能:通过对原材料的选择和熔炼工艺的控制,提高铸件的材质性能,确保产品的使用寿命和可靠性。
4. 降低生产成本:通过优化工艺流程和提高工艺稳定性,降低生产成本,提高企业的经济效益。
三、质量控制措施1. 原材料控制:a. 严格选择合格的原材料供应商,确保原材料的质量稳定。
b. 对每批原材料进行抽样检测,检测项目包括化学成分、机械性能等。
c. 建立原材料质量档案,对原材料的检测结果进行记录和追溯。
2. 工艺控制:a. 制定详细的工艺流程,包括砂型制备、熔炼、浇注、冷却等各个环节。
b. 对每个工艺环节进行严格的控制,确保每个环节的操作符合标准要求。
c. 建立工艺参数记录表,对每次生产过程中的工艺参数进行记录和分析。
3. 设备控制:a. 对铸造设备进行定期维护和保养,确保设备的正常运行。
b. 对设备进行校准,保证设备的测量精度。
c. 建立设备使用记录,对设备的使用情况进行监控和分析。
4. 检测控制:a. 制定全面的检测方案,包括外观检测、尺寸检测、材质性能检测等。
b. 对每批铸件进行全面检测,确保产品的质量稳定。
c. 建立检测记录,对每次检测结果进行记录和分析。
5. 不良品处理:a. 对发现的不良铸件进行分类和记录,分析不良原因。
b. 制定不良品处理方案,包括返修、报废等措施。
c. 定期对不良品处理情况进行评估和改进。
四、质量控制计划执行1. 制定详细的质量控制计划,包括质量控制目标、控制措施、执行责任人等。
2. 将质量控制计划下发到各个相关部门,并进行培训和宣贯。
压铸控制计划范例
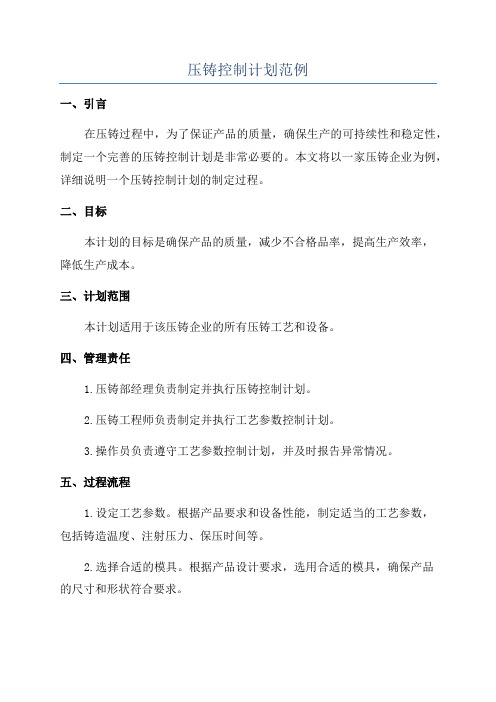
压铸控制计划范例一、引言在压铸过程中,为了保证产品的质量,确保生产的可持续性和稳定性,制定一个完善的压铸控制计划是非常必要的。
本文将以一家压铸企业为例,详细说明一个压铸控制计划的制定过程。
二、目标本计划的目标是确保产品的质量,减少不合格品率,提高生产效率,降低生产成本。
三、计划范围本计划适用于该压铸企业的所有压铸工艺和设备。
四、管理责任1.压铸部经理负责制定并执行压铸控制计划。
2.压铸工程师负责制定并执行工艺参数控制计划。
3.操作员负责遵守工艺参数控制计划,并及时报告异常情况。
五、过程流程1.设定工艺参数。
根据产品要求和设备性能,制定适当的工艺参数,包括铸造温度、注射压力、保压时间等。
2.选择合适的模具。
根据产品设计要求,选用合适的模具,确保产品的尺寸和形状符合要求。
3.准备材料。
选用合适的铸造材料,并按照配方准确称量,防止材料的异相反应和杂质的混入。
4.进行模具预热。
通过对模具进行适当的预热,确保铸造过程中温度的均匀分布。
5.铸造操作。
将准备好的铸造材料倒入模具中,控制注射温度、注射压力和注塑时间。
6.保压操作。
在注射结束后,进行保压操作,以保证铸件的密实性和尺寸精度。
7.铸件取出。
待冷却后,将铸件从模具中取出,并进行修边、打磨等工艺处理。
8.检测和检验。
对铸件进行尺寸、外观、材料成分等多个方面的检测和检验,确保产品符合设计和客户要求。
9.记录和分析。
对每一次生产过程进行记录和分析,及时发现问题并采取纠正措施。
六、控制方法1.控制工艺参数。
通过严格控制工艺参数,如温度、压力、时间等,确保产品的质量和尺寸稳定。
2.定期保养设备。
对压铸设备进行定期保养和维护,确保设备的可靠性和稳定性。
3.培训操作员。
对操作员进行培训,提高其操作技能和质量意识,降低人为错误。
4.定期检测和校准检测设备。
对检测设备进行定期检测和校准,确保测试数据的准确性和可靠性。
5.定期召开质量会议。
通过召开质量会议,总结经验,分享问题,促进团队间的沟通和合作。
铸件质量控制计划
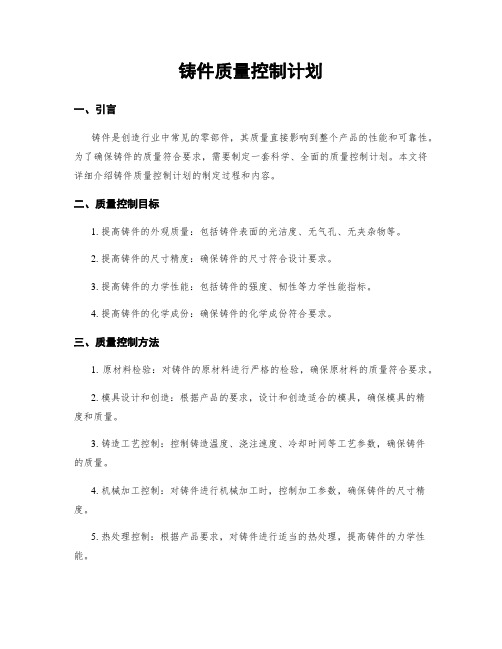
铸件质量控制计划一、引言铸件是创造行业中常见的零部件,其质量直接影响到整个产品的性能和可靠性。
为了确保铸件的质量符合要求,需要制定一套科学、全面的质量控制计划。
本文将详细介绍铸件质量控制计划的制定过程和内容。
二、质量控制目标1. 提高铸件的外观质量:包括铸件表面的光洁度、无气孔、无夹杂物等。
2. 提高铸件的尺寸精度:确保铸件的尺寸符合设计要求。
3. 提高铸件的力学性能:包括铸件的强度、韧性等力学性能指标。
4. 提高铸件的化学成份:确保铸件的化学成份符合要求。
三、质量控制方法1. 原材料检验:对铸件的原材料进行严格的检验,确保原材料的质量符合要求。
2. 模具设计和创造:根据产品的要求,设计和创造适合的模具,确保模具的精度和质量。
3. 铸造工艺控制:控制铸造温度、浇注速度、冷却时间等工艺参数,确保铸件的质量。
4. 机械加工控制:对铸件进行机械加工时,控制加工参数,确保铸件的尺寸精度。
5. 热处理控制:根据产品要求,对铸件进行适当的热处理,提高铸件的力学性能。
6. 检测与测试:使用适当的检测和测试方法,对铸件进行质量检验,确保铸件的质量符合要求。
四、质量控制流程1. 原材料检验流程:a. 对原材料进行外观检查,检查是否有明显的缺陷。
b. 进行化学成份分析,确保原材料的化学成份符合要求。
c. 进行物理性能测试,包括硬度、抗拉强度等指标的测试。
2. 模具设计和创造流程:a. 根据产品要求,设计模具的结构和尺寸。
b. 创造模具,并进行精度检验,确保模具的精度符合要求。
3. 铸造工艺控制流程:a. 设定铸造温度、浇注速度、冷却时间等工艺参数。
b. 进行铸造过程监控,记录关键参数,确保铸件的质量。
4. 机械加工控制流程:a. 设定机械加工参数,包括切削速度、进给量等。
b. 进行机械加工过程监控,记录加工参数和尺寸精度。
5. 热处理控制流程:a. 根据产品要求,选择适当的热处理工艺。
b. 进行热处理过程监控,确保铸件的力学性能符合要求。
铸造控制计划范例
核心小组 Core Team
零件名/ 描述 Part Name/ Description
合金铝锭
供应商/ 工厂 Supplier/ Plant 有限公司
零件/ 工序 编号Part / Process Number
工序名 / 工作描述 Process Name / Operation
Description
热电偶测试仪
100% 每炉
《铸铝锭生产卡》
取样温度
720-740℃
热电偶测试仪
100% 每炉
氢气含量
Z 0.15-0.20ml/100g
测氢仪
1次 每炉
《铸铝锭生产卡》
精炼温度
Z 730-750℃
热电偶测试仪
100% 每炉
炉内处理
保温炉
渣滓含量
精炼时间
Z 20-25分钟 Z 铝水表面无明显渣滓
时钟 目测、K模试验
目测核对
样品 Sample
容量 Size
频率 Freq.
1次 每批
验证供应商材质报告 1次 每批
化学元素分析
1次 每批
验证供应商材质报告 1次 每批
磅秤
100% 每炉
光谱分析仪
1次 每炉
热电偶测试仪
100% 每炉
自动温控仪
连续 每炉
目测、K模试验
100% 每炉
防错
控制方法
prevent inaccuracy
客户质量批准/日期(如要求) Customer Quality Approval/Date (If Req'd)
其他批准/日期(如要求) Other Approval/Date (If Req'd)
铸造生产过程的质量控制
口不平,银白色,细晶粒,有时在中心有些缩松,三角试片尖角部位的白口 消失或仅有1-2mm,说明球化孕育正常。
铸件材质检测
金相显微镜
直读光谱仪
通过辅助试块、光谱试样来验证生产铸件材质
6.铸件的漆膜质量检验
用涂-4检验油漆的浓度16-18S,画格仪来检测漆膜的附着 力大于I ,漆膜测厚仪测量漆膜厚度30-40UM
• 2.4 球化处理反应时间大于50秒。用取样勺从铁水表面200㎜以下取适量铁 水浇注三角试样和光谱试块,待三角试块冷却至暗红色放入水中冷却,打断 观察球化效果
• 2.5 球化后的铁水加除渣剂,迅速扒渣,扒渣完成后,加覆盖剂。 • 2.5 球化孕育之后,球化质量判断:球化后三角试片两侧及顶部有凹陷,断
案例2(内部质量)
解决方案:
1.提高铁水的纯净度(球 化包、炉内、球化扒渣)
2.使用陶瓷泡沫过滤片
该铸件为制动缸体,浇 注重量84kg,浇注时间 13-16S.
问题描述:
铸件在加工时,渣 眼废品太多
铸件质量的稳定,取决于每个生产过程质量的可控
备注:由于铸造过程的特殊性(如原材料、造型设备、操作方式的差 异),下面出现的技术参数仅供参考。
离合器壳体 玉米机箱体
HT250
差(制)动器壳 HT250
1.9--2.3 3.1-3.3 1.7-2.0 3.3-3.5 1.9-2.2
≤0.20 ≤0.030 ≤0.015 0.8-1.0 ≤0.12 ≤0.12 0.4-0.6 ≤0.12 ≤0.12
Ti ≤ 0.030
5.2铁水的球化及浇注
FBO造型
3.砂芯的制作
冷芯盒射芯机
射芯机大林砂50-100目芯 砂,芯子在保证合适的强 度时,要尽量降低芯子的 发气量;注意铸件飞翅的 发生(浇注时芯子出现裂 缝)
铸造产品控制计划
铸造产品控制计划1.引言铸造工艺是一种通过将熔化的金属或合金注入到预先制作好的模具中,并在冷却固化后获得所需形状和尺寸的方法。
铸造是一种常见的制造工艺,用于生产各种各样的产品,包括汽车零件、机械零件、建筑材料等。
为了确保铸造产品的质量和可靠性,需要制定一份详细的铸造产品控制计划。
2.目标和范围本铸造产品控制计划的目标是确保铸造产品在制造过程中符合设计要求和质量标准。
本计划适用于所有进行铸造生产的环节,包括原材料采购、模具制作、熔炼、铸造、冷却固化、清理和检验等。
本计划还将涉及到设备和工艺参数的控制,员工培训和监督等。
3.质量管理体系3.1质量目标确保铸造产品在制造过程中的合格率达到99%。
提高生产效率,每小时产量达到设定的目标值。
减少铸造产品的不良率,控制不良数量在每月2%以内。
3.2质量控制流程3.2.1原材料采购确保采购的原材料符合设计要求和标准规范。
建立供应商评估体系,对每个供应商进行定期评估和审核。
3.2.2模具制作制定模具制作工艺和参数,确保模具质量和寿命。
建立模具保养和维修计划,定期检查和维护模具。
3.2.3熔炼严格控制熔炼过程中的温度和时间,确保金属或合金的成分符合要求。
定期检查和校准熔炼设备,确保精确控制熔炼参数。
3.2.4铸造严格按照工艺要求进行铸造,确保产品形状和尺寸的准确性。
定期检查和校准铸造设备,确保每个铸件的质量和可靠性。
3.2.5冷却固化控制冷却速度和固化时间,确保产品的力学性能和表面质量。
建立冷却固化工艺参数数据库,用于指导生产操作和质量分析。
3.2.6清理和检验对铸造产品进行定期清理,确保产品表面干净和光滑。
对每个铸件进行非破坏性检测和尺寸检验,判断铸件的质量是否合格。
3.2.7员工培训每位员工需要接受相关培训,了解铸造的工艺和质量要求。
定期进行员工技能考核,确保员工的操作和检验水平符合要求。
3.2.8监督和审核建立内部审核制度,定期对各个环节进行审核和评估。
建立质量问题反馈机制,及时处理和解决质量问题。
低压铸造控制计划
低压铸造控制计划低压铸造控制计划一、背景介绍低压铸造是一种常用的金属铸造工艺,通过在一定温度和压力下,将熔融金属注入模具中,冷却硬化后得到所需的铸件。
具有成本低、生产效率高、品质稳定等优点,在汽车、机械、航空等领域得到了广泛应用。
二、产品要求根据客户需求,我公司需要生产铝合金汽车零部件,产品要求以轻量化、高强度、耐腐蚀等为主要特点。
三、生产工艺低压铸造生产工艺主要包括以下几个步骤:1. 原料准备:选用适当的铝合金材料,并按照比例进行混合。
2. 加热熔炼:将铝合金材料加热至熔化状态,通常采用电炉进行加热。
3. 模具准备:根据产品的形状和尺寸,选择合适的模具,并对模具进行预处理,以防止粘铸等问题。
4. 注入铸造:将熔化的铝合金注入到模具中,控制注入时间、速度和压力等参数。
5. 冷却硬化:铝合金在模具中冷却后逐渐硬化,待完全硬化后,将铸件取出进行后续处理。
四、关键控制参数为了确保产品质量,需要对低压铸造过程进行严格的控制。
下面是几个关键控制参数的介绍:1. 温度控制熔炼过程中需要控制熔融铝合金的温度,确保熔化彻底,避免太高或太低的温度对铸件质量产生不利影响。
2. 压力控制在注入铸造过程中,需要控制注入的压力,过高的压力可能会导致气孔、缺陷等问题,过低的压力则可能影响成形效果。
3. 注入时间控制注入时间的长短对成形效果有较大影响,过短可能导致铸件不完整,过长则可能导致铸件过度填充,影响产品质量。
4. 冷却时间控制在铸造过程中,需要控制冷却时间,以确保铝合金充分冷却硬化,避免产生内应力和变形等问题。
五、控制计划基于以上关键控制参数,制定以下低压铸造控制计划:1. 检查原料和模具准备情况,确保原料质量良好,并检查模具的准备情况,保证模具的完整性和准确性。
2. 对熔融铝合金进行温度控制,控制温度在合适的范围内,确保熔融彻底。
3. 在注入铸造过程中,控制注入的压力,确保合适的压力范围内进行注入,并进行记录。
4. 控制注入时间,根据产品的要求和模具的情况,确定合适的注入时间,并进行记录。
- 1、下载文档前请自行甄别文档内容的完整性,平台不提供额外的编辑、内容补充、找答案等附加服务。
- 2、"仅部分预览"的文档,不可在线预览部分如存在完整性等问题,可反馈申请退款(可完整预览的文档不适用该条件!)。
- 3、如文档侵犯您的权益,请联系客服反馈,我们会尽快为您处理(人工客服工作时间:9:00-18:30)。
序号 No.
特性 Characteristics
产品
Product
过程 Process
特殊 特性 分 类
Special Char. Class
产品 / 过程规范 / 公差 Product / Process Specification /
Tolerance
来料检验入库 备料
规格型号 化学成分
机械性能 成分
核心小组 Core Team
零件名/ 描述 Part Name/ Description
合金铝锭
供应商/ 工厂 Supplier/ Plant 有限公司
零件/ 工序 编号Part / Process Number
工序名 / 工作描述 Process Name / Operation
Description
材料清单一致 满足国家标准 满足国家标准 满足国家标准 按照《铸铝锭生产卡》
化学成分
熔炼温度
Z 满足用户标准 Z 740-780℃
渣滓含量
炉温
1050℃ 铝水表面无明显渣滓
创建日期 (Orig.)
修订日期 Date (Rev.)
客户工程批准/日期(如要求) Customer Engineering Approval/Date (If Req'd)
客户质量批准/日期(如要求) Customer Quality Approval/Date (If Req'd)
其他批准/日期(如要求) Other Approval/Date (If Req'd)
方法 Methods
评价 / 测量技术 Evaluation / Measurement
Technique
目测核对
样品 Sample
容量 Size
频率 Freq.
1次 每批
验证供应商材质报告 1次 每批
化学元素分析
1次 每批
验证供应商材质报告 1次 每批
磅秤
100% 每炉
光谱分析仪
1次 每炉
热电偶测试仪
100% 每炉
自动温控仪
连续 每炉
目测、K模试验
100% 每炉
防错
控制方法
prevent inaccuracy
Control Method
入库单
《原材料检验报告》
《化学成分分析单》
《原材料检验报告》
《铸铝锭生产卡》
《铸铝锭生产卡》
熔炼
熔炼炉
设备检查 加复盖剂
20-30Kg/炉
磅秤
100% 每炉
加分离剂
20-30Kg/炉
100% 每炉
时间
加入分离剂后3-5分钟扒渣 时钟
100% 每炉
加硅温度
Z 800-850℃
100% 100%
每炉 每炉
《铸铝锭生产卡》
静置时间
Z 20-25分钟
时钟
100% 每炉
《铸铝锭生产卡》
在线处理
流槽、除气装 置、过滤装置
WW-PLUS-FR-02-01-E,CH / Rev 07 (01-April-2004)
氢气含量 渣滓含量
加复盖剂
转子速度 气流量
10Kg Z 0.15-0.20ml/100g Z 铝水表面无明显渣滓 Z 300-400转/分 Z 2立方米/小时
供应商/工厂批准/日期 Supplier/Plant Approval/Date
供应商编码 Supplier Code
其他批准日期/日期(如需要) Other Approval/Date (If Req'd)
机器, 设备, 夹具, 生 产工具
Machine, Device,Jig,Tools
For Mfg.
Page 1 of 2
铸造
铸造机
成品检验
包装入库 全尺寸全性能检查
外观
铸造温度 外观 化学成分 机械性能 针孔度 硬度 规格型号 外观、性能
无缺料、溢出、裂纹、表面无 明显气孔、缩孔、渣滓
目测、K模试验
Z 700-725℃
热电偶测试仪
无缺料、溢边、裂纹、表面无 明显气孔、缩孔、渣滓
目测
Z 满足用户标准
光谱分析仪
Z 满足用户标准
委外
Z 满足用户标准
委外
Z 满足用户标准
委外
标识清楚
目测
满足用户标准
计量器具
100%
100% 5% 1次 1次 1次 1次
100% 1次
每批
每炉 每炉 每炉 每炉 每炉 每炉 每炉 每年
《铸铝锭生产卡》 《试验报告》 《试验报告》 《试验报告》
全尺寸检验报告
报废
重新调试 报废,全检 报废 报废 报废 报废 重新标识 隔离评审
磅秤 测氢仪 目测、K模试验 转速器 流量计
100% 1次 100% 1次 1次
每炉 每炉 每炉 开机 开机
每次生产 《铸铝锭生产卡》 前检查石 墨转子与 叶片接头 是否漏气
、堵塞
应对计划及纠正措施
Reaction
Plan
退货 退货 退货 退货 重新调配 重新调试 重新调试 重新调试 继续除渣
重新调试 重新调试 重新调试 重新调试 重新调试 调整参数 重新调试 重新调试 继续除渣 重新调试 重新调试 调整参数 继续除渣 重新调试 重新调试
WW-PLUS-FR-02-01-E,CH / Rev 07 (01-April-2004)
Page 2 of 2
热电偶测试仪
100% 每炉
《铸铝锭生产卡》
取样温度
720-740℃
热电偶测试仪
100% 每炉
氢气含量
Z 0.15-0.20ml/100g
测氢仪
1次 每炉
《铸铝锭生产卡》
精炼温度
Z 730-750℃
热电偶测试仪
100% 每炉
炉内处理
保温炉
渣滓含量
精炼时间
Z 20-25分钟 Z 铝水表面无明显渣滓
时钟 目测、K模试验
控制计划 Control Plan
样件
Prototype 控制计划编 号 Control 零件号/ 最新更改水平
Part Number/ Latest
Change Level
试生产 Pre-launch
QF/CP—001
√
生
产 主要联系人/电话
Production Key Contact/Phone