质量功能展开技巧
FMEA与CP的开发方法与技巧

FMEA与CP的开发方法与技巧FMEA(潜在失效模式及后果分析——(Potential)Failure Mode and Effect Analysis)默菲定律:所有可能出错的地方都将会出错!FMEA的定义:FMEA是在产品设计阶段和过程设计阶段,对构成产品的系统、子系统、零件(产品),对构成过程的各工序逐一进行分析,找出所有潜在失效模式,并分析其可能的后果,从而预先采取必要的措施,以提高产品的质量和可靠性的一种系统化的活动。
一、FMEA的目的,学习目的:掌握FMEA的概念和运用时机,发现、评价产品/过程中潜在的失效及该失效的后果,确定能够避免或减少这些潜在失效发生的措施。
FMEA是对确定设计或过程必须做哪些事情才能使顾客满意这一过程的补充。
FMEA是一种风险分析的方法,是一种设计评审的活动。
所有的FMEA都关注设计,无论是产品设计或者是过得设计。
FMEA文件是设计(产品、过程)输出的结果。
二、什么是 FMEA ?●FMEA 是先期质量策划中评价潜在失效模式及其起因的一种工具●依照其发生失效的风险优先排列,并采取行动排除或降低其发生的方法●为未来使用和持续改进提供文件化的预防经验/方法●FMEA自身并不是问题的解决者,它通常与其它问题解决的工具联合使用,“FMEA提出问题解决的时机并不是解决问题”●将问题扼杀在摇篮之中。
三、FMEA 的特点和目的特点:——FMEA开始于一个过程所有功能的定义(功能驱动)——FMEA必须由小组进行,以确保其有效(团队力量)1)失效还未产生,可能发生但不一定会发生;2)在产品或过程设计阶段前开始;3)小组活动,小组由各种有经验和专业知识的人构成;4)分析的工具使用专用表格,作为动态文件使用和更改;5)核心是缺陷预防;6)贯穿整个过程、产品和服务周期;7)动态的、文件化的、系统的小组活动。
目的:(主要目的:筛选着重点!)——识别关键特性和重要特性。
——聚焦于产品和过程问题的消除,防止问题再次发生。
质量管理方法
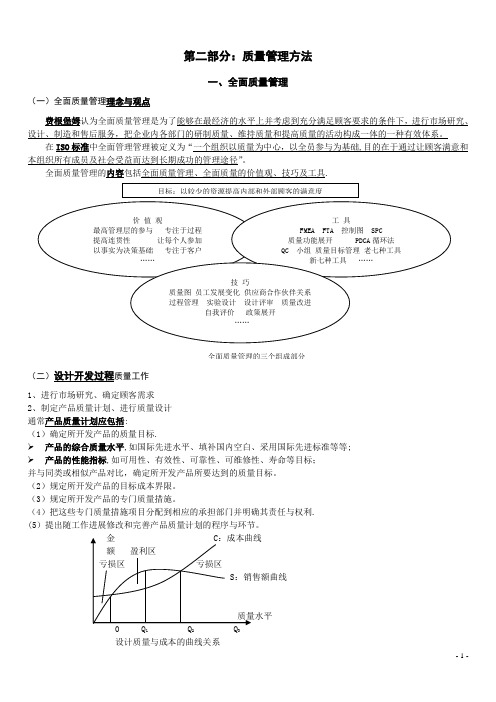
第二部分:质量管理方法一、全面质量管理(一)全面质量管理理念与观点费根堡姆认为全面质量管理是为了能够在最经济的水平上并考虑到充分满足顾客要求的条件下,进行市场研究、设计、制造和售后服务,把企业内各部门的研制质量、维持质量和提高质量的活动构成一体的一种有效体系。
在ISO标准中全面管理管理被定义为“一个组织以质量为中心,以全员参与为基础,目的在于通过让顾客满意和本组织所有成员及社会受益而达到长期成功的管理途径”。
全面质量管理的内容包括全面质量管理、全面质量的价值观、技巧及工具.全面质量管理的三个组成部分(二)设计开发过程质量工作1、进行市场研究、确定顾客需求2、制定产品质量计划、进行质量设计通常产品质量计划应包括:(1)确定所开发产品的质量目标.➢产品的综合质量水平,如国际先进水平、填补国内空白、采用国际先进标准等等;➢产品的性能指标,如可用性、有效性、可靠性、可维修性、寿命等目标;并与同类或相似产品对比,确定所开发产品所要达到的质量目标。
(2)规定所开发产品的目标成本界限。
(3)规定所开发产品的专门质量措施。
(4)把这些专门质量措施项目分配到相应的承担部门并明确其责任与权利.(5)提出随工作进展修改和完善产品质量计划的程序与环节。
12 3设计质量与成本的曲线关系3、设计评审评审的目的在于确定提供评审的设计结果是否与设计要求一致,以及在进入下一阶段之前是否应做出改变,它也应确定在提出进一步的对策之前,用于下一阶段的文件是否足够。
同时它也是为了能及时发现和纠正设计中存在的缺陷与不足。
4、试制、试验与鉴定通过试制、试验与鉴定,可以取得大量质量情报.根据这些质量情报,一则可以确认设计意图与质量目标的实际符合程度,二则可以反馈给设计人员进一步完善设计。
5、设计更改的控制——设计变更会一直伴随整个新产品开发的过程。
6、产品图样和设计文件的发放控制(三)制造过程的质量工作1、人员准备2、物资和能源准备3、装备准备4、工艺准备5、计量仪器准备6、设计组织生产方案7、质量控制系统设计,质量职责确认8、验证工艺及装备(四)销售和使用过程的质量工作(1)在销售过程中进行市场调查,收集市场信息,确定用户和市场对产品需求;(2)搞好产品流通过程中的质量职能,作好产品交付;(3)搞好产品宣传介绍、推销以及广告活动,完成售前和售后服务.(五)服务质量管理1、生产与服务的区别生产与服务主要区别一览表2、服务开发的质量管理服务企业的质量管理一直未受到足够重视,主要原因有:①相当多的服务企业规模较小,资源相当有限;②一些公共服务部门竞争性较低,没有创新的动力③还有一些服务行业受政府管制较多,服务企业可能没有进行服务创新的机会④最重要的一点是由于服务的创新要比一般产品的创新更加困难3、服务设计质量管理-—服务设计是服务质量体系中的重要因素。
QFD质量功能展开对产品设计创新的要求

QFD质量功能展开强调跨部门、跨领域的协作,有助于打破企业内部的部门壁垒,实现资 源的优化配置和高效利用。
QFD质量功能展开简介
01
定义
QFD质量功能展开(Quality Function Deployment)是一种系统性的
方法,旨在将客户需求转化为具体的产品设计要素、零部件特性、工艺
• 绿色环保:环保意识的提高使得绿色设计成为产品设计的重要趋势。QFD质 量功能展开可以引入绿色环保理念,将环保因素纳入顾客需求和产品设计中, 推动企业实现可持续发展。
• 拓展应用领域:目前QFD质量功能展开主要应用于制造业领域,未来可以进 一步拓展至服务业、医疗、教育等领域。建议企业积极探索QFD质量功能展 开在不同领域的应用,推动其更广泛的实践和发展。
。
02
QFD质量功能展开在产品 设计中的应用
确定顾客需求和期望
01
调研与分析
通过市场调研、用户访谈、问 卷调查等方法,收集顾客对产
品的需求和期望。
02
需求整理
对收集到的需求进行整理、分 类和优先级排序,形成清晰的
需求列表。
03
需求转化
将顾客需求和期望转化为可衡 量的指标,如性能、可靠性、
安全性等。
跨部门协作不畅
传统流程中,设计、研发、生产等部门之间的沟通协作不够顺畅 ,容易导致信息传递失真和资源浪费。
缺乏持续改进机制
传统流程缺乏对产品设计方案的持续改进机制,难以适应市场和 客户需求的变化。
QFD质量功能展开在流程中的嵌入
1 2
需求分析阶段
通过QFD方法,将市场和客户需求转化为具体的 设计要求和指标,为后续设计提供明确的方向。
设计方案制定阶段
OTS和PVS解释[技巧]
![OTS和PVS解释[技巧]](https://img.taocdn.com/s3/m/fc994931bc64783e0912a21614791711cc797902.png)
OTS和PVS解释OTS是指首次样件,然后会有个PVS首批样件。
再接下来的是2TP/2天试生产验收。
接下来才是正式订单及量产。
OTS是工程认可,PVS是质量部负责JIS(Just In Sequence),简单地说就是JIT及时供货的一种特殊而极端的状态。
JIT的基本思想可以被概括为:在需要的时候,按需要的量生产并提供所需要的产品,也就是通过对库存的管理,达到无库存或库存量最小的状态,为此而出现了包括“看板”在内的一系列具体方法。
对照JIT,JIS可以说是对库存的要求达到了极端。
通俗地讲,整车厂要什么部件,供应商就送什么部件,当然实际送货时是按一定的频次送货。
通常这些零部件价值较高,体积较大,再加上整车厂对其保质期有一定的要求,整车厂一般不存放库存。
为此,一些供应商不惜通过设置一定的成品库存来应对整车厂的要求,也就是采取“批量生产,顺序供货”的模式,这种模式在一定程度上缓解了供应商的“难堪”,但却积蓄着较高的浪费和风险。
SEPIC(single ended primary inductor converter) 是一种允许输出电压大于、小于或者等于输入电压的DCDC变换器。
输出电压由主控开关(三极管或MOS管)的占空比控制。
这种电路最大的好处是输入输出同极性。
尤其适合于电池供电的应用场合,允许电池电压高于或者小于所需要的输入电压。
比如一块锂电池的电压为3V ~ 4.2V,如果负载需要3.3V,那么SEPIC电路可以实现这种转换。
另外一个好处是输入输出的隔离,通过主回路上的电容C1实现。
同时具备完全关断功能,当开关管关闭时,输出电压为0V。
QFD法(Quality Function Deployment,质量功能展开),也称质量功能配置、质量机能展开、质量功能部署QFD法简介您的公司在引进一项对于公司的生存和发展至关紧要的新产品或新服务时,是否面临战略性的选择问题?可以设想有一种方法,在您尝试之前就能告诉您该项目的潜在功能,能够帮助你降低从开发设计到正式生产的30%时间,而且能够提高产品质量和降低项目投入成本。
质量功能展开
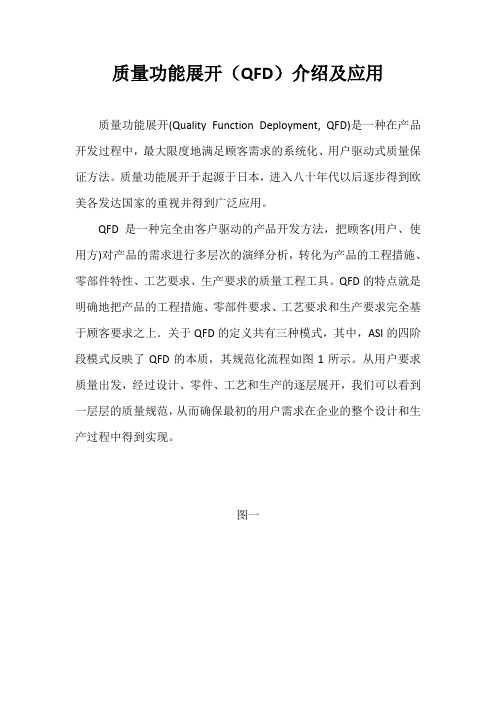
图一
质量功能展开(QFD)的作用 有形的效益:大大减少研制时间;有效地减少后期的设计更改; 在开发计阶段就开始降低成本;提高设计可靠性;降低企业的管理成 本。无形的效益:使顾客更加满意;健全企业质量保证活动;QFD 数 据库:可用于同一系列或类似的其他产品上:开发设计和生产工序中 各种技能技巧诀窍的积累。改进产品规划的基础。
冰箱的质量屋
工程 措施 顾 客 需 求 制冷速度快 噪音小 省电 可靠度高 重 要 度 5 3 3 4
压 缩 机 性 能 5*
线 管 材 质
功
本 产 品
改 进 后
国 内 对 手
国 际 对 手
率
9 7 5 7 研 发 新 压 缩 机
1 1 3 7 采 用 优 质 材 料
Hale Waihona Puke 1 3 4 4 5 1 4 4 4 5 9 4 5 4 5 1 4 4 4 5 供 0.73 0.84 0.80 1.00 需 小 于 市场竞争能力指数 M 1 KW
6 下一级展开的技术需求的选择 按照 QFD 瀑布展开模型, 冰箱规划矩阵质量屋中的技术需求, 要进 一步转换为零件规划矩阵。 一般地, 不是照搬式地直接将本级质量 屋的技术需求移到下一级质量屋的用户需求栏目中, 需要筛选。 筛 选需遵循下列原则: 技术需求重要度越大, 越应考虑将其转换到下一级质量屋。 若用户 对某项技术需求现状不满意,则要考虑将其转换到下一级质量屋。 相互间具有强相关, 尤其是强负相关的技术需求应考虑转换到下一 级质量屋。 7 具体计算
技术竞争能力指数: 本产品(109 × 3 + 45 × 4 + 39 × 5) ÷ 5 × (109 +
45 + 39)=0.73 改进后(109 × 4 + 45 × 5 + 39 × 5) ÷ 5 × (109 + 45 + 39)=0.89
质量功能展开方法详解

质量功能展开方法详解质量功能展开(Quality Function Deployment,简称QFD)是一种通过将客户需求和企业的设计、制造、服务等各个环节紧密联系起来的方法。
通过分析市场需求,将顾客的期望转化为产品或服务的特征,并将这些特征逐步地传导至企业内部的各个层面,以实现高质量和高满意度的目标。
本文将详细讲解质量功能展开方法的步骤和应用技巧。
一、质量功能展开的基本步骤1. 识别和收集顾客需求:首先,需要通过市场调研等方法,识别和收集顾客的需求和期望。
这些需求可以来自市场调查、用户反馈、竞争对手的产品分析等渠道。
2. 确定顾客需求的重要性:在收集到大量需求后,需要通过市场调研数据的分析,确定各个需求的重要性。
可以使用数量化的方法,如加权平均法、层次分析法等。
3. 将顾客需求转化为特征:将顾客的需求从抽象的描述转化为具体的产品或服务特征。
要确保这些特征具备详细的可操作性,便于后续环节的具体设计和实施。
4. 建立特征与工程特性的关联:将产品或服务特征与不同层面的工程特性进行关联。
这可以通过召开跨学科小组会议,将市场需求与技术、设计等方面相结合,确保关联的准确性和实用性。
5. 执行展开矩阵:根据特征与工程特性的关联,形成展开矩阵。
展开矩阵可以清晰地展示各个层面的特征和特性之间的关系,为后续的产品设计和过程改善提供依据。
6. 制定改进计划:根据展开矩阵的结果,制定产品或服务的改进计划。
将产品或服务的特征和特性转化为具体的操作指导,确保质量和满意度的提升。
二、质量功能展开的应用技巧1. 利用工具和方法:在执行质量功能展开过程中,可以借助一些工具和方法来提高效率和准确性。
比如层次分析法、加权平均法可以帮助确定需求的重要性;展开矩阵可以用电子表格软件或专业软件进行绘制。
2. 引入多方参与:质量功能展开需要跨学科、跨职能的合作和协调。
引入多个部门和团队的参与,确保各个环节的顾客需求得到有效地传导和实现。
3. 及时调整和改进:质量功能展开是一个持续改进的过程,需要根据实际情况及时调整和改进。
如何实现全过程质量管理
如何实现全过程质量管理课程描述:全过程质量管理是全面质量管理的一个重要组成部分。
全过程质量管理,顾名思义,就是要求对整个产品生命过程进行质量控制。
那么,产品生命过程包括哪些环节?又怎样来对这些环节进行质量管理呢?本课程将结合实际案例,为您一一阐述实现全过程质量管理的方法与技巧。
解决方案:他山之石,可以攻玉!虽然不同行业或不同企业在实现全过程质量管理时,都会有一些差异,但万变不离其宗!下面我们从实战经验中给大家总结一些方法流程,以便大家参考借鉴!好的。
所谓全过程质量管理,就是对贯穿产品整个生命周期始终的各个过程进行质量管理。
一般来说,有以下几个环节:第一环节:产品前期策划质量管理第二环节:产品生产过程质量管理第三环节:产品客户投诉质量管理第四环节:产品持续改善质量管理产品前期策划质量管理。
首先要确立产品开发项目,做好客户对产品的需求转化,并确定产品的关键特性。
其次要做好样件试制质量管理,做好FMEA(失效模式故障分析)和样件质量验证。
再次,做好产品试生产阶段的质量管理,一方面要进行工艺验证;另一方面是确定好关键工序,评估出致命因子,并根据致命因子设置关键工序。
最后,要做好量产阶段质量管理,对量产工艺和质量控制计划进行修正,同时确定关键工序过程能力(CPK)。
产品生产过程质量管理包括三个方面内容。
第一个方面是原材料控制,包括原材料总体不良率的控制和批次不良率的控制,不可忽略其一。
第二个方面是生产过程质量控制。
这里再讲生产过程控制另外两点,一个是关键检验工序的控制,主要是控制关键检验工序的不良率和检出率;另一个是特殊工序的控制。
第三个方面是检验控制,在进行产品检验时,要严格依照检验标准,根据实际情况选择正确的检验手段。
产品客户投诉质量管理,一个是客户投诉的处理流程,另一个是纠正和预防措施的制定。
产品持续改善质量管理,主要包括两个方向,一个是对内的质量改善,另一个是对外的质量改善,即客户需求改善。
对内质量改善要在做好两点,即材料改善,以及作业流程和方法的改善。
QFD培训资料
QFD的常用术语
顾客需求
顾客对产品或服务的需求和期 望,通常用问卷、访谈等方式 收集。
关键工序
生产过程中对产品质量影响较 大的工序,通常需要重点控制 和管理。
质量特性
产品或服务的质量要求,通常 用指标或标准来衡量。
技术要求
为实现顾客需求而制定的技术 标准、规范和要求。
质量控制
通过各种方法和技术对生产过 程进行控制,以保证产品或服 务的质量符合要求。
VS
详细描述
该公司在产品开发过程中,运用QFD将客 户需求转化为设计要求,确保产品符合客 户需求。通过QFD的运用,产品质量得到 了显著提升,客户满意度也大幅提高。
案例二:某企业运用QFD提升产品竞争力
总结词
运用QFD优化产品设计,提高产品性能和 降低成本,增强市场竞争力。
详细描述
该企业运用QFD对产品进行优化设计,提 高产品性能的同时降低成本。通过这种方 式,企业成功地提高了产品的市场竞争力 ,获得了更多的市场份额。
QFD培训资料
2023-11-07
目 录
• QFD概述 • QFD的核心思想 • QFD的实操技巧 • QFD的案例分析 • QFD的总结与展望 • 附录:QFD常用工具与表格
01
QFD概述
QFD的定义
质量功能展开(Quality Function Deployment,QFD)是一种将顾客需求转化 为产品和服务的质量要求的方法。
如何进行技术实现分析
01
02
03
技术可行性评估
评估产品或服务的技术可 行性,包括技术难度、开 发周期、成本等方面。
技术实现方案
根据产品或服务的特性, 制定技术实现方案,包括 硬件设计、软件开发、测 试等方面。
《质量管理实战:方法、技巧与工具一本就够》笔记
《质量管理实战:方法、技巧与工具一本就够》阅读记录目录一、书籍概述 (2)1.1 作者介绍及出版信息 (3)1.2 书籍核心内容概览 (3)二、质量管理的核心方法与技巧 (4)2.1 质量管理体系建立与执行 (6)2.1.1 质量管理的基础理念 (7)2.1.2 质量管理体系的构建步骤 (8)2.1.3 质量管理体系的执行与监控 (9)2.2 质量管理的核心技巧 (11)2.2.1 问题分析与解决技巧 (12)2.2.2 质量改进与创新方法 (13)2.2.3 团队建设与沟通协作 (15)三、质量管理的实战案例分析 (16)3.1 案例分析概述及学习方法 (17)3.1.1 案例分析的重要性 (18)3.1.2 实战案例学习的方法与步骤 (19)3.2 实战案例分析 (20)3.2.1 案例一 (21)3.2.2 案例二 (23)3.2.3 案例三 (23)四、质量管理的常用工具与运用 (24)4.1 质量管理的常用工具介绍 (26)4.1.1 PDCA循环管理法 (27)4.1.2 流程图分析法 (28)4.1.3 统计质量管理方法 (29)4.2 工具的实际应用与案例分析 (30)4.2.1 PDCA循环管理法的应用实例 (32)4.2.2 流程图分析法在问题解决中的应用 (33)4.2.3 统计质量管理方法在质量控制中的应用 (35)五、质量管理的挑战与对策探讨 (36)一、书籍概述《质量管理实战:方法、技巧与工具一本就够》是一本全面介绍质量管理的实用指南,旨在帮助读者在竞争激烈的市场中提高产品和服务的质量,从而提升企业竞争力。
本书以实战为导向,通过丰富的案例分析和实用的技巧和方法,使读者能够在短时间内掌握质量管理的核心理念和工具。
书籍首先介绍了质量管理的概念和重要性,然后详细阐述了质量管理的三大过程:质量策划、质量控制和质量改进。
在质量策划部分,本书强调了明确质量目标和制定相应的质量要求的重要性,以确保产品和服务能够满足顾客需求。
运用质量功能展开构建血站质量屋
运用质量功能展开构建血站质量屋王婧;何勖;胡慧颖;朱明【摘要】从管理工程角度出发,尝试运用质量功能展开(QFD)方法,构建血站质量屋.运用鱼骨图分析血站服务质量影响因素,细分血液采集、血液标本检测、血液使用环节服务对象的需求与期望,依次构建血站质量屋“左墙”、“天花板”、“屋顶”、“房间”、“右墙”和“地板”,为血站提高服务水平、实施改进措施提供方法参考.【期刊名称】《中国卫生质量管理》【年(卷),期】2016(023)003【总页数】3页(P100-102)【关键词】QFD;血站;服务;质量屋【作者】王婧;何勖;胡慧颖;朱明【作者单位】中国医学科学院/北京协和医学院输血研究所四川成都610052;中国医学科学院/北京协和医学院输血研究所四川成都610052;中国医学科学院/北京协和医学院输血研究所四川成都610052;中国医学科学院/北京协和医学院输血研究所四川成都610052【正文语种】中文First-author's address Institute of Blood Transfusion,Chinese Academy of Medical Sciences and Peking Union MedicalCollege,Chengdu,Sichuan,610052,China血站服务质量对整个输血服务具有重要影响。
《血站质量管理规范》要求,血站须开展顾客满意度调查来测评献血服务质量。
质量功能展开(Quality Function Deployment,QFD)是由日本质量专家水野滋和赤尾洋二首先提出的。
QFD是一种由传统产品的设计方式向现代设计方式进行的转变,即由传统设计到试制再到调整,转变为主动的、预防型的设计产品与开发。
这种将系统工程思想运用到产品的设计、开发和研制的全过程,就是把顾客的要求和期望展开到产品设计中去,并最终将产品的功能结合到产品研发过程中,综合取得顾客满意。
- 1、下载文档前请自行甄别文档内容的完整性,平台不提供额外的编辑、内容补充、找答案等附加服务。
- 2、"仅部分预览"的文档,不可在线预览部分如存在完整性等问题,可反馈申请退款(可完整预览的文档不适用该条件!)。
- 3、如文档侵犯您的权益,请联系客服反馈,我们会尽快为您处理(人工客服工作时间:9:00-18:30)。
“令人兴奋的质量”线处于横轴上 方,也在顾客的期望质量上方,代表着超 越顾客期望的质量水平。令人兴奋的质 量充分体现着以顾客为中心和创新的成 果,它已经达到了魅力质量的程度。 但是,今天令人兴奋的质量在明天 就可能是基本质量。市场竞争的压力将 促使着商家不断超越顾客日益增长的期 望。
•
第一层次
• ◇市场占有率持续下降; • ◇潜在的客户与市场有待开发; • ◇过多的救火作业,例如重新设计,大幅方案 修改; • ◇部门间沟通欠佳,问题常发生在灰色界面地 带; • ◇无合理的资源分配; • ◇作业过程中缺乏明确且合理的需求的惊喜
惊喜 兴奋
顾客的 潜在需求
质 量 创 新
Quality Creation
现在至将来
魅力质量:满足顾客潜在的需求使产品或服务 达到意想不到的质量,顾客产生愉悦的效果 。
(1)无关心质量/需求
童年的Jim和Mary Mary要搬家了, 来跟Jim告别。 “没有人过家家了, 不过,看我的手枪, 啪啪!”
主要内容:
一、QFD 概述 二、质量功能展开的四个阶段 三、QFD 原理与方法
一、QFD 概述
1、QFD的概念
2、QFD产生和发展 3、QFD的作用 4、QFD的效果 5、QFD的应用时机
一、QFD概述
1、质量机能展开(QFD)的概念
QFD是把顾客或市场的需求转化为 产品的设计要求、零件特性、工艺要求、 生产要求的多层次的演绎分析方法。
卡诺(Kano)模型
满意度
令人兴奋的 质量
竞争压力
顾客满意区域
期望质量 0 顾客不满意区域 基本质量 质量
卡诺模型是著名质量专家狩野纪昭先生提出的, 它揭示了顾客满意与质量的关系。 卡诺模型表明,顾客对任何商品都有最基本质 量要求,他们认为商品具备基本质量是理所当然的, 就像电冰箱能使水变成冰,移动电话能使人清晰地 听到对方讲话一样。如果这些基本质量没有达到, 顾客肯定不会满意。 “期望质量”是一条过原点的直线,代表着顾 客对商品的明确要求。如电冰箱要耗电低、噪音小; 移动电话要待机时间长、对人体无辐射。卡诺模型 表明期望被满足得越多,顾客的满意度越高。
◇降低设计成本
◇提高顾客满意度
◇增强企业竞争力 ◇优化企业资源配置
• • • • •
QFD思想:“需求什么”和“怎样 来满足”,在这种对应形式下顾客的需 求不会被曲解,产品的功能不会有遗漏 和冗余,避免功能过剩或功能不足,实 现了人力和物力资源的优化配置。
如何减少未满足的客户需求 , 避免过度 研发 ?
3
4
期望质量:具备该质量要素感到满意,不具备该质量要素就会不满。
(4)当然质量/需求
又20年过去了
Jim习惯了和Mary的生活, 一切变得那么自然。 家里永远有一个温柔的妻 子和温热的饭菜在等他。
当然质量:具备该质量要素感到是理所当然的,不具备该质量要素就会不满。
3、QFD的作用
◇减少设计更改 ◇缩短研发周期
丰田应用QFD后,成本降低1/3,开发周 期缩短一半。 克莱斯勒从设计到制造,包括拧紧螺母 的工序,全方位地采用QFD,在短期内开发 出价格为8975美元的彩虹(NEON)车。
菲亚特公司用于Cascade车的开发设计。 1990年又用于汽车选型评价,在节约时间上 获得了“戏剧性效果”。
5、QFD的应用时 机 • ◇顾客抱怨;
2、QFD产生和发展
QFD首先出现于20世纪60年代的日本, 70年代初在三菱重工有限公司所属的神户造 船厂首次应用。80年代中期传入北美,并开 始用于服务业。经过美、日企业及有关专家 的努力,QFD方法得到了不断地完善和发展。 近年来,QFD方法引起了我国企业的 注意,并被逐步引入到企业管理中。
满足顾客的基本需求
符合 技术标准
基本 需求
质 量 控 制
Quality Control
1950年代
理所当然质量:满足顾客最基本的质量要 求,致力于生产符合技术标准的产品。
第二层次
满足特定的顾客需求
顾客 满意
特定的 顾客需求
质 量 管 理
Quality Management
1970年代
期望质量:满足客户提出的要求,以 “顾客满意”为目标。
质 量 功 能 展 开 (QFD) Quality Function Deployment
企业竞争的演变 降 低 80年代 成 本 提 高 质 量
顾客
70年代
90年代
服 后 售 快 鱼
务 慢 鱼
世 纪 初
21
创新
企业通过对市场需求的快速反应, 由大鱼吃小鱼转变为快鱼吃慢鱼。
随着市场竞争的日趋激烈,企业只有 迅速、准确地把握市场需求,用较短的时 间开发出低成本、高质量的产品,才能在 竞争中立于不败之地。在众多的产品开发 方法中,QFD正是提高质量、促进创新、 增强企业核心竞争力的理想方法。
无关心质量:无论具备还是不具备该质量要素,都不被关心,可忽略不计。
(2)魅力质量/需求
20年后
Jim偶遇Mary,Mary 优雅的气质深深吸引了Jim, Jim觉得世界从此 变得更阳光。
魅力质量:具备该质量要素感到满意,不具备该质量要素也不会不满。
(3)期望质量/需求
又过了几年
1 2
Jim和Mary结婚了, 两个人开始形 影不离的生活,不 允许哪怕一天不在 一起厮守。
QFD是一种顾客驱动的产品开发方 法,按照顾客的需求和偏好来设计产品。
质量功能展开的过程
顾客世界 技术世界
顾 客 需 求
设 计 要 求
零 件 特 性
工 艺 特 征
生 产 要 求
质量功能展开体现了以市场为方向, 以顾客需求为产品研发唯一依据的指导思 想。它使产品的全部研发活动由顾客或市 场需求来驱动,从而保证了产品的市场竞 争力,提升产品开发的成功率。
4、QFD的效果(美国乔治.佩瑞总结)
• ☆有形效益
• • • • • ①研发周期缩短30%-60%; ②减少后期的设计更改40%-60%; ③在开发设计阶段就降低成本20%-40%; ④提高设计可靠性; ⑤降低管理成本。
•
☆无形效益:
①顾客更加满意; ②健全企业质量保证活动; ③QFD数据库可用于同一系列或类似产品,是开 发设计和生产工序中各种技能、诀窍的积累; ④改进产品规划的基础,产品更具竞争优势; ⑤改进部门间的协作与联系; ⑥提高了企业开发设计人员的水平。