炼钢转炉冶炼低碳钢脱氧合金化工艺优化精编版
炼钢转炉冶炼低碳钢脱氧合金化工艺优化
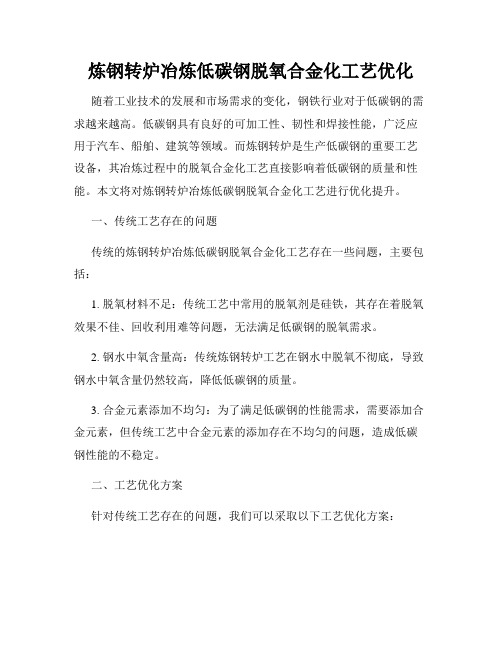
炼钢转炉冶炼低碳钢脱氧合金化工艺优化随着工业技术的发展和市场需求的变化,钢铁行业对于低碳钢的需求越来越高。
低碳钢具有良好的可加工性、韧性和焊接性能,广泛应用于汽车、船舶、建筑等领域。
而炼钢转炉是生产低碳钢的重要工艺设备,其冶炼过程中的脱氧合金化工艺直接影响着低碳钢的质量和性能。
本文将对炼钢转炉冶炼低碳钢脱氧合金化工艺进行优化提升。
一、传统工艺存在的问题传统的炼钢转炉冶炼低碳钢脱氧合金化工艺存在一些问题,主要包括:1. 脱氧材料不足:传统工艺中常用的脱氧剂是硅铁,其存在着脱氧效果不佳、回收利用难等问题,无法满足低碳钢的脱氧需求。
2. 钢水中氧含量高:传统炼钢转炉工艺在钢水中脱氧不彻底,导致钢水中氧含量仍然较高,降低低碳钢的质量。
3. 合金元素添加不均匀:为了满足低碳钢的性能需求,需要添加合金元素,但传统工艺中合金元素的添加存在不均匀的问题,造成低碳钢性能的不稳定。
二、工艺优化方案针对传统工艺存在的问题,我们可以采取以下工艺优化方案:1. 优化脱氧剂的选择:传统的硅铁脱氧剂可以通过其他脱氧剂进行替代,例如铝、锰等。
这些脱氧剂具有良好的脱氧效果和易回收利用的特点,可以提高低碳钢的质量。
2. 加强脱氧过程控制:通过提高脱氧剂的加入量和延长脱氧时间,确保炉料中的氧含量完全脱氧。
可以采用自动控制系统,实时监测钢水中氧含量,调整脱氧剂的加入量,实现钢水的有效脱氧。
3. 合金元素均匀添加:采用先进的合金元素添加技术,确保合金元素的均匀分布。
可以利用真空脱气设备将合金元素均匀加入钢水中,或者采用复合脱氧剂,使脱氧剂和合金元素同时添加,提高低碳钢的合金化效果。
4. 优化工艺参数:通过对炉温、转炉容量、吹氧时间等工艺参数的优化调整,提高低碳钢的冶炼效果。
可以利用计算机模拟技术对工艺参数进行优化设计,以实现低碳钢冶炼过程的最佳效果。
三、优化方案的效果及推广通过实施上述工艺优化方案,可以显著提高炼钢转炉冶炼低碳钢脱氧合金化的效果,进一步提升低碳钢的质量和性能。
转炉炼钢脱氧工艺的优化方法分析

12Metallurgical smelting冶金冶炼转炉炼钢脱氧工艺的优化方法分析牟贝成(天津荣程联合钢铁有限公司,天津 300350)摘 要:在炼钢过程中,转炉炼钢脱氧方式应用越来越多样化,而且钢液脱氧效果控制同样也是炼钢过程的重要内容,能够确保整个钢产品质量不受影响。
本文根据以往工作经验,对转炉炼钢脱氧工艺内容进行总结,并从沉淀脱氧工艺优化、脱氧方式的优化、脱氧工艺优化前后效果对比三方面,论述了转炉炼钢脱氧工艺的优化方法分析,希望对相关工作能够起到一定的帮助作用。
关键词:转炉;炼钢脱氧工艺;沉淀脱氧中图分类号:TF713.5 文献标识码:A 文章编号:11-5004(2020)23-0012-2 收稿日期:2020-12作者简介:牟贝成,生于1984年,男,汉组,山东省潍坊市人,助理工程师,本科,研究方向:钢水冶炼、浇注及钢坯轧制。
随着社会经济发展形式的转变,钢铁行业同样也需要实现创新,引进一些新的工艺,控制好产品的生产成本,促使产品质量得到本质性提升。
站在转炉炼钢角度来说,脱氧工艺领域之中一直存在问题,所以说,想要真正实现工艺的全面优化,应采用高效的钢液脱氧处理措施,让炼钢成本中的脱氧成本得到全面控制,确保钢产品质量稳步上升,为相关企业发展创造有利条件。
1 转炉炼钢脱氧工艺实际转炉炼钢过程中,能够实现生铁中碳元素的部分氧化,最终形成化学和物理性质较高的钢,进而完成整个冶炼过程。
反观炼钢液,内部氧气的存在形式为溶解氧以及非金属杂物形式,主要产生自吹氧炼钢和原料等环节之中。
想要将钢中的硫和磷等元素控制到钢种所需的目标值,则需要大量的氧气或者主要通过氧化反应,因此,氧化反应的产生显得十分重要,人们可以通过氧化合物出现,将更多的杂质析出。
但同时钢液中的含氧量也会迅速提升,相关工作人员需要进行脱氧处理,即使这样在晶界附近,还是会析出氧化亚铁,这对于连铸坯凝固组织结构及稳定性极为不利。
如果无法实现全面的脱氧处理,容易导致钢塑性大幅下降,甚至还会出现热脆情况,致使钢铁出现氧化现象,进而在钢铁之中混入氧化物,降低钢产品的力学性能。
炼钢转炉冶炼低碳钢脱氧合金化工艺优化

一、项目基本情况成果登记号:二、项目简介三炼钢供CSP低碳钢种主要为SPHC、SPHCZ,均属于铝镇静钢,年产在180万吨左右。
原来的低碳钢脱氧合金化工艺如下:1、使用铝块进行脱氧、使用中碳锰铁进行合金化。
2、具体加入方法在出钢前加入铝块,出钢1/3后加入中碳锰铁合金化。
近年来随着炼钢成本压力的增加,以及合金降成本的要求,现对低碳钢脱氧合金化工艺进行了优化。
随着转炉底吹快换技术的使用,使转炉底吹系统在整个炉役期都处于良好的状态,转炉底吹搅拌效果有了稳定的保证。
转炉冶炼低碳钢时保证了脱碳效果的快速、稳定。
冶炼低碳钢钢水碳控制能力有了较大的提高,杜绝了钢水碳脱不下去、搅拌效果差导致的钢水碳含量成分不均匀等现象的出现,为使用碳粉代替部分铝进行预脱氧工艺以及使用高碳锰铁代替中碳锰铁进行很进化合金化工艺的推行,提供了基础保障。
措施如下:1、出钢前期使用碳粉进行预脱氧,降低铝制品的消耗。
2、使用低价的高碳锰铁代替中碳锰铁进行合金化,高碳锰铁在出钢前期首先加入,随后加入碳粉,利用钢水中的氧脱除高碳锰铁中的碳,减少低碳钢增碳。
3、以铝粒代替铝块进行脱氧,便宜对铝制品加入量进行控制。
在出钢后期加入铝粒进行深脱氧并对锰进行还原。
由于铝制品脱氧剂用量降低。
钢水中氧化铝夹杂减少,增加钢水洁净度。
实施后锰合金消耗吨钢降低元。
铝制品消耗吨钢降低元。
2、详细科学技术内容1、原正常脱氧工艺在转炉冶炼低碳钢脱氧合金化工艺未优化之前,原来的低碳钢脱氧合金化工艺使用其缺点如下:1、由于铝锭体积较大,加入包中不易熔化,出钢时漂浮在钢液 面上,常常发生烧损现象造成浪费消耗增加,还造成了钢水中Al 2O 3夹杂的增多, 对钢水的浇铸和钢材的成品性能产生不利的影响。
且有白烟冒出造成环境污染。
2、钢水铝含量不均匀,炉后钢包样酸容铝波动大,成分代表性差,给精炼处 理造成一定的困难。
统计了 6个月的炉后钢包样酸容铝含量其结果如图3、为了防止钢水增碳使用中碳锰铁进行合金化,成本比较高。
转炉冶炼脱氧合金化方案优化设计

3. School of Materials Science and Engineering, North China University of Science and Technology, Tangshan 063210, China)
M 冶金冶炼 etallurgical smelting
转炉冶炼脱氧合金化方案优化设计
周会玲1,张 茜2,韩新月3,刘维姗1,陈丽梅2
(1. 华北理工大学经济学院,河北 唐山 063210 ;2. 华北理工大学冶金与能源学院,河北 唐山 063210 ;
3. 华北理工大学材料科学与工程学院,河北 唐山 063210)
摘 要 :近年来,我国金属冶炼生产流程工艺进步幅度显著提高,脱氧合金化是冶炼过程中的重要工艺环节,其关键在
于如何在优化合金配料。首先,根据合金收得率公式得出 C 和 Mn 元素的历史收得率,建立基于因子分析的收得率影响
因素模型得出影响 C 和 Mn 元素收得率的综合指标。然后,建立 C 和 Mn 元素收得率与影响因素的多元线性回归方程,
ZHOU Hui-ling1, ZHANG Qian2, HAN Xin-yue3, LIU Wei-shan1, CHEN Li-mei2
(1.School of Economics, North China University of Science and Technology , Tangshan 063210, China;
根据有关数据,并结合相关资料可以看出,可以通过焦 增碳剂和碳化硅(55%)以及其他合金料含金属元素量 [1], 结合其高炉合金液体反应的化学方程式,计算出碳元素的合 金加入量 GC, 代入公式(1)中,得到脱氧合金化时碳元素的 历史收得率散点图,C 的历史收得率为 85% 左右,同理得出 Mn 的历史收得率为 90% 左右。 1.2 模型的求解
探讨炼钢生产中转炉炼钢脱氧工艺
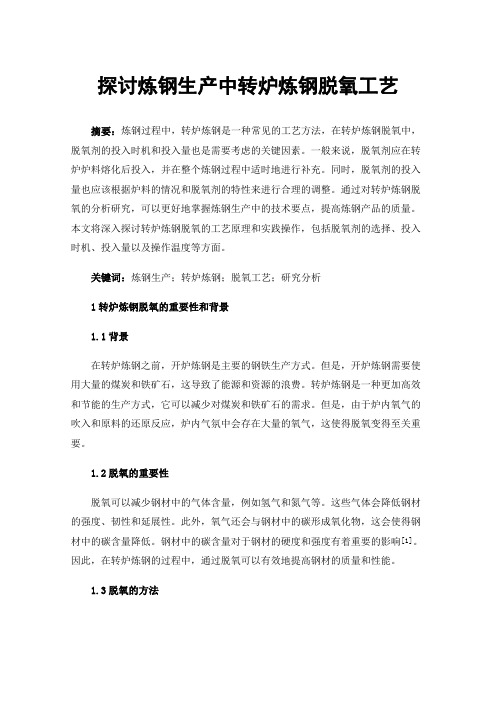
探讨炼钢生产中转炉炼钢脱氧工艺摘要:炼钢过程中,转炉炼钢是一种常见的工艺方法,在转炉炼钢脱氧中,脱氧剂的投入时机和投入量也是需要考虑的关键因素。
一般来说,脱氧剂应在转炉炉料熔化后投入,并在整个炼钢过程中适时地进行补充。
同时,脱氧剂的投入量也应该根据炉料的情况和脱氧剂的特性来进行合理的调整。
通过对转炉炼钢脱氧的分析研究,可以更好地掌握炼钢生产中的技术要点,提高炼钢产品的质量。
本文将深入探讨转炉炼钢脱氧的工艺原理和实践操作,包括脱氧剂的选择、投入时机、投入量以及操作温度等方面。
关键词:炼钢生产;转炉炼钢;脱氧工艺;研究分析1转炉炼钢脱氧的重要性和背景1.1背景在转炉炼钢之前,开炉炼钢是主要的钢铁生产方式。
但是,开炉炼钢需要使用大量的煤炭和铁矿石,这导致了能源和资源的浪费。
转炉炼钢是一种更加高效和节能的生产方式,它可以减少对煤炭和铁矿石的需求。
但是,由于炉内氧气的吹入和原料的还原反应,炉内气氛中会存在大量的氧气,这使得脱氧变得至关重要。
1.2脱氧的重要性脱氧可以减少钢材中的气体含量,例如氢气和氮气等。
这些气体会降低钢材的强度、韧性和延展性。
此外,氧气还会与钢材中的碳形成氧化物,这会使得钢材中的碳含量降低。
钢材中的碳含量对于钢材的硬度和强度有着重要的影响[1]。
因此,在转炉炼钢的过程中,通过脱氧可以有效地提高钢材的质量和性能。
1.3脱氧的方法转炉炼钢中有两种主要的脱氧方法,即硅脱氧和铝脱氧。
硅脱氧是最常用的方法,它通过在炉内加入硅来将氧气与硅反应,从而减少炉内氧气含量。
硅脱氧可以有效地减少氧气含量,但同时也会增加钢材中硅的含量。
铝脱氧则是一种更加高效的脱氧方法,它可以将氧气与铝反应,从而减少氧气含量,同时不会增加钢材中其他元素的含量。
铝脱氧可以生产出更加纯净的钢材。
2氧化铝脱氧法在转炉炼钢中的应用2.1背景在传统的转炉炼钢过程中,气氛中存在大量的氧气,这会使钢中存在过多的气体,如氮气、氧气和氢气等。
这些气体会导致钢中的气孔和夹杂物增多,从而降低钢的质量和性能。
炼钢生产中转炉炼钢脱氧工艺

炼钢生产中转炉炼钢脱氧工艺炼钢生产中转炉炼钢脱氧工艺摘要:由于钢铁行业之间的竞争越发激烈,使得各个钢铁企业逐渐增强了对生产成本以及产品质量的控制,怎样运用先进技术工艺来提升产品质量,减少投入成本成为了现阶段钢铁企业提升行业竞争力的重点。
在转炉炼钢的实际生产过程中,氧气的产生是必然的,因此我们需要先了解氧对炼钢生产以及钢产品带来的危害,并掌握脱氧的有效方式,再对脱氧工艺予以有效运用与完善,以此来提升钢液脱氧处理的实际效果。
这样就能够在确保钢产品质量的基础上,减少投入成本,让炼钢生产能够安全、高效地进行。
关键词:炼钢;转炉;脱氧工艺1?炼钢过程中的质量影响因素分析炼钢过程中要进行质量和设备的控制,炼钢各个环节都要进行原料的供给以及操作条件的合理组织等等,以此让炼钢的基本要素达到要求。
在炼钢过程中对炼钢质量形成影响的主要因素有钢炉,本文主要是从转炉的背景下进行研究分析的,氧气转炉中的氧气含量以及铁水的处理等等,因此以下主要是对氧气的存在对钢液产生的影响以及处理办法进行研究分析,旨在提升钢铁的强度和质量。
2?氧在炼钢中的产生以及危害分析在钢液当中,氧气一般是以一种非金属夹杂物的形式存在,有的也是以溶解氧气的方式存在,氧基本来自于原料和吹氧炼钢的生产过程中。
无论是哪一种,炼钢的方式方法要想除去其中的一些化学杂质,如碳、磷、硅、锰等等元素就需要使用其中的氧气,产生一种氧化反应,让氧气和相关的杂质之间有效的结合在一起,由此产生氧化合物,让杂质被析出。
钢液中氧的存在是不可避免的,因此在吹氧炼钢的过程中,要伴随着钢液中氧化和杂质含量的降低对钢液当中氧气的含量会有提升性的促进作用,如果钢液中的氧气没有经过有效的处理,氧含量非常高的钢液在凝固的过程中就会和已有的钢液发生反应,结晶,并且出现氧化亚铁,这种氧化亚铁物质在钢液中存在,铸坯被破坏,对钢产品的质量会产生直接性的影响,严重还会出现变形的现象,有热脆产生,还可能会让钢铁出现进一步的氧化现象。
转炉冶炼低碳钢脱氧工艺的改进
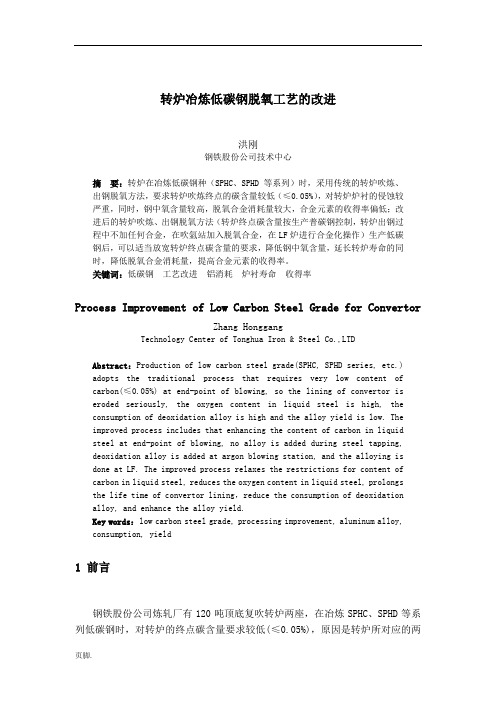
转炉冶炼低碳钢脱氧工艺的改进洪刚钢铁股份公司技术中心摘要:转炉在冶炼低碳钢种(SPHC、SPHD等系列)时,采用传统的转炉吹炼、出钢脱氧方法,要求转炉吹炼终点的碳含量较低(≤0.05%),对转炉炉衬的侵蚀较严重,同时,钢中氧含量较高,脱氧合金消耗量较大,合金元素的收得率偏低;改进后的转炉吹炼、出钢脱氧方法(转炉终点碳含量按生产普碳钢控制,转炉出钢过程中不加任何合金,在吹氩站加入脱氧合金,在LF炉进行合金化操作)生产低碳钢后,可以适当放宽转炉终点碳含量的要求,降低钢中氧含量,延长转炉寿命的同时,降低脱氧合金消耗量,提高合金元素的收得率。
关键词:低碳钢工艺改进铝消耗炉衬寿命收得率Process Improvement of Low Carbon Steel Grade for ConvertorZhang HonggangTechnology Center of Tonghua Iron & Steel Co.,LTDAbstract:Production of low carbon steel grade(SPHC, SPHD series, etc.)adopts the traditional process that requires very low content ofcarbon(≤0.05%) at end-point of blowing, so the lining of convertor iseroded seriously, the oxygen content in liquid steel is high, theconsumption of deoxidation alloy is high and the alloy yield is low. Theimproved process includes that enhancing the content of carbon in liquidsteel at end-point of blowing, no alloy is added during steel tapping,deoxidation alloy is added at argon blowing station, and the alloying isdone at LF. The improved process relaxes the restrictions for content ofcarbon in liquid steel, reduces the oxygen content in liquid steel, prolongsthe life time of convertor lining,reduce the consumption of deoxidationalloy, and enhance the alloy yield.Key words:low carbon steel grade, processing improvement, aluminum alloy,consumption, yield1 前言钢铁股份公司炼轧厂有120吨顶底复吹转炉两座,在冶炼SPHC、SPHD等系列低碳钢时,对转炉的终点碳含量要求较低(≤0.05%),原因是转炉所对应的两台薄板坯连铸机(意大利达涅利公司的FTSC型)对钢水的质量要求较严格,考虑精炼处理过程中的增碳及尽量避开钢种成份的包晶区需要成品钢水的碳含量≤0.06%,这使转炉终点的氧含量偏高,尤其是在转炉炉役的后期,转炉的复吹效果变差,终点的碳氧浓度积较高,一般情况下转炉终点的氧含量要达到800PPm 以上,对转炉炉衬的侵蚀较严重,而且脱氧及合金化所消耗的合金成本较高,我厂的此类钢种产量比例约占薄板坯产量的30%左右,每月约5万吨,因此,需要对现有的冶炼及脱氧合金化工艺进行优化,以降低生产成本。
炼钢生产中转炉炼钢脱氧工艺分析

炼钢生产中转炉炼钢脱氧工艺分析摘要:对于钢铁企业而言,如果想要切实的提升自身在市场中的核心竞争力,就要通过现代化的生产工艺来不断的提升钢产品的品质,不断降低生产的成本。
在转炉炼钢的过程中,会产生大量的氧气。
如果在钢液中含有过多的氧气,必然会对钢产品的品质和质量产生直接的影响。
为此,了解和掌握转炉冶炼以及炼钢生产实际,氧气产生的危害,并采用科学合理的脱氧工艺,对提高钢产品质量,提高钢厂生产产能,从推动钢厂持续健康发展有着非常重要的意义。
关键词:炼钢生产;转炉;炼钢;脱氧工艺1转炉冶炼的概述转炉冶炼是在高炉高温条件下将生铁进行相应的氧化处理,来控制和降低生铁内碳元素含量,来有效保证钢材质量。
在熔点上生铁和钢材有所不同,同时,含碳量也存在很大差异,钢材含碳量在2%以下,同时相较于生铁熔点更高,大约为1450℃~1500℃。
但是铁的熔点就稍微低一点,大约为1100℃~1200℃。
其次,钢中的铁和碳元素会形成碳化铁固溶体,因此随着碳的容量的不断增加,其硬度和强度也会逐渐增加,但整体的韧性和成型性会有所降低。
它在物理性、化学性和机械性等方面表现很好,可用于拉伸、压制、轧制、冲压以及拉伸等深加工,整体而言用途很广泛。
转炉炼钢的主要成分就是低碳钢,低碳钢转炉脱碳的整体速度比较快,而且钢中含有的气体含量比较低,从而保证了钢具有良好的塑性,焊接性和深冲性强,因此,低碳钢常用于制造低碳软钢丝、热轧和冷轧钢板、冷弯钢板和镀锌板等。
可以看出,由转炉钢制成的各种硬钢丝、结构钢和轴承钢得到了很好的使用。
2氧在炼钢中的产生以及危害无论采用何种方法进行炼钢,主要目的是将其中的化学杂质清除,特别是锰、硅、磷、碳等化学杂质清除过程当中,会应用其中的氧气,引发氧化反应,让杂质和氧气共同结合在一起,形成一种新的氧化合物,并析出其中的杂质。
氧在钢液中是不可避免而存在的,所以吹氧炼钢时,由于钢液氧化以及杂质含量不断下降,氧气在钢液中的含量也会不断提升,氧气在钢液中如果未得到全面的处理,钢液中含氧量较高,待其凝固时,便会和钢液产生反应,形成结晶,同时也会生成氧化亚铁,由于钢液当中氧化亚铁的存在,会破坏掉铸坯,从而影响钢产品质量,更甚者引发变形问题,出现热脆情况,还会造成钢铁氧化问题。
- 1、下载文档前请自行甄别文档内容的完整性,平台不提供额外的编辑、内容补充、找答案等附加服务。
- 2、"仅部分预览"的文档,不可在线预览部分如存在完整性等问题,可反馈申请退款(可完整预览的文档不适用该条件!)。
- 3、如文档侵犯您的权益,请联系客服反馈,我们会尽快为您处理(人工客服工作时间:9:00-18:30)。
炼钢转炉冶炼低碳钢脱氧合金化工艺优化精编
版
MQS system office room 【MQS16H-TTMS2A-MQSS8Q8-MQSH16898】
附件1
一、项目基本情况
二、项目简介
三、主要完成人员名单(特等奖15人、一等奖9人、二等奖7人、三等奖5人)
其它申报材料
1、………………………项目承包合同书;
2、………………………检验试验报告;
3、……………………主要设计图纸;
4、……………………本项目以往的获奖及有关验收、鉴定、评审情况。
填写说明
1、《项目名称》:要准确、简明、具体,并反映出项目所属的技术领域和特征,字数(含符号)不得超过30个汉字。
2、《主要完成人》:按完成人对该项目创造性贡献大小的顺序填写,其中对获特等奖的成果发主研人1—15名荣誉证书,获一等奖的成果发主研人1—9名荣誉证书,获二等奖的成果发主研人1—7名荣誉证书,获三等奖的成果发主研人1—5名荣誉证书。
3、《主要完成单位》:指对该项目的完成做出创造性贡献的主要单位。
4、《主要完成协作单位》:与主要完成单位协作完成项目的主要协作方,要求协作方盖章。
5、《申报单位》:科技成果申报单位。
6、《申报日期》:提交成果申报书的日期。
7、《申报单位意见》:申报单位对项目明确作出客观的评价,并由该单位主管厂(处)级领导签字后,加盖单位公章。
8、《研究起止时间》:起始时间指项目下达或开始研制时间。
完成时间指论文公开发表、项目通过验收、鉴定或投产的时间。
9、《成果应用时间及地点》:指成果正式投产时间或技术措施正式应用于实践的时间及地点。
10、《项目来源》:选择适当的类别在□内打“∨”。
11、《项目概况》:填写项目所属技术领域、立项背景、主要内容、特点及应用推广情况。
12、《详细科学技术内容》:是考核评价该项目是否符合授奖条件的主要依据,应详述该项目实质性的技术内容,包括总体思路、技术方案和实施效果。
13、《关键技术及创新点》:是申报项目的核心部分及评奖的必要条件,也是审查项目、处理争议的关键依据。
写明本项目在原来的基础上有实质性创新的内容,应简明、准确、完整。
14、《保密要点》:指明申报项目需要保密的技术内容。
15、《经济、社会效益情况》:逐年填写项目实施后的增值、增利及创收情况。
要求内容真实客观。
对项目实施后所产生的直接或间接经济效益进行说明,要求列出计算公式,并注明公式中各项数据的意义、单位及数据来源。
社会效益情况应扼要地说明项目在推进科技进步、提高生产管理水平、保护资源环境等方面所起的作用。
16、《专利情况》:简要写明该项目申请专利情况。
17、《主要完成人员名单》:根据完成人员对项目贡献大小按顺序填写人员情况。
18、《其它材料》:将所列有关内容以书面形式附项目申报表后,其中《本项目以往的获奖及有关验收、鉴定、评审情况》应将有关验收、鉴定及评审意见复印件附后。
按A4纸进行装订。
19、申报材料用A4纸打印2份,左装订。
字体要求:仿宋_GB2312,四号字,单倍行距。
附件2
邯钢科技成果申报协议书
经___________________与_________________友好协商,就关于__________________项目申报公司科技成果的有关事宜达成如下协议:
一、本成果的主要完成单位:_______________________
二、本成果的主要协作单位:________________________
三、本成果的申报单位:____________________________
四、成果的研究起止时间:___________________________
五、成果的应用地点及时间:_________________________
六、本成果主要完成人员名单:
七、本成果的申报经过各完成单位协商同意,完成单位、完成人员排序
无异议,特此说明。
主要完成单位(盖章)主要协作单位(盖章)
主管领导签字:主管领导签字:。