注塑生产中常见的问题
注塑品质问题总结范文

一、前言注塑工艺在塑料制品的生产中占据着重要的地位,然而,在注塑生产过程中,品质问题时有发生,严重影响了产品的质量和企业的声誉。
为了提高注塑产品的品质,减少品质问题的发生,现将我司近期注塑品质问题进行总结分析,并提出改进措施。
二、品质问题总结1. 产品外观缺陷(1)表面有油污、划痕、气泡等。
(2)产品尺寸不稳定,存在较大公差。
2. 产品内部缺陷(1)产品内部有空洞、缩孔、熔接痕等。
(2)产品内部有冷料、飞边等杂质。
3. 材料问题(1)原材料质量不稳定,导致产品性能波动。
(2)材料配比不当,影响产品性能。
4. 设备问题(1)模具设计不合理,导致产品缺陷。
(2)设备磨损严重,影响产品质量。
5. 操作问题(1)操作人员技能水平不足,导致产品品质下降。
(2)生产过程不规范,存在安全隐患。
三、原因分析1. 原材料问题:原材料质量不稳定,供应商管理不到位。
2. 设备问题:设备维护保养不及时,模具设计不合理。
3. 操作问题:操作人员技能水平不足,生产过程不规范。
4. 管理问题:品质管理制度不完善,缺乏有效的监督机制。
四、改进措施1. 优化原材料采购流程,提高原材料质量。
2. 加强设备维护保养,确保设备正常运行。
3. 提高操作人员技能水平,规范生产过程。
4. 完善品质管理制度,加强监督机制。
5. 加强与供应商的沟通与合作,提高原材料质量。
五、总结通过本次注塑品质问题总结,我司将针对存在的问题,采取有效措施进行改进。
在今后的生产过程中,我们要高度重视注塑品质问题,不断提高产品质量,以满足客户需求,提升企业竞争力。
同时,要加强员工培训,提高整体素质,确保生产过程规范化、标准化。
相信在全体员工的共同努力下,我司的注塑品质一定会得到全面提升。
注塑车间问题点和改善对策

在注塑车间,可能会遇到各种问题,这些问题在生产过程中需要特别关注并寻求相应
的改善对策。
以下是常见的问题点以及相应的改善措施:
1. 产品质量问题:在注塑过程中,可能会出现短射、翘曲、裂纹、瑕疵等质量问题。
要改善这些问题,首先要进行原因分析,如模具设计、注塑工艺参数和原材料等。
针
对性地对问题进行调整(如调整注塑速度、压力、温度等),并进行严格的质量控制。
2. 设备故障:"机器、模具和辅助设备可能都会发生故障。
正确的维护和保养是防止故障的关键,例如定期检查润滑系统、更换磨损零件、定期清洁模具等。
3. 低生产效率:提高生产效率是提升注塑车间竞争力的关键。
改善方法包括:减少模
具更换和调试时间、采用自动化设备减少人工干预、优化生产排程和工艺参数等。
4. 浪费问题:在注塑过程中,可能会产生原材料、能源和人力等方面的浪费。
合理安
排生产计划、提高原材料利用率、节约能源(如优化加热和制冷系统)等措施,可以
降低浪费并提高整体效益。
5. 安全问题:注塑车间的生产安全非常重要,包括操作安全、消防安全、职业健康等
方面。
加强员工培训,提高安全意识和操作技能;确保车间内部的通风、照明和消防
等条件良好;合理布局生产线,以避免安全隐患。
6. 人员问题:员工流动性、技能短缺等问题可能影响注塑车间的生产效率和质量。
通
过制定合理的员工福利、培训和晋升政策,可以提高员工满意度和职业素养,从而提
高生产效果。
综上所述,在面对注塑车间的各种问题时,应想方设法地改进生产流程、提高效率和
质量、确保安全,并充分关注员工的发展及满意度。
注塑常见缺陷和原因分析
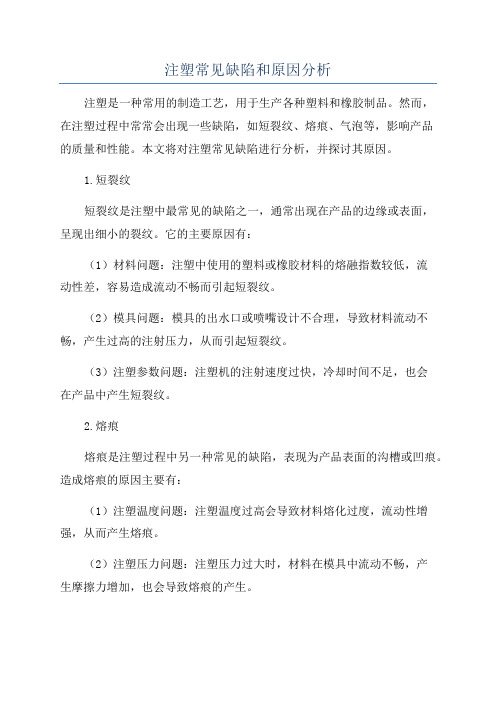
注塑常见缺陷和原因分析注塑是一种常用的制造工艺,用于生产各种塑料和橡胶制品。
然而,在注塑过程中常常会出现一些缺陷,如短裂纹、熔痕、气泡等,影响产品的质量和性能。
本文将对注塑常见缺陷进行分析,并探讨其原因。
1.短裂纹短裂纹是注塑中最常见的缺陷之一,通常出现在产品的边缘或表面,呈现出细小的裂纹。
它的主要原因有:(1)材料问题:注塑中使用的塑料或橡胶材料的熔融指数较低,流动性差,容易造成流动不畅而引起短裂纹。
(2)模具问题:模具的出水口或喷嘴设计不合理,导致材料流动不畅,产生过高的注射压力,从而引起短裂纹。
(3)注塑参数问题:注塑机的注射速度过快,冷却时间不足,也会在产品中产生短裂纹。
2.熔痕熔痕是注塑过程中另一种常见的缺陷,表现为产品表面的沟槽或凹痕。
造成熔痕的原因主要有:(1)注塑温度问题:注塑温度过高会导致材料熔化过度,流动性增强,从而产生熔痕。
(2)注塑压力问题:注塑压力过大时,材料在模具中流动不畅,产生摩擦力增加,也会导致熔痕的产生。
(3)模具设计问题:如果模具中的出水口或喷嘴设计不合理,也会在产品表面形成熔痕。
3.气泡气泡是注塑中常见的缺陷,表现为产品内部或表面的空腔。
气泡的形成原因有:(1)材料问题:注塑材料中含有过多的水分或挥发性物质,注塑过程中被加热蒸发,生成气泡。
(2)注塑温度过高:高温会导致材料熔化过度,容易产生气泡。
(3)注塑压力问题:过高的注塑压力会使材料在注塑过程中产生剧烈的振动,从而引起气泡。
(4)模具问题:模具中存在堵塞或不良的冷却系统,也会导致气泡的产生。
4.缩短问题缩短是指产品在冷却过程中出现尺寸缩小的现象。
产生缩短的主要原因有:(1)注塑温度过低:低温会使注塑材料的熔融程度不足,流动性降低,产生缩短。
(2)冷却时间不足:注塑材料冷却时间不足会导致产品未完全固化,容易产生缩短。
(3)注塑压力问题:过大的注塑压力会使产品产生内部的应力,引起尺寸缩小。
(4)模具问题:模具中存在过多的冷却系统,会导致材料过度冷却而使产品缩短。
注塑过程中常见的问题及解决方案

注塑过程中常见的问题及解决方案一、飞边(披锋)1. 问题描述- 这飞边就像塑料偷偷长出来的小翅膀,在注塑件的边缘或者分型面那里冒出来,看着可闹心了。
就像好好的一块蛋糕,边缘突然多出了一些不规则的奶油坨坨。
2. 解决方案- 首先得检查模具的合模力。
要是合模力不够,那塑料就会像调皮的小孩从门缝里挤出来。
适当增加合模力,把模具紧紧抱住,让塑料乖乖待在该待的地方。
- 模具的磨损也会导致飞边。
就像穿破了的鞋子会漏脚指头一样,磨损的模具缝隙变大了。
这时候就得修模啦,把那些磨损的地方补一补或者磨平。
- 注塑压力也不能太大。
如果压力太大,塑料就像被大力士猛推的水,到处乱流。
降低注塑压力,找到一个合适的值,既能把模具填满,又不会让塑料溢出来。
二、短射(缺料)1. 问题描述- 短射就像给一个杯子倒水,结果没倒满一样。
注塑件看着不完整,有些地方该有塑料的却空着,就像一个没发育好的小怪物。
2. 解决方案- 先看看注塑压力是不是太小。
压力小的话,塑料就像没力气的小蚂蚁,爬不到模具的每个角落。
增加注塑压力,让塑料充满整个模具型腔。
- 塑料的流动性也很关键。
如果塑料太黏,就像浓稠的糨糊,很难流到模具的远端。
这时候可以提高料筒温度,让塑料变得稀一点,流动性更好,就像把糨糊加热变成稀粥一样,能顺利流到各个地方。
- 浇口尺寸也可能有问题。
要是浇口太小,就像一个小得可怜的水龙头,水流不出来多少。
适当扩大浇口尺寸,让塑料能畅快地流进模具。
三、气泡(气穴)1. 问题描述2. 解决方案- 注塑速度可能太快了。
塑料像一阵风呼呼地冲进模具,把空气都裹在里面了。
降低注塑速度,让塑料慢慢流进去,就像散步一样,这样空气就有机会跑出来了。
- 模具的排气也很重要。
如果模具没有排气孔或者排气不良,空气就被困在里面出不来。
在模具上开排气槽或者使用透气钢材料,给空气一条逃跑的路。
- 塑料干燥不彻底也会产生气泡。
如果塑料里有水份,加热的时候就会变成水蒸气,形成气泡。
注塑问题点及解决方法
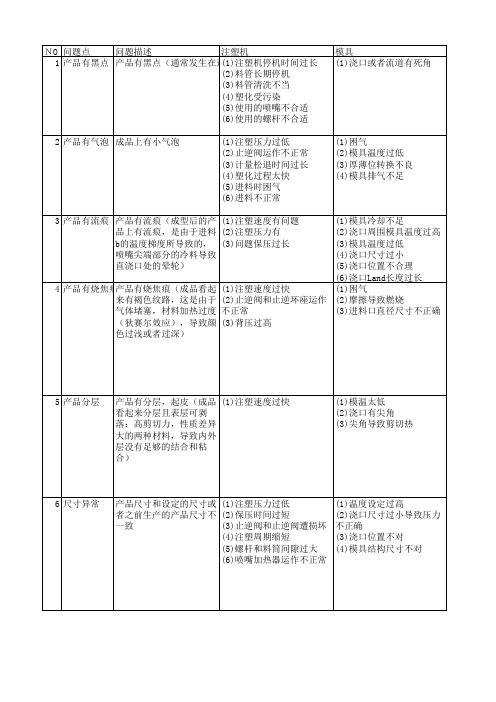
材料
解决方法
提供者
(1)原材料物理污染 (1)用合适的材料清洗系统
(4)检查止逆阀
(5)确保排气良好
(6)增加浇口尺寸
(7)缩短排气道长度
(1)熔化温度过低
(1)调整注塑速度
MoldMasters
(2)增加一个大的冷料区
(3)在流道尾端增加一个冷料井
(4)使用加热进料背板
(5)确认是否有死角部位并消除
(1)材料熔化加热过度 (1)清理堵塞的排气槽
MoldMasters
化不足
a.降低料管温度
(4)色母不匹配
b.降低螺杆转速
(5)材料在料管中驻留 C.降低背压
的时间过长
(3)降低喷嘴温度
(4)调整材料在料管中驻留的时
间
(5)调整回收料使用的比率
(6)调整周期时间
(7)检查外部污染源
(8)确保所有部位的冷却完成
(1)粘性过低
(1)降低注塑速度
MoldMasters
(2)熔化温度过高
(1)确认冷却循环时间
MoldMasters
(2)降低注塑压力
(3)减少保压时间
(4)减少注塑时间
(5)调整进料
(6)减少模具关闭的时间
(7)提高型芯温度
(8)降低喷嘴温度
(9)检查模具是否有弯曲或不正
确的脱模角熔化温度过低
(1)检查排气
MoldMasters
模具注塑常见问题及解决方法

模具注塑常见问题及解决方法模具注塑是一种常见的制造工艺,广泛应用于汽车、电子、家电等行业。
然而,在注塑过程中常会遇到一些问题,例如产品质量不合格、生产效率低下等。
本文将针对这些常见问题进行分析,并提出相应的解决方法。
1. 产品尺寸不准确产品尺寸不准确是模具注塑过程中常见的问题之一。
造成尺寸不准确的原因可能有很多,例如模具设计不合理、注塑机调试不当等。
解决这个问题的方法是对模具进行优化设计,确保模具的尺寸精度和稳定性;同时,对注塑机进行精确调试,保证注塑过程的准确性。
2. 产品表面缺陷产品表面缺陷是另一个常见的问题,例如气泡、痕迹、烧焦等。
这些表面缺陷会影响产品的外观和质量。
要解决这个问题,可以从以下几个方面入手:优化模具通气系统,确保注塑过程中的气体能够顺利排出;调整注塑参数,控制注塑温度和压力,避免过高或过低造成烧焦或气泡;定期清洁模具,防止灰尘和杂质对产品表面造成影响。
3. 模具磨损严重模具在长期使用过程中会出现磨损,导致产品尺寸不准确或者产生其他问题。
要解决这个问题,可以采取以下几种措施:定期对模具进行保养和维护,及时更换磨损严重的零部件;使用高质量的模具材料,提高模具的耐磨性;注塑过程中控制好注塑温度和压力,避免过高过低造成模具磨损。
4. 注塑机故障注塑机故障是导致生产效率低下的主要原因之一。
为了避免注塑机故障,可以采取以下几个措施:定期对注塑机进行维护和保养,清洁注塑机内部的杂质和积聚物;使用高质量的注塑机零部件,避免因零部件质量差导致故障;培训操作人员,提高其对注塑机的操作技能和维修能力。
5. 塑料材料选择不当塑料材料的选择对注塑产品的质量和性能有很大影响。
如果选择的塑料材料不合适,可能会导致产品强度不足、耐热性差等问题。
因此,在进行模具注塑之前,应仔细选择合适的塑料材料,根据产品的要求和使用环境来进行选择。
6. 生产成本过高生产成本过高是许多企业关注的问题。
要降低生产成本,可以从以下几个方面入手:优化模具设计,减少材料的浪费;提高注塑机的效率,减少能耗;采用高效的生产工艺,提高生产效率。
注塑常见问题点及对策
不良原因分析
缺陷: 缩水
缩水
不良原因分析
定义:
缩水
壁厚处表面的原料由于体积收缩,固化时在 成品表面出现凹陷痕迹
对策
增加射压 模具减少壁厚 增加计量检查逆止阀
增加保压 加大胶口 检查逆止阀
不良原因分析 缺陷: 烧焦
烧焦
不良原因分析
烧焦 成品表面出现黑色碳化粉末状物质, 主要是模腔内残留空气引起的
品不能从外面看到,只有将其刨开才可见 到。壁厚处的中心时冷却最慢的地方,因 此,迅速冷却快速收缩的表面将原料拉引 起来产生空隙,形成气泡。
1、原料没烘干,水份气化而产生气泡。 2、背压不足,螺杆卷入空气,产生气泡。 3、原料温度高,产生气体造成气泡。
不良原因分析
气泡
4、壁厚产品中心是冷却最慢的地方,迅速 冷却,快速收缩的表面将原料拉引起来, 产生空洞,造成气泡,(加保压加时间)。 5、壁厚较大的产品,由于难以去掉模具的 空气,卷进空气产生气泡(请减慢射出速 度)。
程不稳定
对策
优化成型参数
检查周边设备
调整背压
缩短成型周期
使用机械手
结语
谢谢大家!
对策
降低射压与保压
降低最后射速
延长冷却时间
加大顶出面积
改变胶口位置
加大脱模角
抛光处理
不良原因分析
强度不足
成品比较脆弱,容易断裂
对策
提高射出速度
提高模温
提高料温
缩短成型周期
改进胶口
设加强肋
检查原料
不良原因分析
光泽度不均
成品表面亮度或颜色不均匀
对策
调整料温
提高模温
清洗料管
提高背压
模具抛光
注塑常见问题及分析
1.塑料缩水就是塑料收缩的问题,很少有资料谈过.塑料收缩有四种情况:热收缩、相变收缩、取向收缩、压缩收缩与弹性恢复。
收缩过程有三部分组成:浇口凝固前的收缩、冷却收缩和脱模后收缩。
2. 缩水的主要原因:1,注射量不够2,熔体温度过高3,注射压力和保压压力过小4,注射时间和保压时间过少5,注射速度过大6模具温度不当3. 缩孔的主要原因:1,注射量不够2,注射压力太低3,注射速度不当4,模具温度过低4.注塑件缺胶、不饱模---Short Shot原因分析☐塑胶熔体未完全充满型腔。
☐塑胶材料流动性不好。
❖对策☐制品与注塑机匹配不当,注塑机塑化能力或注射量不足。
☐料温、模温太低,塑胶在当前压力下流动困难,射胶速度太慢、保压或保压压力过低。
☐塑料熔化不充分,流动性不好,导致注射压力损失大。
☐增加浇口数,浇口位置布置要合理、多腔不平衡排布充填。
☐流道中冷料井预留不足或不当,冷料头进入型腔而阻碍塑胶之正常流动,增加冷料穴。
☐喷嘴、流道和浇口太小,流程太长,塑胶填充阻力过大。
☐模具排气不良时,空气无法排除。
5.披峰(毛边)---Burring & Flashing❖原因分析☐塑胶熔体流入分模面或镶件配合面将发生-Burring。
☐锁模力足够,但在主浇道与分流道会合处产生薄膜状多余胶料为Flash ❖对策☐锁模力不足,射入型腔的高压塑胶使分模面或镶件配合面产生间隙,塑胶熔体溢进此间隙。
☐模具(固定侧)未充分接触机台喷嘴,公母模产生间隙。
(没装紧)☐模温对曲轴式锁模系统的影响。
☐提高模板的强度和平行度。
☐模具导柱套摩损/模具安装板受损/拉杆(哥林柱)强度不足发生弯曲,导致分模面偏移。
☐异物附着分模面。
排气槽太深。
☐型腔投影面过大/塑胶温度太高/过保压。
6.❖表面缩水、缩孔(真空泡)--Sink Mark & Void & Bubble❖原因分析☐制品表面产生凹陷的现象。
☐由塑胶体积收缩产生,常见于局部肉厚区域,如加强筋或柱位与面交接区域。
注塑模具问题点汇总清单
注塑模具问题点汇总清单一、外观问题1. 飞边(披锋)- 这模具做出来的产品边缘毛毛糙糙的,就像人没刮干净胡子似的。
在合模的地方或者一些薄壁处,老是有多余的塑料跑出来,形成飞边,影响产品的外观,也可能会刮伤人呢。
2. 缩水痕- 产品表面有那种凹下去的小坑洼,就像人脸上突然长了麻子一样。
在产品壁厚比较厚的地方,冷却的时候不均匀,就容易出现这种缩水痕,看起来可丑了。
3. 流痕- 那些像波浪一样的纹路在产品表面,就像有人在塑料还没干的时候乱划了几笔。
塑料在模具里流动的时候不顺畅,就产生了这种流痕,让产品看起来很不精致。
4. 气泡- 产品里面有像小珠子一样的空洞,就像面包没发好里面有大气泡一样。
注塑的时候,空气没排干净或者塑料里有水分,就会产生这种气泡,感觉产品就像个空心萝卜。
5. 熔接痕- 产品表面有一条明显的线,就像衣服上缝了一道歪歪扭扭的补丁。
不同的塑料流在模具里汇合的时候没融合好,就出现了熔接痕,把产品的美观都破坏了。
6. 表面光泽度不一致- 有的地方亮晶晶的,有的地方却雾蒙蒙的,就像人穿了件一半是绸缎一半是粗布的衣服。
可能是模具表面的光洁度不一样,或者脱模剂喷得不均匀造成的。
二、尺寸问题1. 尺寸偏差过大- 做出来的产品大小跟设计的不一样,有的地方大得像个胖子,有的地方小得像个瘦子。
可能是模具的型腔尺寸没加工准确,或者注塑的时候温度、压力等工艺参数影响了塑料的收缩率。
2. 形状变形- 本来应该是方方正正的产品,结果变成了歪歪扭扭的四边形,就像被人捏过的橡皮泥。
可能是模具的结构不合理,在脱模的时候对产品施加了不均匀的力,或者冷却不均匀导致产品变形。
三、结构问题1. 脱模困难- 产品在模具里就像被胶水粘住了一样,死活不愿意出来。
可能是拔模斜度不够,或者模具的表面粗糙度太大,摩擦力太大,让产品卡在里面出不来。
2. 模具零件损坏- 像那些顶针啊、滑块啊,有时候会断掉或者磨损得很厉害。
就像人的牙齿掉了或者磨平了一样,顶针断了就没法正常顶出产品,滑块磨损了可能会导致合模不严或者产品表面划伤。
注塑过程中存在的问题及解决办法
注塑过程中存在的问题及解决办法在注塑过程中,可能会出现一些问题,影响产品的质量和生产效率。
下面列举一些常见的问题及解决办法:1. 热熔物质不充分:热熔物质的充填不充分可能会导致制品的短射或缩水等问题。
解决办法是检查喂料系统,确保熔料能够充分填充模具的所有空间,同时调整熔融温度和压力以适应具体材料和模具的要求。
2. 热熔物质的脱模性差:脱模性差可能导致产品拉伸、变形、形状不完整等问题。
解决办法是优化注塑工艺参数、或改进模具设计,增加脱模剂的使用量,确保热熔物质能顺利脱模。
3. 模具磨损严重:在长时间使用后,模具可能会出现磨损,导致制品尺寸偏差增大、质量下降。
解决办法是定期检查模具状态,必要时进行维护和修复,并妥善保养模具,延长使用寿命。
4. 模内气泡和气体线:模具填充时,可能会产生气泡或气体线,这会对产品的外观和性能造成影响。
解决办法是优化注塑压力和速度,以减少气体产生;在设计模具时,合理设置通气口和冷却系统,以排除气泡。
5. 温度控制不准确:温度是影响注塑过程和产品性能的重要因素,如果温度控制不准确,可能导致产品变形、气泡、表面瑕疵等问题。
解决办法是使用高质量的注塑机和热控系统,严格控制加热和冷却时间,确保温度分布均匀。
注塑过程中存在的问题多种多样,解决办法也需因情况而异。
因此,对于每个具体问题,需要仔细分析原因并采取相应的措施,以确保最终生产出符合要求的产品。
注塑过程中存在的问题及解决办法可以从多个方面展开,下面将深入探讨一些常见的问题,并提供相应的解决办法。
1. 模具设计问题:模具是注塑过程中至关重要的部分,如果设计不合理,就会导致一系列问题。
常见的问题包括产品尺寸偏差大、表面粗糙、开裂等。
解决办法是优化模具的进料系统和冷却系统,确保充填均匀,并增加冷却时间和加热时间。
2. 注塑机参数调节不当:注塑机的温度、压力和速度等参数设置不当,会导致产品质量问题。
例如,温度过高或过低会导致材料熔化不完全或固化不充分;压力过高或过低会影响产品的密度和强度。
- 1、下载文档前请自行甄别文档内容的完整性,平台不提供额外的编辑、内容补充、找答案等附加服务。
- 2、"仅部分预览"的文档,不可在线预览部分如存在完整性等问题,可反馈申请退款(可完整预览的文档不适用该条件!)。
- 3、如文档侵犯您的权益,请联系客服反馈,我们会尽快为您处理(人工客服工作时间:9:00-18:30)。
注塑生产中常见的问题1. 刚开机时产品跑披锋,生产一段时间后产品缺胶的原因及解决方案。
刚开机时注塑机料管内的熔胶由于加热时间长,熔胶粘度低,流动性好,产品易跑披锋,生产一段时间后由于熔胶不断把热量带走,造成熔胶不足,粘度大,流动性差,使产品缺胶。
在生产一段时间后,逐渐提高料管温度来解决。
2. 在生产过程中,产品缺胶,有时增大射胶压力和速度都无效,为什么?解决方法?是因为生产中熔胶不断把热量带走,造成熔胶不足,胶粘度大,流动性差,使产品缺胶。
提高料管温度来解决。
3. 产品椭圆的原因及解决方法。
产品椭圆是由于入胶不均匀,造成产品四周压力不匀,使产品椭圆,采用三点入胶,使产品入胶均匀。
4. 精密产品对模具的要求。
要求模具材料刚性好,弹变形小,热涨性系数小。
5. 产品耐酸试验的目的产品耐酸试验是为了检测产品内应力,和内应力着力点位置,以便消除产品内应力。
6. 产品中金属镶件受力易开裂的原因及解决方法。
产品中放镶件,在啤塑时由于热熔胶遇到冷镶件,会形成内应力,使产品强度下降,易开裂。
在生产时,对镶件进行预热处理。
7. 模具排气点的合理性与选择方法。
模具排气点不合理,非但起不到排气效果,反而会造成产品变形或尺寸变化,所以模具排气点要合理。
选择模具排气点,应在产品最后走满胶的地方和产品困气烧的地方开排气。
8. 产品易脆裂的原因及解决方法。
产品易脆裂是产品使用水口料和次料太多造成产品易脆裂,或是料在料管内停留时间过长,造成胶料老化,使产品易脆裂。
增加新料的比例,减少水口料回收使用次数,一般不能超过三次,避免胶料在料管内长时间停留。
9. 加玻纤产品易出现泛纤的原因及解决方法是由于熔胶温度低或模具温度低,射胶压力不足,造成玻纤在胶内不能与塑胶很好的结合,使纤泛出。
加高熔胶温度,模具温度,增大射胶压力。
10. 进料口温度对产品的影响。
进料口温度的过高或过低,都会造成机器回料不稳定,使加料量不稳定,而影响产品的尺寸和外观。
11. 透明产品有白点的原因及解决方法。
透明产品有白点是因为产品内进入冷胶造成,或料内有灰尘造成的。
提高射嘴温度,加冷料井,原料注意保存,防止灰尘进入。
12. 什么是注塑机的射出能力?射出能力※※=射出压力(kg/cm2)×射出容积(cm3)/100013. 什么是注塑机的射出马力?射出马力PW(KW)=射出压力(kg/cm2)×射出率(cm3/sec)×9.8×100%14. 什么是注塑机的射出率?射出率V(cc/sec)=p/4×d2×g d2::料管直径g:料的密度15. 什么是注塑机的射胶推力?射胶推力F(kgf)=p/4(D12-D22)×P×2 D1:油缸内径D2:活塞杆外径P:系统压力16. 什么是注塑机的射胶压力?射胶压力P(kg/cm2)=[p/4×(D12-D22)×P×2]/(p/4×d17. 什么是注塑机的塑化能力?塑化能力W(g/sec)=2.5×(d/2.54)2×(h/2.54)×N×S×1000/3600/2 h=螺杆前端牙深(cm)S=原料密度18. 什么是系统压力?与注塑压力有什么区别?系统压力(kg/cm2)=油压回路中设定最高的工作压力,注塑压力是指注塑时的实际压力,两者不相等。
19. 注塑机液压用油的要求:(1)适当的粘度和良好的粘温性能(2)良好的润滑性和防锈性;(3)良好的化学稳定性,不易气化成胶质;(4)搞泡沫性好;(5)对机件及密封装置的腐蚀性要小;(6)燃点(闪点)要求,凝固点要低。
20. 液压油粘度对注塑机的影响?当系统工作环境温度较高时,应采用较高粘度的油,反之,应采用较低粘度的油,系统工作压力较高时,应采用粘度较高的,因为在高压,密封较困难,泄漏是主要问题,反之,系统工作压力较低,宜采用粘度较小的油,当液压系统的工作部件运转速度高时,油液的流速也高,这时压力损失也将增加,而泄漏量相对减小,宜采用粘度较低的油,反之,工作部件运动速度低时,宜采用粘度较高的油。
21. 松退的设定。
松退正确位置=过胶圈移动位置+螺杆越位距离22. 松退位置设定的重要性。
松退位置设定过大,会造成回料吸氧,使胶料氧化和产生气泡。
位置设定过小,使料筒内压力大,剪切力过高使胶料分解,射嘴流涎。
位置误差不能超过0.4mm.23. 熔胶位置的设定。
熔胶位置=产品的重量/(最大行程/最大熔胶量)24. 气辅注塑的主要优点:能抽空厚型材料芯部,制成空心管件,可节省材料,缩短周期时间。
在注塑中采用气体可使压力均匀分布,当塑料冷却和固化时,气体可通过膨胀对塑料的体积收缩进行补偿。
降低模塑制品内应力,从而提高外形稳定性,消除变形和翘曲现象。
25. 活塞杆外径中间小,两头大问题?由于中孔针过热产品收缩不均衡,造成活塞杆外径中间小,两头大.中孔针可采用散热快的磷铜材料来做,模具在产品中间部分排气.26. 球面丝印后开裂问题.由于产品表面存在应力,造成丝印后开裂.增加模具温度,减小应力;可用退火的方法消除应力.27. 眼镜架,水口边易断问题.射胶压力和保压压力大,水口边残存内应力,造成产品易断.尽量减小射胶压力和保压压力,适当提高模具温度来解决.28. 电器外壳,四个装配柱子,打螺丝时爆裂问题.由于柱子存在夹水线,造成产品装配柱子易暴裂.模具增加排气,适当提高模温,加快射胶速度来减小夹水线.29. 产品变形问题.产品变形主要是热收缩时不平衡造成产品变形,或由于产品本身内应力作用下使产品变形.30. 透明PC外壳气泡问题。
原料干燥不够;产品存在胶厚薄不均现象,模具排气不良,原料易分解都可能造成产品气泡. 充分干燥原料,增大模具排气,尽量减少胶厚薄不均现象.31. 复印机,磁性材料的啤塑问题。
应采用高模温,快速射胶方法.32. 产品包胶,水口边缩水问题。
模具排气不良,射胶速度慢,保压压力和时间不够,都能造成水口缩水. 增大模具排气,适当提高射胶速度,增加保压压力和时间.33. 产品内应力,造成产品放置一段时间后爆裂问题。
由于产品内残存应力,产品放置一段时间后由于应力的作用,使产品爆裂. 提高啤塑时的模具温度,降低射胶压力,来消除产品应力,产品可用退火的方法消除应力.34. ABS料在用黑色色母时,造成产品易断裂脱皮问题。
是色母的颜料中用了碳粉过多原因,造成产品脱皮.更换色母颜料.35. 一台180吨14安士机,产品一出四CD盒共120克,外观良好,无批峰,但其中一只重2克,为什么?模具产品一出四,由于模具进胶不平衡造成其中一只产品啤塑饱满,密度大,出现重2克现象.36. 一台100吨液压曲肘机使用了三年,模具锁紧后,经常打不开。
是由于机器曲肘磨损,造成开模不平衡,所以模具锁紧后,会经常打不开.37. 一台7安士机使用了二年,出现射胶不稳定,一啤批峰一啤缺胶,换过油封和分胶头,系统压力也稳定,就不行。
由于螺杆磨损或损坏,造成回料不匀,所以会出现射胶不稳定.38. 一台150吨新机啤PP水口料半年,原来熔胶最快3秒,而现在要6秒。
由于螺杆磨损,造成回料慢.39. 一啤塑师父在调试一产品,出现缺胶,速度或压力升一点,产品没反应,再升一点就出批峰?机器锁模机构磨损,造成锁模有间隙,所以会出现披锋.40. 一台机用了二年,啤货时炮筒中间温度偏高,关了电源也没用。
由于螺杆磨损变得粗糙,啤塑回料时磨擦产生热,使炮筒中间温度偏高.41. 某厂有新旧机十几台,油封经常漏油,换了一段时间又漏?油温过高使油封易老化损坏,漏油;油缸芯子磨损,造成刮坏油封漏油.42. 油泵电机起动电路的讲解。
油泵电机起动是采用星三角起动43. 省电泵原理讲解。
省电泵即为变流量泵,当机器有动作时,压力油通过油阀油缸推动机械动作,再回到油箱,当机器没有动作时,压力油直接回到油箱。
44. 电子线路板输入与输出的讲解。
由各个动作感应开关和电子尺等信号输入电子版,电脑通过运算后再输出给油阀,执行动作。
45. 油封顽固性漏油的原因及预防。
油缸芯子磨损刮坏油封,造成顽固性漏油,保持油缸芯子干净,避免磨损预防刮坏油封造成漏油。
46. 压力与流量线性对注塑工艺的影响。
压力与流量线性成比例,对注塑工艺的参数准确和稳定有着重要意义。
47. 生产周期变慢的原因及改善措施。
生产周期变慢的原因主要是冷却时间延长,和螺杆因磨损使回料时间加长。
改善模具冷却效果,缩短冷却时间,更换磨损的螺杆,使回料时间缩短,加快生产周期。
48. 熔胶时发出尖叫声的原因与处理方案。
熔胶时发出尖叫声是由于螺杆与料磨擦发出的或螺杆与炮筒磨擦发出的。
对螺杆抛光处理或电镀,使表面光滑减小磨擦;调整螺杆的中心度使它不与炮筒发生磨擦。
49. 锁模平行度的检测与调整方法。
用四个百分表测定机器锁模时哥林柱的拉伸长度,看是否在允许公差内,来检测哥林柱锁模平等度。
然后调整哥林柱大螺母来调整锁模平行度。
(看另一本书《注塑机原理》)50. 哥林柱折断的原因与预防措施。
哥林柱折断的原因是由于锁模不平等造成的。
调整锁模平行度来预防哥林柱折断。
51. 曲肘磨损的原因分析。
曲肘磨损的原因是,曲肘润滑不良造成的。
52. 螺杆及分胶头折断的原因与预防。
螺杆及分胶头折断的原因,是由于塑胶还没达到熔化温度或料筒内有铁块卡※螺杆,在回料时,压力大造成扭断螺杆及分胶头。
53. 冷却器容易漏水的分析。
由于冷却水的酸性或咸性过大,腐蚀冷却器的管道,造成冷却器易漏水。
54. 氮气射胶的安装与应用。
氮气射胶是安装在射胶油路中的一个附加装置,在射胶时,氮气迅速澎胀挤压液压油,使液压油流速增快来达到快速射胶。
55. 气体辅助设备的应用。
气体辅助是啤塑产品时,在产品中充气,使产品里面空的,可减少塑胶材料。
56. 开环与闭环油路的比较。
开环与闭环油路的比较就是闭环油路在射嘴处多加了一个压力传感器,当设定参数与实际数据偏差时,压力传感器就会反馈信号给电脑,电脑就会修正偏差值,使设定值与实际值相等。
57. 水平度对注塑机台的影响。
注塑机水平度对机器的开锁模平衡有重要意义,对机器的运行平稳起到保证作用。
58. 模板(头板、二板、尾板)破裂的原因与预防措施。
模板破裂的原因主要是模板内存有内应力,在应力的作用下,模板破裂,模板在加工时,应及时消除应力,可以防止模板破裂。
59. 使用工程塑料时,熔胶扭力不足和射胶压力不足的解决方案。
使用工程塑料时,熔胶扭力不足可能增大一级熔胶马达来解决,射胶压力不足可以采用减小螺杆直径来解决。
60. 料管中段温度偏高的原因与解决方案。
料管中段温度偏高,主要是螺杆表面光滑度不够,螺杆与料相磨擦造成的。
应对螺杆表面抛光处理或电镀。