热室压铸机的结构
压铸机的工作原理与本体结构
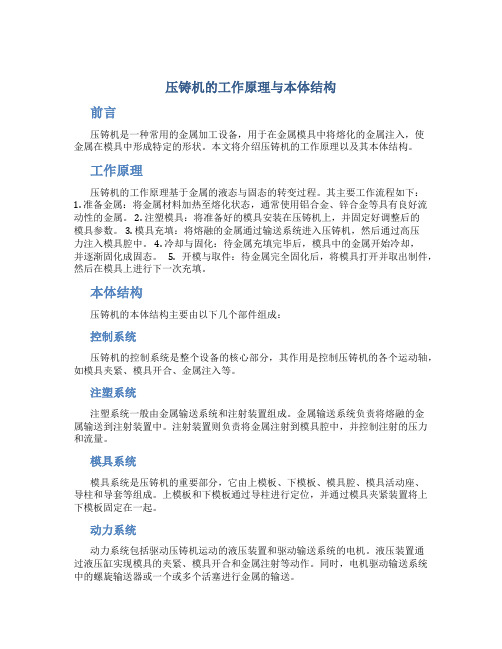
压铸机的工作原理与本体结构前言压铸机是一种常用的金属加工设备,用于在金属模具中将熔化的金属注入,使金属在模具中形成特定的形状。
本文将介绍压铸机的工作原理以及其本体结构。
工作原理压铸机的工作原理基于金属的液态与固态的转变过程。
其主要工作流程如下:1. 准备金属:将金属材料加热至熔化状态,通常使用铝合金、锌合金等具有良好流动性的金属。
2. 注塑模具:将准备好的模具安装在压铸机上,并固定好调整后的模具参数。
3. 模具充填:将熔融的金属通过输送系统进入压铸机,然后通过高压力注入模具腔中。
4. 冷却与固化:待金属充填完毕后,模具中的金属开始冷却,并逐渐固化成固态。
5. 开模与取件:待金属完全固化后,将模具打开并取出制件,然后在模具上进行下一次充填。
本体结构压铸机的本体结构主要由以下几个部件组成:控制系统压铸机的控制系统是整个设备的核心部分,其作用是控制压铸机的各个运动轴,如模具夹紧、模具开合、金属注入等。
注塑系统注塑系统一般由金属输送系统和注射装置组成。
金属输送系统负责将熔融的金属输送到注射装置中。
注射装置则负责将金属注射到模具腔中,并控制注射的压力和流量。
模具系统模具系统是压铸机的重要部分,它由上模板、下模板、模具腔、模具活动座、导柱和导套等组成。
上模板和下模板通过导柱进行定位,并通过模具夹紧装置将上下模板固定在一起。
动力系统动力系统包括驱动压铸机运动的液压装置和驱动输送系统的电机。
液压装置通过液压缸实现模具的夹紧、模具开合和金属注射等动作。
同时,电机驱动输送系统中的螺旋输送器或一个或多个活塞进行金属的输送。
加热与冷却系统为了确保金属材料能达到熔化温度并保持一定时间,压铸机通常配备了加热系统。
加热系统利用电热元件或者火焰进行金属的加热。
另外,压铸机也需要冷却系统来加快金属的冷却与固化速度,以便更快地进行模具开模与取件操作。
总结压铸机是一种重要的金属加工设备,其主要工作原理是通过金属的液态与固态的转变将金属注入模具腔中进行成型。
压铸机的构造和功能
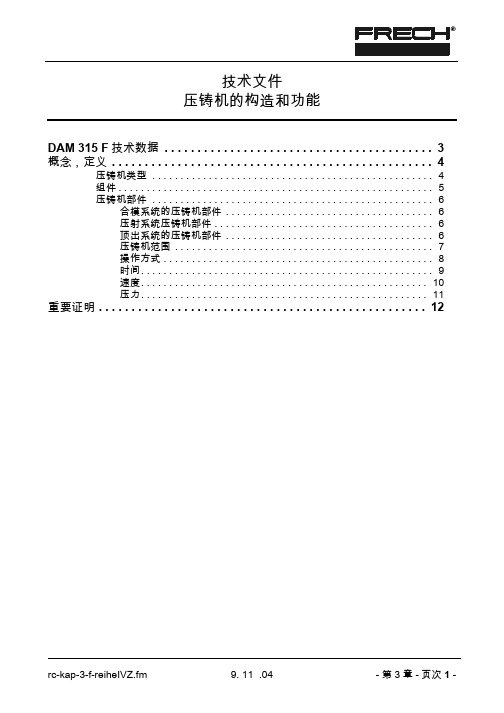
rc-kap-3-f-reihe.fm
技术文件 压铸机的构造和功能
组件
概念
合模单元
压射单元
顶出机构单元 抽芯单元 自动大杠抽出装置 自动顶出机构联轴器 自动模具夹紧装置
定义
该单元用来开模与合模,并且保持合模状态以对抗凝固 阶段施加于金属上的力。 该单元把金属液从压室压入模具里,并且在凝固阶段使 金属处于压力下。 该单元把铸件从模具型腔中顶出。 该单元触发和控制抽芯运行。 该装置把大杠自动抽出,以便于模具调整。 该装置使压铸机的顶出板与模具的顶出机构自动联结。 该装置自动把模具夹紧到压铸机板上。
是铸造所用的材料。
指压室和压射冲头均位于保温炉中金属熔液液面下的压 铸机。
指按测定数量把金属熔液从单独的保温炉输送到压室的 压铸机。
- 页次 4- 第 3 章 -
9. 11 .04
Oskar Frech GmbH + Co. KG, D-73614 Schorndorf
热室压铸机简介

第一章热室压铸机简介热室压铸机由柱架、机架、打料、液压、电器、润滑系统等部件组成。
钢令及锤头浸于料壶中,壶内装有熔融的锌、锡等有色金属合金。
熔融的合金在压力作用下,注射到安装在模板上的模具内,并保持高压直至熔融合金完全凝固为止。
本厂热室压铸机具有设计先进,制造精良,性能好,速度快,节能等特点。
液压系统选用世界著名的YUKEN及TOKIMEC 产品,控制系统采用先进的三菱PLC。
整机操作方便,性能稳定,维修简单,安全可靠。
高压和高速是本机压铸的特点,金属液在一定的压力作用下凝固成铸的过程中,压射比压,填充时间,压射速度和增压时间等性能指标,都可以通过电脑系统而得到稳定和可靠的调整,以达到满意的生产效果。
本厂热室压铸机可压铸大小不同的锌,锡等有色金属合金产品。
,产品广泛应用于汽车工业,电工,电子仪器工业,玩具工业,家庭用具工业和计算器等高科技工业。
该热室压铸机为我公司系列产品之一,其主要参数与性能符合相关标准的规定。
敬请顾客放心使用。
第二章重点提示事项一、液压系统选用的液压油或防火液必须是下列牌号中的一种,并要绝对保证其清洁度。
N46#或N68#抗磨液压油注意:要绝对保证液压油的清洁二、必须定期(三个)检查及随时调整机架导轨面的水平,并保证水平度(纵,横)在0.2mm/m以内。
三、集中润滑泵的润滑油必须选用下列牌号中的一种,并保证润滑油的清洁,以保证各润滑点的润滑。
20#或30#润滑油(机油)注意:保证润滑油的清洁,以保证各润滑点的润滑。
四、在快速(二速)状态下,严禁打空锤。
五、每个黄油咀处必须选用二硫化钼锂基脂注射润滑,并保证清洁及注射用量。
六、氮气瓶必须充氮气,氮气瓶箍严禁拆除。
七、严禁拆除安全门及安全保护装置。
八、严禁私自拆除或更换油路系统的零配件。
不遵守上述之提示而产生的后果,本机制造商不承担保修责任及安全事责任。
第三章安全事项一、防止电击整机必须接地良好。
严禁简化安全保护装置。
选择合适的电源线截面积,不得过电源。
压铸机结构及原理

压铸机结构及原理压铸机是一种常见的金属加工设备,用于将熔化的金属注入铸模中,形成所需的零件或产品。
它具有结构简单、操作方便、生产效率高等优点,因此广泛应用于汽车、电子、家电等行业。
一、压铸机的结构压铸机一般由注射系统、温度控制系统、压紧系统、保压系统、润滑系统、电气控制系统等部分组成。
1.注射系统:注射系统是压铸机的核心部分,主要由熔融炉、喷嘴、注射缸、注射杆等组件组成。
熔融炉将金属加热到熔化温度,并保持一定的温度稳定性。
喷嘴连接注射缸和铸模,通过控制注射缸的运动来控制金属的注入。
2.温度控制系统:温度控制系统用于控制熔融炉的加热温度,确保金属能够达到适宜的熔化温度,并保持一定的恒定温度。
温度控制系统通常由温度传感器、控制器、加热元件等组成。
3.压紧系统:压紧系统用于保证铸模的稳定性和密封性。
它通常由压力缸、活塞、压紧板等部分组成。
压力缸通过活塞的运动产生一定的压力,使铸模能够紧密地固定在压铸机上。
4.保压系统:保压系统用于在注射完成后,保持一定的压力,确保零件在凝固过程中能够保持形状和密度。
保压系统通常由保压缸、保压插头等部分组成,通过操纵保压插头的运动来实现保压过程。
5.润滑系统:润滑系统主要用于减少摩擦和磨损,保证各个部件能够顺利运行。
润滑系统通常由润滑油箱、润滑泵、润滑管路等组成。
6.电气控制系统:电气控制系统用于控制和监控压铸机的运行状态。
它通常由主控制面板、电气元件、传感器等部分组成。
二、压铸机的工作原理压铸机的工作原理可以简要概括为以下几个步骤:1.加热金属:首先,将金属加热到适宜的熔化温度,通常使用熔融炉进行加热,并通过温度控制系统保持恒定的温度。
2.注射:在金属达到熔化温度后,通过控制注射缸的运动,将熔化的金属注入铸模中。
注射缸前进时,金属从喷嘴流入模腔,填充整个模腔空间。
3.固化:注射完成后,保持一定的压力,进行保压,使金属在凝固过程中保持形状和密度。
保压完成后,金属开始凝固。
第七章 铝(镁)合金铸造成形设备及控制 ppt课件

图7-16 低压铸造浇注过程参数变化曲线图
PPT课件
31
7.2.1 低压铸造原理及工艺过程
表7-4 低压铸造加压过程各阶段参数说明
阶段 参数
时间
O→A 升液管阶
段 t1
压力 ∕MPa
P1=h1rμ
加压速度
∕
V1= P1∕t1
(MPa∕s)
加压过程的各个阶段
A→B 充型阶段
B→C 增压阶段
C→D 保压阶
dP)PT直课件线后退,退出型外,放下铸件 23
7.1.3 压铸生产自动化
图7-14 取件机械手结构及原理图
1—齿条 2—传动齿轮 3—曲柄转轴 4—副液压缸 5—弹簧 6—主液压缸
7—油管 8—座板9—滑架 10—活塞杆 11—支架 12—曲柄 13—连杆
14—摇杆 15P—PT课手件臂 16—手掌
(1)低压铸造设备的结构组成 ① 主机 ② 保温炉 ③ 升液管
PPT课件
39
7.2.3 低压铸造设备结构
(2)低压铸造机的类型及构造 低压铸造是金属液体在压力作用下由下而上地充填型腔 并在压力下凝固成形的一种方法,由于所用的压力较低 (通常0.02~0.06MPa),故称之为低压铸造。低压铸造装 备一般由保温炉及其附属装置、模具开合机构、气压系 统和控制系统组成。按模具与保温炉的连接方式,可分 为顶置式低压铸造机和侧置式低压铸造机。
充型速度在低压铸造参数中具有头等重要的意义。目前 在工厂里常见的废品多半是气孔和氧化夹渣,这主要是 充型速度控制不良所引起的。充型速度又决定于通入坩 埚的气体压力的增长速度(称加压速度),因此正确地 控制和掌握加压速度是获得良好铸件的最终关键。加压 速度值,即:
Vp=P充∕t
热室压铸机与冷室压铸机的区别

热室压铸机与冷室压铸机的区别
展开全文
压铸机一般分为热室压铸机和冷室压铸机两大类。
在结构上两种压铸机是存在差别的,热室压铸机与冷室压铸机的区别主要是射料部分,热室压铸机的压室和坩埚是连在一起的(压室置于坩埚内),锤头运动方向垂直于水平面,见图1,射出机构一般与水平面有一定的斜度(方便金属液回流);冷室压铸机的压室与坩锅是分开的,冲头运动方向平行于水平面,需要靠人工或是自动给汤机的机械手将金属液从坩锅舀入压室,见图3。
注:冷室压铸机分为卧式冷室压铸机与(全)立式冷室压铸机,本文主要指卧式冷室压铸机。
图1 热室压铸结构示意
图2 热室压铸机实物图(兴行热室压铸机)
图3 冷室压铸结构示意
布勒
海天
悦马特
固德威
锐达
意特佩雷斯
海铸
图4 冷室压铸机实物图
在性能上两种压铸机的差别在于:
热室压铸机生产效率高,吨位一般不超过800吨,通常用于生产小件(适用压铸锌合金、镁合金等),实际生产锤头压射速度一般在1m/s左右;
冷室压铸机生产效率低,吨位范围上限可达5000吨以上,通常用于生产大件(适用铝合金,镁合金,铜合金),实际生产冲头压射速度一般在2m/s左右。
压铸机结构及原理

压铸机结构及原理压铸机是一种通过将熔融金属注入模具中,并施加压力来制造金属制品的机器。
它主要由注射系统、锁模系统、润滑系统、冷却系统、电气系统等组成。
下面将详细介绍压铸机的结构和工作原理。
注射系统是压铸机的核心部件,主要由注射缸、注射活塞、喷嘴等组成。
在工作过程中,金属材料首先被加热熔化,然后被注射活塞推进进入模腔。
注射系统需要具备较高的压力和温度控制能力,以确保金属材料能够完全充填到模具中。
锁模系统用于将模具锁定在机器上,以确保注射过程中模具不会移动。
它主要由锁模机构、锁模缸等组成。
在工作过程中,模具会被锁定在机器上,并且在注射完成后才会解锁,以方便取出成品。
冷却系统用于控制模具温度,以确保成品能够迅速冷却并保持形状稳定。
它主要由冷却管路和冷却水箱组成。
通过冷却系统,可以将冷却水送入模具中,降低模具温度,使金属迅速固化。
润滑系统用于保持机器各个运动部件的润滑状态,以减少摩擦和磨损。
它主要由润滑泵和润滑剂管路组成。
润滑系统需要定期维护和更换润滑剂,以确保机器的正常运行。
电气系统用于控制压铸机的各项功能,包括注射、锁模、冷却等。
它主要由控制器、电动机、传感器等组成。
电气系统是整个压铸机的大脑,可以通过控制器设置注射时间、温度、压力等参数,以确保产品的质量要求。
压铸机的工作原理是利用液压系统,通过液体的压力来实现金属的注射和模具的锁定。
液压系统主要由液压泵、液压缸、液压控制阀等组成。
在工作过程中,液压泵将液压油从液压油箱抽取并供应给液压缸和液压控制阀。
通过控制液压控制阀的开关,可以实现不同的工作模式,如注射、锁模等。
具体工作过程如下:首先,将金属材料加热至熔化温度,然后注入注射缸中。
接着,控制液压泵加压,将熔融金属通过注射活塞推入模腔中。
注射完成后,液压系统将注射缸回位,准备下一次注射。
然后,液压系统将锁模缸加压,将模具紧密锁定在机器上,防止其移动。
模具锁定后,液压泵停止供油,保持锁定状态,直到产品冷却完成。
压铸机基本结构

压铸机基本结构压铸机是一种用于铸造金属制品的机械设备,其基本结构由以下几个部分组成:机架、铸造系统、液压系统、控制系统和辅助系统。
1. 机架:机架是压铸机的支撑结构,通常由铸铁或钢材制成。
它的主要作用是提供稳定的支撑和保持各个部件的相对位置关系。
机架上通常还安装有操作面板、控制开关和显示屏等操作控制元件。
2. 铸造系统:铸造系统是压铸机的核心部分,包括模具、注射系统和压力系统。
模具是用来制造铸件的工具,通常由两个或多个模具组成。
注射系统由注射筒和注射活塞组成,它的作用是将熔化的金属注入模具中。
压力系统通过液压缸提供所需的压力,将熔化的金属充实到模具中,确保铸件的密实性和形状精度。
3. 液压系统:液压系统是控制压铸机各个部件运动的动力来源,主要由液压泵、液压阀和液压缸等组成。
液压泵负责将液压油从油箱中抽取,并通过液压阀控制液压油的流动方向和压力大小。
液压缸则根据液压系统的指令,驱动机械部件进行运动,如开合模具、注射活塞的前后移动等。
4. 控制系统:控制系统是压铸机的智能化部分,主要由PLC(可编程逻辑控制器)和触摸屏等组成。
PLC是一个可编程的电子设备,可以根据预设的程序控制压铸机的运行,实现各个动作的协调和顺序控制。
触摸屏则是人机交互界面,通过它可以设置工艺参数、监控生产过程和进行故障诊断等操作。
5. 辅助系统:辅助系统包括冷却系统、润滑系统、气动系统和电气系统等。
冷却系统用于控制压铸过程中的温度,保证铸件的质量。
润滑系统则负责给机械部件提供润滑油,减少磨损和摩擦。
气动系统用于控制压铸机的气动元件,如气缸和气动阀等。
电气系统负责控制电动机和各种传感器的运行,确保压铸机的正常工作。
压铸机的基本结构是由机架、铸造系统、液压系统、控制系统和辅助系统等部分组成。
这些部分相互配合,完成金属铸造的全过程。
压铸机在现代工业中具有广泛的应用,可以制造出各种形状复杂的金属制品,如汽车零部件、电子产品外壳等。
随着科技的发展,压铸机的结构和性能也在不断改进和创新,以适应不断变化的市场需求。
- 1、下载文档前请自行甄别文档内容的完整性,平台不提供额外的编辑、内容补充、找答案等附加服务。
- 2、"仅部分预览"的文档,不可在线预览部分如存在完整性等问题,可反馈申请退款(可完整预览的文档不适用该条件!)。
- 3、如文档侵犯您的权益,请联系客服反馈,我们会尽快为您处理(人工客服工作时间:9:00-18:30)。
培训课题:力劲压铸机的结构
培训目的:了解热室压铸机的结构及特点
主要内容:1.热室压铸机的填原理
电气控制系统是保证机器按预定的压力、速度、温度和时间进行工作,它主要由电动机及各种电器元件、仪表、电器线路组成。
一、热室压铸机填充原理
当压射锤头上升时,坩锅内的金属液通过料壶入口进入料壶压室中,合模后,在锤头下压时,金属液沿着通道从射嘴头填充至压铸模型腔中凝固成型,压射锤头回升,开模取出铸件,完成一个压铸循环,如图1-2所示。
图1-2
二、主要结构分析
现以力劲机械厂有限公司生产的热室压铸机为例来分析热室压铸机的主要结构,如1-3所示为力劲热室压铸机总体结构示意图。
(一)合模装置
合模装置若按实现合模力的方式分为三种:机械式合模装置、液压式合模装置、液压机械式合模装置。
机械式合模装置:电动机的动力由齿轮、曲肘、连杆传动、使动型座板沿拉杆作开、合模运动,整个装置调整复杂,目前已很少采用。
1、液压双曲肘合模装置的工作特点
(1)增力作用:通过曲肘连杆系统,可以将合模液压缸的推力放大16-26倍,与液压式合模装置相比,高压油消耗减小、合模液压缸直径减小、泵的功率相应减小。
(2)合、开模运动速度为变速:如图1-5所示,在合模过程中,动型座板移动速度由零很快升到最大值,以后又逐渐减慢,随着曲肘杆逐渐伸直至终止时,合模速度为零,机构进入自锁状态(锁模状态)。
在开模过程中,动型座板移动由慢速转至快速,再由快速转慢至零。
非常符合机器整个运动设计要求。
(3)当压铸模合紧且肘杆伸直时,可以撤去合模(锁模)液压缸的推力,合模系统仍然会处于合紧状态。
2、顶针液压缸组件
目前普遍采用液压顶出装置,其顶出力、速度、时间都可以通过液压系统调节。
如图1-6所示为力劲热室压铸机顶针液压缸组件图。
在机器开模后,顶针液压缸活塞杆推出,从而带动压铸模中的推杆将铸件从模具型腔中顶出。
3、调模机构
压铸机在设计过程中,需要设置调模装置以适用在一定范围内的各种压铸模,在机器技术参数中,应确定最大模具厚度和最小模具厚度尺寸作为机器使用者选定压铸模的参数,如图1-12所示。
这个最大与最小模具厚度的调整量是通过调模装置实现的。
如图1-4所示,调模装置是用调模电动机或液压马达带动传动机构使锁模柱架的尾板和动型座板沿拉杆作轴向运动,从而达到增大或缩小动、定型座板之间间距的目的。
(二)压射装置
压射装置的结构性能对压射力、压射速度和压铸件的质量起着决定性的作用,如图1-7所示为力劲热室压铸机压射装置图,在压射立座上装配有压射液压缸组件和扣嘴液压缸组件及液压蓄能器(见图1-3),压射活塞杆在液压油的作用下按一定的速度向上(或向下)运动,从而带动压射锤头在压射室内运动,压射速度分为两段,第二段速度由于液压蓄能器的液压补充而实现快速压射,并可用调速手轮调节压射速度。
扣嘴液压缸组件的作用是通过扣嘴活塞杆的运动带动合(锁)模柱架运动,使安装在定型座板上的模具入料口离开射嘴头或与射嘴头吻合。
(三)液压蓄能器装置
液压蓄能器的用途是在液体压力下容纳一个液体量,并在需要时再给出。
液压蓄能器的种类及结构如图1-8所示,热室压铸机一般采用第3、4种,在压射运动中起增压作用。
1—重量式蓄能器
2—弹簧式蓄能器
3—活塞式蓄能器
4—气囊式蓄能器
5—薄膜式蓄能器
图1-8 蓄能器的种类
活塞式蓄能器主要适用于大体积和大流量,其中氮气和液体被一个自由运动的活塞分
离。
活塞在一个液压缸套中活动并通过密封圈分别密闭气体和液体,最大增压比,即气体压力对最大工作压力的比例为1:10。
预先充填压力应低于最小工作压力5bar。
气囊式蓄能器:氮气和液体由密封的弹性皮囊分离,氮气是在皮囊中,最大压力为1:4。
它的工作特点是:感应灵敏、迅速、运行惯性低。
气囊式蓄能器的结构如图1-9所示。
气囊式蓄能器的工作原理:如图1-10所示,充液时,液压系统的液压油推开盘形阀流入钢质容器内并将皮囊中的氮气压缩至一定体积;放出液体时,液压油从盘形阀口流出进入到所需容器,气囊中的氮气压力起推动液压油、压紧盘形阀的作用。
盘形阀能限制气囊被压
出孔外。
压铸机的动作流程
热室压铸机的动作循环一般以模具闭合时开始计算。
通过锁模油缸和双曲肘放大机构的工作,将模具闭合,在闭合过程式经历锁模压力、锁模低压当确认模具内无异物时,高压锁模将模具锁紧。
当确认模具锁紧时,锁模装置作扣前动作,使射咀与模具入水口贴合,位置确认到位后,压射系统才以高速、高压将金属熔液压射到型腔内。
当熔料在型腔内冷却凝固后,即开模时间到后,压射头回位,同时作扣后动作。
使射咀头
与温度较低的模具分开。
开模时间到后,模具开型由高压到开模压力,由开型时的慢速到快速到慢速,以防止对机
铰及尾板的冲击。
开模到位并感应到开模终止吉制,顶出装置将零件顶出。
由机械手将零件冲落,零件
落下时由电眼自动检测计数。
然后由喷雾装置向模腔喷射脱模剂后,关门到位进行下一个循
环。