冻干技术指导原则(4.21)1
现代冻干技术

现代冻干技术岳兵为了生存,人类摄取食物需要水分; 为了生存,人类保存食物必须去除水分; 为了更好地生存,人类很多生活资料必须彻底地去除水分。
---Mr.Yarlish1.冻干的应用干燥是保持物质不致腐败变质的方法之一。
干燥的方法许多,如晒干、煮干、烘干、 喷雾干燥和真空干燥等。
但这些干燥方法都是在 0℃以上或更高的温度下进行。
干燥所得 的产品,一般是体积缩小、质地变硬,有些物质发生了氧化,一些易挥发的成分大部分会 损失掉,有些热敏性的物质,如蛋白质、维生素会发生变性。
微生物会失去生物活力,干 燥后的物质不易在水中溶解等,更谈不上外观或性能的恢复,因此干燥后的产品与干燥前 相比在性状上有很大的差别。
冷冻干燥就是把含有大量水分的物质,预先进行降温冻结成固体,然后在真空的条件 下使水蒸汽直接升华出来,而物质本身剩留在冻结时的冰架中,因此它干燥后体积不变, 疏松多孔冻干过程1.1.冷冻干燥的特点:1食品伙伴网一.冷冻干燥在低温下进行,因此对于许多热敏性的物质特别适用。
如蛋白质、微生物之 类不会发生变性或失去生物活力。
食品的营养成分和风味损失很少,可以最大限度地保留 原有的成分、味道、色泽和芳香。
因此在医药、食品、植物学等方面得到广泛地应用。
二.在低温下干燥时,物质中的一些挥发性成分损失很小,适合一些化学产品,药品和食 品干燥。
三.在冷冻干燥过程中,微生物的生长和酶的作用无法进行,因此能保持原来的性状。
四.由于在冻结的状态下进行干燥,因此体积几乎不变,保持了原来的结构,不会发生浓 缩现象。
2食品伙伴网所以,在考古,档案保存方面也有特定的应用价值。
五.由于物料在升华脱水以前先经冻结,形成稳定的固体骨架,所以水分升华以后,固体 骨架基本保持不变、干制品不失原有的固体结构,保持着原有形状,多孔结构的制品呈海 绵状具有很理想的速溶性和快速复水性。
冻干后的产 品结构六.由于物料中水分在预冻以后以冰晶的形态存在,原来溶于水的无机盐之类的溶解物质 被均匀分配在物料之中。
冻干技术指导原则
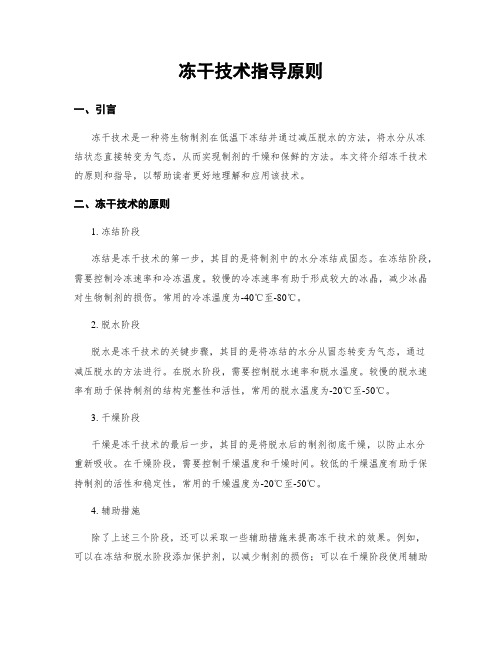
冻干技术指导原则一、引言冻干技术是一种将生物制剂在低温下冻结并通过减压脱水的方法,将水分从冻结状态直接转变为气态,从而实现制剂的干燥和保鲜的方法。
本文将介绍冻干技术的原则和指导,以帮助读者更好地理解和应用该技术。
二、冻干技术的原则1. 冻结阶段冻结是冻干技术的第一步,其目的是将制剂中的水分冻结成固态。
在冻结阶段,需要控制冷冻速率和冷冻温度。
较慢的冷冻速率有助于形成较大的冰晶,减少冰晶对生物制剂的损伤。
常用的冷冻温度为-40℃至-80℃。
2. 脱水阶段脱水是冻干技术的关键步骤,其目的是将冻结的水分从固态转变为气态,通过减压脱水的方法进行。
在脱水阶段,需要控制脱水速率和脱水温度。
较慢的脱水速率有助于保持制剂的结构完整性和活性,常用的脱水温度为-20℃至-50℃。
3. 干燥阶段干燥是冻干技术的最后一步,其目的是将脱水后的制剂彻底干燥,以防止水分重新吸收。
在干燥阶段,需要控制干燥温度和干燥时间。
较低的干燥温度有助于保持制剂的活性和稳定性,常用的干燥温度为-20℃至-50℃。
4. 辅助措施除了上述三个阶段,还可以采取一些辅助措施来提高冻干技术的效果。
例如,可以在冻结和脱水阶段添加保护剂,以减少制剂的损伤;可以在干燥阶段使用辅助干燥剂,以加快干燥速度;还可以在整个过程中进行监测和控制,以确保冻干过程的稳定性和一致性。
三、冻干技术的应用冻干技术在生物制药、食品工业、化妆品等领域有着广泛的应用。
以下是一些冻干技术的应用案例:1. 生物制药冻干技术被广泛应用于生物制药领域,用于制备蛋白质药物、疫苗、抗体等生物制剂。
通过冻干技术,可以将生物制剂制备成干粉状,便于储存、运输和使用,同时保持制剂的活性和稳定性。
2. 食品工业冻干技术在食品工业中用于制备冻干食品,例如冻干蔬菜、水果和咖啡等。
通过冻干技术,可以将食品中的水分脱除,延长食品的保质期,同时保持食品的营养成分和口感。
3. 化妆品冻干技术在化妆品领域中用于制备冻干粉状化妆品,例如冻干面膜和冻干粉底等。
冻干机工艺的一般原则和标准操作规程

冻干机工艺的一般原则和标准操作规程第四章冻干工艺的一般原则和标准操作规程第一节冻干工艺的一般原则制品的冻干过程是一个较为复杂的工艺过程。
它不仅要求该过程严格遵守制品的冻干工艺曲线而且要求所使用的冻干设备也同时能够满足它的要求。
本章节对冻干工艺的一般过程提出一些指导性原则仅供操作人员在使用的过程中结合自身制品的特性进行参考。
冷冻干燥过程共分三个过程即预冻结过程、升华干燥第一阶段干燥过程、解析干燥第二阶段干燥过程。
一、预冻结过程预冻是冷冻干燥的第一步在预冻结过程中预冻速率、预冻温度和预冻时间是影响后面过程的主要因素。
若预冻没有冻好产品冻结不实在进入第一阶段升华干燥时产品可能出现“沸腾”现象而引起喷瓶或冻干后制品表面凹凸不平影响外观如果冷的过低则不仅浪费了能源和时间。
而且对某些产品还会降低存活率。
因此预冻之前应确定以上三个数据。
1、预冻速率预冻速率的快慢对制品冻结中晶粒的大小、活菌的存活率和升华的速率均有影响。
一般来说慢冻晶粒大产品外观粗糙不容易损伤活菌但升华速度快而速冻则与此相反。
因此需要选择一个合理的冷却速度以得到较高的存活率较好的物理性状和溶解度且利于干燥过程中的升华。
2、预冻温度预冻温度必须低于制品的共晶点温度根据预冻的方法不同而略有差异一般来说搁板温度应低于制品共晶点510?。
各种制品的共晶点温度是不同的同一制品而不同浓度的制品的共晶点温度也会有所不同。
需要进行严格的测试才能得到。
3、预冻时间预冻所需的时间要根据不同的具体条件来确定。
总的原则是应使制品的各部分完全冻牢。
通常冻干箱的搁板从室温25?降到-40?预冻时间约1.5小时。
在达到预冻温度后再保持12小时确保整箱全部制品完全冻结。
仅是个经验值根据冻干机不同总装量不同物品与搁板之间接触不同预冻的时间会有差异。
具体预冻时间可由实验测得。
二、升华干燥过程在升华干燥阶段要考虑三方面的因素产品中的温度分布升华时的温度限制升华速率。
1、产品中温度分布产品中冰的升华是在升华界面处进行升华时所需的热量由加热设备通过搁板提供。
冻干工艺确认

冻干工艺确认一、冻干原理介绍冻干工艺是一种通过冷冻和升华过程去除水分的方法。
在冷冻阶段,物料被冷却到冰点以下,水分形成冰晶。
在升华阶段,冰晶直接从固态转化为气态,从而去除水分。
冻干工艺具有较好的保存物料原有结构和营养成分的优点,广泛应用于药品、食品、生物制品等领域。
二、设备与工具介绍冻干工艺需要使用冻干机来实现。
冻干机主要由制冷系统、真空系统、加热系统和控制系统等组成。
常用的工具有称量纸、量筒、烧杯、移液管等,用于物料的称量、配制和转移等操作。
三、物料准备与处理在物料准备阶段,需要根据工艺要求对物料进行筛选、清洗和预处理。
对于一些特殊物料,需要进行特定的处理,如破碎、混合、调节pH值等。
物料的处理过程需严格控制,确保其质量和纯度满足要求。
四、操作过程确认操作过程确认是确保冻干工艺稳定和可靠的关键环节。
在操作过程中,需要确认物料的配制、装盘、搁架的摆放、温度和真空度的控制等步骤的准确性和合理性。
此外,还需要根据物料的特性和要求调整工艺参数,以达到最佳的冻干效果。
五、质量检测与控制质量检测和控制是确保冻干工艺产品质量的重要措施。
在检测和控制过程中,需要对物料的成分、颜色、水分含量等指标进行检测和分析。
同时,还需要对冻干产品的外观、结构、营养成分等进行评估和检测,确保产品符合相关标准和客户要求。
六、冻干效果评估冻干效果评估是对冻干工艺效果的评价和总结。
评估内容包括冻干产品的外观、含水量、复水性、营养成分保留情况等。
通过对这些指标的综合评价,可以对冻干工艺的效果进行全面的评估和总结,为后续的工艺改进和优化提供依据。
七、安全风险评估在冻干工艺过程中,可能存在一些安全风险,如机械故障、电气事故、化学品泄漏等。
因此,需要对整个工艺过程进行安全风险评估,识别潜在的安全隐患,并采取相应的措施进行预防和控制。
同时,还需要加强员工的安全培训和教育,提高员工的安全意识和应急处理能力,确保生产安全。
冻干工艺经验

冻干知识培训真空冷冻干燥的原理第一节冷冻干燥的原理干燥是保持物质不致***变质的方法之一。
干燥的方法许多,如晒干、煮干、烘干、喷雾干燥和真空干燥等。
但这些干燥方法都是在0℃以上或更高的温度下进行。
干燥所得的产品,一般是体积缩小、质地变硬,有些物质发生了氧化,一些易挥发的成分大部分会损失掉,有些热敏性的物质,如蛋白质、维生素会发生变性。
微生物会失去生物活力,干燥后的物质不易在水中溶解等。
因此干燥后的产品与干燥前相比在性状上有很大的差别。
而冷冻干燥法不同于以上的干燥方法,产品的干燥基本上在0℃以下的温度进行,即在产品冻结的状态下进行,直到后期,为了进一步降低产品的残余水份含量,才让产品升至0℃以上的温度,但一般不超过40℃。
冷冻干燥就是把含有大量水分物质,预先进行降温冻结成固体,然后在真空的条件下使水蒸汽直接升华出来,而物质本身剩留在冻结时的冰架中,因此它干燥后体积不变,疏松多孔在升华时要吸收热量。
引起产品本身温度的下降而减慢升华速度,为了增加升华速度,缩短干燥时间,必须要对产品进行适当加热。
整个干燥是在较低的温度下进行的。
冷冻干燥有下列优点:一.冷冻干燥在低温下进行,因此对于许多热敏性的物质特别适用。
如蛋白质、微生物之类不会发生变性或失去生物活力。
因此在医药上得到广泛地应用。
二.在低温下干燥时,物质中的一些挥发性成分损失很小,适合一些化学产品,药品和食品干燥。
三.在冷冻干燥过程中,微生物的生长和酶的作用无法进行,因此能保持原来的性装。
四.由于在冻结的状态下进行干燥,因此体积几乎不变,保持了原来的结构,不会发生浓缩现象。
五.干燥后的物质疏松多孔,呈海绵状,加水后溶解迅速而完全,几乎立即恢复原来的性状。
六.由于干燥在真空下进行,氧气极少,因此一些易氧化的物质得到了保护。
七.干燥能排除95-99%以上的水份,使干燥后产品能长期保存而不致变质。
因此,冷冻干燥目前在医药工业,食品工业,科研和其他部门得到广泛的应用。
冻干粉针剂(化学制剂)生产质量技术指导原则
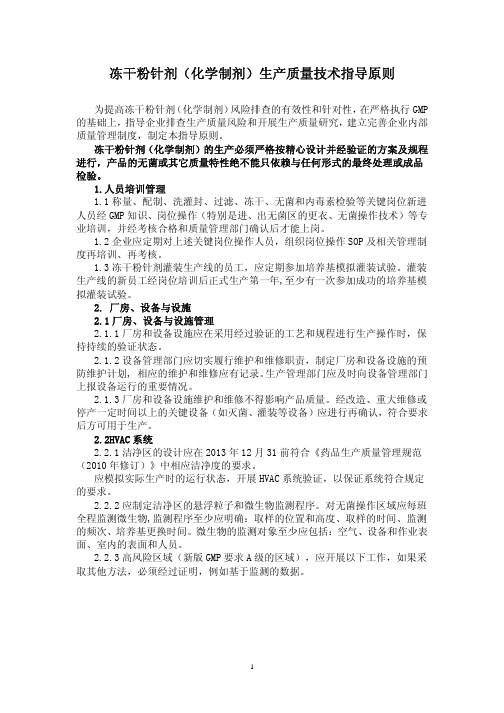
冻干粉针剂(化学制剂)生产质量技术指导原则为提高冻干粉针剂(化学制剂)风险排查的有效性和针对性,在严格执行GMP 的基础上,指导企业排查生产质量风险和开展生产质量研究,建立完善企业内部质量管理制度,制定本指导原则。
冻干粉针剂(化学制剂)的生产必须严格按精心设计并经验证的方案及规程进行,产品的无菌或其它质量特性绝不能只依赖与任何形式的最终处理或成品检验。
1.人员培训管理1.1称量、配制、洗灌封、过滤、冻干、无菌和内毒素检验等关键岗位新进人员经GMP知识、岗位操作(特别是进、出无菌区的更衣、无菌操作技术)等专业培训,并经考核合格和质量管理部门确认后才能上岗。
1.2企业应定期对上述关键岗位操作人员,组织岗位操作SOP及相关管理制度再培训、再考核。
1.3冻干粉针剂灌装生产线的员工,应定期参加培养基模拟灌装试验。
灌装生产线的新员工经岗位培训后正式生产第一年,至少有一次参加成功的培养基模拟灌装试验。
2. 厂房、设备与设施2.1厂房、设备与设施管理2.1.1厂房和设备设施应在采用经过验证的工艺和规程进行生产操作时,保持持续的验证状态。
2.1.2设备管理部门应切实履行维护和维修职责,制定厂房和设备设施的预防维护计划, 相应的维护和维修应有记录。
生产管理部门应及时向设备管理部门上报设备运行的重要情况。
2.1.3厂房和设备设施维护和维修不得影响产品质量。
经改造、重大维修或停产一定时间以上的关键设备(如灭菌、灌装等设备)应进行再确认,符合要求后方可用于生产。
2.2HVAC系统2.2.1洁净区的设计应在2013年12月31前符合《药品生产质量管理规范(2010年修订)》中相应洁净度的要求。
应模拟实际生产时的运行状态,开展HVAC系统验证,以保证系统符合规定的要求。
2.2.2应制定洁净区的悬浮粒子和微生物监测程序。
对无菌操作区域应每班全程监测微生物,监测程序至少应明确:取样的位置和高度、取样的时间、监测的频次、培养基更换时间。
制剂的冻干原理和技术
[医用制剂]制剂药品的冻干原理和技术药用制剂原理-工艺-技术篇:对制剂药品冷冻干燥方法、冻干工艺优缺点及冻干机设备组成的介绍。
制剂药品的冻干原理和技术冷冻真空干燥是制剂药品常用的一种干燥方法,简称冻干。
冷冻干燥是保持物质不致腐败变质的方法之一。
干燥的方法有很多,比如晒干、煮干、烘干、喷雾干燥以及真空干燥。
但这些方法都是在0℃以上或更高的温度下进行的。
干燥的产品一般是体积缩小;质地变硬;有些物质发生了氧化;一些易挥发的成分会损失掉;一些热敏性的物质,如维生素、蛋白质会发生变性;微生物失去生物活力;干燥后的物质不易溶解在水中。
因此,干燥后的产品与干燥前相比在性状上有很大的差别。
而冷冻干燥不同于以上的干燥方法,产品的干燥基本上在0℃以下的温度进行,即在产品冻结状态下进行的。
直到后期,为进一步降低产品的残余水份,才让产品的温度升高到0℃以上,但通常不超过40℃。
制剂药品的冷冻干燥就是把液态的药品预先降温冻结成固体。
然后在真空条件下使冻结的水分以水蒸气的形态从固体中升华出来,而药品的有效成分剩留在冻结时的冰架子中,因此制剂药品干燥后的体积不变、疏松多孔。
冰在升华时要吸收热量,从而引起冻结药品制剂本身温度的下降,导致升华速度的减慢,为了增加升华的速度,缩短干燥时间,就必须对药品进行适当的加热。
整个干燥是在较低的温度下进行的。
制剂药品的冻干工艺有以下的优点:(1)液体药剂加工方便,简化了无菌作业的过程,冻干过程是在低温下进行,因此对许多热敏性的物质特别适用。
如生物药剂中的活性蛋白质、微生物之类的制剂,不会在冻干过程中发生变性或失去生物的活性。
因此在冻干技术在医药上得到广泛的应用。
(2)在低温干燥过程中,制剂药品中一些挥发性成份损失很小。
(3)在冷冻干燥过程中,微生物的生长和活性酶的作用无法进行,因此保持原来的性状,提高了干粉的稳定性。
(4)由于在冻结状态下进行干燥,因此制剂药品的体积几乎不发生变化,保持了原来的结构,不会发生浓缩现象。
冷冻干燥操作指南
一、预冻样品盘或西林瓶盛装的液态样品需放在超低温冰箱中预冻。
预冻温度取决于所做样品的冰点,Tpre-freezing Tfreezing point -10℃。
如果冰点未知,应在-40℃下冷冻2小时以上。
最好过夜。
有两种冷冻方式:1.静态冷冻:将样品盘或西林瓶放在搁板上,搁板与样品应同时放在超低温冰箱中预冻。
2.旋转冷冻:圆底烧瓶或桶形冻干瓶盛装的液态样品需放在旋冻器或液氮中旋转冷冻,直至样品均匀地涂布在冻干瓶表面。
注意:以上两种冷冻方式,样品厚度均不能超过1cm。
二、准备仪器及使用仪器操作顺序:1.先打开真空泵,预热约20~30分钟;关闭泵。
2.打开主机电源开关,观察控制器上的冷凝室温度显示,当冷凝室内的温度降至-40℃以下时,将预冻好的样品和搁板从超低温冰箱中取出,放在干燥室内。
3.检查所有的外挂瓶阀,确认其处于关闭状态(大头向上)。
4.检查仪器右侧的放水阀,确认其处于关闭状态。
5.打开真空泵,使系统开始抽真空。
观察控制器上的真空值显示,当真空值降至0.1mbar以下时,主干燥开始。
外挂瓶操作的注意事项:1.只有当真空值降至0.1mbar以下时,才可挂外挂瓶。
2.将预冻好样品的冻干瓶顶在阀口,将橡胶阀非常缓慢地旋至开启状态(大头向下),确定瓶被吸牢后,外挂瓶挂好。
干燥时间应根据样品种类的不同及干燥条件的不同,控制在12~24小时左右。
三、结束实验及关闭仪器关闭仪器顺序:1.先卸外挂瓶:将橡胶阀缓慢地旋至关闭状态(大头向上),待放气声完全停止后,再拆下外挂瓶。
2.外挂瓶全部卸完后,关闭真空泵。
3. 从任一橡胶阀口非常缓慢地向开启方向旋转阀门,听到轻微放气声时,停止等待气体进入. 观察控制器上的真空值显示,当真空值显示在200mbar以上时,可稍微增大放气量.直至与外界大气压平衡时,将全部阀门打开。
4.关闭主机,移走罩子(注意:一定要将罩子反放在垫子上),取出样品。
5. 实验结束后,必须要对冷凝室进行除霜,用干净的布擦净腔内的水分,保持腔体内清洁;从主机侧板上拉出排水管,接好容器,打开放水阀,将除霜水放净,关闭放水阀。
冻干工艺知识
冻干粉针异常现象寻根究底在冻干粉针的生产过程中,经常会出现一些异常情况,影响产品质量。
生产人员必须从产品的处方设计、生产工艺参数、生产环境的控制、操作员工的卫生情况等多方面进行有效控制,并对生产设备、洁净区环境、冻干曲线等进行有效验证,才能有效地避免冻干产品的异常现象,提高产品质量。
现象一:含水量超标冻干粉针剂质量标准中规定的含水量较低。
造成其含水量超过标准的主要原因是:装入容器的药液过多,药液层过厚;干燥过程中供热不足,使其蒸发量减少;真空度不够,水蒸气不能顺利排出;冷凝室温度偏高,不能有效地将水蒸气捕集下来;冻干时间较短;真空干燥箱的空气湿度高;出箱时制品温度低于室温而出现制品吸湿等。
措施:生产人员须针对不同原因采取相应的解决方法。
如按药液体积调整西林瓶规格,减少装液厚度,一般应控制在10~15mm;加强热量供给,促进水分蒸发;检查真空度不高的原因,排除泄漏点或真空系统的异常;降低冷凝器温度在-60℃以下;重新试制冻干曲线,确保冻干制品含水量合格;对放入箱内的气体要进行除菌及脱水干燥处理,尤其是易吸潮的制品更要注意;制品出箱时的温度要略高于生产环境温度。
现象二:喷瓶喷瓶是由于预冻时温度没有达到制品共熔点以下,制品冻结不实;或升华干燥时升温过快,局部过热,部分制品溶化成液体,在高真空度条件下,少量液体从已干燥固体表面穿过孔隙喷出而形成。
措施:为了防止喷瓶,应严格控制预冻温度在共熔点以下10℃~20℃,并保持2小时以上,使药品冻实后再升温。
同时升华干燥时的供热量要控制好,适当放慢升温速度,且控制温度不超过共熔点。
这样可以克服喷瓶现象。
现象三:外观不合格冻干粉针的正常外观应是颜色均匀,孔隙致密,保持冻干前的体积、形状基本不变,形成块状或海绵状团块结构。
但是,如果溶液重量浓度大于30%,则制品易出现萎缩、塌陷、不饱满的情况。
另外,干燥时冻结的表面最先脱水形成结构致密的干燥外壳,下面升华的水蒸气从已干燥表层的分子之间的间隙逸出。
冻干工艺
(二)冷冻干燥制品的工艺
水溶液
预先冻结
升华除去水分
高温低压
再干燥
干燥
(二)冷冻干燥制品的工艺
• 1. 测定产品共熔点 • 新产品冻干时,先应测出其低共熔点 (eutectic point),然后控制冷冻温度在低共 熔点以下,以保证冷冻干燥的顺利进行。 • 低共熔点是在水溶液冷却过程中,冰和溶 质同时析出结晶混合物(低共溶混合物)时的 温度。 • 测定低共熔点的方法有热分析法和电阻法, 热分析法通过绘制冷却曲线就可求出。
第五节 注射用无菌粉末
• 注射用无菌粉末简称粉针。凡是在水溶液 中不稳定的药物,如青霉素G、先锋霉素 类及一些医用酶制剂(胰蛋白酶、辅酶A)及 血浆等生物制剂,均需制成注射用无菌粉 末。 • 将冷冻干燥法制得的粉末,称为注射用冷 冻干燥制品, • 而用其它方法如灭菌溶剂结晶法、喷雾干 燥法制得的称为注射用无菌分装产品。
(4)再干燥:当升华干燥阶段 完成后,为尽可能除去残余的水, 需要进一步干燥。 • 再干燥温度,根据制品性质确定, 如0℃、25℃等。制品在保温干 燥一段时间后,整个冻干过程即 告结束
(三) 冷冻干燥过程中常出现的异常现象及处理方 法
• 1.含水量偏高 • 装入容器液层过厚,超过10~15mm; • 干燥过程中热量供给不足,使蒸发量减少; 真空度不够,冷凝器温度偏高等,均可造 成含水量偏高, • 可采用旋转冷冻机及其它相应的办法解决。
(二)生产工艺
• 1. 原材料准备 • 安瓿或小瓶及胶塞均按本章第三节和第四 节所述方法处理,但均需进行灭菌。 • 无菌原料可用灭菌结晶法、喷雾干燥法制 备,必要时需进行粉碎,过筛等操作,
• 2. 分装 • 分装必须在高度洁净的无菌室中按照无菌 操作法进行。 • 用人工或机器分装,分装机宜有局部层流 装置。
- 1、下载文档前请自行甄别文档内容的完整性,平台不提供额外的编辑、内容补充、找答案等附加服务。
- 2、"仅部分预览"的文档,不可在线预览部分如存在完整性等问题,可反馈申请退款(可完整预览的文档不适用该条件!)。
- 3、如文档侵犯您的权益,请联系客服反馈,我们会尽快为您处理(人工客服工作时间:9:00-18:30)。
冻干粉针剂(化学制剂)药品质量安全专项工作生产质量技术指导原则为了提高冻干粉针剂(化学制剂)生产质量风险评估、管理的有效性,指导企业在严格执行GMP的基础上,有序开展药品生产质量风险排查和生产质量研究,进一步完善企业内部质量管理制度。
在新版GMP实施前,我们在相关企业质量风险管理经验的基础上,针对关键工序和岗位,制定了本指导原则。
冻干粉针剂(化学制剂)的生产必须严格按精心设计并经验证的方案及规程进行,产品的无菌或其它质量特性绝不能只依赖与任何形式的最终处理或成品检验。
1.人员培训管理1.1称量、配制、灌封、过滤、冻干、无菌和内毒素项目检验等关键岗位新进人员经GMP知识、岗位操作等专业培训、考核合格后,经质量管理部门确认后才能上岗。
无菌区操作人员的培训、考核,应重点关注进、出无菌区的更衣和无菌操作要求(包括生产操作和安装时的姿势、动作幅度及速率等)。
1.2企业应定期对上述关键岗位操作人员,组织岗位操作SOP及相关管理制度再培训、再考核。
1.3冻干粉针剂灌装生产线的员工,应定期参加培养基模拟灌装试验。
灌装生产线的新员工经岗位培训后,在正式上岗生产的第一年内,至少有一次参加成功的培养基模拟灌装试验。
2. 厂房、设备与设施2.1厂房、设备与设施管理2.1.1厂房和设备设施应采用经过验证的工艺和规程进行生产操作,并应保持持续的验证状态。
2.1.2设备管理部门应切实履行维护和维修职责,制定厂房和设备设施的预防维护计划, 相应的维护和维修应有记录。
生产管理部门应及时向设备管理部门上报设备运行的重要情况。
2.1.3厂房和设备设施维护和维修不得影响产品质量。
经改造、重大维修或停产一定时间以上的关键设备(如灭菌、灌装等设备)应进行再确认或评估,符合要求后方可用于生产。
2.2HVAC系统2.2.1洁净区的洁净要求应在2013年12月31前,符合《药品生产质量管理规范(2010年修订)》中相应洁净度的要求。
应开展HVAC系统验证,验证结果符合规定,并与实际生产相适应。
2.2.2应制定洁净区的悬浮粒子和微生物监测程序。
应对无菌操作区域微生物进行动态监测,监测程序至少应明确:取样的位臵和高度、取样的时间、监测的频次、培养基更换时间。
对表面和操作人员的监测,应当在关键操作完成后进行。
2.2.3高风险区域(新版GMP要求A级的区域),应开展以下工作,如果采取其他方法,必须经过证明,例如基于监测的数据。
项目及内容频次要求(至少)悬浮粒子静态测试1次/3月空气流速测定1次/半年高效过滤器的完整性测试(应采用气溶胶法)1次/年流向/型测试(如气雾试验录像)1次/年环境和人员微生物监控每班备注:设备、厂房等采用表面取样法,应开展回收率验证,考虑操作的可重复性。
ISO14644推荐使用接触盘水平采样点的理想方法如下:培养基表面应与采样点接触不少于10s(或按说明书进行操作),向整个接触表面施加恒定均匀的压力(如施加的质量约为25g/cm2),不得有环形或线性运动。
装臵有接触并拿开后,要加盖并尽快用适当的培养条件培养。
2.2.4应建立适当压差控制。
在压差十分重要的相邻级别区域之间应安装压差表,记录压差数据,并在结果超标时有明确的纠偏措施。
推荐在灌装间等核心区域建立压差超标的报警系统。
2.2.5连续生产时,无菌区空气净化系统必须保持连续运行,维持相应的洁净度级别。
推荐设立送风机组故障的报警系统。
生产过程中因故停机再次开启空气净化系统,时限应在验证范围内,并应经评估和确认此次偏差不影响产品质量,产品才能放行。
较长时间的停机后再次开启空气净化系统,应当进行必要的测试以确认能达到规定的洁净级别要求。
2.2.6结合验证和历史数据回顾分析,制定适当的悬浮粒子和微生物监测警戒限度和纠偏限度,并在结果超标时有明确的纠偏措施。
2.3注射用水系统2.3.1应模拟实际生产时的运行状态,开展注射用水系统验证,以保证工艺用水符合规定的要求。
根据验证结果确定运行、监控等管理制度,保证注射用水系统按验证要求持续运行。
2.3.2连续生产时,注射用水系统应保持70℃以上保温循环,循环水泵不得停止工作。
注射用水系统停用(循环水泵停止工作)超过验证时限的,恢复使用前应对全系统进行清洁、消毒,并按规定检测符合要求(微生物限度除外)后才能投入使用。
但产品放行审核时,注射用水监测结果必须作为放行的依据。
2.3.3 注射用水系统日常运行使用时,企业应该制定注射用水系统取样和监控计划,应在线监控总送、回水管及储罐的温度,并定期监测微生物、细菌内毒素、总有机碳等指标。
2.3.4应当制定注射用水系统水质监测的警戒限度和纠偏限度,进行趋势分析,并在结果超标时有明确的纠偏措施。
2.3.5注射用水系统应定期维护、保养及处理,定期对呼吸器、过滤器进行完整性检查。
2.3.6应建立注射用水系统的清洗和消毒规程,规程至少应明确:清洗和消毒的方法、采用的清洗剂或消毒剂的名称、清洗和消毒的频次。
注射用水系统使用纯蒸气消毒的,至少应明确压力、温度、时间等参数,消毒前应对管路排空情况进行确认。
2.4纯蒸汽2.4.1 应制定企业内控质量标准和检验标准操作程序,定期对纯蒸汽进行检验。
其内控质量参照注射用水质量标准,至少包括细菌内毒素。
2.5过滤系统2.5.1应制定过滤系统除菌性能试验计划,及时开展验证工作。
除菌过滤器使用后,必须采用适当的方法立即对其完整性进行检查并记录。
2.5.2应当采取措施降低过滤除菌的风险。
宜安装第二只已灭菌的除菌过滤器再次过滤药液,最终的除菌过滤滤器应当尽可能接近灌装点。
2.5.3应根据验证和过滤器材质、孔径及耐压范围、耐温范围、耐酸碱范围等情况,确定工艺参数,包括压力、时间、温度,确定过滤器的清洗、安装、灭菌(温度、压力、时间)、使用次数、灭菌前后的储存等要求。
不同品种产品不应交叉使用除菌过滤器,对除菌过滤器进行编号管理。
2.5.4任何明显偏离正常时间或压力的情况应当有记录并进行调查,调查结果应当归入批记录。
2.6灭菌设备2.6.1灭菌柜(含隧道烘箱)的温度分布测试、灭菌情况再确认及其高效过滤器的检漏工作,至少1次/年。
隧道烘箱还应当开展风速及悬浮粒子数监测,至少1次/年。
2.6.2所有灭菌设备所用热电偶等测温设备在验证前均应校正。
对腔室底部有排水口的灭菌柜,应测定并记录该点在灭菌全过程中的温度数据。
2.6.3湿热灭菌柜灭菌时需真空操作的,每年还应对腔室做检漏测试。
应定期对灭菌配备的呼吸器进行完整性测试。
2.6.4委托第三方进行确认/验证的,企业质量管理部门必须参与全过程,并对方法及数据进行确认。
2.6.5实际生产时,应严格按确认/验证时确定的灭菌温度、压力、时间、装载量及装载分布(用照片或图片记录)、传送速度(专指隧道烘箱)进行灭菌。
2.7冻干设备2.7.1冻干机温度分布测试(热分布试验)、真空泄漏率检查,至少1次/年。
在以下情况下应进行泄漏测试:①真空状态恶化时;②泄漏率超过警戒标准进行校准和纠偏后;③根据历史记录和经验设定的确认周期已不满足实际情况的需要时;④经过检修后,可能影响真空状态的。
2.7.2采用CIP进行在线清洗的,应定期对清洁方法进行确认,以达到设定的要求。
对于带有SIP的冻干机,每年需对SIP效果进行生物指示剂挑战试验。
如果调整灭菌程序,需重新进行验证试验。
2.7.3采用人工方式进行清洁/消毒的,应有详细的操作程序以保证每次清洗/消毒操作的一致性。
其清洁/消毒方法应进行必要的验证,如清洁/消毒后对最难清洗点进行擦拭取样,擦拭样的微生物检测结果应≤1CFU,并合理规定擦拭点位臵、面积及擦拭要求。
并定期对清洁状况进行监测,如可见异物、TOC和电导率等。
2.7.4应定期对冻干设备进行维护保养和确认,对冻干设备自带的过滤器进行完整性检测。
2.8与药品(含内包材,下同)直接接触的气体2.8.1应对与药品直接接触的(包括用于吹扫西林瓶内注射用水、药液压滤、冻干后恢复平衡等)气体系统进行验证和定期的再验证,以保证符合要求。
与灭菌后的内包材和除菌过滤后药液直接接触的气体,还应定期监测,项目至少包括微生物、悬浮粒子、油份、水份等。
2.8.2应根据验证情况和使用期限等有关数据,定期检查与药品直接接触的气体如压缩空气、氮气过滤器及呼吸器的完整性。
3.生产管理3.1人员操作3.1.1无菌操作区的人员应严格控制(不得超过培养基灌装验证时的人数),并按经验证的规程进行生产,不得用手或洁净服的任何部位直接接触产品、无菌包装材料、关键表面。
3.1.2无菌操作区的人员应避免快速走动或操作,并尽量避免身体进入仍处于敞口状态的产品或包材等上方的保护层流。
并定期对人员的手部、口罩进行消毒或更换。
3.1.3无菌操作区的人员每次进入无菌区域,应重新更换无菌外衣,已更换的无菌外衣未清洗灭菌前不得重复使用。
3.1.4灌装开始到冻干进箱前,应尽量避免操作人员进、出灌装间。
3.2容器具、管道及设备的清洗、消毒及灭菌3.2.1所有直接接触药品的容器、用具、滤器、管道、设备等,均应按照要求进行清洗、灭菌,并尽可能选用适宜的方法除去热原。
3.2.2对于采用塑料、橡胶等材质制造的容器具、硅胶管、灌装针、滤器、滤膜等,采用湿热灭菌的方式灭菌,并应经验证。
3.2.3对于不锈钢或者玻璃等可耐高温的容器具,应采用干热灭菌的方法除去热原、灭菌。
3.2.4对于较大型的配制罐、药液储罐系统,应选用在线清洗(CIP)和在线消毒(灭菌)的方式进行清洗和消毒(灭菌),验证时应确认清洗水的内毒素符合要求。
3.2.5应明确灭菌后的设备及管路等安装规程,应规定人员安装方法、安装顺序等,避免储存、安装过程中的再次污染。
3.3胶塞、西林瓶及铝盖等包材的清洗和灭菌3.3.1胶塞的清洗、硅化、灭菌、干燥等处理过程,应严格监控每一步骤的质量情况,如灭菌和干燥的时间、温度、压力等应符合要求。
应对胶塞清洗方法进行验证,验证应重点关注细菌内毒素清除效果;应按验证方法清洗,应检测最终淋洗水的可见异物。
灌装结束后剩余胶塞,如重复清洗、灭菌,应经验证并规定使用次数。
3.3.2应按验证方法进行西林瓶清洗和灭菌,定时抽取检查清洁情况,控制洗瓶速度、注射用水压力、洁净压缩空气压力等,并监控隧道烘箱的温度、压差、履带传送速度等。
灭菌后的瓶子暴露或离开灭菌柜后,宜在4小时内使用。
3.3.3应考虑铝盖特性、已盖塞产品的密封性、生产运行稳定性等因素,制定合适的控制微生物方法及规程。
3.4厂房和环境清洁消毒3.4.1生产结束后,应按照操作规程对配制和无菌区及相关的厂房、设备、容器立即清洁并及时消毒(或灭菌),清洁、消毒(或灭菌)方法和效果应得到验证。
3.4.2通过验证,应明确清洁剂和消毒剂的名称、浓度、配制方法、除菌过滤方法、储存要求、使用量和使用时限。