非对称泵控单出杆液压缸实验方法研究
非对称液压缸的动态特性仿真研究_郝前华

第 6期
郝前华等 :非 对称液压缸的动态特性仿真研究
9 87
由铲斗自重 通过 连杆 传 递到 活塞 杆上 的 负载 力 FL′。 该 负 载力 FL′与铲 斗液 压 缸瞬 时 长度 L有 关 [ 10] 。 为简化分析 , 假设在时间 t=0时 , 对液压缸输入一阶跃负载力 FL =2 500 N, 同时输入一阶跃 流量 Q1 =110 L/min。
第 6期
郝前华等 :非 对称液压缸的动态特性仿真研究
9 85
现加速或减速的瞬态过程 。非对称液压缸的动态特性分析就是对这一瞬态过程中的输出压力和活塞运 动速度变化进行分析 [ 4] 。对液压系统的动态特性 , 国内有很多学者做了研究 。罗艳蕾 [ 5] 对液压节流调 速系统动态特性进行了仿真 , 崔昊等 [ 6] 对一开关型阀控液压缸进行了仿真与优化 , 史显忠等 [ 7] 对由对
根据式 (7)、(8)可求得外负载和流量单作用下液压缸活塞的速度 , 根据式 (9)、(10)可求得外负载 和流量单作用下液压缸工作腔的输出压力 。在外负载和流量的共同作用下 , 由叠加原理可知 , 液压缸的 输出压力和速度是它们单独作用于液压缸所引起的输出之和 。
根据式 (5)、(6)和图 2非对称液压缸方框图 , 在 MATLAB软件中建立铲斗液压缸仿真模块图 , 如图 3所示 。
质量 (kg);u为非对称液压缸活塞运动速度 (m/s);B为
粘性阻尼系数 (N· s/m);FL为负载力 (N)。 非对称液压缸工作腔的流量连续方程 [ 4]
图 1 非对称液压缸 ——— 负载系统 Fig.1 Theloadedsystem ofasymmetrical
Q1 =A1 u+CiP1 +Vβe1 ddPt1 ,
泵控非对称液压缸系统高精度位置控制方法

泵控非对称液压缸系统高精度位置控制方法王玄;陶建峰;张峰榕;吴亚瑾;刘成良【期刊名称】《浙江大学学报(工学版)》【年(卷),期】2016(050)004【摘要】针对已开发的单向比例泵控非对称液压缸系统实验平台,为了实现该类系统的无超调位置控制,通过分析系统的工作原理及特性,基于系统的流量连续性方程和力平衡方程,提出采用带约束的三阶状态空间模型来描述单向比例泵控非对称液压缸系统的方法.基于模型预测控制理论和QPhild二次优化算法,设计适用于该模型的模型预测控制器来保证系统的无超调位置输出.实验结果表明,运用模型预测方法能够避免换向阀切换引入的系统非线性,有效地解决泵控非对称液压缸系统的超调问题,实现多约束条件下的高精度位置控制.【总页数】6页(P597-602)【作者】王玄;陶建峰;张峰榕;吴亚瑾;刘成良【作者单位】上海交通大学机械与动力工程学院,上海200240;上海交通大学机械与动力工程学院,上海200240;上海交通大学机械与动力工程学院,上海200240;上海交通大学机械与动力工程学院,上海200240;上海交通大学机械与动力工程学院,上海200240【正文语种】中文【中图分类】TH137;TP271【相关文献】1.非对称液压缸伺服泵控系统控制模型及其参数辨识研究 [J], 徐坤;朱灯林;梅志千;陈成2.泵控非对称液压缸系统能效特性对比研究 [J], 王波;李运华;赵斌;葛磊;权龙3.非对称泵控单出杆液压缸系统特性分析 [J], 马艳斌;赵斌;郝云晓4.泵控非对称液压位置系统自适应Backstepping控制 [J], 许文斌;曾乐5.基于预测控制的单向比例泵控非对称液压缸系统控制方法 [J], 王玄;陶建峰;张峰榕;吴亚瑾;刘成良因版权原因,仅展示原文概要,查看原文内容请购买。
阀控非对称液压缸建模方法研究
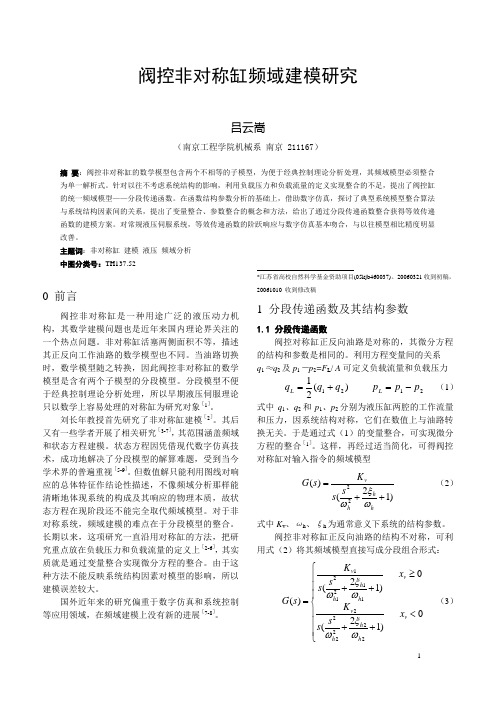
阀控非对称缸频域建模研究吕云嵩(南京工程学院机械系南京 211167)摘要:阀控非对称缸的数学模型包含两个不相等的子模型,为便于经典控制理论分析处理,其频域模型必须整合为单一解析式。
针对以往不考虑系统结构的影响,利用负载压力和负载流量的定义实现整合的不足,提出了阀控缸的统一频域模型——分段传递函数。
在函数结构参数分析的基础上,借助数字仿真,探讨了典型系统模型整合算法与系统结构因素间的关系,提出了变量整合、参数整合的概念和方法,给出了通过分段传递函数整合获得等效传递函数的建模方案。
对常规液压伺服系统,等效传递函数的阶跃响应与数字仿真基本吻合,与以往模型相比精度明显改善。
主题词:非对称缸建模液压频域分析中图分类号:TH137.520 前言阀控非对称缸是一种用途广泛的液压动力机构,其数学建模问题也是近年来国内理论界关注的一个热点问题。
非对称缸活塞两侧面积不等,描述其正反向工作油路的数学模型也不同。
当油路切换时,数学模型随之转换,因此阀控非对称缸的数学模型是含有两个子模型的分段模型。
分段模型不便于经典控制理论分析处理,所以早期液压伺服理论只以数学上容易处理的对称缸为研究对象[1]。
刘长年教授首先研究了非对称缸建模[2]。
其后又有一些学者开展了相关研究[3-7],其范围涵盖频域和状态方程建模。
状态方程因凭借现代数字仿真技术,成功地解决了分段模型的解算难题,受到当今学术界的普遍重视[5-9]。
但数值解只能利用图线对响应的总体特征作结论性描述,不像频域分析那样能清晰地体现系统的构成及其响应的物理本质,故状态方程在现阶段还不能完全取代频域模型。
对于非对称系统,频域建模的难点在于分段模型的整合。
长期以来,这项研究一直沿用对称缸的方法,把研究重点放在负载压力和负载流量的定义上[2-6],其实质就是通过变量整合实现微分方程的整合。
由于这种方法不能反映系统结构因素对模型的影响,所以建模误差较大。
国外近年来的研究偏重于数字仿真和系统控制等应用领域,在频域建模上没有新的进展[7-8]。
泵控非对称液压缸系统能效特性对比研究

泵控非对称液压缸系统能效特性对比研究王波;李运华;赵斌;葛磊;权龙【摘要】以现有对称泵控非对称缸系统和新型三油口泵控非对称缸系统为对象,对四象限工况下两种系统的能效特性进行了对比研究.介绍了两种系统的工作原理,对系统能效进行了理论分析,进一步在Simulation X软件中进行了仿真研究,并讨论了负载力大小对系统能效的影响.仿真结果表明,与对称泵控系统相比,三油口泵控系统第Ⅰ象限内,可提高系统能量效率7.6%,减少系统能量损失66%;第Ⅲ象限内,可提高系统能量效率21.2%,减少能量损失86.4%,因此具有更好的能效特性,节能效果显著.【期刊名称】《液压与气动》【年(卷),期】2018(000)010【总页数】7页(P8-14)【关键词】对称泵;三油口泵;四象限工况;能效特性【作者】王波;李运华;赵斌;葛磊;权龙【作者单位】太原理工大学新型传感器与智能控制教育部与山西省重点实验室,山西太原 030024;北京航空航天大学自动化科学与电气工程学院,北京 100191;太原理工大学新型传感器与智能控制教育部与山西省重点实验室,山西太原 030024;太原理工大学新型传感器与智能控制教育部与山西省重点实验室,山西太原 030024;太原理工大学新型传感器与智能控制教育部与山西省重点实验室,山西太原030024【正文语种】中文【中图分类】TH137引言传统液压阀控系统响应速度快、控制精度高,但存在节流损失大、系统效率低和能量浪费大等问题[1]。
为了提高系统能量效率,最直接的方法是采用泵控系统,通过控制液压泵的排量或转速,直接无节流损失地驱动液压执行器,具有较高的能量效率[2]。
根据执行元件的不同,泵控系统进一步可分为泵控对称缸(马达)和泵控非对称缸两种。
其中,泵控对称缸系统研究起步较早,技术成熟,已广泛应用于飞机舵机等系统。
而泵控非对称缸系统、液压泵流量与液压缸两腔面积不匹配,如何补偿液压缸面积差造成的不对称流量是其需要解决的首要问题[3]。
关于非对称缸液压跃变问题的分析

0 引言
非对称液压缸也称单出杆缸,因其具有工作空 间小、结构简单和成本低廉等诸多优点而早已被广 泛采用,在汽轮机调门控制中几乎都采用伺服阀控 非对称缸控制,但相对于阀控对称缸而言,非对称 缸系统在特性上有很大的变化,分析也比较麻烦。 在汽轮机 DEH 控制中,经常会出现由于非对称缸结 构所固有的动态特性非线性,伺服阀换向时,液压 缸两腔压力就会产生压力跃变,影响 DEH 控制系统 的特性,造成调节汽门的波动,以致整个机组的转 速波动,负荷摆动等结果,所以有必要对伺服阀控 非对称缸工作过程中产生的压力跃变现象进行分析 及处理,降低油缸的压力跃变,改善整个 DEH 控制 特性,提高机组运行品质。
B 0
+P (11) PP ,( A→ B ) =(7) +(9) 1.0 0.9 0.8 0.72 0.64
A B 0
+P (11) PP ,( A→ B ) =(7) +(9) 1.0 0.57 0.33 0.21 0.14
A B 0
+P (12) PP ,(B→ A ) =(8) +(10 ) 1.0 1.0 1.2 1.2 1.3
得:
3
,
FB FA = P0 − PB FB
2
FA PB = P0 − PB FB
(5)
F F A A 0 − P B = P B F P F B B
3
3
F 3 F 3 A A P 1+ B 0 F = F P B B
2
3
(6)
(3)
当F
A
= FB
时, P
A
+ PB = P0
液压缸试验方法
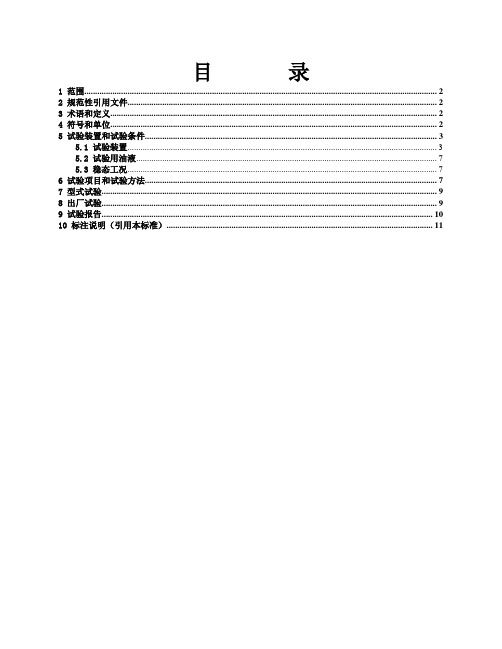
目录1 范围 (2)2 规范性引用文件 (2)3 术语和定义 (2)4 符号和单位 (2)5 试验装置和试验条件 (3)5.1 试验装置 (3)5.2 试验用油液 (7)5.3 稳态工况 (7)6 试验项目和试验方法 (7)7 型式试验 (9)8 出厂试验 (9)9 试验报告 (10)10 标注说明(引用本标准) (11)液压缸试验方法1 范围本标准规定了液压缸试验方法。
本标准适用于以液压油(液)为工作介质的液压缸(包括双作用液压缸和单作用液压缸)的型式试验和出厂试验。
本标准不适用于组合式液压缸。
2 规范性引用文件下列文件中的条款通过本标准的引用而成为本标准的条款。
凡是注日期的引用文件,其随后所有的修改单(不包括勘误的内容)或修订版均不适用于本标准,然而,鼓励根据本标准达成协议的各方研究是否可使用这些文件的最新版本。
凡是不注日期的引用文件,其最新版本适用于本标准。
GB/T 14039-2002 液压传动油液固体颗粒污染等级代号(ISO 4406:1999,MOD)GB/T 17446 流体传动系统及元件术语(GB/T 17446-1998,idtI SO 5598:1985)3 术语和定义在GB/T 17446中给出的以及下列术语和定义适用于本标准。
3.1最低起动压力the minimum pressure液压缸起动的最低压力。
3.2无杆腔the cavity with out piston rod液压缸没有活塞杆的一腔。
3.3有杆腔the cavity with piston rod液压缸有活塞杆伸出的一腔。
3.4负载效率load efficiency液压缸的实际输出力与理论输出力的比值。
4 符号和单位本标准使用的符号及其单位见表l。
表1 符号和单位5 试验装置和试验条件5.1 试验装置5.1.1液压缸试验装置见图1和图2。
试验装置的液压系统原理图见图3~图5。
图1 加载缸水平加载试验装置图2 重物模拟加载试验装置1——过滤器;2——液压泵;3——溢流阀;4——单向阀;5——电磁换向阀;6——单向节流阀;7——压力表开关;8——压力表;9——被试缸;10——流量计;11——温度计。
第1章阀控非对称缸液压伺服系统2
1
1 n
压差 P1 0
15
10 P2 ,P2',P20
5
0
-2
-1
0
1
FL (N )
有杆腔压力变化
2
3
10 4
P2
Ps
FL / 1 n
A1
P20
PS 1
FL A1 n
P' Ps FL / A1
2
1 n
P2 0
P1(MPa) P2(MPa)
阀与缸不完全匹配( m≠n )
xv 0
p1气蚀条件
p1超压条件
n3
m2
Ps A1
FL m2
Ps A1
( p1限制条件)
(1 n
p2超压条件
n2
)Ps A1
;
FL
P As 1 (p2限制条件)
p2气蚀条件
p' 1
气蚀条件
p1' 超压条件
xv 0
nPs
A1
FL
(1
n m2
n3 m2
)Ps
A1
nPs A1 FL n2 Ps A1
1.0 0.75 0.5 0.25
0
FL=APL (PL/PS) 1 (PSA)
QL Cd wxv
1 (Ps
xv xv
PL )
Q0 Cd wxvmax
1 Ps
QL xv 1 xv PL
Q0 xvmax
xv Ps
V0 (Q0(Qmax-))
b、对称阀控非对称缸输出特性
v=Q1/A1 V0max+
液压缸试验方法
目录1 范围 (2)2 规范性引用文件 (2)3 术语和定义 (2)4 符号和单位 (2)5 试验装置和试验条件 (3)5.1 试验装置 (3)5.2 试验用油液 (7)5.3 稳态工况 (7)6 试验项目和试验方法 (7)7 型式试验 (9)8 出厂试验 (9)9 试验报告 (10)10 标注说明(引用本标准) (11)液压缸试验方法1 范围本标准规定了液压缸试验方法。
本标准适用于以液压油(液)为工作介质的液压缸(包括双作用液压缸和单作用液压缸)的型式试验和出厂试验。
本标准不适用于组合式液压缸。
2 规范性引用文件下列文件中的条款通过本标准的引用而成为本标准的条款。
凡是注日期的引用文件,其随后所有的修改单(不包括勘误的内容)或修订版均不适用于本标准,然而,鼓励根据本标准达成协议的各方研究是否可使用这些文件的最新版本。
凡是不注日期的引用文件,其最新版本适用于本标准。
GB/T 14039-2002 液压传动油液固体颗粒污染等级代号(ISO 4406:1999,MOD)GB/T 17446 流体传动系统及元件术语(GB/T 17446-1998,idtI SO 5598:1985)3 术语和定义在GB/T 17446中给出的以及下列术语和定义适用于本标准。
3.1最低起动压力the minimum pressure液压缸起动的最低压力。
3.2无杆腔the cavity with out piston rod液压缸没有活塞杆的一腔。
3.3有杆腔the cavity with piston rod液压缸有活塞杆伸出的一腔。
3.4负载效率load efficiency液压缸的实际输出力与理论输出力的比值。
4 符号和单位本标准使用的符号及其单位见表l。
表1 符号和单位5 试验装置和试验条件5.1 试验装置5.1.1液压缸试验装置见图1和图2。
试验装置的液压系统原理图见图3~图5。
图1 加载缸水平加载试验装置图2 重物模拟加载试验装置1——过滤器;2——液压泵;3——溢流阀;4——单向阀;5——电磁换向阀;6——单向节流阀;7——压力表开关;8——压力表;9——被试缸;10——流量计;11——温度计。
非对称轴向柱塞泵配流盘泵控液压系统液压挖掘机论文
非对称泵配流特性及其在挖掘机动臂回路中的应用【摘要】液压挖掘机是最为常用的土方机械之一,作为一种多功能的工程机械,在建筑施工机械中有着非常重要的地位,由于其强大多功能适应性,在整个世界范围内都有很大的发展潜力。
目前市场上所使用的大多数挖掘机的液压系统都是运用各种控制阀来实现压力,流量和方向的控制,基于这种液压控制系统的传统液压挖掘机被称之为阀控挖掘机。
由于各类方向阀、压力阀和流量阀的飞速发展,阀控液压系统理论已经发展比较完善。
阀控式液压挖掘机占据很大的市场份额。
但是由于阀控液压系统本身存在的不可避免的节流损失问题,在增大系统装机功率的同时,导致阀控液压挖掘机出现燃油使用量大、耗油高、排放差、液压系统发热量大、效率低等问题。
近些年来随着人们的环保意识越来越强,高效节能的呼声越来越高,液压系统的各种控制技术及传动方式之间的竟争日趋激烈,节能型挖掘机必然会成为挖掘机发展的方向和趋势,挖掘机液压系统面临着节能减排的重大技术革新问题。
如何降低液压挖掘机的能耗、提高其能量利用率是各国液压挖掘机生产企业接下来要追求的主要目标,这也是论文的基本出发点。
阀控液压系统控制系统本身成为制约挖掘机技术进一步发展的技术难题,对比了泵直接闭式控制对称液压缸和泵控马... 更多还原【Abstract】 Hydraulic excavator is one of the most commonlyused earth mover, as one kind of the multi-functionalengineering machineries, because of its powerfulmulti-functional adaptation,Hydraulic excavator has a very important role in the construction machinery, and has a great potential in the whole world market. Currently, most of the hydraulic excavators used the variety of valves to control the pressure, flow and direction of hydraulic system, this based on the hydraulic control system traditional ... 更多还原【关键词】非对称轴向柱塞泵;配流盘;泵控液压系统;液压挖掘机;【Key words】New axial piston pump;Valve plate;Pump controlled hydraulic system;Mini hydraulic excavator;【索购硕士论文全文】Q联系Q:138113721 139938848 即付即发目录摘要3-6ABSTRACT 6-8第一章绪论13-271.1 课题研究的背景及科学意义131.2 电液控制系统的发展和运用13-231.2.1 阀控液压系统介绍14-181.2.2 泵控液压系统18-231.3 计算机仿真技术简介23-241.3.1 仿真技术产生的背景23-241.3.2 仿真技术的发展241.4 论文的主要研究内容和创新点24-271.4.1 论文研究的主要内容251.4.2 论文研究的创新点25-27第二章新配流原理及新型液压泵三维模型27-412.1 多学科仿真软件SimulationX功能介绍27-302.1.1 仿真软件SimulationX建模方式282.1.2 SimulationX的标准模型库28-292.1.3 SimulationX的主要特点29-302.2 三维建模软件Pro/E功能介绍30-322.3 新配流原理介绍32-342.3.1 新配流方案的提出32-332.3.2 系统集成技术控制方案33-342.4 新配流方案的特点34-362.4.1 两种配流方案的共同特点34-352.4.2 两种配流方案的对比352.4.3 新配流方案噪声来源分析35-362.5 两种新型液压泵三维模型36-402.5.1 液压泵普通元件模型36-382.5.2 液压泵核心元件模型38-392.5.3 泵总装模型39-40第三章串联型三配流窗口轴向柱塞泵特性研究41-613.1 串联型三配流窗口泵配流方案41-423.2 串联型三配流窗口柱塞泵建模及仿真42-473.2.1 单柱塞配流面积43-453.2.2 泵泄漏量计算45-473.2.3 单柱塞模型473.3 压力流量特性47-533.3.1 斜盘满偏角时泵出口排量47-483.3.2 不同转数下泵的各口流量曲线48-493.3.3 非死点过渡区域分析49-503.3.4 阻尼孔对流量压力脉动的影响503.3.5 软管对流量脉动的影响50-523.3.7 仿真验证52-533.4 泵几何结构及样机53-543.4.1 配流盘及泵后盖结构53-543.4.2 泵的缸体和样机结构543.5 试验验证54-593.5.1 时域分析55-563.5.2 频域分析56-583.5.3 噪声特性分析58-593.6 结论59-60第四章并联型双作用轴向柱塞泵特性研究61-874.1 双作用配流方案61-634.1.1 双作用配流方案的提出61-624.1.2 双作用泵缸体及样机模型62-634.2 应用前景63-654.3 双作用配流方案建模与仿真65-714.3.1 单柱塞配流面积计算65-694.3.2 泵泄漏量计算69-704.3.3 单柱塞模型70-714.4 泵压力流量特性研究71-734.4.1 单作用泵模式71-724.4.2 双作用泵模式72-734.5 仿真与试验对比73-794.5.1 时域分析74-764.5.2 频域分析76-774.5.3 泵噪声特性分析77-794.6 两种双作用泵对比79-844.6.1 回路控制原理79-814.6.2 试验对比分析81-844.7 结论84-854.8 本章小结85-87第五章泵控差动缸回路在小型挖掘机上的运用87-1095.1 阀控式小型液压挖掘机简介87-885.2 试验平台YC60-7小型挖掘机介绍88-895.3 阀控挖掘机虚拟样机的建立89-965.3.1 挖掘机三维实体模型89-945.3.2 阀控挖掘机液压系统模型建立94-965.4 挖掘机工作部分泵控系统的运用96-1025.4.1 新型液压泵模型975.4.2 泵直接控制差动缸回路模型97-1015.4.3 泵直接控制系统在挖掘机工作部分上的运用101-1025.5 两种系统能量消耗情况102-1075.5.1 阀控挖掘机工作循环及能量消耗103-1065.5.2 泵控挖掘机能量消耗106-1075.6 本章小结107-109第六章论文总结与工作展望109-1136.1 论文总结109-1106.2 工作展望110-113参考文献。
阀控非对称液压缸数学模型及建模方法研究
MECHANICAL ENGINEER阀控非对称液压缸数学模型及建模方法研究炘李晓园,陈,叶鹏,李鑫,徐祥,蒋辉,李琼柱(红塔烟草(集团)有限责任公司玉溪卷烟厂,云南玉溪653100)摘要:非对称液压缸两腔结构参数不同,给阀控非对称缸数学建模带来了较大的困难。
文中针对现行阀控非对称液压缸数学模型及简化方法作了分析比较,提出了一种新的简化方法,并据此导出了较为精确的数学模型。
关键词:非对称液压缸;数学模型;建模方法;辅助方程中图分类号:TH137文献标志码:A文章编号:1002-2333(2020)08-0104-04 Research on Mathematical Model and Modeling Method of Valve Controlled Asymmetric Hydraulic Cylinder LI Xiaoyuan,CHEN Xin,YE Peng,LI Xin,XU Xiang,JIANG Hui,LI Qiongzhu (The Second Workshop of Cigarette Packaging of Yuxi Cigarette Factory,Hongta Tobacco(group)Co.,Ltd.,Yuxi653100,China) Abstract:The structural parameters of the two chambers of the asymmetric hydraulic cylinder are different,which brings great difficulties to the mathematical modeling of the valve-controlled asymmetric cylinder.This paper analyzes and compares the current mathematical models and simplified methods of valve-controlled asymmetric hydraulic cylinders, proposes a new simplified method,and derives a more accurate mathematical model based on this.Keywords:asymmetric hydraulic cylinder;mathematical model;modeling method;auxiliary equation0引言液压控制系统的种类及分类方法很多,根据液压放大器与执行元件的不同组合,可分成阀控缸、阀控马达、泵控缸、泵控马达4种[1-2],其中阀控缸响应快、精度高、应用最广。
- 1、下载文档前请自行甄别文档内容的完整性,平台不提供额外的编辑、内容补充、找答案等附加服务。
- 2、"仅部分预览"的文档,不可在线预览部分如存在完整性等问题,可反馈申请退款(可完整预览的文档不适用该条件!)。
- 3、如文档侵犯您的权益,请联系客服反馈,我们会尽快为您处理(人工客服工作时间:9:00-18:30)。
非对称泵控单出杆液压缸实验方法研究王爱红;韦关龙;刘等卓;吕振峰;成杰【摘要】非对称泵是一种可平衡单出杆液压缸有杆腔和无杆腔不对称流量的新型高效节能元件,对消除或减少液压系统能量损失具有显著效果,故需要在现有研究基础上从原理、功能及使用等方面不断完善改进,以便于投入到工程应用中.由于非对称泵结构的特殊性,进行泵控单出杆液压缸台架实验设计是非对称泵在液压回路中使用的基础性研究.实验回路中,非对称泵A油口接单出杆液压缸有杆腔、B油口接单出杆液压缸无杆腔、C油口接蓄能器、利用DSpace控制非对称泵斜盘倾角,达到变量控制液压缸.理论和实验表明,非对称泵可以有效匹配单出杆液压缸有杆腔和无杆腔不对称流量,实现非对称泵控单出杆液压缸的有效节能控制.【期刊名称】《太原科技大学学报》【年(卷),期】2017(038)006【总页数】5页(P440-444)【关键词】非对称变量泵;单出杆液压缸;斜盘倾角;DSPACE【作者】王爱红;韦关龙;刘等卓;吕振峰;成杰【作者单位】太原科技大学机械工程学院,太原030024;太原科技大学机械工程学院,太原030024;太原科技大学机械工程学院,太原030024;太原科技大学机械工程学院,太原030024;太原科技大学机械工程学院,太原030024【正文语种】中文【中图分类】TH322负载敏感控制系统当几个执行器同时工作,只有压力最高的负载效率较高,其他负载用压差补偿会产生较大的节流损失[1]。
为了消除阀控系统的节流损失,原德国汉堡工业大学Monika教授在1998年提出将全泵控技术用于工程车辆上,以变量泵/马达为控制元件消除节流损失、实现能量回收利用[2]。
实验表明在轮式装载机上采用泵控差动缸液压系统,燃油消耗量可降低15~25%[3],挖掘机采用泵控技术,可降低燃油消耗49% [4].国外Rexroth公司、美国Vickers公司、德国Aachen工业大学液压研究所、普渡大学、Hamburg工业大学等 [5-7],国内哈尔滨工业大学、北京航空航天大学、太原理工大学等对泵控技术都进行了相关研究[8-11]。
泵控单出杆液压缸需要用液压阀来平衡有杆腔和无杆腔的不对称流量,造成系统复杂。
非对称泵是一种可平衡单出杆液压缸有杆腔和无杆腔不对称流量的新型高效节能元件,对消除或减少液压系统能量损失具有显著效果,故需要在现有研究基础上从原理、功能及使用等方面不断完善改进,以便于投入到工程应用中。
非对称泵通过改变斜盘角的角度大小和方向实现排量大小和液压油流向的调整,从而对液压缸的举升和下降进行控制。
若转速不变,当非对称泵斜盘倾角为正值时,B 口和T口为出油口, A口为进油口,处于液压泵工况,液压缸举升货物。
当货物降落时,改变非对称泵斜盘倾角方向及大小,则 B口和T口为进油口、A口为出油口,非对称泵处于马达工况,进行势能回收,其原理如图1所示。
实验台主要部件包括由液压缸等组成的执行系统;由dsPACE、电液伺服阀等组成的控制系统;由电机组成的动力系统,由泵站等组成的供油系统;由扭矩传感器、位移传感器、流量压力传感器等组成的测试系统等部分,如图2所示。
控制系统原理为,在dSPACE上有模拟信号转数字信号A/D接口和数字信号转模拟信号D/A.位移传感器将电阻信号经电压转换后,将信号线接入dsPACE A/D接口,在电脑端中MATlab和Controldesk中既可以显示并保存位移电压信号;角度传感器输出匹配电压后,信号先经过A/D接口将信号转化成数字信号,该信号经PCI总线输入电脑,经过Controldesk与MATlab/Simulink闭环系统处理,将反馈信号经D/A转换后发送给电液伺服阀控制伺服阀的开度,继而改变斜盘角度,信号流如图3所示。
扭矩传感器发出的信号经过测量仪可以实时显示,同时通过RS-232串口可以直接和电脑进行数据传输。
当电脑发出指令后既可从测试仪中获得15位浮点数组数据,接线原理如图4所示。
蓄能器最低工作压力p1、最高工作压力p2、充气压力p0、充气体积V0、以及蓄能器有效工作体积ΔV为:ΔV =AL式中,A—液压缸活塞工作面积,为0.003 m2;L—活塞杆最大行程,为0.75 m,则ΔV为2.3 L.液压缸无杆腔压力pw1为:pw1=F/A液压缸需提供的顶推力F为10 976 N.则由式(2)可得pw1为3.5 MPa.由于液压蓄能器的最大压力应大于系统的最高压力,并考虑到蓄能效果,本试验选取6.4 L10 Mpa的蓄能器。
非对称泵输出功率为:P=ηppVpnp式中,P—泵的驱动功率,W; pp—液压泵的最大工作压力Pa,取泵额定压力的0.8倍; Vp—液压泵排量,mL/r; η—液压泵的效率,柱塞泵为0.9~0.95,np—液压泵转速,r/s.非对称泵排量为40 mL/r,将相关参数带入式(3)可得P=2.3 kW,则选择电机功率为2.5 kW.液压缸型号为HSGL01-63/DE,缸径63 mm,杆径45 mm,最大行程750 mm,推力49 870 N,拉力34 480 N.根据液压缸的行程选择了最大测量行程为800 mm的位移传感器,精度达到正负0.5%.调节泵站压力使其达到试验要求的1.5 Mpa.打开Controldesk和Dspace系统,确认输入角度数值为零;启动电机后微调非对称泵斜盘倾角,使非对称泵供油压力和负载压力平衡,液压缸处于相对静止位置。
在Controldesk系统中设置非对称泵斜盘倾角,使油液压缸开始举升,采集压力流量、位移、角度等数据。
当液压缸上升至顶端,改变非对称泵斜盘倾角,使油液压缸下降,图5为MATLAB/Simulink中控制斜盘倾角闭环反馈回路。
图6为非对称泵控单出杆液压缸±5°斜盘倾角时液压缸位移曲线,由图可知,液压缸在刚开始起升时有冲击,这与蓄能器瞬间释放压力有关,随后变平稳并以相同加速度上升。
下降过程同样稳定且速度更快,原因是上升时需要克服自重,下降时自重变成驱动力增大了液压缸下行加速度。
其上升和下降分别用时为17.46 s和8.963 s.图7为非对称泵控单出杆液压缸在±10°斜盘倾角时液压缸位移曲线,上升用时9.183 s,下降用时6.005 s,液压缸作业速度快于±5°斜盘倾角。
B口和T口的流量和压力一个起降工况的测试曲线如图8(a)、(b)所示,图8(b)中出现压力峰值(溢流阀设定安全压力值),主要是由于液压缸到达极限位置时,由于非对称泵斜盘倾角正负转化和液压缸运行方向改变的不一致,造成非对称泵流量在过渡期间向蓄能器和有杆腔充油,导致压力上升最后从溢流阀流出。
同时,蓄能器的充放特性也会造成系统中压力脉冲。
图9(a)中可以看出在液压缸上升时B口和T口的流量分别为7 L/min和10 L/min,下降时流量变大,这与下降时速度较快有关。
对比斜盘倾角为±5°和±10°两种情况,可知大斜盘倾角时非对称泵控单出杆液压缸压力流量更稳定。
斜盘倾角为±5°和±10°时非对称泵功率曲线如图10所示,可知±10°斜盘倾角非对称泵输出功率大于±5°斜盘倾角,系统相应也更快。
基于Controldesk和Dspace系统的非对称泵控单出杆液压缸实验,验证了非对称泵控单出杆液压系统可以实现非对称变量泵对液压缸的位移和速度的有效控制,说明了该原理的正确性和可行性,为理论上的近一步完善和控制策略的改进提供了实验基础。
也为非对称泵控单出杆液压在工程上的应用做了试验台架上的测试。
【相关文献】[1] SH CHO, NOSKIEVI P. Position tracking control with load-sensing for energy-saving valve-controlled cylinder system[J]. Journal of Mechanical Science and Technology, 2012, 26(2): 617-625.[2] M IVANTYSYNOVA. Variable displacement pump will be of great developmental potential[C]// lst IFK, Aachen, Germany, 1998: 359-371.[3] RAHMFELD R, IVANTYSYNOVA M. Displacement controlled linear actuator with differential cylinder- a way to save primary energy in mobile machines[C]//ICFP 2001: Fifth International Conference on Fluid Power Transmission and Control,2001: 296-301. [4] WILLIAMSON C, ZIMMERMAN J, IVANTYSYNOVA M. Efficiency study of an excavator hydraulic system based on displacement controlled actuators[C]// ASME Symposium on Fluid Power and Motion Control,Bath, UK, 2008.[5] RAHMFELD R.Development and control of energy saving hydraulic servo drivers for mobile machine[D]. Hamburg: Technische Universitaet Hambur7g, 2002.[6] WILLIAMSON C, LEE S, IVANTYSYNOVA M. Active vibration damping for an off-road vehicle with displacement controlled actuators[J]. International Journal of Fluid Power, 2009, 10(3): 5-16.[7] JROSE, IVANTYSYNOVA M. A study of pump control systems for smart pumps[C]// Proceedings of the 52nd National Conference on Fluid Power, 2011: 683-692.[8] 付永领, 张卫卫, 纪友哲. 电机泵阀作动系统的分级压力控制及效率分析[J]. 北京航空航天大学学报, 2011, 37(12): 1552-1556.[9] JIANG JH. Direct drive variable speed electro-hydraulic servo system to position control of a ship rudder[C]// 4th IFK,Dresden, Germany, 2004: 103-114.[10] 权龙. 转速可调泵直接闭环控制差动缸伺服系统的动特性[J]. 机械工程学报, 2003,39(2): 13-17.[11] 权龙,廉自生.应用进出油口独立控制原理改善泵控差动缸系统效率[J].机械工程学报,2005,41(3): 124-127.。