新半导体工艺制程教程方法
半导体制作工艺流程
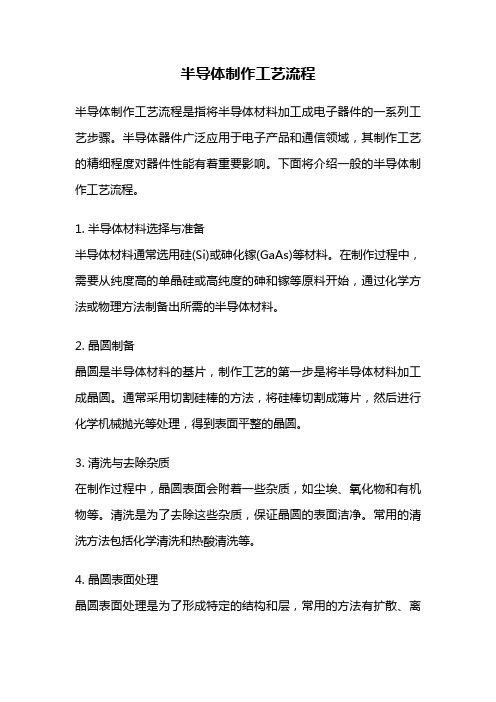
半导体制作工艺流程半导体制作工艺流程是指将半导体材料加工成电子器件的一系列工艺步骤。
半导体器件广泛应用于电子产品和通信领域,其制作工艺的精细程度对器件性能有着重要影响。
下面将介绍一般的半导体制作工艺流程。
1. 半导体材料选择与准备半导体材料通常选用硅(Si)或砷化镓(GaAs)等材料。
在制作过程中,需要从纯度高的单晶硅或高纯度的砷和镓等原料开始,通过化学方法或物理方法制备出所需的半导体材料。
2. 晶圆制备晶圆是半导体材料的基片,制作工艺的第一步是将半导体材料加工成晶圆。
通常采用切割硅棒的方法,将硅棒切割成薄片,然后进行化学机械抛光等处理,得到表面平整的晶圆。
3. 清洗与去除杂质在制作过程中,晶圆表面会附着一些杂质,如尘埃、氧化物和有机物等。
清洗是为了去除这些杂质,保证晶圆的表面洁净。
常用的清洗方法包括化学清洗和热酸清洗等。
4. 晶圆表面处理晶圆表面处理是为了形成特定的结构和层,常用的方法有扩散、离子注入、溅射等。
其中,扩散是通过高温加热将掺杂物扩散到晶圆表面,形成特定的电子掺杂浓度分布;离子注入是将掺杂离子注入晶圆表面,改变其电子性质;溅射是利用高能离子轰击晶圆表面,使其表面原子沉积形成特定结构和层。
5. 光刻与光刻胶光刻是将芯片上的图形投射到光刻胶上,在光刻胶上形成图形。
光刻胶是一种对紫外光敏感的聚合物,通过紫外光照射、显影等步骤,可以形成所需的图形。
6. 离子蚀刻与湿法蚀刻离子蚀刻是利用高能离子轰击晶圆表面,使其表面原子沉积形成特定结构和层。
湿法蚀刻是通过特定的化学液体,将晶圆表面的非遮蔽区域溶解掉,形成所需的结构。
7. 金属沉积与蚀刻金属沉积是将金属沉积在晶圆表面,形成导线、电极等结构。
常用的金属沉积方法有物理气相沉积、化学气相沉积和电镀等。
蚀刻是将多余的金属去除,使得只有所需的结构。
8. 封装与测试半导体器件制作完成后,需要进行封装和测试。
封装是将芯片封装在塑料或陶瓷封装体内,以保护芯片并方便与外部电路连接。
半导体制造工艺流程

半导体制造工艺流程半导体制造工艺是半导体芯片制造的基础流程,也是一项复杂且精细的工艺。
下面是一份大致的半导体制造工艺流程,仅供参考。
1. 半导体材料的准备:半导体材料通常是硅,需要经过精细的提纯过程,将杂质降低到一定程度,以确保半导体器件的性能。
还需要进行晶体生长、切割和抛光等工艺,以制备出适用于制造芯片的晶片。
2. 晶片清洗和处理:经过前面的准备步骤后,晶片需要进行清洗,以去除表面的杂质和污染物。
清洗包括化学溶液浸泡和超声波清洗等步骤。
之后,通过化学气相沉积等工艺,在晶片上形成氧化层或氮化层,以保护晶片表面。
3. 光刻和光刻胶涂布:在晶片表面涂布一层光刻胶,然后通过光刻机将设计好的芯片图案投射在胶涂层上,形成光刻胶图案。
光刻胶图案将成为制作芯片电路的模板。
4. 蚀刻:将光刻胶图案转移到晶片上,通过干式或湿式蚀刻工艺,将未被光刻胶保护的部分材料去除,形成电路图案。
蚀刻可以通过化学溶液或高能离子束等方式进行。
5. 激光刻蚀:对于一些特殊材料或细微的电路结构,可以使用激光刻蚀来实现更高精度的图案形成。
激光刻蚀可以通过激光束对材料进行精确的去除。
6. 金属薄膜沉积:在晶片表面沉积金属薄膜,以形成电路中的金属导线和连接器。
金属薄膜通常是铝、铜等材料,通过物理气相沉积或化学气相沉积等工艺进行。
7. 金属薄膜刻蚀和清洗:对金属薄膜进行蚀刻和清洗,以去除多余的金属,留下需要的导线和连接器。
8. 测量和测试:对制造好的芯片进行电学性能的测试和测量,以确保其符合设计要求。
9. 封装和封装测试:将芯片封装在外部环境中,通常采用芯片封装材料进行密封,然后进行封装测试,以验证封装后芯片的性能和可靠性。
10. 最终测试:对封装好的芯片进行最终的功能和性能测试,以确保其满足市场需求和客户要求。
以上是半导体制造的基本流程,其中每个步骤都需要高度的精确性和专业技术。
半导体制造工艺的不断改进和创新,是推动半导体技术不断进步和发展的重要驱动力。
半导体制作工艺流程

半导体制作工艺流程第一步:芯片设计芯片设计是半导体制作的第一步,主要由工程师根据需求设计出电路的布局和结构,并进行功能电路的分析和模拟。
第二步:晶圆制备晶圆制备是指通过将高纯度的单晶硅材料经过晶体生长,然后切割成一片薄的圆盘状。
晶圆的制备过程包括硅材料的提纯、晶体生长技术、硅晶圆的切割和去除杂质等步骤。
第三步:化学气相沉积(CVD)化学气相沉积是一种将气体中的化学物质在热腔中化学反应生成固态材料的过程。
CVD可以用来在晶圆表面沉积薄膜,例如用于电子器件的绝缘层、金属线等。
第四步:物理气相沉积(PVD)物理气相沉积是指将固态材料通过蒸发或溅射技术直接沉积在晶圆表面上。
PVD可以用来制备金属层、合金层、氧化层等。
第五步:光刻光刻是一种将芯片设计图案转移到晶圆上的技术。
首先,在晶圆上涂覆一层光刻胶,然后使用光刻机将设计图案通过光刻胶曝光到晶圆上。
曝光后,通过显影将未曝光的区域去除,形成所需电路的图案。
第六步:蚀刻蚀刻是一种将晶圆上的特定区域物质溶解或者刻蚀掉的过程。
蚀刻可以通过湿蚀刻或干蚀刻的方式进行。
湿蚀刻使用化学试剂将晶圆表面的材料溶解,而干蚀刻则通过物理或化学反应将晶圆表面的材料移除。
第七步:离子注入离子注入是指将离子束注入到晶圆中,并通过控制注入的能量和剂量来改变晶圆表面或内部的材料性质。
离子注入可以用来增强或改变半导体材料的导电性能。
第八步:金属化金属化是指对晶圆进行金属薄膜的沉积、电镀和制作金属导线等工艺。
通过金属化,可以连接晶圆上不同区域的电路,形成完整的电子器件结构。
第九步:封装封装是将芯片组装到封装盒中,保护芯片并提供连接器和引脚等功能。
封装工艺包括晶圆切割、引脚焊接、封装胶固化等步骤,在这一步骤完成后,半导体芯片即可用于实际应用。
总结:半导体制作工艺流程是一个非常复杂和精密的过程,涉及到多种工艺技术和设备。
只有经过严格的流程控制和质量检测,才能确保芯片的质量和性能。
随着半导体技术的不断发展,工艺流程也在不断演变,为芯片的性能和制造成本提供更好的平衡。
半导体制造工艺流程

半导体制造工艺流程1.单晶硅材料制备:利用高纯度的硅源材料,通过化学方法或物理方法制备出单晶硅片。
这些单晶硅片用于制造芯片的基底。
2.潮湿腐蚀:将单晶硅片放入一定浓度的酸中进行腐蚀,以去除表面的氧化层和杂质,使得单晶硅表面更加平整。
3.清洗:用化学溶液对单晶硅片进行清洗,去除表面的杂质和有机物。
4.氮氧化:将单晶硅片放入氮气环境中进行热氧化,生成一层氮氧化物的薄膜。
这个薄膜在后续工艺中用于隔离器件。
5.光刻:将光刻胶涂在氮氧化层上,然后通过曝光和显影的方式将芯片的图案转移到光刻胶上,形成光刻图案。
6.腐蚀和沉积:将芯片放入化学溶液中进行腐蚀,去除曝光没有覆盖的区域,然后进行金属沉积。
金属沉积可以形成导电层或者连接层。
7.退火:通过高温处理,使得芯片中的材料发生结晶和扩散,提高电子器件的性能。
退火还有去除应力、填充缺陷和提高结晶度的作用。
8.清洗:用化学溶液清洗芯片,去除残留的光刻胶和沉积物,保证芯片的纯净度。
9.蚀刻和沉积:使用干法或湿法蚀刻技术,去除部分芯片表面材料,形成电子器件的结构。
然后再进行金属或者氧化物的沉积,形成电极或者绝缘层。
10.清洗和检测:再次清洗芯片,以确保芯片的纯净度。
然后进行各类检测,如电性能测试、材料分析等,以保证芯片质量。
11.封装:将芯片放入封装材料中,进行电缆连接和封装。
然后将封装好的芯片焊接到PCB板上,形成最终的电子产品。
以上是一般的半导体制造工艺流程,其中每个步骤都有详细的工艺参数和设备要求。
随着技术的不断发展,半导体制造工艺也在不断改进和创新,以提高芯片的性能和生产效率。
半导体芯片制作流程工艺
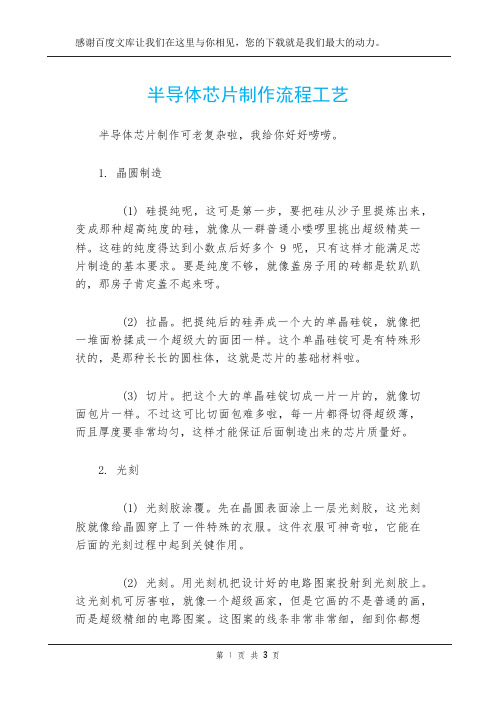
半导体芯片制作流程工艺半导体芯片制作可老复杂啦,我给你好好唠唠。
1. 晶圆制造(1) 硅提纯呢,这可是第一步,要把硅从沙子里提炼出来,变成那种超高纯度的硅,就像从一群普通小喽啰里挑出超级精英一样。
这硅的纯度得达到小数点后好多个9呢,只有这样才能满足芯片制造的基本要求。
要是纯度不够,就像盖房子用的砖都是软趴趴的,那房子肯定盖不起来呀。
(2) 拉晶。
把提纯后的硅弄成一个大的单晶硅锭,就像把一堆面粉揉成一个超级大的面团一样。
这个单晶硅锭可是有特殊形状的,是那种长长的圆柱体,这就是芯片的基础材料啦。
(3) 切片。
把这个大的单晶硅锭切成一片一片的,就像切面包片一样。
不过这可比切面包难多啦,每一片都得切得超级薄,而且厚度要非常均匀,这样才能保证后面制造出来的芯片质量好。
2. 光刻(1) 光刻胶涂覆。
先在晶圆表面涂上一层光刻胶,这光刻胶就像给晶圆穿上了一件特殊的衣服。
这件衣服可神奇啦,它能在后面的光刻过程中起到关键作用。
(2) 光刻。
用光刻机把设计好的电路图案投射到光刻胶上。
这光刻机可厉害啦,就像一个超级画家,但是它画的不是普通的画,而是超级精细的电路图案。
这图案的线条非常非常细,细到你都想象不到,就像头发丝的千分之一那么细呢。
(3) 显影。
把经过光刻后的晶圆进行显影,就像把照片洗出来一样。
这样就把我们想要的电路图案留在光刻胶上啦,那些不需要的光刻胶就被去掉了。
3. 蚀刻(1) 蚀刻过程就是把没有光刻胶保护的硅片部分给腐蚀掉。
这就像雕刻一样,把不要的部分去掉,留下我们想要的电路结构。
不过这个过程得非常小心,要是腐蚀多了或者少了,那芯片就报废了。
(2) 去光刻胶。
把之前用来形成图案的光刻胶去掉,这时候晶圆上就留下了我们想要的电路形状啦。
4. 掺杂(1) 离子注入。
通过离子注入的方式把一些特定的杂质原子注入到硅片中,这就像给硅片注入了特殊的能量一样。
这些杂质原子会改变硅片的电学性质,从而形成我们需要的P型或者N型半导体区域。
半导体制造流程及生产工艺流程
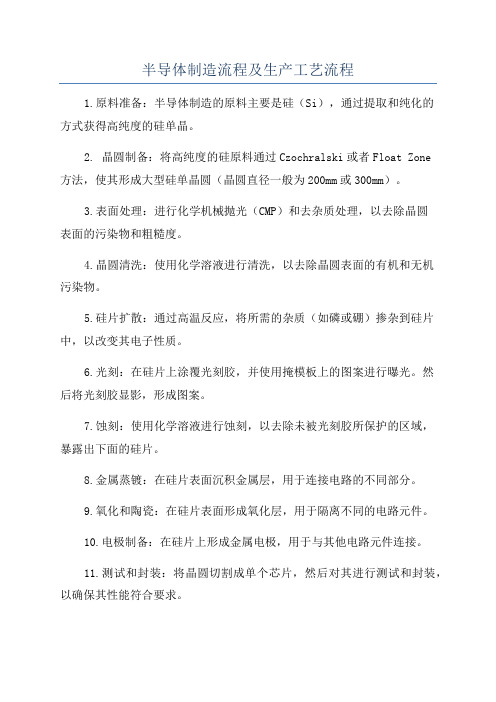
半导体制造流程及生产工艺流程1.原料准备:半导体制造的原料主要是硅(Si),通过提取和纯化的方式获得高纯度的硅单晶。
2. 晶圆制备:将高纯度的硅原料通过Czochralski或者Float Zone方法,使其形成大型硅单晶圆(晶圆直径一般为200mm或300mm)。
3.表面处理:进行化学机械抛光(CMP)和去杂质处理,以去除晶圆表面的污染物和粗糙度。
4.晶圆清洗:使用化学溶液进行清洗,以去除晶圆表面的有机和无机污染物。
5.硅片扩散:通过高温反应,将所需的杂质(如磷或硼)掺杂到硅片中,以改变其电子性质。
6.光刻:在硅片上涂覆光刻胶,并使用掩模板上的图案进行曝光。
然后将光刻胶显影,形成图案。
7.蚀刻:使用化学溶液进行蚀刻,以去除未被光刻胶所保护的区域,暴露出下面的硅片。
8.金属蒸镀:在硅片表面沉积金属层,用于连接电路的不同部分。
9.氧化和陶瓷:在硅片表面形成氧化层,用于隔离不同的电路元件。
10.电极制备:在硅片上形成金属电极,用于与其他电路元件连接。
11.测试和封装:将晶圆切割成单个芯片,然后对其进行测试和封装,以确保其性能符合要求。
以上是半导体制造的主要步骤,不同的半导体产品可能还涉及到其他特定的工艺流程。
此外,半导体制造过程还需要严格的质量控制和环境控制,以确保产品的可靠性和性能。
不同的半导体生产流程会有所不同,但大致上都包含以下几个关键的工艺流程:1. 前端制程(Front-end Process):包括晶圆清洗、来料检测、扩散、光刻、蚀刻、沉积等步骤。
这些步骤主要用于在硅片上形成电子元件的结构。
2. 中端制程(Middle-end Process):包括溅射、化学机械抛光、化学物理蚀刻、金属蒸镀等步骤。
这些步骤主要用于在晶圆上形成连接电子元件的金属线路。
3. 后端制程(Back-end Process):包括划片、电极制备、测试、封装等步骤。
这些步骤主要用于将芯片进行切割、封装,以及测试芯片的性能。
半导体制造工艺流程大全
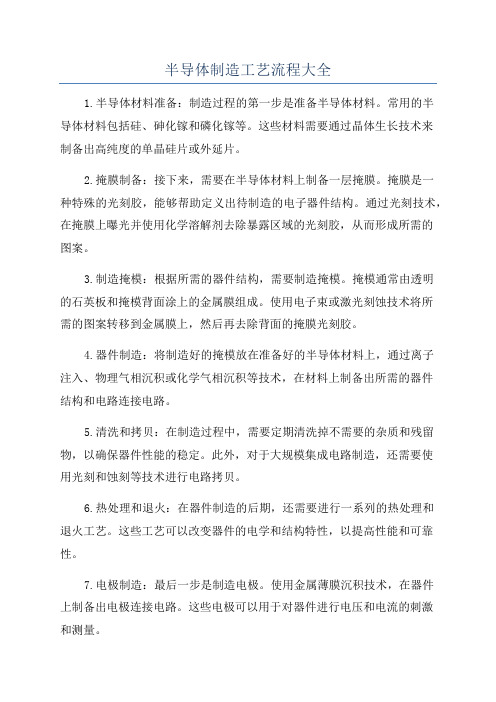
半导体制造工艺流程大全1.半导体材料准备:制造过程的第一步是准备半导体材料。
常用的半导体材料包括硅、砷化镓和磷化镓等。
这些材料需要通过晶体生长技术来制备出高纯度的单晶硅片或外延片。
2.掩膜制备:接下来,需要在半导体材料上制备一层掩膜。
掩膜是一种特殊的光刻胶,能够帮助定义出待制造的电子器件结构。
通过光刻技术,在掩膜上曝光并使用化学溶解剂去除暴露区域的光刻胶,从而形成所需的图案。
3.制造掩模:根据所需的器件结构,需要制造掩模。
掩模通常由透明的石英板和掩模背面涂上的金属膜组成。
使用电子束或激光刻蚀技术将所需的图案转移到金属膜上,然后再去除背面的掩膜光刻胶。
4.器件制造:将制造好的掩模放在准备好的半导体材料上,通过离子注入、物理气相沉积或化学气相沉积等技术,在材料上制备出所需的器件结构和电路连接电路。
5.清洗和拷贝:在制造过程中,需要定期清洗掉不需要的杂质和残留物,以确保器件性能的稳定。
此外,对于大规模集成电路制造,还需要使用光刻和蚀刻等技术进行电路拷贝。
6.热处理和退火:在器件制造的后期,还需要进行一系列的热处理和退火工艺。
这些工艺可以改变器件的电学和结构特性,以提高性能和可靠性。
7.电极制造:最后一步是制造电极。
使用金属薄膜沉积技术,在器件上制备出电极连接电路。
这些电极可以用于对器件进行电压和电流的刺激和测量。
半导体制造是一个高度精密和复杂的过程,需要使用多种材料和技术。
根据所制备器件的不同,工艺流程也会有所不同。
此外,随着科技的发展,新的材料和工艺技术也在不断涌现,使半导体制造工艺变得更加多样化和复杂化。
以上只是半导体制造工艺流程的一个简要概述,实际的制造过程会更加复杂和详细。
不同的半导体制造公司和研发机构可能会有特定的流程和工艺参数。
因此,在实际应用中,需要根据具体需求和材料特性来设计和优化制造工艺流程。
半导体制造工艺流程

半导体制造工艺流程一、引言随着现代科技的飞速发展,半导体技术成为了各个领域中不可或缺的重要基础。
而半导体制造工艺流程则是半导体晶圆生产的关键环节之一、本文将详细介绍半导体制造工艺流程的基本步骤和各个环节所涉及的具体工艺。
二、半导体制造工艺流程1.半导体晶圆清洁:首先需要将半导体晶圆进行清洁处理,以去除表面的杂质和污染物。
这一步骤通常通过使用化学溶液进行清洗,如硝酸、氢氟酸等。
2.晶圆扩散:在晶圆表面进行扩散处理,将一些所需的杂质元素或金属离子引入到晶圆表面,以调整半导体材料的电学性能。
这一步骤通常使用扩散炉进行,通过加热晶圆并与所需气体反应,使其在晶圆表面沉积。
3.光罩制备:通过利用光刻技术,制备用于掩膜的光罩。
光罩是由光刻胶覆盖的晶片,通过在特定区域曝光和显影,形成所需的图案。
4.光刻:将光罩与晶圆进行对位,通过紫外线照射和显影,将光刻胶所曝光区域中的图案转移到晶圆表面。
这一步骤可以定义出晶圆上的电路结构。
5.蚀刻:通过使用化学腐蚀物溶液,将未被光刻胶保护的区域进行蚀刻,以便去除不需要的物质。
这一步骤通常使用干法或湿法蚀刻。
6.沉积:在晶圆表面沉积所需的物质层,如金属、氧化物等。
通过化学气相沉积或物理气相沉积的方法进行。
这一步骤用于制备导线、电容器等元件的电介质层或金属电极。
7.退火:通过加热晶圆并使用气体或纯净的其中一种环境,使其在特定温度和时间下进行退火处理。
这一步骤旨在消除应力,提高晶圆的导电性和结构完整性。
8.电镀:在晶圆表面涂覆金属层,通常使用电化学方法进行。
这一步骤主要用于形成连接器或其他需要导电层的电路结构。
9.封装测试:将晶圆进行切割和封装,形成单个芯片。
然后通过进行功能测试和可靠性测试,以确保芯片的质量和性能。
10.出厂测试:对封装好的芯片进行全面的测试和筛选,以确保只有符合规格要求的芯片进入市场。
三、结论以上是半导体制造工艺流程的基本步骤和环节。
每个步骤都是半导体制造中不可或缺的重要环节,一环扣一环,相互依赖。
- 1、下载文档前请自行甄别文档内容的完整性,平台不提供额外的编辑、内容补充、找答案等附加服务。
- 2、"仅部分预览"的文档,不可在线预览部分如存在完整性等问题,可反馈申请退款(可完整预览的文档不适用该条件!)。
- 3、如文档侵犯您的权益,请联系客服反馈,我们会尽快为您处理(人工客服工作时间:9:00-18:30)。
单晶通常采用两种制作方法: 一. 直拉法(Czochralski法)
在真空腔室内,把多晶硅放在石英坩埚中 加热到1500° 用0.5cmX10cm的籽晶体,逆时针旋转提拉。 可制 成8寸、1-2M的晶棒。 可提纯到 99.999999999 % 纯度
二. 区熔法
此种方法可以生长极高纯度的硅单晶。 但区熔生长的缺点是很难引入浓度均匀的掺杂。
2000 1992 1965 1975 1981 1987
50mm 100mm 125mm 150mm 2′ 4′ 5′ 6′ 8′
200mm 12′
300mm
在国内也不是很普及。
不同尺寸的硅片—从开始生产 —到生产高峰 — 再到逐步淘汰的生命周期
100mm 1975年 150mm 14年 1983年 200mm 20年 1987年 300mm 1995年 10年 1984年 20年 20年? 在美国已经淘汰 1997年 2003年 30年 2007年 2017年 40年 40年 2035年?
是一种双极和CMOS兼容工艺。主要用于静态随 机存储器、高速电路和数模混合电路的设计。 采用两种工艺的目的主要是充分利用两种工艺各 自的特点, BiCMOS工艺技术对于不同的电路设计方法具有极 强的适应性
典型的PN结隔离的掺金T T L电路工艺流 程
硅平面工艺主要由氧化—扩散—掺杂三个工艺组成
衬底制备 基区光刻 基区扩散 一次氧化 再氧化 再分布及氧化 隐埋层光刻 隔离扩散 发射区光刻 隐埋层扩散 隔离光刻 背面掺金 外延淀积 热氧化 发射区扩散
线宽
间距
关键尺寸
4.1.2 每块芯片上的元件数
减小一块芯片上的特征尺寸使得可以在硅片上制作更多的元件。对于 微处理器,芯片表面的晶体管数可以说明通过减小CD来增加芯片的集成 度。由于芯片上的晶体管数量连年极具增加,芯片性能也提高。
1600
微处 1400 理器 1200 上的 总的 1000 晶体 管数 800 ,以 百万 600 为单 400 位
100M
10M 晶 体 管 100K 8086 1M 80286 80386 80486
本腾
500 Pentium Pro
10K 4004
每 秒 百 1.0 万 条 指 0.1 令
25 .01
8080
年度
1975
1980
1985
1990
1995
2000
关于微处理器的摩尔定律
4.1.4
功耗
芯片性能的另一方面是在器件工作过程中的功耗。随着器 件的微型化,功耗也相应减小。这已成为便携式电子产品市场 增长的一个关键性能参数。
半导体工艺制程
一. 二. 三.
半导体相关知识 半导体前工序介绍 半导体后工序介绍
1.
半导体相关知识
1. 集成时代的开始
从晶体管的发明到 大规模集成电路的广泛使用 经过了六十年发展 晶体管(1947年)—大规模集成电路(ULSI) 大于1KK百万以上
2. 硅片尺寸的演化
随着IC规模的增大,管芯面积也急速增大,迫使要 采用大直径硅片,以提高产能。 84年以前使用1寸 2寸 90年4寸 目前使用8英寸(200mm)、12英寸(300mm)转变。 现在6寸也没有完全普及
二、中测
生产过程中经常要对各种样片(陪片)进行测试。 经过Wafer Fab制程后,硅片上形成数千上万个电 路,一般称之为管芯或晶粒(Die)。在一般情形下,同 一片硅片上制作相同的器件,但是也有可能在同一片 晶圆上制作不同规格的产品。 制作完成的硅片必须使用探针台对所有管芯进行 100%的直流参数测试,以测试其电气特性。不合格 管芯将会被打上记号(Ink Dot),可以用磁性墨水, 最后经过划片分离后吸走。此程序即称之为晶圆测试 制程(Wafer Probe)。然后将管芯分割成独立的管 芯去做最后的封装。
P
- - ++ - - ++ N - - ++
半导电路的设计和制造技术的快速发展,导致也促 进了半导体生产制造新设备和新工艺的不断引入。每隔 18到24个月,半导体产业就引进新的制造技术。 硅片制造技术的改变受到用户需求的驱使。用户要 求更快、更可靠和更低成本的芯片。要达到这些要求,芯 片制造商需要在一个硅片上缩小管芯尺寸、提高芯片速 度、减少功耗。 最大限度地提高芯片性能 提高芯片可靠性 追求降低芯片成本
100
0
1972
1976
1980
1984 1988
1992
1996 2000
年度
芯片可靠性提高
4.1.6 降低芯片价格
半导体微芯片的价格一直持续下降。到1996年之前 的近50年中,半导体芯片的价格以一亿倍的情况下降。
10 4 标准管 2 微型管 双极晶体管 10
真空管 半导体器件
MSI 集成电路
一、工艺处理制程
目前生产工艺的难点不在于我们不知道怎样做,而是在 于由于受到设备限制使我们无法完成想要做的工艺
半导体制作主要是在硅片上制作电子器件(晶体管、电容、 逻辑闸等)以达到一定的逻辑功能。在上述各道工艺中技术最复 杂且资金投入最多的就是微处理器Microprocessor),所需工序 多达数百道,加工设备也先进、昂贵,甚至上千万一台。净化厂 房对温度、湿度与尘埃含量均需严格控制。 虽然生产工艺随着产品种类与所使用的技术有关;但基本工 艺步骤通常是: 硅片-清洗(Cleaning)—氧化(Oxidation)—沉淀—光刻—蚀 刻—离子注入等多次重复的工序进行。在硅片上制作晶体管、二 极管、电阻,完成带有逻辑功能的集成电路的加工与制作。
第一次光刻—N+埋层扩散孔
1。减小集电极串联电阻
2。减小寄生PNP管的影响
要求: 1. 杂质固浓度大 2. 高温时在Si中的扩散系数小, 以减小上推 3. 与衬底晶格匹配好,以减小应力 SiO2 N+-BL P-SUB
涂胶—烘烤---掩膜(曝光)---显影---坚膜—蚀刻—清洗 —去膜--清洗—N+扩散(P)
相 对 值
1
器件尺寸
LSI
10
-2
VLSI
价格
10
-4
10美元=1晶体管
-6
ULSI
10
10美元=IG U盘
IG U盘 =? 管子
10
-8
10
-10 1930 1940 1950 1960 1970 1980 1990 2000 年度
半导体芯片价格降低
5. 电子时代的划分
20世纪50年代: 晶体管技术
三、IC 封装制程
IC封装制程(Packaging): 无论采用塑封还是瓷封或金属管壳封装都 是为了制作电路的保护层,避免电路受到机械 性划伤或高温破坏。也有不做封装就使用的。 从环境、用途、成本考虑。 用户市场的需求
四. 半导体制造工艺分类
MOS型 双极型
PMOS型
NMOS型
CMOS型
饱和型
非饱和型
BiCMOS
TTL
IIL
ECL/CML
一
双极型工艺:
A 在每个器件间要做隔离区(PN结隔离、全介质 隔离及PN结、介质混合隔离) ECL (非饱和型) (不掺金) 、TTL/DTL (饱 和型) 、STTL (饱和型)
B 在元器件间自然隔离 IIL(饱和型)
二
MOS IC 工艺: 是根据栅工艺分类 A 铝栅工艺 B 硅栅工艺 其他分类 1 、(根据沟道) PMOS、NMOS、CMOS 2 、(根据负载元件)E/R、E/E、E/D
硅是4 价元素 价层价电子为4个 掺入 V 族元素-- 磷P、砷As、锑Sb 价层中价电子为5个与硅原子结合多出1个价电子 成为导电电子,带负电,形成N型硅: 掺入 III族元素-- 硼B 、镓Ga 价层中价电子为3个而与硅原子结合后少一个价电 子产生一个空穴,带负电,形成P型硅: PN结:
4.1 提高芯片性能和集成度
4.1.1 关键尺寸(CD)
特征尺寸的过去与将来的技术节点
1988 1992 1995 1997 1999 2001 2002 2005 CD (µm ) 1.0 0.5
现在已经进入 纳米时代
0.35 0.25
0.18
0.15
0.13 0.10
接触孔
1 毫米(mm) = 1 000 微米( µm ) 1 微米( µm ) = 1000 纳米(nm)
20世纪60年代: 工艺技术
20世纪70年代: 竞争
20世纪80年代: 自动化 20世纪90年代: 批量生产 21世纪: 器件进入规模时代和智能时代
半导体制造分为
前道工序(Front End)制程
晶圆处理制程(Wafer Fabrication; 简称 Wafer Fab) 管芯中测(Wafer Probe); 中测直流参数测试 “在整个加工过程中每一步都含各种测试” 后道工序(Back End) 制程 封装(Packaging) 成测(Initial Test and Final Test) 成测交、直流参数测试
200 40
1997 1999 2001 2003 2006 2009 2012 年度
总的晶体管/芯片增长
4.1.3
摩尔定律
1964年,戈登摩尔—半导体产业先驱者和英特尔公司的创始人。 预言在一块芯片上的晶体管数量大约每隔一年翻一番。 这就是业界著名的摩尔定律(后来在1975年被修正为预言没18个月翻一 番)。摩尔定律在微处理器的发展上(晶体管数),是惊人的准确。
铝合金 淀积钝化层
反刻铝
压焊块光刻
铝淀积
中测
接触孔光刻
再分布及氧化
晶体管横向刨面图
B
C
E P P P+