自动轧管机组生产工艺
轧管工艺流程

轧管工艺流程轧管工艺是一种将钢坯加工成管道的工艺,其具有工艺简单、生产效率高、成本低等优点,是现代钢铁生产中广泛采用的一种技术。
下面我们将针对轧管工艺流程进行整体介绍并详细描述每个环节,希望能够对读者有所帮助。
一、轧管工艺流程1.原材料准备:将钢坯进行切割、热处理等预处理工艺,使其达到生产要求。
2.热轧:将预处理后的钢坯通过热轧机组进行加热和轧制,以形成钢卷。
3.钢卷开卷:将钢卷通过开卷机进行开卷,并利用飞剪机对钢卷进行切割。
4.焊接:将切割后的钢板进行输送,并通过高频焊接技术进行焊接。
5.冷卷:将焊接后的钢管通过冷卷机进行加工,形成成品钢管。
6.成品加工:对成品钢管进行校直、切断等加工工艺,使之符合生产要求。
7.检验:对成品钢管进行外观质量和物理性能等方面的检验。
8.包装和运输:对符合生产要求的成品钢管进行包装和运输。
以上为轧管工艺的整体流程,下面对每个环节进行详细描述。
二、详细步骤分析1.原材料准备轧管的原材料多采用热轧钢板,也有一部分采用冷轧钢板及其他原材料。
对于热轧钢板来说,由于长时间的热轧加工过程,其内部结构已经较为均匀,因此需要对其进行裁切。
裁切工艺的要求是尽可能减少切头和切尾缺陷,同时能够满足不同材料规格及尺寸的需求。
裁切后的钢板还需进行热处理,以消除内部应力,提高钢板性能,这样才能满足后续工艺的需要。
2.热轧钢坯经预处理后,进入热轧机组进行轧制,形成钢卷。
热轧一般使用粗轧和精轧两种轧制工艺。
粗轧采用完成度较低的轧辊进行轧制,使钢坯变形量大,锻造性能得到改变。
粗轧后的钢坯进入精轧机组进行精轧,精轧主要分为单机和多机轧制两种方式。
单机精轧是指通过精轧机组一次性完成轧制的工艺,多机轧制则是通过多台机组的不同轧制次序,逐步完成产品的轧制加工。
3.钢卷开卷轧制完成后的钢卷进入开卷机组,通过卷扬、卷弯等方式将钢卷完成开卷,以进行下一步的加工处理。
为了提高加工效率,减少废料产生,开卷后的钢卷需通过飞剪机进行切割,使之得到符合要求的钢板。
钢管轧机生产工艺流程

钢管轧机生产工艺流程
序号流程步骤具体内容
1 坯料准备选择合适的钢坯,进行检验、清理和锯切,确保坯料尺寸和质
量符合要求。
2 加热将坯料放入加热炉中加热至合适的轧制温度。
3 穿孔通过穿孔机将加热后的坯料穿成空心毛管。
4 轧管使用轧管机对毛管进行轧制,使其壁厚和外径达到预定尺寸。
5 定径或减
径根据产品要求,通过定径机或减径机对轧后的钢管进行尺寸精度调整。
6 冷却采用空冷、水冷或缓冷等方式对钢管进行冷却。
7 矫直使用矫直机对冷却后的钢管进行矫直,消除弯曲和扭曲。
8 探伤检测采用无损探伤方法(如超声波、涡流等)检测钢管内部和表面
的缺陷。
9 切头尾切除钢管两端的不规则部分,保证长度和质量。
10 表面处理对钢管进行酸洗、磷化、涂油等表面处理,提高防锈和防腐性
能。
11 成品检验对成品钢管进行尺寸、性能、外观等方面的最终检验。
12 包装入库检验合格的钢管进行包装,然后入库储存或发货。
热轧钢管生产工艺流程
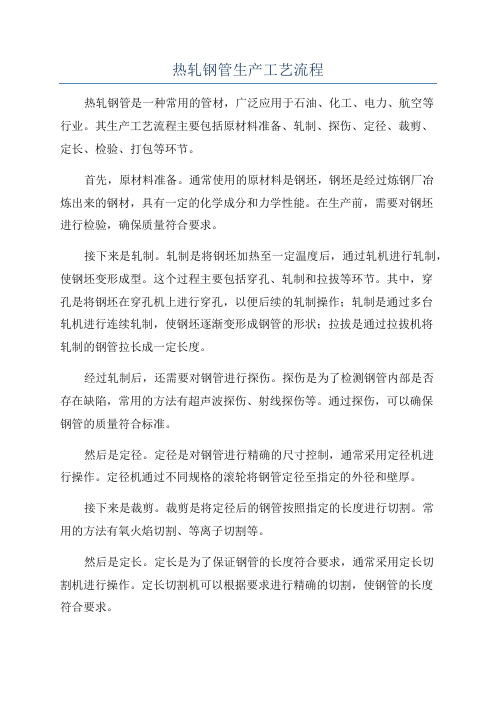
热轧钢管生产工艺流程热轧钢管是一种常用的管材,广泛应用于石油、化工、电力、航空等行业。
其生产工艺流程主要包括原材料准备、轧制、探伤、定径、裁剪、定长、检验、打包等环节。
首先,原材料准备。
通常使用的原材料是钢坯,钢坯是经过炼钢厂冶炼出来的钢材,具有一定的化学成分和力学性能。
在生产前,需要对钢坯进行检验,确保质量符合要求。
接下来是轧制。
轧制是将钢坯加热至一定温度后,通过轧机进行轧制,使钢坯变形成型。
这个过程主要包括穿孔、轧制和拉拔等环节。
其中,穿孔是将钢坯在穿孔机上进行穿孔,以便后续的轧制操作;轧制是通过多台轧机进行连续轧制,使钢坯逐渐变形成钢管的形状;拉拔是通过拉拔机将轧制的钢管拉长成一定长度。
经过轧制后,还需要对钢管进行探伤。
探伤是为了检测钢管内部是否存在缺陷,常用的方法有超声波探伤、射线探伤等。
通过探伤,可以确保钢管的质量符合标准。
然后是定径。
定径是对钢管进行精确的尺寸控制,通常采用定径机进行操作。
定径机通过不同规格的滚轮将钢管定径至指定的外径和壁厚。
接下来是裁剪。
裁剪是将定径后的钢管按照指定的长度进行切割。
常用的方法有氧火焰切割、等离子切割等。
然后是定长。
定长是为了保证钢管的长度符合要求,通常采用定长切割机进行操作。
定长切割机可以根据要求进行精确的切割,使钢管的长度符合要求。
接下来是检验。
检验是对钢管进行各项性能指标的检测,包括化学成分、力学性能、尺寸精度等。
只有通过检验合格的钢管才能进入下一环节。
最后是打包。
根据客户要求,将合格的钢管进行打包,以便运输和使用。
综上所述,热轧钢管的生产工艺流程主要包括原材料准备、轧制、探伤、定径、裁剪、定长、检验、打包等环节。
通过这些环节,可以确保热轧钢管的质量和尺寸符合要求,以满足客户的需求。
Accu_Roll轧管机工艺特性析
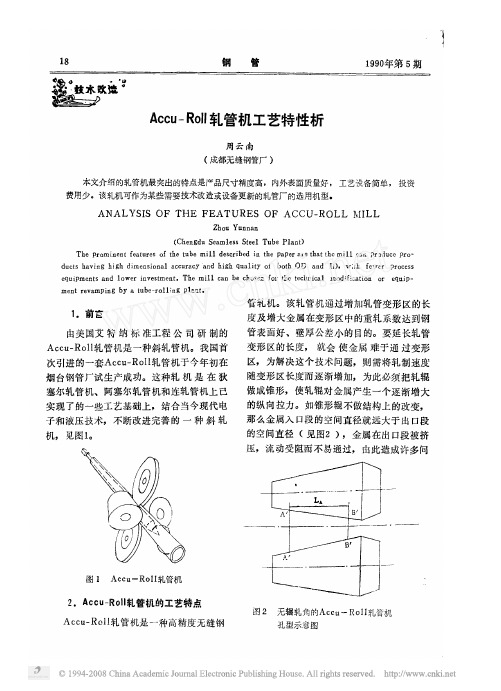
那 么 金 属 入 口 段 的 空 间直 径 就 远 大 于 出 口 段 见图
,
机
,
见图
金属 在 出 口 段被挤
,
流 动 受 阻而 不 易通 过
由此 造 成 许 多 间
{ 叹 止一 叮一
} 、
图
一
一
轧管机
轧 管 机 的工 艺特点
图
无辗 轧 角 的
孔 型示 意 图
一
轧管机
一
轧 管 机 是 一 种 高 精度 无 缝 钢
轧 管 机 在 中 国 的投 产
明 了 上 述 工 艺 特 点的优 越 性
。
大导 盘
,
竺
增 加 推力
,
,
采 用 大 导 盘 可 以 精确 导 向
减 少 阻力
,
改善金属流动
。
,
增加 金 属稳 定
节
。
性
。
导 盘 与轧辊 组 成 一 个 封 闭 孔 型 导 盘 可作上 下
、
使钢管
图
一
轧管 机 孔 型 示 意 图
一
及
,
,
。
轧管 机 产 品 精 度 高
,
产量 中
,
一
工 艺 的 总变 形 量 为
,
。
左右
,
等
,
消 耗较 低
,
、
工 艺 设 备简 单
品种多
适
、
单机压缩 比 为
理论
,
较 小 的压 缩 比 对 钢 管 根据现 代 塑性变 形
应性强
该 轧 机 完 全 可 作 为 自动 轧 管 机
。
内 在 质 量 没 有不 利 影 响
三辊轧管机
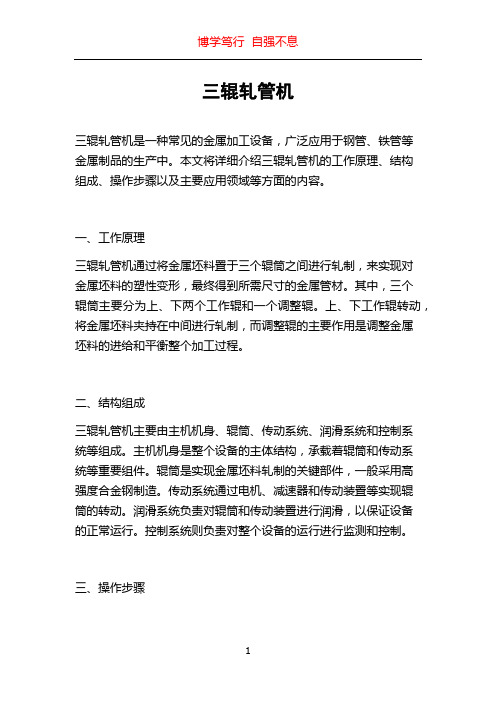
三辊轧管机三辊轧管机是一种常见的金属加工设备,广泛应用于钢管、铁管等金属制品的生产中。
本文将详细介绍三辊轧管机的工作原理、结构组成、操作步骤以及主要应用领域等方面的内容。
一、工作原理三辊轧管机通过将金属坯料置于三个辊筒之间进行轧制,来实现对金属坯料的塑性变形,最终得到所需尺寸的金属管材。
其中,三个辊筒主要分为上、下两个工作辊和一个调整辊。
上、下工作辊转动,将金属坯料夹持在中间进行轧制,而调整辊的主要作用是调整金属坯料的进给和平衡整个加工过程。
二、结构组成三辊轧管机主要由主机机身、辊筒、传动系统、润滑系统和控制系统等组成。
主机机身是整个设备的主体结构,承载着辊筒和传动系统等重要组件。
辊筒是实现金属坯料轧制的关键部件,一般采用高强度合金钢制造。
传动系统通过电机、减速器和传动装置等实现辊筒的转动。
润滑系统负责对辊筒和传动装置进行润滑,以保证设备的正常运行。
控制系统则负责对整个设备的运行进行监测和控制。
三、操作步骤1. 将金属坯料放置在进料口处,调整辊筒的间隙,使其与金属坯料接触。
2. 启动三辊轧管机,在保证设备正常运行的前提下,逐渐提高辊筒的转速,使其夹持金属坯料并开始轧制。
3. 根据所需的管材尺寸,逐步调整辊筒的间隙,控制金属坯料的压缩和轧制过程。
4. 在轧制过程中,及时对设备进行润滑,确保运行平稳。
5. 当金属坯料完成轧制后,停止设备并取出轧制好的金属管材。
四、主要应用领域三辊轧管机广泛应用于石油、化工、天然气、航空航天等领域。
主要用于制造各种规格的钢管、铁管、无缝管等金属管材。
在石油行业中,三辊轧管机被用于生产石油输送管道,可有效提高管道的质量和密封性能。
在化工领域,三辊轧管机可制造各种规格的化工管道,用于液体、气体等介质的输送。
而在航空航天领域,三辊轧管机则用于制造飞机、导弹等航空器件所需的金属管材。
总结起来,三辊轧管机是一种常见的金属加工设备,通过对金属坯料的轧制,实现对金属管材的制造。
它具备工作原理简单、操作方便等优点,因此在石油、化工、航空航天等领域的金属管材生产中广泛应用。
Φ720mm周期轧管机组的工艺和设备

炉和机械式室式加热炉、淬火水池、控冷设施,超 声波探伤机、磁粉探伤机,压力矫直机和内外修磨 机等多台设备。
2 主要设备组成和特点
Φ720 mm 周期轧管机组的主要设备有:环形 加热炉、立式水压冲孔机、二辊桶形辊穿孔机、喂 料器、周期轧管机、热锯、步进式再加热炉、5 机 架三辊定径机。其主要设备的特点如下。
1) 立式水压冲孔机 25 MN 水压冲孔机本体主要部件组成如图 2 所示。 主工作缸为柱塞缸,在压力为 28 MPa 的介质 作用下,产生的公称压力为 25 MN。回程缸为差 动式柱塞缸,缸体安装在机架的两侧,生产回程力 3.45 MN。活动横梁主要用来传递冲压力,同时起 冲杆的导向作用。活动横梁上部用压圈与主柱塞连 接定位,下部安装有冲杆,活动横梁导向形式为 X 形,当活动横梁或机架热胀冷缩时,导向可以沿 X 方向自由伸缩,保持活动横梁运动灵活。导向装置 安装在机架的四侧,作活动横梁和定位脱料装置导 向用。定位脱料装置在机架内做升降运动,主要起 冲杆的模口定位和回程脱料作用。移动工作台在由 工作台支座和辅助座组成的导向面上移动,工作台 移动由移动油缸驱动。工作台上装有冲孔凹模,工 作台两个工位(冲孔位和上料位,上料位同时也是
偿,能精确保证 90°翻转,保证产品质量,减少咬 入打头次数。
(4) 制动刷具备调节功能,可灵活实现轧制节 奏同步,并保证芯棒上的毛管处于正确的位置。
(5) 油作为制动介质,在制动和冷却空气活塞 时可防止生锈。
(6) 机械限制可调喂入量,可实现每一个轧制 周期都有一个均匀而准确的喂入量,以保证钢管尺 寸精度。
Key words:Pilger pipe mill;Sizing mill;Vertical hydraulic piercing;Process flow;Technical parameters
轧管机的工作原理简介

轧管机的工作原理简介1. 轧管机的工作原理简介轧管机是一种用于制造金属管材的机械设备。
它通过将金属材料经过多次轧制,使其形成所需的管材形状和尺寸。
在轧制过程中,轧管机主要通过热轧或冷轧两种不同的工艺来完成。
下面将介绍轧管机的工作原理以及它的关键组成部分。
2. 热轧轧管机的工作原理热轧轧管机主要用于加工高温金属坯料,如钢坯。
它的工作原理可以概括为以下几个步骤:步骤一:物料预热将钢坯通过加热炉等设备进行预热。
这么做的目的是提高钢材的可塑性,使其更容易塑性变形。
步骤二:入口端对齐将预热后的钢坯送入轧管机,通过辊道和辊缝的定位,将钢坯的入口端对齐,以确保轧制的准确度和稳定性。
步骤三:辊道轧制在钢坯进入辊道后,它会被传送到辊缝之间。
辊道上的辊子组按照一定规律布置,当钢坯经过时,辊子组作用下的压力使得钢坯逐渐变薄并改变形状。
这一步骤通常需要多个辊子组的连续作用,以实现所需的深度和形状。
步骤四:尺寸定型经过一系列的轧制后,钢坯的形状和尺寸已经接近最终要求。
此时,进一步通过调整和矫正辊缝间距、辊子组的排布等方式,以确保钢坯的精度和尺寸满足要求。
步骤五:产出经过尺寸定型后,经过轧制的钢坯被切割成所需长度,并通过传送带等方式将成品管材输送到下一个制造环节,如焊接或后续的加工工艺。
3. 冷轧轧管机的工作原理与热轧轧管机相比,冷轧轧管机主要用于加工室温下的金属坯料,如冷轧钢板。
其工作原理与热轧轧管机类似,但有一些区别。
冷轧轧管机不需要对金属坯料进行预热,因为它们已经处于室温下。
在入口端对齐之后,钢坯进入辊道,经过一系列的辊子组轧制,使其形成所需形状和尺寸。
不同之处在于,冷轧过程中对钢板施加的压力较小,以避免在金属坯料加工过程中出现塑性变形不良或其他结构性问题。
冷轧轧管机通常需要进行多次轧制,以逐渐达到所需尺寸和形状。
与热轧相比,冷轧后的成品管材表面更加光滑,并且具有更高的尺寸精度。
4. 轧管机的关键组成部分无论是热轧还是冷轧轧管机,它们都由一些关键组成部分构成,以实现其工作原理。
ACCU—ROLL新型斜轧管机工艺技术操作规程

一、ACCU—ROLL轧机技术操作规程1.ACCU—ROLL轧机主要技术性能:1.1 穿孔空心坯规格:外径:Φ150~Φ305mm壁厚:9.23~32.75mm长度:4.79-10.00M1. 2 Accu—Roll轧机出口荒管构规格:外径: Φ 150~Φ295mm壁厚:3.23~24.75mm长度:11.32-19.50MAccu-Roll轧机出口荒管速度:uV= 0.3~1.0M/SAccu-Roll轧机喂入角:5º~10ºAccu-Roll轧机辗轧角:10º~15º2 生产前的准备工作:2.1 检查轧机区域液压、干油、稀油、高压水、通风系统、设备状况,确保工作正常。
2.2 检查轧机区域各机械设备状况,确保空负荷试车正常。
2.3 检查轧机区域各电气设备、控制、硬件系统,操作台各部位登仪表是否完好、准确,确保工作正常。
2.4 检查轧机区域工具的规格和使用状态是否符合生产要求(详见工具配换表及轧制尺寸表)。
2.5 检查轧机区域各故障显示和报警系统,确认工作正常。
2.6 检查轧机区域冷却水,芯棒、导盘润滑系统,确保工作正常。
2.7 检查轧机区域各操作开关,程序控制开关,确认复位。
2.8 在确认设备状况正常,配换工具符合要求,轧机及辅机各调整参数满足生产后,方可进行手动分区启动,空负荷连动运行。
3 Accu-Roll轧机区域的调整:Accu-Roll轧机区域的调整主要分为:速度调节、压力调节和位置调节三种。
3.1速度调节:它分为自动速度和手动速度调节:3.1.1 自动速度调节:通过改变MMI速度的设定值,由程序实现速度自动控制。
3.1.2 手动速度调节:手动操作台上电位器旋钮实现速度调节。
3.2 位置调节:在进行位置调节时,须保证各调节回路处于无负荷状态,调整部位的锁紧系统处于低压锁紧状态,在轧机区需要随规格变化而调整的回路有:预穿台高度调整、斜送辊高度调整、抱瓦开口度调整,导盘和轧辊调整。