船体曲面分段装配中心(流水线)方案提纲
船体分段装配工艺
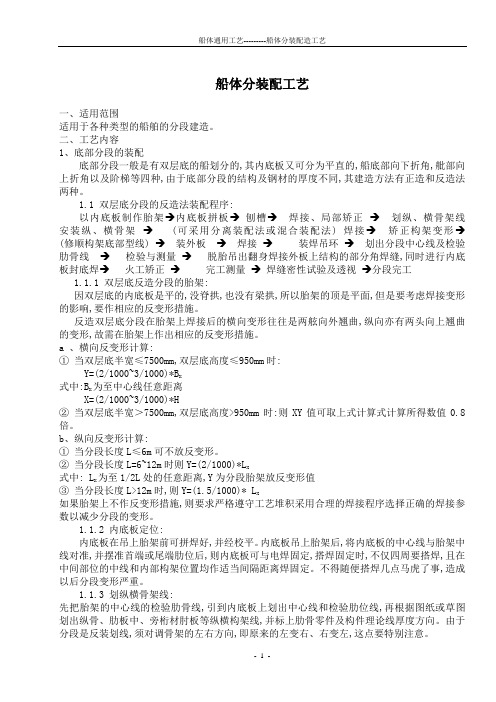
船体分装配工艺一、适用范围适用于各种类型的船舶的分段建造。
二、工艺内容1、底部分段的装配底部分段一般是有双层底的船划分的,其内底板又可分为平直的,船底部向下折角,舭部向上折角以及阶梯等四种,由于底部分段的结构及钢材的厚度不同,其建造方法有正造和反造法两种。
1.1 双层底分段的反造法装配程序:以内底板制作胎架→内底板拼板→刨槽→焊接、局部矫正→划纵、横骨架线安装纵、横骨架→ (可采用分离装配法或混合装配法) 焊接→矫正构架变形→(修顺构架底部型线) →装外板→焊接→装焊吊环→划出分段中心线及检验肋骨线→检验与测量→脱胎吊出翻身焊接外板上结构的部分角焊缝,同时进行内底板封底焊→火工矫正→完工测量→焊缝密性试验及透视→分段完工1.1.1 双层底反造分段的胎架:因双层底的内底板是平的,没脊拱,也没有梁拱,所以胎架的顶是平面,但是要考虑焊接变形的影响,要作相应的反变形措施。
反造双层底分段在胎架上焊接后的横向变形往往是两舷向外翘曲,纵向亦有两头向上翘曲的变形,故需在胎架上作出相应的反变形措施。
a 、横向反变形计算:①当双层底半宽≤7500mm,双层底高度≤950mm时:Y=(2/1000~3/1000)*BX为至中心线任意距离式中:BXX=(2/1000~3/1000)*H②当双层底半宽>7500mm,双层底高度>950mm时:则XY值可取上式计算式计算所得数值0.8倍。
b、纵向反变形计算:①当分段长度L≤6m可不放反变形。
②当分段长度L=6~12m时则Y=(2/1000)*LX式中: L为至1/2L处的任意距离,Y为分段胎架放反变形值X③当分段长度L>12m时,则Y=(1.5/1000)* LX如果胎架上不作反变形措施,则要求严格遵守工艺堆积采用合理的焊接程序选择正确的焊接参数以减少分段的变形。
1.1.2 内底板定位:内底板在吊上胎架前可拼焊好,并经校平。
内底板吊上胎架后,将内底板的中心线与胎架中线对准,并摆准首端或尾端肋位后,则内底板可与电焊固定,搭焊固定时,不仅四周要搭焊,且在中间部位的中线和内部构架位置均作适当间隔距离焊固定。
船体加工与装配

船体加工精度控制
总结词
船体加工精度控制是确保船体装配质量和船舶性能的重要环节,涉及到船体零 部件加工、组装和焊接等多个环节。
详细描述
影响船体加工精度的因素较多,如加工设备精度、工艺参数、操作技能等。为 提高加工精度,需要加强设备维护和精度校准,制定合理的加工工艺和操作规 程,加强质量检测和控制。
船体装配效率提升
03
船体加工与装配中的问题与解决方案
船体结构强度问题
总结词
船体结构强度问题主要表现在船体结构在受到外力作用时易 发生变形或断裂,影响船舶的安全性能和使用寿命。
详细描述
船体结构设计不合理、材料选用不当、焊接质量差等都可能 导致船体结构强度问题。为解决这一问题,需要优化船体结 构设计,合理选用高强度材料,加强焊接质量控制,并进行 严格的强度试验和检测。
船体结构
该型船体采用典型的三段式结构,包括艏、 舯、艉三部分。
装配流程
先进行分段装配,然后进行总段装配,最后 进行整体装配。
加工工艺
采用数控机床进行精确加工,确保各段船体 的尺寸和形状符合设计要求。
质量控制
采用严格的质量控制体系,确保船体的加工 与装配精度。
某新型船体的加工与装配案例
船体设计
该型船体采用流线型设计,以减小阻 力并提高航速。
船体装配质量检测
质量检测是确保船体装配质量的 重要环节,包括对船体结构的检 测、焊接质量的检测以及对设备
和系统的测试等。
质量检测过程中,需要采用先进 的检测技术和设备,如激光测距 仪、超声波探伤仪等,对船体的
各个部位进行全面检测。
质量检测完成后,需要对检测结 果进行分析和评估,对不合格的 部分进行整改和修复,确保船体 的质量和性能符合规范和标准。
船体分段合拢施工要领 胎架制造、检验及一些注意事项

船体分段合拢施工要领为确保船体分段合拢后的主要尺度和外壳线型等符合图纸及相关船东、船级社的要求,特拟订本施工要领:1.根据图纸在船台(坞)上勘划出待合拢船舶的船体中心线和数根平行中心线,假定中心线及各分段的肋骨检验线,大接缝端线、船底水平线、船的总长、型宽、两柱间水线分别用漆笔或洋冲在船台(坞)上及标杆(坞墩)上做好标记。
2.货舱底部分段合拢定位1)将分段吊至船台的合拢处,调整分段中心线与船台中心线(假定中心线)吻合;将分段置于垫墩上,然后调整分段水平度,使各误差在公差范围内,分段一次定位结束后,需将各项数据记录完整。
2)按设计图纸规定的肋检线、半宽尺寸,测量分段接缝区的余量并勘测出余料线做好记录,测定各项数据经自检互检确认无误,并报专检确认后方可切割余量,并打好焊接坡口。
3)将分段吊起重新调整分段的中心线、肋检线与船台上线条吻合,再调整分段水平及高度符合标准要求,检查其与已合拢的几个分段肋检线的间距,保证在公差范围内及龙骨变形情况,做好自检互检记录经专检确认后进行定位焊及加强,分段二次定位结束。
4)待二次定位装配结束,须自查、互查合拢区结构完整性、板缝间隙、焊接坡口打磨情况等,测量各项数据的正确性确认无误后,报专检验收合格并报船东船检认可后方可进行焊接作业。
3.其它规则分段合拢定位1)此类分段包括货舱区舷侧、纵/横舱壁分段、甲板分段等。
2)在内底上勘划出待合拢的纵/横向舱壁、舷侧分段的结构线、肋检线,并标注好结构理论线方向。
3)分段合拢程序参见(2),舷侧段、横舱壁分段等需调整分段垂直度、高度、梁拱值、纵壁距中位置,甲板或平台的纵/横向高度、肋检线位置等,甲板需调整中心线(假定)、甲板水平度、肋检线与内底上肋检线的相交偏差等。
4.带主机座分段合拢定位1)分段合拢程序参见(2)。
2)分段中心线调整时按主机座中心线为依据并进行调整,而且要与船台中心线吻合,其误差在规范范围内。
3)分段水平及高度调整时应调整主机座面板,以四角水平及基座面板距基线高度为依据,并将调整后的所有数据做好详细记录,对主机座分段合拢时加以全过程重点监控。
船体装配讲义

第一章船舶分段的划分第一节船舶装配概述零件部件分段(总段)船台、船坞散装件1)部件装配:将加工好的零件装焊成小组件或大组件。
2)分段装配:将加工好的部件进行组装,形成分段的过程。
方箱子分段平面分段流水线3)分段总组:曲面分段、曲面分段进行组装,形成形成主体结构的分段。
4)总装大合拢:将总组好的分段到船台或船坞进行焊接的的过程。
1 分段建造装配顺序:铺板划线定位安装构件盖面2 分段制造方法1)放射法:先装纵骨,再装中间的肋板和间断桁材,交叉进行,最后吊中桁材。
2)插入法:先装间断桁材,再装肋板,最后吊中桁材,适用于中型船、横骨架式。
3)分离法:先装纵骨、间断桁材、中桁材,再插入肋板,适用于平直纵骨结构分段。
4)框架法:分段铺板焊接和划线在分段场地进行,而构架在专用胎架上进行制造,最后将构架所形成的框架整体吊上分段进行焊接。
分段构架装配采用那几种方法,这些方法的主要工序如何?船体装焊工艺路线,归纳起来有几条部序,四大部序。
第二节分段划分及编码方法一、分段划分的原则1)分段重量的选择受船厂起重能力和运输能力的限制。
2)生产负荷的均衡性分段数量的位置要于船台(船坞)装焊顺序和进度相符合。
3)船体结构的合理性分段划分的结构合理性,是船体结构特点对分段大接头的强度要求。
4)施工工艺的合理性A 扩大分段装配焊接的机械化、自动化范围。
B 分段大接缝布置的合理性,分段大接缝布置的合理不仅可以保证船体结构的合理,而且可以简化装配工作。
C 分段接头形式的合理性,单断面接头和阶梯形接头,板和骨架错开,错开距离在一档肋距内。
D 分段划分充分考虑钢材分段长度尽量与钢板规格或型才规格保持一致,我公司板材或型材长度一般为12m。
E 扩大预舾装。
二、分段编码横向位置代码数量顺序代码分段层次代码分段构造代码(这里表示底部)分段区域代码(这里表示货舱区)分段构造代码:底部 B Botton边底W Wing舷侧S Side上甲板 D Deck横隔舱T Transverse bulkhead纵隔舱L Longitudinal bulkhead半立体分段G特殊分段尾柱SF烟囱FU挂舵臂RH分段层次代码:0 底部分段1 上甲板及面层各分段2 二甲板3 三甲板1、请代入船体划分的原则2、说明CB05P/S、EG11P/S、FG21第二章分段与总段的制造(胎架部分)第一节胎架的划分一、胎架基准面的切取1 胎架的作用:作为制造分段的专用工装设备。
船体分段制作工艺流程

船体分段制作工艺流程船体分段现场制造工艺流程生产范围大组立是船舶制造的一种生产管理模式,是船体分段装配的一个生产阶段。
就是将零件和部件组成分段的生产过程。
人员搭配大组立生产以班为单位,一个班一般分为三到四个班组,一个班组的成员有一个组长、三个师傅、六个徒弟、两个电焊工、一个打磨工。
图纸资料大组立相关图纸有零件明细表、产品完工图、制作工艺、焊接工艺等。
工具割枪、米尺、线垂、千斤顶、水平尺、水平管、花兰螺丝、铁锤、铁楔、角尺、电焊机、自动二氧化碳焊接、打磨机机舱双层底大组立机舱双层底工艺流程胎架或平台准备——铺内底板——构件安装位置划线——构件安装——焊接——管铁舾装安装焊接——外板安装——焊前检查——构件与外板焊接——打磨——密性实验——交验装配作业标准分段长:L <±4mm分段宽: B <±4mm分段高:H <±4mm分段方正度:(内底板四角水平)<±8mm(加测机座内底板水平)货舱双层底大组立工艺流程胎架或平台准备——内底板拼装——自动二氧化碳焊接——构件安装位置划线——内底纵骨安装焊接——构件小组(肋板)安装焊接——舾装——补漆¬外底板拼装——焊接——构件安装位置划线——外底纵骨装焊——组装完成——焊接——打磨——舾装——完工检查——报验装配作业标准分段长:L <±4mm分段宽:B <±4mm分段高:H <±3mm分段方正度:<4mm (内、外底板对角线差值)分段扭曲度:<±8mm (内底板四角水平)纵骨端平面度:<±4mm内、外底板中心线偏差<±3mm内、外底板肋位线偏差<±3mm货舱顶边水舱大组立货舱顶边水舱分段工艺流程胎架或平台准备——斜板拼装——焊接——构件安装位置划线——斜板纵骨安装焊接——构件(肋板)安装焊接——舾装——补漆¬甲板拼装——焊接——纵骨装焊——组装完成——焊接——打磨——舾装——完工检查——报验装配作业标准分段长: L <±4mm分段宽: B <±4mm分段高: H <±4mm分段方正度:(测上甲板)<4mm分段扭曲度:(上甲班)<±8mm纵骨端平面:<±4mm货舱舭部大组立工艺流程胎架或平台准备——斜底板拼装——焊接——构件安装位置划线——斜底纵骨安装焊接——构件小组(肋板)安装焊接——舾装——补漆¬外底板拼装——焊接——构件安装位置划线——外底纵骨装焊——组装完成——焊接——打磨——舾装——完工检查——报验装配作业标准分段长: L <±4mm分段宽: B <±4mm内底高:H1±3mm舭部尖顶高:H2±4mm分段方正度:(测斜板)<4mm分段扭曲度:(测斜板)<±8mm。
船舶曲面分段制造成组技术研究
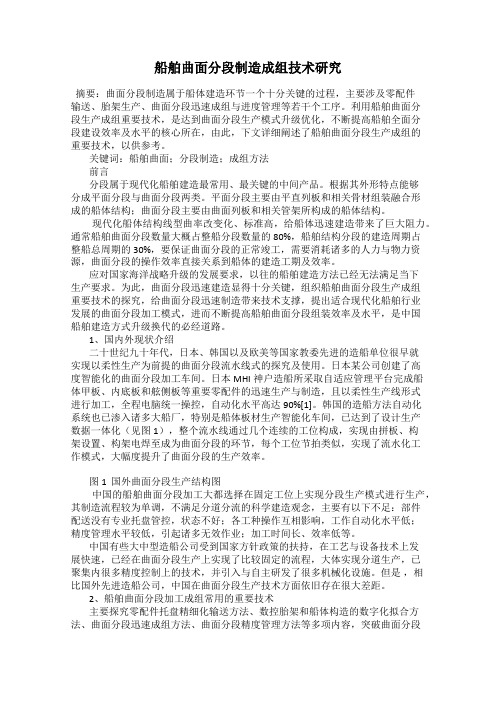
船舶曲面分段制造成组技术研究摘要:曲面分段制造属于船体建造环节一个十分关键的过程,主要涉及零配件输送、胎架生产、曲面分段迅速成组与进度管理等若干个工序。
利用船舶曲面分段生产成组重要技术,是达到曲面分段生产模式升级优化,不断提高船舶全面分段建设效率及水平的核心所在,由此,下文详细阐述了船舶曲面分段生产成组的重要技术,以供参考。
关键词:船舶曲面;分段制造;成组方法前言分段属于现代化船舶建造最常用、最关键的中间产品。
根据其外形特点能够分成平面分段与曲面分段两类。
平面分段主要由平直列板和相关骨材组装融合形成的船体结构;曲面分段主要由曲面列板和相关管架所构成的船体结构。
现代化船体结构线型曲率改变化、标准高,给船体迅速建造带来了巨大阻力。
通常船舶曲面分段数量大概占整船分段数量的80%,船舶结构分段的建造周期占整船总周期的30%,要保证曲面分段的正常竣工,需要消耗诸多的人力与物力资源,曲面分段的操作效率直接关系到船体的建造工期及效率。
应对国家海洋战略升级的发展要求,以往的船舶建造方法已经无法满足当下生产要求。
为此,曲面分段迅速建造显得十分关键,组织船舶曲面分段生产成组重要技术的探究,给曲面分段迅速制造带来技术支撑,提出适合现代化船舶行业发展的曲面分段加工模式,进而不断提高船舶曲面分段组装效率及水平,是中国船舶建造方式升级换代的必经道路。
1、国内外现状介绍二十世纪九十年代,日本、韩国以及欧美等国家教委先进的造船单位很早就实现以柔性生产为前提的曲面分段流水线式的探究及使用。
日本某公司创建了高度智能化的曲面分段加工车间。
日本MHI神户造船所采取自适应管理平台完成船体甲板、内底板和舷侧板等重要零配件的迅速生产与制造,且以柔性生产线形式进行加工,全程电脑统一操控,自动化水平高达90%[1]。
韩国的造船方法自动化系统也已渗入诸多大船厂,特别是船体板材生产智能化车间,已达到了设计生产数据一体化(见图1),整个流水线通过几个连续的工位构成,实现由拼板、构架设置、构架电焊至成为曲面分段的环节,每个工位节拍类似,实现了流水化工作模式,大幅度提升了曲面分段的生产效率。
船体分段装配流程
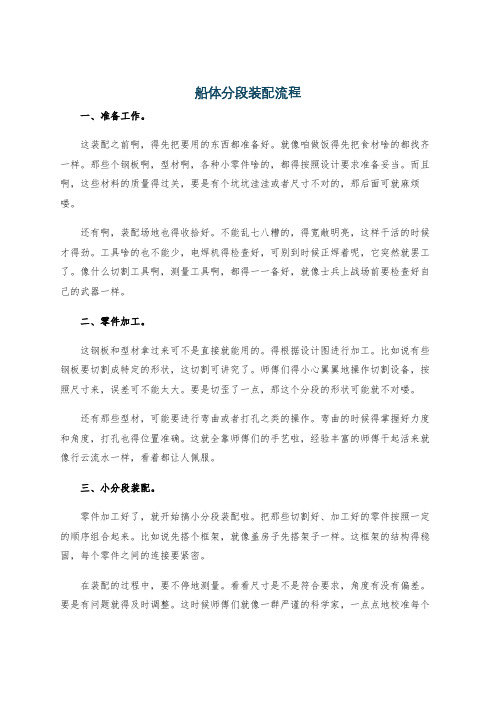
船体分段装配流程一、准备工作。
这装配之前啊,得先把要用的东西都准备好。
就像咱做饭得先把食材啥的都找齐一样。
那些个钢板啊,型材啊,各种小零件啥的,都得按照设计要求准备妥当。
而且啊,这些材料的质量得过关,要是有个坑坑洼洼或者尺寸不对的,那后面可就麻烦喽。
还有啊,装配场地也得收拾好。
不能乱七八糟的,得宽敞明亮,这样干活的时候才得劲。
工具啥的也不能少,电焊机得检查好,可别到时候正焊着呢,它突然就罢工了。
像什么切割工具啊,测量工具啊,都得一一备好,就像士兵上战场前要检查好自己的武器一样。
二、零件加工。
这钢板和型材拿过来可不是直接就能用的。
得根据设计图进行加工。
比如说有些钢板要切割成特定的形状,这切割可讲究了。
师傅们得小心翼翼地操作切割设备,按照尺寸来,误差可不能太大。
要是切歪了一点,那这个分段的形状可能就不对喽。
还有那些型材,可能要进行弯曲或者打孔之类的操作。
弯曲的时候得掌握好力度和角度,打孔也得位置准确。
这就全靠师傅们的手艺啦,经验丰富的师傅干起活来就像行云流水一样,看着都让人佩服。
三、小分段装配。
零件加工好了,就开始搞小分段装配啦。
把那些切割好、加工好的零件按照一定的顺序组合起来。
比如说先搭个框架,就像盖房子先搭架子一样。
这框架的结构得稳固,每个零件之间的连接要紧密。
在装配的过程中,要不停地测量。
看看尺寸是不是符合要求,角度有没有偏差。
要是有问题就得及时调整。
这时候师傅们就像一群严谨的科学家,一点点地校准每个数据。
而且啊,连接的方式也有很多种,有的是焊接,有的是用螺栓连接,这都得根据具体的要求来操作。
四、中分段装配。
小分段装配好了之后呢,就该把这些小分段组合成中分段啦。
这就像是把小积木拼成大积木一样。
不过这个过程可没那么简单哦。
要考虑到各个小分段之间的对接精度,不能有太大的缝隙。
在对接的时候,可能还需要对一些小分段进行微调。
这个时候就考验师傅们的耐心和技术啦。
他们得像摆弄艺术品一样,让每个中分段都完美地组合在一起。
船舶分段建造作业指导书

船舶分段建造作业指导书批准: 编制:审核: 修订内容摘要系统文件新制定修订 日期修订 单号批准修订 版次 页次 审核分段建造作业指导书1、目的本指导书阐述了分段建造程序及分段精度的控制方法,旨在保证船舶分段质量满足船东及船级社的要求。
2、合用范围合用于本公司船舶分段建造全过程。
3、职责3.1 船研所负责提供分段施工图、施工要领、建造规范以及建造精度标准,并及时对图纸上存在的错误、遗漏等问题进行修正。
3.2 公司总调室负责总体生产计划的下达。
3.3 钢结构创造部负责分段建造详细计划的编制。
3.4 工程管理科负责分段作业计划的安排、产品质量的控制以及生产过程中的调度和协调;同时负责对施工人员提出技术要求,并现场进行指导。
3.5 工程管理科负责分段建造细则工艺的编制。
3.6 安全管理科负责对生产过程中的安全进行监控。
3.7 检验科负责对分段创造过程中的精度、创造质量进行检查控制。
4、实施4.1 工程管理科在产品开工之前应先组织施工人员进行分段建造规范及有关节点图册的学习。
4.2 施工人员在接收到分段图纸后应先熟悉图纸,掌握施工要领以及施工工艺,以确保在施工过程中对图纸不存在含糊感觉。
4.3 工程管理科根据分段作业计划要求于分段开工前填写送料申请单交准备工区,工程管理科材料接收人在准备工区送料结束核对齐全后,在送料通知单存根联上签字,交准备工区留存备查。
4.4 部件预制4.4.1 施工过程中应按照图纸核对零件号安装,并且检查此代号是否符合图纸上规定的尺寸要求。
4.4.2 施工过程中应检查零、部件的材质是否符合图纸要求。
4.4.3 施工过程中要按照装配节点图册及焊接规格表进行施工。
4.4.4 板列预装及“T”型材预装a. 板列预装前应先检查零件上的数控粉线是否准确或者重新划出结构安装线,标出理论线位置及折边方向,然后再安装其上面的结构。
b.“T”型直梁采用倒装法,要先在面板上划出腹板安装线再安装腹板,“T”型弯梁采用侧装法安装,装配完工后在腹板上划出辅助检验线,以检验“T”型材经焊接后的型线是否准确,并作为火工矫正线型的依据。
- 1、下载文档前请自行甄别文档内容的完整性,平台不提供额外的编辑、内容补充、找答案等附加服务。
- 2、"仅部分预览"的文档,不可在线预览部分如存在完整性等问题,可反馈申请退款(可完整预览的文档不适用该条件!)。
- 3、如文档侵犯您的权益,请联系客服反馈,我们会尽快为您处理(人工客服工作时间:9:00-18:30)。
船体曲面分段装配中心(流水线)研究
1.装配中心(流水线)总布置方案图
2.装配中心(流水线)主要技术参数(参考附件1:平面分段主要
参数设置)
3.船体曲面分段装配中心(流水线)装配工艺流程图(参考附件1:
平面分段主要参数设置),各工序技术特点说明,物流方式。
4.主要设备清单
5.各工序的微流程(PPR)撰写视频脚本
6.
附件1:平面分段主要参数确定参考
1.主要参数
1.2 STIFFENER SPACING/纵骨间距
For fillet welding of stiffeners the following table describes the max. and min. distances between stiffeners.
下面表格是描述了角焊时纵骨(加强材)最大及最小值间距。
列出的最大最小的焊接间距为两个对焊枪间的距离。
Stiffener type 纵骨类型Stiffener dim.(Height/width)
纵骨尺寸(高度/宽度)
Stiffener min.
Spacing
纵骨间距最小值
Max. Stiffener
spacing
焊接间距最大值
Bulb
球扁钢
All types 600 mm 950mm
T-pro型材
到850/150
到850/300mm
600 mm
750mm
950mm
L-profile 角钢到600/150mm
到600/200mm
600 mm
700mm
950mm
For T-profiles and L profiles: 150mm flange width is maximum for the minimum stiffener spacing 600.
对于T型材及角钢来说,最大盖板宽度150mm的型材,最小的纵骨间距600。
For T-profiles: 300mm flange width the minimum stiffener spacing is 750mm. 对T型材来讲:300mm盖板宽度型材,最小纵骨间距为750mm.
For L profiles: 200mm flange width the minimum stiffener spacing is 700mm. If, in some cases, 2 L-profiles are mounted with flanges towards each other, then spacing must be increased accordingly.
对角钢来讲,200mm宽度盖板的型材,最小间距为700mm.如果某些情况下,两角钢盖板相对安装,间距须相应增加。
For bulb profiles max and min. size can be welded with 600 mm spacing.
球扁钢最大最小尺寸都可以按照600mm间距焊接。
Max –and min. welding spacing are the distance between 2 opposite welding torches./最大最小焊接间距为两相对焊头之间距离。
Stiffener type/
纵骨型材类型
Stiffener dim.
(Height/width)/
纵骨型材尺寸
(高度/宽度)
Min. stiffener
welding spacing/
最小纵骨焊接间距
Max. stiffener
welding spacing/
最大纵骨焊接间距Bulb/球扁钢All types 1200 mm 1900 mm
T-profile/T型材
Up to/
最大
Up to/
最大
850/150 mm
850/300 mm
1200 mm
1500 mm
1900 mm
L-profile/角钢
Up to /
最大
Up to/
最大
600/150 mm
600/200 mm
1200 mm
1400 mm
1900 mm
附件2 曲面分段生产流程图。