塑料模具装配技术要求
模具的装配技术
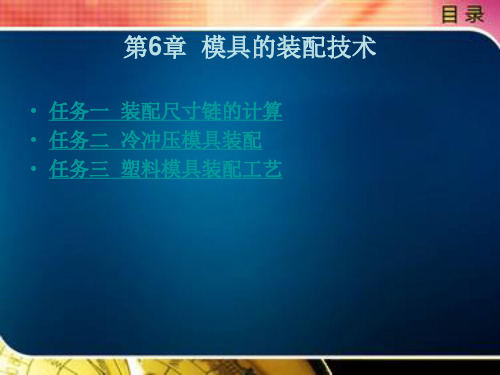
下一页 返回
任务二 冷冲压模具装配
一、冷冲压模具装配的技术要求 1.模具的总体装配精度
(1)装配前要检查模具各零件的材料、儿何形状、尺寸精度、表面粗糙 度和热处理硬度等是否符合图样要求。各零件的工作表面是否有裂纹 和机械损伤等缺陷,有则视为不合格件。 (2)装配完成后,模具各零件间的相对位置精度必须保证。尤其是一种 冲压件需要儿套冲模才能得到,冲模制造要保持一定的连续性,这时 冲压件的有些尺寸与儿套冲模零件尺寸有关,需特别注意。 (3)所有存在相对运动的模具零件,应保证位置准确、配合间隙合理、 运动平稳。 (4)模具的螺钉、销钉等紧固零件,要牢固可靠,不应出现松动和脱落。 (5)模架的公差等级满足冲压件所需的精度要求。
上一页 下一页 返回
任务三 塑料模具装配工艺
6.滑块抽芯机构及抖导柱的装配 滑块抽芯机构装配后,应保证型芯与凹模达到所要求的配合间隙,
滑块运动灵活,有足够的行程,有正确的起止位置。滑块装配常常要 以凹模的型面为基准,因此,它的装配要在凹模装配后进行。
上一页 下一页 返回
任务三 塑料模具装配工艺
三、塑料注射模具总装配 1.总装配技术要求
上一页 下一页 返回
任务二 冷冲压模具装配
二、冷冲压模具模架的压入法装配 1.模架装配的技术要求
(1)装配成套的模架,上模座上平面对下模板下平面的平行度、导柱中 心线对下模板下平面的垂直度、导套孔的中心线对上模座上平面的垂 度应符合相应公差等级的要求。 (2)组成模架的各零件应符合相应的技术标准和技术文件。 (3)压人上、下模的导套、导柱,压人后应牢固、不可松动,离安装表 面应有1~2 mm的距离。 (4)装配成套的模架,各零件的工作表面不应有碰伤、裂纹及其他机械 损伤。 2.模架的装配工艺
塑胶模具的制作规范
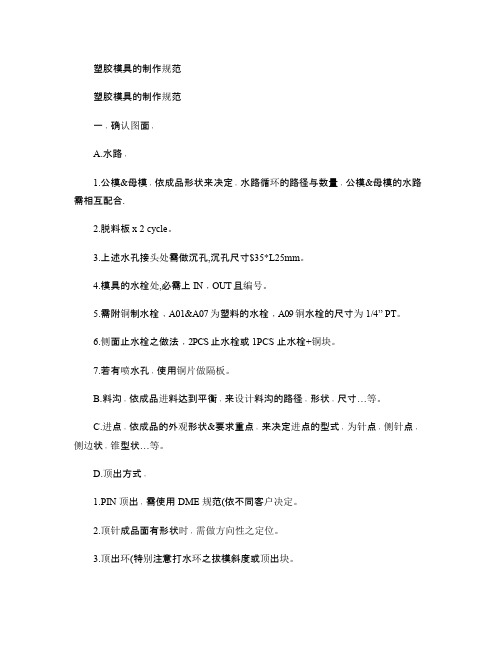
塑胶模具的制作规范塑胶模具的制作规范一﹐确认图面﹐A.水路﹐1.公模&母模﹐依成品形状来决定﹐水路循环的路径与数量﹐公模&母模的水路需相互配合.2.脱料板x2cycle。
3.上述水孔接头处需做沉孔,沉孔尺寸$35*L25mm。
4.模具的水栓处,必需上IN﹐OUT且编号。
5.需附铜制水栓﹐A01&A07为塑料的水栓﹐A09铜水栓的尺寸为1/4”PT。
6.侧面止水栓之做法﹐2PCS止水栓或1PCS止水栓+铜块。
7.若有喷水孔﹐使用铜片做隔板。
B.料沟﹐依成品进料达到平衡﹐来设计料沟的路径﹐形状﹐尺寸…等。
C.进点﹐依成品的外观形状&要求重点﹐来决定进点的型式﹐为针点﹐侧针点﹐侧边状﹐锥型状…等。
D.顶出方式﹐1.PIN顶出﹐需使用DME规范(依不同客户决定。
2.顶针成品面有形状时﹐需做方向性之定位。
3.顶出环(特别注意打水环之拔模斜度或顶出块。
E.定位块X4﹐于公母模板360度/4﹐加长方型之定位块﹐增加基准面之精度(材质:SKD-61中国塑料模具网F.模仁方式﹐1.锁公母模仁之螺丝﹐设计时愈多愈好﹐且需平均分配﹐使模仁与模座接触面更密合﹐锁螺丝时需封称锁入﹐且扭力一致。
2.公母模仁均须有卡入模座之定位梢。
3.所有insert之模仁形状为圆形时需做定位﹐且只能单方向组装﹐避免组装时方向错误。
G.4支导柱需有1pcs做偏心﹐X﹐Y轴各偏10mm。
H.模具的螺丝孔及螺丝﹐须为DME的公制规范。
I.回位销封边要有耐顶板﹐材质为TDAC+氮化处理。
J.若有斜销及滑块﹐三面需加耐磨板﹐且必须有油槽(材质﹐TDAC+氮化处理。
K,需安装计数器﹐INSERT的型式(A09客户才需要。
L.模具的长﹐宽﹐高﹐定位环与KO孔﹐需配合客户的机台尺寸。
M.若为三板模﹐A09为外部开闭器﹐A为内部开闭器。
N,CHECK母模与脱料板间﹐分开的距离是否足够﹐机械手取出料头﹐考虑LGP 的长度&机台的最大行程。
模具技术标准

版本:拨杆与拨左右单边0.1~0。
15 ±0。
05盘三:模具的总体要求参考模具协会的标准,本公司依照以下要求.大量生产模(250,000— 1,000,000模或以上),具体要求如下:1。
要有详细模具结构图。
2.精确的散件图.3. 用Mold—flow软件模拟模具注塑过程、注射分析、压力分布及温度分布,以确定最好的入水位置、流道尺寸、疏气位置等。
4。
模胚的A、B板及通腔背板均用28Hrc硬度的钢材;(内采用镶嵌模腔)。
5.上、下模及镶件使用硬度为48Hrc或以上的钢料,所有移动的零件应使用硬钢,而且必须有限位及定位锁.6.模具尽可能自动断水口.如可能,尽量使用潜水、细水口、香蕉型水口、并要考虑热流道的可行性。
7.模具设计应具备最大限度的冷却,上、下模肉高温度点应该个别地冷却.8.顶出方法应尽可能使流道与产品自动掉下,避免运用多次顶出方法。
9.模具应能够全自动生产,大的零件应能够轻松取出。
10.顶针板必须有导向柱,顶出限位,以及模具支撑柱。
11.安装浇口定位环应与塑机尺寸匹配12.非天侧处有油缸装置,必须有油缸立柱。
13.模具装配后的闭合高度以及安装部分的配合尺寸,顶出形式、开模距离等均符合客户使用的设备技术条件要求。
14.模具应具备所有的安全特性,以预防受到意外的损害及错误的安装。
15.上、下模需要精确的配合,有插穿位的地方,模具一定要有直身锁.16.需要高温及热流道的模具,必须有隔热板。
17.所有可替换的元件必须是标准件。
18.模具外表面无凹痕/切割片/凿子/磨头/锉刀等痕迹。
19.冷却水要在非操作侧进出,冷却、气动系统应标记进出口标志。
20.模具上的水、液、气、电路的进出口应采用封口措施防止异物进入。
塑料橡胶模具技术条件

塑料、橡胶模具技术条件(HB2198-89)1 主题内容与适用范围本标准规定了塑料、橡胶模具的零件加工和装配的技术要求以及模具的材料及材料代用、验收、包装、运输和保管的基本规定。
本标准适用于塑料、橡胶模具的设计、制造及验收。
2 引用标准GB4170 塑料注射模具零件技术条件GB8846 塑料成型模具术语及定义GB1801 公差与配合尺寸至500mm孔、轴公差带与配合GB1804 公差与配合未注公差尺寸的极限偏差GB1184 形状和位置公差未注公差的规定GB1239 普通圆柱螺旋弹簧GB196 普通螺纹基本尺寸HB0—84 热固性塑料模塑制品技术条件HB5888 航空辅机产品用字体和符号3 技术要求3.1 零件的加工要求3.1.1 要求镀铬的成型表面,应进行抛光、镀铬、抛光。
铬层厚度为0.005~0.01mm,铬层应均匀,不允许有积铬、腐蚀及剥落等缺陷。
3.1.2模具成型零件之间的配合,其同一配合部分各处应保持一致,如图A-1左图R与A、B一致;在未注公差处按已注明公差的配合要求,如图A-1右图R与A、B一致。
3.1.3 塑料及硬橡胶模具,成型表面未注明脱模斜度时,不允许有影响脱模的反斜度及其它缺陷。
3.1.4 模具分型面及组合件的结合面应很好贴合,局部间隙不大于0.02mm 。
3.1.5 模具成型表面的内外锐角、尖边,图样上未注明圆角时,允许有半径不大于0.3 mm 的圆角(分型面及结合面除外)。
当不允许有圆角时,应在图样上注明。
3.1.6 成型表面及构成成型表面的角度偏差,图样未注明时,其极限偏差按表A-1规定。
属配合角度时,需同时满足3.1.2条或3.1.4条规定(图A-2)。
表A-1 角度短边长度L(mm ) ≤10 >10~50 >50~120 >120~400 >400 角度值 ±45′ ±30′ ±15′ ±7′ ±5′ 极限 偏差线性值 (mm )±0.013L±0.013L±0.013L±0.013L±0.013L3.1.7 成型表面非转接半径R 的偏差,图样未注明时,其极限偏差按表A-2规定(图A-3、 图A-4)。
塑料模具设计与制作要求

塑料模具设计与制作要求1 范围本标准规定了本公司塑料模具的设计与制作要求。
本标准适用于本公司的塑料模具制作与验收。
2规范性引用标准下列文件中的条款通过本标准的引用而成为本标准的条款。
凡是注日期的引用文件,其随后所有的修改单(不包括勘误的内容)或修订版均不适用于本标准。
凡是不注日期的引用文件,其最新版本适用于本部分。
Q/MB05.003-2003 塑料模具设计制造规范3 技术要求3.1模具的设计要求3.1.1模具分类根据模架尺寸将模具分为大、中、小三类。
a)模架尺寸6060以上称为大型模具;b)模架尺寸3030~6060之间为中型模具;c)模架尺寸3030以下为小型模具。
3.1.2模架选用与设计的要求3.1.2.1优先选用标准模架,具体按《龙记标准模架》执行。
3.1.2.2若选用非标准模架,应优先选用标准板厚,具体参照《龙记标准模架》。
3.1.2.3大型非标模架,导柱直径不小于φ60mm,导套孔壁厚不得小于10mm,回针孔壁厚为 35~40mm,回针直径不小于φ30mm。
3.1.2.4大型非标模架A板、B板起吊螺丝孔为M36~M48。
3.1.2.5如有可能产生较大侧压力时(型腔深度超过50mm),非标大型模架应设计原身止口,以后模套住前模。
3.1.2.6模架3030以上就必须增加顶针板导柱2-4个。
3.1.2.7订购模架时必须注意方铁的高度。
3.1.3注塑参数校核方法3.1.3.1容模尺寸校核a)模具厚度+顶出距离+取出产品的距离<最大开模距离;b)模具厚度>注塑机模板最小闭合距离,而<注塑机模板最大闭合距离;c)码模板尺寸小于注塑机模板的最大装夹尺寸。
3.1.3.2锁模力:F≥P.A.S10-²其中F:注射机的公称锁模力(t);P:模内平均压力(25~40Mpa);A:投影面积(包括产品、流道)cm²。
3.1.4型腔排位要求3.1.4.1型腔排位有利于各腔同时、均匀进胶;3.1.4.2多腔模各腔间距不小于20mm,大产品深腔根据强度面增加,模腔与镶件边不得少于20~25mm,多胶模的同一个产品保证进胶位置一致。
第五章模具装配
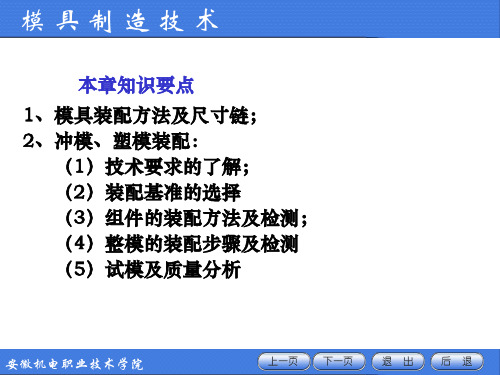
模具制造技术
第二节 装配尺寸链
一、装配尺寸链的概念
模具装配中,将与某项精度指标有关的各个零件尺寸 依次排列,形成一个封闭的链形尺寸组合,称为装配尺 寸链。其特征是封闭性
1.封闭环的确定 间接得到的尺寸称为封闭环,A0尺寸
2.组成环的查找 增环 、减环
3.快速➢确定增环和减环的方法
模具制造技术
4、滑块抽芯机构的装配
装配凹模(或型芯)、加工滑块槽
压印、钻型芯固定孔
装配滑块型芯
安徽机电职业技术学院
模具制造技术
滑块的复位、定位
用定位板作滑块复位时的定位 用滚珠作滑块复位时的定位
安徽机电职业技术学院
模具制造技术
5、锁紧位置的装配
模具闭合时,模紧块 斜面必须和滑块斜面均 匀接触,保证有足够的 锁紧力,闭合时分模面 之间应保留0.2mm 的间 隙 ,滑块斜面修磨
b=(a-0.2)*sinα
安徽机电职业技术学院
模具制造技术
6、斜导柱的装配
1、型芯装入型芯固定板为型芯组件。
2、安装导块,位轩确定后,用夹板将 其夹紧。
3、安装定模板锁楔。保证楔斜面与滑 块斜面有70%以上的面积密贴。闭模, 检查间隙x值是否合格。
4、镗导柱孔。将定模板、滑块和型芯 用夹板夹紧,在卧式镗床上镗斜导柱孔。
安徽机电职业技术学院
模具制造技术
3、推杆的装配
(1)将推板、推杆固定板、支承板 重叠,锥导柱、导套孔。 (2) 支承板与动模板(型腔、型芯) 重叠 , 配钻复位杆孔,配钻支承 板上的推杆孔 (3) 推杆装配装配: 1) 将推杆孔人口处和推杆顶端倒 出小圆角或斜度、不溢料。
2) 检查推杆尾部台肩厚度及推板固定板的沉孔深度, 保证装 配后有 0.05mm 的间隙、修磨。3) 将推杆及复位杆装入固定 板,盖上推板,用螺钉紧固。4) 检查及修磨推杆及复位杆顶 端面。 安徽机电职业技术学院
注塑模具装配工艺规范标准
注塑模具装配工艺规一、装配工艺概述注塑模具装配是注塑模具制造过程中重要的后工序,模具质量与模具装配紧密联系,模具零件通过铣、钻、磨、CNC、EDM、车等工序加工,经检验合格后,就集中装配工序上;装配质量的好坏直接影响到模具质量,是模具质量的决定因素之一;没有高质量的模具零件,就没有高质量的模具;只有高质量的模具零件和高质量的模具装配工艺技术,才有高质量的注塑模具。
注塑模具装配工艺技术控制点多,涉及围到方方面面,易出现的问题点也多,另外,模具周期和成本与模具装配工艺也紧密相关。
《注塑模具装配工艺规》针对在注塑模具装配工序上所可能发生的技术点作出规,注塑模具装配分为部装和总装,其工艺技术要求如下:1.装配好的模具其外形和安装尺寸应符合装配图纸所规定的要求。
2.定模座板上平面与动模座板下平面须平行,平行度≤0.02/300。
3.装配好的模具成型位置尺寸应符合装配图纸规定要求,动、定模中心重复度≤0.02mm。
4.装配好的模具成型形状尺寸应符合装配图纸规定要求,最大外形尺寸误差≤+0.05mm。
5.装配好的模各封胶面必须配合紧密,间隙小于该模具塑料材料溢边值50%,避免各封胶面漏胶产生披峰。
保证各封胶面有间隙排气,能保证排气顺畅。
6.装配好的模具各碰插穿面配合均匀到位,避免各碰插穿面烧伤或漏胶产生披峰。
7.注塑模具所有导柱、导套之间的滑动平稳顺畅,无歪斜和阻滞现象。
8.注塑模具所有滑块的滑动平稳顺畅,无歪斜和阻滞现象,复位、定位准确可靠,符合装配图纸所规定的要求。
9.注塑模具所有斜顶的导向、滑动平稳顺畅,无歪斜和阻滞现象,复位、定位准确。
10.模具浇注系统须保证浇注通道顺畅,所有拉料杆、限为杆运动平稳顺畅可靠,无歪斜和阻滞现象,限位行程准确,符合装配图纸所规定的要求。
11.注塑模具顶出系统所有复位杆、推杆、顶管、顶针运动平稳顺畅,无歪斜和阻滞现象,限位、复位可靠。
12.注塑模具冷却系统运水通道顺畅,各封水堵头封水严密,保证不漏水渗水。
塑料模具技术要求
塑料模具制造标准要求30条为提高模具品质档次,最大限度减少模具质量问题投诉,交给客户满意的模具,对模具制造常见问题进行总结、归纳,并建立标准,按要求执行。
1.小于2020的模胚,a、b板之间需要做撬模坑;大于2020的模胚所有模板包括顶针板间都要做撬模坑。
2.模胚导柱导套要加工排气槽,以防导柱导套拉伤。
3.模具上不得有尖角,需要倒角处理。
特别指明的地方除外。
4.内模和模具零件未经同意不得有烧焊。
5.模具产品的外围必须要在适当的位置开排气槽,排气槽规格请参考模具设计手册。
6.尽可能避免使用打磨机在模具上打磨,如果非要用打磨机加工,必须用油石省光(特别是分型面)7.内模胶位面的表面处理必须依照bom表,或者其它正式通知的技术要求执行。
非胶位面上的加工纹路(线切割,铣床,cnc锣床,火花机)也要用油石省亮。
8.所有内模材料,模胚等级要求必须依据订单,或者设计审核过程中正式确认的技术要求进行采购。
必须提供材质证明,如果是硬模,必须提供热处理报告。
所有相关证明。
9.所有模具的前后内模,镶件,行位,斜顶,直顶(推块),铲鸡等需要在底面或者侧面加工一个腰圆形的坑位,把材料名和硬度刻出来。
10.行位,推块,铲鸡,唧嘴等重要易磨损零件必须进行氮化加硬处理。
11.行位必须有定位。
定位方式有弹弓,波珠,hasco(dme)标准行位夹等等,具体需要按照各个项目的要求。
行位需要有压条,耐磨板。
压条,耐磨板必须使用耐磨硬料,需要加上油槽。
12.行位斜导柱必须压紧,不能转动和松动。
斜导柱尾部必须要加工成半球形或圆锥台形,有利于保证行位正常运动。
同一行位上有两支或者两支以上斜导柱的,斜导柱的长度、大小和倾斜度必须相同。
13.斜顶座位必须使用耐磨硬料。
斜顶必须加工油槽,斜顶座一般用2510或cr12加硬到hrc40-45度,因为斜顶座受到的是冲击负荷,所以不能太硬否则会断裂,并在所有的直角位置倒角c角。
需要有斜顶导向板(青铜)。
中国注塑模架标准最新规范
中国注塑模架标准最新规范一、概述注塑模具是塑料加工行业的关键组成部分,其标准化对于提高生产效率、降低成本、保证产品质量具有重要意义。
本规范旨在为模具设计、制造和使用提供统一的技术要求。
二、适用范围本规范适用于各类塑料注射成型模具的设计和制造,包括但不限于单色、双色、多色及特殊成型工艺的模具。
三、材料要求1. 模具材料应具有良好的硬度、耐磨性和抗腐蚀性,以适应不同的工作环境和成型要求。
2. 模具钢材应符合国家标准或行业标准,确保材料的一致性和可靠性。
四、设计要求1. 模具设计应考虑塑料流动性、冷却速度和收缩率等因素,确保成型件的尺寸精度和表面质量。
2. 模具结构应简洁合理,便于拆卸、清洗和维护。
五、制造工艺1. 模具制造应采用精密加工技术,确保模具的尺寸精度和表面光洁度。
2. 模具的关键部件应进行热处理,以提高其硬度和耐磨性。
六、装配与调试1. 模具装配应严格按照设计图纸进行,确保各部件的配合精度。
2. 模具调试应在实际生产条件下进行,以验证模具的成型能力和稳定性。
七、质量检验1. 模具在出厂前应进行全面的质量检验,包括尺寸精度、表面质量、材料性能等。
2. 检验结果应符合本规范的要求,并附有相应的检验报告。
八、维护与保养1. 模具在使用过程中应定期进行清洁和维护,以延长模具的使用寿命。
2. 发现模具有损坏或磨损时,应及时进行修复或更换。
九、安全与环保1. 模具设计和制造过程中应严格遵守国家安全生产法规,确保操作人员的安全。
2. 模具材料和制造过程中产生的废弃物应符合环保要求,进行妥善处理。
十、附录本规范附录包含模具设计和制造过程中常用的参考数据、计算公式和图例,供设计和制造人员参考。
以上规范为注塑模架设计和制造提供了一套完整的技术指导,有助于提升模具行业的整体水平和竞争力。
塑料模具的装配
第20页/共22页
第21页/共22页
感谢您的观看!
第22页/共22页
第14页/共22页
图7 推杆的装配 1-螺帽 2-复位杆 3-垫圈 4-导套 5-导 柱 5-推板 7-推杆固定板 8-推杆 9-支承
板 10-动模板 11-型腔镶块
第15页/共22页
3.推杆的装配与修磨 ①将推杆孔入口处和推杆顶端倒成小圆角或斜度。 ②修磨推杆尾部台肩厚度,使台肩厚度比推杆固定 板沉孔的深度小0.05mm左右。 ③装配推杆时将导套4的推杆固定板7套在导柱5上, 然后将推杆8复位杆2穿入推杆固定板、支承板和型腔 镶块推杆孔,而后盖上推板6,并用螺钉紧固。
图3 螺纹连接式固定型芯
第7页/共22页
对某些有方向要求的型芯,当螺纹拧紧后型芯的实际位 置与理想位置之间常常出现误差,如图4所示。
图4 型芯的位置误差
第8页/共22页
3.单件圆形整体型腔凹模的镶入法如图5所示。 这种型腔凹模镶入模板,关键是型腔形状和模板相对 位置的调整及其最终定位。调整的方法有以下几种: (1)部分压入后调整 型腔凹模压入模板极小一部 分时,用百分表校正其直边部分。当调至正确位置时, 再将型腔凹模全部压入模板。 (2)全部压入后调整 将型腔凹模全部压入模板以 后再调整其位置。用这种方法时不能采用过盈配合,一 般使其有0.01~0.02㎜的间隙。位置调整正确后,需用 定位件定位,防止其转动。
第17页/共22页
当推杆数量较多时,装配应注意两个问 题:一是应将推杆与推杆孔进行选配,防 止组装后,出现推杆动作不灵活、卡紧现 象。二是必须使各推杆端面与制件相吻合, 防止顶出点的偏斜,推力不均匀,使制件 模时变形。
- 1、下载文档前请自行甄别文档内容的完整性,平台不提供额外的编辑、内容补充、找答案等附加服务。
- 2、"仅部分预览"的文档,不可在线预览部分如存在完整性等问题,可反馈申请退款(可完整预览的文档不适用该条件!)。
- 3、如文档侵犯您的权益,请联系客服反馈,我们会尽快为您处理(人工客服工作时间:9:00-18:30)。
塑料模具装配技术要求(2009/11/23
17:22)
目录:公司动态
浏览字体:大中小
塑料模种类比较多,即使同一类模具,由于成形塑料种类不同,开头和精度要求不同,装配方法也不尽相同.因此在组装前应仔细研究分析总装图.零件图,了解各零件的作用,特点及其技术要求,确定装配基准.通过装配,最后全面达到产品的各项质量指标,模具动作精度和使用过程中的各项技术要求.
1. 装配基准装配基准可大致分为:
(1)以塑料模中的主要工作零件如型芯,型腔和镶快等作为装配的基准件,模具的其它零件都有装配基准件进行配制和装配。
(2)以导柱导套或模具的模板侧基面为装配基准面进行修整和装配.
2. 模具装配精度
模具装配精度包括:(1)各零,部件的相互间精度,如距离尺寸精度,同轴度,平等度,垂直度等.(2)相对运动精度,如传动精度直线运动和回转运动精度等.(3)配合精度和接触精度,如配合间隙,过盈量接触状况等.(4)塑料成形件的壁厚大小.新制模具时,成形件壁厚应偏于尺寸的下限.
3. 修配原则
(1)修配脱模斜度,原则上型腔应保证大端尺寸在制件尺寸公差范围内,型芯应保证小端尺寸在制件尺寸公差范围内.(2)角隅处圆角半径,型腔应偏小,型芯应偏大(3)当模具既有水平分型面又有垂直分型面时修正时应使垂真分型面接触时水平分型面稍稍留有间隙。
小型模具只需涂上红后相互接触即可,大型模具间隙约为0.02mm左右.(4)对于用斜面合模的模具,斜面密合后,分型面处应留有
0.02-0.03mm的间隙.(5)修配表面的圆弧与直线连接要平滑,表面不允许有凹痕,锉削纹路应与开模方向一致.。