注塑件过程失效模式及分析PFMEA
pfmea过程潜在失效模式及后果分析案例(从原材料-加工-出货整套案例分析)

1、注射压力大 2、锁模力不够 3.模具分型面有异物
4 调节注射压力 作业准备验证,适当调
整,并进行工艺监控 清理模具分型面
产品不合格
2
C 4.塑料温度太高
调节 56
5
制品质量符合 要求
气泡
1.原料含水分、溶剂或 易挥发物
3
原料检验
2.塑料温度太高或受热 时间长,易降聚或分解
标签贴错 漏检 纸箱受潮变形 数量不准确
产品型号错
误,顾客不满 2
意
不良品混入, 影响客户使用
5
纸箱变形破损 3
顾客不满意
1
C 包装人员粗心 C 检验人员操作失误 C 纸箱堆积太高 C 仓库计数错误
3 检查、更正 3 检验、及时标记 3 检查、更正 3 检查、更正
2 42
1 21
3 18 4 60 3 27 26
3.注射压力太小
调节注射压力
4.注射柱塞退回太早 产品不合格 7 A
5.模具温度太低
调节注射温度
6.注射速度快
调节注射速度
2 42
7.在料筒加料端混入空 气
6
制品质量符合 要求
凹痕、缩水
产品不合格 7
1、流道浇口太小
4
2、塑料件太厚或厚薄 不均
3、浇口位置不当
4、注射保压时间太短 A 5、加料量不夠
过程潜在失效模式及后果分析 (PFMEA)
类型/部件: 车型年:
核心小组:
设计责任: 关键日期:
RPN DETECT
OCCUR CLASS SEV
项目
设计功能/要 求
潜在失效模式
潜在失效后果
1 原材料采购 原材料不合格
注塑过程PFMEA失效模式及后果分析
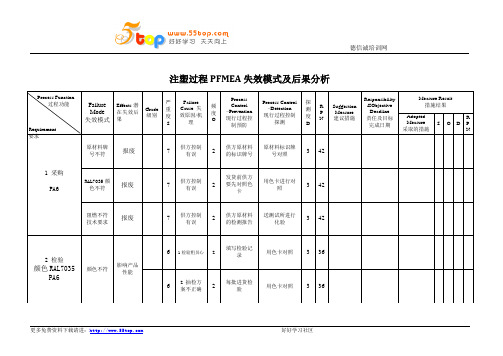
德信诚培训网更多免费资料下载请进: 好好学习社区注塑过程PFMEA 失效模式及后果分析Failure Mode 失效模式 Effects 潜在失效后果Grade 级别严重度SFailure Cause 失效原因/机理频度OProcess Control –Prevention 现行过程控制预防Process Control –Detection 现行过程控制探测探测度DR P N Suggestion Measure 建议措施Responsibility &Objective Deadline 责任及目标 完成日期Measure Result 措施结果Adopted Measure 采取的措施S O D RPN1 采购PA6原材料牌号不符报废 7供方控制有误2供方原材料的标识牌号 原材料标识牌号对照3 42RAL7035颜色不符报废 7供方控制有误2发货前供方要先对照色卡用色卡进行对照3 42阻燃不符技术要求报废 7供方控制有误2供方原材料的检测报告 送测试所进行化验3 422 检验颜色RAL7035PA6颜色不符影响产品性能61检验粗员心 2填写检验记录用色卡对照 3 3662 抽检方案不正确2每批进货检验用色卡对照 3 36Process Function过程功能Requirement 要求。
注塑件过程失效模式及后果分析表模板(PFMEA)

6
包装破损
零件污染,客户投 诉
5
产品碰伤砸伤 客户投诉
6
装箱时确认不足 货物堆积过高
搬运不规范
2
无
3
试验后制定合理堆 积标准
2
无
100目测 100目测 100目测
5 60 5 75 4 48
标签贴错 发错货,客户投诉 5
标签与实物未核对 2
无
100目测
4 40
产品数量不正确
客户投诉
6
80-出货检验
关键尺寸超差
第 1 页,共 2 页
注塑件过程失效模式及后果分析表模板(PFMEA)
零件号
设计责任部门
FMEA 编号
零件名称
关键日期
编制人
车型/年份
系统/子系统/部件
编制日期
核心小组
序号
过程
潜在的失效模式
严 潜在的失效后果 重
度
级 别
潜在的失效原因/机理
频 度 数
现行预防性设计控 制
现行探测性设计控 制
探 测 度
5 60 5 75
建议措施
责任人和目标 完成日期
无
采取的措施
严频探 R 重度测 P 度数度 N
无
无
无
无
不同产品分区放置, 并做好标识
6
2 5 60
无
对纸箱进行固定 6 2 5 60
无
无
无
无
无
不同产品分区放置, 并做好标识
6
2 5 60
无
对纸箱进行固定 6 2 5 60
无
40-原材料烘料
烘料时间不对 烘料温度不对
表面料花 色差
pfmea过程失效模式与后果分析报告

通过深入分析,我们确定了导致这些失效的潜在原因,包 括设备老化、操作规程不完善、员工培训不足、原材料质 量控制不严格以及工艺参数设置不合理等。
对未来工作的建议和展望
改进措施建议
持续改进计划
未来研究方向
基于PFMEA的结果,我们提出了一系 列改进措施,包括更新设备、优化操 作规程、加强员工培训、严格控制原 材料质量以及调整工艺参数等。这些 措施旨在减少失效发生的风险,提高 生产过程的可靠性和稳定性。
为了确保改进措施的有效实施,我们 制定了持续改进计划。该计划包括定 期评估改进效果、监测潜在问题的出 现以及调整改进措施等。通过持续改 进,我们期望能够不断优化生产过程 ,提高产品质量和客户满意度。
在报告的最后,我们提出了一些未来 可能的研究方向。这些方向包括进一 步探索失效模式与潜在原因之间的关 系、研究新的失效分析方法以及开发 更加智能化的失效预测模型等。通过 深入研究,我们期望能够为企业的持 续改进提供更有力的支持。
失效模式
汽车发动机性能下降
后果
影响汽车动力性能,可能导致油耗增加、排放超标
潜在原因
制造过程中材料、工艺、设备等方面的问题
风险评估
高风险,需采取措施进行改进
案例二:电子产品制造过程的PFMEA分析
失效模式
电子元件短路
潜在原因
制造过程中元件组装、焊 接等环节出现问题
后果
产品功能失效,可能引发 安全事故
提前发现和预防问
题
PFMEA是一种预防性的质量工具 ,它通过提前发现和预防潜在的 问题,减少后期修改和返工的成 本。
优化设计和过程
PFMEA分析结果可以为设计和过 程的改进提供指导,帮助企业优 化产品和过程的性能、可靠性和 安全性。
印刷注塑PFMEA失效模式分析范例

机种名称: FMEA日期: 制 定:
修 订: 审 核:
严
频
制程功能 潜在失效模式 潜在失效效应
重 度
潜在失效起因
发 度
(S)
(O)
现行控制方式
生产日期:
核 准:
探 测 度
风 险 序 数
(D) RPN
建议改善方案及优先级
编
号:
版
本: A0
第1页 共1页
措施结果
执行单位 责任人
实际改善措施
3
75
车间领班、品管参与监督:要求 干燥时间≥4小时
邹勇
加料员与领班、品管共同 确认:干燥时间应为4H以 5 上
3
3 45
正常生产每3万模次进行保养一
正常生产每3万模次进行
3 72 次;隔数日再生产之前,进行需 邹勇 保养一次;隔数日再生产 4 3 3 36
检修保养
之前,需进行检修保养
注塑
产品缺料/尺 与相关件配合不到 寸偏差/变形 位/不能装配
识 ②印刷面首件确认,每2
6
2
3 36
目
小时核对一次
转序
防护不当
划伤/折伤
4
物料转序防护不到位,作业 员操作不当
5
①用物料车整卷进行周转 ②各管理人员不定时监督稽查
①导入使用吸塑盘转序 4 80 ②对作业员转序作业规范进行培 曾金镇 使用吸塑盘进行周转
训及宣导
4 3 3 36
印刷
印刷颜色差异
与样件不一致,导 致不良报废
4
72
①成型模做方向标识防呆 ②SOP上突出此漏失
梁德刚
①成型模做防呆方向标识 ②SOP已突出此漏失
注塑PFMEA范本
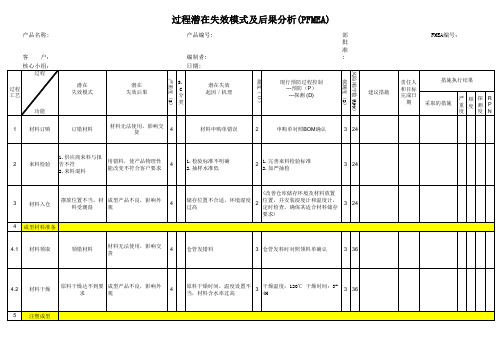
1.制作参数参 照表;提高调 机员的技术水
平 2.经常性清洗 及更换模具配
件
7
2
3 42
5.3 首件确认
外观不良 产品尺寸超差
客户投诉,退货
4
客户投诉,退货
5
2
2 16
未按成型工艺参数表设定
按成型工艺参数表重新设定参数
2
3 30
产品名称:
客 户: 核心小组:
过程 过程 工艺
功能
6 生产自检
潜在 失效模式
类
现行预防过程控制 ---预防(P) ---探测 (D)
过程责任部门:注塑 部 批 准 :
FMEA编号:
建议措施
责任人 和目标 完成日
期
措施执行结果
采取的措施
严频探 R 重度测 P 度 度N
客户投诉,退货
4
产品包装不合理
3
检讨包装书,并修正
3 36
产品名称:
客 户: 核心小组:
过程 过程 工艺
功能
1 材料订购
潜在 失效模式
订错材料
风险顺序数(RPN) 探测度(D)
频度(O)
严重度(S)
过程潜在失效模式及后果分析(PFMEA)
产品编号:
潜在 失效后果
编制者: 日期:
S. C 分
潜在失效 起因/机理
类
现行预防过程控制 ---预防(P) ---探测 (D)
3.锁模力不够,料温过高, 注射压力过大,保压时间过
长,保压压力过大 4.模温过低,注射速度过 3
快,注射压力过大 5.注射速度过快,注射压力
过大 6.保压时间不合理,注射压
力不合理(第二段) 7.原材料中含有一定阻燃
塑料注塑成型PFMEA分析

等)N
度度度
射出机料管4定期清理料管模具日常保1次/30分464机台尽可能固定颜色生管/注塑
有黑斑养生产
缩水4保压过小2依照标准成型成型条件每批216
条件表点检表
8保压过小2依照标准成型成型条件每批232
条件表点检表
胶芯穿孔4模具灌点2零件寿命管制成型条件每批216
过大点检表
8模具灌点2零件寿命管制成型条件每批232
过大点检表
■
包装
混料6
未按照标准
作
2
依照制造通知
单填写
224标签贴错6
未按照标准
作业
2
依照制造通知
单填写
224功能丧失
无法组装
无法组装
外观不良
功能丧失
外观不良。
吹塑、注塑产品pfmea报告
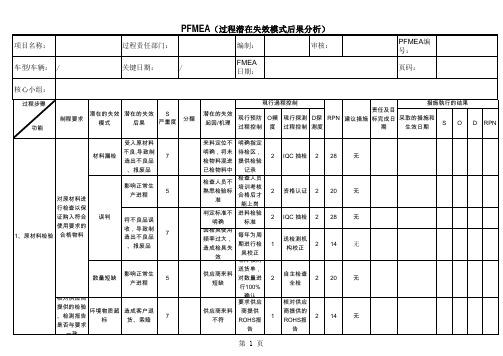
7
2
3 42
依据产品
料胚厚度不 足
标准书要 求,通过 吹塑机台
3
首检/自检 2
/巡检
42
无
厚薄控制
型胚气压过 大导致边料
过多
操作员根 据气压状 况适时调
整
3
自检
2 42
无
第3页
PFMEA(过程潜在失效模式后果分析)
项目名称:
过程责任部门:
用吹塑机通
车型/车辆: /过温度/时
间/空气压
3、产品成型 力把塑胶原
核心小组: 料吹胀成符
合规定尺寸
过程步骤
的制品
关键日期:
/
功能
潜在的失效 潜在的失效 S
制程要求
模式
后果
严重度 分類
编制:
FMEA 日期:
审核:
PFMEA编 号:
页码:
現行過程控制
措施執行的结果
责任及目
潜在的失效
现行预防 O頻 現行探测 D探 RPN 建议措施 标完成日 采取的措施和
、检测报告
7
标
货、索赔
是否与要求
一致
来料定位不 明确指定
明确,将未 待检区,
2 IQC 抽检 2 28
无
检物料混进 提供检验
已检物料中 记录
检查人员
检查人员不
培训考核
熟悉检验标
2 资格认证 2 20
无
合格后才
准
能上岗
判定标准不 进料检验
2 IQC 抽检 2 28
无
明确
标准
因检具使用
每年为周
频率过大,
17
比对色板验 收,保留色板
- 1、下载文档前请自行甄别文档内容的完整性,平台不提供额外的编辑、内容补充、找答案等附加服务。
- 2、"仅部分预览"的文档,不可在线预览部分如存在完整性等问题,可反馈申请退款(可完整预览的文档不适用该条件!)。
- 3、如文档侵犯您的权益,请联系客服反馈,我们会尽快为您处理(人工客服工作时间:9:00-18:30)。
产品报废 5
材料存放标识丢失
4
分区存放
20
___
___
___
_
_
_
_
材料失效 产品质量下降: ●表面油漆附着 力下降,漆面经 注塑成型 过长时间后脱 落,使顾客对外 产品表面无不 产品表面银丝 观不满意 良缺陷,注塑 尺寸精确 ●涂装后产品表 面容易产生裂 纹,外观质量使 顾客不满意 5
遗漏使用
5
先进先出
48
___
___
___
_
_
_
_
6
产品无内包装
3
作业指导书规 操作工自检,检 2 定 验员巡检 库房管理制度 库管员每天检查 2 规定 一次
36
___
___
___
_
_
_
_
半成品入库贮 存 打孔 孔位准确到位
产品变形
产品性能下降, 6 顾客不满意 产品装配不良, 5 使顾客不满意
堆放层数过高
3
36
___
45
___
___
___
_
_
_
_
潜在失效模式及影响分析
(过程FMEA)
项目名称:侧围 车辆年/车辆类型: 核心小组: 过程 功能 要求 严 频 重 级 潜在失效起因/机理 度 度 别 O S 仓库设施不好 材料受潮 产品表面出现银 5 丝产品质量下降 空气中湿度过高 仓库存贮 仓库环境良 好,摆放整 齐,记录完整 6 加强防护 5 现行过程控制 预防(P) 探测(D) 探 测 度 D R P N 过程责任部门: 生产科 关键日期: FMEA编号: 页码:第 页 共5页 编制者: FMEA日期(编制): 责任及 目标 完成日期 措施所产生的后果 采取的措施 S O D R P N _
(过程FMEA)
项目名称:侧围 车辆年/车辆类型: 核心小组: 过程 功能 要求 严 频 重 级 潜在失效起因/机理 度 度 别 O S 现行过程控制 预防(P) 探测(D) 探 测 度 D R P N 过程责任部门: 生产科 关键日期: FMEA编号: 页码:第 页 共5页 编制者: FMEA日期(编制): 责任及 目标 完成日期 措施所产生的后果 采取的措施 工艺监控: 1/2小时 巡检、全检 S O D R P N 48
6
2
4
注塑成型
产品表面粗糙
模具定期维 生产科 模具1万模左 修保养 2003.8.25 右保养1次
6
2
3
36
产品表面无不 良缺陷,注塑 与相关零件不匹 产品尺寸偏大 尺寸精确 配,使顾客不满 6 或偏小 意 外观质量下降, 使顾客对外观不 4 满意 6
压力表失准 ▲ 材料熔融指数 偏大 纸箱偏大或偏小
50
___
___
___
_
_
_
_
时间计电器失准,导 计电器定期校 操作工自检,检 3 3 致材料干燥时间不够 准 验员首检、巡检
45
___
___
___
_
_
_
_
5
温度表失准,导致干 温度表进行定 操作工自检,检 4 2 燥温度过高或过低 期校准 验员首检、巡检
40
___
___
___
_
_
_
_
潜在失效模式及影响分析
潜在 失效模式
潜在 失效后果
建议的措施
产品表面缩痕
外观质量下降, 使顾客对外观不 6 满意
工艺监控: 仪表失准: 仪表定期校准 操作工自检,检 1/2小时 生产科 注塑压力、时间、温 5 工艺监控: 4 120 验员首检、巡检 巡检、操作 2003.8.25 度设定不当 1次/2h 工全检 ▲ 模具型腔划伤 5 模具定期维修 操作工自检,检 3 保养 验员首检、巡检 90
潜在 失效模式
潜在 失效后果
建议的措施
提供资源
库管员每天检查 2 一次 库管员每天检查 2 一次 库管员每天检查 2 一次 库管员每天检查 1 一次 库管员每天检查 2 一次
50
___
___
___
_
_
_
60
___
___
___
_
_
_
_
杂质混入
5
环境不干净
4 定期卫生检查
40
___
___
___
_
_
_
_
材料错用
___ 生产科 2003.8.25Leabharlann _____
_
_
孔位偏移
夹具松动
5 定期校准夹具
操作工自检,检 5 125 验员首检、巡检
定期校准
1年校准1次
5
2
5
50
潜在失效模式及影响分析
(过程FMEA)
项目名称:侧围 车辆年/车辆类型: 核心小组: 过程 功能 要求 打孔 孔位准确到位 严 频 重 级 潜在失效起因/机理 度 度 别 O S 电钻迟钝 现行过程控制 预防(P) 探测(D) 探 测 度 D R P N 过程责任部门: 生产科 关键日期: FMEA编号: 页码:第 页 共5页 编制者: FMEA日期(编制): 责任及 目标 完成日期 措施所产生的后果 采取的措施 S O D R P N _
潜在失效模式及影响分析
(过程FMEA)
项目名称:侧围 车辆年/车辆类型: 核心小组: 过程 功能 要求 严 频 重 级 潜在失效起因/机理 度 度 别 O S 现行过程控制 预防(P) 探测(D) 探 测 度 D R P N 过程责任部门: 生产科 关键日期: FMEA编号: 页码:第 页 共5页 编制者: FMEA日期(编制): 责任及 目标 完成日期 措施所产生的后果 采取的措施 S O D R P N _
潜在 失效模式
潜在 失效后果
建议的措施
产品质量下降 熔融指数偏大 大:产品飞边 或偏小 小:产品缺料 拉伸强度未达 到标准要求 断裂伸长度率 偏大或偏小 Izod缺口冲击 原材料/外协 未达到要求 件检验 材质性能良 洛氏硬度偏大 好,符合规定 或偏小 要求,外观良 好 弯曲强度偏大 或偏小 弯曲弹性模量 未达到要求 热变形温度偏 高或偏低 原材料错判 产品质量下降
检验员首检、末 压力表定期校 检,对产品关键 3 准 装配尺寸进行检 查 5
3
54
___
___
___
_
_
_
_
产品飞边
原材料进货检 操作工自检,检 2 验 验员首检、巡检 操作工自检,检 2 验员巡检
40
___
___
___
_
_
_
_
包装
产品性能、外观 产品变形、表 质量下降,顾客 面擦毛 不满意
4 纸箱进货检验
3
42
___
___
___
_
_
_
▲ 原材料错判 产品质量下降 顾客不满意 7
检测设备仪表失准; 操作工全检、检 2 定期检定设备 设备未检定 验员首检、巡检 5 70 进行测量系 质量科 测量系统系统 7 统分析 2003.8.20 分析 1 5 35
漏检
5
检验员粗心
3 凭抽检单入库 检验员互相监督 3
潜在 失效模式
潜在 失效后果
建议的措施