使用UG进行塑料模具设计
ug注塑模具设计实例

ug注塑模具设计实例以下是一个简单的注塑模具设计实例,模具设计的基本概念和步骤。
设计案例:一个简单的塑料瓶盖模具1. 确定产品尺寸和形状产品是一个简单的塑料瓶盖,直径为20mm,高度为3mm。
瓶盖表面有纹理,以增加摩擦力,方便开启。
2. 确定模具结构模具采用典型的双板模结构,由动模板和定模板组成。
动模板上设有型腔,定模板上设有浇口和流道。
3. 确定型腔布局由于瓶盖尺寸较小,可以采用一模一腔的布局。
型腔布置在动模板上,浇口和流道布置在定模板上。
4. 设计浇口和流道浇口和流道的设计需要考虑塑料的填充和流动。
本例中,采用点浇口,浇口直径为1mm,流道直径为4mm。
5. 设计推出机构推出机构用于将成型后的产品从模具中推出。
本例中,采用推杆推出,推杆直径为8mm,数量为4个。
推杆安装在动模板上,推出时推动瓶盖脱离型腔。
6. 设计冷却系统冷却系统用于将成型过程中的热量从模具中带走,防止产品变形和开裂。
本例中,采用水管冷却,水管直径为4mm,布置在动模板和定模板上。
7. 设计排气系统排气系统用于将成型过程中的气体从模具中排出,防止气体的积聚和压力的升高。
本例中,采用排气槽,排气槽直径为2mm,数量为4个。
排气槽布置在定模板上。
8. 设计模具零件加工工艺性模具零件的加工需要考虑其工艺性。
本例中,采用数控加工中心进行加工,材料选择不锈钢。
9. 设计模具装配工艺性模具装配需要考虑其工艺性。
本例中,采用螺钉连接动模板和定模板,并使用定位销进行定位。
以上是一个简单的注塑模具设计实例,希望能帮助您更好地理解模具设计的基本概念和步骤。
ug注塑模具设计实例
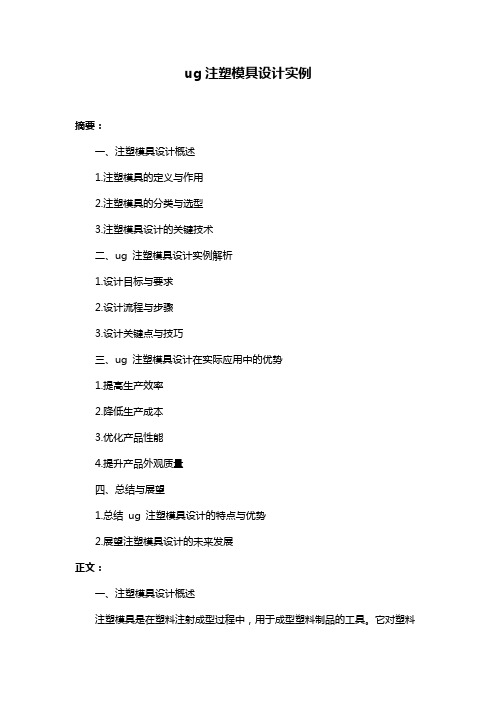
ug注塑模具设计实例摘要:一、注塑模具设计概述1.注塑模具的定义与作用2.注塑模具的分类与选型3.注塑模具设计的关键技术二、ug 注塑模具设计实例解析1.设计目标与要求2.设计流程与步骤3.设计关键点与技巧三、ug 注塑模具设计在实际应用中的优势1.提高生产效率2.降低生产成本3.优化产品性能4.提升产品外观质量四、总结与展望1.总结ug 注塑模具设计的特点与优势2.展望注塑模具设计的未来发展正文:一、注塑模具设计概述注塑模具是在塑料注射成型过程中,用于成型塑料制品的工具。
它对塑料进行准确塑形,保证制品的尺寸、形状、表面质量和物理性能。
注塑模具的设计是注塑成型工艺的关键环节,决定着产品的质量、成本和生产效率。
注塑模具主要分为热流道注塑模具、冷流道注塑模具和双色注塑模具等。
选型时需要根据产品的特点、生产批量和成本要求进行综合考虑。
注塑模具设计的关键技术包括:浇注系统设计、冷却系统设计、脱模机构设计、模具材料选择等。
这些技术影响着模具的性能、使用寿命和生产成本。
二、ug 注塑模具设计实例解析1.设计目标与要求本次设计的目标是制作一个高质量的注塑模具,用于生产一款手机壳。
要求模具具有良好的脱模性能、较长的使用寿命和较低的生产成本。
2.设计流程与步骤设计流程主要包括:分析产品结构、设计模具结构、分型面设计、浇注系统设计、冷却系统设计、脱模机构设计、模具材料选择、模具组装和出图。
3.设计关键点与技巧(1)分析产品结构:了解产品的形状、尺寸、材料和工艺要求,为模具设计提供依据。
(2)设计模具结构:根据产品特点,选择合适的模具类型,如热流道注塑模具。
(3)分型面设计:合理设置分型面,保证制品的质量和成型过程的顺利进行。
(4)浇注系统设计:设计合理的浇注系统,确保塑料充满模具,同时避免产生缺陷。
(5)冷却系统设计:设计高效的冷却系统,保证模具的快速冷却,提高生产效率。
(6)脱模机构设计:设计易于操作、安全的脱模机构,降低生产成本。
基于UG的注塑模具设计分模方法

定 的瞎 面 , 然后 使 用 “ 换 ” 变 命令 完成 其余 两个 面的复 制 ,最后使 用 “ 已存在 的表 面 ” (x t g uf e命令将 这三个 曲面转化为 补片体 。最终 E ii r c) sn S a
补 片的效果 , 图 2所示 。 如 () 3 创建 拆 分面
扇 叶 最 后 的分 模 结 果 作 ” 具 条 中 的 工
合 后 的 片 体 之 然后 使 用 “ 变换 ” 令 , 到 型芯 和 命 得 启动 U G后 , 入建 模 环境 , 改 工 作 坐标 系 , Z 问分 割体 特 征 的创建 。 进 修 使 C
方 向 为开模 方 向 。 ( ) 置收 缩率 2设 型腔 是分 解 视 图 , 图 8所示 。 如
型腔 与 型 芯 的创 建 , 风
如 图 5所示 。
() 6 创建 型 芯和 型腔
第一步: 创建求差特征。 单击“ 特征操作” 工具条中的“ 求
差” 命令 , 工件 与风扇 叶实体之间求差特征 的创 建。 完成
第二 步 : 拆
芯与型腔 ” 令 , 成 分型芯和型腔 。 命 完
先 单 击 “ 征 操 特 “ 割体” 令 , 分 命 完 成 工 件 与 缝
工具 。 文介 绍 了注塑模 具 分模 的基 本原 理 和方 法 , 于 本 基 Mo zr 模 块 和建 模模 块 平 台 ,以风 扇 叶 塑件 为 例 , l Wi d d a 详 细 阐述 了 自动分 模 与手 工 分模 方 法 的分模 过 程 ,为 注
的片 体 , 图 7所 示 。 如
完成 分型 面的创建 , 图 4 如 所示 。 第三 步 : 取 区域 。 抽 使用 “ 抽取 区域 与分型线 ” 令 , 命 核 对 总面数等 于型腔 面数 与型芯 面数之 和 , 完成 区域 复制 。 第 四步 : 建 型 芯 创 与型 腔 。使 用 “ 建 型 创
ug注塑模具设计教程

ug注塑模具设计教程UG注塑模具设计是一种CAD软件,广泛应用于注塑模具的设计和制造过程中。
它具有强大的功能和灵活性,可以帮助工程师快速、高效地进行模具设计。
下面是一个简单的UG注塑模具设计教程,帮助初学者了解基本操作和流程。
首先,需要打开UG软件,然后选择创建新文件。
接下来,在顶部菜单栏中选择“文件”->“新建”->“零件”。
然后,选择适当的单位制和零件模板,点击“确认”。
接着,我们需要绘制模具的零部件轮廓。
在左侧的工具栏中选择适当的绘图工具,如线段、圆等,根据设计要求绘制模具的外形。
可以使用各种绘图和编辑工具对零件进行修整和调整。
完成零部件的绘制后,可以选择进行参数化建模。
这就是给零件添加尺寸和约束,并通过修改尺寸值来实现模具的形状调整。
参数化建模是UG的一个重要特性,它可以帮助设计师在设计过程中灵活地进行修改和优化。
接下来,我们可以对零件进行三维建模。
选择适当的工具,如拉伸、旋转、挤压等,根据需要将零件的二维轮廓转化为三维实体。
可以使用各种操作如修整、倒角等对模具进行进一步的完善和优化。
完成零部件的三维建模后,可以创建装配体。
选择菜单栏中的“装配体”选项,将各个零部件放置在正确的位置上,并设置适当的装配关系和约束。
这样可以模拟模具在实际使用过程中的动作和关系,方便进行后续的设计和分析。
最后,可以进行模具的细节设计和分析。
可以使用菜单栏中的各种工具和功能,如切削、填充、检查等,对模具进行进一步的细化和检验。
可以生成模具的图纸,并导出相关文件以供制造和生产使用。
UG注塑模具设计教程中还涉及很多其他的工具和功能,这里只是简单介绍了基本操作流程。
初学者可以通过学习和实践,逐渐掌握UG软件的使用技巧和方法。
在实际的模具设计中,还需要结合具体的需求和制造工艺进行综合考虑和优化。
希望这个简单的UG注塑模具设计教程能够对初学者有所帮助。
基于UG的注塑模具研究

基于UG的注塑模具研究一、本文概述随着现代制造业的快速发展,注塑模具作为塑料制品生产中的重要工艺装备,其设计、制造和应用水平直接影响到产品的质量和生产效率。
因此,对注塑模具的研究与改进一直是制造业领域的热点课题。
本文旨在探讨基于UG(Unigraphics N,一款广泛应用的CAD/CAM/CAE 集成软件)的注塑模具研究,通过对UG软件在注塑模具设计、分析、优化等方面的应用进行深入分析,以期提高注塑模具的设计效率、制造精度和使用性能。
本文将首先介绍注塑模具的基本原理和分类,阐述注塑模具在现代制造业中的重要地位和作用。
接着,重点分析UG软件在注塑模具设计中的应用,包括模具型腔设计、浇注系统设计、冷却系统设计等方面。
还将探讨UG软件在注塑模具分析和优化方面的功能,如模具流场分析、结构强度分析、热平衡分析等。
通过实际案例的分析和比较,展示UG软件在注塑模具研究中的实际应用效果,为相关领域的研究人员和工程师提供有益的参考和借鉴。
通过本文的研究,旨在推动基于UG的注塑模具设计的理论创新和技术进步,为提升我国制造业的整体竞争力和可持续发展贡献力量。
二、注塑模具基础知识注塑模具,亦称为塑料注射模具,是塑料加工工业中广泛使用的一种成型工具。
它的主要工作原理是,通过注塑机将熔融的塑料注入模具型腔,经冷却固化后,获得所需形状和尺寸的塑料制品。
注塑模具的设计、制造质量直接影响到产品的质量和生产效率,因此,对注塑模具的研究具有重要意义。
注塑模具通常由动模、定模两大部分组成,动模和定模在注塑机的合模机构作用下闭合,形成模具型腔。
模具型腔的形状和尺寸决定了塑料制品的外形和尺寸。
另外,注塑模具还包括浇注系统、导向机构、脱模机构、侧向分型与抽芯机构、温度调节系统等组成部分,这些部分共同保证了注塑过程的顺利进行。
在注塑模具的设计过程中,需要考虑的因素包括塑料的性能、产品的结构、注塑机的类型及规格、模具的制造工艺等。
设计合理的浇注系统可以保证塑料在模具型腔中均匀流动,避免产生气泡、缩孔等缺陷。
使用UG进行塑料模具设计
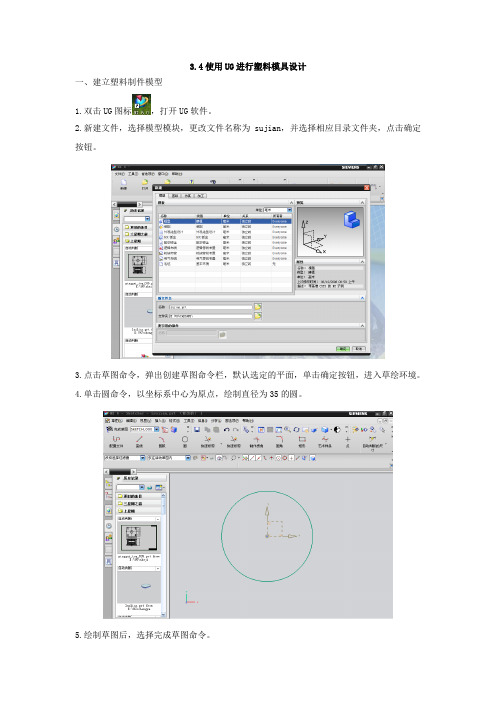
3.4使用UG进行塑料模具设计一、建立塑料制件模型1.双击UG图标,打开UG软件。
2.新建文件,选择模型模块,更改文件名称为sujian,并选择相应目录文件夹,点击确定按钮。
3.点击草图命令,弹出创建草图命令栏,默认选定的平面,单击确定按钮,进入草绘环境。
4.单击圆命令,以坐标系中心为原点,绘制直径为35的圆。
5.绘制草图后,选择完成草图命令。
6.在工具栏中点击拉伸命令,之后弹出拉伸命令工具栏,选择草绘的圆,设置拉伸高度为18,拔模角度为5,点击确定。
7.移动坐标系位置。
点击WCS命令,在弹出命令栏中将ZC改为1.5,其余默认,点击确定。
此时坐标系原点向上移动1.5mm。
8.选则平移后的XC-YC作为草绘平面,绘制直径为32的圆,点击完成草图。
9.点击拉伸按钮,原则上步草绘曲线作为拉伸曲线,在限制中将结束改为直至选定对象,选择实体上表面作为终止面,将布尔运算改为求差,拔模角度为5。
倒角大小为1.5,单击确定。
完成零件体建立。
1.点击开始—所有应用模块—注塑模向导,进入模具设计。
此时弹出注塑模工具条。
2.点击项目初始化项目,进行初始设计,将材料改为ABS,其余默认,点击确定。
Z轴改为向下,点击鼠标中键确定。
4.建立模具工作坐标。
点击模具CSYS,弹出对话框,选择选定面的中心命令,选择口的圆环表面,单击确定,此时模具坐标就移到分模面了。
5.点击工件按钮,将开始设为15,结束设为25,单击确定。
6.点击分型工具按钮,弹出分型管理器,对工件进行分型,建立模具型芯和型腔。
7.选择编辑分型线按钮,创建分型线。
弹出分型线对话框,选择自动搜索分型线,点击确定。
弹出对话框,点击选择体,选择零件,点击确定。
完成分型线的建立。
8.建立分型面。
点击创建/编辑分型面按钮,弹出创建分型面对话框,点击创建分型面,在弹出的分型面对话框中选择扩大的曲面,在弹出的对话框中拖动滚动条,增大分型面大小。
创建结果如图所示。
9.建立型腔和型芯区域。
ug注塑模具设计流程
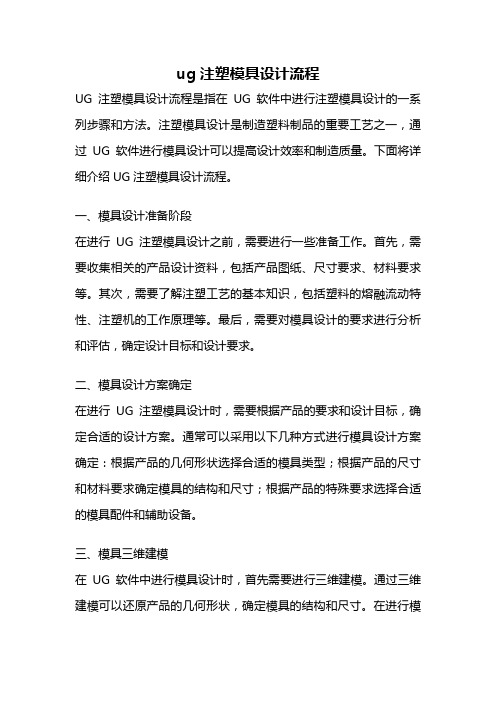
ug注塑模具设计流程UG注塑模具设计流程是指在UG软件中进行注塑模具设计的一系列步骤和方法。
注塑模具设计是制造塑料制品的重要工艺之一,通过UG软件进行模具设计可以提高设计效率和制造质量。
下面将详细介绍UG注塑模具设计流程。
一、模具设计准备阶段在进行UG注塑模具设计之前,需要进行一些准备工作。
首先,需要收集相关的产品设计资料,包括产品图纸、尺寸要求、材料要求等。
其次,需要了解注塑工艺的基本知识,包括塑料的熔融流动特性、注塑机的工作原理等。
最后,需要对模具设计的要求进行分析和评估,确定设计目标和设计要求。
二、模具设计方案确定在进行UG注塑模具设计时,需要根据产品的要求和设计目标,确定合适的设计方案。
通常可以采用以下几种方式进行模具设计方案确定:根据产品的几何形状选择合适的模具类型;根据产品的尺寸和材料要求确定模具的结构和尺寸;根据产品的特殊要求选择合适的模具配件和辅助设备。
三、模具三维建模在UG软件中进行模具设计时,首先需要进行三维建模。
通过三维建模可以还原产品的几何形状,确定模具的结构和尺寸。
在进行模具三维建模时,可以使用UG软件提供的各种建模工具和功能,如绘制、修剪、拉伸、倒角等。
通过不断调整和优化模具的三维模型,可以得到满足产品要求的模具设计方案。
四、注塑工艺分析在进行UG注塑模具设计时,需要进行注塑工艺分析。
通过注塑工艺分析可以评估模具的可制造性和工艺性,确定注塑过程的参数和工艺要求。
注塑工艺分析可以通过UG软件中的模流分析工具进行,通过模流分析可以模拟注塑过程中的熔融流动、充填、冷却等过程,评估模具的充填性能和冷却效果,优化模具设计。
五、模具细节设计在进行UG注塑模具设计时,需要进行模具的细节设计。
模具的细节设计包括模具的分型面设计、模腔和模芯的设计、冷却系统的设计、顶出机构的设计等。
在进行模具细节设计时,需要考虑模具的可制造性、可装配性和可维修性,同时还需要考虑产品的要求和工艺的要求。
通过UG软件提供的各种设计工具和功能,可以方便快捷地完成模具的细节设计。
ug注塑模具设计实例
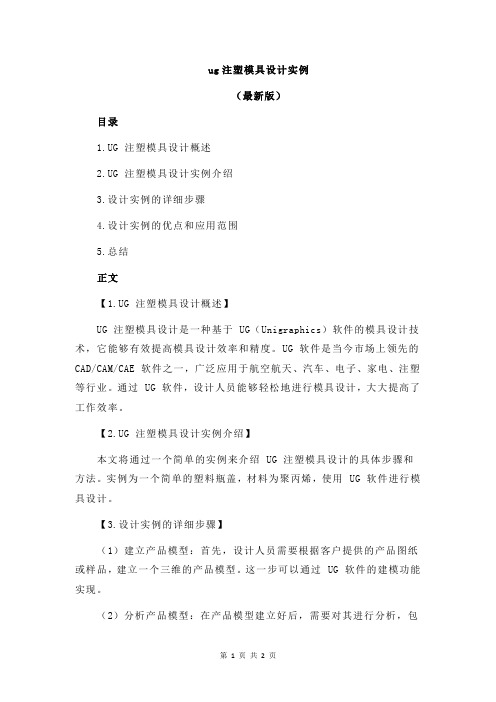
ug注塑模具设计实例(最新版)目录1.UG 注塑模具设计概述2.UG 注塑模具设计实例介绍3.设计实例的详细步骤4.设计实例的优点和应用范围5.总结正文【1.UG 注塑模具设计概述】UG 注塑模具设计是一种基于 UG(Unigraphics)软件的模具设计技术,它能够有效提高模具设计效率和精度。
UG 软件是当今市场上领先的CAD/CAM/CAE 软件之一,广泛应用于航空航天、汽车、电子、家电、注塑等行业。
通过 UG 软件,设计人员能够轻松地进行模具设计,大大提高了工作效率。
【2.UG 注塑模具设计实例介绍】本文将通过一个简单的实例来介绍 UG 注塑模具设计的具体步骤和方法。
实例为一个简单的塑料瓶盖,材料为聚丙烯,使用 UG 软件进行模具设计。
【3.设计实例的详细步骤】(1)建立产品模型:首先,设计人员需要根据客户提供的产品图纸或样品,建立一个三维的产品模型。
这一步可以通过 UG 软件的建模功能实现。
(2)分析产品模型:在产品模型建立好后,需要对其进行分析,包括分析产品的结构、材料、尺寸公差等,以便在模具设计中充分考虑这些因素。
(3)模具设计:在分析好产品模型后,就可以开始进行模具设计了。
这一步包括确定模具的类型、设计模具的结构、确定模具的尺寸等。
(4)模具制造:在模具设计好后,需要根据设计图纸制造模具。
这一步通常由专门的模具制造厂完成。
(5)模具试模:模具制造好后,需要进行试模。
通过试模,可以检查模具的设计和制造是否存在问题,如果存在问题,需要及时进行修正。
【4.设计实例的优点和应用范围】UG 注塑模具设计具有许多优点,包括设计精度高、效率高、操作简单等。
这使得它广泛应用于各种注塑产品的生产中。
无论是简单的日用品,还是复杂的机械零件,都可以通过 UG 注塑模具设计进行生产。
- 1、下载文档前请自行甄别文档内容的完整性,平台不提供额外的编辑、内容补充、找答案等附加服务。
- 2、"仅部分预览"的文档,不可在线预览部分如存在完整性等问题,可反馈申请退款(可完整预览的文档不适用该条件!)。
- 3、如文档侵犯您的权益,请联系客服反馈,我们会尽快为您处理(人工客服工作时间:9:00-18:30)。
3.4使用UG进行塑料模具设计
一、建立塑料制件模型
1.双击UG图标,打开UG软件。
2.新建文件,选择模型模块,更改文件名称为sujian,并选择相应目录文件夹,点击确定按钮。
3.点击草图命令,弹出创建草图命令栏,默认选定的平面,单击确定按钮,进入草绘环境。
4.单击圆命令,以坐标系中心为原点,绘制直径为35的圆。
5.绘制草图后,选择完成草图命令。
6.在工具栏中点击拉伸命令,之后弹出拉伸命令工具栏,选择草绘的圆,设置拉伸高度为18,拔模角度为5,点击确定。
7.移动坐标系位置。
点击WCS命令,在弹出命令栏中将ZC改为1.5,其余默认,点击确定。
此时坐标系原点向上移动1.5mm。
8.选则平移后的XC-YC作为草绘平面,绘制直径为32的圆,点击完成草图。
9.点击拉伸按钮,原则上步草绘曲线作为拉伸曲线,在限制中将结束改为直至选定对象,选择实体上表面作为终止面,将布尔运算改为求差,拔模角度为5。
倒角大小为1.5,单击确定。
完成零件体建立。
1.点击开始—所有应用模块—注塑模向导,进入模具设计。
此时弹出注塑模工具条。
2.点击项目初始化项目,进行初始设计,将材料改为ABS,其余默认,点击确定。
Z轴改为向下,点击鼠标中键确定。
4.建立模具工作坐标。
点击模具CSYS,弹出对话框,选择选定面的中心命令,选择口的圆环表面,单击确定,此时模具坐标就移到分模面了。
5.点击工件按钮,将开始设为15,结束设为25,单击确定。
6.点击分型工具按钮,弹出分型管理器,对工件进行分型,建立模具型芯和型腔。
7.选择编辑分型线按钮,创建分型线。
弹出分型线对话框,选择自动搜索分型线,点击确定。
弹出对话框,点击选择体,选择零件,点击确定。
完成分型线的建立。
8.建立分型面。
点击创建/编辑分型面按钮,弹出创建分型面对话框,点击创建分型面,在
弹出的分型面对话框中选择扩大的曲面,在弹出的对话框中拖动滚动条,增大分型面大小。
创建结果如图所示。
9.建立型腔和型芯区域。
点击抽取区域和分型线按钮,弹出抽取区域对话框,选择Cavity region,在设置中选择创建区域,点击搜索区域,弹出搜索区域对话框,选择型腔区域任意一个面,点击确定,完成型腔区域创建。
同理,完成模具型芯区域的创建。
10.创建模具型腔和型芯。
点击创建型腔和型芯按钮,弹出定义型腔和型芯对话框,选择All Regions,单击确定,如果方向相反则点击法线方向。
完成模具型腔和型芯的创建。
11.查看结果。
点击窗口,选择sujian_prod_003.prt查看模具型腔和型芯。
12.建立一模多腔。
(1)点击型腔布局,弹出型腔布局窗口,单击编辑布局中的变换按钮,弹出变换对话框,
选择旋转类型,同时选择工件边缘点作为旋转点,角度为180度,单击确定,如图所示。
(2)依照上述方法,再分别进行两次变换,角度分别为90、180。
然后选择编辑布局中的自动对准中心。
(3)点击编辑部局中的编辑插入腔按钮,弹出刀槽对话框,选择R=10,单击确定,完成刀槽建立。
槽。
任意选中一个动模,右键单击,选择设为工作部件。
点击开始,将UG改为建模状态,单击倒圆角命令,选择倒角位置,大小设为10mm,单击确定,完成型腔圆角建立。
同理进
行型芯圆角建立。
最后,点击编辑中的全部显示,完成注塑模具型腔、型芯的建立。
三、调入模架以及后处理
1.点击模架按钮,弹出模架管理对话框,在布局信息中给出模具长、宽、上模板高度和下模板高度。
选择2525模架,将型腔固定板高度AP改为46,CP改为106,单击确定调入模架,完成装配。
2.修剪模板腔体。
单击腔体按钮,弹出腔体对话框,选择型腔固定板,单击工具选项中的查找相交,系统自动查找型腔固定板中的嵌入件,单击应用;同理,选择型芯固定板创
建腔体。
其效果如图所示。
型腔固定板型芯固定板
3.添加定位圈。
经过测量,定模板座的凹槽圆半径为45,深5。
单击标准件图标,弹出标准件管理对话框,加载法兰盘。
将DIAMETER设为120,BOTTOM_C_BORE_DIA设为38,单击确定。
4.测量距离——测浇口套的总长。
点击分析—测量距离,弹出测量距离窗口,类型改为投影距离,选择方向为Z方向,然后选择顶面为开始对象,选择分型面为结束对象,显示结果为72mm,即浇口套总长为72mm。
确定,完成浇口套的加载。
其中,CATALOG_DIA为浇口套外径设为16,HEAD_HEIGHT为头部深度设为16,O为浇口小头直径设为3.5,RADIUS_DEEP为球头深度设为5,CATALOG_LENGTH为深度,用测量值减去头部深度,即72-16=56mm,HEAD_DIA为头部直径设为38,其余默认。
隐藏上面部分零件后,效果如图。
6.模具修剪。
修剪定模固定板以及定模座。
点击编辑—全部显示,显示所有部件。
单击腔体命令,选择定模座和定模固定板作为目标体,选择浇口套和定位圈作为工具体,单击确定。
击确定,完成流道引导线串定义。
选中刚刚创建的引导线,点击重定位,弹出重定位对话框。
选择旋转,角度改为45度,点击确定,最后点击确定。
在复制方法中选择移动,点击确定。
开始创建流道通道。
在创建流道通道中,横截面设为半圆命令,R=5,流道位置改为型腔,冷料位置选择两
端,单击确定,完成流道创建。
8.创建浇口。
单击浇口图标,弹出浇口设计窗口。
位置改为型腔,按照默认的浇口尺寸,单击应用,弹出点窗口,此时选择浇口起始位置,选择冷料穴下方,点击确定。
弹出矢量对话框,选择与XC轴成一定角度,角度设为45,点击确定。
9.修剪流道、浇口套和浇口道。
选择腔体命令,选择型腔为目标体,选择浇口套、浇口和流道作为工具体,单击确定;选择浇口道作为目标体,流道作为工具体,单击确定。
结果如图。
10.创建推杆。
点击标准件按钮,弹出标准件管理对话框,在分类中选择Injection,直径取3,长度设为125,单击确定,弹出点对话框,选择推杆位置,单击确定,完成创建。
11.推杆后处理。
点击顶杆后处理按钮,弹出顶杆后处理对话框,按默认设置,选择顶杆作为目标体,点击修剪组件,单击确定按钮。
12.推杆型腔修剪。
单击型腔按钮,选择推杆固定板和动模固定板作为目标体,选择推杆作为工具体,单击确定。
13.创建冷却水道。
单击冷却水道按钮,弹出冷却组件设计对话框,将PIPE_THEARD 改为M8,单击确定,弹出选择一个面对话框,选择定模板的侧面,单击确定,弹出点对话框,任选一点,弹出位置对话框,选择面中心,将D1设为60,D2设为10,单击确定后,点击取消,完成水道创建。
选择刚刚创建的水道,进行参数编辑。
点击尺寸,对水道尺寸进行修改。
14.添加水堵。
选择冷却水道按钮,将尺寸设为M10,单击确定,完成水堵的添加。
堵作为工具体,单击确定,结果如图。
的孔右键点击删除。
17.创建复位杆。
单击标准件按钮,选择return pin复位杆,直径改为6,长度设为102,单击确定。
弹出点对话框,选择XC为105,YC为60,单击确定,同理,创建另外4根复位杆。
18.复位杆型腔修剪。
选择推杆固定板和动模固定板作为目标体,选择复位杆作为工具体,单击确定。
19.采用分析中的测量工具测量从分型面到动模底板的距离为102mm。
20.创建拉料杆。
单击标准件按钮,进行参数设置,选择中心作为基点,单击确定,完成拉料杆的创建,将长度改为95。
21.拉料杆型腔修剪。
选择动模和动模固定板作为目标体,选择拉料杆作为工具体,单击确定,完成修剪。
22.创建推板导套。
单击标准件按钮,选择推板导套,设置尺寸,选择位置,单击确定。
之
后进行型腔修剪,方法同前。
位置,单击确定。
其创建位置选择导套中心。
创建两个导套后进行动模底板型腔修剪。
24.删除动模底板上多余的零件以及零件孔。
25.创建动模底板上的注塑机顶杆孔。
右键单击动模底板,将其设为工作部件,选择建模模块的孔功能,创建一个通孔,直径为15mm。
26.最终结果显示。