输油站内管线腐蚀穿孔的控制
油田地面管线腐蚀穿孔原因分析与处理方法

油田地面管线腐蚀穿孔原因分析与处理方法摘要:由于我国石油产业的迅速发展,地下油气管道已被越来越多地用于贮存运输。
但是,由于长期的服役以及外部环境的腐蚀,导致了地下管道存在着许多问题,在这些情况下,管道的腐蚀、穿孔尤为严重。
这些现象不但会给油田的正常开采带来很大的影响,也会给周围的环境带来很大的负面影响。
为此,从腐蚀、穿孔等角度,对管道故障产生的原因进行了分析,并提出了切实可行的解决方案。
关键词:油田地面管线;腐蚀穿孔原因分析;处理方法引言腐蚀是一种物质由于受到环境的影响而引起的破坏。
对于石油工程来说,管线腐蚀是一个由来已久的问题,会影响到其的正常运行,如果对机电安装项目的管理与控制工作不重视,这将导致巨大的资源浪费,带来巨大的经济损失。
在油田生产中,如何降低地表管道的穿孔腐蚀是一个十分重要的课题。
在实际操作中,为了有效地降低腐蚀时间,必须增强对这一问题成因的认识,并据此制订出相应的预防措施,因此,应加强对引起地下管线腐蚀的主控因素的把握,研究出降低地下管线腐蚀的对策,以提高油田的经济效益。
一、油田地面管线穿孔腐蚀类型(一)电化学腐蚀这种腐蚀现象多发生在地面管道中,具有腐蚀性,由此造成的管线腐蚀,在油田开采过程中,会产生大量的废水,每天的废水量很大,占到了油田中的85%,因此,油田废水是管道中共同的组成成分。
而且,污水的成分比较复杂,里面包含了很多的化学物质和溶解性气体,此外,还会出现具有强烈腐蚀性的硫化物,从而加剧了输油管线的内部腐蚀问题。
(二)微生物腐蚀油井中的氯离子含量很高,特别是在靠近海洋的近海油田,使土壤含盐量很高,含盐量很高,主要是氯化物,将会造成地面管道的腐蚀状况。
在一些油气田中,管道电阻率很低,在海岸附近的油气田中,每一套电阻率仅为25欧姆,可以看出,相对于一些陆上油田,由于土壤具有极强的腐蚀性,所以这种管道在土壤中会受到更大的腐蚀。
(三)流体冲刷腐蚀石油管线中的污水具有高流速,且含有从油田开采出来的流体,流体具有盐分难溶性、含大量泥沙等特点,在输送过程中会对管线产生一定的破坏。
分析油田地面集输管线腐蚀穿孔及防治措施

[1]何力源.油田地面集输管线腐蚀穿孔分析及防治措施[J].化工设计通讯,2019,45(08):37-38.
[2]宁野.油田地面系统管线腐蚀穿孔原因及防治策略[J].化工管理,2019(21):223-224.
[3]王强.油田地面系统管线腐蚀穿孔原因及防治策略[J].全面腐蚀控制,2018,32(07):110-111.
1.2受冲刷腐蚀持续作用
输送流体于管道中高速流动会在管道内壁产生冲刷腐蚀,特别是在三通、弯头与肘管处,由于流体方向与速度产生突变,使紊流明显增加,产生更严重的冲刷腐蚀。在受到冲刷腐蚀作用后,金属表面将产生腐蚀产物,产物不断成膜,导致新金属直接裸露于腐蚀介质,使管道不断变薄,造成腐蚀穿孔。
1.3管材质量问题
分析油田地面集输管线腐蚀穿孔及防治措施
摘要:针对油田中的地面集输管线,在介绍其腐蚀穿孔产生原因的基础上,提出行之有效的防治措施,包括采用碳钢与缓蚀剂相结合的防腐模式、选取非金属管线、做好管线的定期检测,以此为实际的管线防腐工作提供技术参考,保证防腐的有效性、可行性与经济性。
关键词:油取非金属管线
近几年,我国对非金属管的关注度越来越高,地面集输管网对这一管线的使用也逐渐增多。以某些油田为例,其非金属管线实际使用量可以达到管线总长度50%,主要用在口径相对较小的干线管与单井集油当中。若从腐蚀风险的角度考虑,对于非金属管,其内外部都具有良好的防腐性能,实际的腐蚀风险相对较小。管线类型的选择与施工都会对该管的实际防腐效果造成很大影响。在实际的选型过程中,应对具体使用工况进行综合考虑,特别是压力与温度适宜范围,如果选型不当,将引起泄漏与爆管。在现场施工中,不仅要严格按照设计要求进行管线敷设,而且还要防止管线受到损伤[4]。对此,做好选型与施工,保证施工质量,是这一防腐蚀措施的关键所在,必须引起相关人员的高度重视。
浅谈有关油田集输管线的腐蚀原因及质量控制

浅谈有关油田集输管线的腐蚀原因及质量控制油气是我国各领域发展重要的资源,在油气资源开采过程中,依靠集输管线将油气运输到储存区域。
但是油气中存在较多的腐蚀物质,严重腐蚀集输管线,此外集输管线受到自然因素等影响,会加速腐蚀速度。
本文围绕油田集输管线的腐蚀原因以及质量控制展开讨论,腐蚀原因主要分为集输管线质量、防腐层老化以及运输过程等,针对上述问题进行深入的讨论,为防腐蚀实施的控制措施提供参考依据。
标签:集输管线;腐蚀;电解质;质量控制引言:现阶段油田集输管线主要使用金属材料,而油气中存在较多的腐蚀物质,长期受到腐蚀物质的侵蚀,导致集输管线腐蚀情况不断加剧,严重影响到集输管线的使用效率和寿命。
若未能及时处理集输管线出现的腐蚀问题,从集输管线中渗漏出的油气,会严重污染周围的环境。
在对集输管线出现的腐蚀情况进行分析发现,集输管线需要出现氧化反应,并且形成电解液,利用导体使带电离子不断的运用,造成集输管线出现腐蚀情况。
1.油田集输管线的腐蚀原因1.1集输管线质量问题集输管线主要使用金属材料,由于金属材料会与尤其中的相关物质发生化学反应,致使管线出现腐蚀情况。
所以集输管线的材料是引发腐蚀问题的直接原因,集输管线使用的材料,应具备良好的抗氧化、抗腐蚀等性能。
选用具备较高的抗腐蚀性能金属材料,可以避免金属管线出腐蚀问题。
许多集输管线都会选用质量较差的材料,而且金属材料在焊接过程中,极易出现焊缝,油气利用焊缝侵蚀集输管线,在焊缝位置产生电解反应,并且反应范围不断扩大,导致管線腐蚀速度不断加快。
1.2防腐层老化问题我国多数的油田都处在温度较低的地区,油田会增加保温措施,避免集输管线受冻影响到正常的集输工作。
但是集输管线长时间在地质结构中,受到地质环境的影响,管线的防腐层会出现不同程度的老化情况,一旦防腐层出现老化,地质结构的水等自然物质会侵蚀到管线。
目前集输管线使用的防腐层,主要材料为沥青,在防腐层会出现纵向裂纹,正是纵向裂纹的影响,裂纹范围不断扩大,导致防腐层与管线出现脱离情况,外界的腐蚀物质会附着在管线上,加速管线腐蚀速度。
BZ34油田油气水混输管线腐蚀穿孔原因与控制建议

电偶腐蚀的发生。 ③ 采用表面处理技术,可以 在油管接箍表面进行磷化处理, 增 加油管接箍的耐腐蚀性能;可在接 箍表面镀铜, 有效的改善接箍抗粘 扣性能。 ④ 采用橡胶复合油管接箍增 加油管与接箍的密封性, 防止油管 螺纹的腐蚀。 ⑤ 提高除氧效率,采用性能 优良的除氧剂, 提高注入水的除氧 效率,降低腐蚀的发生。 ⑥ 机械装配,在油管与接箍 装配时,规范操作规程,避免出现 过大预紧力, 导致螺纹连接处表面 力腐蚀的发生。
2.3 保温棉吸水性试验
保温棉是最为常用的保温材 料。保温层材料由矿物经煅烧、 粘
2.4 腐蚀产物分析
全面腐蚀控制 第 24 卷第 1 期 2010 年 1 月
21
海洋石油 Offshore Oil
(假定该管道没有更换过) 那么内 , 腐蚀是不可避免的, 根据测厚的数 据, 判断该段管道设计壁厚应该为 8mm 左右; (2) 该管道输送介质中含有气 体,管道长时间处于轻微震动状 态,因此存在金属疲劳的可能; (3)局部外腐蚀是腐蚀穿孔的 主要原因。失效管道上,较大面积 两个腐蚀部位并不联通,因此小面 该段管道保温层外部镀锌铁皮(暂 定)在使用过程中受到损伤,连接 处形成孔道或者保温层搭接处密封 未做好,导致保温层不能将外部液 体环境和内部保温棉完全隔开;在 下雨天 (也可能是施工失误) 雨水 , 顺着镀锌铁皮缝隙流入保温棉,保 (上接第 18 页) 的油管,溶解速度反而减小,所以 总体而言,油管没有腐蚀,而接箍 发生了腐蚀。另外, 完井液和海水 在环空中的存在还会对接箍造成冲 刷腐蚀。 相关文献表明,在接箍和油管 连接处还可能存在应力集中,如果 在油管和接箍相接触的地方存在应
海洋石油 Offshore Oil
BZ34 油田油气水混输管线腐蚀穿孔 原因与控制建议
油田地面集输管线腐蚀穿孔分析及防治措施

油田地面集输管线腐蚀穿孔分析及防治措施摘要:石油生产工业当中,输送过程作为其中很重要的一个环节,开采出原油和天然气等自然资源都通过储存,后期才能对这些自然进行加工处理和开采运用。
石油生产企业中集输占据着很重要的地位,但是从现阶段石油集输可以看出,其中依然存在一些不良因素。
由此,文章专门针对油田地面集输管线腐蚀穿孔防治的问题进行阐述,采取有效对策将其运输过程出现的危险以及有害因素降低。
关键词∶油田地面;集输管线;腐蚀;穿孔;防治对策1导致油田地面集输管线腐蚀穿孔的主要因素1.1防腐层受损或老化从目前日常生活中可以看出,集输管线腐蚀现象的发生很多都是由于老化原因而导致。
首先是因为附近生活环境自然因素所造成,这些因素会使这种管线出现老化问题,并且这也是一个很重要的因素,由于集输管线在使用期间会长期裸露在外,跟空气大面积进行接触,风吹日晒,并且受到一些恶劣天气影响,导致其老化速度越来越快。
如果这种管线出现严重的穿孔现象,操作者对这种管线进行焊接和制作过程中,焊接的一些地方会由于时间流逝而发生一些裂纹。
由于集输管线长期使用,裂纹现象也会越来越大,逐渐对集输管线的正常运转造成不利影响。
若在裂纹非常大的情况下,会导致钢管以及表层出现分开情况,如果遇到非常恶劣的天气,比如雨雪交加的天气会导致这种现象逐渐扩大。
不能及时对这些裂纹进行修复会发生腐蚀穿孔的情况。
基数管道的表面会有一层防腐剂,若这个防腐剂经过风吹日晒就会脱落,这样就会失去自身的粘结性,其次因为各项因素的影响,集输管线在运送期间,员工安装时没有办法依靠人力来完成这项操作。
或者因为一些企业在对集输管线运送进行设计过程中,技术人员缺乏专业性的知识和全面综合能力素养、理论知识,由于这些问题的发生都会使员工在安装过程中,并没有运用更科学的制度不断去进行这项操作。
对技术管线进行安装过程中,要求管理者通过运用车辆进行运输和管理,在实际运送过程中还会发生相互碰撞的情况,若员工对此没有提高重视,导致这项关心的表面遭到损坏。
油田集输系统原油管道腐蚀穿孔原因及防腐措施探讨
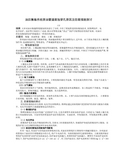
油田集输系统原油管道腐蚀穿孔原因及防腐措施探讨ffF摘要:文章对油田集输管线腐蚀原因进行了分析,介绍了埋地管道的防腐蚀技术,从物理防护、电化学防护、涂层等方面进行了论述,指出对管线实施“热点”保护可取得较好的保护效果,对油田的设备腐蚀的防护措施提出一些相应的建议。
关键词: 集输原油管道腐蚀土壤阴极保护胜利油田某油田属于滩海环境,原油输油管线主要以钢管为主,近年来,由于原油含硫以及土壤的腐蚀作用,造成腐蚀穿孔,管线老化,严重威胁管道安全运行。
一.管线腐蚀现状受沿海气候、土壤盐碱含量高等因素影响,某集输管网电化学腐蚀强烈,采用检漏仪对全其中一条原油输送管线进行检漏,共检出漏点300余处,泄漏段管线中上部尚好,中部以下外防护层破损严重,管壁腐蚀减薄严重。
二.腐蚀原因分析管线腐蚀环境主要包括四个方面:土壤、地下水、大气、输送介质。
(一)土壤腐蚀土壤是由多种无机物、有机物、水和空气组成的极其复杂的不均匀多相体系,土壤的颗粒之间存在着大量的孔隙,孔隙中充满空气和水,盐类溶解在水中,土壤就成为电解质,土壤各处的组成和性能存在差异,透气性条件不一致,氧的渗透率变化幅度很大,形成氧浓差腐蚀。
另外,土壤里的金属表面因土壤结构不均匀以及因金属本身存在的不均匀性还存在微电池腐蚀。
土壤中的硫代硫酸盐、硫氧化细菌等细菌也对管道产生腐蚀作用。
(二)地下水腐蚀地下水的腐蚀性与土壤关系密切,主要致腐因素是含盐量,特别是氯化物的含量,使地下水成为一种促进化学腐蚀和电化学腐蚀的电解液。
(三)大气腐蚀某油田的受海洋大气影响,相对湿度较高,金属表面易形成薄液层,加上海盐粒子含量高,环境温差变化较大,距海岸越近,腐蚀程度越强,而且趋势明显。
(四)输送介质腐蚀油田集输输送介质包括原油、原油和水的混合物、水,主要与设备内部的腐蚀过程有关,主要腐蚀介质有硫、硫化物、氯盐、酸性水、氢等。
三.防腐措施的探讨常用的防腐蚀技术分两种,电化学法和物理法。
油田埋地管线腐蚀穿孔原因与预防措施
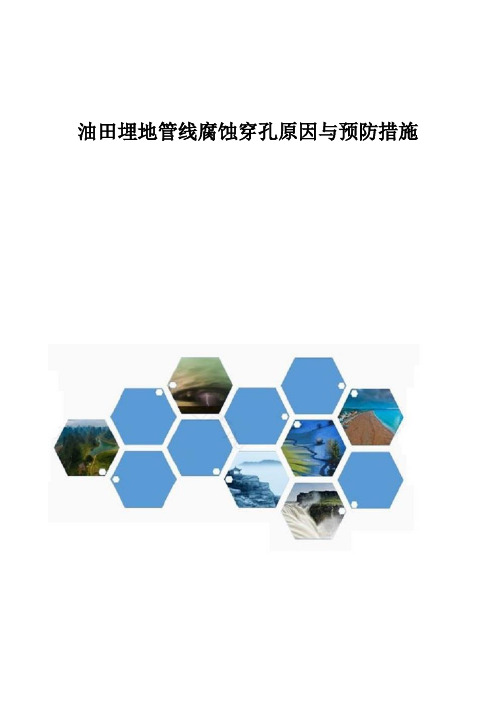
油田埋地管线腐蚀穿孔原因与预防措施摘要在油田生产过程中,我们的井、站、间的各种管线经常会遇到管线穿孔的问题,穿孔不仅造成浪费并污染环境,而且也造成明显的经济损失,通过分析发现管线穿孔的主要原因是防腐层老化、应力破坏、吸潮起泡、阴极剥离和防腐层施工质量及性能差,以及在其它施工过程中开工破土,管线受到外力拉伸,造成管线变形、断裂、防腐层破裂,脱壳失了去保护作用,降低了管线的使用寿命。
主题词管线腐蚀防腐层穿孔因素集输管线是油田的命脉,安全无泄漏是我们不懈的追求,为了减少管线的腐蚀穿孔,防腐层作为管线的绝缘屏障,将被保护体与腐蚀环境隔离,从而达到抑制管线腐蚀的目的,确保管线长期安全运行。
1、管线防腐层失效的因素:1.1管线防腐层老化,失去保护作用。
油水井管线的防腐层长期处于潮湿的环境中,其大分子降解时发生水解反应,高分子材料在较高的温度下易断链,使其粘结性越来越差,防腐层的粘接力和粘接强度在抵抗高剪切力的条件下,也受机械损坏,高剪切应力来源于粘土,这一机械损坏还会因高温而加剧,粘性土壤主要由于受冷热气流循环而引起的土壤的胀缩,土壤与管道产生位移而造成防腐层褶皱。
1.2地下管线吸收潮气造成防腐层起泡失效地下水透过有机覆盖层处于低劣的湿态附着状态,此Fe2+时水溶解在水中的腐蚀剂直接与钢管接触,当腐蚀进行时,产生的Fe2+、OH造成覆盖层下的渗透压池,因此形成泡而膨胀,剥开覆盖层,暴露出裸钢腐蚀的痕迹。
1.3阴极剥离造成防腐层起泡失效由于阴极保护不当引起的保护的电位过负,保护电流增大,产生H2从而起泡,防腐层与钢管的表面粘接较差,因此更容易导致防腐层的剥离。
1.4防腐层本身质量原因钢管在涂敷前的表面处理工序,若达不到有关规范所要求的等级,将引起管道防腐层剥离,防腐层与钢管的表面粘接不良容易而引发管线腐蚀穿孔。
1.5在施工时而造成的防腐层损坏管线在出厂前质量都是符合要求,而在施工现场,受作业环境的影响,焊接接头的防腐质量却不易保障,覆盖层与钢管表面污垢处理不干净,粘接力较差,防腐层与钢管极易造成脱壳,失去保护作用。
关于油田地面集输管道腐蚀穿孔风险分析及对策

关于油田地面集输管道腐蚀穿孔风险分析及对策发布时间:2021-04-21T02:31:36.385Z 来源:《中国科技人才》2021年第6期作者:刘晓雪[导读] 通常来讲,若集输管道的壁厚存在损耗,那么则表明管道的整体结构的完整性得到降低,当损耗达到一定程度时,会造成严重的经济损失和安全事故,而由于石油的油气存在易燃、易爆、易扩散的特质,因此,一般在发生事故的同时也存在不同程度的环境污染。
我国国内某油田在近年来频繁发生事故,原因就在于地面集输管道存在着腐蚀穿孔,因此该油田当前的任务就是对集输管道进行防腐维护,以保证生产的安全性。
大庆油田有限责任公司第五采油厂太北作业区黑龙江大庆 163000摘要:油田地面集输管道是油田的开发重要的组成部分,若管道存在腐蚀和穿孔的风险会使油田开发的安全性受到极大的威胁,所以,对集输管道的腐蚀风险进行明确,并此案去相应的措施进行预防是非常重要的,本次研究主要以国内的某油田存在集输管道腐蚀穿孔风险为例,对油田地面集输管道腐蚀穿孔风险进行分析,主要发现管道内壁中存在的腐蚀性物质分别为H2S和CO2,其是由矿化度较高的水层中在电化学腐蚀条件下所导致的,并通过研究可知,致使管道腐蚀穿孔风险存在的关键性因素为采出液体的含水率比较高,除此之外,若H2S和CO2共同存在,再加之Cl-的腐蚀程度加深加速,则会导致管道的腐蚀情况更为严重,因此,针对这些问题可以针对关键性的风险因素进行制定相应的预防治理措施,例如对管道内涂层管加大、采用一些符合管道、在管道中加入一些缓蚀剂等等,对管道内部的腐蚀情况进行缓解,从而降低腐蚀的风险,使石油开发得以正常进行。
关键词:集输管道;腐蚀;穿孔:风险分析;对策通常来讲,若集输管道的壁厚存在损耗,那么则表明管道的整体结构的完整性得到降低,当损耗达到一定程度时,会造成严重的经济损失和安全事故,而由于石油的油气存在易燃、易爆、易扩散的特质,因此,一般在发生事故的同时也存在不同程度的环境污染。
- 1、下载文档前请自行甄别文档内容的完整性,平台不提供额外的编辑、内容补充、找答案等附加服务。
- 2、"仅部分预览"的文档,不可在线预览部分如存在完整性等问题,可反馈申请退款(可完整预览的文档不适用该条件!)。
- 3、如文档侵犯您的权益,请联系客服反馈,我们会尽快为您处理(人工客服工作时间:9:00-18:30)。
输油站内管线腐蚀穿孔的控制
摘要:本文主要探讨了输油站内管线发生腐蚀穿孔这一现象的形成原因以及其控制对策。
文章是以某地的多个输油站为例,分析研究了站内管线发生腐蚀穿孔的具体情况,并通过站内管线取样测试和分析来确定腐蚀穿孔的成因,最后提出了控制输油站内管线腐蚀穿孔的防治对策,以供参考借鉴。
关键词:输油站管线腐蚀穿孔控制措施在最近一段时期内,某地的多家输油站都相继出现了管线泄漏的问题,经过检查发现是管道因被某些物质侵蚀后腐蚀穿孔而造成的,石油的泄漏不但造成了资源浪费,而其也为工作人员的日常管理维护工作带来很大麻烦。
技术维修人员及时对管线漏油问题进行了简要处理,在保证输油站正常运行的基础上,对发生腐蚀穿孔的管线进行了分析研究。
通过多次的研究与分析后,最终确定了导致管线发生腐蚀穿孔的主要原因是因为在管线的死油管段因长期没有流动,而使得其中物质受到影响而发生了侵蚀作用,使管道形成了小孔而造成石油泄漏。
在明确了成因后,维修人员立即制定了处理应对方案,采取了控制措施,避免管线内再出现死油管段,以防止管线再次发生穿孔泄漏事故。
1、站内管线腐蚀穿孔情况
由于某地的多处输油站都出现了管线腐蚀穿孔事故,为了能够更全面的掌握事故原因,我们对这些输油站的管线都进行了细致的检查与分析。
调查发现,其中一家输油站的管线发生穿孔事故的位置
在过滤器的旁边,阀门的后面架空的管线底部,并且经工作人员描述,该位置已经发生了多次穿孔问题;而另一家输油站的管线发生穿孔的位置是在给油泵的入口处一段架空管线的底部,管道所呈现出的腐蚀穿孔孔洞的形状是椭圆性,孔洞周边有毛坯。
另外,还有一家输油站也发生了管线穿孔事故,其位置是在装船泵房北侧的室外一段埋在地下的管线中。
这样来看,管线的腐蚀穿孔位置都不在同一个位置,那么是什么导致了其形成了腐蚀穿孔现象呢?
我们又对所有的穿孔管线进行了分析比对,最终发现了它们的共同点,即这些管线都是为输送进口原油而建设的,且出现穿孔的这部分管线很少被使用到,是属于一段死油管段,而发生穿孔的位置都在管线的底部,且曾多次发生穿孔,除了腐蚀穿孔的地方以外,管线的其他部分的壁厚是正常的。
2、站内管线取样测试及分析
为了能够进一步的确定输油站管线发生腐蚀穿孔的成因,我们对站内的管线进行了原油取样,并通过比较分析,来对样品做出了详细的检测与分析。
具体的测试方法与测试结果分析如下所示:
2.1 站内管线取样测试
取样点选取在发生腐蚀穿孔位置的附近处,结合输油站场现场实际情况,在两个输油站现场取样。
取出的试样为黄色的透明液体,含有少量杂质,该管段处为死油段且存在大量的水。
为了考察管道输送的油品性质,分别在两输油站取样口取样。
2.2 测试结果分析
根据取样的实际情况来看,输油站开孔后取出的样品含有大量水,证明了发生腐蚀穿孔的最主要原因就是管道中出现了明显的油水分层。
对取出的样品水含量进行分析,取样处管道内存留的积水已经达到了一定的数量。
综合其他的测试数据,认为小孔腐蚀也正是输油站内管线腐蚀的最主要原因。
根据样品的化验结果可看出,输油站发生腐蚀穿孔事故处取得的油样中氯离子含量为27 803.9 mg / l,远远高于标准含量。
根据孔蚀理论,氯离子是孔蚀的“激发剂”,而且随着介质中氯离子浓度的增加,孔蚀电位下降,使孔蚀更容易发生。
另外,输油站事故处取得的油样矿化度非常高,矿化度高的水导电率高,加速了电化学反应,加快了腐蚀速度。
且样品的化验结果中ph值为7.75,ph 值在中性左右最易发生小孔腐蚀。
总之,从这次的样品测试中我们可以看出,造成输油站管线腐蚀穿孔的原因是因为管线原本是输送的原油,而原油中含有较多的硫,再加上这些管线都不是经常被使用到,因为成为了死油管段,使得管线在硫离子长期的作用下侵蚀成孔,从而引发石油泄漏。
3、控制输油站内管线腐蚀穿孔的对策
在确定了输油站内管线的破坏成因后,就可以采取有针对性的措施来应对这一问题,做好防护工作,避免管线再次发生腐蚀穿孔,影响输油站的正常运行。
在此,笔者提出了几点对策建议,以供借鉴参考。
3.1避免死油段的产生,定期活动死油段。
死油区是造成管道内
腐蚀的最大威胁,如何减少并去除死油区至关重要,定期活动死油区是切实可行的办法。
建议对长期静置的死油段进行收集或排放,定期清扫所积聚的腐蚀产物,缩短死油腐蚀管道的时间,有效控制管道内腐蚀。
3.2控制影响管线发生小孔腐蚀的措施有:由于的孔蚀多半是由于含有氯离子的介质引起的,应尽可能地降低进口原油中氯离子的含量,可以通过脱盐处理来实现;腐蚀介质中,金属阳离子与侵蚀性卤化物阴离子共存时,氧化性金属离子对孔腐蚀起促进作用,应尽可能降低进口原油中这些金属离子的含量,可以通过脱盐处理来实现;一般高ph值一般不易引起腐蚀,因此适当提高ph值以减缓腐蚀;温度升高能严重降低孔蚀电位,易发生孔蚀并加剧腐蚀速度,为了减缓管线的内腐蚀,应降低适当温度。
3.3工艺改进。
控制管道内腐蚀最常用的方法是用有机、油溶性缓蚀剂。
一般的,这些缓蚀剂为具极性的碳氢化合物,容易在管内壁形成保护膜。
缓蚀剂的选择需要缓蚀剂厂家根据油品的性质进行选择。
流速较低时,不足以使铁垢、赃物、杂质等保留在油品中,容易在管道低洼处沉积,加之水的存在,就会形成局部腐蚀电池,引起并加速腐蚀。
油流的速度越快,其对积水的携带能力越强;油品流速越快,水膜的厚度减小也越明显,因此建议适当增大管输介质的流速。
流速范围的下限值应使腐蚀性杂质悬浮在管输介质中,使管道内积存的腐蚀性杂质降至最少。
由于在管段的内部腐蚀已经发生,夏季温度高时死油段受热膨胀容易引起压力升高,导致腐蚀
加剧。
建议适当降低运行压力,避免憋压、减缓腐蚀速度,从而使构件的服役寿命增加。
3.4改善油品性质。
进口原油中的腐蚀介质主要有盐、硫、氮、酸值及水等。
一般情况下,含硫原油及高含硫原油的腐蚀性普遍高于一般的低硫原油,故应进行脱硫处理。
因此,对于还未进入收油首站的油品,应首先取样分析判断输油站场输送的进口原油的油品性质,如果分析后证明进口原油与腐蚀性相关的参数含量超标,应该对油品进行处理,如脱盐处理、脱水处理、脱氮处理及脱硫处理等。
4、结语
本文通过分析某地区的几个输油站的实际管线故障情况,研究了导致管线发生腐蚀穿孔的主要成因为原油的长期侵蚀,并就如何应对和防治这一问题提出了一些建议。
希望通过本文能够为其他输油站发生同类管线故障问题时提供一些参考,以提高输油站的运行管理水平。
参考文献
[1]李勃.中原油田的腐蚀现状及提高腐蚀控制水平的途径,[j],油田地面工程,1991
[2]陈学群.硫化物夹杂对低碳钢孔蚀扩展的影响,[j],中国腐蚀与防护学报,2000。