国内二甲基二氯硅烷饱和酸水解工艺发展现状
二甲基二氯硅烷浓酸与恒沸酸水解方法比较

有机氯硅烷是整个有机硅化 学的支柱 , 大部分 的有机硅产 品( 如硅油、硅橡 胶、硅树脂) 由二甲基二氯硅烷水解制得 的 是 聚二 甲基硅氧烷( 基础聚合物 ) ,再与 调节 剂、交联剂 、封头剂 等加工制成 , 被认为是有机硅 的正规产品 。 聚硅氧烷具有很 多 优异的物理、化学性能 ,如耐高低 温性能、耐辐射性、耐氧化 性、高透气性、耐候性 、脱模性、憎水性 以及生理惰性等 。其 应 用遍 及航天、航空 、化工、冶金、乃至 人们 日常生活、医疗 保健各 个领 域 j 。 二 甲基二氯硅烷( 以下简称二甲) 水解常用的方法 有两种I: j J 种是恒沸酸水解 , 其水解方法是 用恒沸 酸( 2 %) 约 wt 循环并 1 通过水解二 甲基二氯硅烷使盐酸浓 度达 到饱和浓度 , 再通过蒸 馏脱吸装置获得气相氯化氢 , 该方法需要 消耗 大量的能量 以及 大量的稀盐酸 ; 另一种方法是浓酸水解 , 这种 水解 方法可 以直 接 获得 气相 氯化氢而无需蒸馏脱 吸装置 , 但是粗 水解物含氯量 高 ,进 一步中和会导致氯 的损 失和废 水污染 。文章 以 6 t 0 k/ a 二甲基 二氯硅烷 水解为例 , 对两种水解工 艺过程的耗能、设备 投 资、 占地投 资等进 行计算分析 ,浓酸 水解 方法 因其成本低、 能耗低 、流程短、废液排放少等 优点 , 将逐渐取代 恒沸酸水解 方法成为 聚硅氧 烷生产的新的发展趋势 。
21 0 0年 第 8 期
广
东
化
工
91
第 3 卷 总第 2 8期 7 0
Ⅵ v g c e .o n w.d h m c m
二 甲基 二氯硅烷浓 酸与恒 沸酸水解 方法 比较
周 艳 霞
( 岛科技 大 学 化 工 学 院 ,山东 青 岛 2 64 ) 青 60 2
二甲基二氯硅烷水解物

二甲基二氯硅烷水解物概述二甲基二氯硅烷水解物是一种常见的有机硅化合物,分子式为(CH3)2SiCl2(OH)2。
它具有无色液体的外观,是一种具有较高的表面活性的物质。
二甲基二氯硅烷水解物可以广泛应用于涂料、橡胶、塑料、纤维等行业,该化合物的水解反应能够产生硅醇和盐酸。
硅醇具有良好的粘附性和耐候性,因此二甲基二氯硅烷水解物被广泛用作粘接剂、双组分涂料的预处理剂以及表面处理剂等。
本文将详细介绍二甲基二氯硅烷水解物的性质、制备方法、应用领域以及安全注意事项。
性质•分子式:(CH3)2SiCl2(OH)2•分子量:163.04 g/mol•外观:无色液体•熔点:-48°C•沸点:135°C制备方法二甲基二氯硅烷水解物的制备方法可分为直接合成和间接合成两种。
直接合成二甲基二氯硅烷水解物可以通过二甲基氯硅烷和水反应得到。
反应过程中,水与二甲基氯硅烷发生水解反应,生成硅醇和盐酸。
然后,通过蒸馏和提纯等步骤,得到二甲基二氯硅烷水解物。
直接合成的反应方程式如下:(CH3)2SiCl2 + 2H2O → (CH3)2Si(OH)2 + 2HCl间接合成二甲基二氯硅烷水解物的间接合成方法是通过二甲基氯硅烷与乙醇发生反应,生成二甲基乙氧基硅烷。
随后,二甲基乙氧基硅烷与氯化氢反应,形成二甲基二氯硅烷。
最后,通过水解反应,得到二甲基二氯硅烷水解物。
间接合成的反应方程式如下:(CH3)2SiCl2 + 2C2H5OH → (CH3)2Si(OCH2CH3)2 + 2 HCl(CH3)2Si(OCH2CH3)2 + 2HCl → (CH3)2SiCl2 + 2C2H5OH (CH3)2SiCl2 + 2H2O → (CH3)2Si(OH)2 + 2HCl应用领域二甲基二氯硅烷水解物是一种常见的有机硅化合物,具有较多的应用领域:1.涂料:二甲基二氯硅烷水解物可用作高效粘接剂,提高涂料、油漆等的附着力和抗候性。
国内外有机硅行业市场现状与发展趋势
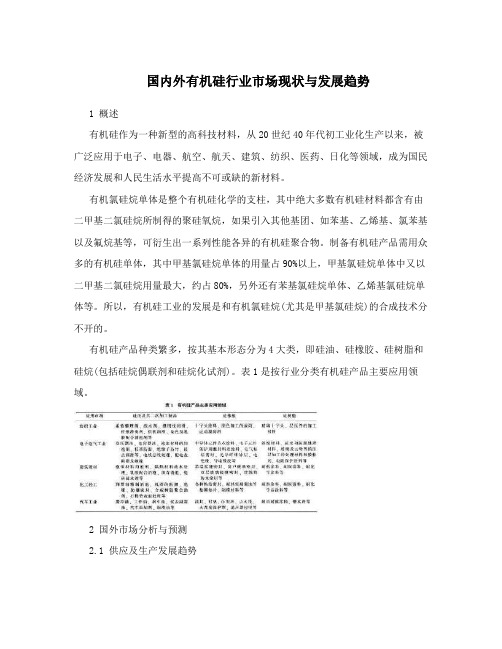
国内外有机硅行业市场现状与发展趋势1 概述有机硅作为一种新型的高科技材料,从20世纪40年代初工业化生产以来,被广泛应用于电子、电器、航空、航天、建筑、纺织、医药、日化等领域,成为国民经济发展和人民生活水平提高不可或缺的新材料。
有机氯硅烷单体是整个有机硅化学的支柱,其中绝大多数有机硅材料都含有由二甲基二氯硅烷所制得的聚硅氧烷,如果引入其他基团、如苯基、乙烯基、氯苯基以及氟烷基等,可衍生出一系列性能各异的有机硅聚合物。
制备有机硅产品需用众多的有机硅单体,其中甲基氯硅烷单体的用量占90%以上,甲基氯硅烷单体中又以二甲基二氯硅烷用量最大,约占80%,另外还有苯基氯硅烷单体、乙烯基氯硅烷单体等。
所以,有机硅工业的发展是和有机氯硅烷(尤其是甲基氯硅烷)的合成技术分不开的。
有机硅产品种类繁多,按其基本形态分为4大类,即硅油、硅橡胶、硅树脂和硅烷(包括硅烷偶联剂和硅烷化试剂)。
表1是按行业分类有机硅产品主要应用领域。
2 国外市场分析与预测2.1 供应及生产发展趋势随着需求的增加,国外有机硅单体的生产能力一直在不断的扩大,截止到2007年底,生产能力已达到319万t(以二甲基二氯硅烷计,以下同。
二甲基二氯硅烷经水解得到DMC和D4,通常按2t粗二甲基二氯硅烷得1tDMC或D4计)。
1由于有机硅单体生产以及后加工均为技术密集型,因此长期以来有机硅为相对垄断性行业。
主要生产企业有美国道康宁公司、美国迈图公司、德国瓦克公司、中国蓝星集团和日本信越公司,该五大公司产能合计占全球总产能的77%。
2007年世界有机硅市场竞争结构见图1。
道康宁公司是目前世界上最大的有机硅单体及材料的生产商,其有机硅单体的生产能力总计为86万t,a,占全球产能的27%,分别在美国、英国和日本建有生产装置,目前正在张家港与德国瓦克公司合作建设新的生产装置,2007年其有机硅业务的销售额为49.4亿美元,较2006年增长了13%(主要来自Hemlock Semiconductor Corp。
提高二甲水解反应效果及降低水解物残余氯的方法

工业技术幸福生活指南89幸福生活指南提高二甲水解反应效果及降低水解物残余氯的方法邓雅欣 曹利全 孙景阳 张向杰 范玉东唐山三友硅业有限责任公司 河北 唐山 063305;河北省有机硅新材料技术创新中心 河北 唐山 063305摘 要:就目前主流的二甲基二氯硅烷浓酸水解技术存在的水解物中残余氯偏高的问题,提出解决方案,同时提高二甲水解反应效果,包括改进一环路反应控制,采用连续水洗及吸附分离。
关键词:二甲基二氯硅烷;浓酸;水解物;残余氯引言二甲基二氯硅烷水解物是绝大部分有机硅材料的基础原料[1-2]。
二甲水解技术主要有两种方式,分别为恒沸酸水解与浓酸水解。
浓酸水解因具有低能耗,得到的HCl 气体可直接用于氯甲烷生产等优点,得到了广大有机硅厂家的青睐。
目前国内大部分厂家,均在逐步淘汰恒沸酸水解技术,采用浓酸水解技术[3]。
但浓酸水解技术也存在一个行业难题,水解物中残余氯含量偏高。
高氯含量的水解物对下游产品的生产控制及产品质量具有极大的影响。
本文主要从生产控制角度阐述几种既提高水解反应效果又降低水解物中残余氯的方法。
1、反应环节控制二甲基二氯硅烷浓酸水解反应主要发生在一环路,主要分为两步:(CH 3)2SiCl 2+H 2O →(CH 3)2Si (OH )2+2HCl(n+m )(CH 3)2Si (OH )2→n[(CH 3)2SiO]+mH-[(CH 3)2SiO]-OH+nH 2O氯硅烷的水解反应为可逆反应,我们可以根据勒夏特列原理剖析浓酸水解反应条件对反应的影响。
首先水解反应为吸热反应,因此温度越高越能向正反应方向进行,与此同时,反应温度的升高有利于加快反应速率。
其次是反应中的盐酸浓度对反应的影响。
常压下,盐酸浓度最高为36%-37%,而浓酸水解反应压力一般控制在0.15MPa-0.2MPa ,此时盐酸浓度可达到45%左右,盐酸浓度的升高不利于反应向正反应方向进行[4]。
再次,在工业生产上,连续大流量进料,物料能否与水充分接触,也将对反应速率起到决定性的影响。
二甲基二氯硅烷水解物

二甲基二氯硅烷水解物
二甲基二氯硅烷,简称DMDCCS,是一种常用的硅烷类添加剂,广泛应用于水处理、皮革制造和纤维加工领域等。
DMDCCS的水解物是一种耐热、耐水、抗氧化性强的非离子性表面活性剂,具有较好的润湿性能和生物降解性,因此被广泛应用于化妆品、洗涤剂、食品
添加剂等领域。
二甲基二氯硅烷分子结构简单,化学性质稳定,具有良好的加工性能和机械强度,因
此被广泛应用于在高强度环境下加工成各种形状的制品。
DMDCCS水解物是通过将二甲基二氯硅烷溶解在水中,使其发生水解反应,生成硅醇和二氧化硅。
硅醇基团能够吸附在各种
材料表面,形成保护膜,改善材料的性能。
DMDCCS水解物具有较强的润湿性能,能够降低表面张力,促进材料表面的吸附和扩散。
它的润湿性能与表面活性剂相比具有更短的时间,更高的效率和更好的持久性。
同时,它
的聚集数比表面活性剂的聚集数低,能够更好地保持润湿性能和稳定性。
DMDCCS水解物还具有优异的稳定性和生物降解性。
它在加工和使用过程中不易被分解,能够长期保持稳定性,并不会对环境和人体产生危害。
与此同时,它的分子结构简单,好
生物降解,因此有利于环境保护和可持续发展。
甲基二氯硅烷水解

甲基二氯硅烷水解
一、酸性水解
在酸性条件下,甲基二氯硅烷的水解反应通常涉及到催化剂的存在。
催化剂如硫酸、磷酸或铝硅酸盐等可以提高反应速率并降低活化能。
水解过程中,首先会生成相应的甲硅烷醇,这是一种非常活泼的中间体,可以进一步发生脱水或水合反应。
此外,由于酸的存在,可能会发生一系列副反应,如氯的取代、聚合以及与水的加成等。
二、碱性水解
在碱性条件下,水解反应通常涉及氢氧化钠、氢氧化钾或氢氧化铵等。
这种水解过程相对温和,避免了在酸性条件下可能发生的剧烈副反应。
在碱性水解中,甲硅烷醇会迅速与水反应生成硅烷醇盐和氢气。
硅烷醇盐可能进一步发生水解或脱氯等反应。
此外,由于碱性的调节,可以有效地控制副反应的发生。
三、歧化反应
甲基二氯硅烷的歧化反应是指同一物质在反应过程中发生自分解,产生两种不同的物质。
在某些条件下,甲基二氯硅烷可能会发生歧化反应,生成氯甲烷和硅仿。
这种反应通常需要在特定的温度和压力条件下进行,同时需要特定的催化剂。
- 1、下载文档前请自行甄别文档内容的完整性,平台不提供额外的编辑、内容补充、找答案等附加服务。
- 2、"仅部分预览"的文档,不可在线预览部分如存在完整性等问题,可反馈申请退款(可完整预览的文档不适用该条件!)。
- 3、如文档侵犯您的权益,请联系客服反馈,我们会尽快为您处理(人工客服工作时间:9:00-18:30)。
国内二甲基二氯硅烷饱和酸水解工艺发展现状有机硅材料的研究起始于19世纪中叶,1863年,法国化学家弗里德尔(C.Friedel)及克拉夫茨(J.M.Crafts)从SiCl4与ZnEt2出发,首先制得了含Si-C键的有机硅化合物(单体)SiEt4。
1874年,拉登堡(denburg)由Hg-Ph2与SiCl4反应制得了有机氯硅烷(PhSiCl3)。
1904年,英国化学家基平(F.S.Kipping)应用格利雅法(Grignard)合成了可水解的硅烷R n SiCl(4-n)在此期间,迪尔塞(W.Dilthey)将Ph2SiCl2水解制得Ph2Si(OH)2,并进而缩合制得六苯基环三硅氧烷(Ph2SiO)3,这是产生的第一个环状硅氧烷化合物,对推动聚硅氧烷的发展起到了重要的作用。
1941年E.G.Rochow发明了直接法合成R n H m SiCl4-(n+m)的技术,此法由于原料易得、工序简单、不用溶剂、时空产率高,且易实现连续化大生产等优点,因而一经面世便很快取代了格利雅法,奠定了有机硅工业化生产的基础。
至今它仍是国内外合成甲基氯硅烷的惟一方法;同时在合成乙基及苯基氯硅烷等方面也占有重要的地位。
1947年,通用电气公司成立有机硅部,首先采用直接法合成甲基氯硅烷工艺,从此有机硅工业得到了快速的发展,甲基氯硅烷合成、单体分离技术、二甲的水解工艺等也得到了快速发展。
1饱和酸水解工艺有机氯硅烷是整个有机硅化学的支柱,其中大部分有机硅聚合物是从二甲基二氯硅烷水解制得的二甲基硅氧烷出发而制得的。
到20世纪80年代,随着甲基氯硅烷及有机硅聚合物的生产技术成熟,甲基氯硅烷产量进一步扩大,其生产成本大幅度下降。
由于甲基氯硅烷产量及产品品种的增加,分离纯化技术的进步及聚合工艺的改进、环状及线型聚硅氧烷的开发与应用,推动了氯硅烷的水解工艺以更高的速度发展,其中,尤以二甲基二氯硅烷(以下简称二甲)的水解工艺为主,从恒沸酸水解工艺向饱和酸水解工艺发展。
二甲的饱和酸水解工艺是让二甲基二氯硅烷在饱和酸(在反应要求的温度和压力条件下盐酸处于饱和浓度)中闭路循环水解。
饱和酸水解所用的盐酸处于一种闭路循环状态,向系统中输入的只是二甲和水,输出物为水解物和气态氯化氢,跟恒沸酸水解工艺相比减少了盐酸输出时水解物的夹带量,故水解物的收率较高;联产氯甲烷时的能耗也大大下降。
饱和酸水解反应分多级进行,二甲在一级水解循环系统经过静态混合器反应和相分离器后,得到带压的气相氯化氢,气相氯化氢经过冷却除油、去杂质和干燥后,可以直接用于合成氯甲烷或用水吸收制得工业用盐酸;二甲由于是在饱和酸中水解,在一级水解循环系统中不能完全水解,可形成α,ω-二氯聚二甲基硅氧烷[(ClMe2SiO(Me2SiO)nSiMe2Cl)],没有充分完全水解的α,ω-二氯聚二甲基硅氧烷进入到后面的水解循环系统继续水解(多级水解),经过多级处理后完全水解,它们进一步发生自身或相互间的缩合反应,得到合格的硅氧烷(线性体、环体),自身的缩合反应得到环体、相互间的缩合反应得到线性体。
后面水解产生的稀盐酸作为前一级反应的补充水(稀盐酸浓度在水洗工序逐级下降)。
这种水解工艺的优势在于:固定投资少,省去了脱吸氯化氢装置;能耗低,避免了水解时冷却和盐酸脱吸时加热;无废水及废酸外排,进去的水洗水逐级向前输送,最终输送到一级反应循环系统用作二甲的反应补充水,产生的氯化氢直接用于合成氯甲烷或吸收生产工业盐酸;一级反应循环系统中的浓盐酸在水解环路形成闭路循环使用;水解收率高等。
国外从20世纪80年代开发并申请饱和酸水解工艺的专利,并在20世纪90年代工业化。
1985年GE最早申请了有关饱和酸水解工艺的专利,1991年道康宁申请了一步法制备硅氧烷中产出无水氯化氢专利;1995年Wacker 申请了制备聚二甲基硅氧烷工艺专利,该专利涉及两步水解;1998年罗地亚申请了有机卤硅烷水解制备聚有机硅氧烷的工艺专利,该专利采用三步或更多步水解工艺并且产生带压的气相HCl,2001年罗地亚又在上述专利的基础上申请专利:采用水煮工艺替代碱中和工艺;2001年日本信越公司申请了“连续的有机氯硅烷水解”专利,该专利连续的有机氯硅烷水解包括至少三段反应,该专利突出了零排放的饱和酸水解工艺。
国外申请的专利描述内容虽然不一样,但核心内容都是一样的:通过饱和酸水解工艺获得带压可以直接用于合成氯甲烷的气相氯化氢和满足市场需求的水解物产品。
2国内饱和酸水解工艺发展现状为了控制二甲基二氯硅烷饱和酸水解工艺的技术,Wacker、罗地亚等公司先后在中国申请了专利保护。
近年来,国内主要有机硅厂也相继申请了饱和酸水解工艺专利和与该工艺相关的技术专利。
近年来,国内掀起了甲基氯硅烷生产热潮许多省市在扩建、新建60、100、200kt/a规模的甲基氯硅烷生产厂,在浙江、江苏、江西、山东、山西、青海、四川和天津等省市都建立了一定规模的甲基氯硅烷生产厂,目前国内具有规模、产品牌号较多的甲基氯硅烷生产企业尤以新安化工和江西星火为主。
在国内新建的有机硅企业中,二甲基二氯硅烷饱和酸水解工艺被广泛应用,逐渐取代了恒沸酸水解工艺,饱和酸水解工艺在国内应用也变得成熟。
当前国内的饱和酸水解工艺技术路线虽仍有改进之地,但基本上是成熟可行的。
有些企业通过从国外引进饱和酸水解工艺技术,而有部分企业的饱和酸水解工艺是通过自主研发出来的,其中大部分已经申请了专利。
1985年4月吉林化学工业公司研究院申请了有机氯硅烷水解工艺专利:提出了等当量水水解有机氯硅烷的新工艺,其特征在于采用静态混合器为水解反应器,用饱和盐酸循环操作,水解是在压力下进行的;反应生成的氯化氢全部以气态形式回收,回收率达90%-98%;制得的水解物符合以后各工艺的要求。
有机氯硅烷连续水解新工艺,它的主体设备是反应器和相分离器。
其特征在于反应器是静态混合器,用有机氯硅烷体积的60-100倍(最佳为75倍)的常态下盐酸饱和溶液循环操作,有机氯硅烷水解所需的水以水或盐酸中的水加入,其量与有机氯硅烷中的氯的量之比为1.05-1.1:1,水解反应压力是在9.8-30×10Pa(最佳为16.3-21×10Pa),温度为20-50℃(最佳为35℃±5℃),物料在反应器中的总停留时间为10-150s(最佳25s±2s)。
2003年8月,江西星火有机硅厂申请了有机二氯硅烷的连续水解工艺专利:提出了一种有机二氯硅烷连续水解工艺,该工艺包括至少三级的循环水解反应系统。
每级水解单元包括混合反应器、内循环反应器(特别在第一级反应器,具有气-液相分离器之功效),外循环相分离器组成;每级水解反应单元相对独立,但各级水解单元之间是连续运行的,即上一级的水解聚有机硅氧烷连续进入下一级的水解反应单元,而下一级的水解盐酸又连续地补充到上一级。
该方法包括在第一级水解反应单元产生气相的无水氯化氢,该氯化氢可直接用于合成氯代烷烃,而氯代烷烃为合成有机氯硅烷的起始原料。
2006年9月,蓝星化工新材料股份有限公司申请了有机二氯硅烷的多级连续水解制备聚有机硅氧烷和气相氯化氢的方法专利:该专利是用至少三级的循环水解反应系统对有机二氯硅烷进行连续水解,每级循环水解反应系统又包括两循环单元:内循环单元、外循环单元;每级水解反应系统相对独立,上一级的水解聚有机硅氧烷连续进入下一级的水解反应系统,而下一级的水解盐酸又连续地补充到上一级;在上一级水解反应系统与下一级水解反应系统之间,上一级带压粗水解物L1进入脱气装置除去大量的游离的氯化氢,形成低氯含量的水解物L1′(氯的质量分数<10%)进入下一级反应器。
该专利降低了每一级水解反应后水解物中氯化氢气体含量,使生产容易操作、产品质量稳定、收率高,干燥的无水氯化氢气体压力也稳定。
2008年7月,山东东岳有机硅材料有限公司申请了一种甲基氯硅烷浓酸水解连续生产水解物的方法专利:该专利提出的方法包括下列步骤:一是甲基氯硅烷与浓酸在水解反应器中进行水解反应生成HCl和液体水解物,反应体系中水与甲基氯硅烷的量之比为0.12-0.18:1,反应温度35-45℃,操作压力0.2-0.4MPa,甲基氯硅烷与浓酸在水解反应器中停留时间40-60s;二是反应生成的氯化氢从水解反应器释放出来经冷凝器和除雾器处理后,得到用于氯甲烷生产的氯化氢气体;三是水解反应器中的液体水解物先后经一级相分离器和二级相分离器分离,分离出含油的酸性水溶液和酸性水解物;四是上述由一级相分离器和二级相分离器分离出的含油的酸性水溶液混合后经预热器进入水解反应器,进行循环反应操作。
分理出的酸性水解物进入蒸汽塔,蒸汽塔蒸汽用量与甲基氯硅烷加入量之比为0.12-0.18:1,进入蒸汽塔的酸性水解物经蒸煮后,分别经三级相分离器、四级相分离器分离,分离出的下层含油微酸性水再泵入二级相分离器循环使用,分离出的上层油相为低聚硅氧烷产物。
2008年12月,浙江恒业成有机硅有限公司申请了降低二甲基二氯硅烷水解气相氯化氢中杂质含量的工艺方法的专利。
2005年,新安化工与俄罗斯国家化学元素有机化学和技术研究所合作开发15kt/a二甲基二氯硅烷水解物生产工艺技术开发项目被杭州市科技局作为2005年首批杭州市国际合作项目之一立项。
当时国内二甲基二氯硅烷水解直接产生水解物和干燥氯化氢气体工艺技术还处于空白阶段。
合作项目于2006年8月建成投产。
目前,该工艺技术在新安化工已经运用成熟,水解收率和HCl的得率均接近理论值,无废酸和废水产生,既经济又环保,符合国家提倡的发展循环经济时代要求。
2008年,该项目通过了科技部国际科技合作计划办公室组织的专家组验收。
在这之后,新安化工运用该工艺技术在其控股子公司浙江开化合成材料有限公司建立了饱和酸水解工艺,取代了恒沸酸水解工艺;目前新安化工在公司本部正在建立饱和酸水解工艺Ⅱ期项目,计划于2009年7月建成投产,投产后新安化工的水解工艺全为饱和酸水解工艺,恒沸酸水解工艺在新安化工正式宣布退出历史舞台。
综上所述,虽然各个企业申请的专利描述内容不近相同,但核心内容都是一样的:水解反应都由多级反应循环系统组成,每级水解反应系统相对独立,二甲在一级水解循环反应系统在饱和盐酸中与水进行反应生成水解物和氯化每,其核心设备装置是二甲静态反应混合器、相分离器和HCl气体净化器。
核心技术是一级反应循环系统为带压的,控制反应器中的盐酸在反应要求的温度和压力条件下处于饱和浓度;二甲带入的氯元素全部以气态氯化氢形式外出;在一级反应循环系统没有完全水解的二甲进入后面反应系统继续水解;一级反应循环系统分离出来的HCl气体进行除油和除杂质;控制每一级反应循环系统中水解物带出的HCl量尤为关键,水解物带出的HCl量逐级降低,且每一级都有一个具体的控制参数,偏离此参数意味着水解反应失控;最后除去水解物中的Cl-。