萃取设备
萃取机原理

萃取机原理萃取机是一种常用的化工设备,广泛应用于化工、制药、食品等领域。
它通过将混合物与溶剂接触,利用不同物质在不同溶剂中的溶解度差异,实现对目标成分的分离和提取。
萃取机的原理可以简单概括为“溶质在两种不同相的分配系数不同”,即溶质在两种溶剂中的溶解度不同,从而实现分离和提取的目的。
首先,让我们来了解一下萃取机的基本构造。
萃取机通常由萃取塔、进料口、出料口、溶剂回收装置、搅拌器等部分组成。
其中,萃取塔是实现物质分离的关键部件,它内部通常填充有填料或者设有板式结构,以增加接触面积,促进混合物与溶剂的充分接触。
进料口用于加入混合物,出料口则用于收集提取后的物质。
溶剂回收装置则可以将溶剂进行回收利用,提高了设备的经济性。
在萃取机工作时,首先将混合物加入到萃取塔中,然后向其中加入适量的溶剂。
通过搅拌器的作用,混合物与溶剂充分接触,使得目标成分在两种不同相的溶解度产生差异。
随后,通过控制温度、压力等条件,使得目标成分在不同相中的分配系数达到最大化,从而实现目标成分的分离和提取。
萃取机的原理基于溶质在不同溶剂中的溶解度差异,因此选择合适的溶剂对于提高萃取效率至关重要。
通常情况下,溶剂的选择应考虑到目标成分在其中的溶解度高,同时对其他成分的溶解度低,以便实现目标成分的有效提取。
此外,溶剂的选择还应考虑到其对环境的影响,避免对环境造成污染。
除了溶剂的选择外,萃取机的操作条件也对提取效果有着重要影响。
比如,温度的选择可以影响溶质在不同相中的溶解度,从而影响分离和提取的效果。
此外,操作压力、搅拌速度等参数的选择也会对萃取效果产生影响。
总的来说,萃取机的原理是基于溶质在不同溶剂中的溶解度差异,利用这一差异实现对目标成分的分离和提取。
在实际应用中,合理选择溶剂、控制操作条件对于提高萃取效率至关重要。
希望本文对萃取机的原理有所帮助,谢谢阅读!。
萃取的基本装置

萃取的基本装置萃取是化学分离技术中一种重要的方法。
其原理是利用两种相互不溶的液体之间的分配性差异性,从混合溶液中分离出目标分子。
萃取的实现需要借助于一系列的基本装置,下面我们来一一了解这些基本装置,以期更好地理解萃取的原理与操作。
一、液-液两相萃取干燥装置液-液两相萃取干燥装置是萃取实验中常用的一种装置。
该装置主要由干燥管、橡胶塞和萃取漏斗三部分组成。
其操作原理是将混合物接在萃取漏斗上,使目标化合物从水相中提取到有机相中,然后在干燥管中对有机相进行脱水,获得目标化合物。
二、锥形瓶萃取干燥装置锥形瓶萃取干燥装置是适用于大量样品处理的一种基本装置。
其结构主要包括一个底盘、一只锥形瓶和一个牛头真空阀等组成。
该装置主要通过真空泵抽取加入样品的有机相,萃取出目标物,然后通过牛头阀控制有机相的流动,最后在锥形瓶中进行脱水。
三、旋转蒸发器旋转蒸发器是萃取过程中常用的一种去除有机溶剂的基本装置。
其主要部分包括蒸馏瓶、旋转马达、水浴锅、恒温水箱等。
其原理是将有机相溶剂倒入蒸馏瓶内,然后通过旋转马达使溶剂均匀蒸发,最后在水浴锅中进行加热并通过恒温水箱控制温度,从而获得目标化合物。
四、活性炭床活性炭床是一种常用的废气处理设备,在萃取实验中也有一定的应用。
其结构主要包括气相进口、气相出口、炭床以及废气处理系统等组成。
其原理是将有机废气通过炭床进行吸附和净化,获得干燥、清洁的废气。
以上就是萃取实验中常用的一些基本装置,不同的萃取方法需要不同的装置来实现。
通过对这些基本装置的了解,我们可以更好地理解萃取过程的原理,并在实验中更加的灵活应用。
萃取设备的原理

萃取设备的原理
萃取设备的原理是利用物质在两种互不相溶(或微溶)的溶剂中溶解度或分配系数的不同,使溶质物质从一种溶剂内转移到另外一种溶剂中的方法。
以下是几种常见的萃取设备及其工作原理:
1.微波萃取设备:该设备利用微波加热将原料中的有效成分进行分解、裂解、挥发等反应后,使水分子产生共振效应,从而使水分子被活化。
然后通过离心装置将水分子从水中分离出来,再经过过滤装置除去杂质后得到高浓度的萃取液。
2.超声波萃取设备:其利用超声波在液体中传播时产生的空穴效应和邻近效应来提取物质的一种方法。
3.逆流色谱法设备:其采用一种特殊结构的固定相来分离混合物中各组分的方法。
4.固相微萃取设备:其利用固体颗粒的表面官能团与溶剂之间的相互作用力来进行溶质的选择性提取的技术。
不同的萃取设备适用于不同的物料和环境,选择合适的萃取设备可以提高萃取效率、降低成本、减少对环境的污染等。
第五章萃取设备计算
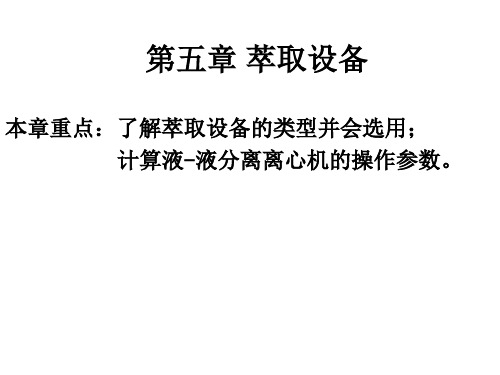
大于轻液出口内径:DL = 30 mm 同时应该小于DH = 44.1mm
• 可以选择37.4、39.0、41.1、43.8。
• 校核轻液和重液界面半径 rs
需要校核rs
rs
H rH 2 LrL2 H L
1000
43.2
2
880152
时,分界半径rS仅随重液出口半径rH而变
化。
rH ,rS
此时,界面外移,有利于轻液分离,反之
rH ,rS
界面内移,有利于重液分离。
重液出口半径rH的取值范围
重液出口半径rH的上限(最大值),当rS = rf 轻液混入重液出口.
rsrf rH 2H H rL L 2 L
可 r H 得 r f2 H L r L 2L H
– 液-固萃取:(浸取)(Leaching )。如用丙酮提 取菌丝体中的灰黄霉素。
– 液-液萃取: 溶剂萃取(溶媒萃取) – 双水相萃取
第一节 萃取设备
分段式萃取 混合过程和分离过程在分别在两个独立的设备
中进行;
连续式萃取: 若上述两过程在一个综合性设备中。
液-液萃取设备:
• 分段萃取 • 混合设备 混合罐
dm的液体在半径r处所受到的离心力dF:
dF 2 r dm dm 2r h dr dF 2h2r2dr
在r处圆筒面上所受压强
dp dF 2 rdr 2rh
• 对于轻液,在轻液出口至分界半径范 围内,积分得:
psdp p1
2
rs
L rL rdr
ps p122L(rs2rL2)
对于重液相,在重液出口至分界 半径范围内,积分得:
psdp p2
萃取过程及设备

萃取是利用系统中组分在溶剂中有不同的溶解度来分离混合物的单元操作,利用相似相溶原理,萃取有两种方式:液-液萃取,用选定的溶剂分离液体混合物中某种组分,溶剂必须与被萃取的混合物液体不相溶,具有选择性的溶解能力,而且必须有好的热稳定性和化学稳定性,并有小的毒性和腐蚀性。
如用苯分离煤焦油中的酚;用有机溶剂分离石油馏分中的烯烃;用CCl4萃取水中的Br2.固-液萃取,也叫浸取,用溶剂分离固体混合物中的组分,如用水浸取甜菜中的糖类;用酒精浸取黄豆中的豆油以提高油产量;用水从中药中浸取有效成分以制取流浸膏叫“渗沥”或“浸沥”。
虽然萃取经常被用在化学试验中,但它的操作过程并不造成被萃取物质化学成分的改变(或说化学反应),所以萃取操作是一个物理过程。
萃取是有机化学实验室中用来提纯和纯化化合物的手段之一。
通过萃取,能从固体或液体混合物中提取出所需要的化合物。
用溶剂从液体混合物中提取其中某种组分的操作称为液/液萃取。
萃取是利用溶液中各组分在所选用的溶剂中溶解度的差异,使溶质进行液液传质,以达到分离均相液体混合物的操作。
萃取操作全过程可包括:1.原料液与萃取剂充分混合接触,完成溶质传质过程;2.萃取相和萃余相的分离过程;3.从萃取相和萃余相中回收萃取剂的过程。
通常用蒸馏方法回收。
现以提取含有A、B两组分的混合液中的A组分为例说明萃取操作过程。
选用一种适宜的溶剂S,这种溶剂对欲提取的组分A应有显著的溶解能力,而对其它组分B应是完全不溶或部分互溶(互溶度越小越好)。
所选用的溶剂S称为萃取剂。
待分离的混合液(含A+B)称为原料液,其中被提取的组分A称为溶质,另一组分B(原溶剂)称为稀释剂。
萃取过程的三个步骤:(1)首先将原料液(A+B)与适量的萃取剂S在混合器中充分混合。
由于B与S不互溶,混合器中存在S与(A+B)两个液相。
进行搅拌,造成很大的相界面,使两相充分接触,溶质A由原料液(稀释剂B)中经过相界面向萃取剂S中扩散。
萃取设备的操作与控制概要
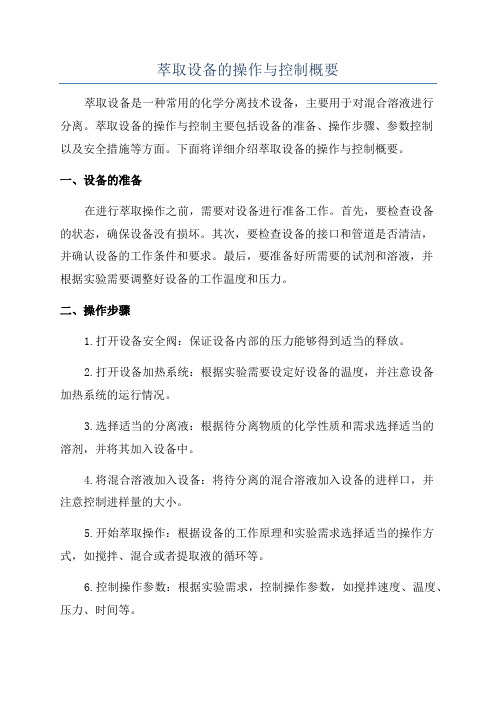
萃取设备的操作与控制概要萃取设备是一种常用的化学分离技术设备,主要用于对混合溶液进行分离。
萃取设备的操作与控制主要包括设备的准备、操作步骤、参数控制以及安全措施等方面。
下面将详细介绍萃取设备的操作与控制概要。
一、设备的准备在进行萃取操作之前,需要对设备进行准备工作。
首先,要检查设备的状态,确保设备没有损坏。
其次,要检查设备的接口和管道是否清洁,并确认设备的工作条件和要求。
最后,要准备好所需要的试剂和溶液,并根据实验需要调整好设备的工作温度和压力。
二、操作步骤1.打开设备安全阀:保证设备内部的压力能够得到适当的释放。
2.打开设备加热系统:根据实验需要设定好设备的温度,并注意设备加热系统的运行情况。
3.选择适当的分离液:根据待分离物质的化学性质和需求选择适当的溶剂,并将其加入设备中。
4.将混合溶液加入设备:将待分离的混合溶液加入设备的进样口,并注意控制进样量的大小。
5.开始萃取操作:根据设备的工作原理和实验需求选择适当的操作方式,如搅拌、混合或者提取液的循环等。
6.控制操作参数:根据实验需求,控制操作参数,如搅拌速度、温度、压力、时间等。
7.定期采集样品:根据实验需求,在适当的时间点采集样品以进行分析检测。
8.完成操作工作:根据实验结束条件,完成萃取操作并关闭设备。
三、参数控制控制萃取设备的参数可以有效地提高萃取效果和实验结果的准确性。
常见的参数控制有以下几个方面:1.温度控制:根据所需的操作温度,设置设备的加热系统,并通过温度传感器实时监测设备的温度。
根据实验需求,可以进行温度的调节和控制,以保持温度的稳定性和准确性。
2.搅拌控制:通过调节搅拌速度和时间,可以有效地提高混合均匀度和分离效果。
搅拌控制可以通过设备的搅拌器或搅拌电机来实现,并可以根据实验需求进行调整。
3.压力控制:根据设备的工作原理和操作要求,对设备的压力进行控制。
如压力传感器可以实时监测设备的压力,并根据实验需求进行调节和控制。
4.时间控制:萃取操作中的循环时间、反应时间、提取时间等,都可以通过设备的计时器进行控制。
萃取设备_精品文档

萃取设备1. 引言萃取设备是化学工程领域中常用的一种设备,用于从混合物中分离出某种物质。
萃取是一种基于不同物质在不同溶剂中溶解度不同的原理进行分离的方法。
萃取设备广泛应用于制药、化工、食品等行业中,具有很高的分离效率和操作灵活性。
2. 萃取设备的原理萃取设备的基本原理是利用两种或多种溶剂的相互溶解性差异,使得要分离的物质在某一种溶剂中溶解度更高,从而实现分离的目的。
常见的萃取设备包括萃取塔、萃取柱、液-液萃取装置等。
2.1 萃取塔萃取塔是一种常用的分离设备,通常由一个或多个填料层和进料喷嘴组成。
原料混合物从塔顶部进入,然后通过填料层,与溶剂进行充分接触。
在接触的过程中,物质会根据其在不同溶剂中的溶解度分配到不同的相中。
随着物质的分配平衡的达成,相中的物质逐渐分离出来。
2.2 萃取柱萃取柱是另一种常见的萃取设备,通常由填料料床和进出料口组成。
原料混合物从柱顶部进入,经过填料料床,与溶剂进行接触和混合。
不同物质在接触过程中根据其在溶剂中的溶解度分配到不同的相中,从而实现分离。
2.3 液-液萃取装置液-液萃取装置是一种更为复杂的萃取设备,常用于分离难分离的物质。
它包括两个以上的相分离器和循环泵。
原料混合物通过循环泵进入相分离器,与溶剂进行接触并混合,然后经过相分离器进行液-液分离。
随后,得到的上层液相和下层液相分别排出。
3. 萃取设备的应用萃取设备广泛应用于各个行业中,下面以制药、化工、食品三个行业为例,介绍其在实际应用中的具体情况。
3.1 制药业中的应用在制药业中,萃取设备常用于从天然植物中提取有效成分,如植物提取物、草药提取物等。
以植物提取物为例,制药企业可以利用选择性溶解性差异,将植物中的有效成分分离出来,进一步提炼和纯化,以用于制药领域。
3.2 化工业中的应用在化工行业中,萃取设备常用于从化工废水中回收和处理有价值的化合物。
一些有机溶剂和废水中的有机物具有溶解度差异,通过萃取设备可以将有机物从废水中分离出来,实现资源的回收和废水的处理。
直观演示7大萃取设备的结构和原理

直观演示7大萃取设备的结构和原理萃取(Extraction)是分离液体混合物的一种单元操作,依据液体混合物中各组分在溶剂中溶解度的差异分离液体混合物,俗称抽提。
萃取设备——离心萃取机————混合·沉降萃取器————脉冲筛板萃取塔————筛板萃取塔————填料萃取塔————往复筛板萃取塔————转盘筛板萃取塔——萃取设备简介萃取设备又称萃取器,其作用是实现两液相之间的质量传递。
对萃取设备的基本要求是使萃取系统的两液相之间能够充分混合、紧密接触并伴有较高程度的湍动;同时使传质后的萃取相与萃余相能够较完善的分开。
萃取设备的种类很多,按两相接触方式,可分为逐级接触式和连续接触式;按形成分散相的动力,可分为无外加能量与有外加能量两类,前者只依靠液体送入设备时的压力和两相密度差在重力作用下使液体分散,后者则依靠外加能量用不同的方式使液体分散;此外,根据两相逆流的动力不同,可分为重力作用和离心力作用两类。
常用的萃取塔型①转盘塔在工作段中,等距离安装一组环板,把工作段分隔成一系列小室,每室中心有一旋转的圆盘作为搅拌器。
这些圆盘安装在位于塔中心的主轴上,由塔外的机械装置带动旋转。
转盘塔结构简单,处理能力大,有相当高的分离效能,广泛应用于石油炼制工业和石油化工中。
②脉动塔在工作段中装置成组筛板(无溢流管的)或填料。
由脉动装置产生的脉动液流,通过管道引入塔底,使全塔液体作往复脉动。
脉动液流在筛板或填料间作高速相对运动产生涡流,促使液滴细碎和均布。
脉动塔能达到更高的分离效能,但处理量较小,常用于核燃料及稀有元素工厂。
③振动板塔将筛板连成串,由装于塔顶上方的机械装置带动,在垂直方向作往复运动,借此搅动液流,起着类似于脉动塔中的搅拌作用。
萃取塔设计主要是确定塔的直径和工作段高度。
先从液体流量除以操作速度,得出塔截面,算出塔径。
然后根据塔的特性以及物系性质和分离要求,确定传质单元高度和传质单元数,最后两者相乘即得塔的工作段高度。
- 1、下载文档前请自行甄别文档内容的完整性,平台不提供额外的编辑、内容补充、找答案等附加服务。
- 2、"仅部分预览"的文档,不可在线预览部分如存在完整性等问题,可反馈申请退款(可完整预览的文档不适用该条件!)。
- 3、如文档侵犯您的权益,请联系客服反馈,我们会尽快为您处理(人工客服工作时间:9:00-18:30)。
液-液萃取与萃取设备1.液-液萃取1.1概述液-液萃取亦称溶剂萃取,是在液体混合物中加入与其不完全相溶的液体为溶剂,造成第二相,利用原液体中的某些成分在两液相之间不同的分配关系将有效成分分离开。
这是一个液-液之间的传质过程。
液-液萃取具有处理能力大、分离效果好、回收率高、可连续操作以及易于自动控制等特点。
在石油化工、湿法冶金、原子能工业、生化、环保、食品和医药工业等领域得到广泛的应用。
目前萃取技术的发展还依赖于实验室的研究,从中试规模摸索工艺条件,然后再放大到工业装置。
国外已有专业生产萃取设备的公司,并提供可做实验的小型实验装置,以实验提供设计参数,给用户提供整套技术服务。
我国至今为止尚无一家专业制造萃取设备的企业,萃取设备仍依赖专业研究机构的特殊设计以应用于特定体系。
1.2萃取应用场合蒸馏与萃取的区别:蒸馏:是利用混合液中各组分的挥发度不同来达到分离的目的;萃取:是利用某组分在不同溶剂中溶解度的差异来达到分离的目的。
液-液萃取主要用于以下几种情况:A.溶液中各组分的沸点非常接近,即各组分的相对挥发度接近于1,用蒸馏方法很不经济;B.溶液中含有大量的低沸点的物质,或者低沸点组分的汽化潜热较大,用蒸馏方法回收时,需要消耗的大量的热能;C.溶液中某些组分形成恒沸物,用蒸馏方法难以分离;D.溶液中要回收的组分,属于热敏性物质,蒸馏时容易分解、聚合或发生其他化学变化;E.提取很稀溶液中有价物质,如提取液中的铀、麻黄草浸煮液中的麻黄素;F.分离极难分离的金属,如锆与铪、钽与铌等。
1.3影响萃取的主要因素A.溶剂的选择;溶剂选择一般考虑以下因素:(1).溶剂的选择性:表征溶剂的分离能力,类似于蒸馏中的相对挥发度。
选择性系数等于1,没有分离效果。
选择性系数必须大于1。
(2).分配系数:分配系数与溶质浓度、温度有关。
(3).萃取容量:萃取容量要大,可以减小溶剂的循环量。
(4).溶剂的溶解度:溶剂的溶解度要小,以降低溶剂的损耗。
(5).溶剂的物性:主要是密度与界面张力。
需要有适当的密度差及界面张力。
B.萃取设备的选择萃取过程实际上是一个相际平衡的过程。
(1).将一相分散到另一相中,形成很大的相界面面积;(2).在分散相液滴和连续相接触时,发生传质,并使传质过程进行到接近平衡的程度;(3)分散相液滴的凝并。
在萃取过程中液滴的这种“分散-凝并-再分散”的过程,就使得“分散-传质-凝并”,“再分散-传质-凝并”过程不断地循环。
传质机理过程对萃取设备的性能具有重要的影响。
2.萃取设备的选择对于一个液液萃取过程来说,选择合适的传质设备,是一件比较重要的工作,但也是比较困难的工作。
各种传质设备具有不同的特性,而且萃取过程及萃取系统中各种因素的影响也是错综复杂的。
设备的选型应考虑系统的性质和设计特性:(1).系统所需要的理论级数:为完成一定的分离要求,萃取设备必须具有所需要的理论级数。
所需要的理论级数较少,如2-3级,一般无机械搅拌的设备可以选用,如填料塔、筛板塔等。
所需要的理论级数较多,如5级以上,就必须选用具有外加能量的萃取设备,如转盘塔、振动塔。
当需要更多的理论级数时,如稀土萃取过程往往需要几十级,甚至几百级,此时一般只能选用混合澄清器。
(2).处理量:设备的处理量往往由生产任务所决定。
所要求的处理量大,可选用转盘塔、筛板塔,Kuhni塔;处理量较小,可选用填料塔,脉冲筛板塔、脉冲填料塔等。
(3).停留时间:在萃取操作中如果系统对停留时间有要求时,如抗菌素生产中,发酵液的萃取,往往要求在萃取设备中停留时间较短,此时可选用离心萃取器。
如果系统伴有较慢的化学反应,要求有足够的停留时间时,采用混合澄清器也是合适的。
(4).相比:系指分散相和连续相的流量比,对于塔式萃取设备,为了产生较大的接触面积,通常将流量大的一相作为分散相。
相比过大,非搅拌型的塔不宜选用,而应该选用搅拌型的塔,混合澄清器基本上不受相比大小的影响。
(5).系统的物理性质:系统的物理性质对萃取设备的选择有密切的关系。
两相密度差大可选用塔式萃取器;反之应选用离心萃取器;系统的界面张力大,粘度高,则应考虑有外加能量的萃取设备,以保证较大的接触面积;界面张力小,可选用填料塔,若系统具有腐蚀性的,则应优先考虑填料塔。
(6).设备与操作、维修费用:选用萃取设备时,除需要考虑设备的制造费用外,还要考虑设备的操作和维修费用。
包括设备内的物料存储量,尤其是溶剂的存储量、溶剂的回收费用及溶剂的损耗。
(7).设备的安装场地:设备的安装场地应根据实际情况确定,场地面积有限应选用塔式设备;若场地高度有限,则可考虑混合澄清器。
3.涡轮搅拌萃取塔涡轮搅拌萃取塔是一种装有多孔板的机械搅拌型萃取设备。
Kühni塔是典型的涡轮萃取塔,也是目前应用最为成功的一种涡轮萃取塔,该塔于20世纪60年代由瑞士Kühni 公司提出,70~80年代在欧洲得到广泛的工业应用。
涡轮塔的结构搅拌室主要部件:A.安装在中心轴上的涡轮混合器。
B.用于在垂直方向上隔开各个隔室的固定孔板。
涡轮混合器是一个双入口的径向流动叶轮,以产生涡轮萃取塔隔室的特征流型。
涡轮搅拌萃取塔的优点:A.级效率高;B.相比大;C.结构简单;D.操作方便;E.处理量大;F.适应性强。
涡轮萃取塔是液-液萃取中的重要设备,可以在分离要求较高的场合中使用,尤以其结构简单、操作方便、处理量大、适应性强为特点,因而受到人们的普遍关注。
涡轮搅拌萃取塔已经在萃取工业中得到了广泛的应用。
世界上已经有超过3000个涡轮搅拌萃取塔用于实验室研究、工艺过程开发和工业生产,直径从6cm 的小型实验塔,直至5.4m的工业塔。
涡轮萃取塔应用的工业领域有:石油化工工业用于芳烃抽提和从原油馏分中萃取润滑油;制药和化工工业中用于从水溶液萃取维生素,苷,生物碱及其他有机物;从水溶液中萃取醋酸;回收和净化N,N-二甲基苯甲酸胺、吡啶、二甲亚砜、二氯苯等溶剂;萃取香草类化合物和从糖浆中萃取柠檬酸等;湿法冶金工业用于从镍、钴中回收锌,从浸出液和粗磷酸液中回收铀;环境工程废水处理工业用于从废水中萃取除酚和硝基苯等有机物,化纤生产废水除锌等。
4.研究成果的实施华东理工大学化工学院长期从事着萃取工艺及装置的研究,先后研究过填料萃取塔、转盘塔、改进型转盘塔、偏心转盘塔、立式混合澄清塔、涡轮搅拌萃取塔等多种萃取设备,并取得许多成果。
目前在国内已有多台不同直径的萃取塔在石油化工、精细化工、医药工业中得到应用。
实验室萃取塔:Ф75mm-300mm 处理量:10kg/h-200kg/h工业萃取塔的设计规模:Ф500mm-1.8m 处理量:500kg/h-16000kg/h目前萃取技术的发展还依赖于实验室的研究,从中试规模摸索工艺条件,然后再放大到工业装置。
由于萃取系统涉及的领域范围之大,到目前为止还没有一套完整的设计方法可不依赖于实验数据进行放大的。
随着这种高效率的涡轮搅拌萃取塔的不断被应用,我们对该塔进行了大量的并逐步深入的研究。
包括对塔的几何结构、塔内的流体流动和传质特性进行研究。
通过研究,基本掌握了涡轮搅拌萃取塔设计方法及塔内构件的几何尺寸参数。
建立了传质与返混的通用性数学模型,为工业装置的设计提供可靠的实验数据与数学模型。
萃取塔方面的部分研究论文:(1).倪信娣,章寿华,于筛成,苏元复等. 糠醛-润滑油系统的流体力学和传质研究.石油炼制【J】.1981 ,(2)33-37(2).诸富根,倪信娣,于筛成,苏元复等.转盘塔与改进型转盘塔.化学工程【J】.1983(3)1-7(3).F.G.Zhu,X.D.Ni,S.C.Yu,Y.F.Su., A MODIFIED ROTATING DISKCONTACTOR WITH WIRE MESH COALESCERS. ISEC’83 SESSION TITLES. 1984(80)238. 115-123(4).S.H.ZHANG,S.C.YU,Y.F.SU.,A Model Liq.-Liq.Extraction ColumnPerformance-The Influence of Drop Size Distribution on Extraction Efficiency.Can.J.Chem.Eng. 1985,63(2), 212-226(5).于筛成,倪信娣,周永传等.矩鞍形填料萃取塔的研究.化工装备技术【J】.1985(6)1-8(6).毛向荣,于筛成,朱志华等. 涡轮搅拌萃取塔的模型研究.化工装备技术【J】.2007,28(3):23-28(7).于筛成,毛向荣等.机械搅拌类萃取塔.专利号:ZL200620046646.4 授权日期07.10.17萃取塔应用实例:麻黄素生产-转盘塔、填料塔紫杉醇生产-涡轮搅拌萃取塔柠檬酸生产-转盘塔、涡轮搅拌萃取塔香兰素生产-涡轮搅拌萃取塔精细化工生产-涡轮搅拌萃取塔废水处理-涡轮搅拌萃取塔部分工业化应用单位:内蒙古通辽市爱民制药厂内蒙古赤峰市赤峰制药厂新疆制药厂新疆和硕麻黄素厂新疆巩留麻黄素厂河南新乡有机化工厂河南焦作鑫安有限公司浙江嘉兴中华化工集团有限公司上海酵母厂浙江嘉兴中华化工集团中石油吉化香兰素厂。