设计潜在失效模式及效应分析.
设计失效模式及效应分析(DFMEA)

6
Development of a Design FMEA 设计FMEA的开始 设计 的开始
First Step of DFMEA: IDENTIFY DESIGN INTEND 第一步 : 确定设计意图 “Listing of what design is expected to do and what is expected not to do” “列出设计期望做什么和不期望做什么?
FMEA Date (Orig.) ______(Rev.)____ehicle(s)____________________
7
8 Core Team__________________________________________________________________________________________________________________________
Subsystem Level
Frame Function: –Provides stable attachment for seat support Potential Failure Mode(s) Structural failure seat support Excessive deflection of seat support Function: –Provides pleasing appearance Potential Failure Modes(s) Finish (shine)deteriorates Paint chips
Component Level Upper Frame
DFMEA(设计失效模式与效应分析)-20121123

※ RPN(風險順序數):計算並記錄糾正後的RPN值的結果。
14
設計FMEA分析步驟
15
設計FMEA嚴重度評估標準
16
設計FMEA發生率評估標準
17
設計FMEA難檢度評估標準
18
設計FMEA改善對策提出時機
The timing to provide solution / 提出改善對策之時機
以利追蹤
※ Planning Stage(設計階段):填上依據目前所進行分析標的物所處之開發階段 ※ Design Responsibility (設計責任):填入負責的設計與開發之工程師全名
※ Prepared By(編制者):填入負責編制DFMEA的工程師的姓名
※ Part Name/Program(系統、子系統或零部件的名稱及編號):填入適當的分析級別並
12
設計FMEA分析表說明(Ⅲ)
※ POTENTIAL CAUSE(S) / MECHANISM(S) OF FAILURE(失效的潛在原因或機理) :填入每一
個失效模式的所有可以想到的失效原因或失效機理。
※ DESIGN CONTROLS(現行設計管制):填入已經完成或承諾要完成的預防措施、設計確認
DFMEA(設計失效模式與效應分析)
Design Failure Mode and Effect Analysis
1
什麽是FMEA ?
※
FMEA是一種系統方法,使用制式表格及問題解決
方法以確認潛在失效模式及其效應,並評估其嚴重度、 發生度、難檢度(探測/偵測)及目前管制方法,從而計算
風險優先指數(RPN),最後採取進一步改善方法,如此
持續進行,以達防患失效模式及效應發生於未然
失效模式与效应分析

上失效模式与效应分析(failure modes and effects analysis, FMEA)¾又名:潜在失效模式与效应分析(PotentialfaiIUre modes and effects analysis),失效模式、影响与危害性分析(failure modes, effects, and criticality analysis, FMECA)A概述失效模式与效应分析(FMEA)是一步步地识别在设计、生产或装配过程以及最终产品和服务中全部可能失效的一种方法。
“失效模式”意思是可能产生某些失效的方式或模式。
失效是任何的错误或者缺陷,尤其是那些影响顾客的、潜在的或实际的。
“效应分析”指的是争论这些失效的后果或效应。
这些失效依据他们结果的严峻性、发生的频率以及被检测到的简洁度优先排序。
FMEA的目的是从有最高的、优先级的开头来实行行动消退或者削减失效。
FMEA通常把当前有关失效的学问以及所实行的行动文档化,用于持续的改进。
FMEA用于设计中预防失效的发生,之后又用于正在进行的过程操作中的掌握。
抱负地说, FMFA 开头于产品的概念设计阶段,贯穿于产品或服务的整个生命期中。
FMEA在19世纪40年月最早被应用于美国的军队中,然后在航空和自动化行业得到进一步的进展应用。
一些行业已经把FMEA的标准正规化,下面是一个综述。
在实行FMEA过程之前,需通过其他的参考资料和培训,从而学习更多关于组织和行业的标准和具体的方法。
>适用场合•当一个产品或服务正在被设计或者重复设计时,在QFD之后或者在设计完成之后;•当以全新的方式应用现有的过程、产品或服务时;•在形成新的或改进过程的掌握方法以前;•当对现有的过程、产品或服务方案改进的时候;•当分析现有的过程、产品或者服务失效缘由时;•贯穿于过程、产品或者服务的生命期中定期进行检查。
>实施步骤这只是一个也许的过程,具体的细节则随着组织或行业的标准而有所变化。
设备潜在失效模式及效应分析

设备潜在失效模式及效应分析设备潜在失效模式及效应分析(FMEA)是一种系统性的方法,用于识别设备潜在的失效模式及其可能的影响。
这种方法可以帮助组织预测设备可能出现的问题,从而采取预防性措施来避免这些问题的发生。
在进行设备潜在失效模式及效应分析时,首先需要确定设备要分析的功能或特性。
然后,对于每一个功能或特性,需要识别所有可能的失效模式。
失效模式是指设备在执行其功能或特性时可能发生的故障方式。
一旦失效模式被确定,下一步就是对每种失效模式进行评估,确定其可能的影响。
这些影响可以涉及到安全、质量、生产效率、环境和成本等方面。
通过对失效模式和其影响进行分析,可以确定哪些失效模式是最严重的,从而可以优先采取措施来预防或减轻这些失效的影响。
设备潜在失效模式及效应分析对于预测设备可能出现的故障非常有益。
通过这种分析,组织可以采取有效的措施来避免或减少设备故障可能造成的负面影响。
这不仅可以提高设备的可靠性和可用性,还可以降低维护成本,提高生产效率,保护员工安全,保护环境等。
总之,设备潜在失效模式及效应分析是一种重要的工具,可以帮助组织预测设备可能的故障,并制定相应的预防措施。
这种分析方法不仅可以提高设备的可靠性和可用性,还可以降低维护成本,提高生产效率,保护员工安全和环境等方面都具有重要作用。
设备潜在失效模式及效应分析(FMEA)是一种系统性的方法,用于识别设备潜在的失效模式及其可能的影响。
这种方法可以帮助组织预测设备可能出现的问题,从而采取预防性措施来避免这些问题的发生。
在进行设备潜在失效模式及效应分析时,首先需要确定设备要分析的功能或特性。
然后,对于每一个功能或特性,需要识别所有可能的失效模式。
失效模式是指设备在执行其功能或特性时可能发生的故障方式。
失效模式的识别可以通过对设备的历史数据、技术文档、专家意见等进行调研,以找出设备可能存在的各种故障情况。
一旦失效模式被确定,下一步就是对每种失效模式进行评估,确定其可能的影响。
FMEA讲义
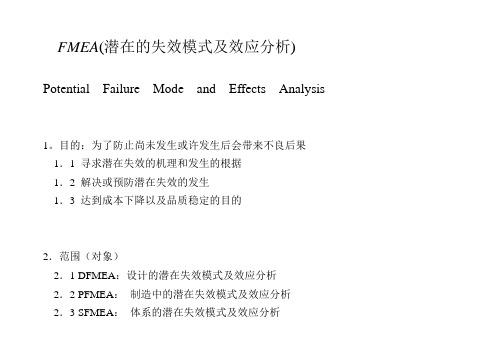
FMEA(潜在的失效模式及效应分析) Potential Failure Mode and Effects Analysis1。
目的:为了防止尚未发生或许发生后会带来不良后果1.1 寻求潜在失效的机理和发生的根据1.2 解决或预防潜在失效的发生1.3 达到成本下降以及品质稳定的目的2.范围(对象)2.1 DFMEA:设计的潜在失效模式及效应分析2.2 PFMEA:制造中的潜在失效模式及效应分析2.3 SFMEA:体系的潜在失效模式及效应分析3.定义3.1 潜在失效后果:是指失效模式对顾客的影响,从这一角度讲,顾客可以是下一道工序,后续工序或工位/代理商/车主。
4.研究方法计算公式SxOxD=RPNS(severity): 严重度O(occurrence):频度D(detection):探测度RPN:风险顺序数5.DFMEA设计中的失效模式与效应分析S--严重度数建议评价准则a)严重度是潜在失效模式对顾客的影响后果的严重程度的评价指标。
b)后果严重度数一般只能通过修改设计来实现。
c)非三大汽车厂的供应商一般从第八级开始计算。
O-- 频度数建议评价准则a)频度是指具Array体的失效起因/机理发生的频率。
b)频度的分级规则可以是采用可能的失效率来估计(参考类似产品),也可以采用统计数据如统计制程控制SPCD-- 不易探测度数的评价准则a)不易探测度:是指用现行的设计控制方式来发现失效的可能性的评价指标。
DFMEA运用流程:(1)对设计过程采用流程分析(2)对每一动作进行潜在失效的分析(针对高风险进行FMEA)(3)对各个设计作业的潜在失效进行S。
O。
D的级数判定,并提出支持理由。
(4)通过S。
O。
D级数值计算RPN值,并依大小进行排序(5)RPN的判定规则a)根据公司实际情况确定当RPN值达到一个限度时进行处理,如: RPN≧30b)将所有的RPN值按柏拉图进行排列,比如排在前10位的要处理(6)针对要处理的RPN项目采取相应的纠正预防措施,达到RPN降低的目的(7)重新排列RPN,执行(5)/(6)。
FMEA、DFMEA、PFMEA学习资料
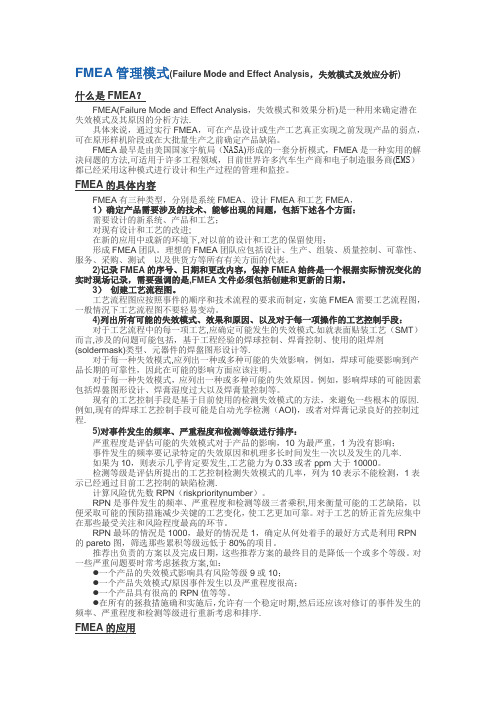
FMEA管理模式(Failure Mode and Effect Analysis,失效模式及效应分析)什么是FMEA?FMEA(Failure Mode and Effect Analysis,失效模式和效果分析)是一种用来确定潜在失效模式及其原因的分析方法.具体来说,通过实行FMEA,可在产品设计或生产工艺真正实现之前发现产品的弱点,可在原形样机阶段或在大批量生产之前确定产品缺陷。
FMEA最早是由美国国家宇航局(NASA)形成的一套分析模式,FMEA是一种实用的解決问题的方法,可适用于许多工程领域,目前世界许多汽车生产商和电子制造服务商(EMS)都已经采用这种模式进行设计和生产过程的管理和监控。
FMEA的具体内容FMEA有三种类型,分別是系统FMEA、设计FMEA和工艺FMEA,1)确定产品需要涉及的技术、能够出现的问题,包括下述各个方面:需要设计的新系统、产品和工艺;对现有设计和工艺的改进;在新的应用中或新的环境下,对以前的设计和工艺的保留使用;形成FMEA团队。
理想的FMEA团队应包括设计、生产、组装、质量控制、可靠性、服务、采购、测试以及供货方等所有有关方面的代表。
2)记录FMEA的序号、日期和更改内容,保持FMEA始终是一个根据实际情況变化的实时现场记录,需要强调的是,FMEA文件必须包括创建和更新的日期。
3)创建工艺流程图。
工艺流程图应按照事件的顺序和技术流程的要求而制定,实施FMEA需要工艺流程图,一般情況下工艺流程图不要轻易变动。
4)列出所有可能的失效模式、效果和原因、以及对于每一项操作的工艺控制手段:对于工艺流程中的每一项工艺,应确定可能发生的失效模式.如就表面贴装工艺(SMT)而言,涉及的问题可能包括,基于工程经验的焊球控制、焊膏控制、使用的阻焊剂(soldermask)类型、元器件的焊盤图形设计等.对于每一种失效模式,应列出一种或多种可能的失效影响,例如,焊球可能要影响到产品长期的可靠性,因此在可能的影响方面应该注明。
DFMEA-和-DVP含义

DFMEA 和DVP&RDFMEA (设计潜在失效模式与效应分析) 和DVP&R (设计确认计划和报告)设计潜在失效模式与效应分析(DFMEA) 是一种评估耐牢度对抗潜在失效的设计的方法,也是汽车公司要求的新产品开发过程的一个组成部分——产品质量先期策划和控制计划(APQP)的关键部分。
在设计DFMEA的时候,必须要考虑从过去测试经验和行动中得到的教训,这些教训用来在今后将风险最小化。
设计风险在历史数据和工程分析的基础上进行评估。
DFMEA在常规流程的严重程度、发生频率和探测能力的基础上区分行动计划的优先次序。
设计确认计划和报告是以设计潜在失效模式与效应分析(DFMEA)为基础。
它是一个工作文件,帮助在验证开发过程中管理人员,同时它也是确保产品可靠性和达到客户要求的一个工具。
它是汽车公司要求的新产品开发过程的一个组成部分——产品质量先期策划和控制计划(APQP)的关键部分。
样件控制计划和DVP&R(设计验证计划&报告)有什么区别样件控制计划是描述对样件的尺寸、功能和性能检验的控制要求;DVP&R也是描述对设计验证对象,也就是样件的检验要求请问这两个之间有什么具体区别呢?还有,样件也分为手工样件、OTS样件等,是都需要分别编制样件控制计划吗我个人觉得控制计划重点在于制造前的控制缺陷的产生,而DVP是事后的对于产品的验证是否符合图纸或规范。
样件控制计划要说明你的产品如何生产,如何检验(包括性能,功能,外观和日常检验,检验频次也该规定)!!!DVP是用来编制验证产品性能和功能实验的计划,而且DVR是用来记录你的试验结果的,所以两者的作用实际是不同的!至于手工样件和工装样件,作业工具不同,可能也需要分别编制,这个我不是很确定,或者可以引用手工样件的控制计划,把不同部分指出.哈哈,问高手吧特别是样件本身也有很多阶段的,比如手工样件、DV样件、工厂OTS样件和客户OTS样件,是否需要分别编制样件控制计划呢?按楼上的说法,DVP中是不用规定对尺寸的检验要求了?手工样件和OTS样件不一样,所以他们各自都需要各自的控制计划。
DFMEA评估

DFMEA评估概述DFMEA(Design Failure Mode and Effects Analysis,设计失效模式与效应分析)是一种系统性的方法,用于评估产品设计中的潜在失效模式和效应。
通过识别、评估和优化潜在的设计失效,可以减少产品设计过程中的风险,并提高产品质量和可靠性。
目的DFMEA评估的目标是在产品设计阶段尽早发现潜在的失效模式,并采取适当的措施来减轻或消除这些失效对产品性能和可靠性的影响。
通过实施DFMEA评估,可以:- 提前预测产品在使用过程中可能出现的问题;- 识别和分析潜在失效的原因和效应;- 评估失效的严重程度、容忍度和频率;- 优化设计,减少潜在失效的风险。
DFMEA评估过程DFMEA评估通常包括以下步骤:1. 选择评估的设计项目:确定需要进行DFMEA评估的设计项目,可以是整个产品、子系统或单个零部件。
2. 制定评估团队:组建一个具有相关专业知识和经验的评估团队,涵盖设计、工艺、制造和测试等领域。
3. 收集设计信息:收集和整理与设计项目相关的信息,包括设计相关文档、规范和标准等。
4. 识别失效模式:通过头脑风暴、经验分享和专家讨论等方式,识别与设计项目相关的潜在失效模式。
5. 评估失效的严重程度:对每个失效模式进行评估,确定其对产品性能和可靠性的影响程度。
6. 识别失效原因:分析每个失效模式的可能原因,找出导致失效的根本因素。
7. 评估失效的容忍度:评估每个失效模式是否被容忍,并确定容忍度的阈值。
8. 评估失效的频率:评估每个失效模式的发生频率,包括概率分析和经验估计。
9. 制定改进措施:为每个失效模式制定相应的改进措施,减轻或消除潜在的失效影响。
10. 跟踪实施情况:跟踪和记录改进措施的实施情况,并进行必要的调整和追踪。
总结DFMEA评估是一种重要的工具,可以帮助产品设计团队尽早发现和解决潜在的设计问题。
通过对潜在失效模式和效应的识别、评估和优化,可以提高产品设计的质量和可靠性,并降低产品开发过程中的风险。
- 1、下载文档前请自行甄别文档内容的完整性,平台不提供额外的编辑、内容补充、找答案等附加服务。
- 2、"仅部分预览"的文档,不可在线预览部分如存在完整性等问题,可反馈申请退款(可完整预览的文档不适用该条件!)。
- 3、如文档侵犯您的权益,请联系客服反馈,我们会尽快为您处理(人工客服工作时间:9:00-18:30)。
样机系统性能 试验
4
40
5
1.冷凝风机电机 被卡死
样机系统性能 试验
4
40
1.电磁离合器及 其它电控系统电 流量过大
初始设计 方案时, 样机系统性能 2 参照同类 试验 产品设计
4
40
1.空调系 统内异响 9.空调总成冷凝 器总成≤79dB 蒸发器总成噪声 ≤AdBA 2.蒸发风 空调噪音大, 机,冷凝风 不能满足标 机轴承有 准要求 异音 3.蒸发风 机及冷凝 风机电机 有异音
4 设计图纸 中明确作 出要求. 3 喷淋试验 4 48
有水进入风 道
安装时,打密封胶 的要求不明确
制冷系统停 止运行
管路内部清洁度 未达到标准要求
12.空调总成最 大负荷的制冷运 行,空调按试验 工况规定最大负 荷工况试验条件 稳定运行1小时 后,各部件无损 坏
制冷系统停 止运行 控制相应的 风机停止运 行 制冷系统停 止运行
4
60
4.无法提 供舒适环 境
不能满足标 准要求及顾 客要求,顾客 不满意
5
2.空调噪音超出 标准范围
4
40
3.制冷量未达到 设计要求
4
50
1.冷凝器芯体换 热面积设计偏小
5
设计变更增加扁 5 175 管数量,增大换 热面积
设计变更增加扁 管数量,增大换热 面积
7
3
3
63
2.蒸发风机,冷凝 风机选型过小 空调制冷 量无法达 2.空调总成制冷 到设计要 量28KW 求,制冷量 偏小
保压检漏
3
63
保压检漏 保压检漏
3 4
63 96
5.管接头 连接处泄
制冷剂泄漏, 不能满足标 准要求
5*
1.接头未拧紧 制冷量设计偏小 (关键部件压缩机 、蒸发器、冷凝 器、膨胀阀设计 选型不当) 压缩机轴功率过 大
1.空调制 冷量偏小 7.空调总成能效 比≥1.9W/W 2.压缩机 驱动功率 过大 1.蒸发风 机耗电功 率过大 2.冷凝风 8.辅件耗电功率 机耗电功 ≤2.5KW 率过大 3.电磁离 合器及其 它电控系 统总功率 过大
样机系统性能 试验
3
54
1.蒸发器芯体管 件焊接处虚焊
蒸发器芯体保 2 设计图纸 压检漏 中对各焊 接处作出 明确要求
2
28
7
2.冷凝器 管件焊接 处漏
制冷剂泄漏, 不能满足标 准要求
7
1.冷凝器芯体管 件焊接处虚焊
设计图纸 中对各焊 接处作出 冷凝器芯体保 2 明确要求 压检漏 设计图纸 中对各部 冷凝器,蒸发 3 件的配合 器芯体保压检 公差作出 漏 明确要求 设计图纸 5 中明确要 求. 初始设计 方案时, 3 参照同类 产品设计 计算 3 设计图纸 中对紧固 4 件扭矩做 明确要求 保压检漏
管路内部清洁度 未达到标准要求
图纸设计 2 时标明清 过程检验 洁度要求 参照同类 样机系统性能 2 产品设计 试验 计算
3
35
系统停止运 行
8
冷媒充注量过多
4
64
14.空调总成最 大负荷的制冷运 行连续运行1小 时后,停机3分, 再启动应能连续 运转1小时,但在 启动运行的最初 5分内允许过载 连续出现 保护器跳开,其 保护状态 后不允许动作; 在运行的最初5 分内过载保护器 不复位时,而在 停机不超过30分 内复位的,应能 连续运行1小时 。
2
28
3.冷凝器, 制冷剂泄漏, 蒸发器芯 不能满足标 体端板处 准要求 6.空调总成气密 铜管破裂 性:制冷剂泄漏 14g/年 制冷剂泄漏, 不能满足标 准要求
1.两器端板与管 件配合间隙大,将 铜管磨破. 1.安装密封圈未 蘸冷冻油 5 *
2
35
3
75
4.密封圈 泄漏.
2.选择密封圈线 径偏小 3.接头未拧紧
4.排水管设计垂 直方向太高
4
样机系统性能 试验
5
80
5.蒸发器芯体翅 片用了光铂材料 6.蒸发器盖板贴 保温太薄,结露
2
样机系统性能 试验 样机系统性能 试验
3
24
3
5
60
1.底座预 埋蒸发风 机铝板底 11.空调总成空 面未贴PE 调器在低温工况 胶板进行 下运行正常,蒸 保温 发器风道不应有 结露,空调出风 口不应有结露
3
样机系统性能 试验
3
63
制冷量无法 达到客户要 求顾客不满 意
7
*
3.膨胀阀选型过 大
3
样机系统性能 试验
3
63
4.蒸发器芯体换 热面积设计偏小
5
样机系统性能 试验
设计变更增加多 5 175 一排管,增大换 热面积
设计变更增加多 一排管,增大换器 面积
7
3
3
63
5.压缩机选型排 量偏小
5
样机系统性能 试验
4
60
5
玻璃钢底座开裂
3
30
5
蒸发器内盖与空 调底座密封不好
40
60
5
低压冷媒管保温 不好
5
75
1.选定蒸发风机 风量太小 蒸发风量达 不到设计要 蒸发风机 求,影响空调 风量偏小 制冷量,不能 满足客户要 求
样机系统性能 试验
3
54
6
*
2.蒸发器回风口 设计过小
样机系统性能 试验
3
54
3.风机之间靠的 太近,风阻大. 1.蒸发器 芯体管件 焊接处 制冷剂泄漏, 不能满足标 准要求
2
70
1.经振动 试验后,玻 空调漏水,不 璃钢底座 能满足标准 或盖板损 要求 坏 2.经振动 部件脱落,系 试验后,紧 统无法正常 固件松动 工作
7
玻璃钢底座或盖 板设计厚度不足
初始设计 方案时, 2 参照同类 耐振试验 产品设计 厚度 初始设计 方案时, 5 明确紧固 过程检验 件矩值大 小 初始设计 方案时明 确紧固 值,选择 4 保压检漏 合适的保 压值确保 无虚焊或 不牢固 设计时, 按客户提 供的弧度 进行设计 设计时将 玻璃外壳 强度适当 提高. 设计时对 出风口外 置,排水 3 孔位置进 行合理安 装 设计图纸 中应对打 3 胶处理明 确提出.
探 测 度
风险 序数
1.无法调 节温度
பைடு நூலகம்
8
1.蒸发风量过大 或过小 2.车身保温效果 差及车门车窗密 封效果差 3.制冷剂泄漏 1.空调总成 1.调节温度 2.调节湿度 3.提供舒适的环 3.无法保 境 证舒适湿 度 4.制冷剂充注量 不足
2
增加高低 压开关, 控制面板 初始设计 方案时, 样机系统性能 参照同类 试验 产品设计 计算 2 产品设计 评审 样机系统性能 试验 样机系统性能 试验
3
35
4
紧力矩紧固不足
3
60
3.空调总成 机械安全要求 空调设计保证在 正常运输,安装 和使用时具有可 3.经振动 试验后,气 制冷量达不 靠的稳定性 密性试验 设计要求 有泄漏
6
1.铜管焊接处有 虚焊或不牢固 2.管接头螺母松 动
3
72
车顶安装 开孔处漏 水
淋雨时车顶 安装开孔处 水流入车内
1.空调设计的弧 度与客户提供的 车顶弧度不符合 5 2.空调顶置玻璃 作业过程中变形 3
样机系统性能 试验
2
16
2
28
2.达不到 车内设定 温度
制冷效果降 低顾客不满 意
7
3
35
舒适性降低, 顾客不满意
7
1.蒸发器蒸发风 量过大或过小
增加高低 1 压开关, 控制面板 参照同类 1 产品设计 计算 初始设计 方案时, 2 参照同类 产品设计 计算
2
14
2
14
样机系统性能 试验
4
56
境
1.蒸发风量过大 或过小
初始设计 方案时, 样机系统性能 4 参照同类 试验 产品设计 计算 初始设计 方案时, 样机系统性能 3 参照同类 试验 产品设计 进行风机 初始设计 方案时, 样机系统性能 2 参照同类 试验 产品设计 计算 初始设计 方案时, 参照同类 产品设计 初始设计 方案时, 参照同类 产品使用 型号 初始设计 方案时, 参照同类 产品使用 型号 初始设计 方案时, 参照同类 产品设计 计算 初始设计 方案时, 参照同类 产品选型 样机系统性能 试验
劲达技术(河源)有限公司
设计潜在失效模式及效应分析 (DFMEA) 顾客: 核心小组: 徐旭东/技术、制造中心总监 郭冬青/总师办主任 FMEA编号: FMEA版本号: AvtoRef Lux Co.Ltd. 万金/出口部经理 徐仁/品管中心总监 邝维盛/客车空调技术部经理 DFMEA-08002 08 A/0 负责人: 编制人: 批准: FMEA编制日期: 零件编号/最新更改水平: FMEA更新日期: KL-XB3 崔健总裁 邝维盛/技术中心客车空调部经理 2009.07.01 供方/工厂: 供方/工厂地址: 关键日期: 零件名称和描述: 河源明珠开发区力王大道1号 2010.02.03 顶置式系列空调 劲达技术(河源)有限公司 措施结果 严 探 频 风险 潜在失效 潜在失效的 重 级 潜在失效的起因/ 现行预防 现行探测设计 测 责任和项目 严 项目功能/要求 度 序数 建议措施 频 模式 后果 度 别 机理 设计控制 控制 度 完成日期 采取的措施 重 (O) PPN 度 (S) (D) 度 基本功能丧 失不能满足 标准要求及 顾客要求 1.关键部件压缩 机、蒸发器、冷 凝器、膨胀阀出 现故障 2.制冷剂严重泄 漏 产品设计 评审 1
喷淋试验
3
45
淋雨时车顶 的水经出风 口和回风口, 流入车内 出风口海绵 出风口漏 长时间浸泡 水 后,形成漏水 通道