失效模式与效应分析模板
FMEA失效模式效应分析表-
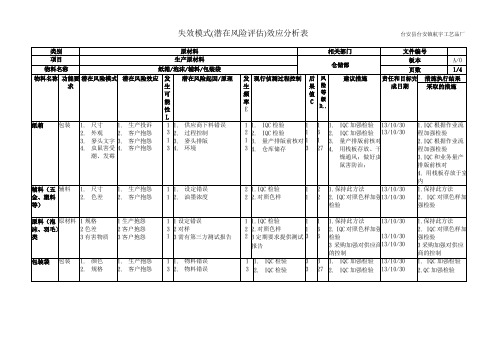
失效模式(潜在风险评估)效应分析表
台安县台安镇航宇工艺品厂
类别
成品
相关部门
文件编号
项目 物料名称
包装好的成品 成品
仓储部
板本
A/0
页数
3/4
功能要求 潜在风险模式 潜在风险效应 发 生 可 能 性 L
潜在风险起因/原理
发 现行侦测过程控制 生 频 率 E
后风
果险 值等 C级
D..
建议措施
责任和目标
行组装和包装
1 2、质检不到位
2 2.加强检验
3 18 7 14
1.严格按客人 13/10/30 和包装流程进 行组装和包装 2.员工自检和 13/10/30 品检全检相结 合的检验方式 彻底执行,保 证质量
1.严格按客人和包装 流程进行组装和包装 2.员工自检和品检全 检相结合的检验方式 彻底执行,保证质量
燥通风;做好虫
鼠害防治;
2 1.IQC 检验 2 2.对照色样
1 2 1.保持此方法
13/10/30
1 2 2. IQC 对照色样加强13/10/30
检验
1.IQC 根据作业流 程加强检验 2.IQC 根据作业流 程加强检验 3.IQC 和业务量产 排版前核对 4. 用栈板存放于室 内 1.保持此方法 2. IQC 对照色样加 强检验
台安县台安镇航宇工艺品厂
半成品
相关部门
文件编号
制程半成品 工序
生产部
板本
A/0
页数
2/4
发 潜在风险起因/原理 生 可 能 性 L
3 1. 操作不良 3 2. 破损 3 3. 伤害身体,影响健康
发 现行侦测过程控 后 风
生
制
dfmea 模板
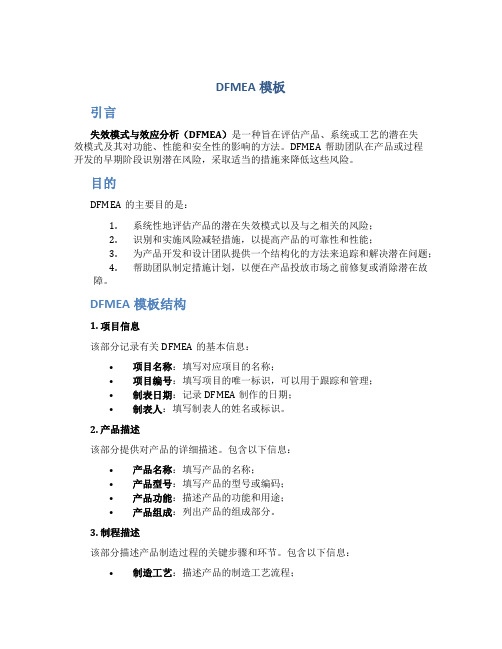
DFMEA模板引言失效模式与效应分析(DFMEA)是一种旨在评估产品、系统或工艺的潜在失效模式及其对功能、性能和安全性的影响的方法。
DFMEA帮助团队在产品或过程开发的早期阶段识别潜在风险,采取适当的措施来降低这些风险。
目的DFMEA的主要目的是:1.系统性地评估产品的潜在失效模式以及与之相关的风险;2.识别和实施风险减轻措施,以提高产品的可靠性和性能;3.为产品开发和设计团队提供一个结构化的方法来追踪和解决潜在问题;4.帮助团队制定措施计划,以便在产品投放市场之前修复或消除潜在故障。
DFMEA模板结构1. 项目信息该部分记录有关DFMEA的基本信息:•项目名称:填写对应项目的名称;•项目编号:填写项目的唯一标识,可以用于跟踪和管理;•制表日期:记录DFMEA制作的日期;•制表人:填写制表人的姓名或标识。
2. 产品描述该部分提供对产品的详细描述。
包含以下信息:•产品名称:填写产品的名称;•产品型号:填写产品的型号或编码;•产品功能:描述产品的功能和用途;•产品组成:列出产品的组成部分。
3. 制程描述该部分描述产品制造过程的关键步骤和环节。
包含以下信息:•制造工艺:描述产品的制造工艺流程;•工艺参数:列出影响制造过程的关键参数;•工艺风险:标识可能导致故障的工艺风险。
4. 功能失效模式该部分识别产品在功能上可能出现的失效模式。
包含以下信息:•功能要求:描述产品的功能要求和性能指标;•失效模式:识别可能导致功能失效的模式;•可能原因:分析导致失效模式的可能原因;•失效效应:描述失效模式对产品和系统的影响和后果。
5. 风险与优先级评估该部分通过对失效模式的风险评估确定风险的优先级。
包含以下信息:•风险评估标准:定义用于评估风险的标准和等级;•风险评估矩阵:利用风险评估标准评估失效模式的风险优先级;•风险处理措施:根据评估结果确定风险处理措施。
6. 控制计划该部分描述在制造过程中采取的控制措施以降低风险。
失效模式与效应分析程序FMEA资料
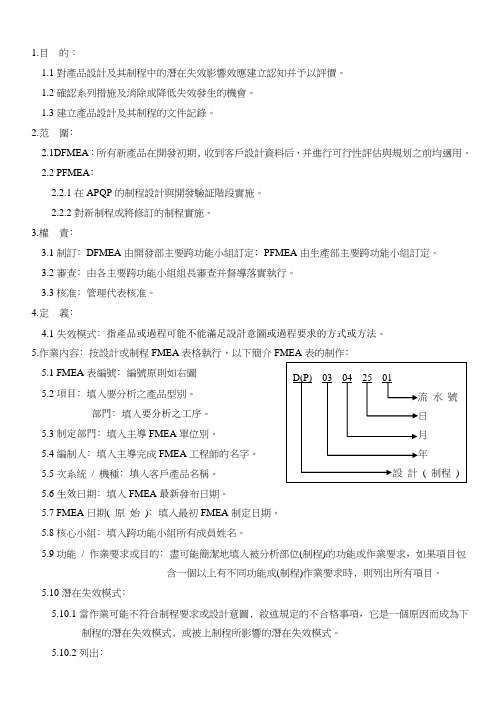
1.目的:1.1對產品設計及其制程中的潛在失效影響效應建立認知并予以評價。
1.2確認系列措施及消除或降低失效發生的機會。
1.3建立產品設計及其制程的文件記錄。
2.范圍﹕2.1DFMEA:所有新產品在開發初期﹐收到客戶設計資料后,并進行可行性評估與規划之前均適用。
2.2 PFMEA﹕2.2.1在APQP的制程設計與開發驗証階段實施。
2.2.2對新制程或將修訂的制程實施。
3.權責﹕3.1制訂﹕DFMEA由開發部主要跨功能小組訂定﹔PFMEA由生產部主要跨功能小組訂定。
3.2審查﹕由各主要跨功能小組組長審查并督導落實執行。
3.3核准﹕管理代表核准。
4.定義﹕4.1失效模式﹕指產品或過程可能不能滿足設計意圖或過程要求的方式或方法。
5.作業內容﹕按設計或制程FMEA表格執行,以下簡介FMEA表的制作﹕5.2項目﹕填入要分析之產品型別。
部門﹕填入要分析之工序。
5.3制定部門﹕填入主導FMEA單位別。
5.4編制人﹕填入主導完成FMEA工程師的名字。
5.5次系統/ 機種﹕填入客戶產品名稱。
5.6生效日期﹕填入FMEA最新發布日期。
5.7 FMEA日期( 原始)﹕填入最初FMEA制定日期。
5.8核心小組﹕填入跨功能小組所有成員姓名。
5.9功能/ 作業要求或目的﹕盡可能簡潔地填入被分析部位(制程)的功能或作業要求,如果項目包含一個以上有不同功能或(制程)作業要求時﹐則列出所有項目。
5.10潛在失效模式﹕5.10.1當作業可能不符合制程要求或設計意圖﹐敘述規定的不合格事項,它是一個原因而成為下制程的潛在失效模式﹐或被上制程所影響的潛在失效模式。
5.10.2列出﹕5.10.2.1每一潛在失效模式假設失效是將發生的﹐但不是必須發生的。
5.10.2.2盡可能敘述失效模式發生于某些作業條件下(如﹕壓力等)和在某些使用條件下(如﹕溫度,高度)。
5.10.2.3一般失效模式含如下各項﹐但不限于此﹕破損、變形、碰傷、錯位、裂紋等。
FMEA失效模式与效应分析
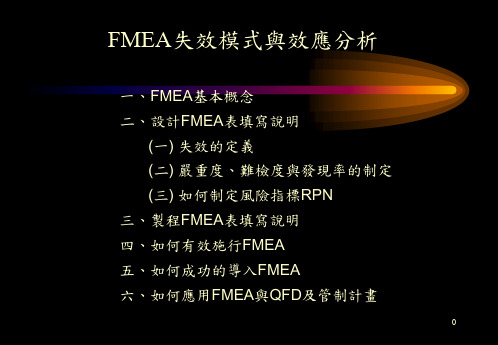
一、FMEA 的基本概念
1. 及時性是成功實施FMEA的最重要因素之一。
2. 它是“事前的預防”而不是“事後的追悔”。
3. 事先花時間進行FMEA分析,能夠容易且低成本 地對產品設計或製程進行修改,從而減輕事後修 改的危機。
4. FMEA能夠減少或消除因修改而帶來更大損失的 機會,它是一個相互作用的過程,永無止境的改 善活動。
2.失效效應分析(failure effect analysis) EA
對每一個失效模式,確定其失效對其上一層模組及最終系統的失 效影響,了解其組件介面失效關聯性,做為改進行動的依據。
3.關鍵性分析(critical analysis)
CA
對每一個失效模式,依其嚴重等級和發生機率綜合評估並予以分
難檢度 15
一、FMEA 的基本概念
腦力激盪法
6 – 3 – 5 原則 6人、3構想、看5次
➢ 禁止批評 ➢ 自由奔放 ➢ 求量 ➢ 搭別人創意便車
成品合格出廠 卻被顧客抱怨 的原因可能有
三菱式 腦力激盪法
➢ 理性過濾,擇取組合,表達具體明確 ➢ 刪除意見要獲得成員大多數同意 ➢ 表達以《名詞+形容詞》方式 ➢ 創意評價
3
一、FMEA 的基本概念
1.對產品設計與製程進行失效分析, 找出元 / 組件的失效模 式,鑑定出它的失效原因,並評估該項失效模式對系統會 產生什麼影響。
2.找出元 / 組件或系統的潛在弱點,提供設計、製造、品保 等單位採取可行之對策,及早進行設計與製程研改,強化 產品品質。
3.書面描述上述分析過程,確保產品品質符合顧客需求。
FMEA” ,而 MIL- STD -1629A因分析項目缺少現行管制方法 故適合設計時使用。 5.FMEA為歸納法之應用,根據零組件的失效資料,由下而上推斷 系統的失效模式及其效應,是一種向前推演的方法。
dfmea模板

dfmea模板DFMEA模板。
DFMEA(Design Failure Mode and Effects Analysis)即设计失效模式与效应分析,是一种用于识别和消除产品设计过程中潜在失效模式的方法。
通过对产品设计的各个环节进行系统化的分析,可以有效地预防和解决产品设计过程中可能出现的问题,提高产品的可靠性和质量。
本文将介绍一个DFMEA的模板,帮助您进行设计失效模式与效应分析。
1. 项目信息。
项目名称:项目编号:项目负责人:审核人:日期:2. 设计要求。
在这一部分,列出产品设计的基本要求和目标,包括性能指标、安全要求、可靠性要求等。
这些要求是进行DFMEA分析的基础,也是确定失效模式和效应的重要依据。
3. 设计部件/系统。
列出产品的各个部件或系统,包括其功能、结构、工作原理等。
对于复杂的产品,可以分模块进行分析,确保每个部件或系统都得到充分的关注。
4. 失效模式。
针对每个设计部件或系统,分析可能出现的失效模式。
失效模式是指产品在设计、制造、使用过程中可能出现的失效形式,包括功能失效、性能下降、安全隐患等。
5. 失效影响。
对于每个失效模式,分析其可能产生的影响,包括对产品性能、安全性、可靠性等方面的影响。
同时也要考虑失效对用户、环境等的影响。
6. 失效原因。
针对每个失效模式,分析其可能的原因。
失效原因可能包括设计缺陷、材料选择不当、制造工艺问题等,通过分析失效原因,可以有针对性地进行改进和预防。
7. 现有控制措施。
列出目前已经采取的控制措施,包括设计控制、制造控制、检验控制等。
分析这些控制措施的有效性,是否能够有效地预防或减轻失效模式的发生。
8. 建议改进措施。
根据对失效模式、影响和原因的分析,提出相应的改进措施。
这些改进措施应该具有针对性和可行性,能够有效地提高产品的可靠性和质量。
9. 评估和优先级。
对提出的改进措施进行评估和排序,确定哪些措施应该优先实施。
评估可以考虑改进措施的成本、效果、紧急程度等因素。
FMEA-失效模式与效应分析表

FMEA编号/FMEA NO.:12575490 项 目 名 称:排气管(左)
文件编号/FILE NO. :M10-001-1.0源自(PROCESS FMEA)
过程责任部门:M00 FMEA编制日期:2002.11/01 作成 核 准 Process Responsibility:M00 FMEA Date(orig.):2002.11.01 Prepared By Approval By Item:Manifold-lh 车型年/车辆类型:CAMI 关键日期:2003.06/04 FMEA修订日期:2003.8/30 WENWEI ZHU Model Year(s)/Vehicle(s):CAMI Key Date:2003.6.4 FMEA Date(rev.):2003.8/30 主要参加者:谢玮,洪容伟,尤洪,黄松,余肖汉,张闯,柴升军,汪东成,章勇军,苏显辉 Core Team: XIE WEI/HONG RONGWEI/YOU HONG/HUANG SONG/YU XIAOHAN/ZHANG CHUANG/CHAI SHENGJUN/WANG DONGCHENG/ZHANG YONGJUN/SU XIANHUI 措 施 结 果 过程功能 潜在的 潜在的 严重 级 潜在的失效 现行的 频 建议的 责任及目标 风险 不易 顺序 度 措施 完成日期 Action results Process 失效模式 失效后果 度数 别 起因/机理 工艺控制 探测 数 C r O Function Responsibility 采取的措施 度数 l Potential Cause(s) S R Potential c Potential Current Process Recommended & target R S O D a Dete Effect(s) of e Mechanism(s) of P Action 要求 c failure mode Controls Action(s) Completion P s c Failure Failure v N Taken u Requirements date N s OP05 滚珠试验 流道不畅 发动机烧毁 8 F00粗材不良 1 对粗材进行全检 5 40 Steel ball test Flow no Engine F00 Casting NG casting full check smooth burred OP10 铣面 Face milling 平面度0.04 超差 planeness 0.04 oversize 装配后漏气 leak after assembly 5 A 1.刀具磨耗超限 tool wear away too over 2.加工余量太大 Allowance too much 2 经M10试加工后设定刀具 寿命 set-up toolife by M10 after trying 2 余量及加工程式由M10设 定并经试加工确认 set-up allowance and make NC program by M10, checking on trying 粗材尺寸进料检查 check-in-come about the size of casting 3.夹持力太小 clamp power not enough 2 夹持力由生技试加工时确 定,作成作业标准 clamp pressure set up after trying by M10 and write in the instructor 4 24 4 40 4 40
dfmea模板示例
DFMEA模板示例1. 引言在产品开发和制造过程中,设计失效模式与效应分析(DFMEA)是一种常用的工具。
该分析方法可以帮助团队识别和评估设计过程中的潜在失效模式,以及这些失效模式可能对产品质量、性能、安全性以及用户满意度产生的影响。
本文档提供了一个DFMEA模板示例,用于说明如何进行DFMEA分析。
2. DFMEA模板示例2.1 项目信息•项目名称:XYZ产品•项目负责人:John Doe•日期:YYYY-MM-DD2.2 设计过程步骤1.记录设计步骤12.记录设计步骤23.记录设计步骤32.3 设计失效模式与效应分析2.3.1 设计失效模式1•失效模式描述:描述失效模式1的特征和症状•宜发生概率:对该失效模式发生的可能性进行评估(1-10)•严重度:对该失效模式带来的影响进行评估(1-10)•可发现性:对该失效模式是否容易被发现进行评估(1-10)•风险等级:对失效模式的风险进行评估(计算方法:宜发生概率 * 严重度 * 可发现性)2.3.2 设计失效模式2•失效模式描述:描述失效模式2的特征和症状•宜发生概率:对该失效模式发生的可能性进行评估(1-10)•严重度:对该失效模式带来的影响进行评估(1-10)•可发现性:对该失效模式是否容易被发现进行评估(1-10)•风险等级:对失效模式的风险进行评估(计算方法:宜发生概率 * 严重度 * 可发现性)2.4 建议和措施在DFMEA分析的基础上,根据评估结果提出相应的建议和措施,以降低风险等级。
2.4.1 建议和措施1•针对失效模式1,提出相应的建议和措施,例如改进设计、使用更可靠的材料等。
2.4.2 建议和措施2•针对失效模式2,提出相应的建议和措施,例如加强质量控制、优化生产工艺等。
2.5 后续措施跟踪•记录建议和措施的实施情况,并跟踪评估其效果。
3. 结论DFMEA模板示例提供了一个基本的框架,帮助团队进行设计失效模式与效应分析。
通过对潜在失效模式的评估,可以及早发现并解决问题,以提高产品的质量和性能。
FMEA失效模式及效应分析
•1100: • 損失金額(USD) 階 •10:1
段
•3 、裝 配 生 產 階 段
• 1:1
•4 、客 戶 服 務 •5 、客 訴 抱 怨 處 理
•1 10
圖面 生產
• 1/2:1
•1/20:1
100
檢驗
1000
使用
• 10000
變更
PPT文档演模板
FMEA失效模式及效应分析
•1.FMEA簡介
•FMEA的基本方法
PPT文档演模板
FMEA失效模式及效应分析
•1.FMEA簡介
•失效模式分析(Failure Mode and Effects Analysis, 簡稱 FMEA)是一有系統的跨功能小組進行的事先預防活動, 其目的為:
1.認識及評估一產品及製程的潛在失效模式及其影響。 2.確認可以消除或減少潛在失效發生的改善措施。 3.將此過程文件化。 4.產品及製程有變更時, 隨時變更文件。 5.以此文件驗證實際的事先預防活動。
該單位的FMEA分析:現況分析
PPT文档演模板
FMEA失效模式及效应分析
演讲完毕,谢谢听讲!
再见,see you again
PPT文档演模板
2020/11/1
FMEA失效模式及效应分析
FMEA失效模式及效应 分析
PPT文档演模板
2020/11/1
FMEA失效模式及效应分析
• 課程目的:
產品設計及製程規劃時成功地應用FMEA可以減少工程 變更或容易執行變更,更可將潛在的問題事先預防;
認識及評估一產品及製程的潛在失效模式及其影響;
確認可以消除或減少潛在失效發生的改善措施;
將此過程文件化, 以為持續改善的依據;
失效模式与效应分析(HFMEA)范例
NO
4、该危害是否很明确,即使 缺乏控制也能轻易察觉?
YES
NOYES
继续进行HFMEA步骤5
stop
忘记取登机牌 该失效模式或步骤是否会造成 系统相当大的危害?(如危害 指数>8)4分
YES
NO
2、该项是否为整体流程中唯一 的一处弱点或关键?(一旦失 效会造成系统失败)
NO
NO
YES
3、是否已有有效Y的ES控制措施 YES
可侦测该失效模式的发生?
NO
4、该危害是否很明确,即使 缺乏控制也能轻易察觉?
YES
NOYES
继续进行HFMEA步骤5
stop
1旅行社将名字填错 该失效模式或步骤是否会造成 系统相当大的危害?(如危害 指数>8)4分
YES
NO
2、该项是否为整体流程中唯一 的一处弱点或关键?(一旦失 效会造成系统失败)
NO
YES
3、是否已有有效Y的ES控制措施 YES
可侦测该失效模式的发生?
NO
4、该危害是否很明确,即使 缺乏控制也能轻易察觉?
YES
NOYES
继续进行HFMEA步骤5
stop
HFMEA执行步
骤 流 失效 潜在原因 风险 分 决策树分析
程 模式
析
过安 有效证件 1、个人疏忽 检 丢失
严 发 危 问题 重 生 害 是否 性 率 指 为关
数 键点
4 14否
有无有 难检度: 是否 效 衡量 能否明显 进行 控制方 看出失效 矫正 法(监 (失败立 视器等) 即处置)
携带禁止 1、个人疏忽 登记的物 2、无乘机时禁
4 14否
品
医疗失效模式与效应分析
医疗失效模式与效应分析(HFMEA)在检验危急值报告流程中的应用青海红十字医院质管科孙显秀810000关键词:HFMEA 检验危急值管理医疗失效模式与效应分析(Heahh Failure Mode andEffects Analysis,HFMEA)是由美国退伍军人局及国家病人安全中心共同研发的前瞻性危机分析系统。
它通过系统性、前瞻性地检查某个流程可能发生故障的途径,重新设计该流程,以消除故障发生的可能性,使故障的不良结果降到最小。
HFMEA在医疗风险管理中的应用主要包括预防技术故障或设备缺损,提高病人治疗的安全性,以及识别病人和医疗服务者存在的潜在危险因素等。
HFMEA作为医疗机构全面质量改进过程的一部分,旨在提高医疗安全。
1、方法1.1 检验危急值定义:所谓检验“危急值”即当这种检验结果出现时,说明患者可能处于危险的状态,此时如果临床医生能及时得到检验信息,迅速给予患者有效的干预措施或治疗,即可挽救患者生命,否则就有可能出现严重个后果,失去最佳抢救机会。
所以,“危急值”是表示危及生命的检验结果,故把这种检验数据称为危急值1.2 组建HFMEA项目团队2010年11月,成立HFMEA 团队。
团队包括主要的管理者和员工及流程相关知情人,如医务处、检验科、质管科及相关科室的成员。
制定团队目标、时间框架、期望结果,并确定每位团队成员的角色,明确流程界限为从检验科出现危急值到临床科室接到“危急值结果”,医生根据危急值结果及时对病人处理。
1.3绘制检验危急值报告—接受—处理流程图检验科出现危急值确认仪器设备正常后立即复检复检结果无误 5分钟内电话通知临床科室临床科室工作人员(医生/护士)接听到危急值报告内容后在《危急值接受登记本》上详并在《危急值登记本》上详细记录。
细记录将记录内容大声复述一遍给报告人听医生得到危急值结果报告后根据病人临床症状给予及时处理并记录如与临床不符,进行复查,复查结果记录在病历中。
- 1、下载文档前请自行甄别文档内容的完整性,平台不提供额外的编辑、内容补充、找答案等附加服务。
- 2、"仅部分预览"的文档,不可在线预览部分如存在完整性等问题,可反馈申请退款(可完整预览的文档不适用该条件!)。
- 3、如文档侵犯您的权益,请联系客服反馈,我们会尽快为您处理(人工客服工作时间:9:00-18:30)。
潜在失效效应
严重度(S)
特性等级
潜在失效起因/设备失效(缺点预估原因)
发生度(O)
现行预防设计控制/现行预防制程管制
现行检测设计控制/现行检测制程管制
难检度(D)
风险顺序数/风险优先数RPN
建议措施
负责人
与
目标
完成日
措施结果/改善后结果
采取之措施/已采行措施
S
O
D
RPN
BS922512H-03
后段无磁浮
磨擦异音
6
1
1、单体扇叶较重
2、分隔环过长
4
全检变形与缺料部分,毛边修除。
1
32
修正矽钢片(用之前日本矽钢片OK),或修整模具。
主管审核:______________
制表:______________
RE39A品保业务资材
失效模式与效应分析(FMEA)
□DFMEA□PFMEA
客户:/
专案负责人:
生效日期:
分发单位:
失效模式与效应分析编号:
品质管制工程人员:
制程厂区:工程部
机种料号(Part Number):
版次:
机种名称(Part Name/Description):
原始制订日期:
修正日期:
产品类别:□风扇(□Cooler Fan□Blower)□散热器□其它