万吨直馏柴油加氢精制装置简介
直馏柴油加氢装置掺炼催化柴油的技术改进
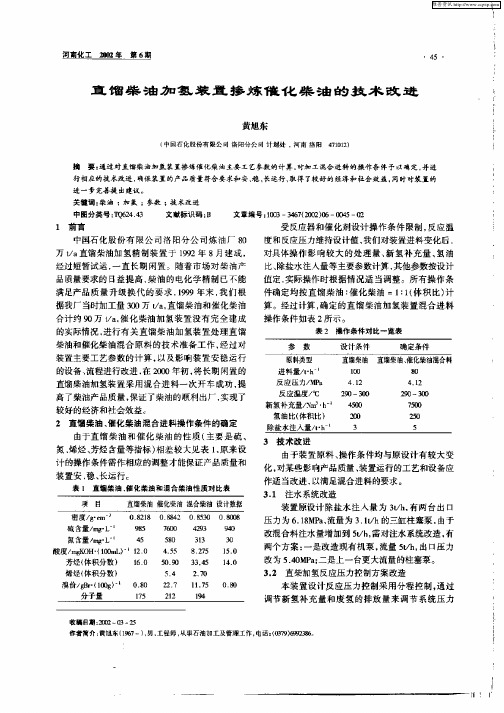
据我厂当时加工量 30 0 万 a直馏柴油和催化柴油 , 合计约 9 万 a催 化柴油加氢装置没有完全建成 0 , 的实 际情 况 , 进行 有 关 直馏 柴油 加氢 装 置处 理直 馏 柴油和催化柴油混合原料的技术准备工作, 经过对
算。经过计算 , 确定的直馏柴油加氢装置混合进料 操作条件如表 2 所示。 表2 操作条件对比一览表 参 数 设 计条 件
1 0 0
确定条 件
装置主要工艺参数的计算, 以及影响装置安稳运行
的设备 、 流程进行改 进 , 20 在 00年初 , 长期 闲置 的 将
——
面———
溴价 g ‘ 0 ) B ( 0 r1g
08 . 2 7 1. 08 0 2 15 7 - 0
本装置设计反应压力控制采用分程控制 2 ( 0 —2 /
!
调节 新氢补充量和废氢的排放量来调节系统压力
作者简介 : 黄旭东( 6 一 , 工程师 . 1 7 ) 男, 9 从事石油加工及管理工作 . 电话 : 3969 3 。 ( 7 ) ". 0 9zm
维普资讯
河 南化 工
抛
年
第 6期
直 馏 柴 油 加 氢 装 置 掺 炼 催 化 柴 油 的 技 术 改 进
黄旭东
( 中国石化股份有 限公司 洛阳分公 司 计划处 , 河南 洛阳 4 11) 702
摘
要: 通过对直馏柴 油加氢装 置掺炼催化 柴油主要 工艺参数的计算 , 对加工混合进料的操作条件 子烈璃定 , 井进
“ 边收边 放” 的方法 ; 为保证 反应 压力控 制平稳 , 调节 及时 , 分程控制 为单 回路 控制 ( 图 2 , 改 见 )将更 加灵
加氢装置介绍

加氢裂化装置原理、流程及特点
加氢裂化是将大分子的重质油转化为广泛使用的小分子 的轻质油的一种加工手段。可加工直馏柴油、催化裂化循环 油、焦化馏出油,也可用脱沥青重残油生产汽油、航煤和低 凝固点柴油。加氢裂化装臵是炼油厂最重要的的生产装臵之 一,在高温、高压、临氢状态下操作。 加氢裂化装臵的工艺流程主要有三种类型方法: ⑴ 一次通过法:所产尾油不参加循环。 ⑵ 部分循环法:所产尾油一部分参加循环,一部分排出 装臵。 ⑶ 全部循环法:所产尾油全部参加循环,不排尾油。 加氢裂化装臵主要设备有加氢精制反应器、加氢裂化反 应器、加热炉、高压热交换器、高压空冷器、高、低压分离 器、高温高压临氢管道、高温阀门等。详见图1、图2、图3、 图4。
2013-8-17 12
H1
H2
H3
凸台
H4
H5
s-k H6
1
图5
2013-8-17
热壁加氢反应器
13
加氢裂化装置常用材料
设备名称
加氢精制、裂化反应器 (设计温度≤ 450 ℃/设 计压力8~20MPa) 高压热交换器(温度≤ 260 ℃)
选用材质
板2.25Cr-1Mo(SA387Gr22CL2) +6.5mm(Tp309+347) 堆焊层 或+4mm(TP347)单层浅熔深堆焊 锻2.25Cr-1Mo(SA336F22CL2) + 6.5mm(Tp309+347) 堆焊层或+4mm(TP347)单层浅熔深堆焊 管程:反应流出物:管箱(碳钢、碳钼钢+4~6mm CA;铬钼钢+3mm CA)管板(碳钢、碳钼钢、铬钼钢 + 8mmTP309+347) 壳程:循环氢、原料:壳体(碳钢、碳钼钢、铬钼 钢+ 3mm CA) 管程:反应流出物:管箱(铬钼钢+3mm 1Cr18Ni9Ti 复合板 或 +6.5mm Tp309+347堆焊层 或 +4mmTP347) 管板(铬钼钢+8mmTP309+347或铬 钼钢+8mmTP410) 壳程:循环氢、原料:壳体(铬钼钢+4mm CA;或 +3mm 1Cr18Ni9Ti 复合板;或+4mmTP347;或 +6.5mm Tp309+347堆焊层) 14
辽化装置介绍
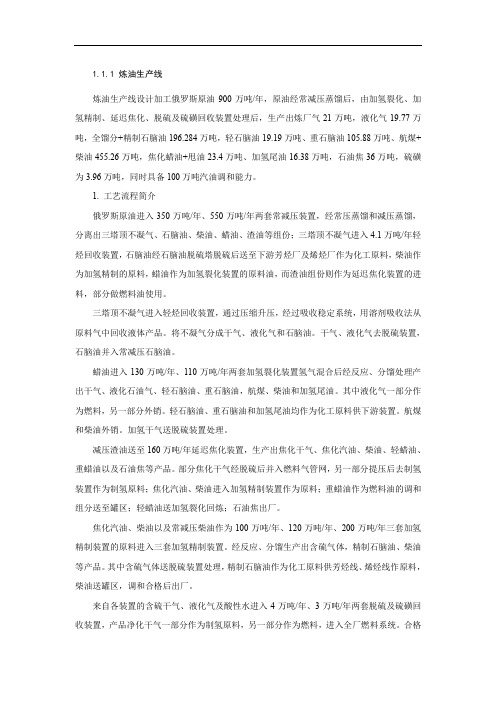
1.1.1 炼油生产线炼油生产线设计加工俄罗斯原油900万吨/年,原油经常减压蒸馏后,由加氢裂化、加氢精制、延迟焦化、脱硫及硫磺回收装置处理后,生产出炼厂气21万吨,液化气19.77万吨,全馏分+精制石脑油196.284万吨,轻石脑油19.19万吨、重石脑油105.88万吨、航煤+柴油455.26万吨,焦化蜡油+甩油23.4万吨、加氢尾油16.38万吨,石油焦36万吨,硫磺为3.96万吨,同时具备100万吨汽油调和能力。
1. 工艺流程简介俄罗斯原油进入350万吨/年、550万吨/年两套常减压装置,经常压蒸馏和减压蒸馏,分离出三塔顶不凝气、石脑油、柴油、蜡油、渣油等组份;三塔顶不凝气进入4.1万吨/年轻烃回收装置,石脑油经石脑油脱硫塔脱硫后送至下游芳烃厂及烯烃厂作为化工原料,柴油作为加氢精制的原料,蜡油作为加氢裂化装置的原料油,而渣油组份则作为延迟焦化装置的进料,部分做燃料油使用。
三塔顶不凝气进入轻烃回收装置,通过压缩升压,经过吸收稳定系统,用溶剂吸收法从原料气中回收液体产品。
将不凝气分成干气、液化气和石脑油。
干气、液化气去脱硫装置,石脑油并入常减压石脑油。
蜡油进入130万吨/年、110万吨/年两套加氢裂化装置氢气混合后经反应、分馏处理产出干气、液化石油气、轻石脑油、重石脑油,航煤、柴油和加氢尾油。
其中液化气一部分作为燃料,另一部分外销。
轻石脑油、重石脑油和加氢尾油均作为化工原料供下游装置。
航煤和柴油外销。
加氢干气送脱硫装置处理。
减压渣油送至160万吨/年延迟焦化装置,生产出焦化干气、焦化汽油、柴油、轻蜡油、重蜡油以及石油焦等产品。
部分焦化干气经脱硫后并入燃料气管网,另一部分提压后去制氢装置作为制氢原料;焦化汽油、柴油进入加氢精制装置作为原料;重蜡油作为燃料油的调和组分送至罐区;轻蜡油送加氢裂化回炼;石油焦出厂。
焦化汽油、柴油以及常减压柴油作为100万吨/年、120万吨/年、200万吨/年三套加氢精制装置的原料进入三套加氢精制装置。
1.2Mt/a柴油加氢装置开工及运行分析
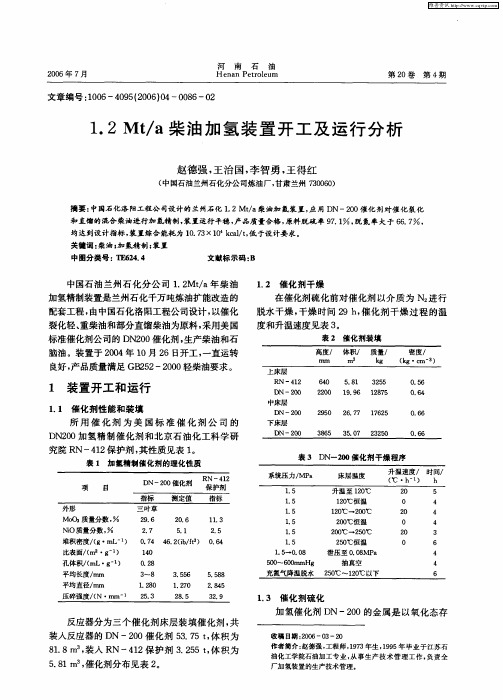
系统存 硫/ g l 【
上硫率 ,
由表 5可见上硫率达 9 . 1 , 8 6 满足加氢催 化 剂 的流化 要求 。
表 8 原 料和产品性质 ( 第二次标定 )
2 装置运行和标定
2 1 装置 运行 .
装置 20 0 4年 1 0月 2 日开 工 , 2 0 6 到 0 6年 2 月底已累计加工量达到 16 23 1t其 中加工催 5 7 , 化柴 油 10 010t直 馏柴 油 5 0 1t焦 化柴 油 2 3 、 88 7 、
o2 .8
3 ~8 12 0 .8
356 .5 120 .7 2. 85 558 . 8 285 . 4 3 9 2.
压碎强度/ N ・ 2 一 ( n l1 n 2 . Βιβλιοθήκη 31 3 催化 剂硫化 .
加氢催化剂 D N一 0 2 0的金 属是 以氧化态存 反应器分为三个催化剂床层装填催化剂 , 共 装入反应器的 D N一20催化剂 5. 5t体积为 0 3 7 , 8 . 。装入 R 18m , N一42保护剂 3 25t体积为 1 . 5 ,
1 2 催 化剂 干燥 .
在催化剂硫化前对催化剂 以介质 为 N 进行 2 脱水 干燥 , 干燥时间 2 , 9h 催化剂干燥过程 的温 度和升温速度见表 3 。
表 2 催化剂装填
良好 , 品质量满足 G 2 2 0 0 产 B 5 —20 轻柴油要求 。
1 装置 开工和 运行
1 1 催化剂性能和装填 .
4 7 。每千克催化剂处理原料 3 .4t 410t 07 。
2 2 装 置标定 结果 .
20 05年 4月 7日至 1 0日对装置 进行 了标 定, 标定的原料为 8 的催化裂化柴油和 2 的 0 0
汽柴油加制氢介绍.ppt
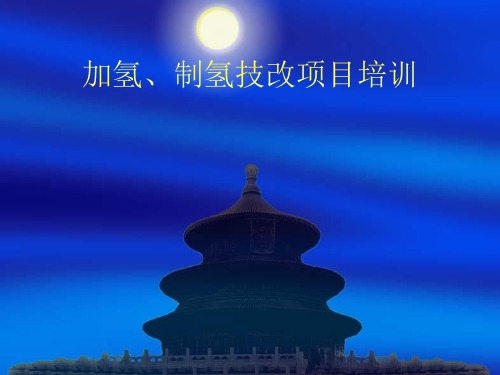
2) 产品氢气压力
≥2.4 MPa.G
3) 产品氢温度
≤40 ℃
4) PSA部分解吸气排气压力
≥0.03 MPa
5) PSA部分氢气回收率(设计值) ≥83 %
3、30万吨/年催化汽油加氢装置 该装置设计点为28.80万吨/年催化汽油,最大加工量为36万吨/年,最小加工量为20
万吨/年。装置主要原料为催化汽油,其主要性质为 :
产品设计目标为: 1) 加氢后汽油产品硫含量<150PPm(主要由专利商保证)。 2) 加氢处理RON损失≯1.5个单位(主要由专利商保证)。 3) 重汽油加氢单元C5+以上液体收率>99.6 m %。 三套装置与一期项目装置共用一套公用工程,并在此基础上新增2台1000m3原料调合罐, 以保证装置进料的平稳性;新上10000m3气柜一台,以缓解火炬系统的压力,并能达到合 理利用装置废气的目的。
该装置设计点为38.56万吨/年,其中直馏柴油、催化柴油、直馏汽油的比例分别为 57.05%、35.17%、7.78%,最大加工量为46万吨/年,最小加工量为26万吨/年。装置原 料主要性质为:
装置产品设计目标为:
1) 精制柴油硫含量: 2) 精制汽油(石脑油)干点: 3) 精制柴油闪点:
≤350ppm ≤200℃ ≥55℃
2 、生产流程简述 1) 生产流程简述 ①反应部分
自罐区来的原料油,按预期的原料比例,首先进入原料调合罐进行调和,然
后在原料油缓冲罐(V3001)液面和流量控制下混合,经原料油脱水器 (SW3001)脱水(保证原料水含量低于350ppm),再通过原料油过滤器(FI3001) 滤去原料中大于25微米的颗粒,然后进入原料油缓冲罐(V3001)。原料油缓冲 罐采用燃料气进行保护。来自原料油缓冲罐(V3001)的原料油经加氢进料泵 (P3001A,B)增压至9.2MPa(G),在流量控制下,经反应流出物/原料油换热器 (E3003A,B)换热后,与混合氢混合进入反应流出物/反应进料换热器(E3001A、B、 C),然后经反应进料加热炉(F3001)加热至反应所需温度,进入加氢精制反应 器(R3001)。该反应器设置三个催化剂床层,床层间设有注急冷氢设施。来自 加氢精制反应器(R3001)的反应流出物,经反应流出物/反应进料换热器 (E3001A、B)、反应流出物/低分油换热器(E3002)、反应流出物/反应进料 换热器(E3001C)、反应流出物/原料油换热器(E3003A、B)依次与反应进料、 低分油、原料油换热,然后经反应流出物空冷器(A3001)冷却至50℃,最后经 反应流出物水冷器(E3011)冷却至45℃进入高压分离器(V3002)。为了防止 反应流出物中的铵盐在低温部位析出,通过注水泵(P3002A、B)将除盐水注至 反应流出物空冷器(A3001)上游侧的管道中。
柴油加氢装置
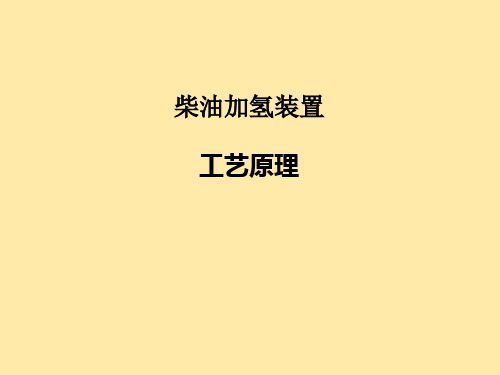
精制反应器内发生的反应
含硫有机物
催化剂
H2
烃类
含氮有机物
H2
催化剂
烃类
含氧有机物
H2
催化剂
烃类
金属有机物
H2
催化剂
烃类
烯烃
催化剂
H2
烷烃
H2S NH3 H2O 金属单质
与重整精制反应不同有:烃类碳数不同,杂质含量不同。 与重整精制反应相同有:均为放热反应,体积缩小反应。
低 分 罐
精制油去分馏塔 污水
在改质反应器内发生的主要反应第1、2步反应,
十六烷值为零
十六烷值约20以上
非柴油组分
想避免第3步反应的发生,就要控制好反应深度,即反应 温度、反应压力、反应空速、氢油比等。
新氢 原料泵
柴油加氢精制装置反应系统工艺流程
循环氢压缩机 冷却器
排放氢
加热炉
1
2
高
低分气
分
罐
低
高 分 罐
污水
冷氢
低分气
低 分 罐
精制油去分馏塔 污水
高分罐分离的是油、水、氢气三相的。
新氢 原料泵
柴油加氢精制装置反应系统工艺流程
循环氢压缩机 冷却器
排放氢
加热炉
1
2
高
低分气
分
罐
低
污水
分 罐
精制反应器
改质反应器
冷氢
精制油去分馏塔 污水
排除的污水中,含有H2S、NH3,这是物 理方法第一次脱除S、N、O元素。
催化剂
烯烃
催化剂
H2
烃类 烃类 烃类 烃类 烷烃
柴油加氢装置(汽柴油生产技术课件)
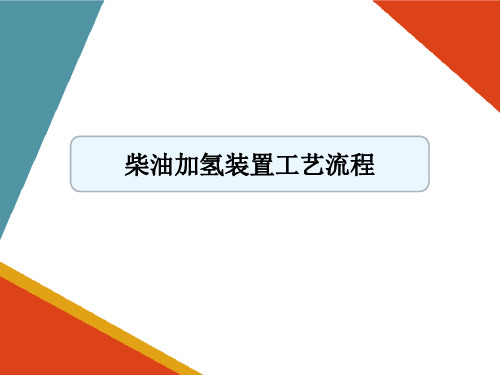
高分罐
LIC 排污
循环氢
LI 低分罐
图5—9 高分罐液位控制示意图
高分罐液位是油相液面高度。偏
高油相和气相分离效果将下降,偏低易形 成高压串低压导致分馏塔操作紊乱。
高分罐界位是水相与油相的界面
高度。偏高油带水,偏低水带油。
高分罐液位的影响因素:
1、高分罐与低分罐压差变化; 2、原料泵出口流量变化; 3、高分罐温度变化。
精制柴油十六烷值偏低,说明反应没有达到部分达到了第2步反应, 也即反应深度不够工艺要求。
1、反应温度偏低; 2、反应压力偏低;
3、催化剂活性偏低; 4、空速偏大。
1、塔顶压力偏 低; 2、塔顶温度偏 高;
精制油从低分罐来 原料泵
回流罐 粗汽油
分 馏 塔
粗汽油干点偏高?
柴油出装置
塔底的轻组分没有气化 上升到塔顶:
低分气
高
分
罐
低
分
分
馏
罐
塔
图5—10 低分罐压力控制示意图
低分罐的作用,一是分担些分馏塔
顶负荷,再是环节高压直接到低压而导致 分离塔的操作紊乱。
低分罐压力的影响因素:
1、高分罐压力变化; 2、分馏塔压力变化; 3、低分罐顶气体出口流量变化; 4、低分罐出口换热器的压降变化。
低分气
从高分罐来 低分罐
石脑油去催化重整装置
分
馏
塔
精制柴油溴价不合格的原
因?
柴油出装置
精制油从低分罐来 原料泵
回流罐
石脑油去催化重整装置
分馏Βιβλιοθήκη 塔精制柴油硫含量超标?
柴油出装置
循环氢压缩机
2、高分罐排污力度 不够工艺要求
新氢
柴油加氢技术总结

柴油加氢技术总结2#柴油加氢装置开工总结宋火军1.开工前的准备1.1 学习装置理论知识生产低硫、低芳烃、低密度、高十六烷值得清洁柴油是今后世界范围内的柴油生产总趋势。
如何满足符合日趋苛刻的车用柴油标准,生产出符合环保要求的清洁柴油将成为炼油技术进步的一个重要课题。
柴油燃料质量升级的趋势与汽油类似,最主要的是对于硫含量的控制,同时对于柴油产品指标中的十六烷值、芳烃含量、冷流动性、密度等也提出了更为严格的要求。
二次加工的柴油含有相当多的硫、氮及烯烃类物质,油品质量差,安定性不好,储存过程容易变质,对直馏柴油而言,由于原油中硫含量升高,环保法规日趋严格,已经不能直接作为产品出厂,也需要经过加氢精制处理。
柴油加氢精制的生产原理就是在一定温度、压力、氢油比、空速条件下,借助加氢精制催化剂的作用,有效的使油品中的硫、氮、氧、非烃类化合物转化为响应的烃类和H2S、NH3和H2O。
另外,少量的重金属则截留在催化剂中,同时使烯烃和部分芳烃饱和,从而得到安定性、燃烧性、情节性都较好的优质柴油产品和粗汽油(裂解料)。
本装置中大量循环氢的存在能保证气相为连续相,液相为分散相,被气相打散的液相在固定床催化剂上从上至下以液滴的形态流过催化剂床层,从而发生一系列的加氢反应。
循环氢在其中的关键作用是:(1)维持反应所需的氢分压,用来维系气相中的氢气向油相溶解的推动力。
(2)控制催化剂床层的温升。
(3)稀释反应物流杂质的浓度,促进深度脱杂质的反应。
1.2 学习开工方案在开工前两个月,车间开始组织操作人员学习开工方案,让每个人对开工都心里有数,了解每一个步骤,提高了操作人员的操作水平,为这次成功的开工打下了基础。
1.3 联系调度,提供合格氮气,在系统催化剂干燥时能满足供应。
1.4 硫化剂与试车用直馏柴油准备充足。
2.催化剂干燥催化剂在包装、储运和装填中,都难免吸附一定水分,吸附水会降低催化剂的活性和强度。
因此催化剂要在预硫化前进行脱水。