300万吨年直馏柴油加氢精制装置简介
柴油精制流程

一、装置简介1、装置组成装置组成:装置由反应部分(包括新氢、循环氢联合压缩机组)、分馏部分、干气脱硫部分、公用工程部分组成。
2、生产方案柴油加氢精制装置采用加氢精制催化剂DN200,以直馏柴油和催化裂化柴油混合油为原料,经过催化加氢反应进行脱硫、脱氢、烯烃饱和及部分芳烃饱和,生产精制柴油,保证柴油达到GB2522000轻柴油质量标准。
二、主要工艺技术路线1、原料油过滤为了防止放反应器因进料中的固体颗粒堵塞导致压降过大而造成的非正常停工,在装置内设置自动反冲洗过滤器,脱除原料油中大于25微米的固体颗粒。
2、原料油惰性气体保护因为原料油与空气接触会生成聚合物和胶质,为有效防止结垢,原料油缓冲罐采用脱硫燃料气气封。
3、高压空冷器前注水加氢过程中生成的H2S、NH3,在一定温度下会生成NH4HS结晶,沉积在空冷器管束中,导致系统压降增大。
因此在反应流出物进入空冷器前注入脱盐水来溶解铵盐结晶析出。
4、高压换热器采用双壳程、螺纹锁紧环形式,提高换热效率,减少换热面积,节省投资。
5、从工艺流程的优化、高效换热设备的应用、新型内构件的设计技术应用等多方面考虑,采用综合节能技术,降低装置的能耗。
6、采用炉前混氢方案,提高换热器效率和减缓加热炉结焦程度。
7、采用板焊结构热壁反应器。
反应器内件包括入口扩散器、分配盘、冷氢箱、出口收集器等,使进入反应器中催化剂床层的物流分布均匀,催化剂床层的径向温差小。
8、反应器入口温度通过调节加热炉燃料来控制,第二、第三床层入口温度通过调节急冷氢量来控制。
三、装置工艺流程原则工艺流程图附后,工艺流程叙述如下:1、反应部分原料油自装置外来,首先经原料油/低分油换热器(E1109)与低分油换热,然后通过原料油过滤器(F11101)进行过滤,除去原料中大于25μm的颗粒,过滤后的原料油进原料油聚结器脱水,然后进入原料油缓冲罐(V1101),再经加氢进料泵(P1101A/B)升压后,在流量控制下,与混合氢混合作为混合进料。
石化公司加氢精制装置设计方案
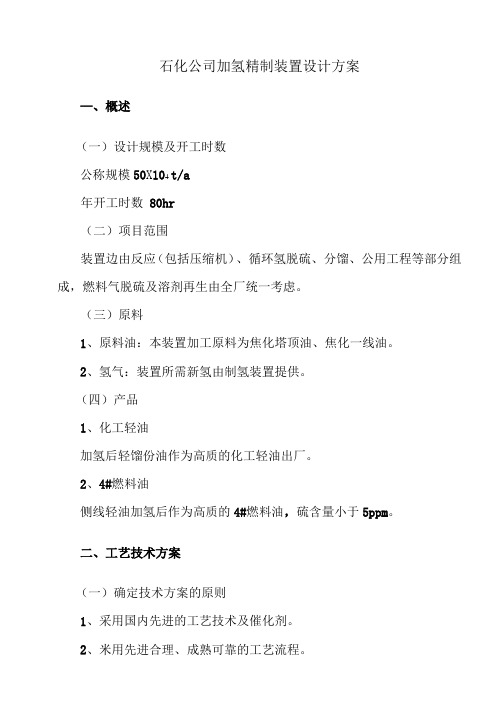
石化公司加氢精制装置设计方案—、概述(一)设计规模及开工时数公称规模50X104 t/a年开工时数80hr(二)项目范围装置边由反应(包括压缩机)、循环氢脱硫、分馏、公用工程等部分组成,燃料气脱硫及溶剂再生由全厂统一考虑。
(三)原料1、原料油:本装置加工原料为焦化塔顶油、焦化一线油。
2、氢气:装置所需新氢由制氢装置提供。
(四)产品1、化工轻油加氢后轻馏份油作为高质的化工轻油出厂。
2、4#燃料油侧线轻油加氢后作为高质的4#燃料油,硫含量小于5ppm。
二、工艺技术方案(一)确定技术方案的原则1、采用国内先进的工艺技术及催化剂。
2、米用先进合理、成熟可靠的工艺流程。
3、选用性能稳定、运转周期长的机械设备。
4、提高自动控制、安全卫生和环境保护水平。
(二)国内外加氢技术现状加氢精制是指油品在催化剂、氢气和一定的压力、温度条件下,含硫、氮、氧的有机化合物分子发生氢解反应,烯烃和芳烃分子发生加氢饱和反应的过程。
加氢精制的目的是脱硫、脱氮和解决色度及贮存安定性的问题,满足日益严格的环保要求。
常规的加氢精制工艺已有几十年的历史,技术上非常成熟。
新进展主要体现在高活性、高稳定性、低成本新型催化剂的研究和开发上。
荷兰AKZO公司目前最好的脱硫催化剂是KF-752和KF-840.KF-752的活性已是60年代中期相应产品的1.7倍,多用于直馏原料。
对于二次加工原料则采用KF-840O埃克森研究和工程公司(ER&E)于1992年实现商业应用的催化剂RT-601,采用新型A12O3载体,使用先进的促进剂浸渍技术,催化剂活性高,特别适合于加工重质、劣质原料。
在加工直硫柴油时,活性与市场上最好的催化剂相当。
独联体的列宁石油化工科学生产联合体开发的KrM-70催化剂也具有很高活性。
在压力为3.0MPa,空速为3.0h-i,温度为350°C时,可将直硫柴油的硫含量由1.03%降至0.26m%,脱硫率达到99.7%o国内近年来也已开发了多种具有世界先进水平的、高性能的馏分油加氢精制催化剂。
1.2Mt/a柴油加氢装置开工及运行分析
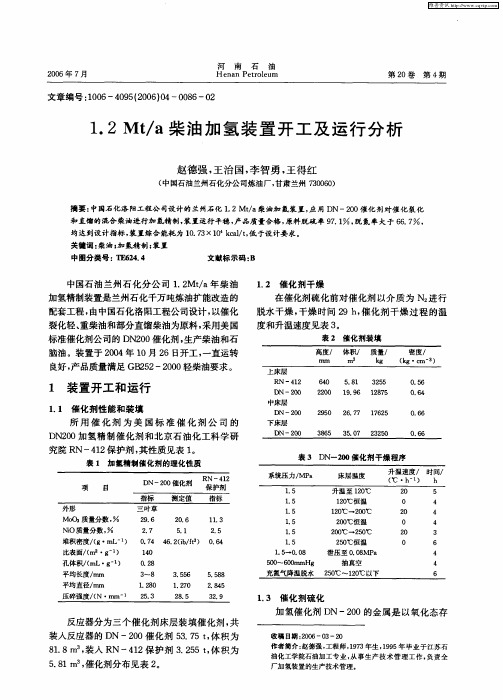
系统存 硫/ g l 【
上硫率 ,
由表 5可见上硫率达 9 . 1 , 8 6 满足加氢催 化 剂 的流化 要求 。
表 8 原 料和产品性质 ( 第二次标定 )
2 装置运行和标定
2 1 装置 运行 .
装置 20 0 4年 1 0月 2 日开 工 , 2 0 6 到 0 6年 2 月底已累计加工量达到 16 23 1t其 中加工催 5 7 , 化柴 油 10 010t直 馏柴 油 5 0 1t焦 化柴 油 2 3 、 88 7 、
o2 .8
3 ~8 12 0 .8
356 .5 120 .7 2. 85 558 . 8 285 . 4 3 9 2.
压碎强度/ N ・ 2 一 ( n l1 n 2 . Βιβλιοθήκη 31 3 催化 剂硫化 .
加氢催化剂 D N一 0 2 0的金 属是 以氧化态存 反应器分为三个催化剂床层装填催化剂 , 共 装入反应器的 D N一20催化剂 5. 5t体积为 0 3 7 , 8 . 。装入 R 18m , N一42保护剂 3 25t体积为 1 . 5 ,
1 2 催 化剂 干燥 .
在催化剂硫化前对催化剂 以介质 为 N 进行 2 脱水 干燥 , 干燥时间 2 , 9h 催化剂干燥过程 的温 度和升温速度见表 3 。
表 2 催化剂装填
良好 , 品质量满足 G 2 2 0 0 产 B 5 —20 轻柴油要求 。
1 装置 开工和 运行
1 1 催化剂性能和装填 .
4 7 。每千克催化剂处理原料 3 .4t 410t 07 。
2 2 装 置标定 结果 .
20 05年 4月 7日至 1 0日对装置 进行 了标 定, 标定的原料为 8 的催化裂化柴油和 2 的 0 0
柴油加氢裂化装置最大量生产重石脑油和喷气燃料改造总结

柴油加氢裂化装置最大量生产重石脑油和喷气燃料改造总结李志敏(中海石油宁波大榭石化有限公司,浙江省宁波市315812)摘要:2.0Mt/a工业加氢裂化装置设计原料为环烷基柴油,主要生产重石脑油和超低硫柴油。
受市场环境变化影响,对产品结构进行了调整,最大量生产重石脑油和喷气燃料。
通过调整产品切割点、增设分馏塔等措施实现了该目的。
工业运转结果表明,以柴油为原料,该装置生产的重石脑油和优质喷气燃料的收率分别为52.98%,29.35%,高价值产品收率超过82.3%,柴油收率仅3.63%。
各馏分产品性质优良,其中喷气燃料烟点30.2mm,硫、氮质量分数均小于0.5μg/g,冰点-53℃。
关键词:柴油加氢裂化装置 重石脑油 喷气燃料 改造方案 标定数据 国内炼油产品逐步走向产能过剩,柴汽比逐步降低[1 3]。
然而为了满足国内外非生产性税费一致性的要求,目前仍然暂缓征收喷气燃料产品消费税,对于有喷气燃料需求的企业,提高喷气燃料/柴油比例成为优化产品结构的重要手段,使柴油加氢装置增产喷气燃料成为现实选择。
通过将直馏柴油精制装置改为生产直馏喷气燃料、调整加氢裂化转化率和切割点等方式可以增产喷气燃料[4 6]。
中海石油宁波大榭石化有限公司2.0Mt/a工业燃料油加氢裂化装置上周期主要以环烷基直馏柴油为原料,生产超低硫柴油和重石脑油等,重石脑油收率达到50%以上。
该装置需要将未转化的柴油最大量地转化为喷气燃料。
GB6537—2018《3号喷气燃料》要求其闪点(闭口)不低于38℃,10%回收温度不高于205℃,50%回收温度不高于232℃。
另外市场上优质喷气燃料大多要求烟点高于25mm,冰点低于-50℃,闪点在40~50℃。
装置前期产品以柴油和石脑油为主,主分馏塔重馏分侧线抽出压力不高,如何在工业装置上满足侧线喷气燃料的产品质量要求也成为现实难题[7 8]。
结合装置实际运行情况,优选了中国石油化工股份有限公司大连石油化工研究院催化剂及工艺,依托中石化洛阳工程有限公司进行设计,在2018年底进行了装置改造建设。
加氢操作规程

加氢操作规程第⼀章装置概况第⼀节装置简介⼀、装置概况:装置由中国⽯化集团公司北京设计院设计,以重油催化裂化装置所产的催化裂化柴油、顶循油,常减压装置⽣产的直馏柴油和焦化装置所产的焦化汽油、焦化柴油为原料,经过加氢精制反应,使产品满⾜新的质量标准要求。
新《轻柴油》质量标准要求柴油硫含量控制在0.2%以内,部分⼤城市车⽤柴油硫含量要求⼩于0.03%。
这将使我⼚的柴油出⼚⾯临严重困难,本装置可对催化柴油、直馏柴油、焦化汽柴油进⾏加氢精制,精制后的柴油硫含量降到0.03%以下,满⾜即将颁布的新《轻柴油》质量标准,缩⼩与国外柴油质量上的差距,增强市场竞争⼒。
该项⽬与50万吨/年延迟焦化装置共同占地⾯积为217m×103m即22351m2;装置建设在140万吨/年重油催化裂化装置东侧,与50万吨/年延迟焦化装置建在同⼀个界区内,共⽤⼀套公⽤⼯程系统和⼀个操作室。
本装置由反应(包括新氢压缩机、循环氢压缩机部分)、分馏两部分组成。
装置设计规模:120×104t/a。
⼆、设计特点:1、根据⼆次加⼯汽、柴油的烯烃含量较⾼,安定性差,胶质沉渣含量多的特点,本设计选⽤了三台⼗五组⾃动反冲洗过滤器,除去由上游装置带来的悬浮在原料油中的颗粒。
2、为防⽌原料油与空⽓接触氧化⽣成聚合物,减少原料油在换热器、加热炉炉管和反应器中结焦,原料缓冲罐采⽤氮⽓或燃料⽓保护。
3、反应器为热壁结构,内设两个催化剂床层,床层间设冷氢盘。
4、采⽤国内成熟的炉前混氢⼯艺,原料油与氢⽓在换热器前混合,可提⾼换热器的换热效果,减少进料加热炉炉管结焦,同时可避免流体分配不均,具有流速快、停留时间短的特点。
5、为防⽌铵盐析出堵塞管路与设备,在反应产物空冷器和反应产物/原料油换热器的上游均设有注⽔点。
6、分馏部分采⽤蒸汽直接汽提,脱除H2S、NH3,并切割出付产品⽯脑油。
7、反应进料加热炉采⽤双室⽔平管箱式炉,炉底共设有32台附墙式扁平焰⽓体燃烧器,⼯艺介质经对流室进⼊辐射室加热⾄⼯艺所需温度,并设有⼀套烟⽓余热回收系统,加热炉总体热效率可达90%。
中石化武汉分公司主要生产装置简介

中石化武汉分公司主要生产装置简介中国石油化工股份有限公司武汉分公司(简称武汉分公司),在中国石化集团武汉石油化工厂整体重组改制中于2000年2月28日成立,主要从事石油加工及部分石油化工产品的生产。
武汉分公司属于以生产燃料油为主的石化企业,是中国500家最大工业企业之一,产品质量保证体系通过ISO9002国际质量体系认证。
公司前身为武汉石油化工厂,始建于1971年,扩建于1975年,于1977年投产,目前已开工生产装置19套。
工厂自投产以来,原油加工能力由250万吨/年增加到500万吨/年。
中国石油化工股份有限公司武汉分公司为生产燃料油为主的石化企业。
加工手段齐全,具有较强的深度加工能力,原油一次加工能力可达500万吨/年,主要加工管混油、进口油和海洋油。
主要产品有:汽油(90#、93#、97#),灯用煤油、航空燃料油、柴油(5#、0#、-10#),石脑油、溶剂油、环烷酸、MTBE、专用重油(1#、2#、3#)、180#重油、工业片状硫磺、石油焦、石油液化气、双壁波纹管等15种产品,12种产品获部优、省优,-10#柴油获国家银质奖,所有产品均通过ISO9002国际质量体系认证。
产品行销鄂、湘、川、渝、云、贵等12个省区,工业片状硫磺等部分产品进入国际市场。
各装置主要情况见下表。
一.#常减压装置简介1#常减压装置以加工管输油为主,原设计年生产能力为250万吨,2004年元月通过扩能改造,处理能力达到350万吨/年。
它包括电脱盐装置、蒸馏装置、电化学精制及减粘装置。
主要产品有:石脑油、200#溶剂油、分子筛料、3#航煤、柴油、燃料油。
二.1#催化裂化装置简介催化剂裂化装置为高低并列式提升管催化剂裂化装置,加工原料主要为减压渣油、蜡油等,改造后设计年生产能力为100万吨。
它主要由反再系统、分馏系统、吸收稳定系统、脱硫系统、脱硫醇系统等组成。
主要产品有:干气、液化气、酸性气、90#汽油、轻柴油、油浆。
三.联合装置简介联合装置由2#常压装置、2#催化裂化装置两部分组成。
加氢精制
1 加氢精制的工艺流程因原料而异,但基本原理是相同 的,如图所示,包括反应系统、生成油换热、冷却、分离 系统和循环氢系统三部分。
2 工艺流程介绍
* 原料油经原料油聚结脱水器脱水后,通过原料油过滤器 除去大于20um的固体颗粒,最后进入原料油缓冲罐。原 料油缓冲罐中的原料经原理泵升压后,与反应产物换热至 215℃,再与来自循环氢压缩机换热和循环氢加热炉的热 循环氢混合后形成15.9MPa、260 ℃的混氢油,在进入反 应器中进行加氢精制反应。 * 自加氢精制反应器来的14.7MPa、402 ℃反应产物经换热 后与加氢裂化反应产物一起进入空冷器,冷却后的反应产 物进入高压分离器和冷低压分离器进行油、气、水三相分 离。冷低分油进入分馏部分,低分气 进入延迟焦化装置, 含硫污水进入酸性水气体装置。
2 加氢原料油中断事故处理预案
一 事故确认与响应 • 缓冲罐液面下降,液位低限报警 • 反应进料指示下降或回零,其控制阀开大,低 限报警 • 反应进料泵停泵指示灯亮 原因 • 原料泵出现故障致供应中断 • 反应进料泵故障 • 反应泵进料控制阀关 • 装置停电
二 应急处理措施
• 罐区原料供应中断 1 联系调度罐区,了解原料中断原因,若短时间内能恢复供料,根据原 料缓冲罐的液位情况,适当降低进料量或改长循环操作 2 若短时间内不能恢复供料,降反应器入口至300摄氏度,装置改闭路 循环 3 若长时间不能恢复进料,按正常停工处理 • 反应进料泵故障 1 立即手动关闭进料控制阀,并将反应器入口逐步降至200摄氏度以下 等待恢复进料 2 到现场关进料泵,原料改界区返回,必要时将控制阀上下游阀关闭 3 分馏系统改短循环操作,多余产品可改污油去加氢原料,停吹汽,关 进塔根阀 4 当反应进料泵恢复后,按开工步骤恢复开工;若长时间不能恢复进料, 按停工步骤进行停工 反应进料控制阀关,可立即到现场改副线控制
加氢型酸性水汽提装置腐蚀分析与防护
文章编号:1000 7466(2018)01 0073 05 加氢型酸性水汽提装置腐蚀分析与防护马红杰a,龚树鹏b(中国石油独山子石化分公司a.研究院;b.科技信息处,新疆独山子 833699)摘要:采用现场宏观腐蚀检查、管线超声波测厚、腐蚀介质分析、在线腐蚀探针监测及能谱分析等方法对加氢型酸性水汽提装置的酸性水储罐、汽提塔顶酸性气线弯头进行了腐蚀分析。
分析结果表明,酸性水中的少量氯化物及酚类物质极易穿透涂层,使得腐蚀介质与金属基体发生腐蚀反应,导致涂层鼓泡、脱落。
汽提塔顶酸性气线弯头背弯处减薄最为严重,主要原因为湿硫化氢腐蚀,而流体的冲刷磨损起到了促进作用,两者循环反复进行导致弯头背弯处快速减薄并穿孔。
针对装置的腐蚀情况,提出了应用效果较好的防护措施。
关键词:储罐;汽提装置;酸性水;腐蚀分析;防护中图分类号:TQ050.7;TE962 文献标志码:B 犱狅犻:10.3969/j.issn.1000 7466.2018.01.015犆狅狉狉狅狊犻狅狀犃狀犪犾狔狊犻狊犪狀犱犘狉狅狋犲犮狋犻狅狀狅犳犎狔犱狉狅犵犲狀犪狋犻狅狀犜狔狆犲犃犮犻犱犻犮犠犪狋犲狉犛狋狉犻狆狆犻狀犵犝狀犻狋犕犃犎狅狀犵 犼犻犲犪,犌犗犖犌犛犺狌 狆犲狀犵犫(DushanziPetrochemicalCompanyofCNPC,a.ResearchInstitute;b.ScienceandTechnologyBureau,Dushanzi833699,China)犃犫狊狋狉犪犮狋:Theacidicwaterstoragetankandacidgaslineofstrippingtowertopwereanalyzedbymeansofin sitemacroscopiccorrosioninspection,lineultrasonicthickness,corrosionmedium,on linecorrosionmonitoringprobeandenergyspectrumanalysismethodforhydrogenationtypeacidicwaterstrippingdevice.Analysisresultsindicatedthatasmallamountofchlorideandphe nolofacidicwaterpenetratedthesurfacecoatingeasily,andcorrosionreactionhappenedbetweencorrosivemediumandmetallicmatrix,whichresultedinbubbling,andfallingoff.Themainrea sonofcorrosionreductiononacidgaslineofstrippingtowertopwaswethydrogensulfidecorro sion,andfluidicerosivewearpromotedcorrosionreduction,leadingtoperforationundertheac tionofcorrosionandfluidicerosivewear.Finally,inviewofthecorrosionsituationofdevices,thebetterprotectivemeasureswereputforward.犓犲狔狑狅狉犱狊:storagetank;strippingunit;acidicwater;corrosionanalysis;protection 某石化公司加氢型酸性水汽提装置于2009年建成投产,生产能力为37t/h。
加氢工艺简介课堂PPT
另外,由于较高效益驱动性,延迟焦化 工艺的得到极大发展,其中焦化汽柴油收率 均在50~60%,但是,由于焦化汽柴油含硫 含氮量较高,烯烃含量高,油品安定性较差, 焦化汽柴油不能直接作为车用,需进行脱去 硫氮化合物,烯烃饱和等深加工,来改善油 品性质。所以,建延迟焦化装置必建加氢精 制装置,否则产品质量得不到解决,那就严 重影响到企业效益。因此加氢装置是石油化 工必建项目,是解决二次油品创优,增加效 益的出路。
8
②环烷酸加氢
5 加氢脱金属 原料油中金属及非金属是以化合物形态存在于
油中,通过加氢反应金属化合物氢解,金属杂质 截留在催化剂上,达到脱出金属非金属的目的。
9
第四节 加氢工艺流程
焦化汽 柴油
加氢 精制
蒸汽汽 提脱硫
出装置
加氢石脑油
分馏
加氢柴油 出装置
10
11
12
ቤተ መጻሕፍቲ ባይዱ
13
第五节 加氢精制催化剂
2 加氢脱硫反应 ①硫醇加氢反应
RSH +H2 →H2S +RH ②硫醚加氢反应
RSR′ +H2 →R′SH + RH R′H +H2S
③二硫化物加氢反应
RSSR + H2 →2RSH — 2RH +H2S RSR +H2S
6
④噻吩加氢反应
3 加氢脱氮反应 ① 吡啶加氢
7
②吡咯加氢 4 加氢脱氧反应 ①苯酚加氢
目录
第一节 第二节 第三节 第四节 第五节 第六节 第七节
加氢精制工艺发展简介 加氢精制原料与产品 加氢精制化学反应机理 加氢精制工艺流程 加氢精制催化剂 加氢装置设备 加氢装置安全知识
1
第一节 工艺发展简介
随着石油化工的发展,我国原油品种不 断增加,油田部分油井所产原油中硫、氮、 氧非烃化合物含量较高,严重影响成品油 的质量,尤其高硫原油对炼油设备有着严 重腐蚀性。为了解决炼油设备腐蚀,油品 质量问题,七十年代,发展催化加氢精制 工艺,通过加氢精制装置脱去原料油中硫、 氮、氧非烃化合物,解决了设备腐蚀、油 品质量大问题。
柴油加氢精制装置节能减排措施
柴油加氢精制装置节能减排措施本文以云南石化公司180万吨/年直流柴油加氢装置为例,对我国自主设计的大型直流柴油加氢精制装置,节能减排措施进行深入研究。
该公司主要生《欧盟车用柴油标准》IV类标准柴油产品。
通过进行装置的首次开工调解和试验验证,此装置在节能减排方面有着自己的特点,自2017年8月首次开工以来有效降低了柴油加氢精制装置的能耗,获取较好的节能减排效果和经济效益。
标签:柴油加氢精制装置;节能减排;措施1 引言云南石化280万吨/年直柴加氢精制装置由寰球工程公司辽宁分公司设计,采用中国石油大庆化工研究中心研制的柴油加氢精制催化剂,以直馏柴油为原料,通过加氢精制生产精制柴油。
设置一台加氢反应器,(预留一台反应器空地,方便以后的技术升级和改造)装填PHF-101柴油加氢精制催化剂及PHF-101P-2、PHF-101P-3系列保护剂。
结合国内现有同类装置的生产经验,反应部分采用热高分和炉前混氢流程,分馏部分采用脱硫化氢汽提塔单塔汽提流程方案,有利于保证装置长周期、平稳、安全运行,提高产品质量和收率,降低装置物耗和能耗。
2 柴油加氢精制装置节能减排调整及措施2.1 调整冷热进料比例云南石化280万吨/年直柴加氢精制装置共有两路进料,一路是来自罐区的冷直馏柴油只有25℃左右的常温进料。
另一路是来自常减压的热直柴有100℃左右的温度。
开工初期进料主要以冷料为主,通过精制柴油-原料油换热器与精制柴油换热,换热后的原料也只能到80-90℃左右,加热炉负荷很大超过了设计负荷。
经后来经过调整,将冷热比例调整到1:9原料的温度达到140-150℃,有效的节约了燃料气的使用量由原来的280m3/h降低到了200 m3/h,节约越80 m3·h 的消耗。
2.2 原料和循环氢双换热节能原料油自装置外来经原料油过滤器进行过滤,除去原料中大于25?m的颗粒,再经过原料油预过滤器,然后通过精制柴油-原料油换热器与精制柴油换热,换热后的原料从100℃换热至140-150℃油进入滤后原料油缓冲罐再经反应进料泵升压后,在流量控制下,与混合氢混合作为混合进料。
- 1、下载文档前请自行甄别文档内容的完整性,平台不提供额外的编辑、内容补充、找答案等附加服务。
- 2、"仅部分预览"的文档,不可在线预览部分如存在完整性等问题,可反馈申请退款(可完整预览的文档不适用该条件!)。
- 3、如文档侵犯您的权益,请联系客服反馈,我们会尽快为您处理(人工客服工作时间:9:00-18:30)。
二、公用工程消耗及辅助设施
8.4、辅助材料消耗
名称 保护剂(TK-10 ) 保护剂(TK-711 ) 精制剂 (UF-120 ) 惰性瓷球( ) Ф3、Ф6、Ф19 DMDS(SF-121D)
Hale Waihona Puke 一次装入量2.294t 5.564t 194.515t
序 引进项目内容 号
数量 备注
1 加氢进料泵组
2 电机国产
2 联合压缩机组
2
3 液力透平
1
4 反应加热炉炉管、急弯弯管
√
5 部分高压临氢阀门、管道及管配件 √
6 DCS系统
1
7 ESD系统
1
一、概 述
1.7、进出装置物料走向
序号 物料名称
流量kg/h 温度℃ 压力Mp 走向
1 直柴
72971
50
0.75 自罐区来
独山子石化 1000万吨/年炼油工程新区炼油
第一联合装置
300×104t/a
直馏柴油加氢精制装置简介
目录
一、装置概述 二、公用工程情况 三、工艺流程介绍及工艺特点 四、原料及主要产品性质 五、主要自动控制方案 六、装置联锁方案 七、主要设备及引进设备简介 八、电气
一、概 述
独山子石化1000万吨/年炼油及120万吨/年 乙烯技术改造工程(炼油部分)第一联合装置 包括四个装置,即:200×104 t/a加氢裂化、 300×104 t/a直馏柴油加氢精制、80×104 t/a 催焦化柴油加氢精制、8×104 m3n/h制氢。其 中300×104 t/a直馏柴油加氢精制装置的原料 为1000×104 t/a常减压蒸馏装置直馏柴油。开 工近期生产硫含量<50ppm的精制柴油产品,最 终设计目标生产硫含量<10ppm、多环芳烃≤2v %的精制柴油产品。
公称规模 300×104 t/a
实际处理量 306.5×104 t/a
年开工时数 8400
h
操作弹性 50-110
%
一、概 述
1.3、平面布置及占地
平面布置在满足有关防火、防爆及安全卫生 标准和规范要求的前提下,尽量采用露天化、集 中化和按流程布置,并考虑同类设备相对集中, 以达到减少占地、节约投资、降低能耗、便于安 全生产操作和检修管理,实现安全生产的目的。 装置占地:
二、公用工程消耗及辅助设施
8.2公用工程消耗
序号 1 2 3 4 5 6 7 8 9 10 11
名称 除氧水 循环冷水 循环热水 1.0MPa 蒸汽 燃料气 氮气 非净化风 净化风 新鲜水 汽提净化水 凝结水
流量Kg/h 13187 235300 235300 12800 1200m3n/h
6566
生产方案
运转周期 反应器入口压力,MPa(G) 反应器入口氢分压,MPa(G) 体积空速,h-1/主剂 体积空速,h-1/保护剂 总体积空速,h-1 反应器入口温度,℃ 反应器出口温度,℃ 催化剂床层平均温度,℃ 循环氢量,nm3/m3进料 反应器入口 化学氢耗,w%
近期设计目标
SOR EOR 6.40 6.40 5.75 5.75
温度℃ 压力Mp 协作关系
66
1.45 自系统管网来
30
0.45 自系统管网来
38
0.20 至系统管网
300 1.3
自系统管网来
40
0.5
常温 0.6
常温 0.6
自系统管网来 自系统管网来 自系统管网来
常温 0.6
自系统管网来
常温 0.95 自系统管网来
66
0.5
自酸性水汽提装置来
109 0.6
至系统管网
2.9
至加氢裂化装置
9 汽提塔顶气 3634
38
0.38 至加氢裂化装置
10 含硫污水
20471
53
0.5
至酸性水汽提
11 含油污水
40
常压 至污水处理场
12 地下污油
50
0.6
至加氢裂化装置
二、公用工程消耗及辅助设施
8.1公用工程
该装置和80×104 t/a催焦化柴油加氢 精制共用地上公用工程设施,这两套装 置再和200×104 t/a加氢裂化装置共用地 下公用工程设施。该装置与同时建设的 常减压、焦化、加氢裂化、制氢、催焦 化柴油加氢精制等装置共用一个中心控 制室、生产办公楼及有关生活设施。
二、公用工程消耗及辅助设施
8.3能耗分析
装置能耗:408.63MJ/吨原料(9.8 ×104 kcal/t原料)
1 装置为热进料,反应加热炉相应热负荷 较小
2 原料泵采用透平驱动,回收能量203kW
3 充分回收反应流出物热量,反应流出物 空冷入口温度较低
4 新氢进装置原料较高,为2.4Mpa,新氢 压缩机用电较小
一、概 述
1.1、设计单位和工艺技术
300×104 t/a直馏柴油加氢精制装置由 反应部分(包括压缩机)、分馏部分及公 用工程三部分构成。
装置界区内的全部工程内容,由中国石 化洛阳石化工程公司设计。
装置采用UOP公司的最新柴油加氢精制 工艺技术,工艺包由UOP公司提供。
一、概 述
1.2、装置能力
2 直柴
291883 100 0.75 自常减压来
3 氢气 4 燃料气
15959m3n/h 40
2.4
自系统来
1300m3n/h 40
0.5
自系统来
5 石脑油或航煤
40
0.75 自罐区
6 精制柴油
362335 50
0.6
至罐区
7 粗石脑油
正常无量 38
1.0max 至加氢裂化装置
8 低分气
168
54
2.5 30.91 2.31 340 349 351 360 348 356
169 0.19 0.19
最终设计目标
SOR EOR 6.57 6.57 5.91 5.91
1.4 30.91 1.34 344 351 358 365 354 361
169 0.28 0.27
一、概 述
1.6、引进设备材料
230×90=20700m2
(含催焦化柴油加氢精制)
一、概 述
1.4、装置定员
序号 岗位 操作 操作定员 管理 技术 辅助 名称 班数 人/ 合计 人员 人员 人员 班
1 班长 4 1 4 2 内操 4 2 8 由一联合装置
统一考虑设置 3 外操 4 3 12
4 总计
12
一、概 述
1.5、主要操作条件
41t 44t
名称 缓蚀剂
年用量 t
15
三、工艺流程介绍及工艺特点
3.1、催化剂 精制催化剂:UF-120 保护剂:TK-10、TK-711
3.2.1、工 艺 流程 反应部分流程简图
反应进料 加热炉
加氢精制反应器
循环氢压缩机
新氢压缩机入口分液罐 新氢
反应流出物/热 原料油换热器