热处理分类
金属热处理工艺的分类及代号

金属热处理工艺的分类及代号金属热处理工艺的分类及代号(GB/T12693-90)1.分类:热处理分类由基础分类和附加分类组成.(1)基础分类根据工艺类型、工艺名称和实践工艺的加热方法,将热处理工艺按三个层次进行分类,见附录表1-1.(2)附加分类对基础分类中某些工艺的具体条件的进一步分类.包括退火、正火、淬火、化学热处理工艺加热介质(附录表1-2);退火冷却工艺方法(附录1-3);淬火冷却介质或冷却方法(附录表(1-4);渗碳和碳氮共渗的后续冷却工艺(附录表1-5),以及化学热处理中非金属、渗金属、多元共渗、熔渗四种工艺按元素的分类.2.代号(1)热处理工艺代号标记规定如下:5热处理 X工艺类型 X工艺名称 X 加热方法附加分类工艺代号(2)基础工艺代号用四位数字表示.第一位数字“5”为机械制造工艺分类与代号中表示热处理的工艺代号;第二,三,四位数字分别代表基础分类中的第二,三,四层次中的分类代号。
当工艺中某个层次不需分类时,该层次用0代号。
(3)附加工艺代号它用英文字母代表。
接在基础分类工艺代号后面。
具体代号见附录表1-2至附录表1-5。
(4)多工序热处理工艺代号多工序热处理工艺代号用破折号将各工艺代号连接组成,但除第一工艺外,后面的工艺均省略第一位数字“5”,如5151-331G表示调质和气体渗碳。
(5)常用热处理工艺代号见附录表1-6。
附录表1-1.热处理工艺分类及代号工艺总称代号工艺类型代号工艺名称代号加热方法代号热处理 5 整热处理体1退火 1加热炉 1正火 2淬火 3感应 2正火和淬火 4调质 5火焰 3稳定化处理 6固溶处理,水韧处理7固溶处理和时效8表面热处理2表面淬火和回火 1电阻 4物理气相沉淀 2化学气相沉淀 3激光 5等离子体化学气相沉淀 4化学热处理3渗碳 1 电子束6碳氮共渗 2渗氮 3 等离子体7氮碳共渗 4渗其他非金属 5其他8渗金属 6多元共渗7溶渗8附录表1-2.加热介质及代号加热介质固体液体气体真空保护气氛可控气氛流态床代号S L G V P C F附录表1-3退火工艺代号退火工艺去应力扩散再结晶石墨化去氢退火球化退火等温退火代号o d r g h s n附录表1-4淬火冷却介质和冷却方法及代号冷却介质和方法空气油水盐水有机水溶液盐浴压力淬火双液淬火分级淬火等温淬火形变淬火冷处理代号a o wb y s p d m n f z附录表1-5渗碳,碳氮共渗后冷却方法及代号冷却方法直接淬火一次加热淬火二次加热火表面淬火代号g r t b附录表1-6常用热处理工艺及代号工艺代号工艺代号热处理 5000 石墨化退火5111g感应加热热处理 5002 去氢退火5111h火焰热处理 5003 球化退火5111s激光热处理 5005 等温退火5121电子束热处理 5006 正火5121离子热处理 5007 淬火5131真空热处理 5000V 空冷淬火5131a保护气氛热处理 5000P 油冷淬火5131o可控气氛热处理 5000C 水冷淬火5131w流态床热处理 5000F 盐水淬火5131b有机水溶液淬火5131y整体热处理 5100 盐浴淬火5131s退火 5111 压力淬火5131p去应力退火 5111o 双价质淬火5231d扩散退火 5111d 分级淬火5131m再结晶退火 5111r 等温淬火5131n变形淬火 5131f 表面淬火和回火 521淬火及冷处理 5131z 感应淬火和回火5212感应加热淬火 5132 火焰淬火和回火 5213真空加热淬火 5131V 电接触淬火和回火 5214保护气氛加热淬火 51312P 激光淬火和回火 5215可控气氛加热淬火 5131C 电子束淬火和回火 5216流态床加热淬火 5131F 物理气相沉积5228盐浴加热分级淬火 5131L 化学气相沉积5238盐浴加热分级淬火 5131mL 等离子体化学气相沉积5248盐浴加热盐浴分级淬火513Ls+m淬火和回火 514 化学热处理530调质 5151 渗碳521稳定化处理 5161 固体渗碳5311S固溶处理,水韧处理5171 液体渗碳5311L固溶处理和时效 5181 气体渗碳5311G表面热处理5200。
钢的热处理

t2 t1
等温时间t M转变量与等温时间的关系
M转变是在Ms~Mf温度范围内迚行,与停留时间无关。
3
转变不完全
多数钢的Mf点在室温以下,因此冷却到室温时 仍会有A存在,称为残余A,用Ar表示。A的含碳 量越高,Ms、Mf就越低,所以Ar就越多。
100 80 60 40 20
4
瞬间形核,高速长大
Ms Mf 20 温度(℃) M转变量与温度的关系
E G A3
900
γ
Accm Arcm Acm
860
820
780
α+γ Ar3 P
Ac3
S
γ+Fe3C
K
740
临界点,它是制定热处理工
艺时选择加热和冷却温度的 依据。
700
α+Fe3C
660 0 0.2 0.4 0.6 0.8 1.0 1.2 1.4
w(C)%
3 钢在加热时的组织转变
3.1 A的形成
A A→F3C A→P A→B Ms
21 32
38
40 43 50 55
HRC
温度/℃
Mf
1 10 102 103 104 105
时间/s
影响C曲线的因素
⑴ 成分的影响
① 含碳量的影响:共析钢的C曲线最靠右,其余向左移动。
Ms 与Mf 点随含碳量增加而下降。
② 合金元素的影响
除Co 外, 凡溶入奥氏体的合金元素都使C 曲线右移。
4
原始组织的影响 ——原始组织越细,相界面越多,越有利于A形核。
4 钢在冷却时的组织转变
连续冷却转变 热处理时常用的冷却方式
等温转变
由于冷却过程大多不是极其缓慢的,得到的组织是不平衡组织,因
热处理零件的结构工艺性

1.热处理的定义指将钢在固态下加热、保温、冷却,以改变钢的内部组织结构,从而获得需要的性能的一种工艺。
2.热处理的特点只通过改变工件的组织来改变性能,不改变其形状。
3.热处理的适用范围只适用固态下发生相变的材料。
4.热处理原理描述热处理时钢中组织转变的规律。
5.热处理工艺根据热处理原理而制定的温度、时间、介质等参数6.热处理分类(1)根据加热、冷却方式的不同及钢的组织变化特点的不同,将热处理工艺分类如下:普通热处理:退火、正火、淬火和回火表面热处理:表面淬火、化学热处理其他热处理:真空热处理、形变热处理、激光热处理(2)根据在零件生产过程中所处的位置和作用不同来分类预备热处理:清除前道工序的缺陷,改善其工艺性能,确保后续加工顺利进行。
最终热处理:赋予工件所要求的使用性能的热处理。
7.热处理时的过热和过冷现象由于实际加热或冷却时,又过热或过冷现象,因此,将钢加热时的实际转变温度分别用Ac1、Ac 3、Accm来表示,冷却时的实际转变温度分别用Ar1、Ar3、Arcm来表示。
5.2 钢在加热时的转变加热是热处理的第一道工序。
加热分两种:一种在临界点A1以下的加热,不发生组织变化,一种是在临界点A1以上的加热,目的是获得均匀的奥氏体组织,这一过程称为奥氏体化。
5.2.1 奥氏体的形成过程钢在加热时奥氏体的形成过程也是一个形核和长大的过程。
以共析钢为例,其奥氏体化过程可简单地分为4个步骤,如下图所示。
第一步:奥氏体晶核形成奥氏体晶核首先在铁素体和渗碳体的界面上形成,因为晶面处的成分和结构对形核有利。
第二步:奥氏体晶核长大奥氏体晶核形成后,便通过碳原子的扩散向铁素体和渗碳体方向长大。
第三步:残余渗碳体的溶解铁素体在成分和结构上比渗碳体更接近于奥氏体,因而先于渗碳体消失,而残余渗碳体则随保温时间延长不断溶解直至消失。
第四步:奥氏体均匀化渗碳体溶解后,其所在部位碳的含量仍比其他部位高,需通过较长时间的保温使奥氏体成分逐渐趋于均匀。
钢的热处理分类

钢的热处理分类
1. 退火!嘿,就像让钢好好地休息一下。
比如说打造一把剑,退火能让剑身更稳定,没那么脆啦,不容易断哦!
2. 正火呀,这就类似给钢来个“提神醒脑”。
你想想啊,制造汽车零件的时候,正火一下,零件就更结实耐用咯!
3. 淬火哦,哇,这可是让钢变得超级强硬的关键一步。
好比运动员要去参加重要比赛,经过淬火的钢就是那最厉害的选手!就像做刀具,淬火后那才叫锋利呢!
4. 回火呢,有点像给刚猛的钢“降降火”。
比如你看那弹簧,经过回火处理,才既有弹性又不会轻易变形呀!
5. 表面热处理,这可真是个神奇的操作。
就像给钢化个美美的妆,让它的表面更耐磨更耐腐蚀呀。
好比自行车的链条,做了表面热处理,就能长久如新啦!
6. 化学热处理,哎呀呀,这可是能给钢带来特别性质的魔法呢!就好像给钢赋予了超能力,像齿轮经过这样的处理,性能那叫一个棒!
7. 渗碳处理呀,是不是感觉很陌生?其实就像给钢加餐补充营养一样。
做一些机械零件的时候,渗碳处理让它们更强大哟!
8. 渗氮处理,这个厉害啦!简直是给钢穿上了一层坚固的盔甲。
像一些高精密的仪器零件,渗氮处理后质量杠杠的嘞!
9. 碳氮共渗,哇哦,这是双重强化啊!就如同给钢来了个组合拳,让它的性能翻倍呀。
总之,钢的热处理分类就是这么奇妙又重要,每一种都有它独特的作用和效果,能让钢变得更出色呀!。
常用热处理设备分类

常用的热处理设备可以分为以下几类:
1. 炉窑类:包括炉窑、炉膛、炉膛炉等。
炉窑类设备主要用于加热和保温处理,常见的有电阻炉、气体炉、真空炉等。
2. 淬火设备:用于对金属材料进行淬火处理,使其获得所需的硬度和强度。
常见的淬火设备有盐浴淬火炉、油浴淬火炉、水淬设备等。
3. 回火设备:用于对淬火后的金属材料进行回火处理,以减轻内应力和提高韧性。
常见的回火设备有回火炉、回火炉膛等。
4. 等离子设备:利用等离子体的高温和高能量对材料进行表面改性和处理。
常见的等离子设备有等离子喷涂设备、等离子刻蚀设备等。
5. 氮化设备:用于对金属材料进行氮化处理,以提高其硬度和耐磨性。
常见的氮化设备有氮化炉、氮化炉膛等。
6. 淬火油设备:用于提供淬火油,对金属材料进行淬火处理。
常见的淬火油设备有淬火油槽、淬火油泵等。
以上是常见的热处理设备分类,不同的设备适用于不同的热处理工艺和材料。
常用热处理分类
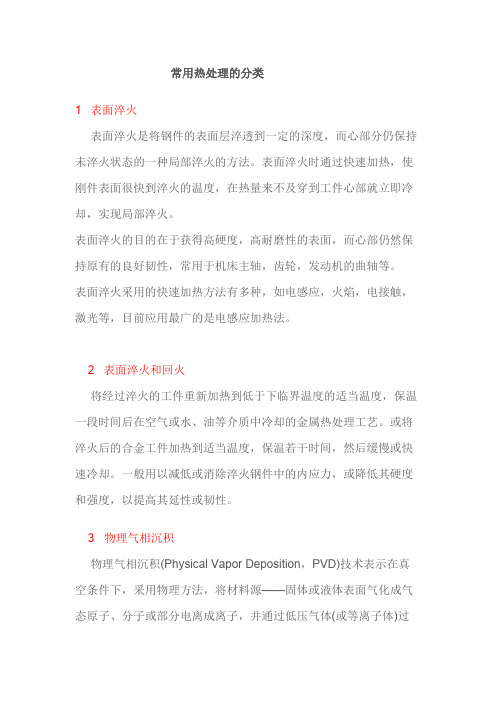
常用热处理的分类1 表面淬火表面淬火是将钢件的表面层淬透到一定的深度,而心部分仍保持未淬火状态的一种局部淬火的方法。
表面淬火时通过快速加热,使刚件表面很快到淬火的温度,在热量来不及穿到工件心部就立即冷却,实现局部淬火。
表面淬火的目的在于获得高硬度,高耐磨性的表面,而心部仍然保持原有的良好韧性,常用于机床主轴,齿轮,发动机的曲轴等。
表面淬火采用的快速加热方法有多种,如电感应,火焰,电接触,激光等,目前应用最广的是电感应加热法。
2 表面淬火和回火将经过淬火的工件重新加热到低于下临界温度的适当温度,保温一段时间后在空气或水、油等介质中冷却的金属热处理工艺。
或将淬火后的合金工件加热到适当温度,保温若干时间,然后缓慢或快速冷却。
一般用以减低或消除淬火钢件中的内应力,或降低其硬度和强度,以提高其延性或韧性。
3 物理气相沉积物理气相沉积(Physical Vapor Deposition,PVD)技术表示在真空条件下,采用物理方法,将材料源——固体或液体表面气化成气态原子、分子或部分电离成离子,并通过低压气体(或等离子体)过程,在基体表面沉积具有某种特殊功能的薄膜的技术。
物理气相沉积的主要方法有,真空蒸镀、溅射镀膜、电弧等离子体镀、离子镀膜,及分子束外延等。
发展到目前,物理气相沉积技术不仅可沉积金属膜、合金膜、还可以沉积化合物、陶瓷、半导体、聚合物膜等。
4 化学气相沉积化学气相沉积(Chemical vapor deposition,简称CVD)是反应物质在气态条件下发生化学反应,生成固态物质沉积在加热的固态基体表面,进而制得固体材料的工艺技术。
它本质上属于原子范畴的气态传质过程。
与之相对的是物理气相沉积(PVD)。
整体热处理1 退火退火是一种金属热处理工艺,指的是将金属缓慢加热到一定温度,保持足够时间,然后以适宜速度冷却。
目的是降低硬度,改善切削加工性;消除残余应力,稳定尺寸,减少变形与裂纹倾向;细化晶粒,调整组织,消除组织缺陷。
常用热处理分类

常用热处理的分类1表面淬火表面淬火是将钢件的表面层淬透到一定的深度,而心部分仍保持未淬火状态的一种局部淬火的方法。
表面淬火时通过快速加热,使刚件表面很快到淬火的温度,在热量来不及穿到工件心部就立即冷却,实现局部淬火。
表面淬火的目的在于获得高硬度,高耐磨性的表面,而心部仍然保持原有的良好韧性,常用于机床主轴,齿轮,发动机的曲轴等。
表面淬火采用的快速加热方法有多种,如电感应,火焰,电接触,激光等,目前应用最广的是电感应加热法。
2表面淬火和回火将经过淬火的工件重新加热到低于下临界温度的适当温度,保温一段时间后在空气或水、油等介质中冷却的金属热处理工艺。
或将淬火后的合金工件加热到适当温度,保温若干时间,然后缓慢或快速冷却。
一般用以减低或消除淬火钢件中的内应力,或降低其硬度和强度,以提咼其延性或韧性。
3物理气相沉积物理气相沉积(Physical Vapor Deposition , PVD)技术表示在真空条件下,采用物理方法,将材料源一一固体或液体表面气化成气态原子、分子或部分电离成离子,并通过低压气体(或等离子体)过程,在基体表面沉积具有某种特殊功能的薄膜的技术。
物理气相沉积的主要方法有,真空蒸镀、溅射镀膜、电弧等离子体镀、离子镀膜,及分子束外延等。
发展到目前,物理气相沉积技术不仅可沉积金属膜、合金膜、还可以沉积化合物、陶瓷、半导体、聚合物膜等。
4化学气相沉积化学气相沉积(Chemical vapor deposition,简称CVD)是反应物质在气态条件下发生化学反应,生成固态物质沉积在加热的固态基体表面,进而制得固体材料的工艺技术。
它本质上属于原子范畴的气态传质过程。
与之相对的是物理气相沉积(PVD )。
整体热处理1退火退火是一种金属热处理工艺,指的是将金属缓慢加热到一定温度,保持足够时间,然后以适宜速度冷却。
目的是降低硬度,改善切削加工性;消除残余应力,稳定尺寸,减少变形与裂纹倾向;细化晶粒,调整组织,消除组织缺陷。
热处理工艺
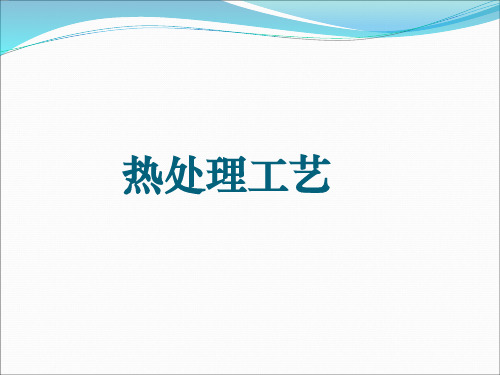
可减少内应力,用于小尺寸工件
盐浴炉
可编辑课件PPT
23
4. 等温淬火法
将工件在稍高于Ms的盐浴或碱 浴中保温足够长时间,从而获 得下贝氏体组织的淬火方法
经等温淬火零件具有良好的综 合力学性能,淬火应力小
适用于形状复杂及要求较高的 小型件
可编辑课件PPT
24
第三节 钢的淬透性
❖淬透性是钢的主要热处理性能 ❖是选材和制订热处理工艺的重要依据之一
可编辑课件PPT
41
在光镜下M回为黑色,A’为白色
0.2%C时,不析出-碳化物,只发生碳在位错附近的 偏聚
2. 残余奥氏体分解
200~300℃时, 由于马 氏体分解,A所受的压 力下降,Ms上升,A’ 分解为-碳化物和过饱 和铁素体,即M回
回火马氏体
可编辑课件PPT
42
3. -碳化物消失,渗碳体Fe3C析出
回火是指将淬火钢加热到A1 以下的某温度保温后冷却 的工艺
一、回火的目的
螺杆表面的 淬火裂纹
1. 减少或消除淬火内应力, 防止变形或开裂
2. 获得所需要的力学性能:淬火钢一般硬度高,脆性 大,回火可调整硬度、韧性
可编辑课件PPT
38
3. 稳定尺寸:M和A’都是非平衡组织,有自发向平 衡组织转变的倾向;回火可使M与A’转变为平衡 或接近平衡的组织,防止使用时变形
大于300℃,由于Fe3C粗化, 马氏体转变为铁素体,硬度 直线下降
可编辑课件PPT
46
三、回火脆性
淬火钢的韧性并不总是随 温度升高而提高
在某些温度范围回火时, 会出现冲击韧性下降的现 象,称回火脆性
- 1、下载文档前请自行甄别文档内容的完整性,平台不提供额外的编辑、内容补充、找答案等附加服务。
- 2、"仅部分预览"的文档,不可在线预览部分如存在完整性等问题,可反馈申请退款(可完整预览的文档不适用该条件!)。
- 3、如文档侵犯您的权益,请联系客服反馈,我们会尽快为您处理(人工客服工作时间:9:00-18:30)。
热处理的作用就是提高材料的机械性能、消除残余应力和改善金属的切削加工性。
按照热处理不同的目的,热处理工艺可分为两大类:预备热处理和最终热处理。
1. 预备热处理
预备热处理的目的是改善加工性能、消除内应力和为最终热处理准备良好的金相组织。
其热处理工艺有退火、正火、时效、调质等。
(1)退火和正火
退火和正火用于经过热加工的毛坯。
含碳量大于0.5%的碳钢和合金钢,为降低其硬度易于切削,常采用退火处理;含碳量低于0.5%的碳钢和合金钢,为避免其硬度过低切削时粘刀,而采用正火处理。
退火和正火尚能细化晶粒、均匀组织,为以后的热处理作准备。
退火和正火常安排在毛坯制造之后、粗加工之前进行。
(2)时效处理
时效处理主要用于消除毛坯制造和机械加工中产生的内应力。
为避免过多运输工作量,对于一般精度的零件,在精加工前安排一次时效处理即可。
但精度要求较高的零件(如座标镗床的箱体等),应安排两次或数次时效处理工序。
简单零件一般可不进行时效处理。
除铸件外,对于一些刚性较差的精密零件(如精密丝杠),为消除加工中产生的内应力,稳定零件加工精度,常在粗加工、半精加工之间安排多次时效处理。
有些轴类零件加工,在校直工序后也要安排时效处理。
(3)调质
调质即是在淬火后进行高温回火处理,它能获得均匀细致的回火索氏体组织,为以后的表面淬火和渗氮处理时减少变形作准备,因此调质也可作为预备热处理。
由于调质后零件的综合力学性能较好,对某些硬度和耐磨性要求不高的零件,也可作为最终热处理工序。
2. 最终热处理
最终热处理的目的是提高硬度、耐磨性和强度等力学性能。
(1)淬火
淬火有表面淬火和整体淬火。
其中表面淬火因为变形、氧化及脱碳较小而应用较广,而且表面淬火还具有外部强度高、耐磨性好,而内部保持良好的韧性、抗冲击力强的优点。
为提高表面淬火零件的机械性能,常需进行调质或正火等热处理作为预备热处理。
其一般工艺路线为:下料--锻造--正火(退火)--粗加工--调质--半精加工--表面淬火--精加工。
(2)渗碳淬火
渗碳淬火适用于低碳钢和低合金钢,先提高零件表层的含碳量,经淬火后使
表层获得高的硬度,而心部仍保持一定的强度和较高的韧性和塑性。
渗碳分整体渗碳和局部渗碳。
局部渗碳时对不渗碳部分要采取防渗措施(镀铜或镀防渗材料)。
由于渗碳淬火变形大,且渗碳深度一般在0.5~2mm之间,所以渗碳工序一般安排在半精加工和精加工之间。
其工艺路线一般为:下料-锻造-正火-粗、半精加工-渗碳淬火-精加工。
当局部渗碳零件的不渗碳部分采用加大余量后,切除多余的渗碳层的工艺方案时,切除多余渗碳层的工序应安排在渗碳后,淬火前进行。
(3)渗氮处理
渗氮是使氮原子渗入金属表面获得一层含氮化合物的处理方法。
渗氮层可以提高零件表面的硬度、耐磨性、疲劳强度和抗蚀性。
由于渗氮处理温度较低、变形小、且渗氮层较薄(一般不超过0.6~0.7mm),渗氮工序应尽量靠后安排,为减小渗氮时的变形,在切削后一般需进行消除应力的高温回火。