三维焊接平台夹具标准
焊装夹具定位设计技术标准
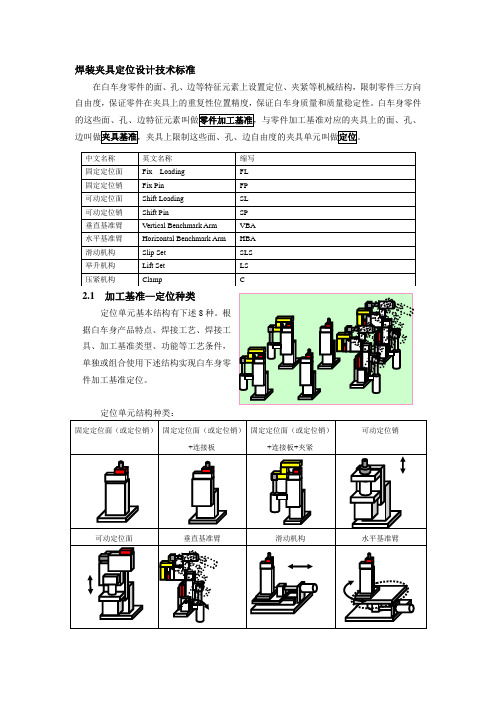
焊装夹具定位设计技术标准在白车身零件的面、孔、边等特征元素上设置定位、夹紧等机械结构,限制零件三方向自由度,保证零件在夹具上的重复性位置精度,保证白车身质量和质量稳定性。
白车身零件2.1 加工基准—定位种类定位单元基本结构有下述8种。
根据白车身产品特点、焊接工艺、焊接工具、加工基准类型、功能等工艺条件,单独或组合使用下述结构实现白车身零件加工基准定位。
定位单元结构种类:2.2定位单元构成定位单元通常由定位块(定位销)、连接板、支座、夹紧块、夹紧臂、铰链、气缸、导向8种基本功能件组成,复杂定位单元需要增加限位块、导轨、二层支座等功能件(如下图所示)。
2.3(白车身零件)加工基准加工基准需要同时满足四大工艺(冲压、焊装、涂装、总装)使用,具有一致性。
加工基准在产品设计时通过工艺评审,最终确定,是完整产品组成的一部分。
按零件面、孔、边的几何特征,加工基准可以划分为:面基准—S(s)、孔基准—H(h)、边基准—E(e);按零件上几何元素功能,加工基准可以划分为:正基准、辅助基准、变换基准等;结合上述两种划分方法,加工基准划分为以下13种,便于使用和管理。
2.4加工基准—定位单元位置精度不同加工基准的定位精度要求不同。
分为三类:孔基准—定位销、面(边)基准—定位块、特殊辅助面基准—定位块。
(1)孔基准—定位销◆孔基准类型:◆定位销、连接板孔配合公差:h7/H7◆ 定位销位置公差:±0.1mm◆ 定位销连接处直径公差:h7◆ 连接板孔直径公差:H7(2) 面基准—定位块◆ 面基准类型:◆ 定位块位置公差:±0.1mm(3) 特殊辅助面基准—定位块◆ 特殊辅助面基准类型:◆定位块位置精度:+0/-0.5㎜e2.5 加工基准—定位单元刚性为保证制造质量的稳定性,要求定位单元的定位件(块、销)装配后其工作方向位置变化<0.1mm 。
既要保证夹具骨架(平台)的结构刚性,还需要保证定位单元的结构刚性。
夹具标准

3、 装配: 3.1. 紧固螺栓采用内六角螺栓,公制标准件,在钢板厚度允许条件下,内六角头应沉入钢板表面 。 紧固需带弹簧垫圈; 3.2. 尽量从上方和侧面安装螺栓; 3.3. 定位销采用GB120-86标准销,自带装卸螺孔; 4、检测 4.1. 零件的检测采用常规量具检测; 4.2. 部件的检测采用常规检测或3D检测; 4.3. 夹具的整体检测采用3D检测,并出具最终检测报告。 4.4 夹具精度: 4.4.1主定位销的位置度公差:±0.1㎜; 4.4.2定位销的加工精度:直径+0.00~-0.05mm; 4.4.3定位面的装配公差:±0.2㎜; 4.4.4 翻转定位机构的重复定位精度:±0.2㎜(Φ200处㎜); 4.5 移动单元: 4.5.1 带有轴承及防尘装置; 4.5.2.设有限位块; 4.5.3.大型移动机构(重量大于80Kg)采用直线轴承; 4.5.4.小型移动机构采用无油润滑轴承; 5 、定位夹紧单元:
5.1 定位销应二维可调,定位销带定位面的应三维可调; 5.2. 定位夹紧块在定位夹紧方向一维调节; 5.3. 尽可能采用标准支承、定位销、连接块、过渡块和限位块,做成易换、易调整、易维修; 6、 材料表面及热处理: 6.1定位块:一般采用16mm厚的钢板,特殊部位采用19mm厚的钢板,材料采用45钢,调质T235 和发黑处理; 6.2定位销:40Cr钢,表面氧化处理,淬火 HRC55-60 ; 6.3 支承座:采用铸钢支承座,为本公司标准支撑座。 7、夹紧方式: 7.1.采用气缸自动夹紧或嘉手的手动夹钳夹紧; 8、 铭牌及标牌: 8.1. 设备设有本公司铭牌及设备标牌; 8.2. 铭牌固定上底板上。铭牌上标明夹具名称、夹具图号、使用车型、验收日期、制造商名称等 , 使用厚度为1㎜的铝板制做; 9、油漆: 9.1 生产线工装夹具均喷涂磁漆(颜色由买主规定),定位面及定位销要求发黑处理,夹具基准 面 要求防锈处理; 9.2 用颜色区分固定零件和运动零件; 9.3 外购件、标准件、非金属材料、铝件等为本色,不油漆; 9.4 所有的表面氧化零件均不油漆。
焊接夹具制造标准

1、目的:本标准规定了焊装夹具制造的技术要求,保持合格产品的质量状态。
2、适用范围:本标准适用于本公司底盘研发中心的焊接夹具。
3、夹具制造规范:3.1夹具BASE板:按照《焊接夹具设计标准》第二条中的2.1执行。
3.2夹具机构组件:3.2.1 夹具焊接件在焊接后须经过焊接应力退火。
焊缝不允许有夹渣、气孔、焊道应丰满,消除焊渣并进行相应的防锈处理。
3.2.2 机构各部分的零件表面粗糙度:Ra1.6~Ra3.2 ;定位销工作面粗糙度:Ra0.8。
3.2.3调整垫片的规格:按照《焊接夹具设计标准》中第六条执行。
3.2.4 气缸选型:按照《焊接夹具设计标准》中第八条执行。
3.2.5 夹具定位、导向部位需整体防护,防止焊接飞溅;在定位面、气缸杆等部位,有防飞溅装置;直线导轨有金属弹性防护,以防止焊接飞溅的粘附。
3.2.6 夹具需做防锈处理。
3.2.7 移动单元带有直线导轨或带固体润滑剂的导套及防尘罩。
3.3定位销要求:3.3.1按照《焊接夹具设计标准》第四条中的4.3执行。
3.3.2所有零部件加工尺寸须符合图纸,不允许零件适配。
3.4定位块、压紧块要求:按照《焊接夹具设计标准》第五条执行。
3.4.1 支撑块与产品形面接触部位依照产品数模的形状进行CNC加工,误差不得大于0.2mm。
3.4.2各接触面与固定安装面的表面加工粗糙度为Ra3.2,定位销孔的粗糙度为Ra1.6。
3.5夹具标识要求:夹具需在非加工表面做永久性醒目标识。
(标识内容包括:夹具所加工零件名称、零件产品号、生产厂家代号、生产日期、夹具外形尺寸。
)3.6夹具制造的一般要求:3.6.1夹具的焊接件均采用焊后热处理退火消除内应力,再进行机械加工。
3.6.2夹具装配使用的固定销,采用带内螺纹的圆柱销,所有组焊夹具所用的定位销规格应统一。
3.6.3夹具上有危险的部位,需有警告标示牌。
3.7夹具标牌、铭牌:按照《焊接夹具设计标准》第十条执行。
3.8夹具外观颜色要求:骨架:清漆黄色RAL1012柠檬黄;底梁上表面:透明清漆;端子箱:浅灰色(RAL7035);L板、压头、螺钉:黑色(RAL9011);防护罩:厚度3mm 黑色(RAL9011);气管:a进气:蓝色 b排气:黑色4、夹具气路要求:按照《焊接夹具设计标准》中第九条执行。
夹具设计标准标准
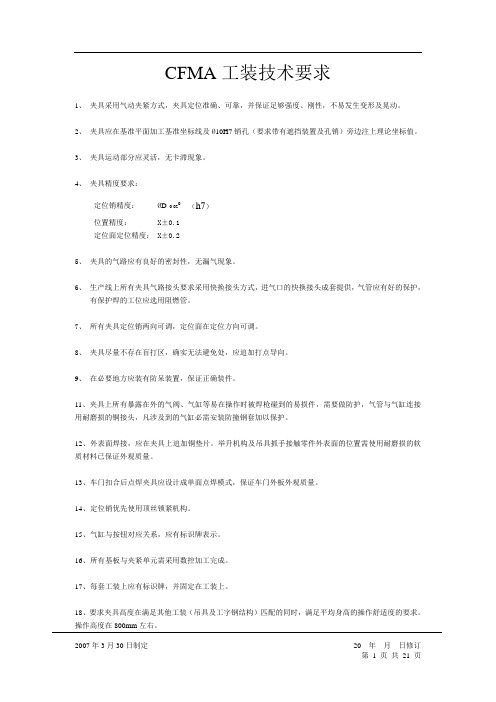
CFMA工装技术要求1、夹具采用气动夹紧方式,夹具定位准确、可靠,并保证足够强度、刚性,不易发生变形及晃动。
2、夹具应在基准平面加工基准坐标线及Ø10H7销孔(要求带有遮挡装置及孔销)旁边注上理论坐标值。
3、夹具运动部分应灵活,无卡滞现象。
4、夹具精度要求:定位销精度:ØD-0.020 (h7)位置精度:X±0.1定位面定位精度: X±0.25、夹具的气路应有良好的密封性,无漏气现象。
6、生产线上所有夹具气路接头要求采用快换接头方式,进气口的快换接头成套提供,气管应有好的保护,有保护焊的工位应选用阻燃管。
7、所有夹具定位销两向可调,定位面在定位方向可调。
8、夹具尽量不存在盲打区,确实无法避免处,应追加打点导向。
9、在必要地方应装有防呆装置,保证正确装件。
11、夹具上所有暴露在外的气阀、气缸等易在操作时被焊枪碰到的易损件,需要做防护,气管与气缸连接用耐磨损的铜接头,凡涉及到的气缸必需安装防撞钢套加以保护。
12、外表面焊接,应在夹具上追加铜垫片。
举升机构及吊具抓手接触零件外表面的位置需使用耐磨损的软质材料已保证外观质量。
13、车门扣合后点焊夹具应设计成单面点焊模式,保证车门外板外观质量。
14、定位销优先使用顶丝锁紧机构。
15、气缸与按钮对应关系,应有标识牌表示。
16、所有基板与夹紧单元需采用数控加工完成。
17、每套工装上应有标识牌,并固定在工装上。
18、要求夹具高度在满足其他工装(吊具及工字钢结构)匹配的同时,满足平均身高的操作舒适度的要求。
操作高度在800mm左右。
19、要求伸缩销机构需带有气缸内置或外置的THK导轨,且要求引出外置直线导轨的润滑加油嘴已便维护。
20、夹具设计时的定位需严格执行CFMA提供的定位Locator-drawing信息,需要改动的需与LAM相应工程师确认。
21、原则要求定位销采用MISUMI品牌,对于个别标准无法统一的定位销,需供应商列出清单并清晰不同点,与CFMA讨论一致后确定方案。
焊接夹具验收标准(含表格)

焊接夹具验收标准一、产品焊接夹具验收流程二、焊接夹具制造完成后,由乙方提出申请,甲方派出技术人员到乙方的现场进行焊接夹具预验收。
二、乙方必须提供以下记录,甲方才能进行预验收工作1、焊接夹具零部件质量检验记录:1)焊接工装外观质量检验。
1) 尺寸精度检验。
2) 焊接夹具材料及热处理检验。
3) 表面粗糙度检验。
2、焊接夹具装配检验记录。
3、焊接夹具动态检验记录。
4、经过清点的焊接夹具清单。
5、焊接夹具与其对应的夹具仕样书的吻合情况自检清单。
乙方根据上述记录整理成焊接夹具自检报告提供给甲方。
三、焊接夹具的预验收1、预验收依据:1)乙方提供并由甲方确认的验收标准。
2)产品数模。
3)焊接夹具技术要求。
4)焊接夹具验收技术要求。
2、预验收程序:1)焊接夹具动、静检验见后附表。
2)焊接夹具动、静检验合格后,在乙方场地进行试焊接,利用合格的冲压件,焊接成一台总成,如符检验精度标准,则视为焊接夹具预验收合格。
四、对焊接夹具预验收过程中存在的问题及应采取的措施,乙方必须记录并形成文件,且经双方签字确认。
若没有形成文件,甲方视为夹具没有经过本次的预验收。
五、包装运输1、焊接夹具在乙方工厂预验收合格后包装发运,包装箱内附包装清单一份。
同时发运焊接夹具设计图纸资料。
2、焊接夹具应进行防水、防锈处理,焊接夹具应装箱,以防止在运输过程中磕碰。
六:焊接夹具在甲方验收时,乙方必须派出技术人员和调整工人到甲方现场进行调试,甲方技术人员配合,在甲方的验收为焊接夹具的最终验收。
七:乙方调试焊接夹具的时间不能影响合同总体进度。
八、焊接夹具的终验收1、终验收的前提是焊接夹具符合《XXX技术要求》。
2、乙方在甲方场地进行焊接夹具的安装、调试并进行焊接。
3、乙方提供了完整的、符合要求的焊接夹具技术资料。
4、能连续稳定地生产出20台合格的总成,则焊接夹具终验收合格。
九、本附件与合同具有同等法律效力。
十、本附件未尽事宜,双方通过协商解决。
甲方代表签字:乙方代表签字:年月日年月日。
焊接制作标准及夹具设计

焊接夹具设计及制造标准总体技术要求:1、所有的夹具均采用气动控制压紧及车型转换方式(特殊规定可采用手动压紧器压紧或不用压紧)。
2、夹具应保证可靠的定位,防止变形,确保装配焊接质量和精度达到产品质量要求。
3、夹具工艺性能优良:各部件装配调整方便、人工焊接易于操作、产品取放方便、有足够的操作空间、操作方便快捷。
4、夹具上产品的高度应在700~800mm之间,对于四周焊接作业困难的应增加360°旋转转盘装置(特殊情况要求还需增加旋转定位锁紧装置)。
5、所有夹具须满足生产纲领的要求。
一、焊接件技术要求:1、焊缝高度不得<5mm、不允许有虚焊脱焊现象、重要部位须采用连续焊缝。
2、焊后清理焊渣、焊缝磨平。
所有部件在焊接后须退火消除应力再进行机加工。
-二、夹具底板1、夹具底板台面全部加工完成后厚度≮20mm,底板与槽钢等加强板料焊接前应校平,留有吊运点或叉车搬运位置,焊后应经退火处理和校平后再进行机加工等后续作业,加工完成后应对台面涂油处理。
2、加强筋规格选用标准(长方形的取最大值):(1)当夹具台面≤1400mm×1400mm时,底板的加强筋应采用10#以上槽钢;(2)当夹具台面>1400mm×1400mm时,底板的加强筋应采用16#以上槽钢;(3)当夹具台面>2000mm×2000mm时,底板的加强筋应采用20#以上槽钢;(4)底座周边的槽钢开口向外,中间加强筋用槽钢的间距不得>700mm.。
3、夹具台面的基准孔及网格坐标线:(1)基准孔:夹具台面上应留有两个坐标系的检测用基准孔,每个方向为两组,每组两个孔,孔径为φ10mm,孔距100mm.(在基准孔附近安装标牌或刻上钢字码,注明坐标数值)(2)网格坐标线:网格坐标线应与产品设计的坐标线对应。
深度及宽度均为0.5mm,间距为200mm.4、夹具台面的周边轮廓尽量与产品零件的轮廓相似,不得有突出的锐角,并尽量往里收,方便操作。
焊装夹具技术要求

附件:焊装夹具技术要求一、焊装夹具方案规划要求:1. 为了保证在产品加工过程中基准的统一,乙方在做夹具仕样书过程中需按照甲方提供的RPS基准系统来确定夹具主定位基准(改造项目需延用原有基准,并保证统一),定位孔及销的圆菱性必须与RPS一致,定位面可在RPS同一基准面上进行适当调整(50mm以内),且必须保证前后工序定位基准统一。
夹具定位点需在RPS定位点的基础上进行适当增加,并保证钣件充分定位。
定位基准若乙方有其它方案的,会签时提出与RPS的差异清单,经甲方书面同意后方可实施。
2. 夹具定位方案设计时,需充分考虑件的强度与定位精度,必要时可将RPS中的菱形定位销改为圆形以及可根据夹具的定位要求适当增加定位面,以保证件的精确、稳定定位。
3. 夹具定位方案设计时,需充分考虑夹具的作业性、结构设计的合理性,对甲方提供的工艺文件中要求的夹具结构、工序的划分可根据实际情况提出合理建议,经甲方书面同意后可进行适当的修改。
如乙方未提出异意的,乙方必须保证所设计、制造出来夹具的作业性、定位性完全满足甲方生产要求。
4. 夹具定位方案设计时,需充分考虑每套夹具上钣件的防错措施,需充分有效的防止左右件、类似件装错;一个件不同方位的装反等情况的发生。
二、夹具材质及热处理要求1.夹具底座BASE要求采用Q235 A板材和槽钢或方钢焊接而成,槽钢或方钢规格要求如下:BASE底板的焊缝采用非连续焊缝,焊后经热处理退火消除应力(不允许采用机械消除应力)并喷砂处理,对于以上要求必须提供充分证明或在加工时甲方将随时进行现场确认。
2.规制块(基准块、压块)必须采用45#钢,并经淬火处理,硬度值为(HRC30~35),表面应进行发黑处理。
3.支撑座采用焊接结构(或者采用铸钢件),不采用铸铁支撑座,支撑座板料厚应应≥15mm,焊后应作退火处理(铸钢件除外),消除应力;焊缝要求牢固、光滑平整、无缺陷;一般高度为150、200、250、300、350,能充分满足互换性要求。
三维柔性焊接平台

干适 涉用 的于 位不 置经 ;常 两拆 端卸 内的 六位 角置 扳; 手外 锁漏 紧部 位 有
1.设计制作精度高;可有效保证焊接产品尺寸;
2.重复定位精度高;不同产品可在一个基础件上精准模块化定位;
3.平台及附件可以延伸扩展;形成可调三维空间尺寸;能适合不同 产品规格的变化,提高了工装的利用率; 4.产品焊接时能快速装夹定位,快速拆卸;提高生产效率;
V型定位件
V型定位件使用动画
Ⅳ、锁紧件
快速锁紧销 快速锁紧销使用动画
两适 端用 扳于 手锁 锁紧 紧力 大 ; 不 经 常 拆 卸 的 位 置 ;
位适 无用 干于 涉拆 位卸 置快 ,, 手经 和常 内更 六换 角及 扳手 手旋 锁外 紧漏 部
位适 有用 干于 涉拆 的卸 位快 置, ;经 内常 六更 角换 扳及 手手 锁旋 紧外 漏 部
专用工装 工装设 计周期 包括机械手的采购时间和专用工装的前期设计时间。尤 其是专用工装的设计过程中必须要详细的了解每一个工 件的尺寸和焊接位置,需要设计者与使用者频繁交流才 可以完成图纸。(设计周期很长) 设计和加工完毕后,专用工装要在车间进行调试,由于 专用工装是针对单一工件开发的,必须详细的与相关工 件吻合,所以要想达到预想的效果,必须要经过反复的 调试才可完成 (调试时间比较长) 由于购入多规格型号多套专用工装,所以一次性投入的 成本很高。(很高) 作为一家公司,一定会不断的进行现有产品的改良和新 产品的开发。而开发试制的过程中同样需要新的焊接工 装。如果是用专用工装,那么一定要等专用工装的开发 设计调试后才能进行公司新产品的试制,这样会严重影 响公司研发的速度。(时间和成本都会严重浪费) 结构设计不可能统一标准化,存在大量非标件成本极高 ,加工难度大,质量难以控制! 专用工装只是针对特定的工件而开发,所以针对性很强 ,只适合单一产品的装夹需求。 焊接范围窄
- 1、下载文档前请自行甄别文档内容的完整性,平台不提供额外的编辑、内容补充、找答案等附加服务。
- 2、"仅部分预览"的文档,不可在线预览部分如存在完整性等问题,可反馈申请退款(可完整预览的文档不适用该条件!)。
- 3、如文档侵犯您的权益,请联系客服反馈,我们会尽快为您处理(人工客服工作时间:9:00-18:30)。
三维柔性组合焊接夹具产品标准三维柔性组合焊接夹具产品标准1.主题内容与适用范围本标准规定了柔性组合焊接夹具产品中三维平台、二维平台、2S平台、支撑元件、定位元件、锁紧元件、压紧元件、连接元件、辅助材料的结构性能、规格、质量验收等。
2.引用标准下列文件中的条款通过本标准的引用而成为本标准的条款,其最新版本都适用于本标准。
GB/T6414 铸件尺寸公差GB/T19022 测量设备的确认与测量过程控制GB3 螺纹收尾、间距、退刀槽、倒角GB145 中心孔GB 6403.3 滚花GB196 普通螺纹、基本尺寸GB197 普通螺纹、公差与配合GB1031 表面粗糙度参数及数值GB1182 形状和位置公差代号及其注法GB1183 形状和位置公差术语及定义GB1184 形状和位置公差未注公差的规定GB3098.1 紧固件机械性能、螺栓、螺钉、和螺柱GB3103.1 紧固件公差螺栓、螺钉和螺母GB11335 未注公差角度的极限偏差GB/T1800 极限与配合总论标准公差与基本偏差TJ36 工业企业设计卫生标准GB/T13384 机电产品包装通用技术条件3.系列术语与定义:三维平台是由主平面及四侧面组成;按设定尺寸均布φ28、φ16二维平台是由主平面及四侧阻块组成;按设定尺寸均布φ28、φ162S平台是由主平面及四侧阻块组成;按设定尺寸均布φ28、φ16定位元件是为了保证工件在加工过程中达到一定尺寸精度要求,而将工件精确定位的元件。
支撑元件是为了保证工件在加工过程中达到一定高度要求,而将支撑件定位在平台上的元件。
锁紧元件是为了保证元件与元件之间的定位锁紧用。
压紧元件是为了保证工件在加工过程中不被位移,而将工件压紧在平台或基础元件上的元件。
连接元件是作用于元件与元件之间的连接作用。
辅助元件是指支撑件、定位件、锁紧件、压紧件、连接件的附件,起替换、辅助作用及对三维平台或二维平台、2S平台,的清洁与保护作用。
4. 产品结构与规格定义:4.1 三维平台是由工作平台和立柱组成;按材料形式可分为焊接件和铸件;.其形式和尺寸见图a 、表c 所示.:图a单位:mm表cφ28系列A1000 1200 1500 2000 2400 3000 B 1000 1200 1500 1000 1200 1500 C 200200200200200200D1200、350、620W4.2 二维工作平板是由工作平板和立柱组成;其形式和尺寸见图2、表2所示.:图2单位:mm 系列H2 200、450、620φ28系列L 2000 2400 W 1000 1200 H1 150 150 H2 200、350、620表24.3 支撑件按形状及用途可分为:L形方箱、U形方箱、支撑模板、支撑角铁;其尺寸见表3。
L形方箱单位:mm 系列规格01 02 03 04 05φ28系列长500 1000 1200 1500 2000 宽200 200 200 200 200 高100 100 100 100 100L型方箱U形方箱单位:mm系列规格01 02 03 04 05 06φ28系列长500 1000 1500 2000 3000 4000 宽200 200 200 200 200 200 高200 200 200 200 200 200U型方箱支撑角铁单位:mm 系列规格01 02 03φ28系列长275 375 375 宽100 100 100 高300 600 800表3支撑角铁4.4 定位件按其用途可分为:定位平尺、定位角尺、平面角尺、V型定位件;其尺寸见表4。
定位平尺单位:mm 系列规格01 02 03 04 05φ28系列长100 150 225 500 1000 宽50 50 50 75 75 高25 25 25 25 25定位平尺定位角尺单位:mm 系列规格01 02 03 04φ28系列长175 175 75 175 宽50 50 50 50 高175 75 75 275平面角尺单位:mm 系列规格01 02φ28系列长175 500 宽175 375 高25 25平面角尺V型定位件单位:mm 系列规格01 02 φ28系列直径φ60φ60角度90°120°表44.5 锁紧件按其结构形式可分为:快速锁紧销、沉头锁紧销;其形式见图3所示。
伸缩式压紧件45度式压紧件固定式压紧件图34.6 压紧件按其结构形式可分为:可伸缩压紧件、固定式快速压紧件、45度压紧件;其形式见图4所示。
图44.7 连接件根据连接形式可分为:角度器、角型连接块、夹管连接套、90度夹紧转角套、45度夹紧转角套;其尺寸见表5。
单位:mm名称角度器 角型连接块夹管连接套90度夹紧转角套45度夹紧转角套φ28系列长500 200 100 90 90 宽 100 200 —— 55 50 高 100 175 —— —— —— 孔径————φ28φ28φ28表5角度器角型连接块5. 质量技术要求5.1 材料5.1.1 制造配件所采用的材料应符合相应的国家标准和行业标准的规定。
5.1.2 采用冷拉圆钢(GB905)、方钢(GB906)、六角钢(GB907)制造的螺栓、螺钉、螺母、垫圈、元件,若钢材外形尺寸符合元件相应尺寸时,其外形可不加工。
5.1.3 工作平台钢件采用Q345;综合机械性能,焊接性及低温韧性,冷冲压及切削性均好,与Q235-A钢相比,强度提高50%,耐大气腐蚀提高20%~38%,低温冲击韧性也优越,经氮化处理硬度值HRC40°;铸件采用HT300,需进行人工时效处理;立柱采用φ89壁厚为8的Q235圆形无缝钢管。
5.1.4 支撑件分别采用Q45、HT300;用于强度、耐磨性要求较高的零件;有较好的耐热性和良好的减振性;铸件需进行人工时效处理。
5.1.5 定位件采用45#;调质处理;强度较高,塑性和韧性最佳,用于制作承受负荷较大的小截面调质件,以及对心部强度要求有一定韧性的表面淬火件。
5.1.6 锁紧件采用45#;调质处理HRC32~35°;锁紧件钢珠淬火处理HRC58~62°。
5.1.7 压紧件采用45#;调质处理;强度较高,塑性和韧性最佳,用于制作承受负荷较大的小截面调质件,以及对心部强度要求有一定韧性的表面淬火件。
5.1.8 连接件分别采用:Q345、A3、45#材质。
5.2毛坯5.2.1 铸件的尺寸公差应符合GB9439的规定,尺寸公差按CT8~9级,JB/ZQ40005。
5.2.2 铸件不许有裂纹、气孔及夹渣等缺陷,浇口、冒口和毛刺等应进行清理,并清除粘着物及氧化皮。
5.2.3 铸件非工作表面应发黑处理或涂防锈漆。
5.2.4 锻件非加工表面不允许有裂纹、烧痕、铁鳞、夹层、氧化皮等缺陷。
5.2.5 工作平台在机加工前应进行时效处理。
5.2.6 锁紧件及压紧件在机加工前,锻件及板材毛坯均应进行调质处理(铸铁毛坯应进行时效处理)。
5.2.7 热处理后的配件不允许有裂纹或龟裂、氧化皮、盐碱等污物。
5.2.8 钢质配件的非磨削表面(特种加工的表面除外)需进行化学氧化处理,氧化膜颜色应美观均匀。
5.3 机械加工要求5.3.1 支撑件、定位件、锁紧件、压紧件、连接件的主要位置公差应符合表6中的规定。
表65.3.1 工作平台主要部件尺寸精度和表面粗糙度应符合图5中的规定。
5.3.2 工作平台未注公差尺寸按IT8-9级。
5.3.3 棱边倒角C2~C3图55.3.4 锁紧销主要尺寸和表面粗糙度应符合图6中的规定。
图65.3.5 压紧件主要尺寸和表面粗糙度应符合图7中的规定。
图75.3.6公差等级等于或小于IT7级的孔、轴形位公差按单一要素包容原则。
5.3.7未注公差尺寸的极限偏差按GB 1804的规定,孔按D10,轴按h7,其余按±IT14/2。
5.3.8未注公差角度的极限偏差按GB 11135规定的中级精度选取。
5.3.9配件表面粗糙度按GB 1031中的第一系列选取。
5.3.10配件上的锐棱均须倒角或倒圆,其尺寸应符合设计图样的规定。
5.3.11配件中心孔应符合GB 145的规定。
5.3.12配件滚花应符合GB 6403.3的规定。
5.3.13 螺纹收尾、间距、退刀槽、倒角按GB 3中的一般值选取。
5.3.14普通螺纹基本尺寸应符合GB 196的规定,公差应符合GB 197的规定,内螺纹按6H, 外螺纹按6g。
5.3.15螺纹表面粗糙度R a值不大于6.3μm,不允许有裂纹、压伤、崩扣等缺陷。
5.3.16螺纹孔中心线对平面的垂直度在100mm长度上不大于0.5mm。
5.3.17螺栓、螺钉的直线度在200mm长度上不大于0.5mm。
5.3.18 螺栓、螺钉、螺母的公差按GB 3103.1的规定。
5.3.19用于紧固元件的螺栓、螺钉其力学性能应符合GB 3098.1中的10.9级规定。
5.3.20完工后的产品加工表面不允许有烧伤、碰伤、划伤(纹路、测量纹路和硬度检验压穴除外)、斑点、毛刺、锈蚀等缺陷,表面应光亮美观。
5.3.21产品若有橡胶制品应按TJ36-79工业企业设计卫生标准规定。
6. 验收6.1 产品验收按设计图样和技术条件的规定。
6.2 产品检验方法可参照JB/T 12588孔系组合夹具元件检验方法。
7. 标志、铭牌、包装7.1 工作台标志的位置应符合图样的规定。
7.2 标志的内容:a. 产品型号;b. 商标或工厂代号;c. 制造年、月;7.3 工作台铭牌的内容:a.产品规格;b.产品编号;c.生产日期;d.不准直接敲击台面;7.4 验收合格的产品经仔细清洗、防锈后入库保存,防锈有效期不少于一年。
7.6工作台及附件出厂的包装按GB/T13384的规定。
7.7 工作台及附件出厂使用的包装箱须有防潮,防锈措施,箱内应有产品质量检测报告及发货清单。