丙烯酸酯橡胶
丙烯酸酯

丙烯酸酯丙烯酸酯,是丙烯酸及其同系物的酯类的总称,能自聚或和其他单体共聚,是制造胶粘剂、合成树脂、特种橡胶和塑料的单体。
比较重要的丙烯酸酯有丙烯酸甲酯、丙烯酸乙酯、2-甲基丙烯酸甲酯和2-甲基丙烯酸乙酯等。
基本信息∙中文名称丙烯酸酯∙外文名称acrylic ester;acrylate∙化学式CH2=CHCOOCH3∙性质橡胶等简介:名称:丙烯酸酯英文名称:acrylic ester;acrylate化学式:CH2=CHCOOR分类:商品牌号很多,根据其分子结构中所含的不同交联单体,加工时硫化体系也不相同,由此可将丙烯酸酯橡胶划分为含氯多胺交联型、不含氯多胺交联型、自交联型、羧酸铵盐交联型、皂交联型等五类。
此外,还有特种丙烯酸酯橡胶,如含氟型及热塑性丙烯酸酯橡胶等性能:丙烯酸酯橡胶的性能受其主要单体丙烯酸烷基酯中烷基碳原子数目的影响。
以丙烯酸酯为基础的橡胶,耐油、耐热性较好;而以丙烯酸丁酯为基础的橡胶,因烷基碳原子数目的增多,对酯基极性基的屏蔽效应增大,因此使耐水性有所改善,同时由于屏蔽效应,减弱了橡胶分子间力,增大了内部塑性,从而使脆性温度降低,耐寒性较好。
若通过上述两种单体并用,则可得到介于两者性能之间的橡胶。
特点:无论哪一种类型的丙烯酸酯橡胶,其分子结构的共同特点有两个:一是高极性;二是完全饱和性。
从而使其具有优越的耐矿物油和耐高温氧化性能。
其耐油性仅次于氟胶,而与一般中高丙烯晴含量的丁腈橡胶相似。
而耐热性介于通用橡胶和硅、氟橡胶之间,比丁腈橡胶使用温度高出30~60℃,最高使用温度180℃,断续和短时间使用可达200℃,在150℃热空气老化数年性能无明显变化。
此外,最重要的是其对含有硫、氯、磷等极压剂的极压型润滑油十分稳定,使用温度可达150℃,间断使用温度可更高些。
而带有双键的丁腈橡胶在含有极压剂的油中,当温度超过110℃时,即发生显著硬化与变脆。
丙烯酸酯橡胶还具有优良的抗臭氧性、气密性、耐屈挠和耐裂口增长性,以及抗紫外线变色性等。
ACM橡胶简单介绍

丙烯酸酯橡胶简介以丙烯酸酯为主要单体经共聚而成的一种合成橡胶,具有耐高温、耐油、抗臭氧和耐紫外线辐照等特殊性能,是一种耐热、耐油的特种橡胶。
主要用作汽车和机车的各种耐热耐油密封圈、衬垫和油封。
丙烯酸酯橡胶发展历史1912年,德国人O.勒姆首次研究了聚丙烯酸酯的硫化。
1944年,美国的C.H.费希尔等开发了丙烯酸乙酯与2-氯乙基乙烯基醚共聚橡胶。
1948年,GOODREACH公司将该产品工业化。
1952年,美国单体公司开始生产丙烯酸丁酯与丙烯腈共聚的丙烯酸酯橡胶。
1955年,日本东亚合成化学也生产了丙烯酸丁酯-丙烯腈共聚橡胶。
1975年美国杜邦公司开发成功丙烯酸酯与α-烯烃共聚的橡胶,其典型代表是丙烯酸乙酯-乙烯无规共聚物和其后的丙烯酸乙酯-乙烯交替共聚橡胶。
这就是AEM橡胶。
丙烯酸酯橡胶的合成路线一类是乳液聚合,其主要品种有丙烯酸丁酯-丙烯腈共聚物,丙烯酸乙酯-丙烯酸丁酯-第三单体(如氯代醋酸乙烯酯等)三元共聚物,如高温胶和低温胶等,有良好的耐热、耐油性,但强度低(拉伸强度约10 MPa)、低温性能差(玻璃化温度Tg为-15~-28℃)。
这类高分子聚合物我们称之为聚丙烯酸橡胶-即大家非常熟悉的ACM橡胶。
另一类是溶液聚合。
丙烯酸酯与α-烯烃的溶液聚合橡胶,产品强度高、低温性能好(Tg为-38℃)。
这类烯聚合物的主要代表产品有美国杜邦化学的乙烯-丙烯酸酯橡胶即AEM。
丙烯酸酯橡胶的生产方法乳液法。
采用阴离子型和非离子型混合乳化剂(如十二烷基硫酸钠和烷氧基聚环氧乙烷),在水介质中将丙烯酸酯(包括乙酯和丁酯)或丙烯腈等乳化,并用水溶性引发剂引发聚合。
胶乳经凝聚、洗涤、干燥等工序即得干胶。
生胶的特性粘数[η]为4~6。
溶液法。
以卤代烃(如二氯甲烷)作溶剂,偶氮化合物作引发剂,以路易斯酸作络合剂,在约1MPa下使丙烯酸酯与α-烯烃(如乙烯)进行交替共聚,胶液经凝聚、回收溶剂后,即得交替共聚橡胶。
若采用过氧化物如过氧化三甲基醋酸叔丁酯作引发剂,在约180MPa的高压下使丙烯酸乙酯与乙烯共聚,则所得橡胶为无规共聚物。
丙烯酸酯橡胶(ACM)的配方及工艺

丙烯酸酯橡胶(ACM)的配方及工艺丙烯酸酯橡胶(ACM)具有优异的耐油、耐热、耐臭氧、抗紫外线等性能,从20世纪60年代末开始,随着高速汽车的发展而在美国、日本等工业先进国家获得较为广泛的应用。
近年,随着我国汽车工业、摩托车工业、电力工业的快速发展以及进口车辆、机具的增多,对ACM的需求已越来越大。
据国家机械工业局规划发展司介绍,国产汽车中采用ACM的车种为12种,2000年汽车装车和维修需要ACM5000t。
电力行业现在也已经逐步使用ACM代替NBR制造变压器的密封件,以提高使用寿命。
特别是现在国内的电网改造给ACM提供了较大的市场,使ACM的应用快速增长。
很多行业已逐步采用ACM替代NBR以提高制品的性能,或替代价格昂贵的氟橡胶以降低成本,或与氟橡胶并用以改善加工性能。
为了满足国内市场对ACM的需求,国家有关部门已将ACM 列入了积极发展的品种之列,一些科研院所和大专院校等都加入到这一领域进行研究和技术开发,研究成果报道增多,给ACM 的应用打下了一定的理论基础。
从80年代末开始,国内先后建立了几套ACM工业化生产装置,部分满足了国内市场的需求。
ACM的配合和加工具有特殊性,各厂家生产的ACM具有不同的配合和加工要求,给ACM的推广应用造成一定难度。
我国的橡胶制品企业多为中小型企业,技术力量薄弱,也影响了ACM的推广应用。
为了使ACM在我国尽快得到推广应用,解决好配合加工中的技术问题成为当前一项迫切任务。
为此,我们将所了解的用户在实际应用中遇到的配合技术问题进行了分析探讨,现介绍如下。
1ACM配合中的常见问题及产生原因在ACM胶料的配合中,比较常见的技术问题主要有:①胶料性能不稳定;②拉伸强度太低;③压缩永久变形和扯断永久变形大;④回弹性差,有的胶料硫化后近似于硬质塑料;⑤耐磨性差;⑥耐高温老化性差;⑦浅色胶料难以配合和硫化,彩色制品在硫化时变色。
出现上述问题的原因是多方面的,主要影响因素有以下几点:(1)生胶质量低或不稳定生胶质量低或不稳定是影响胶料性能的最重要原因。
丙烯酸酯橡胶

低温耐油单体,传统的采用丙烯酸烷氧醚酯 低温耐油单体, 参与共聚,得到ACM耐寒温度为 ℃以下; 耐寒温度为-30℃以下; 参与共聚,得到 耐寒温度为 尔后工业生产中又选用丙烯酸甲氧乙酯为共 聚单体生产耐寒型ACM,进一步降低使用 聚单体生产耐寒型 , 温度. 温度.近年来国外专利报道使用丙烯酸聚乙 二醇甲氧基酯, 二醇甲氧基酯,顺丁烯二酸二甲氧基乙酯等 作为低温耐油单体效果更好. 作为低温耐油单体效果更好.另外杜邦公司 采用乙烯与丙烯酸甲酯溶液共聚, 采用乙烯与丙烯酸甲酯溶液共聚,将乙烯引 入聚合物主链, 入聚合物主链,可以明显提高产品低温屈挠 性等. 性等.
一般选用阴离子或阴离子和非离子复合型乳化剂如十二 烷基磺酸钠;油溶性引发剂异丙苯过氧化氢, 烷基磺酸钠;油溶性引发剂异丙苯过氧化氢,水溶性引 发剂过硫酸盐,过氧化氢和叔丁基过氧化氢等; 发剂过硫酸盐,过氧化氢和叔丁基过氧化氢等;选用叔 十二烷基硫醇或二硫化烷基黄原酸酯做分子量调节剂等. 十二烷基硫醇或二硫化烷基黄原酸酯做分子量调节剂等. 聚合温度一般在50~ 聚合温度一般在 ~100℃,可以通过冷凝回流或逐渐添 ℃ 加单体的方式除去聚合热,以控制聚合速度,减少单位 加单体的方式除去聚合热,以控制聚合速度, 时间发热量. 时间发热量.乳液聚合从水中分离出聚合物需要增加盐 析工序,因此需要添加盐析剂,一般选用Na Cl,CaCl2 析工序,因此需要添加盐析剂,一般选用 , 等盐类,也可选用HCl,H2SO2(次硫酸)等酸类,工业上 等盐类,也可选用 , (次硫酸)等酸类, 常选用CaCl2作盐析剂.盐析时候可用聚丙烯酸钠,聚乙 作盐析剂.盐析时候可用聚丙烯酸钠, 常选用 烯醇等作保护剂,以防止胶粒粘结成团,盐析后可用氢 烯醇等作保护剂,以防止胶粒粘结成团, 氧化钠溶液从胶中洗提出乳化剂,使得生胶易于硫化. 氧化钠溶液从胶中洗提出乳化剂,使得生胶易于硫化. 另外乳聚法ACM的干燥方式,不同公司也会选用不同方 的干燥方式, 另外乳聚法 的干燥方式 如美国氰特公司,日本瑞翁公司采用挤出干燥工艺, 式,如美国氰特公司,日本瑞翁公司采用挤出干燥工艺, 日本东亚油漆公司则为烘干产品. 日本东亚油漆公司则为烘干产品.
原来丙烯酸酯橡胶(ACM)的胶料配合需要这些成分组成?生产工艺也与众不同哦!!!
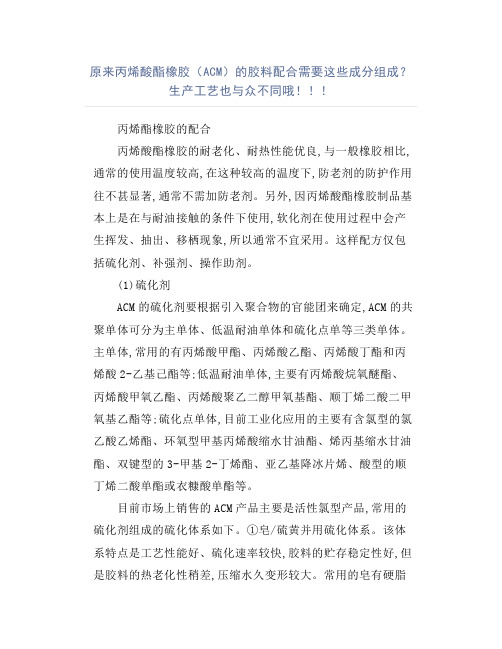
原来丙烯酸酯橡胶(ACM)的胶料配合需要这些成分组成?生产工艺也与众不同哦丙烯酯橡胶的配合丙烯酸酯橡胶的耐老化、耐热性能优良,与一般橡胶相比,通常的使用温度较高,在这种较高的温度下,防老剂的防护作用往不甚显著,通常不需加防老剂。
另外,因丙烯酸酯橡胶制品基本上是在与耐油接触的条件下使用,软化剂在使用过程中会产生挥发、抽出、移栖现象,所以通常不宜采用。
这样配方仅包括硫化剂、补强剂、操作助剂。
(1)硫化剂ACM的硫化剂要根据引入聚合物的官能团来确定,ACM的共聚单体可分为主单体、低温耐油单体和硫化点单等三类单体。
主单体,常用的有丙烯酸甲酯、丙烯酸乙酯、丙烯酸丁酯和丙烯酸2-乙基己酯等;低温耐油单体,主要有丙烯酸烷氧醚酯、丙烯酸甲氧乙酯、丙烯酸聚乙二醇甲氧基酯、顺丁烯二酸二甲氧基乙酯等;硫化点单体,目前工业化应用的主要有含氯型的氯乙酸乙烯酯、环氧型甲基丙烯酸缩水甘油酯、烯丙基缩水甘油酯、双键型的3-甲基2-丁烯酯、亚乙基降冰片烯、酸型的顺丁烯二酸单酯或衣糠酸单酯等。
目前市场上销售的ACM产品主要是活性氯型产品,常用的硫化剂组成的硫化体系如下。
①皂/硫黄并用硫化体系。
该体系特点是工艺性能好、硫化速率较快,胶料的贮存稳定性好,但是胶料的热老化性稍差,压缩水久变形较大。
常用的皂有硬脂酸钠、硬脂酸钾和油酸钠。
②N,N二亚肉桂基-1,-已二胺硫化体系。
采用该体系的硫化胶的热老化性能好,压缩水久变形小,但是工艺能稍差,有时会出现粘模现象,混炼胶贮存期较短,硫化程度不高,一般需要二次硫。
③TCY(1,3,5-三巯基-2,4,6-均三嗪)硫化体系。
该体系硫化速率快,可以取消二段硫化,硫化胶热老化性好,压缩水久变形小,工艺性能一般,但对模具腐蚀性较大,混炼胶的贮存时间短,易焦烧。
环氧型ACM常采用多胺、有机羧酸铵盐、二硫代甲酸盐、季铵盐/脲硫化剂。
为了提高反应速率,改善反应选择性,可采适当的促进剂,如各种路易氏碱或酸等都是有效的。
丙烯酸酯橡胶

丙烯酸酯橡胶应用一、前言:比重1.~1.1丙烯酸酯橡胶(英文简称ACM)是以丙烯酸酯为主单体经共聚而得的弹性体,其主链为饱和碳链,侧基为极性酯基;通常要用硫化点单体参与共聚以使其易于硫化。
由于一次结构为饱和碳链和极性侧基,赋予它很好的耐热、耐老化、耐油性能。
被广泛地应用于各种高温、耐油环境,如轴封、O型圈、输油管和各种垫片等。
特别是汽车的曲轴、汽门阀杆、汽缸垫、排汽管的密封和液压输油管等。
有汽车胶的美称。
根据机械部汽车司1995年的统计,国产车使用ACM密封件件数及单耗量如下车型件/辆(ACM胶料)ACM单耗①(kg/辆)CA7220 0.7上海“桑塔那”0.2神龙“富康”0.5TJ7100 0.1CA21046L 4 0.7南京“依维柯” 4 1.5CA1092-Ⅱ 6 0.8“EQ1092 ” 6 0.1“EQ1141G ”11 0.3标致505 0.7JN “ 1491 ”20 7①已采用的部分关键部件的用量(按国际标准,平均为1.0~1.5kg/辆)随着我国汽车工业的兴起和高速发展,一方面,引进汽车生产线的元件国产化和进口原装车备件的更换都急需ACM胶作耐油密封件。
另一方面,我国原有的载重汽车及乘用汽车等也需要不断提高整车质量,延长大修时间。
加之汽车向高速、节油方向发展,这就要求汽车汽缸的燃烧温度不断提高,近年来随着我国高速公路飞速发展,也要求车速提高,各运转部位密封件的温度也相应提高,许多关键部件均需采用高性能的ACM作高温耐油密封件,以保证整车水平。
因此,特种合成橡胶行业和特胶制品行业都急需集中精力研制开发并工业化生产适合汽车工业需要的各类ACM胶种及其制品,否则将难以改变ACM和制品长期依赖进口的局面。
与其它耐油橡胶相比,丙烯酸酯橡胶具有性能/价格比最优的特点。
它长期使用温度180℃,短期使用温度可达210℃,在各种润滑油、燃料油中膨胀率较低(<10%),汽车变速箱用ACM制品密封可连续行驶15-20万公里而不漏油;而丁腈橡胶虽能耐油性能很好,但耐老化性能和耐温性能较差,汽车用丁腈橡胶密封制品连续使用温度仅为106℃,变速箱部位密封连续行驶仅8000-10000公里即开始漏油。
丙烯酸酯橡胶 合成 生产工艺流程
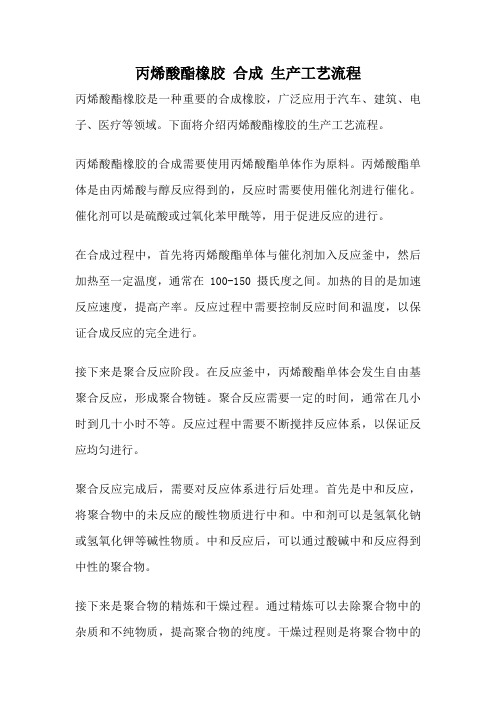
丙烯酸酯橡胶合成生产工艺流程丙烯酸酯橡胶是一种重要的合成橡胶,广泛应用于汽车、建筑、电子、医疗等领域。
下面将介绍丙烯酸酯橡胶的生产工艺流程。
丙烯酸酯橡胶的合成需要使用丙烯酸酯单体作为原料。
丙烯酸酯单体是由丙烯酸与醇反应得到的,反应时需要使用催化剂进行催化。
催化剂可以是硫酸或过氧化苯甲酰等,用于促进反应的进行。
在合成过程中,首先将丙烯酸酯单体与催化剂加入反应釜中,然后加热至一定温度,通常在100-150摄氏度之间。
加热的目的是加速反应速度,提高产率。
反应过程中需要控制反应时间和温度,以保证合成反应的完全进行。
接下来是聚合反应阶段。
在反应釜中,丙烯酸酯单体会发生自由基聚合反应,形成聚合物链。
聚合反应需要一定的时间,通常在几小时到几十小时不等。
反应过程中需要不断搅拌反应体系,以保证反应均匀进行。
聚合反应完成后,需要对反应体系进行后处理。
首先是中和反应,将聚合物中的未反应的酸性物质进行中和。
中和剂可以是氢氧化钠或氢氧化钾等碱性物质。
中和反应后,可以通过酸碱中和反应得到中性的聚合物。
接下来是聚合物的精炼和干燥过程。
通过精炼可以去除聚合物中的杂质和不纯物质,提高聚合物的纯度。
干燥过程则是将聚合物中的水分去除,以提高聚合物的稳定性和质量。
最后是丙烯酸酯橡胶的成型和整形过程。
成型可以通过挤出、压延、注塑等方法进行。
整形则是将成型的丙烯酸酯橡胶进行切割、修整、压制等工艺处理,使其达到所需的形状和尺寸。
丙烯酸酯橡胶的合成生产工艺流程包括原料配制、丙烯酸酯单体与催化剂的反应、聚合反应、后处理、精炼和干燥、成型和整形等步骤。
这些步骤相互关联,每一步都至关重要,只有严格控制每个环节,才能获得高品质的丙烯酸酯橡胶产品。
丙烯酸酯橡胶

丙烯酸酯橡胶应用一、前言:比重1.~1.1丙烯酸酯橡胶(英文简称ACM)是以丙烯酸酯为主单体经共聚而得的弹性体,其主链为饱和碳链,侧基为极性酯基;通常要用硫化点单体参与共聚以使其易于硫化。
由于一次结构为饱和碳链和极性侧基,赋予它很好的耐热、耐老化、耐油性能。
被广泛地应用于各种高温、耐油环境,如轴封、O型圈、输油管和各种垫片等。
特别是汽车的曲轴、汽门阀杆、汽缸垫、排汽管的密封和液压输油管等。
有汽车胶的美称。
根据机械部汽车司1995年的统计,国产车使用ACM密封件件数及单耗量如下车型件/辆(ACM胶料)ACM单耗①(kg/辆)CA7220 0.7上海“桑塔那”0.2神龙“富康”0.5TJ7100 0.1CA21046L 4 0.7南京“依维柯” 4 1.5CA1092-Ⅱ 6 0.8“EQ1092 ” 6 0.1“EQ1141G ”11 0.3标致505 0.7JN “ 1491 ”20 7①已采用的部分关键部件的用量(按国际标准,平均为1.0~1.5kg/辆)随着我国汽车工业的兴起和高速发展,一方面,引进汽车生产线的元件国产化和进口原装车备件的更换都急需ACM胶作耐油密封件。
另一方面,我国原有的载重汽车及乘用汽车等也需要不断提高整车质量,延长大修时间。
加之汽车向高速、节油方向发展,这就要求汽车汽缸的燃烧温度不断提高,近年来随着我国高速公路飞速发展,也要求车速提高,各运转部位密封件的温度也相应提高,许多关键部件均需采用高性能的ACM作高温耐油密封件,以保证整车水平。
因此,特种合成橡胶行业和特胶制品行业都急需集中精力研制开发并工业化生产适合汽车工业需要的各类ACM胶种及其制品,否则将难以改变ACM和制品长期依赖进口的局面。
与其它耐油橡胶相比,丙烯酸酯橡胶具有性能/价格比最优的特点。
它长期使用温度180℃,短期使用温度可达210℃,在各种润滑油、燃料油中膨胀率较低(<10%),汽车变速箱用ACM制品密封可连续行驶15-20万公里而不漏油;而丁腈橡胶虽能耐油性能很好,但耐老化性能和耐温性能较差,汽车用丁腈橡胶密封制品连续使用温度仅为106℃,变速箱部位密封连续行驶仅8000-10000公里即开始漏油。
- 1、下载文档前请自行甄别文档内容的完整性,平台不提供额外的编辑、内容补充、找答案等附加服务。
- 2、"仅部分预览"的文档,不可在线预览部分如存在完整性等问题,可反馈申请退款(可完整预览的文档不适用该条件!)。
- 3、如文档侵犯您的权益,请联系客服反馈,我们会尽快为您处理(人工客服工作时间:9:00-18:30)。
丙烯酸酯橡胶应用一、前言:比重1.~1.1丙烯酸酯橡胶(英文简称ACM)是以丙烯酸酯为主单体经共聚而得的弹性体,其主链为饱和碳链,侧基为极性酯基;通常要用硫化点单体参与共聚以使其易于硫化。
由于一次结构为饱和碳链和极性侧基,赋予它很好的耐热、耐老化、耐油性能。
被广泛地应用于各种高温、耐油环境,如轴封、O型圈、输油管和各种垫片等。
特别是汽车的曲轴、汽门阀杆、汽缸垫、排汽管的密封和液压输油管等。
有汽车胶的美称。
根据机械部汽车司1995年的统计,国产车使用ACM密封件件数及单耗量如下车型件/辆(ACM胶料) ACM单耗①(kg/辆)CA7220 0.7“桑塔那”0.2神龙“富康”0.5TJ7100 0.1CA21046L 4 0.7“依维柯” 4 1.5CA1092-Ⅱ 6 0.8“EQ1092 ” 6 0.1“EQ1141G ”11 0.3标致505 0.7JN “1491 ”20 7①已采用的部分关键部件的用量(按国际标准,平均为1.0~1.5kg/辆)随着我国汽车工业的兴起和高速发展,一方面,引进汽车生产线的元件国产化和进口原装车备件的更换都急需ACM胶作耐油密封件。
另一方面,我国原有的载重汽车及乘用汽车等也需要不断提高整车质量,延长大修时间。
加之汽车向高速、节油方向发展,这就要求汽车汽缸的燃烧温度不断提高,近年来随着我国高速公路飞速发展,也要求车速提高,各运转部位密封件的温度也相应提高,许多关键部件均需采用高性能的ACM作高温耐油密封件,以保证整车水平。
因此,特种合成橡胶行业和特胶制品行业都急需集中精力研制开发并工业化生产适合汽车工业需要的各类ACM 胶种及其制品,否则将难以改变ACM和制品长期依赖进口的局面。
与其它耐油橡胶相比,丙烯酸酯橡胶具有性能/价格比最优的特点。
它长期使用温度180℃,短期使用温度可达210℃,在各种润滑油、燃料油中膨胀率较低(<10%),汽车变速箱用ACM制品密封可连续行驶15-20万公里而不漏油;而丁腈橡胶虽能耐油性能很好,但耐老化性能和耐温性能较差,汽车用丁腈橡胶密封制品连续使用温度仅为106℃,变速箱部位密封连续行驶仅8000-10000公里即开始漏油。
丙烯酸酯橡胶是性能/价格比最优并被广泛地用于高温耐油环境的特种橡胶。
二、国外ACM发展概况及主要品牌:有关ACM的首篇报道始见于1912年德国的Otto Rohm [1] 的专利,他曾用硫磺使聚丙烯酸酯硫化获得了橡胶状物质,但没获得实用性制品。
1944年,美国农业东部地区实验室的Fisher [2、3、4、5] 等人制得了丙烯酸乙酯与2-氯乙基乙烯醚共聚物,可很容易地用硫-硬脂酸皂系硫化。
1948年,美国Goodrich公司首先实现了乳聚ACM的工业化,商品名称为Hycar PA-31 [6] ,后经改进更名为Hycar-4021,Hycar-4031。
1963年美国American Cyanamid公司也开发生产了ACM,商品名称为Cyanacry1。
六十年代中期日本油封公司、东亚油漆公司、瑞翁公司等先后开发生产了ACM。
1978年美国杜邦公司又开发并生产溶聚法ACM[7,主要生产超耐寒级ACM,商品名为VAMAC。
到1988年,计有美、日、意、加拿大、前苏联和西欧(Enichem Polimeri SPA公司)等8个国家16家工厂生产ACM,除美国杜邦公司采用溶聚法生产VAMAC外,其它工厂均采用乳液共聚法。
我国于70年代中期化工研究院曾研制过丙烯酸丁酯(BA)-丙烯腈(AN)共聚橡胶,并在天津染化八厂进行过中试和产品开发[8-9] ,由于产品的加工性能和物性低劣,研制工作中断。
从80年代初国先后有化工大学、化工研究院和科技大学、化工部、橡胶制品研究所等单位对ACM的合成方法、结构和物性、加工和硫化等进行过研究。
1995年9月由我们的技术在油脂化学工业公司有机化工厂建成1m 3 规模的乳聚含氯型ACM,试产两个系列4个牌号的ACM生胶。
生产技术和产品通过了原化工部鉴定,认为:该技术国先进、产品主要指标达到了国外同类产品水平。
生产技术和产品通过了原化工部鉴定,认为:该技术国先进、产品主要指标达到了国外同类产品水平。
通用型丙烯酸酯橡胶的Tg约为-15℃,耐寒型ACM的Tg为-25,超耐寒型ACM 的Tg为-38℃。
在保持丙烯酸酯橡胶高温耐压特性的同时设法改善其耐低温性能是国际上竞相研究的热点。
丙烯酸酯橡胶按其硫化点结构分类可分为:含氯型、环氧性、羧酸型和双烯型等。
目前国外主要生产厂家及品牌见表1 [10,11] :交联点/生产公司耐寒级别标准耐寒超耐寒极超耐寒(含氯型)B.F.Goodrich Hycar4041 4042 4043 American Cyamind R, L C, 35 40, 45日本合成橡胶AREX110 AREX220 AREX310 AREX411日本瑞翁AR71 AR72 AR74 AR72LSAR72HF日本东亚油漆TOA Acron AR801AR825 AR860 AR840日本油封公司PA401 PA402 PA404 PA402S PA404K PA403日信化学RV1220 RV1240 RV1260加拿大Polysar Krynac 881, 882(环氧型)日本合成橡胶AREX120 AREX220 AREX320日本油封公司PA301 PA302(Nox Tite)PA301K PA303 PA312日本瑞翁AR31 AR32 AR54 AR51 AR42(W)AR53(L)日本东亚油漆TOA Acron AR740 AR760日信化学RV1020 RV1040 RV1060意大利Montedison公司Elamprim AR152, 153德国Bayer Acralen Dispersioms(烯类)日信化学RV2520 RV2540 RV2560(其它类)日本油封公司PA501 PA502 PA502LB.F. Goodrich 4051 4052 4053 4054杜邦(羧基)VAMAC P(MA-E),(溶聚法)日本电器化学电化ER P(E-VAC-MA)(溶聚法)日本住友化学エズブしリEMA P(E-MA-GMA)(溶聚法)四、丙烯酸酯橡胶的基本单体构成:构成丙烯酸酯橡胶的共聚单体可分为主单体、低温耐油单体和硫化点单体等三类单体。
1、主单体:常用的主单体有丙烯酸甲酯(MA)、丙烯酸乙酯(EA)、丙烯酸丁酯(BA)和丙烯酸2-乙基己酯(EHA)等;PMA的Tg=5℃,PEA的Tg=-15℃,PBA的Tg=-54℃,PEHA的Tg=-76℃。
随着侧酯基碳数增多,Tg降低,耐油性变差。
为了保持ACM良好的耐油性,并改善其低温性能,人们在单体的侧酯基上引入极性基团,合成了带有极性基的丙烯酸酯单体参与共聚,以期待获得低温-耐油性能的综合平衡。
2、低温耐油单体:在保证丙烯酸酯橡胶的耐油性能不下降的前提下,自60年代起对ACM用低温耐油单体进行了一系列研究开发。
60年代末,人们采用[12,13]丙烯酸烷氧醚酯参与共聚,得到的ACM可基本保持耐油性能而使脆性温度(Tgb)达-30℃以下,70年代生产ACM的公司大都采用丙烯酸甲氧基乙酯为共聚单体生产耐寒型ACM。
为了进一步降低ACM的使用温度,有专利[14] 报道,使用丙烯酸聚乙二醇甲氧基酯作为低温耐油单体,所得ACM的脆性温度可达-45℃。
另一篇专利[15] 报道,使用顺丁烯二酸二甲氧基乙酯作为低温耐油单体,脆性温度可达-42℃。
另外日本合成橡胶公司的专利[16, 17] 报道,结构为CH2=CHCOO-(R)n-COOR1 的单体(其中n=3-8,R1=-CH3, -C2H5)参与共聚,宜可使ACM的脆性温度低于-42℃以下,且伸长率可达300%以上。
对于油环境可大致分为三类:1、对旋转或往复运动起润滑作用的矿物油和润滑脂;2、作为动力传递介质的液压油、液压变矩器油和刹车油;3、汽油、轻油、重油等燃料油。
这些油中,除矿物油外,还包括作为不燃性液压油的磷酸酯类,作为喷气发动机油的二酯类等合成油。
丙烯酸酯橡胶对矿物油有较好的耐油性,但对含酯型的合成油的耐油性不好,对燃油而言,ACM对轻质油的耐油性稍差、对重油的耐油性较好。
为改进ACM对轻质燃油的耐油性,如此丙烯酸酯单体(CH2=CHCOOCH2CH2OCH2CH2CN,或CH2=CHCOO(CH2)5)COOCH2CH2OCH2CH2CN)参与共聚,可大大提高ACM的耐轻质燃料油性能和降低脆性温度[18,19,20]。
另外,杜邦公司采用乙烯与丙烯酸甲酯单体溶液共聚的办法,将乙烯引入聚合物主链,低温下起到“弹性铰链”的作用。
大大提高了ACM的低温屈挠性能,从而降低了ACM的使用温度。
丙烯酸酯橡胶以丙烯酸酯为主要单体经共聚而成的一种合成橡胶,具有耐高温、耐油、抗臭氧和耐紫外线辐照等特殊性能,是一种耐热、耐油的特种橡胶。
主要用作汽车和机车的各种耐热耐油密封圈、衬垫和油封。
丙烯酸酯橡胶-丙烯酸酯橡胶丙烯酸酯橡胶图片以丙烯酸酯为主要单体经共聚而成的一种合成橡胶,具有耐高温、耐油、抗臭氧和耐紫外线辐照等特殊性能,是一种耐热、耐油的特种橡胶。
主要用作汽车和机车的各种耐热耐油密封圈、衬垫和油封。
沿革1912年,德国人O.勒姆首次研究了聚丙烯酸酯的硫化。
1944年,美国的C.H.费希尔等开发了丙烯酸乙酯同2-氯乙基乙烯基醚共聚橡胶,1948年,固特里奇化学公司将该产品工业化。
1952年,美国单体公司开始生产丙烯酸丁酯与丙烯腈共聚的丙烯酸酯橡胶。
1955年,日本东亚合成化学工业公司也生产了丙烯酸丁酯-丙烯腈共聚橡胶。
为克服这种橡胶的低强度和低温性能差等缺点,1975年美国杜邦公司开发成功丙烯酸酯- α- 烯烃共聚橡胶,其典型代表是丙烯酸乙酯-乙烯无规共聚物和其后的丙烯酸乙酯-乙烯交替共聚橡胶。
据悉,它们可在-40~175℃的燃料油环境中长期使用。
随着汽车工业的迅速发展,丙烯酸酯橡胶产量迅速增长。
1963年世界产量为1300~1500t,1984年产量已增至7~8kt。
分类可按合成路线分两类。
一类是乳液聚合橡胶,其主要品种有丙烯酸丁酯-丙烯腈共聚物,丙烯酸乙酯-丙烯酸丁酯-第三单体(如氯代醋酸乙烯酯等)三元共聚物,如高温胶和低温胶等,有良好的耐热、耐油性,但强度低(抗强度约15MPa)、低温性能差(玻璃化温度Tg为-15~-28℃);另一类是丙烯酸酯与α-烯烃的溶液聚合橡胶,产品强度高、低温性能好(Tg为38℃)。
生产方法有两种方法:①乳液法。
采用阴离子型和非离子型混合乳化剂(如十二烷基硫酸钠和烷氧基聚环氧乙烷),在水介质中将丙烯酸酯(包括乙酯和丁酯)或丙烯腈等乳化,并用水溶性引发剂引发聚合。