2020年(发展战略)综述CAE技术的发展和应用
中国的cae软件

边界元分析(BEM)技术
边界元分析技术是一种数值计算 方法,适用于解决边界积分方程 等问题。
在中国,边界元分析技术的研究 和应用也得到了广泛的发展。中 国在边界元分析技术方面拥有丰 富的理论和实践经验,并将其应 用于多个领域,如结构力学、流 体动力学、电磁场等领域。
中国在边界元分析技术方面也取 得了很多成果,包括开发了多种 边界元分析软件,如Fesafe、 Elmer等,这些软件在中国的工 程应用中发挥了重要作用。
04
CATALOGUE
中国cae软件的应用实例
cae软件在机械制造行业的应用
模具设计优化
01
利用cae软件对模具设计方案进行模拟和优化,提高模具的精
度和使用寿命。
生产线规划与仿真
02
通过cae软件模拟生产线流程,优化生产线的布局和生产效率
。
机械部件疲劳寿命预测
03
利用cae软件对机械部件的疲劳寿命进行预测,提前发现潜在
离散元(DEM)技术
离散元技术是一种数值计算方法,适用于解决离散系统的动力学问题。
在中国,离散元技术的研究和应用也得到了广泛的发展。中国在离散元 技术方面拥有丰富的理论和实践经验,并将其应用于多个领域,如地质
工程、机械工程、土木工程等领域。
中国在离散元技术方面也取得了很多成果,包括开发了多种离散元分析 软件,如UDEC、PFC等,这些软件在中国的工程应用中发挥了重要作 用。
拓展国际市场
加强国际合作与交流,开拓国际市场,提 升中国CAE软件的国际影响力。
加强国际合作与交流
合作研究
鼓励国内企业和研究机构与国际先进企业与研究机构开展合作 研究。
技术交流
积极参加国际技术交流活动,分享中国CAE软件的技术成果和 发展经验。
中国CAE行业现状及发展前景分析

中国CAE⾏业现状及发展前景分析中国CAE⾏业现状及发展前景分析CAE指⼯程设计中的计算机辅助⼯程,指⽤计算机辅助求解分析复杂⼯程和产品的结构⼒学性能,以及优化结构性能等,把⼯程(⽣产)的各个环节有机地组织起来,其关键就是将有关的信息集成,使其产⽣并存在于⼯程(产品)的整个⽣命周期。
⽽CAE软件可作静态结构分析,动态分析;研究线性、⾮线性问题;分析结构(固体)、流体、电磁等。
CAE⼴泛应⽤于汽车、航空航天、国防军⼯、电⼦装备等制造业,下游⾏业的产品研发对于CAE具有较⼤的市场需求,有助于驱动业内CAE软件⽔平的提升、CAE⾏业解决⽅案及相关服务的持续完善。
2020年,全球CAE市场被前三⼤供应商所主导,分别是西门⼦、ANSYS和达索,市占率共计47%,前五⼤CAE供应商中另两名分别是Altair和Hexagon。
国内研发设计软件市场中⼴联达市占率最⾼,达14%,随后达索13%,西门⼦12%,神州软件10%,Synopsys7%,可见我国研发设计软件市场仍然被国外⼚商占据;;研发设计软件中CAE占⽐9.57%,近10%,其中主要⼚商为ANSYS、达索、西门⼦、中望和安怀信等,国内三家公司市占⽐均不⾜5%,总占⽐仅6%。
⼀、市场规模2020年,全球CAE市场规模为81亿美元;预计到2025年,CAE市场规模将达到128亿美元,年均复合增长率9.6%。
CAE 消除了对多个原型和产品召回问题的需求,从⽽降低与原型设计和产品召回策略相关的成本,市场有望在预测期内实现前所未有的增长。
运⽤CFD分析电池模块温度的情况增多,延长了电池寿命和性能,将有效推动CAE市场发展。
越来越多的⼯程制造任务被外包给中国、印度、俄罗斯等新兴经济体。
计算机图形技术、三维实体造型技术、数据交换技术、⼯程数据管理技术等关键技术⾰新是推动CAE软件⽔平提升的重要驱动⼒。
“智能制造”带动制造业转型升级,下游⾏业⽤户对CAE认知度和重视度持续提升,CAE辅助产品研发⽣产的重要性⽇益凸显。
CAE技术及其航天领域的应用

CAE技术及其航天领域的应用CAE(计算机辅助工程)技术是一种通过计算机模拟和分析技术,用来帮助工程师在设计、开发和优化产品或系统过程中进行性能预测和验证的技术手段。
在航天领域,CAE技术发挥着重要作用,帮助解决了许多挑战,并提升了航天器的设计、制造和性能。
首先,CAE技术在航天领域的应用非常广泛。
航天器的设计和制造通常涉及复杂的物理学、力学和流体力学问题。
通过使用CAE软件,工程师可以通过建立数值模型,模拟航天器的运行环境和物理行为,预测和分析不同条件下的性能表现,如结构强度,热力学效应和空气动力学特性等。
这有助于工程师快速优化设计,减少试验成本,并提高工作效率。
其次,CAE技术在飞行动力学模拟、轨道设计和飞行控制方面也起着关键作用。
航天器的飞行特性、轨道选择、姿态控制和交会对接等问题需要进行复杂的计算和分析。
CAE技术可以通过数值模拟和仿真,评估不同飞行模式和控制策略的效果,帮助工程师制定合理的方案。
这有助于提高航天器的安全性和飞行效率,并减少操作风险。
此外,CAE技术还在航天器结构和材料方面发挥重要作用。
航天器需要经受极端的温度、压力和振动等环境,因此在设计航天器的结构时需要考虑到材料的力学性能和疲劳寿命等问题。
CAE技术可以通过建立数值模型,分析不同材料和结构设计对应力、应变和振动等因素的影响,预测和优化航天器的结构性能。
这有助于提高航天器的耐久性和可靠性,并减少结构故障的风险。
最后,CAE技术在航天器系统工程中也具有重要作用。
航天器的系统工程涉及多个子系统和组件之间的协调和集成,要求对整个系统进行综合性能分析和评估。
通过使用CAE软件,工程师可以建立整体的数值模型,模拟和预测不同子系统和组件之间的相互影响,以及整体系统在不同操作条件下的性能表现。
这有助于发现潜在的问题和优化点,并改进系统的整体性能。
总之,CAE技术在航天领域的应用可以帮助工程师进行航天器的设计、分析和优化,在结构、力学、热力学和飞行动力学等方面提供关键支持。
综述CAE技术的发展和应用
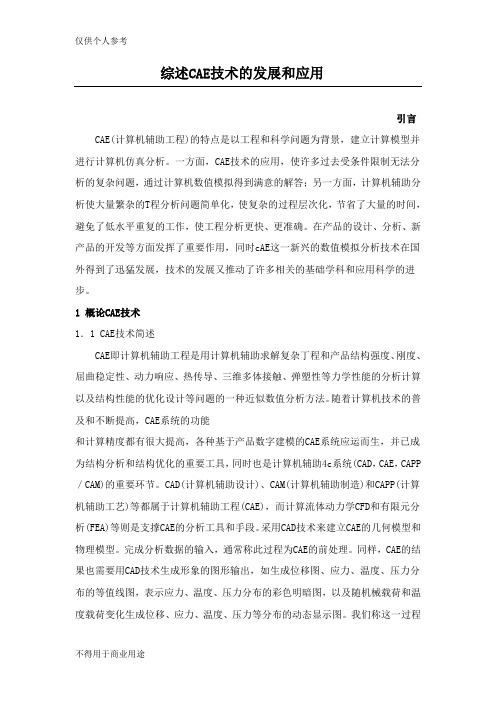
综述CAE技术的发展和应用引言CAE(计算机辅助工程)的特点是以工程和科学问题为背景,建立计算模型并进行计算机仿真分析。
一方面,CAE技术的应用,使许多过去受条件限制无法分析的复杂问题,通过计算机数值模拟得到满意的解答;另一方面,计算机辅助分析使大量繁杂的T程分析问题简单化,使复杂的过程层次化,节省了大量的时间,避免了低水平重复的工作,使工程分析更快、更准确。
在产品的设计、分析、新产品的开发等方面发挥了重要作用,同时cAE这一新兴的数值模拟分析技术在国外得到了迅猛发展,技术的发展又推动了许多相关的基础学科和应用科学的进步。
1 概论CAE技术1.1 CAE技术简述CAE即计算机辅助工程是用计算机辅助求解复杂丁程和产品结构强度、刚度、屈曲稳定性、动力响应、热传导、三维多体接触、弹塑性等力学性能的分析计算以及结构性能的优化设计等问题的一种近似数值分析方法。
随着计算机技术的普及和不断提高,CAE系统的功能和计算精度都有很大提高,各种基于产品数字建模的CAE系统应运而生,并已成为结构分析和结构优化的重要工具,同时也是计算机辅助4c系统(CAD,CAE,CAPP /CAM)的重要环节。
CAD(计算机辅助设计)、CAM(计算机辅助制造)和CAPP(计算机辅助工艺)等都属于计算机辅助工程(CAE),而计算流体动力学CFD和有限元分析(FEA)等则是支撑CAE的分析工具和手段。
采用CAD技术来建立CAE的几何模型和物理模型。
完成分析数据的输入,通常称此过程为CAE的前处理。
同样,CAE的结果也需要用CAD技术生成形象的图形输出,如生成位移图、应力、温度、压力分布的等值线图,表示应力、温度、压力分布的彩色明暗图,以及随机械载荷和温度载荷变化生成位移、应力、温度、压力等分布的动态显示图。
我们称这一过程为CAE的后处理。
1.2 CAE技术发展历程CAE的理论基础有限元法:20世纪40年代起源于土木工程和航空工程中的弹性和结构分析问题的研究。
CAE行业发展现状及趋势分析,CAE咨询细分市场快速发展「图」

CAE行业发展现状及趋势分析,CAE咨询细分市场快速发展「图」CAE行业发展现状及趋势分析,CAE咨询细分市场快速发展「图」一、CAE行业概述CAE(Computer Aided Engineering),即计算机辅助工程,是广泛应用于工业制造业产品研发设计过程中的一种技术工具,通过模拟产品在结构强度、热传导、刚度、运动学等方面的工作状态和表现,CAE可为产品功能、性能的可用性和可靠性提供依据,为企业产品设计提供决策支持,可助力企业降低设计风险、优化设计方案、提升设计效率。
根据软件的适用范围进行划分,CAE软件可以分为通用CAE 软件和专用CAE软件两类。
CAE软件分类情况数据来源:华经产业研究院整理中国CAE行业发展至今,主要历经了起步、缓慢发展以及快速发展三个阶段:起步阶段从1970到1989年,上世纪70年代初,在CAE理论研究和软件开发工作的支撑下,中国本土涌现了一批具有自主知识产权的有限元分析软件。
但是软件的通用性和适用范围相对局限、缺乏整体竞争力限制了此类本土CAE软件的市场化及产业化进程。
缓慢发展阶段从1990到2005年,国外CAE软件厂商进入中国市场,对中国本土CAE软件厂商产生了较大冲击。
本土CAE软件的发展在这一时期则面临一定的制约,受限于资金投入不足等因素,本土CAE软件从基础研究到工程应用、再到软件商业化的进程受阻,本土CAE软件厂商的发展在此阶段发展缓慢。
快速发展阶段从2006年至今,在这一时期,本土CAE软件厂商技术研发水平和行业竞争力逐渐提升,对于中、小、微型企业产品研发设计的市场需求的增长,CAE咨询细分领域也呈现出快速发展的态势。
行业下游汽车、工程机械、航空航天等行业的市场需求持续增大,刺激了CAE市场容量的释放。
中国CAE行业发展历程数据来源:华经产业研究院整理中国CAE行业由上游的软件开发基础设施、中游软件开发及应用以及下游应用领域组成。
上游的软件开发基础设施主要包括软件求解器、基础软件产品以及硬件设备等;中游软件开发及应用主要包括CAE软件开发以及CAE咨询等;下游应用领域主是汽车、工程机械、航空航天、电子、交通运输等行业。
CAE技术的应用和发展趋势-大米的博客-中华工程师网
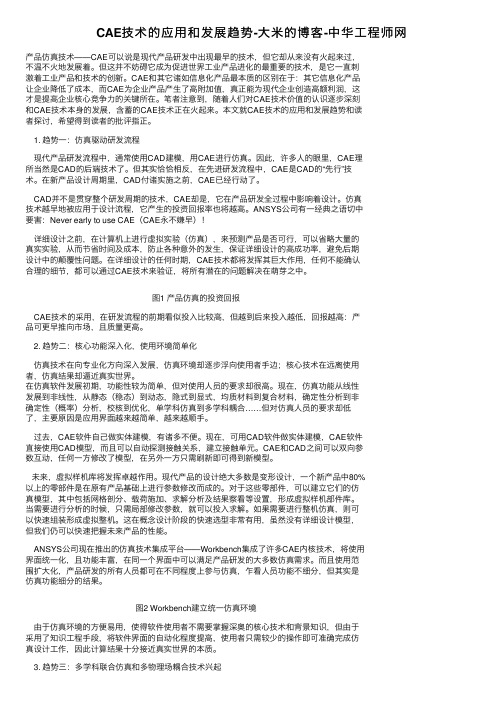
CAE技术的应⽤和发展趋势-⼤⽶的博客-中华⼯程师⽹产品仿真技术——CAE可以说是现代产品研发中出现最早的技术,但它却从来没有⽕起来过,不温不⽕地发展着。
但这并不妨碍它成为促进世界⼯业产品进化的最重要的技术,是它⼀直刺激着⼯业产品和技术的创新。
CAE和其它诸如信息化产品最本质的区别在于:其它信息化产品让企业降低了成本,⽽CAE为企业产品产⽣了⾼附加值,真正能为现代企业创造⾼额利润,这才是提⾼企业核⼼竞争⼒的关键所在。
笔者注意到,随着⼈们对CAE技术价值的认识逐步深刻和CAE技术本⾝的发展,含蓄的CAE技术正在⽕起来。
本⽂就CAE技术的应⽤和发展趋势和读者探讨,希望得到读者的批评指正。
1. 趋势⼀:仿真驱动研发流程现代产品研发流程中,通常使⽤CAD建模,⽤CAE进⾏仿真。
因此,许多⼈的眼⾥,CAE理所当然是CAD的后端技术了。
但其实恰恰相反,在先进研发流程中,CAE是CAD的“先⾏”技术。
在新产品设计周期⾥,CAD付诸实施之前,CAE已经⾏动了。
CAD并不是贯穿整个研发周期的技术,CAE却是,它在产品研发全过程中影响着设计。
仿真技术越早地被应⽤于设计流程,它产⽣的投资回报率也将越⾼。
ANSYS公司有⼀经典之语切中要害:Never early to use CAE(CAE永不嫌早)!详细设计之前,在计算机上进⾏虚拟实验(仿真),来预测产品是否可⾏,可以省略⼤量的真实实验,从⽽节省时间及成本,防⽌各种意外的发⽣,保证详细设计的⾼成功率,避免后期设计中的颠覆性问题。
在详细设计的任何时期,CAE技术都将发挥其巨⼤作⽤,任何不能确认合理的细节,都可以通过CAE技术来验证,将所有潜在的问题解决在萌芽之中。
图1 产品仿真的投资回报CAE技术的采⽤,在研发流程的前期看似投⼊⽐较⾼,但越到后来投⼊越低,回报越⾼:产品可更早推向市场,且质量更⾼。
2. 趋势⼆:核⼼功能深⼊化,使⽤环境简单化仿真技术在向专业化⽅向深⼊发展,仿真环境却逐步浮向使⽤者⼿边;核⼼技术在远离使⽤者,仿真结果却逼近真实世界。
浅谈CAE技术现状及发展趋势
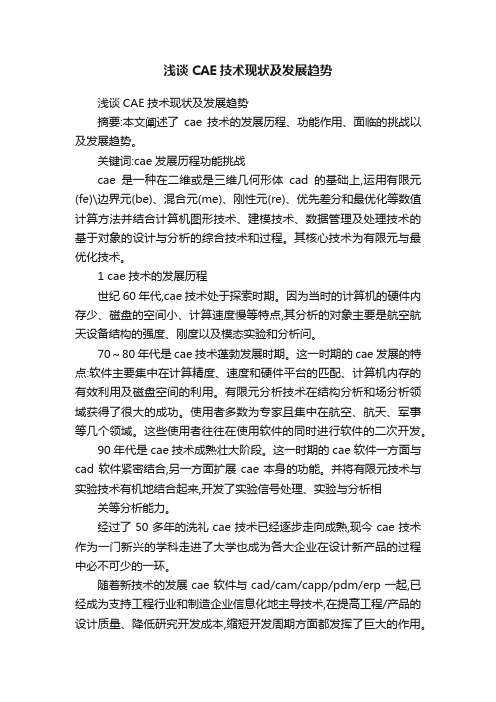
浅谈CAE技术现状及发展趋势浅谈CAE技术现状及发展趋势摘要:本文阐述了cae技术的发展历程、功能作用、面临的挑战以及发展趋势。
关键词:cae发展历程功能挑战cae是一种在二维或是三维几何形体cad的基础上,运用有限元(fe)\边界元(be)、混合元(me)、刚性元(re)、优先差分和最优化等数值计算方法并结合计算机图形技术、建模技术、数据管理及处理技术的基于对象的设计与分析的综合技术和过程。
其核心技术为有限元与最优化技术。
1 cae技术的发展历程世纪60年代,cae技术处于探索时期。
因为当时的计算机的硬件内存少、磁盘的空间小、计算速度慢等特点,其分析的对象主要是航空航天设备结构的强度、刚度以及模态实验和分析问。
70~80年代是cae技术蓬勃发展时期。
这一时期的cae发展的特点:软件主要集中在计算精度、速度和硬件平台的匹配、计算机内存的有效利用及磁盘空间的利用。
有限元分析技术在结构分析和场分析领域获得了很大的成功。
使用者多数为专家且集中在航空、航天、军事等几个领域。
这些使用者往往在使用软件的同时进行软件的二次开发。
90年代是cae技术成熟壮大阶段。
这一时期的cae软件一方面与cad软件紧密结合,另一方面扩展cae本身的功能。
并将有限元技术与实验技术有机地结合起来,开发了实验信号处理、实验与分析相关等分析能力。
经过了50多年的洗礼cae技术已经逐步走向成熟,现今cae技术作为一门新兴的学科走进了大学也成为各大企业在设计新产品的过程中必不可少的一环。
随着新技术的发展cae软件与cad/cam/capp/pdm/erp一起,已经成为支持工程行业和制造企业信息化地主导技术,在提高工程/产品的设计质量、降低研究开发成本,缩短开发周期方面都发挥了巨大的作用。
但对于cae技术的用户企业和提供商而言,cae技术仍然面临着使用复杂,工程师理论知识缺乏,缺少经验以及计算机硬件与软件结合等诸多问题2 cae技术的功能和作用(1)采用各种优化技术,找出产品的最佳设计方案。
cae软件的现状与实施方法

cae软件的现状与实施方法CAE软件的现状与实施方法CAE(计算机辅助工程)软件是一种基于计算机技术的工程分析工具,它可以帮助工程师在设计和制造过程中进行模拟和分析,以便更好地理解和优化产品性能。
CAE软件在工程领域中应用广泛,包括机械、航空、汽车、电子、建筑等多个行业。
本文将介绍CAE软件的现状和实施方法。
一、CAE软件的现状1.市场规模CAE软件市场规模不断扩大,预计到2025年将达到240亿美元。
其中,机械行业是最大的应用领域,占据了市场份额的40%以上。
此外,航空、汽车、电子、建筑等行业也在不断增长。
2.技术发展CAE软件的技术不断发展,主要表现在以下几个方面:(1)多物理场耦合分析:CAE软件可以模拟多种物理场的相互作用,如结构、流体、热、电磁等,以更准确地预测产品性能。
(2)高性能计算:CAE软件可以利用高性能计算技术,加速计算速度,提高分析效率。
(3)云计算:CAE软件可以通过云计算技术,实现分布式计算和协同工作,提高团队协作效率。
3.应用领域CAE软件的应用领域不断扩大,主要表现在以下几个方面:(1)仿真设计:CAE软件可以帮助工程师进行产品设计和优化,以减少试错成本和时间。
(2)产品测试:CAE软件可以模拟产品在不同环境下的工作情况,以便进行产品测试和验证。
(3)生产制造:CAE软件可以帮助工程师进行生产制造过程的模拟和优化,以提高生产效率和质量。
二、CAE软件的实施方法1.需求分析在实施CAE软件之前,需要进行需求分析,明确软件的应用场景和功能需求。
需求分析应该包括以下几个方面:(1)应用场景:明确软件的应用领域和具体应用场景。
(2)功能需求:明确软件需要具备的功能和性能要求。
(3)数据需求:明确软件需要处理的数据类型和数据量。
2.软件选择根据需求分析的结果,选择适合的CAE软件。
选择软件时应该考虑以下几个方面:(1)功能和性能:软件需要具备所需的功能和性能要求。
(2)易用性:软件应该易于学习和使用。
- 1、下载文档前请自行甄别文档内容的完整性,平台不提供额外的编辑、内容补充、找答案等附加服务。
- 2、"仅部分预览"的文档,不可在线预览部分如存在完整性等问题,可反馈申请退款(可完整预览的文档不适用该条件!)。
- 3、如文档侵犯您的权益,请联系客服反馈,我们会尽快为您处理(人工客服工作时间:9:00-18:30)。
(发展战略)综述CAE技术的发展和应用综述CAE技术的发展和应用引言CAE(计算机辅助工程)的特点是以工程和科学问题为背景,建立计算模型且进行计算机仿真分析。
壹方面,CAE技术的应用,使许多过去受条件限制无法分析的复杂问题,通过计算机数值模拟得到满意的解答;另壹方面,计算机辅助分析使大量繁杂的T程分析问题简单化,使复杂的过程层次化,节省了大量的时间,避免了低水平重复的工作,使工程分析更快、更准确。
于产品的设计、分析、新产品的开发等方面发挥了重要作用,同时cAE这壹新兴的数值模拟分析技术于国外得到了迅猛发展,技术的发展又推动了许多关联的基础学科和应用科学的进步。
1概论CAE技术1.1CAE技术简述CAE即计算机辅助工程是用计算机辅助求解复杂丁程和产品结构强度、刚度、屈曲稳定性、动力响应、热传导、三维多体接触、弹塑性等力学性能的分析计算以及结构性能的优化设计等问题的壹种近似数值分析方法。
随着计算机技术的普及和不断提高,CAE系统的功能和计算精度均有很大提高,各种基于产品数字建模的CAE系统应运而生,且已成为结构分析和结构优化的重要工具,同时也是计算机辅助4c系统(CAD,CAE,CAPP/CAM)的重要环节。
CAD(计算机辅助设计)、CAM(计算机辅助制造)和CAPP(计算机辅助工艺)等均属于计算机辅助工程(CAE),而计算流体动力学CFD 和有限元分析(FEA)等则是支撑CAE的分析工具和手段。
采用CAD技术来建立CAE的几何模型和物理模型。
完成分析数据的输入,通常称此过程为CAE的前处理。
同样,CAE的结果也需要用CAD技术生成形象的图形输出,如生成位移图、应力、温度、压力分布的等值线图,表示应力、温度、压力分布的彩色明暗图,以及随机械载荷和温度载荷变化生成位移、应力、温度、压力等分布的动态显示图。
我们称这壹过程为CAE的后处理。
1.2CAE技术发展历程CAE的理论基础有限元法:20世纪40年代起源于土木工程和航空工程中的弹性和结构分析问题的研究。
它的发展能够追溯到AlexanderHrennikoff(1941)和Richardcourant(1942)的工作,他们的方法具有共同的本质特征:利用网格离散化将壹个连续区域转化为壹族离散的子区域,通常叫做元。
HrenfIikofr的丁作离散用类似于格子的网格离散区域;Courant的方法将区域分解为有限个三角形的子区域,用于求解来源于圆柱体转矩问题的二阶椭圆偏。
Courant的贡献推动了有限元的发展。
1963壹1964年Besseling等确认了有限元法是处理连续介质问题的壹种普遍方法。
而后,随着计算机技术的广泛应用和发展,有限元技术依靠数值计算方法,才迅速发展起来。
近10年来。
有限元法的应用范围有了大幅度的提高,已由简单的弹性力学的平面问题扩展到空间问题、板壳问题,由静力问题扩展到稳定性问题、动力学问题和波动问题;分析对象从弹性材料扩展到塑性、粘塑性和复合材料,从固体力学扩展到流体力学、传热学、电磁学等连续介质力学领域。
将有限元分析技术逐渐由传统的分析和校核扩展到优化设计,且和计算机辅助设计(CAD)和计算机辅助制造(CAM)密切结合,形成了当下CAE技术框架。
CAE软件的发展:早期的CAE软件只是计算处理特殊单壹问题的简单程序。
上个世纪60年代开始出现大型通用CAE软件。
于此期间世界三大CAE 软件XX公司:MSC、SDEC和ANSYS先后成立。
1963年MscXX公司开发了sADsAM结构分析软件。
于1965年Msc参和美国国家航空及宇航局(NASA)发起的计算结构分析方法研究,SADsAM也正式更名为Msc/NASTRAN。
1967年sDRCXX公司成立,于1971年推出商用有限元分析软件supertab(I—DEAs)。
1970年sAsIXX公司成立,后来重组后改为称ANSYSXX公司,开发了ANSYS 通用有限元分析软件。
20世纪70—80年代是CAE技术的蓬勃发展时期,这期间许多CAE软件XX公司相继成立。
如致力于发展用于高级1二程分析通用有限元程序的MARcXX公司;致力于机械系统仿真软件开发的MDIXX公司;针对大结构、流固耦合、热及噪声分析的csARXX公司;致力于结构、流体、流固耦合分析的ADINDXX公司等等。
90年代,各CAD软件开发商壹方面大力发展自身CAD软件的功能.如CA,11A、SOUDw0RKs、UG均增加了基本的CAE前后处理及简单的线性、模态方面通过且购另外的cAE软件来增加其软件的cAE功能,如PK(PR0/E)对RAsAN的收购。
于cAD软件商大力增强其软件cAE功能的同时,cAE分析软件也于向cAD靠拢。
如MAc/NATTRAN于1994年收购了PATRAN作为自己的前后处理软件,且先后开发了和cAllA、UG等cAD软件的数据接口。
ANsYs也于大力发展其软件的ANsYs前后处理功能。
sDRcXX公司利用I—DEAs自身的cAD功能强大的优势,积极开发和别的cAD模型传输接口。
先后投放了和PR0/E、UG、cArl’IA等的接口,以保证cAD,cAE的关联性。
同时cAE软件也于积极扩展本身的功能。
ANsYS把其产品扩展为ANsY洲EcHNIcAL。
ANsYs,lS-DYNA。
ANsYs,PREP0sT等多个应用软件。
sDRc则于自己的单壹分析模型的基础上先后形成了多专项应用技术,且将有限元技术和实验技术有机地结合起来。
2CAE技术于内燃机设计中的应用内燃机作为动力机械,其各项指标涉及到燃烧、排放、油耗、密封、强度、噪声等多方面内容,所以对应的分析也涉及到热力学、流动力学、动力学、疲劳分析等多个方面。
而且内燃机的许多零部件,如曲柄连杆机构和配气机构的形状结构、受力,以及发动机的流动、传热传质、燃烧等工作过程十分复杂。
因此建立这些零部件及整机的数学模型是十分困难的,而求解数学模型则更为闲难。
另外于现代内燃机中由于对内燃机的性能和可靠性指标愈来愈高,其中的壹些参数的变化趋势相互制约,参数优化空间相对变小,研发的风险加大;产品开发需要考虑的变量不断增加。
系统的复杂性增大;要求缩短产品开发的周期;降低产品开发的成本和风险。
为满足现代内燃机丁业的发展需要,必须对传统的“绘图+经验+发动机台架试验”的设计方法进行改进。
按照现代研发的基本流程,壹款内燃机的研发主要包括设计、试验、试制、投产等阶段。
cAE分析主要涉及设计和试验阶段,设计和验证阶段的数字化开发可细分为概念设计阶段、布置设计阶段和详细设计阶段。
每个阶段均包含了数字化设计和验证工作的且行和协同:设计工程师按照时间进度提交零部件、装配的子系统及整机的CAD设计数据;验证t程师应用CAE手段对设计部门提交的CAD数据进行包括最基本的尺寸和运动学校核、复杂的动力学分析和功能实现以及最复杂的可靠性分析等进行全方位验证。
2.1概念设计阶段概念设计阶段是发动机产品开发流程中进入工程化开发过程的第壹阶段,也是最重要的阶段。
理论上来说,有关所开发产品的所有重大决策性问题均要于这壹阶段内解决。
概念设计阶段的主要工作有:对前期项目策划阶段完成的市场、法规、竞争对手和竞争机型调查研究的结果进行分析和评估,且转换为概念设计阶段的设计输入;产品设计、工艺设计、生专家们于概念设计阶段需协同进行可行性研究工作;根据产品的市场定位和仓业品牌的内涵,结合当前行业的技术发展水平等因素。
确定所开发产品于性能、质量、成本等方面适当的目标水平、具体指标和规格要求;进行整机系统总体布置研究;确定产品的总体技术方案和各子系统的总体技术路线等。
此阶段的cAE分析多以壹维分析为主,以基本结构和基本参数为输入,于整机级和各大系统级建立虚拟样,通过cAE分析方法确定发动机的基本性能、冷却系统布置、曲轴系布置和和整车的匹配等。
此阶段的cAE 分析任务有:内燃机气体交换过程模拟,此类分析软件主要有GT—Power和AVL-B00st等。
内燃机热动力学分析和整机性能预测.于气体交换的基础上增加发动机缸内燃烧过程的仿真分析,预测发动机的总体性能,如功率、扭矩和燃油消耗率等。
然后反过来确定进气系统、排气系统、由缸盖、缸体和活塞组成的燃烧系统等子系统的主要参数和技术方案。
内燃机冷却系统壹维cFD分析.此类分析软件有cT-C砌等。
内燃机润滑系统壹维cFD分析,此类分析软件有f'10wM 艄ter等。
装备该内燃机的整车的基本性能仿真分析,该类分析软件主要有AVL —Cmise和GT—Drive等。
2.2布置设计阶段:布置设计阶段主要是确定各主要零部件的尺寸和和相互之间的关系及接口,进壹步对概念设计阶段确定的技术方案进行细化。
此阶段的cAD设计工作主要是根据概念设计阶段的cAE仿真结果建立内燃机各大子系统的表面模型,确定和建立各大子系统之间的装配关系和模型等。
CAE仿真分析则需要对所有的概念设计阶段的分析模型进行更新,使之更加具体和复杂,仿真的输出结果也更加详细和准确。
同时。
增加新的壹些cAE仿真分析内容和领域,涉及动力学、有限元、cFD分析等,如应用MsC.ADAMs等行业常用的专业软件建立分析模型,首先埘前端轮系和配气机构子系统的布置设计结果进行各运动零部件之间的装配和运动学关系进行检查和校核.然后开始动力学分析。
缸盖、缸体、曲轴、凸轮轴和连杆五大主要零部件的有限元分析,常用的分析软件有Hyperworks、NAsTRAN、ABAQus、AVL—ExCl7I等。
2.3详细设计阶段:详细设计阶段,数字化开发范围将覆盖所有新设计零部件的全部特性,包括如详细的尺寸、尺寸和几何公差、设计基准、表面粗糙度、热处理和材料技术条件等,于详细设计阶段结束时将保证每壹个零部件的cAD设计数据(包括i维实体设计数据和二维平面设计数据)将能具体指导工厂的生产制造,因此,cAD设计的工作量急剧增长,成为详细设计阶段的主要1二作。
同时,于详细设计阶段将应用CAE分析手段对所有新设计零部件的CAD设计进行分析和验证,以确保于数字化开发阶段解决每个新设计的零部件以及从零部件到各子系统、最后到整机的每个层次均不存于问题。
此阶段,CAE分析的首要任务是对前俩个阶段所有的分析模型根据详细设计阶段能够获得的最全面的设计信息进行最后的更新和拓展,进壹步更准确地验证各零部件、系统和整机的功能和特性。
比如于概念设计和布置设计阶段进行的发动机气体交换壹维cFD分析的基础上将进壹步拓展和更新到进行壹维或三维的进排气噪声分析,进排气系统和发动机缸内流动的=三维cFD分析。
目的是从三维角度考察发动机的气体交换过程和流体于发动机缸内的流动过程,保证发动机各缸进排气的均匀度和发动机缸内流动的最佳化,以及于保证发动机性能设计指标的前提下尽量降低发动机的进排气噪声。