涂装车间节能环保应用案例
涂装车间降本增效方案

涂装车间降本增效方案涂装车间“降本增效”实施方案涂装车间“节能降耗、降本增效”实施方案按照公司2017年提出的“降本增效”相关指示,针对海虹公司正处于爬坡困难阶段的特性,生产成本较高,产品价格过低等严峻的形式,我车间为了进一步降低运行及检修成本,充分发挥车间优势,最大限度的做好的节能降耗、降本增效工作,认真分析了目前车间生产运行指标情况,尤其对可控成本项目的支出情况进行了认真分析。
努力寻找“节能降耗、降本增效”的突破口,为全面实现年度目标,增强车间职工的责任感和使命感研究制定了管理措施和实施方案。
一、“节能降耗、降本增效”目标通过开展“降本增效”实践活动,使全车间牢固树立成本意识、节约意识、效益意识,以创新的思维寻求降本增效的新途径,彻底改变工作中存在的问题,从自身做起,从现在做起,从点滴做起,从节约一度电、节约一滴水做起,通过良好的行为习惯,务实的工作作风,为完成年度目标贡献力量,真正实现公司效益的稳步增长。
二、降本增效领导小组及职责组长:林占宏副组长:孙炳宗钟彪马效农尹享军刘利武组员:常华刘文智吉福家裴少鹏都文明张毅刚张睿桢姚卫国肖利云代致林姚鹏飞袁文彦杨进财崔廷奎汪海华严宝春王万保徐志良魏全才郭红平沈元秀三、节能降耗、降本增效具体措施一)仪表设备及检修、维护方面:1.靠管理降低成本要降低成本,必须抓住管理这个纲。
动力车间仪表工段将强化成本核算,在温度变送器、阀门垫片、螺栓、工器具易耗品(螺丝刀套组、扳手、万用表、内六角套组)、电线电缆、盘根、就地仪表等各个环节加强管理,把生产检修中所用的材料、备品备件等细化到每项检修工作成本中,形成全员、全过程、全方位的成本控制格局,使降低成本落实到每个职工的具体行动中。
在此基础上要加强材料、物资存放管理,车间要对入库的配件进行联合验收,并要求供货商提高备品备件的质量及精度,同时车间对领回的材料、配件进行定制摆放,对轻度有问题仪表要重点保护,避免仪表光使用,不维护,防止仪器仪表损坏程度达到不可维修的程度,造成不必要的成本损失。
喷漆车间环保环境措施
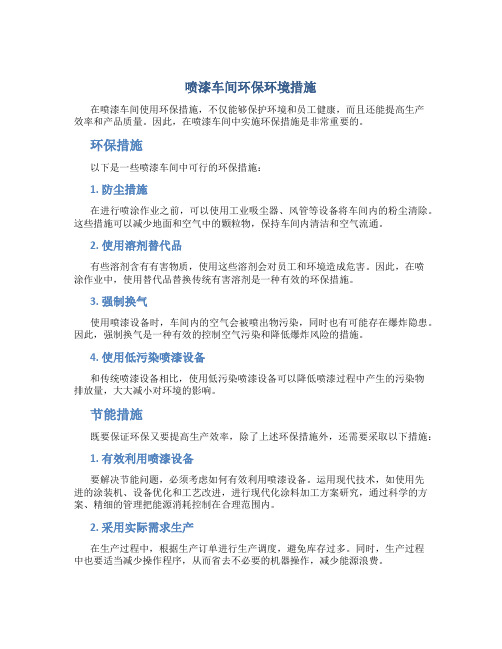
喷漆车间环保环境措施在喷漆车间使用环保措施,不仅能够保护环境和员工健康,而且还能提高生产效率和产品质量。
因此,在喷漆车间中实施环保措施是非常重要的。
环保措施以下是一些喷漆车间中可行的环保措施:1. 防尘措施在进行喷涂作业之前,可以使用工业吸尘器、风管等设备将车间内的粉尘清除。
这些措施可以减少地面和空气中的颗粒物,保持车间内清洁和空气流通。
2. 使用溶剂替代品有些溶剂含有有害物质,使用这些溶剂会对员工和环境造成危害。
因此,在喷涂作业中,使用替代品替换传统有害溶剂是一种有效的环保措施。
3. 强制换气使用喷漆设备时,车间内的空气会被喷出物污染,同时也有可能存在爆炸隐患。
因此,强制换气是一种有效的控制空气污染和降低爆炸风险的措施。
4. 使用低污染喷漆设备和传统喷漆设备相比,使用低污染喷漆设备可以降低喷漆过程中产生的污染物排放量,大大减小对环境的影响。
节能措施既要保证环保又要提高生产效率,除了上述环保措施外,还需要采取以下措施:1. 有效利用喷漆设备要解决节能问题,必须考虑如何有效利用喷漆设备。
运用现代技术,如使用先进的涂装机、设备优化和工艺改进,进行现代化涂料加工方案研究,通过科学的方案、精细的管理把能源消耗控制在合理范围内。
2. 采用实际需求生产在生产过程中,根据生产订单进行生产调度,避免库存过多。
同时,生产过程中也要适当减少操作程序,从而省去不必要的机器操作,减少能源浪费。
3. 采用高效节能设备使用高效节能设备,降低能源消耗和生产成本。
例如,使用高效的喷漆设备,可以降低能源消耗并提高生产效率。
结语在喷漆车间中,实施环保措施和节能措施既有助于保护环境和员工健康,又能提高生产效率和产品质量。
因此,在喷漆车间中加强环保和节能管理,促进可持续发展,具有重要的意义和价值。
节能减排在工业制造中的实践案例有哪些

节能减排在工业制造中的实践案例有哪些在当今全球气候变化和资源短缺的背景下,节能减排已成为工业制造领域的重要课题。
众多企业积极采取各种措施,以实现可持续发展的目标。
下面将为您介绍一些在工业制造中成功的节能减排实践案例。
案例一:某汽车制造企业的能源管理优化这家汽车制造企业深知能源消耗在生产过程中的重要性。
他们首先对整个工厂的能源使用情况进行了详细的监测和分析。
通过安装智能电表和传感器,实时收集各个生产环节的能源数据,包括电力、燃气、水等。
基于这些数据,企业发现涂装车间的能源消耗较大。
于是,他们对涂装工艺进行了改进。
采用了更先进的涂装设备和技术,减少了涂料的浪费,同时提高了涂装效率。
此外,优化了车间的通风系统,通过智能控制,根据生产需求自动调整风量,避免了不必要的能源消耗。
在照明方面,企业将传统的灯具更换为节能型的 LED 灯,并安装了智能照明控制系统,根据自然光照和车间的使用情况自动调节亮度。
这一系列措施使得该企业的能源消耗大幅降低,不仅降低了生产成本,还减少了对环境的影响。
案例二:某钢铁企业的余热回收利用钢铁生产过程中会产生大量的余热,如果不加以利用,将造成巨大的能源浪费。
这家钢铁企业建立了完善的余热回收系统。
在炼铁环节,高温炉渣蕴含着大量的热能。
企业通过余热锅炉将炉渣的热量回收,产生蒸汽用于发电和供暖。
在炼钢环节,高温烟气也被收集起来,通过余热回收装置进行热能转换。
此外,企业还对冷却循环水系统进行了优化,将冷却过程中产生的余热用于周边居民的冬季供暖。
通过这些余热回收利用措施,该钢铁企业不仅减少了能源的外购需求,还提高了能源的综合利用效率,降低了碳排放。
案例三:某电子制造企业的绿色供应链管理这家电子制造企业将节能减排的理念延伸到了整个供应链。
他们在选择供应商时,不仅关注产品质量和价格,还将供应商的环境表现纳入考量。
要求供应商提供原材料的环境认证,确保原材料的生产过程符合环保标准。
同时,鼓励供应商采用绿色包装材料,减少包装废弃物的产生。
化工行业环保技术应用案例
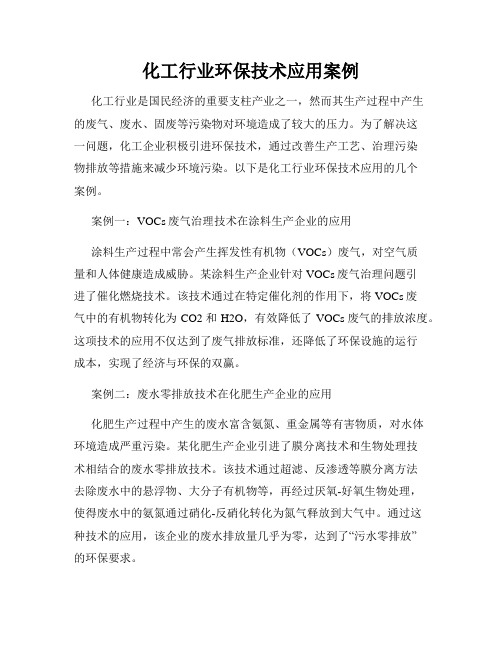
化工行业环保技术应用案例化工行业是国民经济的重要支柱产业之一,然而其生产过程中产生的废气、废水、固废等污染物对环境造成了较大的压力。
为了解决这一问题,化工企业积极引进环保技术,通过改善生产工艺、治理污染物排放等措施来减少环境污染。
以下是化工行业环保技术应用的几个案例。
案例一:VOCs废气治理技术在涂料生产企业的应用涂料生产过程中常会产生挥发性有机物(VOCs)废气,对空气质量和人体健康造成威胁。
某涂料生产企业针对VOCs废气治理问题引进了催化燃烧技术。
该技术通过在特定催化剂的作用下,将VOCs废气中的有机物转化为CO2和H2O,有效降低了VOCs废气的排放浓度。
这项技术的应用不仅达到了废气排放标准,还降低了环保设施的运行成本,实现了经济与环保的双赢。
案例二:废水零排放技术在化肥生产企业的应用化肥生产过程中产生的废水富含氨氮、重金属等有害物质,对水体环境造成严重污染。
某化肥生产企业引进了膜分离技术和生物处理技术相结合的废水零排放技术。
该技术通过超滤、反渗透等膜分离方法去除废水中的悬浮物、大分子有机物等,再经过厌氧-好氧生物处理,使得废水中的氨氮通过硝化-反硝化转化为氮气释放到大气中。
通过这种技术的应用,该企业的废水排放量几乎为零,达到了“污水零排放”的环保要求。
案例三:固废资源化处理技术在石化企业的应用石化企业生产过程中产生的固体废物包括废塑料、废橡胶、废纸板等各类废弃物,对土地资源和生态环境带来了威胁。
某石化企业引进了固废资源化处理技术,将废塑料和废橡胶等固体废物通过热解、裂解等方法转化为可燃气体和液体燃料。
这种资源化处理技术不仅减少了固废的数量,还能够将固废转化为能源,实现了废物变废为宝的环保目标。
上述案例仅为化工行业环保技术应用的几个典型案例,实际上,化工企业在环保技术应用方面还有很多创新和努力。
通过引进和应用环保技术,化工行业能够有效降低对环境的污染,改善生产过程,实现可持续发展。
在未来,我们期待化工行业在环保技术应用方面取得更大的突破和进步,为建设美丽中国做出更大的贡献。
施工期环保措施实施案例与效果

施工期环保措施实施案例与效果在当今社会,环境保护已经成为了各行各业发展过程中必须重视的关键问题。
尤其是在建筑施工领域,由于施工活动可能对周边环境造成多方面的影响,如噪音污染、粉尘污染、水污染和固体废弃物污染等,因此采取有效的环保措施至关重要。
接下来,将为您介绍几个施工期环保措施的实施案例,并分析其取得的效果。
案例一:城市商业综合体建设项目在一个繁华的城市中心,一座大型商业综合体正在如火如荼地建设中。
为了减少施工对周边环境的影响,施工团队采取了一系列环保措施。
在噪音控制方面,施工团队选用了低噪音的施工设备,并对设备进行定期维护和保养,确保其处于良好的运行状态,以降低噪音排放。
同时,合理安排施工时间,避免在居民休息时间进行高噪音作业。
对于必须连续施工的工序,提前向周边居民发布公告,并采取有效的隔音措施,如设置隔音屏障。
在粉尘控制方面,施工现场设置了围墙和围挡,并在出入口安装了车辆冲洗设备,确保驶出工地的车辆不带泥上路。
对易产生扬尘的物料进行覆盖,施工过程中定期洒水降尘。
此外,还安装了扬尘在线监测设备,实时监测施工现场的扬尘浓度,一旦超过限值,立即采取相应的降尘措施。
在水污染控制方面,施工团队建设了完善的排水系统,将施工废水和雨水进行分类收集和处理。
施工废水经过沉淀、过滤等处理达标后,用于施工现场的洒水降尘或绿化灌溉。
对于生活污水,接入城市污水管网进行集中处理。
在固体废弃物处理方面,对施工过程中产生的建筑垃圾进行分类收集和存放,可回收利用的部分进行回收,不可回收的部分及时清运至指定的垃圾填埋场。
对于生活垃圾,设置专门的垃圾桶,并定期由环卫部门清运处理。
通过以上环保措施的实施,该商业综合体建设项目在施工期间有效地减少了对周边环境的影响。
周边居民的投诉明显减少,施工现场的环境质量得到了显著改善。
同时,由于环保措施的有效实施,项目也赢得了当地政府和社会的好评,提升了企业的社会形象。
案例二:高速公路建设项目高速公路的建设往往跨越较大的区域,对环境的影响范围较广。
举例说明本田公司避免浪费,合理利用资源的案例

举例说明本田公司避免浪费,合理利用资源的案例本质上的环保、节能的工厂广汽本田的增城工厂在建设时将节约能源、降低排放作为重要的目标。
广汽本田增城工厂不仅实现了中国汽车行业中第一个“废水零排放”的工厂,将生产对环境的影响降到最低,还是“本质上节能的工厂”。
广汽本田增城工厂在规划时就充分考虑了能源集约化建设。
增城工厂的能源动力站房集中在厂区的中东部,靠近各车间的负荷中心。
在工厂布局中,综合动力站房与公司最大的能耗车间——涂装相邻。
能源动力统一集中供应,在能源节约方面起到了重要作用。
在规划厂房建设时,增城工厂也充分考虑到节能的因素。
增城工厂的厂房建筑采用了节能设计,在屋顶和墙板设置了隔热层,提高了厂房的隔热性能;厂房也充分考虑了自然采光,在白天时采用自然光照明,减少了室内照明用电;综合办公楼采用双层玻璃中空隔热设计,减少了热传导,降低了空调的冷量损失,节约用电。
在能源动力站房的建设中,增城工厂也全面考虑了节能降耗,充分借鉴黄埔工厂的经验,建立了完善的能源供应及自控管理系统。
增城工厂的中央制冷站房采取高低压制冷机组混编,大小制冷机组混编,二次泵循环的系统,最大限度的降低能耗;空压站根据不同用户的需求区别供应压缩空气,采用 0.8Mpa(兆帕)和1.0Mpa两个供应系统,避免了向所有车间提供高压压缩空气所带来的能源浪费;空压站的大容量空压机采用10KV高压电来供电,最大限度的降低了电能变压过程中的能耗。
广汽本田增城工厂项目筹备之初,“建设节能环保的新工厂”就是增城工厂建设项目的目标之一。
增城工厂在环保、节能理念的指导下,在设计和建设过程中,全面地考虑了环保问题,在处理工业及生活废水的处理投入巨资,导入最先进的环境技术“膜处理技术”,废水经过处理后,全部循环使用到厂区的各相应用水点,包括:绿化、马路冲洗、涂装车间工艺用水等,在中国汽车行业中第一个实现“废水零排放”,成为本田公司中第一实现“废水零排放”的样板工厂。
能环保的涂装车间
能环保的涂装车间工程及成套设备公司杜尔将为大众波兹南公司Crafter后继车型的生产建造一整套涂装车间,该车间对水,能源和各种材料的消耗将非常少,能帮助客户实现节能,环保以及可持续发展的目标.工程及成套设备公司杜尔将为大众波兹南公司Crafter后继车型的生产建造一整套涂装车间,该车间对水、能源和各种材料的消耗将非常少,能帮助客户实现节能、环保以及可持续发展的目标。
作为总承包商,杜尔不仅为大众波兹南公司提供喷涂设备,也负责整个项目的承建工作。
安装方面,杜尔将提供PT/ED工艺区的浸涂槽以及1条中涂线、2条底漆线、2条面漆线及喷漆室、烘房、传输系统、废气净化和工作站。
从电泳浸涂工艺开始,杜尔和大众就非常注重项目的可持续性。
所以,此项目将使用既节能又能防止故障、保证安全的电泳浸涂解决方案EcoDC MACS。
该系统采用模块化阳极控制,能在浸涂槽中产生随车身而移动的可控制性电压和电流。
这一概念结合创新的电力电子技术,能保证电压和电流的精确供给,既保证了车身的能源需求,也将最大程度保证车身的涂装质量。
此外,运送车身穿过浸涂槽将由有史以来建造的最长的摆式传输系统完成。
18个EcoRS16型机器人从事汽车底部的喷涂和密封;36个EcoRP E和EcoRP L型机器人,每个都配备了高速旋转雾化器EcoBell3,将从事中涂线及2条底漆线和面漆线的全自动化内外喷涂。
雾化器EcoBell3和换色器EcoLCC2的联合使用使底漆区域的换色通过推压工艺只耗时不到10s。
在推压工艺操作中,油漆阀在整个喷涂工艺完成前处于关闭状态,留在涂料软管中的油漆被推向带有溶剂的雾化器。
换色过程中,油漆的损失量为10~15ml。
标准色的供给方面,大众主要依赖成熟、可靠的循环技术;特殊颜色则通过灵活的挤压专用油漆系统EcoSupply P供给。
通过采用挤压技术(管道检测规格=适用的车身),色料通过管道挤压被推送出去,不会有任何残留。
这尤其提高了材料的使用效率,节省了生产成本。
汽车涂装节能减排的新工艺技术
汽车涂装节能减排的新工艺技术随着现代城市化的快速发展,汽车已经成为人们日常生活中不可或缺的交通工具。
汽车尾气排放所带来的环境问题,特别是空气污染和温室气体排放,已经成为全球性的难题,需要寻求有效的解决方案。
在汽车制造工艺中,涂装是一个重要的环节,而采用节能减排的新工艺技术,可以有效地降低汽车涂装过程中的能源消耗和环境排放。
传统的汽车涂装工艺中常常采用有机溶剂型油漆,这种油漆在固化过程中会释放大量的挥发性有机化合物(VOCs),不仅对人体健康有害,同时也是空气污染的主要来源之一。
通过新的涂装工艺技术,降低VOCs排放,减少化石能源的消耗,成为了当前汽车制造企业面临的重要课题。
在新工艺技术上,水性涂料是一种被广泛采用的替代品。
相比起传统的有机溶剂型油漆,水性涂料具有挥发性有机化合物低、环境友好、对作业人员安全、对涂装设备腐蚀小等诸多优点。
水性涂料的使用还能够显著降低涂装过程中的能源消耗,减少CO2排放,实现节能减排的目标。
水性涂料在应用中也存在一些技术难题,比如涂料的附着力、光泽度、硬度等方面的要求可能不能完全满足,需要不断进行技术创新和改进。
在此背景下,一些汽车涂料和涂装设备的生产企业加大了研发投入,不断推出新型的水性涂料产品和涂装工艺技术。
另一个节能减排的新工艺技术是粉末涂料。
粉末涂料是一种无溶剂、无VOCs排放的环保涂料,具有优异的耐候性、耐化学性和表面效果,被广泛应用于汽车制造领域。
相比水性涂料,粉末涂料还具有携带和储存方便、不受温度影响、遮盖力强等优势,因此在一些汽车生产线上已经开始广泛采用。
值得一提的是,光固化涂料技术也是一项能够节能减排的新工艺技术。
光固化涂料是指在特定波长的紫外光或电子束辐射下,利用光引发剂催化引发反应,实现涂料从液态到固态的转变。
与传统的热固化涂料相比,光固化涂料的固化时间短,能耗低,不需要挥发性有机化合物的固化剂,因此能够有效减少能源消耗和VOCs排放。
在汽车涂装工艺中,适用光固化涂料技术也需要相应的设备改造和调整。
涂装车间改善提案案例
涂装车间改善提案案例
在涂装车间进行生产时,我们经常会遇到一些问题,比如涂装质量不稳定、生
产效率低下、环境污染严重等。
为了解决这些问题,我们提出了一些改善提案,希望能够对涂装车间的生产进行优化。
首先,针对涂装质量不稳定的问题,我们建议引入先进的自动涂装设备,通过
自动化技术来控制涂装厚度和均匀度,从而提高涂装质量的稳定性。
同时,我们还可以加强对涂装工艺的管理和监控,制定严格的操作规程和质量标准,确保每一道工序都能够达到要求的质量水平。
其次,针对生产效率低下的问题,我们建议优化生产线布局,采用流水线作业
模式,减少物料和人员的等待时间,提高生产效率。
同时,我们还可以引入智能化生产管理系统,实现生产过程的实时监控和数据分析,及时发现并解决生产中的瓶颈问题,提高生产效率。
另外,针对涂装车间环境污染严重的问题,我们建议加强对废气和废水的处理,引入先进的环保设备,减少废气和废水的排放,保护环境。
同时,我们还可以加强对涂装材料的选择和管理,选择低挥发性有机物(VOC)的涂料和溶剂,减少有
害物质的排放,保障员工和环境的健康。
综上所述,通过引入先进的设备和技术、优化生产管理和监控、加强环保措施
等方式,我们可以有效解决涂装车间存在的问题,提高涂装质量、生产效率和环境保护水平,实现涂装车间的全面优化。
希望相关部门能够认真考虑我们的改善提案,共同努力,推动涂装车间的持续发展和进步。
涂装车间技术团队优秀事迹
涂装车间技术团队优秀事迹
涂装车间技术团队在过去一年里展现了出色的表现,取得了许多令人瞩目的成就。
以下是他们的一些优秀事迹:
1. 提高生产效率:技术团队引入了先进的涂装设备和自动化系统,通过优化工艺流程和操作方式,大幅提高了涂装车间的生产效率。
他们成功地减少了生产周期、缩短了交付时间,并提高了产能利用率。
2. 提升产品质量:团队致力于不断改进涂装工艺和技术,通过精确的调控涂装参数和材料选择,有效降低了产品的瑕疵率。
他们还引入了质量控制流程,从根本上提高了产品的质量稳定性和一致性。
3. 节约资源:为了减少能源消耗和废料产生,技术团队采用了节能环保的涂装工艺和材料。
他们研发了高效的涂装方案,有效减少了废料的产生,并优化了能源利用效率,实现了资源的可持续利用。
4. 系统升级与优化:团队定期进行设备维护和升级,确保涂装设备的正常运行。
他们还优化了涂装设备的控制系统,提升了操作的便捷性和精确性。
通过引入新技术和工具,他们不断提升团队的整体技术实力。
5. 团队合作与培训:为了提高整个涂装车间的工作效率和质量水平,技术团队注重团队合作和员工培训。
他们组织了各类培训课程,提升了员工的技能水平和专业知识,并鼓励团
队成员之间的合作交流,共同解决问题和提升工作效果。
涂装车间技术团队凭借出色的表现和杰出的成就,为公司带来了巨大的效益和声誉。
他们的优秀事迹不仅在本车间内得到了广泛认可,也在公司内外赢得了良好的口碑。
团队成员以他们的专业素养和奉献精神为公司树立了典范,为行业的发展树立了良好的榜样。
- 1、下载文档前请自行甄别文档内容的完整性,平台不提供额外的编辑、内容补充、找答案等附加服务。
- 2、"仅部分预览"的文档,不可在线预览部分如存在完整性等问题,可反馈申请退款(可完整预览的文档不适用该条件!)。
- 3、如文档侵犯您的权益,请联系客服反馈,我们会尽快为您处理(人工客服工作时间:9:00-18:30)。
31
□Ro-Dip3全旋反向浸渍输送技术的应用
RoDip3输送系统实现车身在前处理、电泳槽体内360°翻转, 使槽体体积大大缩减,同时也缩短了生产线长度,节省设备 安装面积。 采用RoDip3输送系统,产能30JPH的前处理、电泳生产线总 长360米左右,相比传统浸渍是输送系统,缩短超过20%的生 产线长度。
37
的精力和资金进行工艺和设备选型,引进了不少世界 先进的节能环保工艺和技术,在国内同行业内处于领
先地位。
6
2
先进节能环保工艺
□前处理逆流补加技术
涂装车间前处理工艺流程
表调 浸洗 喷淋 脱脂 预脱脂
脱 脂 段
磷化
喷淋
浸洗
纯水洗
沥干
磷 化 段
前处理工艺主要流程:
预脱脂—脱脂—水洗—表调—磷化—二次水洗—纯水洗—沥干
24
□节能型烘干烤箱的应用
加热 区
加热 区
加热 区
保温 区
保温 区
烤箱加热采用独立加热和焚烧废气换热相结合的方 式,将废气焚烧后的热量重新利用到烤箱加热环节 中,代替了传统的全部采用独立加热的方式,减少 了燃烧炉的使用量。
25
□节能型烘干烤箱的应用
设备布局紧凑,节省安装空间;
密封效果好,冷空气进气量小,热量损失小,节能 20%~30%; 减少了燃烧炉的数量,大大提高了能源的利用率,; 减少了废气排放量,总废气排放量可减少约50%; 新鲜空气经过加热后进入烤箱,有效解决了冷凝滴液现 象的产生。
28
□先进的烤箱废气处理系统
车间引进德国杜尔的废气处理系统TAR。 来自烘干室的废气经过位于TAR外壳的废气热交换器,使其温 度升高到500°C左右,再经过燃烧室700°C以上的高温喷燃, 使废气中的VOC成分完全分解; 被分解后的高温废气,再陆续经过三级换热后排出,使废气 中蕴含的热能得到充分的利用。
15
□ 电泳漆超滤回收技术
涂料利用率提高,既节省成本又节约资源;
实现废涂料零排放,根源上避免环境污染;
水资源循环利用,避免了资源浪费。
16
□ 水性涂料的应用
喷漆涂料是汽车涂装所产生的污染物的主要来源,目前环保 法规已经对喷漆涂料在环保和健康方面的要求越来越严格; 传统的喷漆涂料中含挥发性有机物(VOC)属于对人体和环 境有害的物质,常接触会使人患急或慢性中毒、职业病等, 通常称为“苯中毒”; 汽车工业发达的国家基本上已经实现低VOC含量的水性涂料 替代传统的有机溶剂型涂料的更新换代。
型、资源节约型、低碳经济型和社会主义和谐型社会
的创建。
4
□背景介绍
我公司积极引入“绿色涂装”理念,将“创建绿色 涂装车间”作为企业经营和发展的目标,倡导“清洁 生产、节能减排、降低成本”的管理方式,将节能环 保的发展方针积极地贯彻到生产实际中。
5
□背景介绍
为建设高端涂装车间,我公司在建厂初期投入大量
11
□ 电泳漆超滤回收技术
电泳涂装技术是利用外加电场使悬浮于电泳液中的颜料和树 脂等微粒定向迁移并沉积于电极之一基底表面的涂装方法。
12
□ 电泳漆超滤回收技术
电泳工艺流程
电泳
一次 喷淋 浸洗 二次 喷淋 新鲜纯 水洗 沥干
水+30% 涂料 排放 电泳后的车身需要4道纯水冲洗清洗工序才能进入到下一工 艺,清洗过程不但消耗大量纯水,而且30%的涂料也会被冲 洗掉排放掉,不仅造成了浪费而且污染环境。
26
□先进的烤箱废气处理系统
烤箱烘干室排放的废气含有大量挥发性有机气体(VOC), 属于有毒有害气体,根据环境保护要求,此类高温废气必须 经过处理达标后才能排放到大气中。
27
□先进的烤箱废气处理系统
废气处理的主要方法是通过高温炉焚烧,焚烧后废气中的 VOC成分被有效分解,但将所有烤箱的废气集中焚烧需要消 耗大量能源,不利于节能减排。
9
□前处理逆流补加技术
前处理逆流补加原理示意图
后 前
补加
表调 浸洗
补加
喷淋 脱脂
补加
预脱脂
前
后
补加
磷化 喷淋 浸洗
补加
纯水洗
所谓逆流补加是指相同功能的槽体间,当前槽槽液不足时后 槽自动向前槽进行补加,以补充前槽的消耗。
10
□前处理逆流补加技术
采用这种“后水前用”槽液逆流补加方式,在保证了后槽液 量及时补充的同时,也保证了前槽槽液的洁净度; 大大提高了水资源的利用率,有利于保护水资源; “后水前用”不单是水资源的多次利用,化学药剂也得到了 充分利用,不但节约了成本,同时也减少了污染排放量,有 利于保护环境;
35
4
结束语
□结束语
本文主要对涂装车间在先进节能环保型工艺和设备的应用方
面进行了介绍,同时也就新旧工艺设备在安装布局、能源利
用、工艺效果以及环境保护等方面的优劣点进行了比对分析。 分析结果表明,车间所应用的节能环保型工艺及设备,与现 行的传统型生产线相比具有诸多的技术优势,在提高产品品质 的同时更兼顾了生产的经济性和环境友好性,为节能减排和环 境保护做出了突出贡献。
29
清漆
VOC(指标)
51 29 20
溶剂型涂装体系 水性涂装体系
色漆
中涂
0
水性涂料体系的VOC削减效果
以色漆线为例,仅用水性底色漆替代溶剂型底色漆就可以削减 VOC排放量80%以上。
采用的水性涂装体系(水性中涂/水性色漆/溶剂型清漆)相比 传统的溶剂型涂装体系,削减VOC的效果十分显著。
19
22
□节能型烘干烤箱的应用
传统直通型烤箱5大问题点:
直通式构造,占地总长度大,设备布局不紧凑; 进出口气密效果差,热两损失较大;
冷空气进气量大;
排放废气量大; 进出口容易出现冷凝滴液现象。
23
□节能型烘干室箱的应用
车间采用德国杜尔的U型回转式烘干炉,结合桥式设 计的进出口作为气封室,大大提高了室体的密封 性; 采用循环往复的运输方式,从接车、载车、送车到 再接车,构成特有的环形输送系统,在保证了工作 效率的同时也提高了设备利用率。
17
□ 水性漆的应用
水性涂料是环保型绿色涂料,采用水性涂料替代现用有机溶 剂型涂料是工业涂装低VOC化的主流措施。 涂装车间中涂和色漆工艺都采用水性漆作为涂料,相比传统 的溶剂型涂料,水性涂料在安全和环保方面的都有本质性的 改变。
18
□ 水性漆的应用
120 100 80 60 40 20
29
□先进的烤箱废气处理系统
第一级换热:700°C左右的高温废气经TAR外壳处的废气热交 换器,对烘干室中排出得废气进行预热,换热后温度降到 500°左右; 第二级换热:500°左右的高温废气再经过烘干室多个热交换 器,对循环热风进行加热,使室内温度恒定在180°上下; 第三级换热:最后废气还会与20°C左右的新鲜空气进行热交 换,最后排出到大气中。
30
□先进的烤箱废气处理系统
烤箱是涂装成车间主要的天然气消耗单元,使用基于TAR的废 气处理系统,燃气利用率可达70%,热效率提高1倍以上,极 大提高了能源利用率,对于涂装节能贡献巨大。 经过逐级换热,在有效利用了废气中热量的同时,废气本身 的温度也随之降低,达到排放标准,与利于环境保护,可谓 一举双收。
33
□壁挂式喷漆机器人
壁挂式喷漆机器人取消了传统落地式机器人的安装底座,采 用悬挂的方式安装固定在室体壁两侧。 采用壁挂式机器人,在一定程度上缩短了喷漆室体宽度,使 室体占用的空间更小,而室体内的可用空间则更大。
34
□壁挂式喷漆机器人
喷漆室需要热量和水分保证温湿恒定,缩减空间同样减少了 热量和水分的消耗,节约了能源和资源; 喷漆室运行过程中要维持一定的正压强,作业空间变小,送 排风量的需求随之减少,节约了风机运行消耗的电能; 室体变窄提高了漆雾捕捉效果,有利于改善室体内工作环 境,保障人体健康。
8
□前处理逆流补加技术
前处理的工艺动作主要以喷淋和浸洗为主,车身每通过一个 盛有特定化学成分的功能槽后,都会经过多个水洗槽冲洗干 净。 车身出槽时会带出一部分槽液进入下一槽体,对后槽(主要 是水洗槽)槽液造成污染,影响清洗效果和工艺质量。 为保证槽液清洁,必然增加排污量和耗水量,造成资源浪费 和环境污染。
13
□ 电泳漆超滤回收技术
电泳漆超滤回收技术,即将超滤系统应用到电泳工艺中,形 成一套完备的槽液循环系统,将流失掉的涂料从水洗溶液中 分离出来,重新返回利用的技术方法。
14
□ 电泳漆超滤回收技术
后段水洗工序中被冲洗掉的废涂料,通过逆流补加方式随纯 水逐级流回电泳主槽中; 超滤系统不断地抽取主槽中的槽液,并对其中的涂料和水进 行超滤分离,分离后的涂料继续返回到主槽中使用,水溶液 则被重新利用到后段的喷淋系统中,进而实现了电泳漆和喷 淋水的循环利用。
涂装车间节能环保 应用案例
主要内容
1
背景介绍 先进节能环保工艺 先进节能环保设备 结束语
2
3
4
业的污染和能耗
大户。汽车涂装的公害主要包括以下危害环境和人类 健康的物质:
1、VOC(挥发性有机化合物);
2、二氧化碳、二氧化硫、氮化物、等; 3、污水和固态废弃物;
32
□Ro-Dip3全旋反向浸渍输送技术的应用
采用Ro-Dip3输送系统使前处理线总槽液量节约15%,电泳 线总槽液量节约33%,其中电泳漆节约量可达28%,大大节 约了药剂和水资源的使用量。 由于槽体体积变小,循环泵的使用数量减少,节约资金和能 源;(总投资节约15%) 车身旋转180°出槽,带液量极少,减少浪费; 100%避免了气泡的产生,工艺质量得到极大保障; 电泳漆膜厚均匀,车体内部膜厚明显提高。