新技术新工艺-细晶铸造
铸造时细化晶粒的方法

铸造时细化晶粒的方法以铸造时细化晶粒的方法为题,我们将介绍一些常用的方法和技术,以帮助读者更好地理解和应用这些方法。
铸造是一种常见的金属加工方法,通过将熔化的金属注入到模具中,并使其冷却固化,从而得到所需的产品。
而晶粒细化则是提高金属材料性能的一种重要手段。
第一种方法是通过合金化来细化晶粒。
在铸造过程中,添加适量的合金元素可以改变金属的凝固行为,从而实现晶粒细化。
常用的合金元素有钛、铌、锆等,它们可以与金属原子形成稳定的化合物或固溶体,阻止晶粒的生长,从而使晶粒变得更为细小。
此外,合金化还可以改善材料的力学性能和耐腐蚀性能。
第二种方法是通过快速冷却来细化晶粒。
当金属迅速冷却时,晶粒生长的时间变得有限,从而使晶粒尺寸变小。
这可以通过增加冷却速度来实现,例如使用冷却剂或冷却介质。
另外,还可以通过减小铸件的尺寸来增加冷却速度,例如使用薄壁结构或小尺寸的模具。
快速冷却还可以提高金属的强度和硬度。
第三种方法是通过机械加工来细化晶粒。
在铸造后,通过进行热处理或热机械加工,可以使晶粒重新结晶,从而得到更为细小的晶粒。
常用的方法有热轧、热拉伸、热挤压等。
这些方法利用了金属在高温下的塑性变形性质,使晶粒重新排列和长大,从而实现晶粒细化。
第四种方法是通过添加细化剂来细化晶粒。
细化剂是一种可以在金属熔体中形成核心的物质,它可以促使晶粒在凝固时形成更多的细小晶核,从而细化晶粒。
常用的细化剂有铝钛合金、钙硅合金等。
这些细化剂可以通过溶解在金属熔体中,形成一种细小的颗粒或化合物,从而提供更多的晶核,使晶粒细化。
第五种方法是通过电磁场作用来细化晶粒。
在铸造过程中,可以利用电磁场的作用来影响金属的凝固行为,从而实现晶粒细化。
例如,通过施加交变电磁场,可以改变金属熔体中的流动模式,促使晶核形成更多的细小晶粒。
此外,还可以利用电磁搅拌技术来改善金属的凝固结构,实现晶粒细化。
通过以上几种方法和技术,可以有效地细化铸造时的晶粒。
这些方法在实际应用中具有一定的局限性和适用范围,需要根据具体的材料和工艺条件进行选择和优化。
细晶铸造工艺研究

细晶铸造工艺研究柳松青【摘要】用热学方法通过实验来研究细晶铸造工艺过程,其中浇注温度和过热温度等关键工艺参数都是经过实验比较确定的,这对实际生产有一定参考作用.实验所得到的细小晶粒结构的试样,其具有优良的低周疲劳性能,并且破断性能没有受到损失.【期刊名称】《铸造设备与工艺》【年(卷),期】2012(000)004【总页数】2页(P33-34)【关键词】细晶工艺;浇注温度【作者】柳松青【作者单位】哈尔滨工业大学,黑龙江哈尔滨150001【正文语种】中文【中图分类】TG24一般来说有3种控制晶粒基本方法:机械方法,化学方法和热学方法。
机械方法,就是当液态金属凝固时进行连续搅拌。
通过搅拌把在凝固时开始形成的枝晶打碎,这样可产生更多的结晶核心,并抑制晶粒长大。
但是,由于凝固受到限制,在晶粒之间产生许多微孔,需要通过热等静压才能使微孔密实。
化学方法包括使用孕育剂,这种孕育剂是一种比合金本身熔点低的化合物,能产生局部不均匀和择优形核位置。
虽然使用这种技术可以得到细晶粒,可是孕育剂能带进一些氧化物成为非金属夹杂物,使形核位置变成疲劳裂纹源。
热学方法是一种较好的方法,在常规铸造工艺中最容易实现。
通过保持低的浇注温度,合金能迅速凝固,因此可控制晶粒长大。
下面用热学方法通过实验来研究细晶铸造工艺过程。
由于熔模铸造能减少加工切削余量降低成本,提高尺寸精度和表面粗糙度以及材料的机械性能,从而达到升级产品档次的目的,并且实验室有熔模铸造所需要压蜡机、制壳机、脱蜡机和感应炉等设备,所以,本次实验采用熔模铸造的方法。
1 铸模系统铸模材料通常被预热到1000℃左右高温,能使耐火材料完全脱气。
然而熔融合金一般是在大约1500℃左右温度下注入模中,额外的热量能产生瞬间排气而带进模中,这样就会产生未填充区。
因此,在这种温度下,铸模材料的渗透性是很重要的。
如果使用一种渗透性好的模壳壁,就能迅速排出气体,使熔融金属充满空腔。
一般熔模铸造工艺使用蜡模和胶状二氧化硅/锆石粉作为表面涂层。
细晶铸造

国外近二十年来集中力量发展了高温合金定向铸造和单晶铸造技术,主要是为了提高航空发动机高压涡轮叶片的高温工作能力,从而增大发动机的推力,并延长其工作寿命。
与此同时,航空发动机的恶劣工况对在中低温条件下工作的低压涡轮叶片、整体叶盘和涡轮机匣等高温合金铸件的低周疲劳寿命提出了更高要求。
但是这类铸件在普通熔模精铸工艺生产条件下,一般为粗大的树枝晶或柱状晶,晶粒平均尺寸大于4mm,较典型的为4~9mm。
由于晶粒粗大及组织、性能上的各向异性,很容易导致铸件在使用过程中疲劳裂纹的产生和发展,这对于铸件的疲劳性能尤其是低周疲劳性能极为不利,并且造成铸件力学性能数据过于分散,降低了设计容限。
随着对发动机的整体寿命和性能要求的进一步提高,改善铸件的中低温疲劳性能及其他力学性能显得十分重要。
这便导致了细晶铸造技术的产生和发展。
工业发达国家,尤其是美国和德国,早在20世纪70年代末就开展了高温合金细晶铸造技术的研究和应用,在20世纪80年代中后期该项技术发展趋于成熟,目前正在航空、航天工业领域中扩大其应用范围,如美国Howmet公司利用细晶铸造技术成功地制造了Mod5A、Mar-M247、IN713C、1N718等高温合金整体涡轮,使涡轮的低周疲劳寿命提高了2~3倍。
德国、法国在新型号航空发动机上也采用了细晶整体涡轮铸件。
国内对高温合金细晶铸造技术的研究从20世纪80年代末开始起步,经过“八五”和“九五”期间的研究和应用,我国航空制造业建立了专门的细晶铸造设备,对高温合金细晶铸造工艺进行了较系统的试验,研制了一批镍基高温合金细晶铸件,并已应用于航空发动机中,在细晶铸造研究领域内取得了重要的进展。
1 细晶铸造的特点和工艺方法1.1 细晶铸造的特点细晶铸造技术或工艺(FGCP)的原理是通过控制普通熔模铸造工艺,强化合金的形核机制,在铸造过程中使合金形成大量结晶核心,并阻止晶粒长大,从而获得平均晶粒尺寸小于1.6mm的均匀、细小、各向同性的等轴晶铸件,较典型的细晶铸件晶粒度为美国标准ASTM0~2级。
一种细晶铸造K465合金低压涡轮叶片组织和力学性能

2021年第1期/第70卷试验研究F O U N D R V53一种细晶铸造K465合金低压涡轮叶片组织和力学性能尹湘蓉,黄中荣,龙阅文,佘玉良,龚晓宁,郭志飞(中国航发航空科技股份有限公司,四川成都610503)摘要:为提高叶片铸件质量和生产效率,对某型机K465合金低压涡轮叶片开展细晶铸造工艺研究,对细晶铸造的精铸低压涡轮叶片的显微疏松、组织进行观察,力学性能及极限疲劳性能进行测试,并与原工艺的叶片对比,验证晶粒细化对涡轮叶片晶粒度和疲劳强度的影响。
结果表明,细晶铸造工艺能使叶片铸件低倍晶粒度、枝晶间距细化,叶片的显微疏松、显微组织与原工艺相比没有变化,但室温拉伸强度略有提高,极限疲劳强度更优。
关键词:K465合金;低压涡轮叶片;细晶铸造;晶粒度;力学性能作者简介:尹湘蓉(1968-),女,研 究员,硕士,主要研究方向为金属材料及热加工工艺。
E-mail: 1106531505@ 中图分类号:TG290.8文献标识码: A文章编号:1001-4977(2021) 01-0053-05收稿曰期:2020-07-15收到初稿,2020-09-20收到修订稿。
细晶铸造工艺是将化学孕育剂(C o A1:04、C o O A120,等)与粘结剂按一定比例配置,混合均匀后涂制铸造工艺型壳内表面。
叶片铸造合金浇注时,合金中的活性元素如A l、T i等,与型壳内表面孕育剂发生置换反应,形成大量异质晶核,使叶片铸件得到由表及里的细晶晶粒,这是一种很有效且简易、实用的晶粒细化工艺方法,被广泛采用。
与普通铸件相比,细晶铸造组织表现为细小的晶粒度、高度弥散分布的细小碳化物质点、细小而均匀的7’相分布。
细晶铸造零件在中低温工作条件下具有明显的性能优势,有利于提高零件的疲劳强度,显著减少铸件力学性能数据的分散度,从而提高铸造零件的设计容限,在航空发动机等轴晶叶片研制和生产中也得到了一定范围的研究和应用,如国外ln718压气机叶片、国内K4I7G、K403、K418、K418B低压涡轮工作叶片、K492M整体叶轮等。
高温合金细晶铸造新技术

高温合金细晶铸造新技术
赵京晨;燕平;彭艳锋;孟祥炜;肖文丰;李曙光;张龙飞;陈兴福
【期刊名称】《航天制造技术》
【年(卷),期】2013(000)006
【摘要】常规的铸造组织存在细等轴晶、柱状晶和粗等轴晶三种晶区。
采用新方
法铸造出来的高温合金铸造组织是分布于整个铸造截面区域内的均匀细等轴晶组织,它不仅晶粒度可以细小得达到锻造晶粒度,且没有织构或流线。
与传统的高温合金细晶铸造相比,因为它注入型腔的不是传统细晶铸造的粥状液体--固、液混合体,而是在工业上首次应用的过冷至熔点以下的单相金属液体,因此具有超强的充型能力。
【总页数】5页(P1-5)
【作者】赵京晨;燕平;彭艳锋;孟祥炜;肖文丰;李曙光;张龙飞;陈兴福
【作者单位】钢铁研究总院,北京 100081;钢铁研究总院,北京 100081;首都航
天机械公司,北京100076;首都航天机械公司,北京100076;首都航天机械公司,北京 100076;首都航天机械公司,北京 100076;钢铁研究总院,北京 100081;钢
铁研究总院,北京 100081
【正文语种】中文
【相关文献】
1.关于"铸造高温合金显微疏松评定方法"和"铸造高温合金晶粒度评定方法"两项航标的说明 [J], 李爱兰;余乾;王晔
2.高温合金细晶铸造技术研究 [J], 汤鑫
3.高温合金细晶铸造技术的发展和应用 [J], 刘发信
4.高温合金细晶铸造工艺及其应用 [J], 袁文明;汤鑫
5.K418高温合金细晶叶片铸造工艺的研究 [J], 汤鑫;刘发信;袁文明;杨爱德
因版权原因,仅展示原文概要,查看原文内容请购买。
高温合金细晶铸造新技术
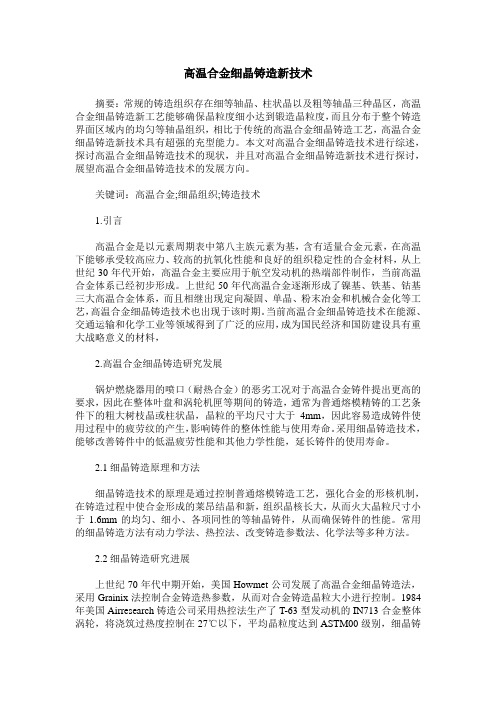
高温合金细晶铸造新技术摘要:常规的铸造组织存在细等轴晶、柱状晶以及粗等轴晶三种晶区,高温合金细晶铸造新工艺能够确保晶粒度细小达到锻造晶粒度,而且分布于整个铸造界面区域内的均匀等轴晶组织,相比于传统的高温合金细晶铸造工艺,高温合金细晶铸造新技术具有超强的充型能力。
本文对高温合金细晶铸造技术进行综述,探讨高温合金细晶铸造技术的现状,并且对高温合金细晶铸造新技术进行探讨,展望高温合金细晶铸造技术的发展方向。
关键词:高温合金;细晶组织;铸造技术1.引言高温合金是以元素周期表中第八主族元素为基,含有适量合金元素,在高温下能够承受较高应力、较高的抗氧化性能和良好的组织稳定性的合金材料,从上世纪30年代开始,高温合金主要应用于航空发动机的热端部件制作,当前高温合金体系已经初步形成。
上世纪50年代高温合金逐渐形成了镍基、铁基、钴基三大高温合金体系,而且相继出现定向凝固、单晶、粉末冶金和机械合金化等工艺,高温合金细晶铸造技术也出现于该时期。
当前高温合金细晶铸造技术在能源、交通运输和化学工业等领域得到了广泛的应用,成为国民经济和国防建设具有重大战略意义的材料,2.高温合金细晶铸造研究发展锅炉燃烧器用的喷口(耐热合金)的恶劣工况对于高温合金铸件提出更高的要求,因此在整体叶盘和涡轮机匣等期间的铸造,通常为普通熔模精铸的工艺条件下的粗大树枝晶或柱状晶,晶粒的平均尺寸大于4mm,因此容易造成铸件使用过程中的疲劳纹的产生,影响铸件的整体性能与使用寿命。
采用细晶铸造技术,能够改善铸件中的低温疲劳性能和其他力学性能,延长铸件的使用寿命。
2.1细晶铸造原理和方法细晶铸造技术的原理是通过控制普通熔模铸造工艺,强化合金的形核机制,在铸造过程中使合金形成的莱昂结晶和新,组织晶核长大,从而火大晶粒尺寸小于1.6mm的均匀、细小、各项同性的等轴晶铸件,从而确保铸件的性能。
常用的细晶铸造方法有动力学法、热控法、改变铸造参数法、化学法等多种方法。
铸造工艺详细分类

铸造工艺详细分类铸造作为一项悠久的金属加工工艺,已经有大约六千年的历史了,而我国更是从公元前一千七百年开始进入青铜器铸造的鼎盛期,且已具有较高水平。
所谓铸造,即是将液体金属浇铸到与零件形状相适应的铸造空腔中,待其冷却凝固后,以获得零件或毛坯的方法。
被铸物质多为原为固态但加热至液态的金属(例:铜、铁、铝、锡、铅等),而铸模的材料可以是砂、金属甚至陶瓷。
因应不同要求,使用的方法也会有所不同。
铸件订单网为您详细介绍一下铸造工艺的几大类别:一、重力铸造重力铸造是指金属液在地球重力作用下注入铸型的工艺,也称浇铸。
广义的重力铸造包括砂型浇铸、金属型浇铸、熔模铸造,泥模铸造等;窄义的重力铸造专指金属型浇铸。
二、压力铸造压力铸造是指金属液在其他外力(不含重力)的作用下注入铸型的工艺。
广义的压力铸造包括压铸机的压力铸造和真空铸造、低压铸造、离心铸造等;窄义的压力铸造专指压铸机的金属型压力铸造,简称压铸。
这几种铸造工艺是目前有色金属铸造中最常用的、也是相对价格最低的。
三、砂型铸造砂型铸造是一种以砂作为主要造型材料,制作铸型的传统铸造工艺。
砂型一般采用重力铸造,有特殊要求时也可采用低压铸造、离心铸造等工艺。
砂型铸造的适应性很广,小件、大件,简单件、复杂件,单件、大批量都可采用。
砂型铸造用的模具,以前多用木材制作,通称木模。
木模缺点是易变形、易损坏;除单件生产的砂型铸件外,可以使用尺寸精度较高,并且使用寿命较长的铝合金模具或树脂模具。
虽然价格有所提高,但仍比金属型铸造用的模具便宜得多,在小批量及大件生产中,价格优势尤为突出。
此外,砂型比金属型耐火度更高,因而如铜合金和黑色金属等熔点较高的材料也多采用这种工艺。
但是,砂型铸造也有一些不足之处:因为每个砂质铸型只能浇注一次,获得铸件后铸型即损坏,必须重新造型,所以砂型铸造的生产效率较低;又因为砂的整体性质软而多孔,所以砂型铸造的铸件尺寸精度较低,表面也较粗糙。
四、特种铸造金属型铸造是用耐热合金钢制作铸造用中空铸型模具的现代工艺。
细晶强化的概念

细晶强化的概念
细晶强化是一种新型的铸态加工技术,它能够改善金属材料的力学性能。
它的原理是,在材料中改变细微的晶粒,使得晶粒结构更紧密,形成细小的晶粒内强化结构,从而提高材
料的强度。
细晶强化的技术已经被广泛应用于航空航天、汽车、机械制造等行业中。
在航空航天领域,已经成功制备出一种超级强力钢,用于制造飞机发动机叶片等大型结构零件。
在汽车行业,细晶强化技术可以制备出耐用的材料,可以比传统铸造技术制备出更强韧的零件,而且可以降低整车重量,用于整车空气动力学等改进。
另外,细晶强化技术在机械制造领域也有着重要的应用,可以制备出更加精密的零件,且
能够抵抗强大的磨擦、弯曲及冲击载荷,使产品更加精致耐用。
此外,这种技术还可以更
有效地利用资源,减少产品制造所需物料及人工成本。
总而言之,细晶强化技术是一项重要的工业技术,能够改善金属材料的力学性能,并在航空航天、汽车等行业中得到了广泛的应用,降低了部件的成本,提高了产品的性能。
它的
用途非常广泛,不仅能够改善材料的强度,更能够更有效地利用资源。
- 1、下载文档前请自行甄别文档内容的完整性,平台不提供额外的编辑、内容补充、找答案等附加服务。
- 2、"仅部分预览"的文档,不可在线预览部分如存在完整性等问题,可反馈申请退款(可完整预览的文档不适用该条件!)。
- 3、如文档侵犯您的权益,请联系客服反馈,我们会尽快为您处理(人工客服工作时间:9:00-18:30)。
新技术新工艺--细晶铸造
细晶铸造
国外近二十年来集中力量发展了高温合金定向铸造和单晶铸造技术,主要是为了提高航空发动机高压涡轮叶片的高温工作能力,从而增大发动机的推力,并延长其工作寿命。
与此同时,航空发动机的恶劣工况对在中低温条件下工作的低压涡轮叶片、整体叶盘和涡轮机匣等高温合金铸件的低周疲劳寿命提出了更高要求。
但是这类铸件在普通熔模精铸工艺生产条件下,一般为粗大的树枝晶或柱状晶,晶粒平均尺寸大于4mm,较典型的为4~9mm。
由于晶粒粗大及组织、性能上的各向异性,很容易导致铸件在使用过程中疲劳裂纹的产生和发展,这对于铸件的疲劳性能尤其是低周疲劳性能极为不利,并且造成铸件力学性能数据过于分散,降低了设计容限。
随着对发动机的整体寿命和性能要求的进一步提高,改善铸件的中低温疲劳性能及其他力学性能显得十分重要。
这便导致了细晶铸造技术的产生和发展。
工业发达国家,尤其是美国和德国,早在20世纪70年代末就开展了高温合金细晶铸造技术的研究和应用,在20世纪80年代中后期该项技术发展趋于成熟,目前正在航空、航天工业领域中扩大其应用范围,如美国Howmet公司利用细晶铸造技术成功地制造了Mod5A、Mar-M247、IN713C、1N718等高温合金整体涡轮,使涡轮的低周疲劳寿命提高了2~3倍。
德国、法国在新型号航空发动机上也采用了细晶整体涡轮铸件。
国内对高温合金细晶铸造技术的研究从20世纪80年代末开始起步,经过“八五”和“九五”期间的研究和应用,我国航空制造业建立了专门的细晶铸造设备,对高温合金细晶铸造工艺进行了较系统的试验,研制了一批镍基高温合金细晶铸件,并已应用于航空发动机中,在细晶铸造研究领域内取得了重要的进展。
1 细晶铸造的特点和工艺方法
1.1 细晶铸造的特点
细晶铸造技术或工艺(FGCP)的原理是通过控制普通熔模铸造工艺,强化合金的形核机制,在铸造过程中使合金形成大量结晶核心,并阻止晶粒长大,从而获得平均晶粒尺寸小于1.6mm的均匀、细小、各向同性的等轴晶铸件,较典型的细晶铸件晶粒度为美国标准ASTM0~2级。
细晶铸造在使铸件晶粒细化的同时,还使高温合金中的初生碳化物和强化相γ'尺寸减小,形态改善。
因此,细晶铸造的突出优点是大幅度地提高铸件在中低温(≤760℃)条件下的低周疲劳寿命,并显著减小铸件力学性能数据的分散度,从而提高铸造零件的设计容限。
同时该技术还在一定程度上改善铸件抗拉性能和持久性能,并使铸件具有良好的热处理性能。
细晶铸造技术还可改善高温合金铸件的机加工性能,减小螺孔和刀刃形锐利边缘等处产生加工裂纹的潜在危险。
因此该技术可使熔模铸件的应用范围扩大到原先使用锻件、厚板机加工零件和锻铸组合件等领域。
在航空发动机零件的精铸生产中,使用细晶铸件代替某些锻件或用细晶铸造的锭料来做锻坯已很常见。
1.2 细晶铸造的工艺方法
细晶铸造晶核的增殖来源于合金液中已存在的或外加的固体形核基底成形核心作用,因此,细化晶粒的关键是增加合金液中的形核基底的数量。
目前增加形核基底的数量的基本方法大致可分为三大类:热控法或改变铸造参数法(VCP法)、动力学法(或机械法)和化学法。
这也是细晶铸造的三类基本工艺方法,如表1所示。
表1 细晶铸造的工艺方法
以达到限制晶粒长大和细化晶粒的
目的一般方法:旋转铸型法、机械振动法、超声波振动法、电磁搅动法等;(2)Grainex法、Mould-Agitation法;(3)
Microcast-X法
工艺参数
铸型温度(t型)、浇注温度)t浇)及精
炼温度(t精)等浇注温度(t铸)和铸型旋转振动参数(速
度、频率)以及铸型冷却速率等
精炼温度(t精)、形核剂加入量
及其加入制度等
晶粒细化典型
尺寸范围
1.60~0.18mm 0.36~0.07mm 1.25~0.12mm
优缺点工艺简单,但铸件容易欠铸、晶粒
度不均匀
晶粒度均匀、合金纯净度高、成形能
力好,但需要建立专用的细晶铸造设
备
工艺简单,但容易引进杂质、
改变合金成分
适用范围形状简单的小尺寸铸件回转体和厚大截面铸件形状简单的小尺寸铸件近年来美国Howmet公司研制和发展的Grainex(简称GX法)和Microcast-X(简称MX法)细晶工艺代表着国际先进水平的细晶铸造工艺方法,目前已投入生产应用。
图1为GX、MX法的晶粒细化典型尺寸范围。
图1 MX、GX法的晶粒细化尺寸范围
其中GX法以动力学法为基础,是高温合金细晶铸造第一代动力学法工艺,它采用较高的过热温度,在合金凝固过程中打碎已凝固的枝晶骨架成为结晶核心,从而细化铸件晶粒。
与热控法相比,GX法浇注过热度较大,因而使铸件薄壁部分容易成形,所获得
的铸件纯净度高,晶粒度细小而均匀,通常能达到ASTM0~2级。
但晶粒形态仍保留着轻微的树枝状,其缺点是不能全面改善铸件的晶粒形态,仅使厚截面部位晶粒细化。
这种方法适用于铸造叶盘和其他一些回转体铸件以及截面厚大的细晶铸件。
MX法是Howmet公司开发的第二代动力学法细晶铸造工艺,其特点是将机械扰动与快速凝固相结合以获得晶粒更加细小的晶胞组织,用此法铸造的铸件晶粒度能达ASTM3~5级或更细,可与变形高温合金零件的晶粒度相媲美,因而能以比GX法更大的幅度提高铸件的力学性能。
直到目前为止,该工艺仍属不公开的专利。
但从有关资料分析,其工艺要点主要包括:①合金精炼后静止降温,使浇注过热度保持在20℃以内。
②浇注时对合金液进行机械或电磁感应扰动,使合金液成细小的液滴流注入预热铸型的型腔。
③在铸型内扰动合金液并提高铸型对合金液的冷却强度,使铸件在整个截面上都能生成均匀、细小、非枝晶的晶胞组织。
MX法现主要用于生产镍基高温合金的熔模铸件、铸锭和可锻坯件。
在20世纪90年代中期国内研究和开发了属于动力学法范畴的细晶铸造工艺——铸型搅动法(Mould-Agitation法),简称MA法,并建立了ZGX-25型细晶铸造真空感应炉。
利用该设备可铸造出外形尺寸达300mm、重量达50kg的细晶铸件。
在该设备上不但能用化学法和热控法铸造细晶叶片、细晶整体结构件,而且还可用铸型搅动法生产出纯净度较高的细晶整体叶盘、涡轮等回转体铸件。
其工艺原理与GX法相近,如图2所示。
图2 MA法工艺原理示意图
ZGX-25型细晶铸造炉具有预热铸型的加热器,并有能使铸型单向/双向旋转功能的机构。
铸型搅动法(MA法)细化铸件晶粒基于在凝固过程中对枝晶破碎、增殖形核质点的原理。
具体工艺步骤为:将模壳装卡在专用的铸型系统中,并预热至规定的型壳温度。
在对合金熔液精炼干净后,调整好浇注温度,然后浇入型壳中,静止一段时间后,铸型双向搅动,直到凝固完毕。
在金属液凝固过程中,通过铸型搅动使铸型壁上最初形成的枝晶被破碎,破碎的枝
晶分布于整个合金液中,因而创造了有效的形核核心,导致铸件产生细小、均匀和等轴的晶粒。
此外,铸型中心到铸型壁的热梯度得到降低,因此不管铸件截面厚度如何变化,都能获得较均匀的等轴晶。
铸型搅动法主要控制的搅动参数为:浇注后合金液在铸型内的静止时间τ静;正转/反转的时间τ正反;正转反转之间换向时间τ换;正转/反转的转速v正反;双向转动的总时间为τ总。
实验中通过变化合金的浇注过热温度Δt浇及搅动参数来得到不同的晶粒度。
铸型搅动工艺的优点在于采用比热控法细晶工艺高得多的浇注温度,因而铸件纯净度高,薄壁部位容易成形。
相比之下,传统的热控法细晶铸造工艺和硼化物沉淀工艺主要依赖于很低的浇注温度,因而导致了非金属夹杂物的诱入。
2 细晶铸造举例
采用铸型搅动法细晶铸造生产了某航空发动机上在中温条件(470~750℃)下使用的整体涡轮。
该整体涡轮直径为147mm,铸件毛重10.5kg,用K418B镍基高温合金铸造,其主要化学成分见表2。
熔模型壳用硅酸乙酯-刚玉砂制壳工艺制成。
合金的熔炼和浇注在自制的ZGX-25型细晶铸造真空感应炉内进行。
铸型在炉内可双向旋转,对注入型腔内的合金液体施加双向搅动作用。
细晶铸造的工艺参数见表3。
表2 K418B合金主要化学成分(质量分数,%)
表3 K418B合金整体涡轮的细晶铸造工艺参数
细晶涡轮经过热等静压(HIP)和热处理。
热等静压工艺为:1200℃/150MPa/4h;热处理工艺为:1180℃,2h,空冷+930℃,16h,空冷。
在热处理后涡轮的轮毂部位沿轴向切取性能试棒,测定室温和高温抗拉性能、高温持久性能和低周疲劳性能。
低周疲劳试验在美国MTS-809电液伺服闭环回路疲劳试验机上进行。
为了便于比较,从K418B合金普通铸造涡轮上切取试棒,其处理工艺、测试条件与细晶涡轮相同。
1.细晶铸造对铸件晶粒度形态及显微组织的改善在上述细晶铸造工艺条件下,所获得的K418B合金细晶涡轮各部位晶粒度列于表4。
它与普通铸造条件下的涡轮晶粒度对比示于图3。