钣金质量控制表
钣金现场质量控制

钣金现场质量控制钣金是一种重要的制造工艺,涉及到许多行业,如汽车制造、航空航天、建筑等。
在钣金加工过程中,质量控制是至关重要的,因为质量问题可能导致产品的不合格和生产成本的增加。
因此,在钣金现场必须进行严格的质量控制,以确保最终产品的质量符合要求。
一、材料质量控制钣金加工的第一步是选择合适的材料。
材料的质量直接影响到最终产品的质量。
在钣金现场,应对材料进行质量检查,包括外观检查、尺寸测量等。
只有当材料符合要求时,才可以继续进行后续的加工工序。
二、加工工序控制在钣金加工过程中,有许多加工工序需要进行控制,以确保产品的质量。
这些工序包括剪切、冲孔、折弯等。
在每个工序中,应对设备进行定期检查和维护,以确保其正常运行。
此外,在每个工序结束后,需要对工件进行检查,以确保其尺寸和形状与设计要求相符。
三、焊接质量控制在钣金加工过程中,焊接是一个重要的环节。
焊接的质量直接关系到产品的强度和密封性。
在焊接过程中,应确保焊接设备的质量和焊接操作的正确性。
焊接接头应符合设计要求,并对焊接接头进行无损检测,以确保其质量。
四、表面处理质量控制钣金制品的表面处理对于产品的外观质量至关重要。
在表面处理过程中,应选用合适的处理方法,如喷涂、阳极氧化、电镀等。
在每个处理步骤中,应确保操作正确,并对处理后的产品进行检查,以确保表面处理质量符合要求。
五、产品检测和测试在钣金现场,应对最终产品进行全面的检测和测试。
这些测试包括尺寸测量、力学性能测试、密封性测试等。
只有当产品通过所。
钣金加工质量控制
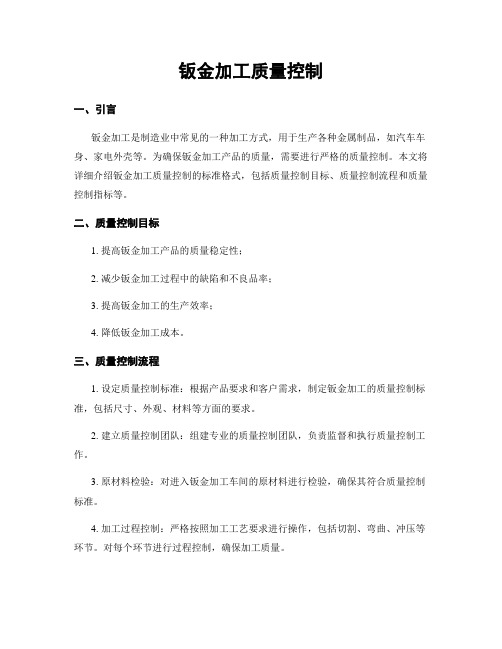
钣金加工质量控制一、引言钣金加工是制造业中常见的一种加工方式,用于生产各种金属制品,如汽车车身、家电外壳等。
为确保钣金加工产品的质量,需要进行严格的质量控制。
本文将详细介绍钣金加工质量控制的标准格式,包括质量控制目标、质量控制流程和质量控制指标等。
二、质量控制目标1. 提高钣金加工产品的质量稳定性;2. 减少钣金加工过程中的缺陷和不良品率;3. 提高钣金加工的生产效率;4. 降低钣金加工成本。
三、质量控制流程1. 设定质量控制标准:根据产品要求和客户需求,制定钣金加工的质量控制标准,包括尺寸、外观、材料等方面的要求。
2. 建立质量控制团队:组建专业的质量控制团队,负责监督和执行质量控制工作。
3. 原材料检验:对进入钣金加工车间的原材料进行检验,确保其符合质量控制标准。
4. 加工过程控制:严格按照加工工艺要求进行操作,包括切割、弯曲、冲压等环节。
对每个环节进行过程控制,确保加工质量。
5. 首件检验:在钣金加工过程中,进行首件检验,以验证加工工艺的可行性和质量控制的有效性。
6. 在线检验:在加工过程中设置在线检验点,对加工中的关键环节进行抽检,及时发现并纠正问题。
7. 终检:对钣金加工产品进行终检,确保产品的质量符合质量控制标准。
8. 不良品处理:对于不合格品,及时进行处理,包括返工、报废等措施。
9. 数据分析和改进:对质量控制过程中的数据进行分析,找出问题的根本原因,并采取相应的改进措施,以提高质量控制水平。
四、质量控制指标1. 尺寸精度:根据产品要求,对钣金加工产品的尺寸进行测量,确保其精度符合质量控制标准。
2. 表面质量:对钣金加工产品的表面进行检查,确保无划痕、凹陷等表面缺陷。
3. 材料质量:对钣金加工所使用的材料进行检验,确保材料的质量符合质量控制标准。
4. 强度和硬度:对钣金加工产品的强度和硬度进行测试,确保其符合产品要求。
5. 不良品率:统计钣金加工过程中的不良品数量,计算不良品率,以评估质量控制的效果。
钣金加工质量控制

钣金加工质量控制钣金加工质量控制是确保钣金制品在生产过程中达到一定标准的一系列措施。
本文将详细介绍钣金加工质量控制的标准格式文本,包括质量控制的目的、流程、要求以及相关数据。
一、质量控制的目的钣金加工质量控制的目的是确保钣金制品的质量符合设计要求和客户需求,提高产品的可靠性和稳定性,降低生产成本,提高企业的竞争力。
二、质量控制流程1. 原材料检验在钣金加工过程中,首先需要对原材料进行检验。
原材料的质量直接影响到最终产品的质量。
检验包括外观检查、尺寸测量、材料成份分析等。
2. 设计和工艺控制在钣金加工过程中,设计和工艺是关键环节。
设计要符合产品的功能和外观要求,工艺要合理,能够保证产品的精度和质量。
通过严格的设计和工艺控制,可以避免加工过程中浮现质量问题。
3. 加工过程控制钣金加工过程中,需要对加工设备进行定期检查和维护,确保设备正常运行。
同时,对加工过程进行监控,及时发现并纠正加工中的问题,避免不良品的产生。
4. 检验和测试在钣金加工完成后,需要对成品进行检验和测试。
检验包括外观检查、尺寸测量、性能测试等。
通过检验和测试,可以确保产品的质量符合标准要求。
5. 不良品处理如果在钣金加工过程中发现不良品,需要及时处理。
不良品可以进行修复,如果无法修复,则需要进行报废处理。
同时,需要分析不良品的原因,并采取措施避免类似问题再次发生。
三、质量控制要求1. 严格遵守相关标准和规范钣金加工质量控制要求严格遵守相关的国家标准和行业规范,确保产品的质量符合法律法规的要求。
2. 建立完善的质量管理体系企业需要建立完善的质量管理体系,包括质量目标、质量责任、质量检查和测试等方面的制度和流程,确保质量控制的有效实施。
3. 加强员工培训和技能提升员工是质量控制的关键环节,企业需要加强员工的培训和技能提升,提高员工的质量意识和技术水平,确保质量控制的有效执行。
4. 使用可靠的检测设备和工具钣金加工过程中需要使用可靠的检测设备和工具,确保检测结果的准确性和可靠性。
钣金制品的质量控制

( )加 丁 3
在 下料 完 成后 ,零 部 件 成 形 主 要 使
用 的是折弯 机 、压力机设 备 。 ( 4)焊 接 焊 接 就 是 将 多 个零 件 组 焊 在 一 起 , 达到加 工 的 目的或 单个 零件 边 缝 焊 接 ,以增 加 其 强 度 ,其 加工方 法 一 般 有 以下 几 种 :C , 体 保 护焊 、 O气 氩弧 焊 、点 焊及 机器 人 焊 接 等 。这 些 焊 接 厅 式 的 选 J 是 根据 实 际要 求 和 材 质 而 定 。我 厂工 具 柜 采 用 的 } = H 焊接 方式是 C , O 气体保 护焊 。 ( )组装 5 依 据工 具 柜 装 配 冈样 ,将 加 工 成 彤
柜零 部件 展 开 冈 的外 形 长 宽 尺 寸 。再转 压力 机 结 合
模具 冲 门扣 手 孑 、切 角成 形 。压 力 机 下 料 是 利 用 分 L
一
程 中 ,往往 因为 焊 接工 艺 不 当 ,板 材 购 进 后 及 半成 品搬 运过 程 中人 为踩 踏 、敲 击 、碰撞 及 存 放等 原 I . 大 1 致使 薄板 材 局部 受 力 、受 高 温 或 长期 露 灭不 平 整 的 存放 ,特别 容 易 产 生 变形 ,变形 的形 式 有 溥 板件 巾
入 了解 。发现 杯 突 深 度 的 试 验 与某 些 材 料 的 顶 破试
缝 的 自动判 断 。
3 .结语
验 方法 有很 多 相 似 之 处 。在 顶 破 试 验 中 , 当试 样 出 现局部 破 坏 时 ,试 验 力 值 会 出现 明 显 的 衰 减 。另 外
分析 杯突试 验 的方 法 与 目的 ,知 道杯 突试 验 是 用 来 检测 金属 板 材 各 向塑 性 变 形 能力 的 ,而金 属 板 材 拉
钣金常用标准

标准编号 GB708-2006 GB709-88 Q/BQB420-2003 GB13237-91 GB3280-92 GB/T17102-1997 GB/T3880-1997 GB/T246-1997 GB/T244-1997 GB13239 GB4156-84 GB/T3098 (1-20) GB/T9798-1997 GB/T9799-1997 (2)制程阶段 公司在制程阶段所遵循的质量控制标准如下表所示: 标准编号 GB/T1804-2000 GB/T1800.4-1999 GB/T1801-1997 GB/T131-93 GB/4457.5-1984 GB324-88 JB/T5067-1999 GB/T1732-1993 GB/T1733-1993 GB/T1740-1979 GB/T1771-1991 GB/T6739-1996 GB/T9761-1988 GB-T9753-1988 GB-T6742-86 GB-T1743-1979 GB-T1763-1979 (3)成品阶段 公司在成品阶段所遵循的质量控制标ห้องสมุดไป่ตู้如下表所示: 标准编号 GB/T2828-1-2003 GB2829-87 标准名称 计数抽样检验程序 周期检查计数抽样程序及抽样表 标准名称 一般公差未注公差的线性和角度尺寸的公差 极限与配合之标准公差等级和孔、轴的极限偏差表 极限与配合公差带和配合的选择 机械制图表面粗糙度符号、代号及其方法 机械制图、剖面符号 焊接符号表示方法 电镀标准 漆膜耐冲击测定法 漆膜耐水性测定法 漆膜耐湿热测定法 色漆和清漆耐中性盐雾性能的测定 涂膜硬度铅笔测定法 色漆的目视比色 色漆和清漆之杯突试验 漆膜弯曲试验 漆膜光泽测定法 漆膜耐化学试剂性测定法 标准名称 冷轧钢板和钢带的尺寸、外形、重量的允许偏差 热轧钢板和钢带的尺寸、外形、重量的允许偏差 连续热镀锌/锌铁合金钢板及钢带 优质碳素结构钢冷轧薄钢板和钢带 不锈钢冷轧钢板 不锈复合钢冷轧薄钢板和钢带 铝及铝合金轧制板材 金属管压扁试验方法 金属管弯曲试验方法 金属材料低温拉伸试验方法 金属杯突试验方法 紧固件机械性能 金属覆盖层之镍电沉积层 金属覆盖层之钢铁上的锌电镀层
汽车钣金操作考核评分表

12
六、其他
项
目
整形结束打磨出裸金属边缘理凹陷区域大于80mm,修复部位不能低于正常区域1mm更不能高于正常区域,钢板强度符合规定要求,钢板出现孔洞,防护用品错戴、漏戴,工具掉落
修复区域未达到要求,钣金件出现孔洞,每项扣6分
防护用品错戴、漏戴,工具掉落,每项扣2分
17
维修时间共计25分钟,超出时间所做项目不计分,出现安全事故不计成绩
检查修复效果:用钢板尺或手触摸进行检测(修复效果不好可重新修整),选用打磨机、砂纸片对缩火位置进行打磨,
打磨处理操作不标准不规范,扣1分
1
五、整 理工位符合7S作业
拆除搭铁线打磨打铁出焊接痕迹清洁除尘,拆除缩火碳棒,关闭修复焊机电源,气源及总电源
操作顺序不准确、漏项,每漏一项扣2分
8
工具的清洁、回位,工位清洁、整理,脱下防护用品,符合6S要求
未清洁除尘、不进行检侧或检测不规范,
扣2-4分
4
四、钣金件进行缩火处理(不需要可不做此项)
检查修复过的钣金件是否进行缩火处理并确定缩火处理区域
操作顺序不正确、漏项、工具掉落工具
随地乱扔,每项扣1分
2
不作
此项
总分
值加
入总
成绩
安装碳棒、调整档位、查找缩火点、进行缩火处理
缩火操作不标准不规范,扣1-2分
2
未能正确选择,每项2分
6
搭铁线固定、焊接点的质量、惯性锤的正确使用
操作不标准不规范,扣2-4分
6
损伤区域的正确修复、用钢板尺或手触摸进行检查
修复操作不规范、没进行检测,扣4-6分
钣金(五金)产品质量的控制
6.5.1尺寸:
用螺纹规检测螺孔。
6.5.2外观:
A.依照客户要求。
B.检查内容:漏攻牙、滑牙、攻错孔、攻偏(攻偏是否影响外观面)、漏工序等。
6.6铆轴检测内容
6.6.1尺寸:
依照图面标准/治具/客供样品。
6.6.2外观:
A.依照客户要求。
B.检查内容:轴歪、轴松、轴间隙、轴缺料、漏铆轴、漏工序等。
6.9打磨检测内容:
6.9.1尺寸:
依照图纸要求/治具/样品。
6.9.2外观:
A.依照样品客户要求/样品。
B.检查内容:脱焊、焊位偏、焊穿、漏焊、变形、压伤、打磨后平面度、角度、直线度、漏工序等。
6.10包装检测内容:
6.10.1尺寸:
特殊情况下,依照客户要求,按图面要求检验,或用治具全检。
6.10.2外观:
6.2数冲检测内容
6.2.1尺寸:
依照图面标准/治具/客供样品。
6.1.2外观:
A.依照客户要求。
B.检查内容:是否要求贴保护膜、压伤、划伤/擦伤、毛刺/毛边、变形、花料、刀痕、节点、模印、字印不清(与图纸要求/样板是否一致)、色差、凸凹痕、色拉凸起、斑点、漏工序等。
6.3冲压检测内容
6.3.1尺寸:
A.依照图纸要求/治具/样品。
B.检查内容:所有钣金(五金)外观缺陷。
19.轴间隙:轴铆接后根部有间隙。
20.轴松动:轴铆接后松动的现象。
21.色差:实际颜色与标准颜色有差异。
22.凸凹痕:表面异常凸起或凹陷。
23.薄膜残留:在电镀/烤漆前,或依据客户要求在包装前应撕除保护膜,而没有去除保护膜干净的不良。
24.针孔:电镀/烤漆表面出现的细小圆孔。
钣金质量控制QC工程图
管制项目3落料200T游标卡尺落料尺寸、外观生产工艺指导书IPQC 1次/小时首件检验记录单、巡检记录表4冲切260T/315T卷尺、游标卡尺印花深度、切角尺寸生产工艺指导书IPQC 4次/小时首件检验记录单、外壳巡检记录表5折弯压筋200T游标卡尺、角度尺折弯角度、压筋深度生产工艺指导书IPQC 1次/小时首件检验记录单、巡检记录表6冲孔110T/160T /200T/260T 游标卡尺、针规冲孔大小、无毛刺生产工艺指导书IPQC 1次/小时首件检验记录单、巡检记录表7铆接110T/TOX焊接机游标卡尺铆接紧凑、无脱焊、法兰松生产工艺指导书IPQC 1次/小时首件检验记录单、巡检记录表8预装N/A N/A 海绵条粘贴位置、数量、型生产工艺指导书IPQC 1次/小时首件检验记录单、巡检记录表9攻丝攻丝机M4、M8通止规防止攻丝孔大、划丝生产工艺指导书IPQC4次/小时首件检验记录单、巡检记录表钣金质量控制Q制程名称主要设备管制方法记录方法NO作业生产设备量测仪器管制项目检验规范进料检验记录表、入厂履历权责单位检查频率根据检验标准进行检验首件检验记录单、巡检记录表1入厂物料检测N/A检验要求设备(卷尺、游标卡尺、电子称)入厂物料质量状态及产品标识检测入厂检验BOMIQC2拉伸压力机高度尺、游标卡尺拉伸外观、尺寸、小帽位置生产工艺指导书IPQC1次/小时。
钣金质量控制QC工程图
钣金质量控制QC工程图钣金质量控制QC工程图1.引言1.1 目的1.2 背景1.3 定义2.质量控制流程2.1 质量控制计划2.1.1 目标和指标2.1.2 资源需求2.1.3 时间安排2.2 原材料检验2.2.1 材料规格及要求2.2.2 检验方法2.2.3 抽样方案2.2.4 检验记录2.3 加工过程控制2.3.1 工艺流程2.3.2 操作规范2.3.3 检验设备2.3.4 过程检验记录 2.4 成品检验2.4.1 检验项目2.4.2 检验标准2.4.3 检验方法2.4.4 非合格品处理 2.5 纠正措施2.5.1 异常处理2.5.2 故障分析2.5.3 纠正和预防措施 2.6 文件和记录管理2.6.1 QC文件管理2.6.2 QC记录管理2.6.3 文件和记录保管要求3.关键指标监控3.1 缺陷率3.2 产品尺寸控制3.3 表面质量评估3.4 工时管理3.5 流程效率评估4.设备与仪器校准4.1 设备管理4.1.1 设备清单4.1.2 设备维护计划4.1.3 设备维护记录4.2 仪器校准4.2.1 校准程序4.2.2 校准频率4.2.3 校准记录5.培训和人员管理5.1 培训计划5.1.1 培训需求分析5.1.2 培训内容5.1.3 培训方法5.1.4 培训记录5.2 人员管理5.2.1 岗位职责5.2.2 考核评估5.2.3 奖惩制度6.安全管理6.1 安全意识培养6.2 安全规范制定6.3 安全事故记录和处理7.附件本文所涉及的法律名词及注释:1.质量控制:是指对产品或服务进行监督和调整,以确保其符合规定的质量要求。
2.QC:质量控制(Quality Control)的缩写。
3.检验:对产品或服务进行全面和系统的评估,以确定其是否符合规定的标准或规范。
4.异常处理:在质量控制过程中,处理发现的异常情况,以确保产品或服务的质量稳定。
5.故障分析:对产品或服务出现故障的原因进行分析,以找出解决问题的方法和措施。
钣金、喷塑(漆)检验标准
钣金类件喷塑(漆)质量检验标准发行版本:NO发行日期:2016.10.1实施日期:2016.10.1归口管理部门:质管部·编制:审核:批准:钣金喷塑检验标准目的为保证我公司产品中钣金件喷塑产品质量,减少图纸对通用要求的描述,规范验收过程中的检验操作,特制定本通用检验标准。
范围本标准适用我公司各类产品的钣金件检验验收,本标准侧重范围,规定了钣金件在质量形成过程中各个工序的检验要求和标准,主要从外观、尺寸控制、技术要求等作出具体检验要求。
其中标准参照国家有关标准与钣金行业标准制定而成。
二、尺寸判定钣金加工尺寸验收标准3. 折弯角度一般公差6. 周边毛刺≥10%t时需打磨处理(t为板厚)±0.5mm±1.0mm±1.0mm±2.0mm 9. V型折弯加工尺寸一般公差10. U型折弯加工尺寸一般公差>500mm±1.0mm±0.5mm±2.0mm±1.0mm11. 折弯R角尺寸确定⑴. 除非设计规定要求,钣金内圆弧角一般随模具角大小。
⑵. 除非设计、图纸另有要求,钣金外圆弧角一般按料厚度大小自然形成。
钣金件整机出厂通用检验标准目的为保证我公司钣金件产品质量,减少图纸对通用要求的描述,完善整机出厂钣金质量控制、检验验收工作,特制定本通用检验标准。
范围本标准适用我公司各类产品的钣金结构件整机出厂通用检验,它是对那些在图纸以及技术要求等文件上未能详尽标列的或没有必要特别指出的基本性及常规性的技术要求进行的归纳和补充说明。
本标准应与技术文件上所标识的技术要求一起并列参照执行,其中标准参照国家有关标准与钣金行业标准制定而成。
检验、验收场地可在装配现场或产品出厂发货地,其结果应一致,且作为最终结果。
一、外形表面检验要求二、外形尺寸检验要求1. 装配总要求⑴.待装配的部件均应为合格件。
⑵.装配应保证实物与图纸一致。
所有的材料、零部件、标准件的更改代替都必须经设计批准。
- 1、下载文档前请自行甄别文档内容的完整性,平台不提供额外的编辑、内容补充、找答案等附加服务。
- 2、"仅部分预览"的文档,不可在线预览部分如存在完整性等问题,可反馈申请退款(可完整预览的文档不适用该条件!)。
- 3、如文档侵犯您的权益,请联系客服反馈,我们会尽快为您处理(人工客服工作时间:9:00-18:30)。
数量:
零件号:零件号:
零件号:零件号:
缺料号码:
形位公差尺寸位置图纸要求实际尺寸
平面度□ok 直线度□ok 圆度 □ok 圆柱度□ok 平行度□ok 垂直度□ok
对称度□ok 同轴度□ok 位置度□ok 倾斜度□ok
序号焊丝(Φ)焊丝型号批次号WPS编号
电流(A)
电压(V)
焊接速度
未焊透咬边余高焊瘤焊缝不均1
合格:□合格:□合格:□合格:□合格:□2返工:□返工:□返工:□返工:□返工:□3飞溅气孔焊接变形不连贯焊错4
合格:□
合格:□合格:□合格:□合格:□角接平焊1F:□横焊2F:□立焊3F:□仰焊4F:□
返工:□
返工:□返工:□
返工:□返工:□
对接
平焊1G:□横焊2G:□立焊3G:□仰焊4G:□1油漆料号1
油漆料号2
黏度涂-4杯25-28 秒秒2黏度涂-4杯28-30 秒秒3湿膜厚度
湿膜尺
140-150μm
μm 3湿膜厚度
湿膜尺
120-140μm
μm 4干膜厚度干膜测厚仪75-105μm μm 4干膜厚度干膜测厚仪150-210μm μm 5新批次测试附着力测试X0Y2等级
级
5新批次测试附着力测试X0Y2等级
级
操作者分析不合格原因:设计□
工艺□物料□设备□人为□环境□量具□操作者:主管:
让步:□
报废:□合格:□
备注:(过程中的不合格在“□ok”内打“×”并在备注栏注明工位和原因)
Mod. Rev.
2,下料
(TOP-1742)
5,折弯
(TOP-1850)
除锈等级Sa1/2:□ok 粗糙度Rz:备注(每板首件需自检,注明返工零件和原因):
备注(注明返工零件和原因):焊接飞溅清除:□ok 工件边缘无锐口:□ok 毛刺清除:□ok 工号:日期:焊接位置
零件号:
角度:零件号:
角度:抽样自检零件号:
角度:
清洁度:□ok 3,坡口
4,打磨
(TOP-1119)
操作者:
工号:
FULL PARTICIPATION IN THE QUALITY MANAGEMENT
尺寸:
尺寸:尺寸:
尺寸:操作者2:
工号:
日期:
10,底漆
(TOP-3792)
11,中间漆
(TOP-3792)
操作者:工号:
日期:
操作者:
工号:
日期:
操作者:
工号:
日期:
操作者:
工号:
日期:
操作者:
质量控制自检表(装配其他部件)
物料描述:
物料号:产品订单号:
图纸号及版本:
操作者2:
工号:
日期:
备注:
1,编程
尺寸:操作者1:工号:操作者:
工号:
日期:
零件号:坡口尺寸:清理铁锈 油污:□ok 操作者2:
工号:日期:
清除熔渣 氧化皮:□ok 操作者1:编程零件对应程序号:程序员:工号:
日期:非编程零件号:抽样自检
操作者1:
工号:
日期:
日期:
数量:日期:尺寸:尺寸:
所有折弯零件号(包括卷圆和喇叭口):工件边缘无锐口:□ok 6,装配
(TOP-1838)
返工结果:
工艺:
12,检验
检验员:
工号:
日期:
返工方案:物料总数:
7,焊接
(TOP-0677)
焊丝型号及焊接参数
缺陷检查(TOP-A0037)
工号:日期:8,打磨
(TOP-1119)
9,喷砂
(TOP-0106)
不合格:。