多模滑动式拉丝机配模计算
铜(铝)滑动式大拉机低滑动率配模以及单线质量的控制
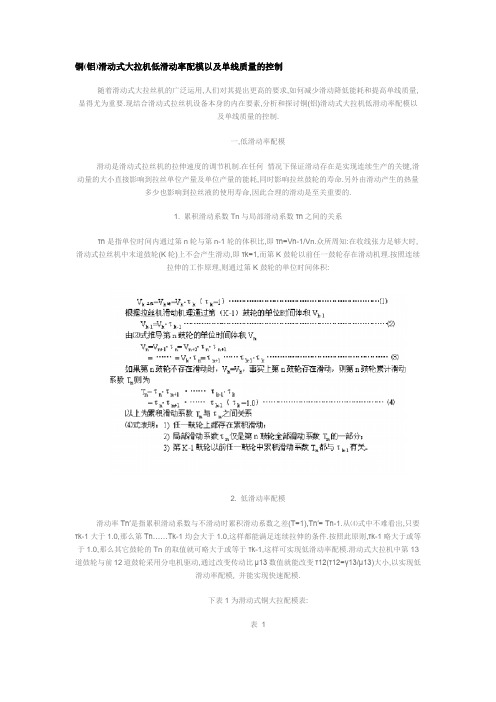
铜(铝)滑动式大拉机低滑动率配模以及单线质量的控制随着滑动式大拉丝机的广泛运用,人们对其提出更高的要求,如何减少滑动降低能耗和提高单线质量,显得尤为重要.现结合滑动式拉丝机设备本身的内在要素,分析和探讨铜(铝)滑动式大拉机低滑动率配模以及单线质量的控制.一,低滑动率配模滑动是滑动式拉丝机的拉伸速度的调节机制.在任何情况下保证滑动存在是实现连续生产的关键,滑动量的大小直接影响到拉丝单位产量及单位产量的能耗,同时影响拉丝鼓轮的寿命.另外由滑动产生的热量多少也影响到拉丝液的使用寿命,因此合理的滑动是至关重要的.1. 累积滑动系数Tn与局部滑动系数τn之间的关系τn是指单位时间内通过第n轮与第n-1轮的体积比,即τn=Vn-1/Vn.众所周知:在收线张力足够大时,滑动式拉丝机中末道鼓轮(K轮)上不会产生滑动,即τk=1,而第K鼓轮以前任一鼓轮存在滑动机理.按照连续拉伸的工作原理,则通过第K鼓轮的单位时间体积:2. 低滑动率配模滑动率Tn′是指累积滑动系数与不滑动时累积滑动系数之差(T=1),Tn′= Tn-1.从⑷式中不难看出,只要τk-1大于1.0,那么第Tn……Tk-1均会大于1.0,这样都能满足连续拉伸的条件.按照此原则,τk-1略大于或等于1.0,那么其它鼓轮的Tn的取值就可略大于或等于τk-1,这样可实现低滑动率配模.滑动式大拉机中第13道鼓轮与前12道鼓轮采用分电机驱动,通过改变传动比μ13数值就能改变τ12(τ12=γ13/μ13)大小,以实现低滑动率配模, 并能实现快速配模.下表1为滑动式铜大拉配模表:表 1从上表中各级τ取值在1.010~1.019之间,均接近1.0,符合低滑动率拉伸范围.3. 提高配模和修模精度,保证低滑动拉伸.从⑷式中不难看出τn减小,相应Tn在减小.当在生产过程模孔dn不断增大,相应τn及Tn在减小,甚至出现Tn<1.0危险情况.在低滑动拉丝生产中,这种变化尤为敏感.因此提高配模及修模精度,才能保证低滑动拉伸,实现高效低能耗生产.二, 保证收线张力均匀,提高单线质量.1. 采用PID过程控制方式,提高同步精度,保证收线张力稳定.以交流电机变频控制为例.在储线装置中联接一传感器,并设定传感器基准位置,在变频器中设定相应的固定基准值.当活动储线轮组上下位发生变化时,传感器输出不同的电位信号,并将此信号作为反馈信号接入变频器中,变频器通过PID运算功能将反馈值与固定基准值比较,并输出相应的频率信号,控制收线电机的转速.由于PID具有积分和微分的无限接近,但不等于固定值的特性,所以当活动储线轮组位置在很小范围内波动,变频器始终进行微小的调节,保证了线速度的同步,从而保证线的张力稳定.2. 改变储线形式,减少抖动.PID控制方式调节使单线始终处在动态平衡状态.单线在储线装置的长度不断发生变化,由此引起线的抖动.这种抖动严重时会造成单线在退火轮上打火,从而烧伤线的表面.通常采用储线方式为活动储线轮组在机体下方,固定储线轮组在机体上方,进线出线都经过活动储线轮.当活动储线轮组位置改变时,活动轮到退火(或定速鼓轮)和活动轮到收线装置之间线的长度都发生相应改变,造成线的张力变化,引起抖动.对此进行改进,将活动储线轮组安装在上方,固定储线轮组安装下方,进线出线都经过固定导轮,这样线到相邻设备长度不随活动储线轮组位置变化而改变,而仅在活动储线轮组与固定储线轮组之间发生改变(如图示1).也就是说,长度的变化被活动储线轮组的移动所吸收了,线的张力不发生变化,因此大大减少线抖动的程度.3. 减少弯曲次数,提倡同一平面的排线收线.单线经过导轮线轮时,由于回转半径R不同,引起线在导线轮表面内外侧线速度不同.导致线在内表面受到挤压,外表面受到拉伸.若经过多次"S"形反复弯曲,会产生如下不利因素:3.1 线的表面产生加工硬化,弹性增加;增加线在塑性变形中产生残余副应力(如拉副应力及压副应力),使得线脱离导线轮后继续变形.3.2 线与导线轮表面摩擦机会增加,线的表面质量难以保证;因挤压而产生了摩擦力,使得收线张力增加,由此可能引起线的拉伸.3.3 由于弯道的增多,收线时瞬间速度变化难以及时反映到储线装置,从而失去有效的控制.针对上述不利因素,提倡减少弯曲次数,保证收线与排线在同平面进行(如图示2).K1为转向轮,不随排线器移动;K2为转向轮,K3,K4为辅助导轮;K2,K3,K4安装于排线器上,随排线器一道移动.这种结构经过两次弯曲,弯曲角度比较大(90°),上述不利因素大大减少,单线品质得到有效的提高.三,结束语本文的内容,仅仅围绕滑动式拉丝设备内在要素, 从设计和制造的角度进行分析及总结.如何进一步提高设备综合性能是我们追求的目标.。
拉丝配模表

1.配模指南-拉丝配模四个步骤和关键数据计算方法概要:拉丝配模是金属丝拉拔时根据坯料尺寸及金属丝尺寸确定拉拔道次、拉丝模模孔尺寸及形状的工作,也叫拉拔程序或拉拔路线的制定。
可以分为单道次拉丝配模和多道次拉丝配模。
拉丝配模主要步骤包括以下四个步骤:1.选择坯料;2.确定中间退火次数;3.确定拉拔道次和分配道次延伸系数;4.配模校核.文章就圆形断面金属拉丝和异型断面金属拉丝两种情况,具体介绍拉丝配模步骤和计算方法。
2.滑动式拉丝机配模原理及配模计算实例介绍概要:拉丝配模指的是我们拉制过程中,对每道拉伸线模进行选择的方法。
合理的配模有两个要点,一是机械;滑动式拉丝机有其固定的拉线轮速比,通过实动式拉丝机配模计算实例,计算拉7.2mm铜杆至1.6mm铜线的相关数据;正文开始:写在前面:拉丝配模方法很多,很容易造成混淆,其中最根本的就是滑动系数的取值问题。
取大了有何优、缺点,取小一点又有何优、缺点,弄明白了,就会在工作中游刃有余。
死套某点,在实际中是不可能做到的。
不是简单计算,用公式一算就满足了。
如果你厂有50台机。
同是拉6种以上规格丝,如果按照某一种公式死套,想想最小要配几套模具。
所谓拉丝模具配完后,就要估计哪只模可能会引起断线。
哪个模会缩丝。
要估计断线是何原因,不要一断线就是铜杆空心,实际上,70%以上的空心铜与断线是自己拉丝造成的。
拉丝模具配模方法最常见的有以下三种:1.应用绝对滑动系数配模方法(J法),应用基础:拉丝机连续拉线,线材在每个塔轮上,单位时间体积是相等的。
2.传统理论配模方法(C法配模),以往定义符号从进线始,这里为了计算机计算方便(用Execl电子表格),刚好相反从出口模开始.3.新理论配模方法(X法配模),应用基础:即安全(不断线)顺利(能连续)拉线,又能把滑动降到最低.三种配模方法各有特点.C法,对设备,模具要求不严;X法和J法对设备精度要求高,对模具公差要求严,操作者的操作水平要求高.X法与系列套模相结合,效果更好.下面对这三种配模方法做具体介绍:一、应用绝对滑动系数配模方法(J法)应用基础:拉丝机连续拉线,线材在每个塔轮上,单位时间体积是相等的。
配模指南-拉丝配模四个步骤和关键数据计算方法

配模指南-拉丝配模四个步骤和关键数据计算方法整理:拉丝模1.什么是拉丝配模?拉丝配模是金属丝拉拔时根据坯料尺寸及金属丝尺寸确定拉拔道次、拉丝模模孔尺寸及形状的工作,也叫拉拔程序或拉拔路线的制定。
可以分为单道次拉丝配模和多道次拉丝配模。
单道次拉丝配模指在一台拉丝机上每次拉拔时金属丝只通过一个模子的拉拔配模。
多道次拉丝配模指在一台拉丝机上金属丝同时连续通过几个或十几个模子的拉拔配模。
它又分滑动式连续多道次拉丝配模和非滑动式连续多道次拉丝配模。
2.拉丝配模步骤和注意事项:拉丝配模主要步骤包括以下4个步骤:(1)选择坯料;(2)确定中间退火次数;(3)确定拉拔道次和分配道次延伸系数;(4)配模校核。
拉丝配模过程中有以下3点注意事项:(1)在保证拉丝过程稳定的条件下,充分利用金属的塑性和最少的拉拔道次达到提高拉拔生产率的目的;(2)合理分配道次延伸系数,以获得精确的尺寸、正确的断面形状及良好的表面质量;(3)配模参数与拉丝机的主要参数相适应。
下面就圆形断面金属拉丝和异型断面金属拉丝两种情况,具体介绍拉丝配模步骤和计算方法。
一、圆断面金属丝配模具体方法1.坯料选择:坯料的尺寸和断面形状应根据成品金属丝要求的状态、尺寸精度、力学性能、金属丝尺寸系列化生产及坯料的生产方式等情况选择确定。
圆丝的坯料一般为轧制、挤压及铸轧的盘条,也有采用连铸或锻造的坯料。
型丝的坯料,除了考虑尺寸大小外,还需考虑断面形状的相似性,以利于由坯料的断面形状逐步过渡到成品型丝断面形状的要求,如矩形丝选择矩形断面的坯料,双沟电车线选择圆形断面的线坯等。
2.确定中间退火次数:在拉拔过程中明显发生加工硬化的金属及合金,需要进行中间退火,恢复塑性利于继续拉拔。
对塑性好的如铜、铝等的粗线,可以不进行中间退火。
中间退火次数N用下式确定:(1)式中λΣ为由坯料至成品丝的总延伸系数;为退火问的平均总延伸系数。
3.确定拉拔道次和分配道次延伸系数拉拔道次n根据总延伸系数(无中间退火时)λΣ或两次退火间的总延伸系数λT和道次平均延伸系数确定:道次延伸系数分配分中间道次的延伸系数相等的及顺次递减的两种方案。
拉丝配模资料2

1 1 1 1 1 1 1 1
— — 1 00 22 . 0 00 1 1. 0 8 0 0 1 0 0 砺 1 00 0 0 1 0 0 67 1. 0 3 01 1. 0 8 01 1, C 2 06 1 0 0 61 1 0 0 01 1 00 47
算 出各 级 值 , 都 保 留 四 位 小 数 。此 时可 也 用 计 算 器 从末 后起 按 f2 l1l … 连续 l・ -i-… l rl
作出全部必要的核算。
主 题 词 : 滑 动 式拉 线机 拉 线
.
/
配 模 计算
/
/
采 用 低 滑 动 及 徽 滑 动 配 摸
~ ” 6
.
安
算 出各 级 值后, 应核 算各 级实际
的基 要求 件 本 和条
1.低 , 滑 动配 模 计 算 最 终 应 达 到 如 下 微 要 求 [: ()局 部滑 动 系 数 f~ 一 应 等 于 1 1 】 l 2 或微 量大 于 1., 2 局 部滑 动 系 数 一 应在 0 () 1
d ≥画、 l , 2:2..×√1 : 2 5 .u=2 4 .7
0 如血 船 坞 ¨ 蝎 埔
反 向配模 计算 法
设 己 知十 七 模 中拉机 的 各级鼓 轮 速 比 如 表 2 所 列, 求 成 品线 径 为 05 I 要 .4mm’ 试 作 低 滑 动配 模 并 求 其 进 线 直 径应 为 多大 ?
运算, 每乘上一数就获得一个 值 , 写下来再
乘 , 至 得 到 T- 直 。
8 .查看垒 部计算结果表明
() l 龟l 1 ~ 均符 台等 于 1 0或 微 量 大 于 . 1. 0的要 求 } ()l 1 0 4 ,也 符合 预定 要 求; 2 r I 2为 .5 7 ()q n铜 杆经 十 三道 拉 伸 后 , 可 得 3 , m】 8 的 最 小成 品 线为 姐 .6IZ,不 宜 再 小; 3 ] ̄ O () 另经 计算 ,十 三道 的累 积 精 动 系 数 4
拉丝设备的配模计算

拉丝设备的配模计算要正确配模,首先要知道所购设备的机械减面率。
这在设备规范里都有注明的。
目前国内拉丝机的机械减面率如下:20D(普通双变频微拉机) 11% i=1.173 定速轮减面率4% i=1.06324VX(立式单变频微拉机) 8% i=1.086 定速轮减面率6% i=1.08622D(立式双变频细拉机) 15% i=1.176 定速轮减面率8% i=1.08624D(立式双变频细拉机) 13% i=1.149 定速轮减面率8% i=1.08624DW(卧式单变频细拉机)13% i=1.149 定速轮减面率8% i=1.08614D(中线伸线机) 15% i=1.176 定速轮减面率8% i=1.08617MD (链条中拉机) 15 % i=1.176 定速轮减面率13% i=1.14917DS (铸造箱体齿轮中拉) 20% i=1.176 定速轮减面率15.5 % i=1.183知道这些设备的减面率,配模就有理论根据了。
一般情况下,考虑到塔轮上的滑差系数,模具的配比要大于设备减面率2---6%之间。
具体选多少,主要看铜线材料好坏,铜材质量好,塔轮上滑动系数取小一点,铜材不好,为了方便把机器开起来,可以把塔轮滑动系数放的大一点。
也就是说,塔轮的滑动系数放小了,对铜材要求高,同时因塔轮上滑动小,塔轮寿命长。
相反,塔轮滑动系数放大,会比较好开,但是塔轮寿命会缩短。
所以要根据自己实际的铜杆质量配模比较理想。
配模公式:1-【(下模)×(下模)÷(上模)×(上模)】=机械减面率+2—6%例如24D的拉丝机,如果知道上模尺寸,推算下模规格,如下:进线0.8MM 24D的机械减面率是13%,按照一般的铜材质量,取塔轮滑动系数在2.5%,这样推导出下模规格是:1-【(下模×下模)÷(0.8×0.8)】=0.155。
拉丝原理及配模

0),反之进线端甭紧则会加大反拉力,从而加大前拉力, 容易导致断线。具体计算过程参加宣天鹏有关滑动拉丝 基本条件的论文,最终得到的结果是:通过拉丝模线材 的延伸系数应
大于相邻塔轮的梯度,表示为μ/ε>1,这样线材在拉拔过 程时而紧绕在塔轮上同步前进,时而松开打滑,当然这 就会对塔轮表面产生磨损,增加功率损耗。 塔轮转动 的线
动率;累积的滑动系数是各道次滑动系数的连乘,累积 滑动率为1-1/累积滑动系数。 资料显示,滑动系数一般 在1.02-1.10之间,铜包钢与模具有着良好的润滑
作用,与塔轮的相对磨损也小,所以有学者建议滑动系 数取在1.01-1.04之内。我们倾向于1.02。 实际拉拔的过 程,因为每道次都预设了滑动,那么离成品模越
滑系数就更大。各道次伸长的分布规律一般是第一道低 一些,这是因为线坯的接头强度较低,线材弯曲不直, 表面粗糙,粗细不匀等,所以预留安全系数要大一些。 第二、三道可以取
高一些,因为经过第一道拉拔后,各种影响安全系数的 因素大大下降,同时金属的变形硬化程度也很小,这时 可以充分利用金属的塑性,而在以后的各道次中,伸长 可以逐道递减,这
与塔轮的相对磨损也小,所以有学者建议滑动系数取在 1.01-1.04之内。我们倾向于1.02。 实际拉拔的过程,因 为每道次都预设了滑动,那么离成品模越远的道
次,塔轮与铜包钢线之间的滑动就越大,塔轮表面磨损 也就越严重,这种滑动的不均匀性会缩短塔轮的使用寿 命,因此要考虑一个累积滑动效应,它是从成品模开始 向进线方向以连乘
口处,依次逐渐降低滑动率,最后降到1.01,箭头图表示 为: 1.01—1.01—1.01模时,与伸长相对应的有一个减面率的概念,也就 是面积减少的比例。比如从1.1拉到1.02,面积比例是 1.1*1.1:1.02*1.02=1.163,进线是1
拉丝原理及配模解析

2%之间,加上滑动率,一般将配比定为13-15%之间,依 据相邻模具的出线口径大小,我们可以直接算出减面率 或者伸长率,或者反过来,已知道某道模具的大小,已 知需要的
与塔轮的相对磨损也小,所以有学者建议滑动系数取在 1.01-1.04之内。我们倾向于1.02。 实际拉拔的过程,因 为每道次都预设了滑动,那么离成品模越远的道
次,塔轮与铜包钢线之间的滑动就越大,塔轮表面磨损 也就越严重,这种滑动的不均匀性会缩短塔轮的使用寿 命,因此要考虑一个累积滑动效应,它是从成品模开始 向进线方向以连乘
伸长率,可以推算上一道次模具的大小。值得一提的是, 在拉拔软线时,一定要注册出线模的局部压缩不能太大, 否则定速轮张力过大会将软线拉伤,导致线径缩小,延 伸下降。
在拉丝领域,人们普遍使用滑动式水箱拉丝机,也就是 卷筒与钢丝线速度存在差距,这样钢丝才能在与卷筒的 接触面打滑,从而产生滑动摩擦力,这个
0),反之进线端甭紧则会加大反拉力,从而加大前拉力, 容易导致断线。具体计算过程参加宣天鹏有关滑动拉丝 基本条件的论文,最终得到的结果是:通过拉丝模线材 的延伸系数应
大于相邻塔轮的梯度,表示为μ/ε>1,这样线材在拉拔过 程时而紧绕在塔轮上同步前进,时而松开打滑,当然这 就会对塔轮表面产生磨损,增加功率损耗。 塔轮转动 的线
力量带动钢丝在每个模具前后实现拉拔。 首先是拉丝
生产的效率问题,参照钢丝生产效率的计算,最关键的 是机器的利用率,出线的大小,以及最快收线速度。如 果按每小时
是有直接关系的,在我公司常规生产中,通过分析统计 发现,铜层变化几乎可以忽略。 再次是模具的工作问
拉丝配模计算

拉丝配模计算信息来源:金属制品日期:2013-12-30 点击:33 文字大小:[大][中][小]拉丝的方式有单拉和连拉两种,单次拉丝机每次通过一个模具拉拔,当一盘丝拉完后,将丝材从卷筒上取下,重新穿头,进行下道次的拉拔。
为提高拉拔速度和减少辅助操作时间,提高生产效率,常将数台单拉机串联起来,组成连续拉丝机,这样一次可连续穿几个模子,实现连续拉拔。
显而易见,在连续拉拔中,丝材直径变细,长度增加,要保证连拉正常运行,丝材与各卷筒(塔轮)之间有一定的配合关系的。
根据通过模具后丝材与卷筒(塔轮)有无相对运动,连续拉丝机可分为非滑动式和滑动式两种。
老式积线式滑轮拉丝机和现代直线式拉丝机拉拔过程中丝材与卷筒之间没有相对滑动,称为非滑动式拉丝机。
水箱式拉丝机拉拔过程中,丝材和塔轮之间存在相对滑动,称为滑动式拉丝机。
9.1. 非滑动拉丝机配模计算9.1.1. 拉拔道次估算减面率是实际生产中最常使用的变形参数,用同一道次减面率连续拉拔数道次后的总减面率,并不等于各道次减面率之和,为便于根据总减面率确定拉拔道次,提供道次减面率与总减面率计算表,如表12。
拉拔时,总减面率的选择和各道次之间减面率分配方法可参考本文6.6节提供的原则确定。
此外线材直径和强度与摩擦力也有一定的关系。
摩擦力过小,牵引力不足,易引起断丝。
摩擦力过大,在滑动时,丝材不易松开,将引起该级阶梯伸出端丝材松弛,塔轮表面压线,甚至断头。
丝材在塔轮表面缠绕圈数过多和塔轮表面出现粗糙或出现沟槽都是造成摩擦力过大的主要原因。
因此,实际操作中一般前几个模子出线端绕2~3圈,接近成品时绕1~2圈。
拉拔较细丝时,所绕圈数应更少,甚至只绕半圈。
十四模拉丝机一般只绕半圈。
9.2.2. 滑动式拉丝机配模计算在滑动式拉丝机上,除最后一道次(K道次)线速等于轮速(B K=V K),因而没有滑动外,其余各道次的轮速均大于线速(V n>B n)。
表示滑动程度大小的概念有:绝对滑动量,相对滑动率(简称滑动率),相对前滑系数(简称滑动系数),累计滑动率,累计滑动系数。
- 1、下载文档前请自行甄别文档内容的完整性,平台不提供额外的编辑、内容补充、找答案等附加服务。
- 2、"仅部分预览"的文档,不可在线预览部分如存在完整性等问题,可反馈申请退款(可完整预览的文档不适用该条件!)。
- 3、如文档侵犯您的权益,请联系客服反馈,我们会尽快为您处理(人工客服工作时间:9:00-18:30)。
一、理论分析 二、应用举例
一、理论分析
1.拉制道次 S0 S k 1 S1 S 2 总 1 2 3 k Sk S2 S3 Sk
如果 则
1 2 3 k
总 k
对上式两边取对数
lg 总 K lg
故
K
lg 总 lg
2.各道的延伸系数
方法一:根据塑性指标和延伸系数分不规律,参考 μ平均值,先选定k-1个μ值,最后一个由μ总/(μ1 μ2······μk-1 求出,经几次试算可达到所要求的分布规律。 方法二:除第一道外,取延伸系数为递减的等比数列, 以最后一道延伸系数为参考值,公比为q,其延伸系数 数列为
总
k 1 a
n aq
k n
n n n
n 2 3 4 k
ab
k 2
, ab
k 3
, a b , a b , a
2
( 2 ) ( 3 ) ( k 2 ) ( k 1 ) k
q
1 2
( k 1 )( k 2 )
3.各道线模孔径
已知进线径 d 0,成品线径 d k。 各道模孔直径按下式计
d n d n 1 n 1
算
n 1,, 4, k 1 2 3,
4.滑动连续多模拉线机
拉线机在速比为递减规律分布时,相对前 滑系数可取相同值; 在速比为相同值时,各道相对前滑系数应 取逐道递减规律分布,以使各道延伸系数 按递减规律分布。
k 1
1
q
2
( k 2 )( k 1 )
( k 1 )( k 2 ) 2
总 1
k 1 a
任意一道的延伸系数
n aq
k n
a
( k 1 )( kBiblioteka 2 ) (k n)总 1
k 1 a
n 2, 4, k 1 3,
d n d n 1 n 1
aq
k 2
,aq
k 3
, a q , a q , a
2
( 2 ) ( 3 ) ( k 2 ) ( k 1 ) k
总 1
a
k 1
q
1 2 3 ( k 2 )
a
公比 q