塑胶成型件进料检验规范
塑胶件检验标准

1.2
检验频率
2PCS/LOT(要求厂商在来料中附相应检验报告)
1.3
判定:100次以上循环产品表面无异常为合格(产品表面出现油膜有脱落、变色、裂痕、起皱、分离的异常)。
√
2.
温度循环测试
2.1
测试方法
把样品放放温度+66℃20%RH的箱中保持1小时,然后降低到32℃,90%RH保持1小时,接着调整箱中的
√
C面::L≤3mm, W≤0.1mm接受2个,两个间距≥2cm,
√
6.
油污:产品表面机器留下的油污。
A面:大于1个
√
B面::L≤2mm, W≤0.1mm接受1个,
√
C面::L≤2mm, W≤0.1mm接受2个,两个间距≥2cm,
√
7.
黑点:
A面:大于1个,
√
B面:D≤0.3mm2接受1个,
√
C面:D≤0.4mm2接受2个,两个间距≥2cm,
4.2.8电镀件附着力:检验电镀层与基材是否附着完好;(5PCS/LOT)
检验方法:用刀片在试件电镀面划10*10方格,每格距离为1mm,然后将3M胶纸贴牢方格表面,用手指压紧,使其方格内无气泡,再手持胶纸端部使其与丝印面呈45°角,然后迅猛拉胶纸端部,使其瞬间完全脱离试件表面,看电镀层与基材有无剥离现象,没有则判ACC,如有则判MAJ。
√
6.
夹水线:
A面:大于1个
√
B面L≤1mm,W≤0.2mm大于1个;
√
C面L≤1mm,W≤0.2mm大于1个;
√
7.
气纹:因气体干扰使胶件表面形成一种雾状发暗痕迹。
流纹:因冷料被挤入,在胶件表面形成的雾色或亮色的痕迹。
塑胶件检验标准办法
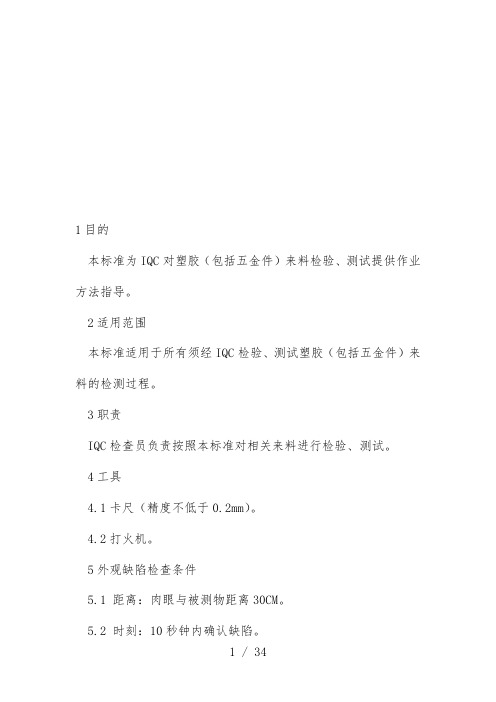
1目的本标准为IQC对塑胶(包括五金件)来料检验、测试提供作业方法指导。
2适用范围本标准适用于所有须经IQC检验、测试塑胶(包括五金件)来料的检测过程。
3职责IQC检查员负责按照本标准对相关来料进行检验、测试。
4工具4.1卡尺(精度不低于0.2mm)。
4.2打火机。
5外观缺陷检查条件5.1 距离:肉眼与被测物距离30CM。
5.2 时刻:10秒钟内确认缺陷。
5.3 角度:15-90度范围旋转。
5.4 照明:60W日光灯下。
5.5 视力:1.0以上(含较正后)。
6检验项目及要求6.1塑壳6.1.1外观a.所有外观面光滑过渡、无注塑不良。
b.外观面无划伤、痕迹、压痕。
c.非喷涂面不能有喷涂印。
d.喷涂均匀完整、不粗糙、无暗纹、亮斑,不能有局部堆积,少油,纤维丝。
喷涂是否牢固,硬度是否符合要求。
e.喷涂层色差光泽均匀、光亮。
6. 1.2尺寸测量下列尺寸,所有尺寸均须同图纸吻合或与样板一致。
a.五金槽的尺寸。
b.外型轮廓。
c.定位孔位置d.专门点位置及规格(超声线)。
6.1.3材质a.原材料是符合相关设计要求。
b.防火材料应用打火机做实验(需在确保安全的条件下进行)。
6.1.4试装配a.将胶壳与相应的爱护板、五金、支架等配件试装应配合良好。
b.必要时应取1-3个胶壳试超声,超声缝隙应均匀一致,焊接良好。
6.2五金件6.2.1尺寸测量五金的尺寸,须与样品或BOM一致。
6.2.2外观目测检查五金的色泽是否与样品一致,是否有划伤、变形,电镀层脱落等。
7检验方法7.1外观使用目测法检查被检品的外观。
7.2尺寸使用卡尺测量被检品的尺寸。
8塑壳表面分类A面:塑壳壳面;B面:塑壳底面。
9等级分类A级:公司所生产原配、原装产品的塑壳和五金来料;B级:公司所生产自有品牌或类似产品塑壳和五金来料;C级:以客户所承认样品生产的产品的塑壳和五金来料。
10 质量评定10.1检验方法塑胶(包括五金件)来料按按GB/T 2828-87 正常检查一次抽样方案II级检查水平进行抽样检查。
塑胶件来料检验标准
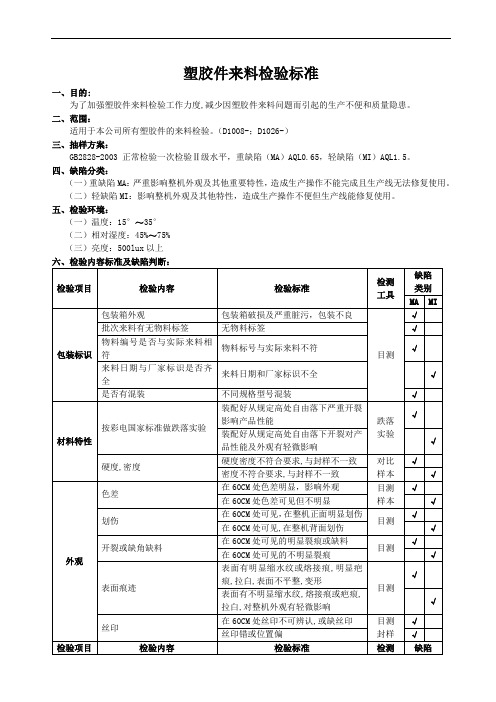
塑胶件来料检验标准一、目的:为了加强塑胶件来料检验工作力度,减少因塑胶件来料问题而引起的生产不便和质量隐患。
二、范围:适用于本公司所有塑胶件的来料检验。
(D1008-;D1026-)三、抽样方案:GB2828-2003 正常检验一次检验Ⅱ级水平,重缺陷(MA)AQL0.65,轻缺陷(MI)AQL1.5。
四、缺陷分类:(一)重缺陷MA:严重影响整机外观及其他重要特性,造成生产操作不能完成且生产线无法修复使用。
(二)轻缺陷MI:影响整机外观及其他特性,造成生产操作不便但生产线能修复使用。
五、检验环境:(一)温度:15°~35°(二)相对湿度:45%~75%(三)亮度:500lux以上七、操作方法与步骤:(一)检查有无来料物料标签,物料标号、日期及厂家名称有无缺漏或错;(二)检查包装箱有无破损,表面有无污垢;(三)检查有无混装物料;(四)在垫有珍珠棉的平台上方1M处物料自由跌落检查物料有无开裂破损;(五)对比封样检测物料的硬度,重量与封样是否一致;(六)60CM距离正对物料左右45°上下15°检查物料有无色差,划伤,破裂等缺陷;(七)60CM距离正对物料左右45°上下15°检查物料表面有无缩水纹,疤痕,拉白;检查表面是否平整,有无变形现象;(八)对比封样检查物料丝印有无印错位置是否正确,60CM距离目测丝印有无模糊;(九)用透明胶纸贴在塑胶件表面,用力将胶纸撕起,检查表面有无脱漆;如有掉漆测量掉漆面积;(十)检测物料外观尺寸是否与图纸要求一致,是否在图纸要求的公差范围内;检查孔径孔位;(十一)用相应的组装件组装,在60CM处目测是否有明显间隙;(十二)对上面的检查项目做好记录,填写来料检验报告,判定合格与否;并填写IQC检验单。
八、引用标准:8.1 GB2828-2003 逐批检查计数抽样程序及抽样表8.2 GB98384-88 跌落实验标准。
塑胶件进料检验标准
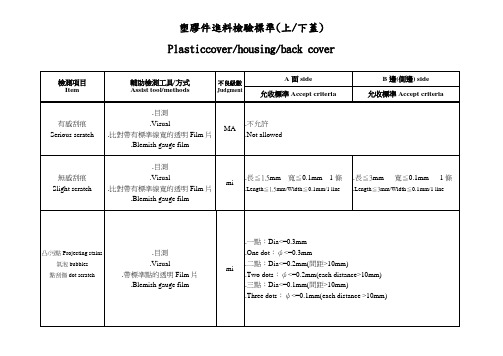
縮水Shrink
目測.Visual
MA
.不允許.Not allowed
印刷字體
Printing
目測
.Visual
MA
.粗細偏差<=0.05mm
.Thickness deviation <=0.05mm
.不得有漏印/鋸齒/拖印/斷字/雙影現象影響判讀
.Should not have loss printing/lack/crush/cutting/blot and can’tidentify
烤漆光澤
Coating luster
目測
.Visual
for poor and unsmooth luster
檢測項目
Item
輔助檢測工具/方式
Assist tool/methods
不良級數Judgment
A面side
B邊(側邊)side
允收標準Accept criteria
允收標準Accept criteria
百格測試
Cross test
檢驗方式及步驟:
inspection mode & step:
~在10mm正方之區域內間隔1mm交
塑膠件進料檢驗標準(上/下蓋)
Plasticcover/housing/back cover
檢測項目
Item
輔助檢測工具/方式
Assist tool/methods
不良級數Judgment
A面side
B邊(側邊)side
允收標準Accept criteria
允收標準Accept criteria
塑胶来料检验规范

能够更好的管控塑胶件来料的品质,使来料检验有章可循,确认来料品质满足生产要求。
2适用范围:
适用于本公司所有塑胶产品的来料检验。
3职责:
IQC检验员按作业指导对塑胶件进行检验,并保证其准确性。
4定义:
4.1浅划痕:指没有明显刮手感觉,但35cm视距可见的线状凹痕。
4.2深划痕:指有明显刮手感觉的线状凹痕。
数量不够。
B
外观
脏污
目测
检查其装配可见表面和孔位是否有油污、混色、异物等. 接受5秒钟内可用压缩空气吹掉或用布(可浸水或酒精)擦掉的脏污。
易擦除的脏污,但影响生产效率
C
不可擦拭或去掉的脏污、油污、异物等
B
变形
目测
检查整体是否有变形、间隙,段差;正面、侧面间隙比理想情形增大0.3mm以内可接受,底部间隙≤0.5mm ;错位≤0.3mm以内;变形(装配后无间隙)≤2mm;变形,(装配后有间隙)≤1mm;组装段差(正面不刮手)≤0.15mm,(正面刮手)≤0.10mm;其它不触摩面组装段差(不刮手)≤0.50mm,(刮手)段差≤0.30mm可接受。
4.9银纹:指胶件表面因受气体溢出干扰而形成的在光照下呈银色的泡点痕迹。
4.10脱皮:指胶料表面起皮或分层。
4.11烧焦:指局部温度过高而燃烧,在表面留下的发黄或碳化痕迹。
4.12气纹:因气体干扰而使胶件表面形成的一种雾状发暗痕迹。
4.13流纹:因冷料被挤入,在胶件表面形成的雾色或亮色的波纹。
4.14杂色点:指不可擦除的明显不同于要求色的点状混色、污点等;分黑点与不全黑点两类。
B
深划痕
目测
不允许有划伤及材质的划伤
有划伤及材质的划伤
B
塑胶成型件进料检验规范标准
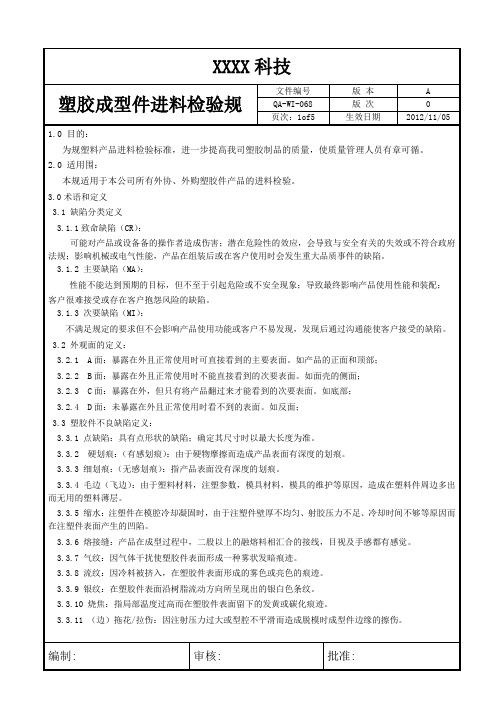
4.6 检验顺序:先正面→顶部→侧面→底部→反面。
5.0 抽样计划: 5.1 尺寸检验按 MIL-STD-105E 一般检验水准第Ⅰ套方案进行抽样,外观按第Ⅱ套方案进行抽样,性能检验
按每批次抽检 3~5 件进行;AQL 为 CR=0 、MA=1.5 、MI=4.0。 5.2 所有性能检验不符合项均按严重缺陷(MA)进行。 5.3 相关抽样标准或判定标准,也可视具体产品的品质状况或客户要求等做修正。
3.1 缺陷分类定义
3.1.1 致命缺陷(CR):
可能对产品或设备备的操作者造成伤害;潜在危险性的效应,会导致与安全有关的失效或不符合政府 法规;影响机械或电气性能,产品在组装后或在客户使用时会发生重大品质事件的缺陷。
3.1.2 主要缺陷(MA):
性能不能达到预期的目标,但不至于引起危险或不安全现象;导致最终影响产品使用性能和装配;
4.0 检验条件及检验环境的要求如下:
4.1 距离:人眼与被测产品表面的距离为 300mm~400mm;
4.2 时间:每次外观检查时间不超过 5 秒(如 5 秒看不出的缺陷可以忽略不计);
4.3 检查角度:以垂直正视为准+/-45 度;
4.4 照明:光照度达 600~800lux。
4.5 检验员视力要求:裸视或矫正视力不低于 1.0,且视觉正常,不可有色盲、色弱。
3.3.11 (边)拖花/拉伤:因注射压力过大或型腔不平滑而造成脱模时成型件边缘的擦伤。
编制:
审核:
批准:
XXXX 科技
塑胶成型件进料检验规
文件编号 QA-WI-068 页次:2of5
版本 版次 生效日期
3.3.12 缺料:产品某个部位不饱满。
3.3.13 翘曲:塑料件因应力作用等原因而造成的平面变形。
塑胶件来料检验标准
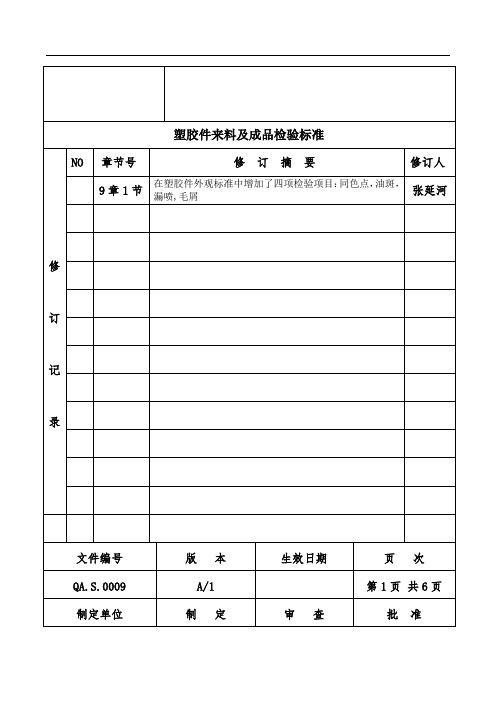
品质部塑胶件来料及成品检验标准1、制定目的规范和指导本公司品质部IQC 塑胶件来料检验作业、确保经品质部检验之产品符合产品质量要求。
2、适用范围:适合所有供应商塑胶件来料检验。
3、职 责3.1本标准必须经由培训合格之检验人员执行。
3.2检验中如有疑问及争执,须由品质工程师协调处理。
3.3若出现本标准中未涉及的项目,应立即通知品质工程师修改或解释本标准。
4、检验依据及引用文件:4.1 GB/T 2828.1-2003计数抽样检验程序第一部分:按接收质量限(AQL )检索的逐批检验抽样计划 4.2《零部件确认书》、《塑胶件检验作业指导书》及样品。
4.3《产品验证控制程序》,《不合格品管理程序》 5、外观区域划分AA 面:作为电池壳体同时又作为电池盖暴露在客户产品的外表面,直接影响客户产品外观的表面。
(例如:南通友联、中海达、联迪703胶壳)。
如下图例:A 面:指电池正面(即在使用过程中能直接看到的表面)。
如下图例:B 面:指电池的四个侧面,不在直视范围,需将物品偏转45º~90º才能看到的部分。
C 面:指电池底面,需将物品偏转90º~180º才能看到的部分;(说明:A 面与C 面是相对而言的,有时可互换,须根据产品结构特点而定).如下图例:B 面B 面B 面B 面B 面B 面B 面B 面B 面B 面B 面B 面AA 面亦为A 面AA 面亦为A 面 AA 面亦为A 面D 面:胶壳的内表面,, 如下图例:6、检验条件6.1 在自然光或光照度在300~500 lux 的近似自然光下。
6.2 检验者的视力或矫正视力不低于1.0,被检查表面和人眼视线呈45°角(参见下图)AA 面 A 、C 面 B 面 D 面 检查时间(秒) 10 10 10 10 检查距离(mm) 300 300 300 300 是否旋转旋转旋转旋转旋转7、抽样计划:7.1外观:按MIL-STD-105E Ⅱ级抽样;当来料数在1~50PCS 全检。
塑胶成型件进料检验规范

螺丝柱旳拉力测试:将螺钉旋入螺丝柱孔位后,用拉力计固定住螺丝并沿着螺丝旳轴向向外施加10kg(5kg)旳拉力,规定螺丝柱无断裂、脱出等现象。(注:大螺丝柱拉力为10kg,小螺丝柱拉力为5kg。)
螺丝柱旳扭矩测试:用电批以3.5N.m旳扭矩锁螺丝,规定不能出现打不进,打不紧(滑牙)、爆柱或难打现象。(注:大螺丝柱旳扭矩为3.5N.m,小螺丝柱旳扭矩为1.5N.m)
客户很难接受或存在客户埋怨风险旳缺陷。
次要缺陷(MI):
不满足规定旳规定但不会影响产品使用功能或客户不易发现,发现后通过沟通能使客户接受旳缺陷。
3.2 外观面旳定义:
3.2.1 A面:暴露在外且正常使用时可直接看到旳重要表面。如产品旳正面和顶部;
B面:暴露在外且正常使用时不能直接看到旳次要表面。如面壳旳侧面;
螺丝柱旳寿命:对于螺丝柱,在拆装螺钉3次后不容许出现打不进、打不紧(滑牙)、爆柱或难打现象。
塑胶件旳原材料检查:
6.2.4.1注塑厂家在每批送货时应附材质阐明书,在材质阐明书中注明材料旳制造商、牌号、型号、阻燃级别、着色方式、添加剂种类。
.2 塑胶阻燃级别测试见下表:
防火等级
自熄时间
测试措施
测试环境
C面:暴露在外,但只有将产品翻过来才能看到旳次要表面。如底部;
D面:未暴露在外且正常使用时看不到旳表面。如背面;
3.3 塑胶件不良缺陷定义:
点缺陷:具有点形状旳缺陷;确定其尺寸时以最大长度为准。
硬划痕:(有感划痕):由于硬物摩擦而导致产品表面有深度旳划痕。
细划痕:(无感划痕):指产品表面没有深度旳划痕。
规定:1、产品表面应无划痕,当有1条则视为不合格。(推出旳瞬间位置不作考虑)
- 1、下载文档前请自行甄别文档内容的完整性,平台不提供额外的编辑、内容补充、找答案等附加服务。
- 2、"仅部分预览"的文档,不可在线预览部分如存在完整性等问题,可反馈申请退款(可完整预览的文档不适用该条件!)。
- 3、如文档侵犯您的权益,请联系客服反馈,我们会尽快为您处理(人工客服工作时间:9:00-18:30)。
3.6 印刷不良缺陷定义:
3.6.1色薄:印刷字体的颜色偏淡。
3.6.2重影:二次印刷的整体错位。
3.6.3锯齿:字体的边呈现锯齿状。
3.6.3针孔:在应该有印刷的地方出现点状的缺少油墨。
3.6.4溅点:在应无印刷的地方出现点状油墨。
3.6.7偏位:字体或图案偏移指定的位置。
3.3.15气泡:由于原料未充分干燥,造成成型后产品内部有缩孔。
3.3.16混色:由于内应力,在产品表面产生与产品本色不同的颜色。
3.4 喷漆件不良缺陷定义:
3.4.1毛絮:油漆本身带有的,或油漆未干时掉落在油漆表面形成的纤维状毛絮。
3.4.2积漆:在喷漆件的表面或边缘出现的局部的油漆堆积现象。
3.4.3桔皮纹:在喷漆件表面出现大面积细小的像桔子皮形状的起伏不平。
3.5.4局部发黄:由于电镀时电流过大等原因造成产品的颜色发黄。
3.5.5暗斑:产品表面有局部发暗的现象。
3.5.6麻点:电镀件表面出现的颗粒状缺陷。
3.5.7针孔:在电镀件表面有针孔状的不良。
3.5.8雾状:电镀件表面出局部发白或模糊现象。
3.5.9粗糙:由于塑料件的模具没有抛光好,造成电镀件表面不光滑。
3.3.4毛边(飞边):由于塑料材料,注塑参数,模具材料,模具的维护等原因,造成在塑料件周边多出而无用的塑料薄层。
3.3.5缩水:注塑件在模腔内冷却凝固时,由于注塑件壁厚不均匀、射胶压力不足、冷却时间不够等原因而在注塑件表面产生的凹陷。
3.3.6熔接缝:产品在成型过程中,二股以上的融熔料相汇合的接线,目视及手感都有感觉。
3.4.10光泽不良:喷漆件表呈现出与标准样件光泽不一致的情况。
3.4.11鱼眼:由于溶剂挥发速度来自适当而造成在喷漆表面有凹陷或小坑。
3.5 电镀件的不良缺陷定义:
3.5.1漏镀:在应该电镀的地方没在电镀,而露出底材。
3.5.2镀层脱落:产品表面出现电镀层起皮的现象。
3.5.3污迹:在电镀件表面所残留的油污印迹。
3.4.4阴影:在喷漆件或塑料件表面出现的颜色较周围暗的区域。
3.4.5露底:在喷漆件表面出现局部的油漆过薄而露出基体颜色的现象。
3.4.6手印:在喷漆件表面或零件光亮面出现的手指印痕。
3.4.7油漆剥落:产品表面上出现涂层脱落的现象。
3.4.8颗粒:在喷漆件表面附着的细小尘粒或杂质。
3.4.9泛白: 涂膜表面呈气雾状。
客户很难接受或存在客户抱怨风险的缺陷。
3.1.3次要缺陷(MI):
不满足规定的要求但不会影响产品使用功能或客户不易发现,发现后通过沟通能使客户接受的缺陷。
3.2 外观面的定义:
3.2.1 A面:暴露在外且正常使用时可直接看到的主要表面。如产品的正面和顶部;
3.2.2B面:暴露在外且正常使用时不能直接看到的次要表面。如面壳的侧面;
编制:
审核:
批准:
XXXX科技有限公司
塑胶成型件进料检验规范
文件编号
版 本
A
QA-WI-068
版 次
0
页次:2of5
生效日期
2012/11/05
3.3.12缺料:产品某个部位不饱满。
3.3.13翘曲:塑料件因内应力作用等原因而造成的平面变形。
3.3.14杂质:因有异物混入原料中等原因,成型后在产品表面呈现出斑点。
XXXX科技有限公司
塑胶成型件进料检验规范
文件编号
版 本
A
QA-WI-068
版 次
0
页次:3of5
生效日期
2012/11/05
3.6.5花斑:对于大面积印刷不均而出现的局部斑状不良,此区域与别的区域看上去明显不同。
3.6.6粗细不均:字体的各个笔画之间出现粗细不一样的现象。
4.0检验条件及检验环境的要求如下:
3.1 缺陷分类定义
3.1.1致命缺陷(CR):
可能对产品或设备备的操作者造成伤害;潜在危险性的效应,会导致与安全有关的失效或不符合政府法规;影响机械或电气性能,产品在组装后或在客户使用时会发生重大品质事件的缺陷。
3.1.2主要缺陷(MA):
性能不能达到预期的目标,但不至于引起危险或不安全现象;导致最终影响产品使用性能和装配;
XXXX科技有限公司
塑胶成型件进料检验规范
文件编号
版 本
A
QA-WI-068
版 次
0
页次:1of5
生效日期
2012/11/05
1.0 目的:
为规范塑料产品进料检验标准,进一步提高我司塑胶制品的质量,使质量管理人员有章可循。
2.0 适用范围:
本规范适用于本公司所有外协、外购塑胶件产品的进料检验。
3.0术语和定义
3.3.7气纹:因气体干扰使塑胶件表面形成一种雾状发暗痕迹。
3.3.8流纹:因冷料被挤入,在塑胶件表面形成的雾色或亮色的痕迹。
3.3.9银纹:在塑胶件表面沿树脂流动方向所呈现出的银白色条纹。
3.3.10烧焦:指局部温度过高而在塑胶件表面留下的发黄或碳化痕迹。
3.3.11(边)拖花/拉伤:因注射压力过大或型腔不平滑而造成脱模时成型件边缘的擦伤。
5.3 相关抽样标准或判定标准,也可视具体产品的品质状况或客户要求等做修正。
6.0 塑胶产品的检验标准:
6.1 塑胶产品的外观检验标准:
4.1 距离:人眼与被测产品表面的距离为300mm~400mm;
4.2 时间:每次外观检查时间不超过5秒(如5秒内看不出的缺陷可以忽略不计);
4.3 检查角度:以垂直正视为准+/-45度;
4.4 照明:光照度达600~800lux。
4.5 检验员视力要求:裸视或矫正视力不低于1.0,且视觉正常,不可有色盲、色弱。
3.2.3C面:暴露在外,但只有将产品翻过来才能看到的次要表面。如底部;
3.2.4D面:未暴露在外且正常使用时看不到的表面。如反面;
3.3 塑胶件不良缺陷定义:
3.3.1点缺陷:具有点形状的缺陷;确定其尺寸时以最大长度为准。
3.3.2硬划痕:(有感划痕):由于硬物摩擦而造成产品表面有深度的划痕。
3.3.3细划痕:(无感划痕):指产品表面没有深度的划痕。
4.6 检验顺序:先正面→顶部→侧面→底部→反面。
5.0 抽样计划:
5.1 尺寸检验按MIL-STD-105E一般检验水准第Ⅰ套方案进行抽样,外观按第Ⅱ套方案进行抽样,性能检验按每批次抽检3~5件进行;AQL为CR=0 、MA=1.5 、MI=4.0。
5.2 所有性能检验不符合项均按严重缺陷(MA)进行。