高温硫化氢腐蚀
石油化工设备常见腐蚀类型及其防腐措施

石油化工设备常见腐蚀类型及其防腐措施(一)低温HCl-H2S-H2O型腐蚀与防腐1、主要腐蚀设备及部位主要腐蚀设备:此腐蚀环境主要存在于常减压装置的初馏塔和常减压塔的顶部(顶部五层塔盘以上部位)及其塔顶冷凝冷却器系统。
腐蚀部位:主要指常压塔上部五层塔盘、塔体及部分挥发线、冷凝冷却器、油水分离器、放水管和减压塔部分挥发线、冷凝冷却器等部位。
在无任何工艺防腐措施情况下,腐蚀十分严重,具体情况为:(1)常压塔顶及塔内构件,如无工艺防腐措施,碳钢腐蚀率高达2mm/a。
采用0Crl3材料作衬里,浮阀则出现点蚀,用18—8型奥氏体不锈钢作衬里则出现应力腐蚀开裂。
(2)冷凝冷却器是腐蚀最严重的部位。
在无任何防腐措施时,碳钢腐蚀率可高达2mm/a。
采用18—8型奥氏体不锈钢制冷凝器则在3个月到4年间陆续出现应力腐蚀破裂。
冷凝冷却器入口端(约100mm)处于高速两相流动时,在胀口处有冲状腐蚀。
空冷器更为严重,碳钢的腐蚀率可高达4mm/a。
(3)后冷器、油水分离器及放水管的腐蚀一般较前项为轻,腐蚀率随冷凝水pH值高低而变,一般为0.5~2.0mm/a。
(4)减压塔顶冷凝冷却器是减顶系统腐蚀主要几种的设备,无任何工艺防腐措施时,碳钢腐蚀率可高达5mm/a。
腐蚀形态:对碳钢为均匀减薄;对Crl3钢为点蚀;对1Crl8Ni9Ti钢则为氯化物应力腐蚀开裂。
腐蚀机理:HCl—H2S—H20部位的腐蚀主要是原油含盐引起的。
原油加工时,原油中所有的成酸无机盐如MgCl2、CaCl2等,在一定的温度及有水的条件下可发生强烈的水解反应,生成腐蚀性介质HCl。
在蒸馏过程中HCl和硫化物加热分解生成的H2S随同原油中的轻组分一同挥发进入分馏塔顶部及冷凝冷却。
当HCl和H2S2、HCl—H2S—H20环境下的防腐蚀措施此部位防腐应以工艺防腐为主,材料防腐为辅。
(1)工艺防腐措施“一脱四注”(原油深度电脱盐,脱后注碱、塔顶馏出线注氨、注缓蚀剂、注水)。
过热器与再热器的高温腐蚀及防止

3、选择合理的炉膛出口烟温,以及在 运行过程中避免出现炉膛出口烟温过高 现象,以减少和防止过热器与再热器结 渣及腐蚀。
4、定时对腐蚀发生。当已存在 高温腐蚀时,过多的吹灰,使灰渣层脱 落,会加速腐蚀的进行。
5、合理组织燃烧,改善炉内空气动力及 燃烧工况,防止水冷壁结渣、火焰中心 偏斜或后移等可能引起热偏差的现象发 生,减少过热器与再热器的沾污结渣。
过热器与再热器的 高温腐蚀与防止
•腐蚀原理 •防止措施
一、腐蚀原理
高温腐蚀主要有硫酸盐型和硫化物型两种。
1 、硫酸盐型腐蚀 硫酸盐型腐蚀主要有两种途径: 一种是灰渣层中的碱金属硫酸盐与SO3 共同作用 产生腐蚀; 另一种碱金属焦硫酸熔盐腐蚀。
2、 硫化物型腐蚀 当管壁附近呈还原性气氛和有硫化氢 (H2S)存在时会产生硫化物型腐蚀。
采取的防止措施有:
1、控制管壁温度 因硫酸盐型和钒氧化物型腐蚀都在较 高温度下产生,且温度越高,腐蚀速度越 快。目前主要采取限制蒸汽参数来控制高 温腐蚀。同时蒸汽出口段不布置在烟温过 高处,并要防止过大的热偏差。
2、采用低氧燃烧技术 降低烟气中SO3和V2O5的含量。试验 表明当过量空气系数小于1.05时,烟气 中的V2O5含量迅速下降,且烟气温度越高, 降低过量空气系数时减少V2O5含量的效果 越显著。
3、 SO2、SO3的生成及腐蚀 SO2和SO3的存在除能促使硫酸盐型 和硫化物型腐蚀发生外,其本身也会直 接对水冷壁产生腐蚀作用。
4、 硫化氢气体腐蚀 当炉内燃烧过程组织不良造成局部 供氧不足会产生大量的H2S气体。H2S除 能够促进硫化物型腐蚀外,还会对管壁 直接产生腐蚀作用。
5、在使用油点火或掺烧油,或烧用含有钒的煤 时,会对过热器或再热器引起钒氧化物型腐蚀。 当燃料中含有钒氧化物(如V2O3)时,在燃烧 过 程 中 会 进 一 步 氧 化 生 成 V2O5 , 熔 点 670~690℃。当V2O5与Na2O形成共熔体时,熔 点降至600℃左右。易于粘结在受热面上,并 发生化学反应生成腐蚀性的SO3和原子氧[0], 对管壁进行高温腐蚀。 燃料中难免含有硫、钠、钾和钒等成分,要 完全避免高温腐蚀是有困难的。 详见腐蚀原理
硫化氢理化性质及危险特性表

硫化氢理化性质及危险特性表物理性质。
| 化学性质。
| 危险特性。
|分子式:H2S。
| 可燃,分解为硫和氢气。
| 毒性:腐蚀性、窒息性。
|分子量:34.08 g/mol | 与氧气反应逐渐分解。
| 危险品分类:剧毒气体。
|外观:无色气体。
| 具有特殊臭蛋味。
| 爆炸极限:4.3%-46.0%体积浓度 |密度:1.535 g/L。
| 高温条件下可以燃烧。
| 燃烧产物:二氧化硫、水。
|熔点:-85.01°C。
| 与金属产生硫化物。
| 危险特性:易燃、易爆。
|沸点:-60.03°C。
| 可溶于水形成硫酸溶液。
| 导电性:不导电。
|硫化氢是一种常见的有毒气体,具有腐蚀性和窒息性。
它是可燃的,可以与氧气反应产生燃烧,燃烧产物为二氧化硫和水。
在高温条件下,硫化氢可以燃烧,具有易燃、易爆的危险特性。
此外,硫化氢还可以与金属产生硫化物。
它具有特殊的臭蛋味,可溶于水形成硫酸溶液,但不导电。
由于硫化氢的剧毒和危险特性,它被归类为剧毒气体。
在使用和处理硫化氢时,应注意防范措施,确保工作环境的安全。
避免直接接触硫化氢,并且要适当通风以确保室内气体浓度低于危险级别。
同时,应遵循合适的防护措施,如佩戴防护眼镜、面罩和防护服等。
以上是硫化氢的一些理化性质和危险特性的简要介绍。
了解硫化氢的危害和特性,对于相关行业和应用领域的工作人员至关重要,以确保他们能够正确地处理和使用硫化氢,以最大限度地降低潜在风险和危险。
高温硫腐蚀
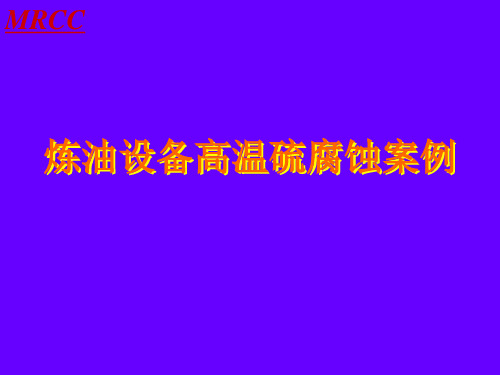
设备材质
➢ 铬含量越高,耐蚀性能越强。Cr含量大于5% 的合金钢具有较好的耐高温硫腐蚀性能。
➢ 一般选用Cr5MO、Cr9MO、Cr13、18-8等材料, ➢ 12CrMO、15CrMO、1.25Cr0.5MO、2.25Cr-1MO是
常用的耐热临氢用钢,不宜用在以高温硫腐蚀 为主的场合.
设备材质
渣油加氢装置:2003“4、19”事故
高温腐蚀主要部位
蒸馏装置: 240℃以上的管线 、设备。
重点监控部位:减 三、减四、减五、 减渣240℃以上的 管线、设备,尤其 注意280℃以上的 管线、设备。
高温腐蚀主要部位
焦化装置: 焦化装置是将减压渣油转化 为石油焦和油气的工艺装置 ,装置原料含硫量大,温度 高,主要腐蚀为典型的高温 硫腐蚀,主要有分馏塔250℃ 以上的侧线、循环线、从分 馏塔经进料泵、加热炉至焦 碳塔的高温渣油线及焦碳塔 底拿油线。
➢ 表现为腐蚀减薄为主。
高温硫腐蚀的几点规律
➢ (1)硫化物含量越高,腐蚀越高。 ➢ (2)温度越高,腐蚀速率越大; ➢ (3)管内介质流速越大,腐蚀越严重;(4)
弯头、大小头、三通、设备进出口接管等易产 生湍流、涡流部位,腐蚀速率高;直管段腐蚀 速率较小; ➢ (5)高温下碳钢腐蚀速率较大。 ➢ 设备材质是目前提高防腐性能的主要手段
•C、 三蒸馏装置:
•换13/1C壳程进口短管(20#钢)2000年2月18日因高温硫腐蚀 减薄穿孔,测厚为1.5mm。
•2000年8月2日减压渣油与减四连通线(20#)腐蚀减薄穿孔。
•2000年3月10日,渣油泵预热线(20#钢)腐蚀穿孔。
•1998年8月测厚发现减四泵(泵22、泵23)出口至一次换热器 (换12/1AB)弯头最薄处为1.3mm,更换为Cr5Mo。
h2s对金属的腐蚀
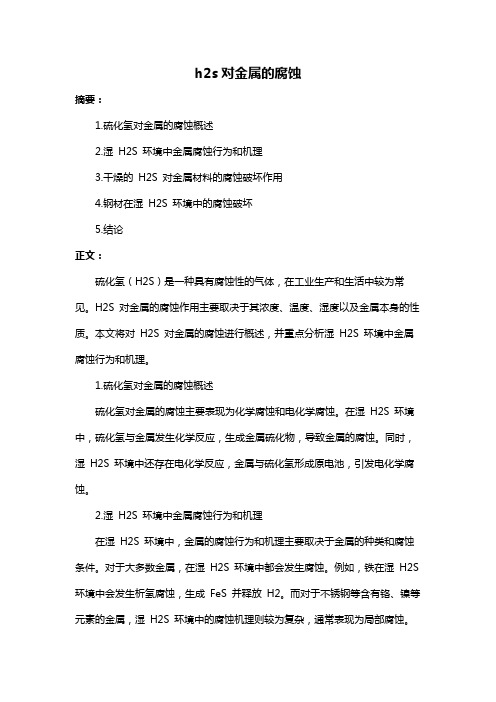
h2s对金属的腐蚀摘要:1.硫化氢对金属的腐蚀概述2.湿H2S 环境中金属腐蚀行为和机理3.干燥的H2S 对金属材料的腐蚀破坏作用4.钢材在湿H2S 环境中的腐蚀破坏5.结论正文:硫化氢(H2S)是一种具有腐蚀性的气体,在工业生产和生活中较为常见。
H2S 对金属的腐蚀作用主要取决于其浓度、温度、湿度以及金属本身的性质。
本文将对H2S 对金属的腐蚀进行概述,并重点分析湿H2S 环境中金属腐蚀行为和机理。
1.硫化氢对金属的腐蚀概述硫化氢对金属的腐蚀主要表现为化学腐蚀和电化学腐蚀。
在湿H2S 环境中,硫化氢与金属发生化学反应,生成金属硫化物,导致金属的腐蚀。
同时,湿H2S 环境中还存在电化学反应,金属与硫化氢形成原电池,引发电化学腐蚀。
2.湿H2S 环境中金属腐蚀行为和机理在湿H2S 环境中,金属的腐蚀行为和机理主要取决于金属的种类和腐蚀条件。
对于大多数金属,在湿H2S 环境中都会发生腐蚀。
例如,铁在湿H2S 环境中会发生析氢腐蚀,生成FeS 并释放H2。
而对于不锈钢等含有铬、镍等元素的金属,湿H2S 环境中的腐蚀机理则较为复杂,通常表现为局部腐蚀。
3.干燥的H2S 对金属材料的腐蚀破坏作用与湿H2S 环境相比,干燥的H2S 对金属材料的腐蚀破坏作用较小。
在常温常压下,干燥的H2S 对金属材料无腐蚀破坏作用。
然而,在高温高压条件下,干燥的H2S 可能会对某些金属材料产生腐蚀破坏。
4.钢材在湿H2S 环境中的腐蚀破坏钢材在湿H2S 环境中的腐蚀破坏较为严重。
湿H2S 环境中,钢材会发生析氢腐蚀和局部腐蚀。
析氢腐蚀导致钢材表面形成大量的FeS,从而引起钢材的腐蚀。
局部腐蚀则使钢材的局部区域受到破坏,导致其性能下降。
5.结论综上所述,硫化氢对金属的腐蚀作用主要取决于其浓度、温度、湿度以及金属本身的性质。
在湿H2S 环境中,金属的腐蚀行为和机理较为复杂,腐蚀破坏作用较大。
硫化氢腐蚀浓度标准
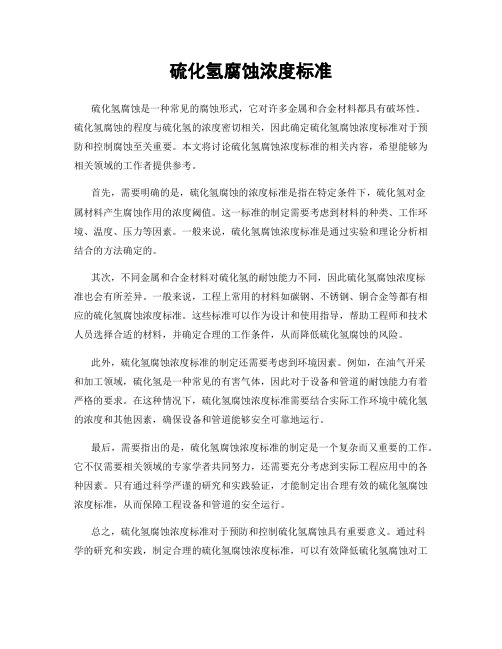
硫化氢腐蚀浓度标准硫化氢腐蚀是一种常见的腐蚀形式,它对许多金属和合金材料都具有破坏性。
硫化氢腐蚀的程度与硫化氢的浓度密切相关,因此确定硫化氢腐蚀浓度标准对于预防和控制腐蚀至关重要。
本文将讨论硫化氢腐蚀浓度标准的相关内容,希望能够为相关领域的工作者提供参考。
首先,需要明确的是,硫化氢腐蚀的浓度标准是指在特定条件下,硫化氢对金属材料产生腐蚀作用的浓度阈值。
这一标准的制定需要考虑到材料的种类、工作环境、温度、压力等因素。
一般来说,硫化氢腐蚀浓度标准是通过实验和理论分析相结合的方法确定的。
其次,不同金属和合金材料对硫化氢的耐蚀能力不同,因此硫化氢腐蚀浓度标准也会有所差异。
一般来说,工程上常用的材料如碳钢、不锈钢、铜合金等都有相应的硫化氢腐蚀浓度标准。
这些标准可以作为设计和使用指导,帮助工程师和技术人员选择合适的材料,并确定合理的工作条件,从而降低硫化氢腐蚀的风险。
此外,硫化氢腐蚀浓度标准的制定还需要考虑到环境因素。
例如,在油气开采和加工领域,硫化氢是一种常见的有害气体,因此对于设备和管道的耐蚀能力有着严格的要求。
在这种情况下,硫化氢腐蚀浓度标准需要结合实际工作环境中硫化氢的浓度和其他因素,确保设备和管道能够安全可靠地运行。
最后,需要指出的是,硫化氢腐蚀浓度标准的制定是一个复杂而又重要的工作。
它不仅需要相关领域的专家学者共同努力,还需要充分考虑到实际工程应用中的各种因素。
只有通过科学严谨的研究和实践验证,才能制定出合理有效的硫化氢腐蚀浓度标准,从而保障工程设备和管道的安全运行。
总之,硫化氢腐蚀浓度标准对于预防和控制硫化氢腐蚀具有重要意义。
通过科学的研究和实践,制定合理的硫化氢腐蚀浓度标准,可以有效降低硫化氢腐蚀对工程设备和管道的危害,保障工程安全运行。
希望本文的内容能够为相关领域的工作者提供一定的参考和帮助。
设备腐蚀类型
设备损伤及其防护一、腐蚀类型对于加氢装置而言,工艺复杂,流程较长。
其显着特点是临氢且高温高压,系统中还有较高浓度的硫或硫化氢存在。
加氢装置主要存在下列腐蚀类型:(1)高温氢腐蚀(2)氢脆(3)湿硫化氢腐蚀(4)高温硫或硫化氢与氢共存的腐蚀(5)硫氢化铵的腐蚀(6)奥氏体不锈钢连多硫酸应力腐蚀开裂(7)奥氏体不锈钢堆焊层的氢致剥离(8)Cr-Mo钢的回火脆化(9)氯离子腐蚀(10)碱脆1 高温氢腐蚀在高温高压条件下氢会渗透扩散到钢材中,与钢中不稳定碳化物的碳发生化学反应生成甲烷,甲烷不能逸出钢外,而是在晶间空穴和非金属夹杂物部位聚集,使钢材鼓泡、裂纹,并引起钢的强度、延伸性和韧性下降与劣化,还伴有晶间断裂。
一旦发生破坏,后果严重,这是加氢装置首先要考虑的问题。
反应部分包括加热炉、反应器、热低分、反应物流换热器及管道都有发生高温氢腐蚀的可能,必须选用能抵抗相应使用条件下高温氢腐蚀的材料。
通常是根据美国石油学会推荐惯例(API941)“炼油厂和石油化工厂高温高压临氢作业用钢”(亦称纳尔逊曲线)来选择。
且可根据使用情况与经验考虑一定的安全裕量。
根据本装置工艺过程的最高氢分压,其钢的使用极限温度不应超过 454℃;钢不应超过330℃。
操作中应严防异常超温,另外,使用过程的维修中,如果有补焊时,必须进行焊后热处理。
2 氢脆氢脆是由氢本身引起的钢材脆化现象,氢原子渗入钢材之后,使钢材中的原子结合里降低,因而造成钢材的延伸率、断面收缩率、冲击韧性显着下降。
但这种脆性是可逆的,一旦将氢从钢中脱出,钢材的力学性能就能恢复。
低温氢开裂的敏感和钢的强度值,氢含量以及容器内所处部位的应力有关。
决定钢抗氢脆最重要的因素是钢的强度值,钢材开裂敏感性随着强度的增加而提高。
高强度钢的氢脆开裂可能在大约150℃以下出现。
氢与钢材直接接触时被钢材吸附,并以原子状态向钢材内部扩散,溶解在铁素体中形成固溶体,使钢材边脆,塑性减小,这种脆性与氢在钢中的溶解度成正比。
锅炉水冷壁的高温硫腐蚀原因及对策
锅炉水冷壁的高温硫腐蚀原因及对策摘要:为避免锅炉水冷壁烟气侧高温硫腐蚀,本文通过对腐蚀原因、机理进行分析,提出行之有效的对策措施,能有效降低锅炉水冷壁低高温硫腐蚀。
提高锅炉运行的安全可靠性。
关键词:水冷壁;燃烧器;硫腐蚀;烟气;失效1引言为了控制锅炉燃烧装置尾部排放烟气中的NOX含量,减少其后部脱硝装置的压力,以空气分级燃烧技术为特征的低氮燃烧器广泛地应用于电站锅炉。
这种燃烧器的原理是:在主燃烧区的过量空气系数维持在0.85,燃料着火后在欠氧条件下燃烧,生成具有还原性的CO气体和焦炭,抑制NOX的生成,并将NO还原。
随着上层燃烬风的补入,过量空气系数增加,未燃尽的燃料在燃尽区充分燃烧。
由于在主燃烧区为欠氧燃烧,其所形成的还原区域,使灰熔点降低,易在附近的水冷壁结焦。
特别是在燃用高硫煤时,燃烧器区域的水冷壁将出现高温硫腐蚀,使炉管失效爆管。
2水冷壁高温硫腐蚀失效的发生机理2.1腐蚀机理关于锅炉水冷壁管的硫腐蚀主要发生在烟气侧热负荷较高区域。
燃煤中硫含量高是引起水冷壁管外侧高温烟气腐蚀的主要因素,当硫含量超过1%时就容易发生硫腐蚀。
水冷壁管的硫腐蚀分硫化物腐蚀、硫酸盐腐蚀和焦硫酸盐腐蚀。
一般来说,水冷壁管的高温腐蚀是管壁附近因欠氧燃烧形成还原性气氛引起的,腐蚀速度随温度升高而增加。
即熔融状态的煤粉在炉膛水冷壁管附近开始分离,使碳和硫聚集在边界层。
由于缺氧局部形成还原性气氛,硫的燃烧和三氧化硫的形成便发生困难,因而游离态的硫和硫化物(硫化氢等),便开始与铁发生反应,使管壁产生硫化物腐蚀。
水冷壁管的高温腐蚀属严重硫化物型腐蚀,腐蚀反应包括氧化和硫化反应,其过程如下:煤粉中的黄铁矿(FeS2)受灼热分解,产生自由态的硫原子。
FeS2=FeS+S管壁周围存在一定浓度的H2S和SO2,也会生成自由的硫原子。
2H2S+SO2=2H2O+3S分解出来的硫,由于缺氧,硫的燃烧和SO3的形成比较困难,便会与管壁金属反应生成FeS。
硫化氢金属腐蚀
精选ppt
14
A、金相组织
索氏体中碳化物呈均匀球形分布者,抗H2S腐 蚀好,珠光体的抗硫性能次之,马氏体最差;
焊接处金属组织呈马氏体,缺陷多,易聚集氢
分子,造成严重氢脆。
因此,在H2S环境的钢材设备要尽量避免损伤 表面或对设备进行冷加工,尽量减少残余应力。
• 氢脆和硫化氢应力腐蚀破裂是呈脆性破坏,在形式 上的特点是产生裂纹,且裂纹的纵深比宽度大几个 数量级,裂纹有穿晶裂纹和晶间裂纹。
精选ppt
7
• 它的发生一般要具备三个基本条件:
• 一定的拉应力、敏感材料和特定的环境
• 这种破坏有如下特点:
• ⑴破裂断口平整无塑性变形;
• ⑵在拉应力时才产生,且主裂纹的方向一般 总是和拉应力方向垂直;
精选ppt
20
2、加入缓蚀剂
原理:金属表面氧化生成钝化膜或改变 金属腐蚀电位起保护作用。
精选ppt
21
• 3、控制溶液的PH值
提高溶液PH值降低溶液中H+含量,可提 高钢材对硫化氢的耐腐蚀能力,维持PH 值在9~11之间,不仅可有效预防硫化氢 腐蚀,又可同时提高钢材疲劳寿命。
• 4、减少硫化氢溶液有管材的接触时间
精选ppt
12
3、硫化氢浓度 腐
蚀
一般浓度越高腐蚀速度
速 度
越快,但高于某一浓度
温度=26。7 ℃
时变慢300-500ppm。
硫化氢的体积分数低于
2× 10-3~5× 10-3mL/L 时,对材料的硬度要求 可以从HRC22放宽一些。 0 300 600 1200
锅炉高温腐蚀、氢腐蚀、垢下腐蚀机理和预防
材料腐蚀与防护在国民经济中的意义 腐蚀危害遍及日常生活和几乎所有的行业,给人 们带来了巨大的经济损失,造成了灾难性的事故, 消耗了宝贵的自然资源。 在工业化国家,腐蚀破坏导致的经济损失估计占 国民生产总值的3%~5%。 世界各国的腐蚀与防护专家普遍认为,如能应用 近代腐蚀科学知识及防腐技术,腐蚀的经济损失 可降低20%~30%。 腐蚀好比材料和设施的“癌症”,因此,同样要 像关注医学、环境保护和减灾一样关注腐蚀问题。 金属腐蚀的本质是金属原子失去电子被氧化的过 程,金属腐蚀一般可分为化学腐蚀与电化学腐蚀。
防止高温腐蚀的措施 加强对燃料的控制 :可通过燃烧前和燃烧中除硫的方法, 降低燃料的含硫量;同时控制适当的煤粉细度,尽可能均 匀各燃烧器之间的煤粉浓度分布; 加强燃烧调整、合理配风(加贴壁风):以达到降低水冷 壁附近还原性气氛和避免烟气直接冲刷水冷壁两个目的; 防止火焰偏斜和局部热负荷过高。 加强对给水的控制 :适当提高高温腐蚀区域水冷壁管内 水流速度,降低管壁温度,严格控制给水品质,避免因水 冷壁管内结垢而影响换热,从而导致水冷壁管壁温度增加; 提高金属抗腐蚀能力:可采用耐腐蚀高合金钢,渗铝管及 在管外喷涂耐腐蚀金属涂层等表面防护方式,降低腐蚀速 度;
金属常见的腐蚀形态与防护 腐蚀形态可分为两大类,即全面腐蚀和局部腐蚀。 全面腐蚀也称均匀腐蚀,是一种常见的腐蚀形态, 其特点是化学或电化学反应在全部暴露的表面或 大部分表面上均匀地进行,金属逐渐变薄,最终 失效。 全面腐蚀造成金属大量损失,但这种腐蚀危险性 较小。 防护措施: ①工程设计时考虑合理的腐蚀裕度, ②合理选材,③涂覆保护层,④添加缓蚀剂,⑤ 阴极保护。
可能对金属具有保护作用
无保护作用
电站热力设备用金属材料不仅要满足热强性的要求,还需 要具有较高的化学稳定性,即耐腐蚀性能。 在大气及弱腐蚀性介质中,腐蚀速度小于0.1mm/a为“耐 蚀”,小于0.01mm/a为“完全耐蚀”; 在强腐蚀性介质中,腐蚀速度小于1mm/a为“耐蚀”, 小于0.1mm/a为“完全耐蚀”; 所谓不锈,是相对而言,是在一定的介质里具有较高的抗 腐蚀性能。 锅炉设备中的受热面管,在运行中其外壁直接与高温火焰 和具有腐蚀性的烟气相接触,其内壁与汽、水相接触,因 而均会产生腐蚀现象。 电站常见的腐蚀损坏类型:蒸汽腐蚀、烟气腐蚀、垢下腐 蚀、苛性脆化、应力腐蚀、腐蚀疲劳。
- 1、下载文档前请自行甄别文档内容的完整性,平台不提供额外的编辑、内容补充、找答案等附加服务。
- 2、"仅部分预览"的文档,不可在线预览部分如存在完整性等问题,可反馈申请退款(可完整预览的文档不适用该条件!)。
- 3、如文档侵犯您的权益,请联系客服反馈,我们会尽快为您处理(人工客服工作时间:9:00-18:30)。
2、腐蚀案例分析——1号柴油加氢T202进料线腐蚀穿孔
(1)事件情况
1号柴油加氢装置汽提塔T202进料管线于2009年2月20日凌晨3:30时左右出现穿孔泄漏,装置随即降压生产,经测厚检查发现T202进料管线整段高温部位管线已整体减薄,最薄处为1.6mm,装置停工把该段管线更换。
图7.1 1号柴油加氢装置汽油管段(φ219×6)减薄穿孔图7.2 减薄管线剖开形貌
(2)管道使用情况
40万吨/年柴油加氢精制装置由原茂名石化设计院设计,建设公司安装。
该装置主要是以二次加工粗柴油或高含硫直馏粗柴油为原料,通过加氢精制,生产储存安定性和燃烧性能都较优良的柴油组分,副产少量粗汽油和瓦斯。
装置的加工流程灵活,也可以直馏煤油为原料,生产优质灯油或航煤。
并考虑了切换焦化粗汽油为原料,生产车用汽油调和组分的可能性。
装置于1991年4月基本建成,7月正式投产。
装置在2003年2月份的大修中进行了扩能改造,柴油处理能力已达到60万吨/年。
2006年8月,装置改造成以焦化汽油为原料,生产高质量的乙烯原料石脑油,目前汽油加氢精制能力为40万吨/年。
汽提塔T202进料线流程如图7.2所示,已部分预热的低分油(含汽油,H2S,H2)经反应产物第一换热器E201与反应产物换热,热塔进料与另一路90℃左右的冷进料混合后得到170℃左右的塔进料油进入汽提塔T202。
此段流程于2003年3月大修时改造完成,原先设计的流程为经反应产物第二换热器E202换热后进入T202,见图中虚线部位,按原流程换热后温度约为250℃;改造后流程为经反应产物第一换热器E201换热,换热后温度大大提高,达到280-320℃。
图7.3 1号柴油加氢装置T202进料管段示意图
对此段管线全面测厚显示,图7.3中红色所示的管段均整体减薄至1.5mm-2.8mm,穿孔的泄漏点就是在此管段的一个弯头前;而冷料线加入以后的管段厚度为5mm-7mm,属于正常厚度范围。
该管线材质为20#碳钢,规格为Φ219×6mm。
(3)腐蚀减薄穿孔原因分析
表7.21号柴油加氢操作参数
时间原料原料硫含量% 处理量m3/h T201进料温度℃D206气体流量
m3/h
20020523 柴油 1.18 85 244 950 20030327 柴油 1.33 57 270 720 20030717 柴油 1.26 92 276 1000 20040701 柴油 1.73 90 257 1000 20050602 柴油 1.89 80 270 900 20060803 柴油 1.56 75 265 859 20060831 汽油0.452 55 177 660 20070517 汽油0.944 64 180 700 20080707 汽油0.586 72 165 800 20090126 汽油0.375 60 159 750
表7.3 1号柴油加氢D206气体组成
时间2002
0523
2003
0327
2003
0717
2004
0701
2005
0602
2006
0803
2006
0831
2007
0517
2008
0703
2009
0101
氢气% 4.64 3.62 4.3 3.7 4.02 3.2 11.33 2.58 5.58 7.3
硫化氢% 52.24 51.68 65.46 65.64 56.02 55.21 16.1 11.74 25.22 17.45 经核算该管线的低分汽油介质工况为:氢气0.5%(v/v);硫化氢1.5%(v/v);流速15m/S;温度约315℃。
腐蚀减薄部位为注冷流前的高温碳钢管线,处于高温S、H2S及高温H2复杂腐蚀的环境。
装置在流程改造以前,该管段热料部分的最高温度为220℃,流程改造以后,热料部分的最高
温度大大提高,碳钢管道腐蚀速率大大增加。
硫腐蚀与温度有关,200℃以后硫腐蚀速度增加,250℃开始加快,350℃~460℃,时达到最强烈速度,硫化物受热后会分解出活性更强的活性硫。
钢高温硫腐蚀的关系通常可通过McConomy曲线计算。
硫腐蚀还与流速有关,在涡流高的地方保护性的硫化膜被冲刷,腐蚀加剧。
高温硫化氢和氢腐蚀通常为均匀腐蚀的形式,发生在约204℃以上的典型温度。
高温下硫化氢对钢的腐蚀反应为:
Fe + H2S FeS + H2
在氢的作用下H2S会加速对钢材的腐蚀,其腐蚀产物较无氢环境生成物相比更富致密性,附着牢固并具有一定保护作用。
在富氢的环境中,原子氢不断侵入硫化物垢层中,造成垢层的疏松多孔,使金属原子和H2S介质互相扩散渗透,从而推进H2S腐蚀的不断进行。
温度和硫化氢的浓度是影响高温硫化氢和氢腐蚀速率的主要因素。
常规分析中材料在高温硫化氢和氢腐蚀条件下的腐蚀速率是通过库柏-高曼(Couper-Gorman)曲线来预测的。
进查表分析该工况下碳钢计算腐蚀速率应<0.54mm/a,但实际腐蚀速率接近1mm/a,说明管道存在超过预期的腐蚀。
目前国外对加氢装置分馏系统的非正常腐蚀也进行了调查,调查结果显示加氢装置分馏系统高温部位腐蚀速率可能高于McConomy和Couper-Gorman预测腐蚀曲线且5Cr~9Cr 材料腐蚀率与碳钢一样高。
(4)处理措施
①更换减薄部位管线(因没有合金或不锈钢材料,更换了20#钢管线),安排定期监测。
②如果操作状况不作变更,建议在停工期间将管道升级为321材质。