故障模式和影响分析应用
故障模式及影响分析

图来确定潜在的故障原因,针对每一个故障模式,应尽可能地列出所想到的故障原因/故障 机理,潜在故障原因/机理应尽可能地描述准确和完整,以便针对相关的原因采取有的放矢 的补救措施。一般来说,确定潜在故障原因应首先从具有最高严重度的故障入手。频度(O) 是指在产品设想的使用寿命内,潜在故障原因/机理出现的可能性。一般从以往类似产品的 资料,如测试报告,顾客满意度报告,顾客退货报告,维修资料等来确定故障发生的频度。
严重度是潜在故障模式发生后,对系统、零件或顾客影响后果的严重程度的评价指标,
它是衡量潜在故障后果的指标。严重度是针对潜在故障后果而言的,减少严重度级别数值,
唯一的方法是修改设计。如果严重度的评价超出了小组的经验或知识范围,应与相关的工程
技术人员进行协商。表 2 给出了一个供参考的严重度分级标准。 表 2 严重度(S)评分表
2 FMEA 的实施步骤
FMEA 技术的分析过程包括识别潜在的故障模式,以及从故障后果的严重度(S)、故
障发生的频度(P)和故障的不可探测度(D)等三个方面评估故障模式。根据这三个方面
的评价得分计算故障的风险顺序数(RPN),风险顺序数高的故障模式即为改进的重点环节,
需分析其发生的原因和机理,拟定改进方案及实施计划。实施改进方案后,应对改进效果进
2
(3)分析潜在故障后果,评价其严重等级 潜在故障后果是指潜在故障模式对系统功能/顾客的影响。要根据顾客(这里所指的顾 客,既包括产品的最终使用者,也包括下一级的设计、制造人员)可能发现或经历的情况来
描述故障后果。要清楚地说明该故障是否会影响到产品的安全性或与政府、行业规定发生不
符。不仅要考虑故障后果对本系统的影响,也要考虑对其他系统、顾客的影响。
装置、统计过程控制、过程评价等过程控制方法。
fmea分析
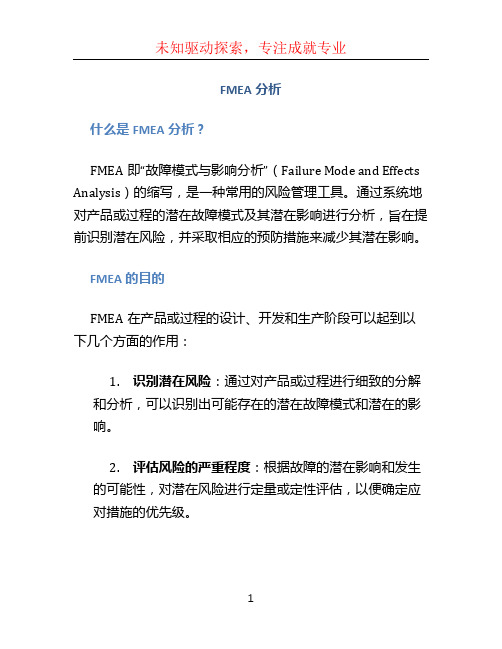
FMEA分析什么是FMEA分析?FMEA即“故障模式与影响分析”(Failure Mode and Effects Analysis)的缩写,是一种常用的风险管理工具。
通过系统地对产品或过程的潜在故障模式及其潜在影响进行分析,旨在提前识别潜在风险,并采取相应的预防措施来减少其潜在影响。
FMEA的目的FMEA在产品或过程的设计、开发和生产阶段可以起到以下几个方面的作用:1.识别潜在风险:通过对产品或过程进行细致的分解和分析,可以识别出可能存在的潜在故障模式和潜在的影响。
2.评估风险的严重程度:根据故障的潜在影响和发生的可能性,对潜在风险进行定量或定性评估,以便确定应对措施的优先级。
3.确定风险控制措施:基于评估的风险严重程度,制定相应的风险控制计划,包括预防措施、检测措施和修正措施,以减少故障发生的可能性和减轻其影响。
4.提高产品和过程可靠性:通过对潜在故障模式和影响的深入分析,可以发现设计或工艺上的问题,并提出相应的改进措施,以提高产品和过程的可靠性。
FMEA的应用步骤FMEA分析一般由以下步骤组成:1.确定FMEA的范围和对象:明确FMEA的应用范围,确定要分析的产品或过程,以及需要参与FMEA分析的团队成员和相关专家。
2.创建FMEA分析表:根据产品或过程的特征和结构,创建FMEA分析表,包括列出可能出现的故障模式、故障后果、故障发生的可能性、目前的控制措施等信息。
3.评估故障的潜在影响和可能性:对每个故障模式进行评估,确定故障的潜在影响和发生的可能性,并进行定量或定性的风险评估。
4.制定风险控制措施:根据风险评估的结果,确定相应的风险控制措施,包括预防措施、检测措施和修正措施,以减少故障的潜在影响和发生的可能性。
5.实施风险控制措施:根据制定的措施,执行相应的行动计划,包括改进设计、制定工艺规范、加强检测和监控等。
6.监控和更新FMEA分析:定期监控和评估已实施的风险控制措施的效果,及时更新FMEA分析表,以反馈和改进措施。
工业自动化生产线故障模式与效果分析FMEA

工业自动化生产线故障模式与效果分析FMEA在工业自动化生产线运行过程中,故障是不可避免的。
为了提高生产线的可靠性和稳定性,有效地预防和解决故障是非常关键的。
故障模式与效果分析(Failure Mode and Effects Analysis, FMEA)是一种常用的工具,可用于识别和评估故障模式,并分析其对生产线的影响。
本文将探讨工业自动化生产线故障模式与效果分析的重要性和应用方法。
一、FMEA的概述故障模式与效果分析是一种系统化的方法,用于确定产品或过程中的潜在故障,并评估故障对系统性能的影响。
它通过识别潜在故障模式和评估其严重性、发生概率和检测能力来进行风险评估,并提出改进措施,以减少或消除故障的可能性。
FMEA是一种常用的质量管理工具,广泛应用于各种领域,包括工业自动化生产线。
二、故障模式识别在进行FMEA之前,需要对工业自动化生产线进行仔细的故障模式识别。
这包括对每个组件和子系统进行分析,确定可能发生的各种故障模式。
例如,生产线的电气系统可能出现电压波动、短路等故障模式;机械系统可能出现轴承损坏、传动带断裂等故障模式。
通过系统地分析每个组件和子系统,可以全面了解潜在的故障模式。
三、故障模式严重性评估在FMEA中,对故障模式的严重性进行评估非常重要。
严重性评估指的是确定故障模式对工业自动化生产线正常运行或产品质量的影响程度。
这可以通过考虑故障的安全性、可靠性、经济性和环境性等因素来评估。
评估的结果可以帮助确定哪些故障模式应该优先处理。
四、故障模式发生概率评估除了严重性评估,故障模式的发生概率也是进行FMEA的重要因素之一。
发生概率评估是指确定故障模式在实际运行中出现的概率。
这可以通过历史数据、模拟分析和专家判断等方法来进行评估。
评估的结果可以帮助确定哪些故障模式是最常见的,从而在制定改进措施时给予更高的优先级。
五、故障模式检测能力评估故障模式的检测能力评估是指评估系统当前的监测和检测手段对故障模式的发现能力。
动力定位船舶的故障模式与影响分析及其应用

93珠江水运2024年01月学术 · 动力定位船舶的故障模式与影响分析及其应用 ·动力定位船舶的故障模式与影响分析及其应用◎ 史赛峰 刘早红 罗良宝 江敏 程世龙 谢峥杰 浙江友联修造船有限公司摘 要:文章介绍和分析了一种多用途海洋工程供应船动力定位系统,在海上试航阶段所进行的FMEA故障模式与影响分析及其验证性试验。
通过对主动性的部件和系统的冗余检查,不间断电源模拟失电和放电试验,对控制软件的响应演示和验证并通过必要的测试修正硬件故障等,按照FMEA分析程序来逐步模拟验证所设计建造的DP2级动力定位系统满足规范和使用要求。
关键词:DP系统;故障模拟;FMEA试验文章是基于通过对某DP2级多用途海洋工程供应船的FMEA (故障模式与影响分析)验证性试验整个过程的参与,完整地记录模拟试验的主要程序步骤和关键点,并验证了该DP2动力定位系统设计和建造的合理性。
DP2指安装有动力定位系统的船舶,在出现单个故障(不包括一个舱室或几个舱室的损失)后,可在规定的环境条件下,在规定的作用范围内自动保持船的位置和艏向[1]。
1.项目介绍所测试项目为89M DP2级多用途海洋工程供应船(MPSV),船长89米,型宽21米,型深7.5米,吃水5.9米,载重吨5131吨,航速11节,挂新加坡船旗,入ABS船级社,其主要用途为海洋工程供应运输和维护作业并可用于配合支持潜水作业。
该船配备4台1881kW发电机为全船提供电力,并可通过主配电板将电力传输到艉部2台1850kW全回转推进器和艏部3台1200kW可调螺距侧向推进器,同时还配有1台940kW辅助发电机为120T克令吊和潜水设备提供电力。
动力定位及控制采用Kongsberg双冗余动力定位(DP)系统K-POS DP-21并配备有2套差分全球定位系统(DGNSS );3套电罗经(Gyro Compass);3套风速风向传感器(Wind Sensor);4套动态参考单元(M RU);1套激光定位系统(C y S c a n );1套雷达定位系统(R A D iu s);1套声呐定位系统(HiPA P)及1套张紧索系统(Tautwire)。
质量控制的FMEA故障模式与影响分析

提供改进方向
FMEA通过分析故障模式及其影响,为企业 提供明确的改进方向和优先级排序,有助于 企业有针对性地开展改进工作,提高改进效 果。
THANKS
流程改进
在生产或服务流程中, FMEA可用来识别潜在的问 题点,优化流程,提高生产 效率和质量。
项目管理
在项目实施过程中,FMEA 可用来评估项目风险,制定 风险应对策略,确保项目顺 利进行。
服务行业
在服务行业中,FMEA可用 来评估服务流程中的潜在问 题,提高服务质量和客户满 意度。
02 FMEA的步骤
05 FMEA的改进措施
设计改进措施
优化产品设计
通过分析故障模式,对产品设计进行优化,降低产品 故障风险。
引入新设计理念
利用新技术、新材料等手段,提高产品的可靠性和性 能。
强化设计验证
增加设计验证环节,确保设计符合预期要求,降低设 计缺陷。
过程改进措施
优化生产流程
通过改进生产流程,降低生产过程中的故障风 险。
VS
矩阵横轴列出故障模式,纵轴列出产 品或过程的功能,通过评估每个故障 模式对每个功能的影响,确定故障模 式的严重度(S)、发生频率(O) 和检测难度(D),进而计算风险优 先数(RPN)。
风险优先数(RPN)
风险优先数是一个数值,用于量化潜 在故障模式的风险,通过将严重度、 发生频率和检测难度的数值相乘得到 。
04 FMEA的实践应用
产品开发过程中的FMEA应用
故障模式识别
在产品开发阶段,FMEA分析有助 于识别潜在的故障模式,包括设 计、制造、装配和使用过程中可 能出现的问题。
风险优先级排序
根据故障模式的发生概率和影响 程度,FMEA可以对风险进行优先 级排序,为后续设计和改进提供 依据。
FMECA(Failure Mode Effects and Criticality Analysis,故障模式、影响及危害性分析)

FMECA出自 MBA智库百科(/)FMECA(Failure Mode Effects and Criticality Analysis,故障模式、影响及危害性分析)目录[隐藏]∙ 1 FMECA简介∙ 2 FMECA的历史发展[1]∙ 3 FMECA的步骤∙ 4 FMECA的运用范围∙ 5 FMECA的应用o 5.1 FMECA在供应链风险管理中的应用[1]o 5.2 FMECA在食品安全追溯中的应用[2]∙ 6 实施FMECA应注意的问题[3]∙7 参考文献[编辑]FMECA简介故障模式、影响及危害性分析(FMECA)是针对产品所有可能的故障,并根据对故障模式的分析,确定每种故障模式对产品工作的影响,找出单点故障,并按故障模式的严酷度及其发生概率确定其危害性。
所谓单点故障指的是引起产品故障的,且没有冗余或替代的工作程序作为补救的局部故障。
FMECA包括故障模式及影响分析(FMEA)和危害性分析(CA)。
故障模式是指元器件或产品故障的一种表现形式。
一般是能被观察到的一种故障现象。
如材料的弯曲、断裂、零件的变形、电器的接触不良、短路、设备的安装不当、腐蚀等。
故障影响是指该故障模式会造成对安全性、产品功能的影响。
故障影响一般可分为:对局部、高一层次及最终影响三个等级。
如分析飞机液压系统中的一个液压泵,它发生了轻微漏油的故障模式,对局部即对泵本身的影响可能是降低效率,对高一层次即对液压系统的影响可能是压力有所降低,最终影响即对飞机可能没有影响。
将故障模式出现的概率及影响的严酷度结合起来称为危害性。
故障模式和影响分析(FMEA)是在产品设计过程中,通过对产品各组成单元潜在的各种故障模式及其对产品功能的影响进行分析,提出可能采取的预防改进措施,以提高产品可靠性的一种设计分析方法。
它是一种预防性技术,是事先的行为,是纸上谈兵的阶段,现已从可靠性分析应用推广到产品性能分析应用上。
它的作用是检验系统设计的正确性,确定故障模式的原因,及对系统可靠性和安全性进行评价等。
故障模式影响及危害分析报告

故障模式影响及危害分析报告一、引言故障模式、影响及危害分析(Failure Mode, Effects, andCriticality Analysis,FMECA)是一种系统性的方法,用于识别和评估系统各个组成部分的潜在故障模式、其可能的影响以及引发的危害程度。
本报告将针对其中一具体系统的故障模式、影响及可能的危害进行详细分析与评估。
二、分析方法本次分析采用FMECA方法进行,该方法的基本步骤包括:确定分析范围、识别故障模式、评估故障后果、确定故障严重程度等。
三、分析结果1.分析范围本次分析针对X系统的核心组件进行,包括A、B、C三个重要的部件。
2.故障模式及可能影响A部件:故障模式1:部件损坏可能影响:A部件损坏将导致系统无法正常工作,停止运行。
故障模式2:部件失效可能影响:A部件失效会引起系统性能下降,并且可能导致其他部件失效。
B部件:故障模式1:部件漏堵可能影响:B部件的漏堵将导致系统无法正常循环,进一步导致系统过热。
故障模式2:部件连接松动可能影响:B部件的连接松动会导致系统间隙扩大,影响系统的密封性能。
C部件:故障模式1:部件精度下降可能影响:C部件精度下降将导致系统测量结果的不准确,给系统带来误导。
故障模式2:部件过载可能影响:C部件过载将导致系统超负荷运行,进而引发短路甚至火灾。
3.故障危害评估为了对故障危害进行评估,我们采用了一个评估矩阵,将故障严重性分为轻微、中等和严重三个等级,评估结果如下:A部件:故障模式1:部件损坏危害等级:严重故障模式2:部件失效危害等级:中等B部件:故障模式1:部件漏堵危害等级:严重故障模式2:部件连接松动危害等级:中等C部件:故障模式1:部件精度下降危害等级:中等故障模式2:部件过载危害等级:严重四、决策和建议根据故障模式、影响及危害分析的结果,我们提出以下决策和建议:1.对于危害等级为严重的故障模式,应优先进行预防措施的制定和执行,以降低系统故障的风险。
质量故障模式与影响分析(FMEA)在质量改进中的应用案例
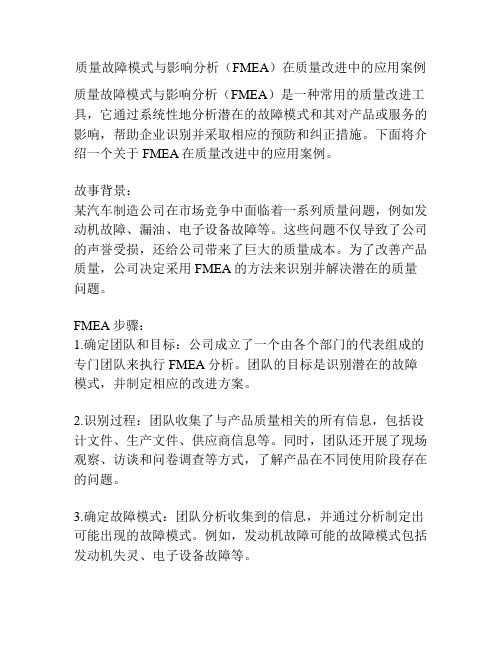
质量故障模式与影响分析(FMEA)在质量改进中的应用案例质量故障模式与影响分析(FMEA)是一种常用的质量改进工具,它通过系统性地分析潜在的故障模式和其对产品或服务的影响,帮助企业识别并采取相应的预防和纠正措施。
下面将介绍一个关于FMEA在质量改进中的应用案例。
故事背景:某汽车制造公司在市场竞争中面临着一系列质量问题,例如发动机故障、漏油、电子设备故障等。
这些问题不仅导致了公司的声誉受损,还给公司带来了巨大的质量成本。
为了改善产品质量,公司决定采用FMEA的方法来识别并解决潜在的质量问题。
FMEA步骤:1.确定团队和目标:公司成立了一个由各个部门的代表组成的专门团队来执行FMEA分析。
团队的目标是识别潜在的故障模式,并制定相应的改进方案。
2.识别过程:团队收集了与产品质量相关的所有信息,包括设计文件、生产文件、供应商信息等。
同时,团队还开展了现场观察、访谈和问卷调查等方式,了解产品在不同使用阶段存在的问题。
3.确定故障模式:团队分析收集到的信息,并通过分析制定出可能出现的故障模式。
例如,发动机故障可能的故障模式包括发动机失灵、电子设备故障等。
4.确定影响:团队评估每个故障模式对产品质量和客户满意度的影响程度。
例如,发动机故障会导致车辆停机,严重影响客户满意度。
5.确定原因:团队分析每个故障模式产生的原因,并列出可能的原因。
例如,发动机故障的原因可能是设计缺陷、生产工艺问题或供应商质量不稳定。
6.确定控制措施:团队制定针对每个故障模式的控制措施,以降低故障发生的可能性或减轻故障对产品的影响。
例如,针对发动机故障,可以加强设计验证、改进生产工艺和加强供应商质量管理等。
7.实施改进:团队将制定的控制措施落实到实际操作中,包括调整设计、改进生产工艺和提高供应商管理等。
同时,团队也要设立有效的跟踪和监控机制,以确保改进方案的有效性。
改进效果:通过FMEA的分析,该汽车制造公司发现了多个潜在的质量问题,并制定了相应的改进措施。
- 1、下载文档前请自行甄别文档内容的完整性,平台不提供额外的编辑、内容补充、找答案等附加服务。
- 2、"仅部分预览"的文档,不可在线预览部分如存在完整性等问题,可反馈申请退款(可完整预览的文档不适用该条件!)。
- 3、如文档侵犯您的权益,请联系客服反馈,我们会尽快为您处理(人工客服工作时间:9:00-18:30)。
指导性文件 GUIDANCE NOTES
GD16‐2017
中国船级社
故障模式和影响分析应用指南
2017
生效日期:2017 年 9 月 1 日 北京
目录
目 录 ................................................................................................................................................1 第 1 章 通 则.............................................................................................................................3
1
5.3 气体燃料发动机系统设计与应用描述 .......................................................................... 42 5.4 FMEA 程序.......................................................................................................................43 5.5 气体燃料相关的系统、设备及操作 .............................................................................. 44 5.6 分析结果的验证..............................................................................................................44 第 6 章 柴油机电控系统 FMEA 应用....................................................................................46 6.1 一般要求..........................................................................................................................46 6.2 FMEA 过程.......................................................................................................................46 6.3 FMEA 报告.......................................................................................................................49 参考文献.........................................................................................................................................50