冲压模具间隙对模具寿命的影响
冲压模间隙的标准是什么【大全】

冲压模具冲裁间隙,根据对模具的研究和改进的经验,尺寸精度、断面垂直度要求高的制件应选用较小间隙值,断面垂直度与尺寸精度要求不高的冲压件,应以降低冲裁力、提高冲压模具寿命为主,可采用较大间隙值。
其值可按下列经验公式来计算:软材料:材料厚度t<1 mm,冲裁间隙c=(3% ~ 4%)tt = 1 ~ 3mm,c = (5% ~8%)tt = 3 ~ 5mm ,c =(8% ~10%)t硬材料:t <1mm,c = ( 4% ~5% )tt = 1 ~ 3mm,c = ( 6% ~8% )tt = 3 ~ 8mm,c = ( 8% ~ 13%)t因此影响间隙值的主要因素是材料性质和材料厚度。
材料比较硬或比较厚,间隙值越大。
在毛坯的送进方向上,具有两个或更多的工位,在压力机的一次行程中,在不同的工位上逐次完成两道或两道以上冲压工序的模具。
综合了单工序模和级进模的特点,利用机械手传递系统,实现产品的模内快速传递,可以大大提高产品的生产效率,减低产品的生产成本,节俭材料成本,并且质量稳定可靠。
扩展资料:结构零件,这类零件不直接参与完成工艺过程,也不和坯料有直接接触,只对模具完成工艺过程起保证作用,或对模具功能起完善作用,包括有导向零件、紧固零件、标准件及其它零件等。
应该指出,不是所有的冲模都必须具备上述六种零件,尤其是单工序模,但是工作零件和必要的固定零件等是不可缺少的。
高速铣削的主轴转速一般为15000r/min~40000r/min,最高可达100000r/min。
在切削钢时,其切削速度约为400m/min,比传统的铣削加工高5~10倍;在加工模具型腔时与传统的加工方法(传统铣削、电火花成形加工等)相比其效率提高4~5倍。
磨削及抛光加工由于精度高、表面质量好、表面粗糙度值低等特点,在精密模具加工中广泛应用。
精密模具制造广泛使用数控成形磨床、数控光学曲线磨床、数控连续轨迹坐标磨床及自动抛光机等先进设备和技术。
冲裁间隙对冲裁件质量的影响及其选择方法

冲裁间隙对冲裁件质量的影响及其选择方法冲裁是一种金属加工工艺,常用于冲压、冲剪、冲孔等生产工艺中。
在冲裁过程中,冲裁间隙是一个至关重要的因素,它直接影响着冲裁件的质量。
合适的冲裁间隙可以保证产品的精度和质量,而不恰当的冲裁间隙则会导致产品质量不佳甚至无法使用。
冲裁间隙的选择对于冲裁件的质量至关重要。
本文将从冲裁间隙对冲裁件质量的影响以及冲裁间隙的选择方法两个方面展开讨论。
一、冲裁间隙对冲裁件质量的影响1. 冲裁间隙对尺寸精度的影响冲裁间隙的大小会直接影响到冲裁件的尺寸精度。
如果冲裁间隙过大,会导致冲裁件的尺寸偏大,影响产品的装配和使用;如果冲裁间隙过小,会导致冲裁件的尺寸偏小,甚至会出现毛刺和变形现象,降低产品的使用价值。
2. 冲裁间隙对表面质量的影响合适的冲裁间隙可以保证冲裁件的表面质量,而不适当的冲裁间隙则会导致冲裁件的表面出现划痕、毛刺等表面缺陷,降低产品的外观质量。
3. 冲裁间隙对材料利用率的影响冲裁间隙的大小直接关系到材料的利用率。
如果冲裁间隙设置过大,会导致材料的浪费;而如果冲裁间隙设置过小,则会导致材料利用率低,增加生产成本。
4. 冲裁间隙对冲模寿命的影响冲裁间隙的选择也会对冲模的寿命产生影响。
合适的冲裁间隙可以减小模具的磨损,延长模具的使用寿命;而不合适的冲裁间隙则会加大模具的磨损,降低模具的使用寿命。
二、冲裁间隙的选择方法1. 根据冲裁件的材料和厚度选择冲裁间隙不同的冲裁材料和厚度需要采用不同的冲裁间隙。
一般而言,对于薄板冲裁,应该选择较小的冲裁间隙;而对于厚板冲裁,则需要选择较大的冲裁间隙。
2. 根据冲裁件的形状和要求选择冲裁间隙不同形状的冲裁件可能需要采用不同的冲裁间隙。
对于边缘光滑度要求较高的冲裁件,应该选择较小的冲裁间隙;而对于需要快速冲裁的冲裁件,则可以选择较大的冲裁间隙。
3. 根据冲裁件的使用要求选择冲裁间隙冲裁件的使用要求也会对冲裁间隙的选择产生影响。
对于需要高精度的冲裁件,应该选择较小的冲裁间隙;而对于一般要求的冲裁件,则可以选择较大的冲裁间隙。
冲裁模间隙的合理取值

xxxx飞机电有限公司xx板料冲压加工中无数的经验证明,冲裁模间隙的选用问题是关系到模具设计是否成功的重要因素,采用合理的间隙对于生产和经济效益都是有利的,从经济的观点出发,采用大间隙可提高模具的使用寿命,降低冲裁力。
1冲裁模间隙与模具寿命在传统设计中总是尽量选用较小间隙,因为模具在使用过程中,间隙会逐渐变大。
在满足产品技术要求的情况下,适当取大间隙可提高模具寿命。
如冲裁1.5mm厚的低碳钢板¢22mm,凸凹模间隙取料厚的8%时,冲8100件就因毛刺过大而刃磨;间隙取料厚20%时,冲51300件才刃磨,模具寿命可提高6倍。
不同材料的模具凸凹模间隙也不尽相同。
2冲裁模间隙与冲裁力的关系冲裁模具的间隙不同对模具和冲裁件所产生的应力不同,因而所需冲裁力也不同。
凸、凹模在小间隙情况下在冲裁断面上除了产生拉应力、剪切应力外还产生了压缩应力,摩擦力也相应增大,使冲裁力急剧增大。
如果冲裁速度增加则同比冲裁力增加幅度更大。
根据凸、凹模间隙的不同冲裁力可按表1选取k 值用如下公式计算:F=kLtτ式中F------冲裁力,Nk------冲裁力系数,与凸、凹模间隙有关,见表1L------冲裁件周边xx,mmt-------材料的厚度,mmτ-------材料的剪切强度,MPa表1冲裁力系数k的取值冲裁间隙Z5%----10%10%----15%15%以上k1.310.9对于要求不太高的冲件,凸、凹模尽量选用大间隙,冲件虽然是略微凹曲的圆台形体但却减小了冲裁力。
3冲裁模间隙的有效条件对凸、凹模间隙的分析是在满足下列条件是进行的:(1)凸模及凹模合理的同心度。
(2)沿冲裁刃口线间隙分布均匀。
(3)冲床滑块运动时不影响凸、凹模的同心度。
(4)冲床工作台牢固平整。
(5)刃口锋利,保证光洁度。
4冲裁模间隙适当加大的好处(1)防止粘模,降低了对润滑的要求。
粘模是由严重摩擦发热而引起的,粘模后粗糙的模具刃口使冲件断面上拉出毛刺,磨损更加严重,很块使模具进入恶性循环,因而模具很快报废。
模具设计中凹凸模间隙对模具寿命的影响
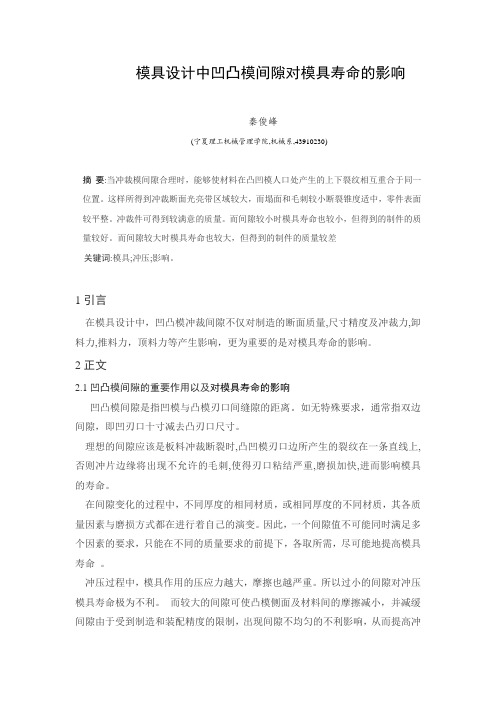
模具设计中凹凸模间隙对模具寿命的影响秦俊峰(宁夏理工机械管理学院,机械系,43910230)摘要:当冲裁模间隙合理时,能够使材料在凸凹模人口处产生的上下裂纹相互重合于同一位置。
这样所得到冲裁断面光亮带区域较大,而塌面和毛刺较小断裂锥度适中,零件表面较平整。
冲裁件可得到较满意的质量。
而间隙较小时模具寿命也较小,但得到的制件的质量较好。
而间隙较大时模具寿命也较大,但得到的制件的质量较差关键词:模具;冲压;影响。
1引言在模具设计中,凹凸模冲裁间隙不仅对制造的断面质量,尺寸精度及冲裁力,卸料力,推料力,顶料力等产生影响,更为重要的是对模具寿命的影响。
2正文2.1凹凸模间隙的重要作用以及对模具寿命的影响凹凸模间隙是指凹模与凸模刃口间缝隙的距离。
如无特殊要求,通常指双边间隙,即凹刃口十寸减去凸刃口尺寸。
理想的间隙应该是板料冲裁断裂时,凸凹模刃口边所产生的裂纹在一条直线上,否则冲片边缘将出现不允许的毛刺,使得刃口粘结严重,磨损加快,进而影响模具的寿命。
在间隙变化的过程中,不同厚度的相同材质,或相同厚度的不同材质,其各质量因素与磨损方式都在进行着自己的演变。
因此,一个间隙值不可能同时满足多个因素的要求,只能在不同的质量要求的前提下,各取所需,尽可能地提高模具寿命。
冲压过程中,模具作用的压应力越大,摩擦也越严重。
所以过小的间隙对冲压模具寿命极为不利。
而较大的间隙可使凸模侧面及材料间的摩擦减小,并减缓间隙由于受到制造和装配精度的限制,出现间隙不均匀的不利影响,从而提高冲压模具寿命模具作用的压应力越大,摩擦也越严重。
所以过小的间隙对冲压模具寿命极为不利。
而较大的间隙可使凸模侧面及材料间的摩擦减小,并减缓间隙由于受到制造和装配精度的限制,出现间隙不均匀的不利影响,从而提高冲压模具寿命。
2.2凹凸模间隙的合理选择由以上分析可见,凸、凹模间隙对冲压件质量、冲压工艺力、冲压模具寿命都有很大的影响。
因此,设计冲压模具时一定要选择一个合理的间隙,以保证冲压件的断面质量、尺寸精度满足产品的要求、所需冲裁力小、冲压模具寿命高。
铝材的冲裁间隙
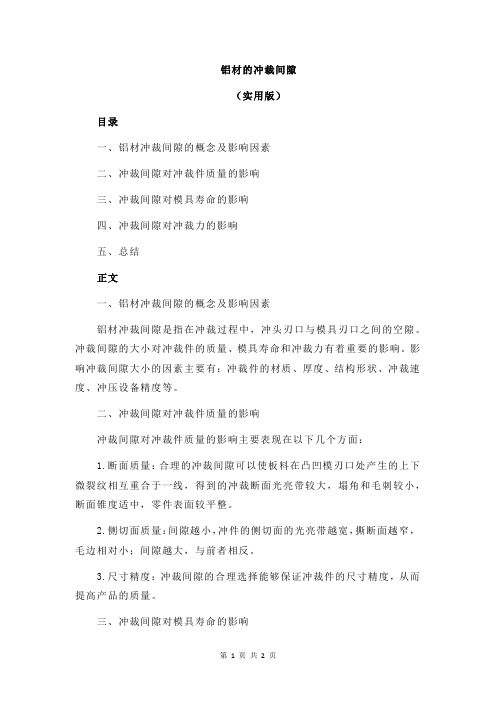
铝材的冲裁间隙(实用版)目录一、铝材冲裁间隙的概念及影响因素二、冲裁间隙对冲裁件质量的影响三、冲裁间隙对模具寿命的影响四、冲裁间隙对冲裁力的影响五、总结正文一、铝材冲裁间隙的概念及影响因素铝材冲裁间隙是指在冲裁过程中,冲头刃口与模具刃口之间的空隙。
冲裁间隙的大小对冲裁件的质量、模具寿命和冲裁力有着重要的影响。
影响冲裁间隙大小的因素主要有:冲裁件的材质、厚度、结构形状、冲裁速度、冲压设备精度等。
二、冲裁间隙对冲裁件质量的影响冲裁间隙对冲裁件质量的影响主要表现在以下几个方面:1.断面质量:合理的冲裁间隙可以使板料在凸凹模刃口处产生的上下微裂纹相互重合于一线,得到的冲裁断面光亮带较大,塌角和毛刺较小,断面锥度适中,零件表面较平整。
2.侧切面质量:间隙越小,冲件的侧切面的光亮带越宽,撕断面越窄,毛边相对小;间隙越大,与前者相反。
3.尺寸精度:冲裁间隙的合理选择能够保证冲裁件的尺寸精度,从而提高产品的质量。
三、冲裁间隙对模具寿命的影响冲裁间隙对模具寿命的影响主要表现在以下几个方面:1.模具磨损:合理的冲裁间隙能够减小模具在冲裁过程中的磨损,从而提高模具的使用寿命。
2.模具断裂:当冲裁间隙过小时,模具在冲裁过程中容易产生过大的应力,导致模具断裂。
3.模具修复:合理的冲裁间隙有利于模具的修复,减少修模费用和时间。
四、冲裁间隙对冲裁力的影响冲裁间隙对冲裁力的影响主要表现在以下几个方面:1.减小冲裁力:大的间隙对冲裁力的影响不是很大,但对卸料力、推件力影响显著,随着间隙的增大,卸料力、推件力都将减小。
2.提高冲裁效率:合理的冲裁间隙能够提高冲裁效率,减少冲裁时间。
五、总结综上所述,铝材冲裁间隙对冲裁件质量、模具寿命和冲裁力都有着重要的影响。
冲裁间隙1剖析

1.冲裁间隙过小和过大时,凸、凹模的受力分析。 2.冲裁间隙变化时,冲裁力及卸料力、推件力、顶件力的相应变化。
2020/3/3
总共27页
27
2
材料厚度t
2020/3/3
总共27页
28
2020/3/3
总共27页
25
思考题
1.什么是冲裁间隙? 2.冲裁间隙过大和过小对模具有什么影响?并作
简要的受力分析。 3.冲裁间隙对冲裁力的影响是有哪些? 4.冲裁间隙由小到大时,卸料力、推件力、顶件
力是怎么变化的? 5.理论计算法的公式是?取决于哪些因素? 6.查表法中,新模具的间隙值应怎么选择?
2020/3/3
总共27页
26
教学目标:
1.了解冲裁间隙的概念。 2.熟悉冲裁间隙对模具寿命的影响。 3.熟悉冲裁间隙对冲裁力及卸料力、推件力、顶件力的影响。 4.掌握确定冲裁模具间隙的方法。
教学重点:
1.过小和过大的冲裁间隙对模具寿命的影响。 2.冲裁间隙由小变大时,冲裁力及卸料力、推件力、顶件力的变化。 3.掌握理论计算法和查表法的使用方法。
计算冲裁模刃口尺寸 时,考虑到模具在使用 过程中的磨损会使刃 口间隙增大,应当按
Zmin值来计算。
总共27页
16
08是冲压用钢板中沸腾钢的一种牌号(中国 称08,日本称S9CK,德国用C10,前苏联用 08)08指的是含碳量万分之八;
2020/3/3
总共27页
17
16Mn是:16Mn叫低合金高强度结构钢 低合 金高强度结构钢:含碳量为0.16%,加入主要 合金元素锰、硅、钒、铌和钛等。
2020/3/3
总共27页
20
每种金属有它自己的再结晶温度,再结晶温度以上的退火即 软态组织 ,以下为硬态组织
冲压模具寿命的影响分析
冲压模具寿命的影响分析作者:蓝卫东来源:《沿海企业与科技》2010年第05期[摘要]模具寿命是指模具在保证产品零件质量的前提下,所能加工制件的总数量,它包括工作面的多次修磨和易损件更换后的寿命。
文章对影响冲压模具寿命的因素作详细分析,并提出相应的改善措施,以提高冲压模具的使用寿命。
[关键词]模具寿命;影响因素;改善措施[作者简介]蓝卫东,柳州职业技术学院机电工程系二级实习指导教师,研究方向:机械制造及加工、数控加工,广西柳州,545006[中图分类号] TG385.2 [文献标识码] A [文章编号] 1007-7723(2010)05-0048-0002一、引言模具寿命是指模具在保证产品零件质量的前提下,所能加工制件的总数量,它包括工作面的多次修磨和易损件更换后的寿命。
模具寿命一般可分为设计寿命和使用寿命,在模具设计阶段就应明确该模具适用的生产批量类型或者模具生产制件的总数量,即模具的设计寿命;在正常情况下,模具的使用寿命应大于设计寿命。
不同类型的模具正常损坏的形式也不一样, 冲压模具失效形式主要为磨损失效、变形失效、断裂失效和啃伤失效等。
然而,由于冲压工序不同、工作条件不同,影响冲压模具寿命的因素是多方面的。
以下就冲压模具在的模具设计、模具制造、模具使用等方面来分析冲压模具寿命的影响因素,并提出相应的改善措施来提高模具的使用寿命。
二、影响冲压模具寿命的因素(一)冲压模具设计方面1.模具设计质量模具从结构、选材,到关键参数的确定,都由模具设计员来确定。
这就要求设计员有较高的技术素质和丰富的实践经验,这样才能保证设计的模具的质量。
2.模具结构合理的模具结构有助于提高模具的承载能力,减轻模具承受的热-机械负荷水平。
例如,模具可靠的导向机构,对于避免凸模和凹模间的互相啃伤是有帮助的。
3.导向机构精度为了提高模具寿命,必须根据工序性质和零件精度等要求,正确选择导向形式和确定导向机构的精度。
准确、可靠的导向,对于减少模具工作零件的磨损,避免凸、凹模啃伤影响极大。
影响冲模寿命的因素和提高其寿命的措施
影响冲模寿命的因素和提高其寿命的措施
康 爱 英 ( 南 信 息 职 业 技术 学 院 湖 南 湖 望城 4 2 0 1 0 0 1
【 要】 摘 模具寿命是指模具因各种原 因而能上能引起 工作 失效, 最终不能修复而报 废之前 所加 工的冲件 总数。模具寿命 分为刃磨寿命 和 模 具总寿命 。本篇主要讨论影响冲压模具寿命的 因素和提高其寿命 的主要措施 。 【 关键词 】 模具 总寿命; 刃磨寿命 ; 冲压工艺及模具设计; 模具材料; 质量; 冶金 锻造和预处理; 模具加工工艺 0引 言 . 1 模具 的热处理工艺对模具寿命 的影 响 _ 3 模具 寿命是指模具因为磨损和其它原 因而失效 . 最终不 能修 复而 模具的热处理包括 : 预先热处理、 粗加 工后的消除应力退火 、 淬火 磨削后或 电加工后消除应力退 火等 模 具的热处理质量对模 报废之前所加工 的冲件总数 。模具寿命分 为刃磨 寿命 和模具 总寿命 。 与 回火 、 模 模具从前一次修复 到下 一次修复前所加工 的最大合格冲件数称 为刃 具的性能与使用寿命影响很大。实践证明 , 具工作零件的淬火变形 使用过程 中的早期断裂等 . 都与模具 的热处理工艺关系很大 磨寿命 : 模具从开始使用 到失效为止所加工 的合 格冲件总数 . 为模 与开裂 , 称 1 模具零件毛坯 的锻造和预处理对模具 寿命 的影 响 . 4 具总寿命 。 模具 寿命与模具类型 、 结构、 模具材 料、 工作条件等有关 . 模 锻造是模具工作零件制造过程 中的重要环节 。 锻件锻造 时会 出现 具寿命 受各种失效形式 的限制 。 各种 缺陷 . 例如 高碳高合金模 具钢锻件 , 因其具 有塑性低 、 变抗力 塑 1影响冲压模具寿命 的主要因素 . 大、 导热性差 、 温度 区间窄 、 锻造 组织缺陷严重 、 淬透性高 、 内应力大等 1 冲压工艺及模具设计对寿命的影响 . 1 特点 , 很容易产生锻造缺 陷。 这些缺陷可导致模具产生裂纹 。 响模具 影 1 . 冲压件 的材料对模具寿命的影响 .1 1 增加模具早期失 效的倾 向。 在生产实际中 , 由于冲压件材料厚度公差较大 、 材料性能波动 、 表 热处理工艺性及热处理后 的强韧性 , 锻造后的模具零件毛坯一般需进行预处理 ( 退火 、 正火 、 调质等 ) , 面质量差和不干净 等. 将造成模具工作零件磨 损加剧 、 崩刃 。 对于冲裁 模, 被冲板料厚度对模具 冲压载荷的影响较大 , 薄板冲裁模(≤1 ) t . 受 以消 除毛坯 中的残余内应力和锻 造组织 的某些缺 陷 .改善加工工艺 5 提高碳化物分 力较小 , 主要失效形式 为磨损 。 厚板 冲裁模 ( 1 ) t . 受力较 大. >5 其失效形 性 。模具钢经过适 当的预处理可使碳化物球化和细化 . 经淬火 、 回火后质量高 , 可大大提高模具寿命。 式为磨损和局部断裂( 刃)对于拉深模 , 崩 。 被拉深板料 的成形性能 、 厚 布均匀性 , 1 模具加工工艺对模具寿命的影响 . 5 度、 表面状况等 , 响模具 冲压载荷的大小和黏着倾 向的程度 。 均影 模具制造一般要经过切 削加工 、 磨削加工和电火花加工。 生产中 . 1 . 模具 的结 构形式对模具寿命的影响 .2 1 加工方法不当 . 加工质量 ( 特别 是表面质量 ) 存在 问题 . 都会显著影 响 整体式模具 由于存在凹凸转 角, 易造成应力集 中. 容 出现开裂 。 模具的耐磨性 、 断裂抗力 、 疲劳强度及热疲 劳抗力等 。 1 .模具的几何参数对模具 寿命 的影响 .3 1 1 .切削加工的影响 .i 5 凸、 凹模 的形状 、 间隙和圆角半径 的大小对模具 的磨损影 响很 大。 切削加 工中若产生加工 尺寸超差 、 尺寸 过渡处无 圆角连接 、 表面 如拉深模 过小 的凸、凹模 圆角半径在拉深过 程中将增大坯料流 动阻 粗糙 度不符合要求等 . 将严重降低模具 的疲劳强度和热疲劳抗力。 力, 增大摩擦力和成形力 , 使模具磨损或冲件拉断 。 15 .. 2磨削加工 的影响 1 .排样和搭边对模具寿命 的影 响 .4 1 在磨削过程 中. 易出现磨削烧伤和磨 削裂纹的质量 问题 . 容 这些 某些 需要往复送料 的排样和过小 的搭边值将 造成模具 的急剧 磨 问题的出现将 大大 降低模具的疲劳强度和断裂抗力 损和凸、 凹模 啃伤 。
冲压模具简答题答案知识讲解
冲压模具简答题答案1、什么是压力机的闭合高度?什么是模具的闭合高度?模具闭合高度与压力机闭合高度之间有什么关系?答:压力机的闭合高度是指滑块处于下死点时,滑块下表面至工作台上表面之间的距离。
模具的闭合高度是指模具在合模状态下,下模座的下平面与上模座的上平面之间的距离。
它们的关系:压力机最大闭合高度-5mm≥模具的闭合高度≥压力机最小闭合高度+10mm2、加工硬化对材料成形有何有利和不利的影响?答:有利一面:可以减少过大的局部变形,使变形更趋均匀,有利于提高材料的成形极限。
不利的一面:使材料变形抗力增加,进一步塑性变形困难,在后续的成形工序前要增加退火工序。
3、在模具排样中,有废料排样与无废料排样各有什么优缺点?答:有废料排样:工件尺寸完全由冲模来保证,精度高,模具寿命高,但材料利用率低。
无废料排样:工件质量差,模具寿命低,但材料利用率高。
4、什么是正装复合模与倒装复合模?答:根据落料凹模是在模具的上模还是下模,将复合模分成正装复合模和倒装复合模。
其中,落料凹模在下模的复合模称为正装复合模,落料凹模在上模的复合模称为倒装复合模。
5、在冲裁模中,正装复合模与倒装复合模各有何特点?答:正装复合模:落料凹模在下模,有压料作用,工件的平整性好,但出件均在模具上表面,操作不便。
用于薄料和工件精度要求高的冲裁件。
倒装复合模:落料凹模在上模,冲出的工件平整性较差,出件铰正装复合模好,操作较方便。
生产常用倒装类型的复合模。
6、什么是冲模的压力中心?确定模具的压力中心有何意义?答:冲模的压力中心就是模具在冲压时,被冲压材料对冲模的各冲压力合力的作用点位置,也就是冲模在工作时所受合力的作用点位置。
在设计模具时,必须使冲模的压力中心与压力机滑块的中心线重合,否则,压力机在工作时会受到偏心载荷的作用而使滑块与导轨产生不均匀的磨损,从而影响压力机的运动精度,还会造成冲裁间隙的不均匀,甚至使冲模不能正常工作。
因此,设计冲模时,对模具压力中心的确定是十分重要的 , 在实际生产中,只要压力中心不偏离模柄直径以外也是可以的。
冲压复习题参考资料
冲压复习题参考资料冲压复习参考资料⼀、冲压是利⽤冲模在冲压设备上对板料施加压⼒(或拉⼒),使其产⽣分离或变形,从⽽获得⼀定形状、尺⼨和性能的制件的加⼯⽅法。
⼆、冲压⼯艺的基本⼯序可以分为:分离⼯序和成形⼯序两⼤类。
还会涉及其他⼯序,如结合⼯序、装配⼯序、修饰包装⼯序等。
三、塑性与变形抗⼒的概念:所谓塑性,是指⾦属材料在外⼒的作⽤下产⽣永久变形⽽其完整性不被破坏的能⼒。
变形抗⼒⼀般来说反映了⾦属在外⼒作⽤下抵抗塑性变形的能⼒。
四、化学成分对塑性变形的影响:1.碳钢中多余的C便与Fe形成硬⽽脆的渗碳体,从⽽使碳钢的塑性降低,变形抗⼒提⾼。
含碳量愈⾼,碳钢的塑性愈差。
2.杂质元素对刚的塑性变形⼀般都有不利的影响。
3.合⾦元素加⼊刚中,塑性降低,变形抗⼒提⾼。
五、变形温度对⾦属塑性变形的影响,其总的趋势是:随着温度的升⾼,塑性增加,变形抗⼒降低。
其主要原因如下:1.随温度的升⾼,发⽣了回复与再结晶。
2.温度升⾼,临界剪应⼒降低,滑移系增加。
3.新的塑性变形⽅式——热塑性产⽣。
4.温度升⾼导致晶界的切变抗⼒显著降低,晶界易于滑动;⼜由于扩散作⽤的加强,及时消除了晶界滑动所引起的微裂纹。
六、根据9种主应⼒图,⽐较材料的塑性好坏: P10七、板料的冲压成形性能包括:抗破裂性、贴模性、定形性(结冻性)。
贴模性是指板料在冲压成形过程中获得模具形状和尺⼨并不产⽣板⾯缺陷的能⼒。
定形性是指制件脱离模具后保持其在模具内既得形状和尺⼨的能⼒。
⼋、延伸率:试样在出现缩颈之前的延伸率叫做均匀延伸率δu;试样屈服阶段的延伸率叫做屈服延伸率δs;试样拉断之前的延伸率叫做总延伸率δ。
延伸率⼤,板料允许的塑性变形程度也⼤,抗破裂性较好。
屈强⽐:屈服强度与抗拉强度之⽐δs/δb叫做屈强⽐。
δs/δb数值⼩,板料由屈服到破裂的塑性变形阶段长,抗破裂性好,有利于冲压成形;δs/δb数值⼩,回弹⼩,定形性好。
可以说,δs/δb数值⼩对所有冲压成形都有利。
- 1、下载文档前请自行甄别文档内容的完整性,平台不提供额外的编辑、内容补充、找答案等附加服务。
- 2、"仅部分预览"的文档,不可在线预览部分如存在完整性等问题,可反馈申请退款(可完整预览的文档不适用该条件!)。
- 3、如文档侵犯您的权益,请联系客服反馈,我们会尽快为您处理(人工客服工作时间:9:00-18:30)。
冲压模具间隙对模具寿命的影响文件排版存档编号:[UYTR-OUPT28-KBNTL98-UYNN208]冲压模具间隙对模具寿命的影响【摘要】利用一轴对称冲裁模形,研究了冲裁变形过程和的各个阶段,间隙变化对冲裁力的影响规以及在不同的间隙条件下,凸模的预期磨损使用寿命的计算方法。
关键词:模具;冲压;影响【Abstract】Basedon as ymmetry blanking model,it interprets the blankingprocess andits deforma-.Discussing val'ioll2 clearance leads tothetrend ofpunchforce.Mlast by the meQll,$oftool weal"c口20配一the life ofpunchfor normoluse beforesharpening to restore its ongincashape.Keywords:Die;Stamping;Influence1引言当前由于产品变化更新较快,同时,大部分技术人员为了保证模具的寿命对模具的选材尽量沿着高端走,模具寿命的问题在冲压类模具企业没有显得特别突出,因而模具寿命在许多冲压类模具企业并没有受到太大的重视。
对于产品批量要求大、模具寿命要求长时,大多生产商为了保证其正常生产节奏,要么采用快换凸模的模具结构形式,要么干脆备用—套模具。
由于对模具没有合理的寿命估算,模具的成本在这个生产过程中就显得特别高。
影响模具寿命的因素有很多,模具材料、模具润滑形式、板材性能、零件表面粗糙度、模具材料热处理工艺、模具几何形状、冲裁间隙都是不可忽略的因素,但实际生产中,板材因产品限定无法更改的,而模具一旦加工出来,就只有润滑形式、模具装配间隙是可调的。
相对于成型类模具,润滑形式对冲裁类模具寿命影响不如间隙影响大,间隙因素为越来越多的技术人员所重视。
目前参考文献关于间隙对模具寿命的影响大多是定性分析,能够定量分析并给出工程技术人员以直接指导的并不多见。
模型建立,如图1所示,一轴对称冲裁模型,为了防止板料在冲压过程中发生翘曲影响冲件平整度,一般需要配置压料板。
算例凸凹模选材均为AISI—D2COLD,凹模内孔直径D凹为lOmm,单边间隙为O.1mm,凸模外径D凸为9.8mm。
为防止刚度矩阵的奇异,凸凹模圆角分别取0.05、0.08ram。
板料为不锈钢AISI304,厚度lmm,杨氏模量E为2.IE5MPa,屈服极限以为365MPa,泊松比7为0.29,为统一计算比较,所有速度按lmm/s(主要便于观察各个细分的计算步,同时防止过大的速度导致板料工具相互嵌入过大,网格重新划分的工作量过大111)。
金属剪切摩擦按o.08计。
2冲裁模间隙对模具寿命的影响在冲裁模的设计中,凸凹模间隙的合理选取,是保证模具正常工作、提高冲片质量、延长模具寿命的一个关键因素。
理想的间隙应该是板料冲裁断裂时,凸凹模刃口边所产生的裂纹在一条直线上,否则冲片边缘将出现不允许的毛刺,使得刃口粘结严重,磨损加快,进而影响模具的寿命。
所以,如何选取合理的凸凹模间隙,是模具设计时不容忽视的问题。
通常情况下,模具设计中间隙一般都按设计手册推荐的间隙值选取。
例如,我厂电机定、转子片为0. 5mm 的硅钢片, 手册推荐的间隙为0 . 0 4 ~0. 07mm ,约为材料厚度的8 %~14 %。
按照这个间隙,冲出的定、转子片毛刺虽能控制在规定范围内。
但由于间隙偏小,使得凸模与被冲的孔之间、凹模与落料之间的摩擦严重,造成凸模和凹模侧壁产生粘结,卸料力增大,影响冲片断面的质量,刃口容易变钝,冲片易出毛刺,且毛刺增长过快,甚至发生凹模胀裂现象,致使模具寿命下降。
且取小间隙时,由于弹性回跳作用,落料件尺寸大于凹模,冲出的孔径小于凸模,从而造成冲片的尺寸精度出现误差。
为提高冲片质量,延长模具寿命,根据国内外资料信息,在实践中对模具间隙做了试验摸索,证明放大间隙是非常有效的。
经过多次对0. 5mm 厚硅钢片冲裁的试验,发现间隙值在材料厚度的20 %左右范围内,即间隙值为0. 09~0. 11mm 最为合适。
采用这个间隙,可以获得如下效果:(1) 提高了冲片质量。
刃口锋利时毛刺小,冲裁过程中毛刺增长缓慢。
(2) 冲片表面平整度大大改善,特别是相邻孔之间。
(3) 凸凹模侧壁无粘结,减小了卸料力。
(4) 延长了模具寿命。
刃磨一次可以保证较的冲次,从而减少刃磨次数,提高了生产效率。
放大间隙还可降低模具制造的费用。
例如,对于冲裁1. 5mm 厚O8F 冷板,手册推荐的间隙值为0. 15~0. 18mm ,用线切割加工凸凹模无法保证模具的间隙(钼丝直径为0. 12mm) ,因此不得不将凸凹模分别切割,结果既费材料又费工时。
当选择较大的间隙时(按料厚的20 %左右) ,则问题迎刃而解,可顺利地一次切割出凸凹模,从而降低模具制造的费用,冲片质量也可保证。
实践证明,合理地放大间隙,可使冲裁质量得到有效的保证,且模具寿命能提高2~3 倍3模具磨损寿命分析在模具的使用过程中,板料与模具之间有较大的摩擦,凸模底部、侧壁;凹模顶部、侧壁都有较大的磨损。
本文凸、凹模的材料均选用从,并且凸模热处理硬度预设HRC56,凹模热处理硬度设为HRC60,板料为不锈钢304,硬度HRCl6。
磨损模型选用Arcard,以ALE(Arbitrary【丑grangeEuler)算法%如图8所示,是料厚为lmm,凸模圆角OD5mm,凹模圆角0.08ram,凸凹模间隙为0.02ram的条件下,冲裁断裂后凸、凹模的整个磨损分布。
分析得出模具底部相对于圆弧侧壁磨损的区域要小,凹模相对凸模来讲磨损区域和磨损程度要小。
根据图8的算例结果,假设模具的公差要求为(m02)mm,就可以算出该凸模的磨损使用寿命,图示最大单次冲裁磨损量是6.25x10-‰,可冲裁次数为0.02/(6.25xlO。
6),即该凸模的使用寿命约为3200次冲裁。
为了使凸模能够得到最初的形状需要刃磨,最小刃磨量可根据最大磨损量的位置和区域大小测量出来。
(本例为0.22)。
根据这种方法,将不同的间隙条件下求得的最大磨损量、磨损区域大小、距离凸模底部的距离等参数,如表l所示。
根据表上的数据町以得出:随着间隙增大,最大磨损量是逐渐减小的,但在间隙超出一定范围之后(本例是0.12)磨损量又会变大,然后逐渐减小。
磨损区域较集中,中心部位多集中在距底部(0.15--0.25)mm的范围。
如图9所示,是根据表2的结果,假设凸模的最大磨损量只有0.02ram时得出的间隙与寿命的关系。
从图中可以看出,随着间隙变大,模具的寿命相应提高,在(o.1-0.12)ram(料厚lmm)寿命较高,(0.12-O.15)mm的间隙寿命急剧下降,然后间隙再增大寿命逐渐提高,但变化比较平缓。
与图9相对应的刃磨量在图10上反映出来,其基本走势与磨损寿命关系图的走势比较一致。
亦即寿命长的凸模为了得到原始形状,相应的刃磨长度也会变大。
较特殊的情况是在(0.15--O.20)mm间隙时。
随着间隙变大,寿命增加,但所需刃磨长度并没有明显增加。
文章不涉及疲劳裂纹出现的刃磨,如果出现疲劳裂纹,为了能够得到合理的冲裁凸模形状,需要及时刃模,以消除裂纹急剧扩展导致凸模报废阿。
4结论间隙是冲裁模具设计、制造过程中一个很重要的因素,长久以来,我国工程技术人员沿用原来苏联的技术标准体系,模具制造间隙整体偏小,模具寿命难以达到理想状态。
本文根据工厂常用的模具钢材D:进行了间隙、变形、寿命相关的分析。
根据分析结果可以得出:(1)间隙随着从零逐渐变大到一定范围,凸模的冲裁力逐渐变小。
由于在小间隙状态下一般采用精冲工艺,压板一般采用齿圈压板,本文为对比试验所有压板均用平面压板。
而且均以压板接触材料为初始边界条件,压板不再施加外力,便于在同一条件下比较。
事实上,压板上所使用的压料力对板料的冲裁是有影响的,如本文的例子在间隙达到0.3mm以上时,凸模所需的冲裁力会变大,而不再继续变小,由于间隙较大,变形的初期更像是拉延变形的过程,若压料力不够大,部分材料会沿着凹模口流入凹模,使得塑性变形的区域变得较大,整体显示出凸模的冲裁力加大。
但在实际模具制造过程中,如此大的间隙已没有实际工程价值。
(2)间隙变大在一定范围内会使模具磨损寿命提高(本文算例为小于12%料厚),超出该范围后寿命会显着降低,然后间隙再变大时(算例大于15%料厚),寿命变化不是特别明显;相应的刃磨量趋势与寿命变化趋势基本一致。
模具的总寿命是在若干次的刃磨后总体表达出来的。
只给出了每次刃磨模具能够使用的寿命。
(3)对于高速冲裁,其真实环境的模拟更为重要,对于小间隙模具在冲裁次数达到2000次/分时,冲头有时温度可达到300。
C以上,此时磨损寿命会比常温更低。
同时在高速冲裁的条件下,凸模与板料刚接触的动态响应产生极大的瞬间冲压力,会造成模具的疲劳破坏,有时比模具磨损寿命更低,所以高速冲裁这个因素不能忽略。
关于这方面的内容留待后续研究,本文不涉及。
参考文献1方刚,曾攀.金属板料冲裁过程的有限元模拟金属学报.2001,137(6) 2贾建军,彭颖红等.精冲过程的韧性断裂上海交通大学学报,1999,33(2)3 DEFORMu8ermanual.19854ASMHandbookCommittee ASM metal shand book[M],roll4P1016 ASMi nternational.19935 Brokken.IXrk.Numerical modeling of ductile fracture in blanking[M].TechnischeUniversiteitEindboverl.Universiteitsdlukkerij TUEindhoven,Eindhoven,TheNetherlands,19996ViggoTvergaard Effectofundedoadsoroverloads in fatigue crack growth by crack--tipblunting Engineering Fracture Meehanics[J],2006,73:869~879。