光学外观标准
外观检测方法
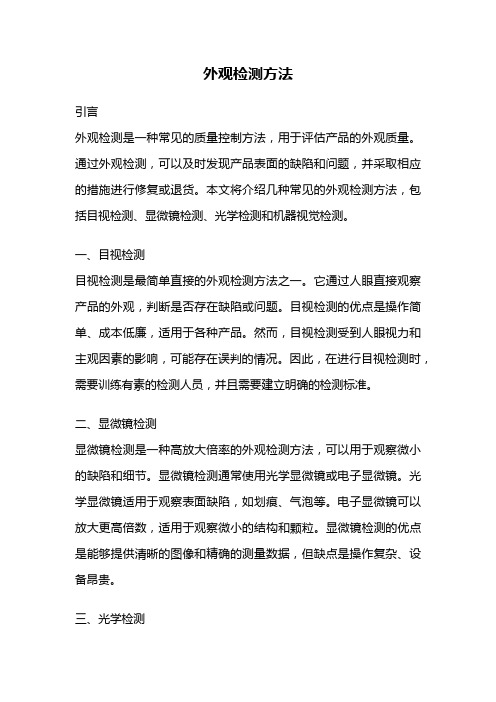
外观检测方法引言外观检测是一种常见的质量控制方法,用于评估产品的外观质量。
通过外观检测,可以及时发现产品表面的缺陷和问题,并采取相应的措施进行修复或退货。
本文将介绍几种常见的外观检测方法,包括目视检测、显微镜检测、光学检测和机器视觉检测。
一、目视检测目视检测是最简单直接的外观检测方法之一。
它通过人眼直接观察产品的外观,判断是否存在缺陷或问题。
目视检测的优点是操作简单、成本低廉,适用于各种产品。
然而,目视检测受到人眼视力和主观因素的影响,可能存在误判的情况。
因此,在进行目视检测时,需要训练有素的检测人员,并且需要建立明确的检测标准。
二、显微镜检测显微镜检测是一种高放大倍率的外观检测方法,可以用于观察微小的缺陷和细节。
显微镜检测通常使用光学显微镜或电子显微镜。
光学显微镜适用于观察表面缺陷,如划痕、气泡等。
电子显微镜可以放大更高倍数,适用于观察微小的结构和颗粒。
显微镜检测的优点是能够提供清晰的图像和精确的测量数据,但缺点是操作复杂、设备昂贵。
三、光学检测光学检测是一种利用光学原理检测产品外观的方法。
常用的光学检测方法包括透射光学检测和反射光学检测。
透射光学检测适用于透明或半透明材料的检测,如玻璃、塑料等。
反射光学检测适用于不透明材料的检测,如金属、陶瓷等。
光学检测的优点是非接触式检测,可以快速扫描大面积的产品外观,但受到光线和环境的影响,可能存在误判的情况。
四、机器视觉检测机器视觉检测是一种利用计算机视觉技术进行外观检测的方法。
它通过摄像机和图像处理算法,对产品的图像进行分析和判断。
机器视觉检测可以实现自动化和高速检测,减少了人为因素的干扰。
它适用于各种产品的外观检测,如电子产品、汽车零部件等。
机器视觉检测的缺点是设备和算法的复杂性,需要专业知识和技术支持。
结论外观检测是一种重要的质量控制方法,可以帮助企业及时发现和解决产品外观质量问题。
不同的外观检测方法具有各自的优缺点,可以根据产品特性和要求选择适合的方法。
光学偏光镜检验标准
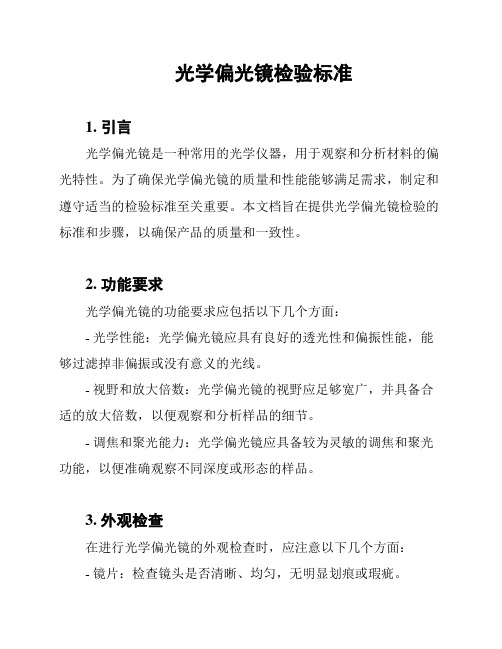
光学偏光镜检验标准1. 引言光学偏光镜是一种常用的光学仪器,用于观察和分析材料的偏光特性。
为了确保光学偏光镜的质量和性能能够满足需求,制定和遵守适当的检验标准至关重要。
本文档旨在提供光学偏光镜检验的标准和步骤,以确保产品的质量和一致性。
2. 功能要求光学偏光镜的功能要求应包括以下几个方面:- 光学性能:光学偏光镜应具有良好的透光性和偏振性能,能够过滤掉非偏振或没有意义的光线。
- 视野和放大倍数:光学偏光镜的视野应足够宽广,并具备合适的放大倍数,以便观察和分析样品的细节。
- 调焦和聚光能力:光学偏光镜应具备较为灵敏的调焦和聚光功能,以便准确观察不同深度或形态的样品。
3. 外观检查在进行光学偏光镜的外观检查时,应注意以下几个方面:- 镜片:检查镜头是否清晰、均匀,无明显划痕或瑕疵。
- 外壳:检查外壳是否完整、无损伤,并确保各个连接点的紧固度。
- 调焦轮和聚光轮:检查调焦轮和聚光轮的灵敏度和平稳性,确保能够正常工作。
4. 光学性能检验光学性能是光学偏光镜检验中最重要的方面之一。
以下是对光学性能的要求和检验方法:- 透光性:使用标准透光度计或比色计,对光学偏光镜的透光性进行测量。
透光度值应在规定范围内。
- 偏振性能:使用线偏光器产生偏振光,并通过光学偏光镜观察偏振光的效果。
偏振光的通透性和过滤效果应符合要求。
5. 视野和放大倍数检验视野和放大倍数是评价光学偏光镜观察效果的重要指标。
以下是对视野和放大倍数的检验要求:- 视野:使用标准目标物进行观察,测量出视野的直径。
视野直径应满足标准要求。
- 放大倍数:使用标准放大倍数标样,通过测量样品物体和镜筒的比例关系,计算出放大倍数。
放大倍数应符合标准要求。
6. 调焦和聚光能力检验调焦和聚光能力是光学偏光镜在不同观察条件下的重要性能之一。
以下是对调焦和聚光能力的检验方法:- 调焦能力:使用标准样品,在不同焦距下进行观察,记录调焦轮的操作灵敏度和观察效果。
- 聚光能力:使用标准聚光目标物,调整聚光轮进行观察,记录聚光的灵敏度和聚焦效果。
光学镜片表面外观检测标准

光学镜片表面外观检测标准您的光学工厂一.定义:表面缺陷标准:依据美国军用标准MIL-O-13830B用两组数字表示表面缺陷大小。
例如40/20(或40-20)前者限制划痕大小,后者限制麻点大小。
道子、亮路、伤、擦痕都统称为划痕。
斑点、坑点、点子都称为麻点。
规定长与宽的比大于4:1的为划痕;长与宽的比小于4:1的为麻点。
当元件的不同区域表面光洁度要求不一样时,等效直径的计算以区域进行:表面质量要求高的内区域其等效直径以内区域为准(如有效孔径的区域),表面质量要求低的外区域计算的是整体元件的等效直径。
如下图元件表面质量要求不同,则在判定A区是否符合要求时,应取内圆直径进行计算。
而B区则取整个元件的圆直径划痕:以美国军用标准《MIL-O-13830》的表面质量划痕样板作为各级数划痕的比对标准。
(注意:美军标未指明划痕的计量单位也即未确定划痕的宽度和深度,只能以实际观察样版为标准。
)这里的划痕级数就是通常的划痕号数,标准样版有10#、20#、40#、60#、80# 5个级。
1.当元件的划痕级数超过表面质量要求的划痕级数时,元件不合格。
例如:元件的表面质量要求为60—40,则代表元件的划痕必须≤60#,如果元件有>60#的划痕,则元件不合格。
2.当元件的划痕级数未超过表面质量要求的级数,但元件存在最大划痕时,所有最大划痕的长度之和应不超过元件直径的1/4。
例如:有一长30mm宽10mm的元件,元件的表面质量要求为60—40,有2条60#长为3 mm划痕。
它的等效直径为20mm1/4D为1/4×20=5mm最大划痕的长度和为:3mm+3mm=6mm6mm>5mm元件最大划伤痕的长度和超过元件直径的1/4。
所以元件不合格。
下图是看到的样品(图片是放大的不是实际尺寸)图中的划痕为20#,且长度>1/4D。
对于表面质量要求20-10该产品不合格。
但本次样品未提出表面质量要求,而是要大家自已决定光洁度等级。
玻璃镜片测试规范
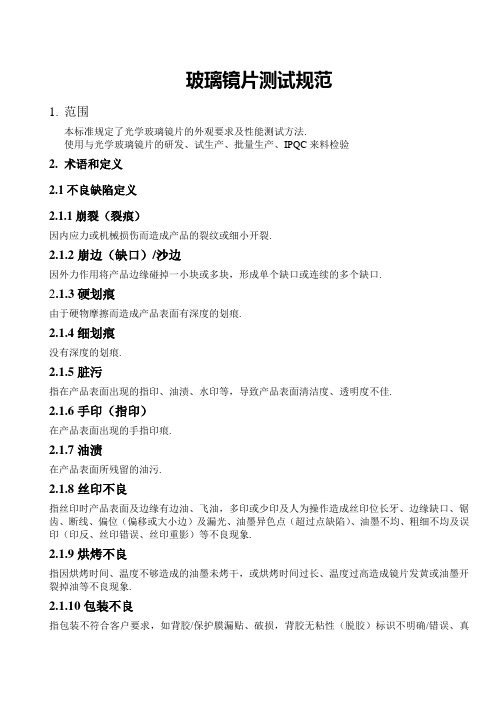
玻璃镜片测试规范1.范围本标准规定了光学玻璃镜片的外观要求及性能测试方法.使用与光学玻璃镜片的研发、试生产、批量生产、IPQC来料检验2.术语和定义2.1不良缺陷定义2.1.1崩裂(裂痕)因内应力或机械损伤而造成产品的裂纹或细小开裂.2.1.2崩边(缺口)/沙边因外力作用将产品边缘碰掉一小块或多块,形成单个缺口或连续的多个缺口.2.1.3硬划痕由于硬物摩擦而造成产品表面有深度的划痕.2.1.4细划痕没有深度的划痕.2.1.5脏污指在产品表面出现的指印、油渍、水印等,导致产品表面清洁度、透明度不佳.2.1.6手印(指印)在产品表面出现的手指印痕.2.1.7油渍在产品表面所残留的油污.2.1.8丝印不良指丝印时产品表面及边缘有边油、飞油,多印或少印及人为操作造成丝印位长牙、边缘缺口、锯齿、断线、偏位(偏移或大小边)及漏光、油墨异色点(超过点缺陷)、油墨不均、粗细不均及误印(印反、丝印错误、丝印重影)等不良现象.2.1.9烘烤不良指因烘烤时间、温度不够造成的油墨未烤干,或烘烤时间过长、温度过高造成镜片发黄或油墨开裂掉油等不良现象.2.1.10包装不良指包装不符合客户要求,如背胶/保护膜漏贴、破损,背胶无粘性(脱胶)标识不明确/错误、真空包装漏气等.2.2不合格的分类按程度不同分为A类不合格、B类不合格、C类不合格三类.2.2.1 A类不合格易导致不安全因素的项目以及导致其基本功能失效的项目.1)镜片破碎2)性能测试不良:抗冲击、附着力、装配.3)尺寸不符:与客户图纸要求不符,影响装配功能.2.2.2 B类不合格可能导致功能失误或降低原有使用功能的项目.外观检测项目内容:如崩边、崩裂、细硬划痕、点缺陷、脏污、烘烤不良、丝印不良、漏光、透光性、色泽、倒边不符要求等.2.2.3C类不合格指对产品的使用性能没有影响或只有轻微影响的项目.1)包装方式不符合客户要求,包装内有异物等.2)标识不全或不符.3)有漏装、多装或错装产品.4)检验记录填写不全或有误.2.3不合格品的定义按不合格类型分为A类不合格品、B类不合格品、C类不合格品.2.3.1 A类不合格品有一个或一个以上A类不合格品,也可能还有B类和C类不合格的单位产品.2.3.2 B类不合格品有一个或一个以上的B类不合格,也可能还有C类不合格的单位产品,但不包含A类不合格的单位产品.2.3.3C类不合格品有一个或一个以上的C类不合格,但不包含A类和B类不合格的单位产品2.4缺陷代码对照表缺陷代码对照表见表1.表1缺陷代码对照表3.外观检验条件及环境的要求.a)距离:人眼与被测无表面的距离为200mm-300mm.b)时间:每片检查时间不超过5-10s(10s内检验不出来的缺陷可以不计)c)检验方法:目视,且监视面与桌面成45°;上下左右转动15°,(透明清晰度、漏光须对光检测,即与灯光呈平行目视检测)d)照明:35w冷白荧光灯,光源距被测物表面400mm-500mm(照度达800Lux-1200Lux).4.检验操作注意事项a)操作人员工作前必须洁净双手,严格执行检验标准,不能误判、漏检.b)产品必须轻拿轻放,按指定的位置放置,标识清楚,随时注意防潮防尘遮盖(无论良品或不良品)c)工作台面必须随时保持干净、整洁.必须以合格的产品转序.5.抽样检验规则1)正常检验批量检查采用GB 2828-87中的一次抽样方案,如批量总数为150片,则样本数位20片.批合格质量水平(AQL)如下所示:AQL取值:— A类不合格品为0.65(性能/尺寸样本数以总样本数的值采用特殊检验水平S-3级正常一次抽样方案)—B类不合格品为1.0(样本数以批量数取样本值,一般检验水平Ⅱ级正常一次抽检方案)—C类不合格品为0.65(样本数以抽样包装箱、袋数取样本值,一般检验水平Ⅱ级正常一次抽检方案)2)加严检验当正常检验时,在连续5批中有两批检验不合格,则从下批起转到加严检验(母体数是150片,抽样32片)3)从加严检验转为正常检验当进行加严检验时,若连续5批检验合格时,则从下批起转到正常检验。
智能眼镜外观检测标准
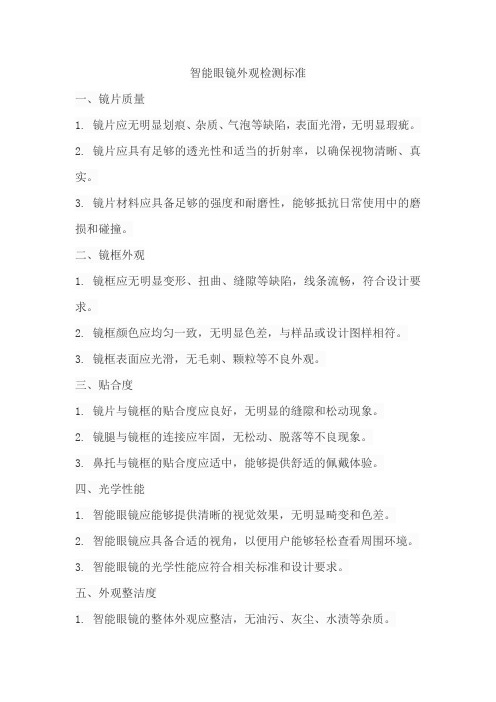
智能眼镜外观检测标准一、镜片质量1. 镜片应无明显划痕、杂质、气泡等缺陷,表面光滑,无明显瑕疵。
2. 镜片应具有足够的透光性和适当的折射率,以确保视物清晰、真实。
3. 镜片材料应具备足够的强度和耐磨性,能够抵抗日常使用中的磨损和碰撞。
二、镜框外观1. 镜框应无明显变形、扭曲、缝隙等缺陷,线条流畅,符合设计要求。
2. 镜框颜色应均匀一致,无明显色差,与样品或设计图样相符。
3. 镜框表面应光滑,无毛刺、颗粒等不良外观。
三、贴合度1. 镜片与镜框的贴合度应良好,无明显的缝隙和松动现象。
2. 镜腿与镜框的连接应牢固,无松动、脱落等不良现象。
3. 鼻托与镜框的贴合度应适中,能够提供舒适的佩戴体验。
四、光学性能1. 智能眼镜应能够提供清晰的视觉效果,无明显畸变和色差。
2. 智能眼镜应具备合适的视角,以便用户能够轻松查看周围环境。
3. 智能眼镜的光学性能应符合相关标准和设计要求。
五、外观整洁度1. 智能眼镜的整体外观应整洁,无油污、灰尘、水渍等杂质。
2. 镜片和镜框表面应无残留物和指纹等痕迹,保持干净整洁。
3. 智能眼镜的各个部件应保持干净整洁,无油污和其他杂质。
六、结构稳定性1. 智能眼镜的结构应稳定,能够在日常使用中保持固定的位置和角度。
2. 镜腿和鼻托的设计应符合人体工程学原理,能够提供舒适的佩戴体验。
3. 智能眼镜的结构设计应能够抵抗一定的冲击和振动,具备足够的耐用性。
七、尺寸精度1. 智能眼镜的尺寸精度应符合设计要求,各个部件的尺寸误差应在允许范围内。
2. 智能眼镜的整体尺寸应符合标准规格,便于用户佩戴和使用。
光学镜片外观检作业规范
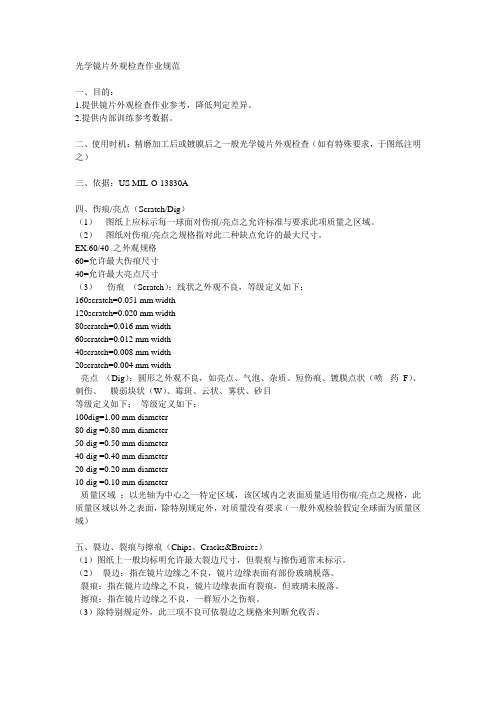
光学镜片外观检查作业规范一、目的:1.提供镜片外观检查作业参考,降低判定差异。
2.提供内部训练参考数据。
二、使用时机:精磨加工后或镀膜后之一般光学镜片外观检查(如有特殊要求,于图纸注明之)三、依据:US MIL-O-13830A四、伤痕/亮点(Scratch/Dig)(1)图纸上应标示每一球面对伤痕/亮点之允许标准与要求此项质量之区域。
(2)图纸对伤痕/亮点之规格指对此二种缺点允许的最大尺寸。
EX.60/40 之外观规格60=允许最大伤痕尺寸40=允许最大亮点尺寸(3)--伤痕(Scratch):线状之外观不良,等级定义如下:160scratch=0.051 mm width120scratch=0.020 mm width80scratch=0.016 mm width60scratch=0.012 mm width40scratch=0.008 mm width20scratch=0.004 mm width--亮点(Dig):圆形之外观不良,如亮点、气泡、杂质、短伤痕、镀膜点状(喷-药F)、刺伤、膜弱块状(W)、霉斑、云状、雾状、砂目等级定义如下:等级定义如下:100dig=1.00 mm diameter80 dig =0.80 mm diameter50 dig =0.50 mm diameter40 dig =0.40 mm diameter20 dig =0.20 mm diameter10 dig =0.10 mm diameter--质量区域:以光轴为中心之一特定区域,该区域内之表面质量适用伤痕/亮点之规格,此质量区域以外之表面,除特别规定外,对质量没有要求(一般外观检验假定全球面为质量区域)五、裂边、裂痕与擦痕(Chips、Cracks&Bruises)(1)图纸上一般均标明允许最大裂边尺寸,但裂痕与擦伤通常未标示。
(2)--裂边:指在镜片边缘之不良,镜片边缘表面有部份玻璃脱落。
iso-10110中文国际光学制图标准.pdf
国际10110光学制图标准的执行——适用于国家点火装置此文件为国际讨论会第44届年会之光学科学、工程学、仪器学会专供材料1999年7月国际10110光学制图标准的执行——适用于国家点火装置摘要1996年,国家点火装置(NIF)工程决定选取ISO-10110标准作为NIF光学制图标准。
7000个大型NIF光学器件和20000多个小型NIF光学器件都将依照ISO-10110标准生产制造。
ISO-10110标准满足NIF光学规范中的所有要求。
它为光学工程师统计、交流光学规范提供了平台。
当没有单独的制图标准能够满足高能量激光系统所需时,ISO-10110标准(及详细备注)解决了这一问题,它成功的将国际制图标准应用到了NIF激光系统当中。
本文将简述利弗莫尔国家实验室的研究结果和ISO-10110制图标准的实施,并列举NIF光学制图的某些案例,以及应用ISO-10110标准的正反意见。
本文重点是NIF光学器件的表面缺陷规格,称为5/。
1. 序言1996年,经172个 ISO技术委员会和1个分技术委员会批准并颁布了ISO-10110文件,文件第1-13章的总标题为“光学和光学仪器——适用于光学元件和光学系统制图”。
ISO-10110标准具体说明了设计情况,以及技术图纸(生产制造和检测中的技术图纸)中对光学元件的功能要求。
此标准已被国际光学供应社团所广泛认可,同时也引起了越来越多美国商家的注意。
在NIF早期作业的准备过程中,采购7000个大型光学器件(孔径尺寸≥40cm)和20000多个小型光学器件(孔径尺寸≤15cm),这将大大超过未来几年的采购量。
在NIF工程未来30年的运作中,美国光学制造业将继续提供返修和更换的器件。
我们试图购买能够满足NIF高端技术、生产安排及成本需求的光学器件。
为研发成功,我们为每个光学器件寻找合适的标准,以便可以向光学供应商清晰的表述要求。
三年半前,当着手为NIF光学器件制定规格时,我们需要一份能够满足光学规范和制图需要的标准。
光学外观标准
50/2*0.1; 2表示膜层允许有2个表面瑕疵等级数为0.1的缺陷
0.1表示表面质量瑕疵等级级数
G表示膜层灰斑瑕疵的符号
G2*0.25; 2表示膜层瑕疵允许的个数
0.25表示膜层瑕疵的等级级数
C表示膜层色斑瑕疵的符号
C2*0.25 2表示膜层瑕疵允许的个数
0.25表示膜层瑕疵的等级级数
表示镜片表面允许有2个宽度为 0.004mm划伤,长度不限.可用等面积 折算成小划痕,保证总面积不变.
光学零件外观标准总结
1 ISO 10110外观标准解读
1.1 ISO 10110标准中外观要求示例:
例:5/2*0.1;C2*1.6;L1*0.01;E0.3
5/表示表面质量瑕疵的符号
5/2*0.1;
2表示外观允许有2个表面瑕疵等级数为0.1的缺陷
表示镜片表面最大允许有2个瑕疵 等级为0.1的缺陷
4
2.5
1.6
1
6/12
2 DIN 3140外观标准解读
2.1 德国标准DIN3140中外观标准解读
例:5/2*0.1;K2*0.004;R0.1 50/2*0.1;G2*0.25;C2*0.25
5/表示非镀膜表面质量瑕疵要求的符号 5/2*0.1; 2表示外观允许有2个表面瑕疵等级数为0.1的缺陷
透过反射可以看见的东西如果轮廓清晰可见的话ng其他参照限度样本纹理歪斜材料不良透过目视可见不可其他参照限度样本此外针对没有包含在以上各项目中的不足点或者是判断不明的东西在协议的基础上放置限度样品来自顾客对合格品德承认是由必要的对于企业标准请按所述要求判定不建议根据等面积法做转化因为其中由最大尺寸限制故转化后不能满足原标准要求
要求检测它的散射。 以上要求均针对通光区域,通光区域之外表面质量应为80-50,除非另有要求。
光学外观标准
3 GB 1185-89
注:外观表面质量等级级数和标准ISO 10110中相同; 拆分方式与标准ISO 10110相同。
13/12
其他标准
4 各标准之间的转换
1.2 1.1 ,即80-50外观,口径20mm转化为ISO10110-7标准后为1*1.1。
注:以上面积计算中,麻点的几何形状为圆形,擦痕为长方形!
光学零件外观标准总结
1 ISO 10110外观标准解读
1.1 ISO 10110标准中外观要求示例:
2/12
1 ISO 10110外观标准解读
1.2 外观对比限度板
使用方法:1)室内光; 2)检验背景为黑色挡板;3)检验光源为24、27W日光灯;4)放置 在灯下反射观察;5)若检验镜片时有使用放大镜则观察限度板时也须使用放大镜; 6)限度板上的线条为该限度要求可允许的最大缺陷,超过此限度为不良.
如Ⅳ级外观,D。=20mm,总面积=0.06284*20=1.2568mm²,转换为ISO10110 为: 1*1.1。
若D。=20mm,回想美国军标中80-50转化为1*1.1,所以GBⅣ级外观对应美国军 标为80-50。
结束 谢谢!
此课件下载可自行编辑修改,此课件供参考! 部分内容来源于网络,如有侵权请与我联系删除!
8/12
3 MIL美国军标中外观解读
美国军标中对光学零件表面质量说明及可接受缺陷规定用"擦痕"、"麻点"说明。擦 痕和麻点用两个代表其限制尺寸的号数来标记,第一个代号是擦痕号,第二个代号是 麻点号。
擦痕指相对长的缺陷,一般长宽比在20:1左右,如:擦痕、划伤、划丝。 麻点指点状缺陷,一般为远的,如麻点、麻坑包含物。
光学透镜检验标准
光学透镜检验标准一、外观检查1.透镜表面应光滑、平整,无明显的划痕、凸起、凹陷等缺陷。
2.透镜边缘应圆润,无锋利的边角,避免对眼睛造成伤害。
3.透镜表面的颜色应均匀一致,无色差、无褪色等现象。
4.透镜的光学表面应无灰尘、水滴、油污等杂质,保证光线的透过效果。
二、尺寸测量1.透镜的尺寸应符合设计要求,测量时应使用精确的量具进行测量。
2.透镜的直径、厚度等尺寸应符合规格要求,保证透镜的装配和使用效果。
3.透镜的孔径、孔距等尺寸应符合设计要求,保证透镜的固定和连接效果。
三、透镜材料检查1.透镜的材料应符合设计要求,选用高透光率、高硬度的光学材料。
2.透镜的材料应具有稳定性,能够抵抗环境的影响,保证透镜的质量和性能。
3.透镜的材料应具有一致性,避免因材料差异导致光学性能的变化。
四、表面质量检测1.透镜表面应无裂纹、气泡、麻点等表面缺陷,保证光线的透过效果。
2.透镜表面应无明显的划痕、磨损等损伤,保证使用的安全性和美观度。
3.透镜表面的粗糙度应符合设计要求,避免影响光学性能和外观质量。
五、光学性能测试1.透镜的光学性能应符合设计要求,包括焦距、折射率、透光率等参数。
2.透镜在规定的光源下应能正常工作,保证光线的聚焦和分散效果。
3.透镜应对光线有较好的会聚能力,保证光线的透过效果和图像的清晰度。
六、耐候性测试1.透镜应能够在不同的环境条件下稳定工作,包括高温、低温、潮湿、干燥等环境。
2.透镜应能够抵抗环境的影响,保证光学性能和使用寿命。
3.透镜在耐候性测试中的表现应符合设计要求,保证使用的可靠性和稳定性。
七、机械强度测试1.透镜应具有一定的抗冲击能力,能够在一定程度的冲击下不发生破裂或变形。
2.透镜的固定方式应牢固可靠,能够保证透镜在使用中的稳定性和安全性。
3.透镜的机械强度应符合设计要求,保证使用的耐久性和稳定性。
八、防尘防水测试1.透镜应具有较好的防尘防水性能,能够在一定的尘埃和水分环境下正常工作。
2.透镜的密封性能应符合设计要求,保证使用的可靠性和安全性。
- 1、下载文档前请自行甄别文档内容的完整性,平台不提供额外的编辑、内容补充、找答案等附加服务。
- 2、"仅部分预览"的文档,不可在线预览部分如存在完整性等问题,可反馈申请退款(可完整预览的文档不适用该条件!)。
- 3、如文档侵犯您的权益,请联系客服反馈,我们会尽快为您处理(人工客服工作时间:9:00-18:30)。