生产线平衡(实例版)分析
生产线平衡(实例版)

2﹑生产线平衡的实施
2.1.2工时测量
1)工具:
时间
山积表
马表
❖观测板、铅笔
时间记录表、计算器
工
山积表
站
山积表:
将各分解动作时间,以迭加式直方图表现的一种 研究作业时间结构的手法.
2﹑生产线平衡的实施
2)测时方式
B
A
净时间量测
开始
(0) a
无需计算 的时间
8
6
4
2
0
S1 S2 S3 S4 S5 S6 S7 S8 S9 S10 S11 S12 S17 S18 S19
理想平衡率
平衡率100%代表﹕ 1.工站之间无等待,前后产能一致 2.工站节拍相同﹐动作量相同(动
作量是指工站中各种必要动素 的时间总量) 3.平衡损失时间为零 4.设计效率最大化 5.前后流程的设计可以更完善
t1 S1-1S1-2 S1-1S1-2
当S1-1不需等 S1-2就能开始,S1 工站时间為﹕ t3+S1-1提前开 始的时间(t4-t3)
工站
3.平衡的步骤
Steps 5:建立新的仿真流程 新的FLOW CHART/ SOP
Steps 6:实施新的仿真流程 改善后时间测量 ❖ 改善后山积表制作
Steps4:山积表平衡
联合操作的工站时间(S1-1>S1-2)
时间
t4 t3 t2
S1标准时间 為﹕t2+t3;S1工站时 间为﹕t4
t1 S1-1 S1-2 S1-1 S1-2
工站
3.平衡的步骤
Steps4:山积表平衡
S1工站时间=?
?
生产线平衡率实例

Nt
=
11.35 mins/台 4.2 mins/台
=
2.702,
or 3
(5)根据排程排产
2
1
1
A
B
G
1.4
H
C
D
E
F
3.25
1.2
.5
1
任务 A C D B E F G H
工位 1
工位2
后续任务 6 4 3 2 2 1 1 0
时间 (Mins) 2
3.25 1.2 1 0.5 1 1 1.4
工位 3
流水线平衡
1.4 H
F 1
任务
A C D B E F G H
工位2
后续任务
6 4 3 2 2 1 1 0
时间 (Mins) 2
3.25 1.2 1 0.5 1 1 1.4
工位 3
C (4.2-3.25)=0.95
Idle=0.2
流水线平衡
2
1
1
A
B
G
C
D
E
3.25
1.2
.5
工位 1
A (4.2-2=2.2) B (2.2-1=1.2) G (1.2-1= 0.2)
Idle=0.2
Idle =0.95
2
1
1
A
B
G
C
D
E
3.25
1.2
.5
工位 1
A (4.2-2=2.2) B (2.2-1=1.2) G (1.2-1=0.2)
流水线平衡
1.4 H
F 1
任务 A C D B E F G H
工位2
后续任务 6 4 3 2 2 1 1 0
生产线平衡案例分析培训

生产线平衡案例分析培训引言在现代制造业中,生产线平衡是一个至关重要的概念。
通过合理的生产线平衡,可以提高生产效率、降低成本、优化资源利用等。
本文将通过分析一个生产线平衡案例,介绍生产线平衡的原理和方法,并探讨如何进行生产线平衡培训。
案例分析假设一个玩具生产厂家拥有一个生产线,负责生产玩具汽车。
该生产线由多个工作站组成,每个工作站负责一道具体的工序。
现有数据如下:•工作站1:个体组装,每小时可完成200辆玩具汽车的组装。
•工作站2:上色,每小时可完成150辆玩具汽车的上色。
•工作站3:质检,每小时可完成180辆玩具汽车的质检。
根据以上数据,可以计算出每个工作站的产能利用率,如下:•工作站1:200/200 = 100%•工作站2:150/200 = 75%•工作站3:180/200 = 90%从上述数据可以看出,工作站2的产能利用率较低,成为生产线上的瓶颈工序。
如果不及时解决这个问题,将会影响整个生产线的效率和产能。
生产线平衡原理和方法生产线平衡是指合理地安排生产线上各个工作站的工作量,使得各个工作站之间的产能相对平衡,解决瓶颈问题,提高生产效率。
生产线平衡的原理和方法主要包括以下几个方面:1. 识别瓶颈工序首先,需要通过数据分析或实地观察,明确生产线上的瓶颈工序。
瓶颈工序指的是生产能力较低,成为整个生产线效率的制约因素的工序。
在上述案例中,工作站2就是瓶颈工序。
2. 改善瓶颈工序针对瓶颈工序,可以考虑以下几种改善方法:•提高工作站的产能:通过增加设备数量、改进工艺或技术等方式,提高工作站的生产能力。
•减少工作站的工作量:通过优化生产流程,简化工序或调整工作站之间的任务划分,减少瓶颈工序的工作量。
在上述案例中,可以考虑增加上色工作站的设备数量或改善工艺,以提高生产效率。
3. 平衡工作站的工作量在解决瓶颈工序的同时,还需要平衡其他工作站的工作量,使得各个工作站的产能相对平衡。
平衡工作站工作量的方法包括:•调整任务划分:根据不同工作站的产能和工作特点,合理划分任务,避免工作站之间的工作量差距过大。
生产线平衡案例分析过程

生产线平衡案例分析过程1. 引言生产线平衡是一种优化生产过程的方法,旨在确保生产线上的工作站之间的工作负载均衡,以提高生产效率和产品质量。
本文将以一个实际案例为例,分析生产线平衡的过程。
2. 案例背景假设某公司生产手机,并且生产线上有三个关键工作站:组装、测试和包装。
每个工作站的工人数量不同,导致工作负载不均衡,组装工作站负责最多的工作量,而测试和包装工作站的工作负载较少。
3. 数据收集为了分析生产线平衡的问题,首先需要收集一些关键数据。
包括每个工作站的工作时间、工人数量以及每个工作站的工作量。
工作站工作时间(分钟)工人数量工作量(数量)组装工作站30 3 200测试工作站25 2 150包装工作站20 2 100通过收集这些数据,可以计算出每个工作站的单位时间工作量,即每分钟能完成的工作量。
根据上表数据,可以得出以下结果:•组装工作站的单位时间工作量为6.67件/分钟(200件/30分钟)•测试工作站的单位时间工作量为6件/分钟(150件/25分钟)•包装工作站的单位时间工作量为5件/分钟(100件/20分钟)4. 分析和优化通过计算每个工作站的单位时间工作量,可以判断哪个工作站是生产线上的瓶颈工作站。
在这个案例中,组装工作站的工作量最大,成为瓶颈,会导致生产线的工作负载不平衡。
为了平衡工作负载,可以采取以下优化措施:•调整工人数量:增加组装工作站的工人数量,以减轻其工作负荷。
•优化工作时间:分析工作时间,寻找减少生产时间的方法,例如改进工艺或引入自动化设备。
•转移工作量:将部分组装工作转移到其他工作站,以平衡各工作站的负载。
5. 优化结果评估经过优化措施的实施后,重新计算每个工作站的单位时间工作量,以评估结果。
工作站工作时间(分钟)工人数量工作量(数量)单位时间工作量(件/分钟)组装工作站30 4 200 5测试工作站25 2 150 6包装工作站20 2 100 5通过调整组装工作站的工人数量,将其增加到4人,重新计算单位时间工作量之后,可以看到组装和包装工作站的工作量现在已经达到了平衡,测试工作站的工作量仍然保持不变。
生产线平衡分析
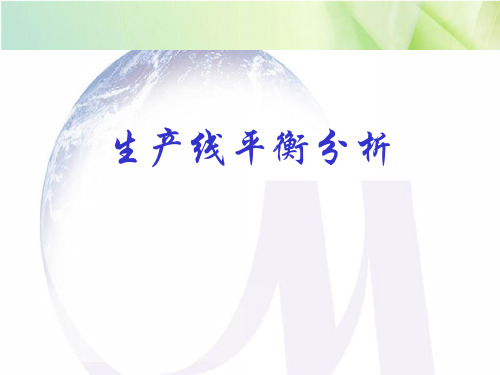
5.00
0.00
搬组搬运装运、蒸、上发倒线器片 插插输输入出管管 焊接一 焊接二
上输装出快管速焊螺接接母头三 检大漏
真空箱充氦氦检气 上输入回管收扎螺氦扎母气带
贴海棉 检查、上下卡线环
二九七.0三
生产线平衡效率=
×一00%=四八.三五%
三二.三三 × 一九
采取ECRS方法对生产线平衡性进行改善
谢谢,
A、对时间长的工序的改善方法:
a、分割作业,把一部分作业分配到时间短的工序中去; b、作业改善,缩短作业时间,如制作夹具、灵活运用工具等; c、作业机械化,提高机械的能力; d、替换技能水平更高的作业人员; e、增加作业员.
B、对时间短的工序的改善方法:
a、分割作业,把这一工程的作业分配到其它工程,省去这一工程; b、从作业时间长的工程拿一部作业过来; c、与其它时间短的工程结合,省去一工程; d、分配两个从以上的工程,尽量让一个人做.
1 装顶盖/贴商标
1
2
3
4
5
合计 平均
读 时间 读 时间 读 时间 读 时间 读 时间
10.9
9.0
9.3
10.1
9.2 48.4 9.7
2
贴生产日期标贴、贴铭牌、注意标 贴
15.5
13.4
14.9
14.0
15.2 72.9 14.6
工
3 装阀母(2个)
位
4 装堵母(3个)
时
间
5 紧固顶盖后
分 6 紧固顶盖前
(4) 插输出管
(2)组后装蒸前发、器(2) 折弯机
氦气 回收
氦质 检电
品放
道
置区
(1)
设备
生产线平衡分析改善案例

生产线平衡分析改善案例引言生产线平衡是指在生产过程中,通过合理分配各个工序的工作量,使得各个工序的产能能够实现平衡,从而提高生产效率、降低成本,并确保产品质量。
本文将以一个实际案例为例,介绍生产线平衡分析和改善的具体过程。
案例背景某电子产品制造公司拥有一条生产线,生产一种电子产品,该产品的组装工序分为A、B、C、D四个子工序。
在目前的生产线上,工序A的生产能力远超其他三个工序,导致A工序成为瓶颈工序,无法满足后续工序的需求,从而影响了整个生产线的效率和产量。
因此,公司决定进行生产线平衡分析,并制定改善方案,以提高生产线的平衡度。
生产线平衡分析1. 数据收集首先,需要收集工序A、B、C、D的工作时间数据,包括每个工序的加工时间、准备时间和等待时间。
这些数据将作为分析的基础。
2. 流程图绘制根据数据收集到的各个工序的时间,并结合实际生产情况,可以绘制出生产线的流程图。
流程图可以清晰地展示每个工序的工作时间和流程顺序,有助于进一步分析。
3. 生产线平衡计算根据流程图,可以计算出每个工序的工作时间总和。
然后,根据目标产量,计算出每个工序的标准工作时间,即每个工序应该占用的时间比例。
通过比较实际工作时间和标准工作时间,可以评估生产线的平衡度。
4. 分析结果根据生产线平衡计算的结果,可以看出工序A的工作时间远超其他工序,导致生产线的不平衡。
这也解释了为什么A工序成为瓶颈工序。
改善方案1. 调整工序A的产能由于工序A是瓶颈工序,可以考虑通过增加设备或优化工艺,提高工序A的产能,以满足后续工序的需求。
这可以通过增加工序A的设备数量、提高工段效率或优化工艺流程等手段实现。
2. 优化其他工序除了调整工序A的产能外,还可以进一步优化其他工序的流程,减少每个工序的工作时间。
例如,可以通过流程改进、工艺优化、培训员工等方式,提高其他工序的效率,从而平衡整个生产线。
3. 调整生产计划根据生产线平衡分析的结果,可以对生产计划进行合理调整。
生产线平衡(实例版)分析共53页文档
•
7、心急吃不了热汤圆。
•
8、你可以很有个性,但某些时候请收 敛。
•
9、只为成功找方法,不为失败找借口 (蹩脚 的工人 总是说 工具不 好)。
•
10、只要下定决心克服恐惧,便几乎 能克服 任何恐 惧。因 为,请 记住, 除了在 脑海中 ,恐惧 无处藏 身。-- 戴尔. 卡耐基 。
谢谢
11、越是没有本领的就越加自命不凡。——邓拓 12、越是无能的人,越喜欢挑剔别人的错儿。——爱尔兰 13、知人者智,自知者明。胜人者有力,自胜者强。——老子 14、意志坚强的人能把世界放在手中像泥块一样任意揉捏。——歌德 15、最具挑战性的挑战莫过于提升自我。——迈克尔·F·斯特利
生产线平衡分析改善案例(PPT53张)
工位间和工位内的多余的WIP为零。
B值=1
一 物 流
物流
顺畅流动 没有停滞
物留
中间停滞 隐藏问题
“一个流”的益处
1. 内建品质管理; 2. 创造真正的灵活弹性; 3. 创造更高的生产力; 4. 腾出更多厂房空间; 5. 改善安全性; 6. 改善员工士气; 7. 降低存货成本。
生产线平衡定义
对生产的全部工序进行均衡,调整作业 负荷和工作方式,消除工序不平衡和工 时浪费,实现“一个流”。
入料
出料
平衡生产线的意义
通过平衡生产线可以综合应用到程序分析、动作分析 、layout分析,搬动分析、时间分析等全部IE手法,提 高全员综合素质 在平衡的生产线基础上实现单元生产,提高生产应变 能力,对应市场变化实现柔性生产系统 减少单件产品的工时消耗,降低成本(等同于提高人 均产量) 减少工序的在制品,真正实现“一个流” 提高作业及设备工装的工作效率
5、生产线平衡的计算
各工程净时间总计 生产线平衡率(%)= 时间最长工程*人员数 *100% 如上图表中,生产线平衡率= 1505 90*19 不平衡率(%)= 100% —平衡率(%) *100% = 88%
对生产线来说,不平衡率越小越好,一般控 制5%-13%之间,至少要控制在15%以下。
案例:工时测定和线平衡计算
降低线体速度,减少生产产量
减少人手(2) 工 作 時 間
因生产需求量降低而 可降低线体速度
将工序3﹑4的工作时 间分配至工序 1﹑2﹑5里﹐从而工 序3﹑4工作岗位的人 手可调配至其它生产 线去。
工序 1
《生产线平衡范例》课件
作业时间分布
通过分析各作业点的作业时间分布情 况,可以判断生产线是否平衡。如果 各作业点的作业时间分布均匀,则说 明生产线平衡较好。
生产线平衡的优化方法
01
02
03
04
调整作业任务分配
根据各作业点的作业能力,合 理分配作业任务,使各作业点
的作业时间尽可能相近。
引入自动化设备
通过引入自动化设备,可以减 少人工操作时间,提高生产效
率。
优化工艺流程
通过优化工艺流程,可以减少 不必要的作业时间和等待时间
,提高生产效率。
加强员工培训
通过加强员工培训,可以提高 员工的操作技能和工作效率, 从而提升生产线平衡水平。
PART 03
生产线平衡的范例分析
范例一:某汽车制造企业的生产线平衡
总结词
通过优化生产线布局和作业分配,提高生产效率和产品质量。
详细描述
该汽车制造企业通过对生产线进行重新布局,合理分配作业任务,减少了生产 过程中的等待、搬运和重复作业时间,提高了生产效率。同时,优化了生产线 上的质量控制点,确保了产品质量。
范例二:某电子产品制造企业的生产线平衡
总结词
通过引入自动化和智能化设备,提高生产效率和产品质量。
详细描述
该电子产品制造企业引入了自动化和智能化设备,减少了生产线上的手工操作, 提高了生产效率。同时,通过设备自带的检测功能,确保了产品质量的稳定性。
重要性
生产线是现代制造业的核心,其运行 效率直接影响到企业的生产成本、产 品质量和交货期。一个高效、稳定的 生产线是企业取得竞争优势的关键。
生产线平衡的目标与意义
目标
生产线平衡的目标是实现生产线的整体最优运作,提高生产 效率和降低生产成本。具体来说,就是要使各工作地的作业 时间尽可能平衡,避免出现空闲或等待时间,确保生产线的 顺畅运转。
生产线平衡案例分析PPT
生产线平衡定义
对生产的全部工序进行均衡,调整作业 负荷和工作方式,消除工序不平衡和工 时浪费,实现“一个流”。
出料
入料
平衡生产线的意义
通过平衡生产线可以综合应用到程序分析、动作分析 、layout分析,搬动分析、时间分析等全部IE手法,提 高全员综合素质
在平衡的生产线基础上实现单元生产,提高生产应变 能力,对应市场变化实现柔性生产系统
90*19
不平衡率(%)= 100% —平衡率(%)
对生产线来说,不平衡率越小越好,一般控 制5%-13%之间,至少要控制在15%以下。
案例:工时测定和线平衡计算
请大家观看电子分厂电装3人柔性线视频
1、一边看一边测试,最后计算平衡率 2、计算一下线小时理论产量 3、提出提升线平衡的思路方法
评分标准 1、2、3、4名分别 100、80、60、40分 计算公式错不得分 计算公式对,结果错,扣10分
• 生产线平衡损失 = 1 - 平衡率 一般要求生产线平衡率达到85%以上
何谓标准工时
标准时间是指,“一个熟练工用规定的 作业方法以标准速度进行作业时所需的作业 时间”。
在熟练度、合理性、工作热情及其他所 有方面都相同的“标准作业员”以标准的作 业方法及一般的努力程度进行作业,次日不 会感到疲劳的“作业时间”。
减少单件产品的工时消耗,降低成本(等同于提高人 均产量)
减少工序的在制品,真正实现“一个流”
提高作业及设备工装的工作效率
生产线平衡计算
• 节拍 – 生产周期
最长工序时间(瓶颈岗位时间)决定了整个生产线的 作业时间,即等于节拍
平衡率
平衡率=
∑(各工序的作业时间) 瓶颈岗位时间*人数
* 100%