复印机小端盖注塑模具设计方案
小瓶盖塑料注塑模具设计说明书
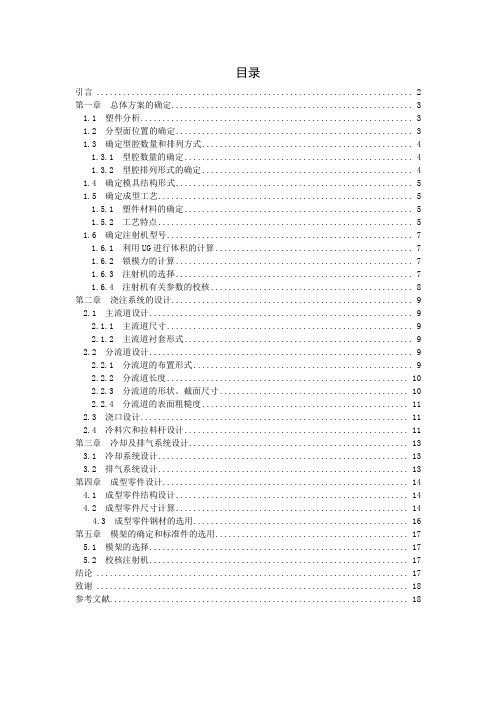
目录引言 (2)第一章总体方案的确定 (3)1.1 塑件分析 (3)1.2 分型面位置的确定 (3)1.3 确定型腔数量和排列方式 (4)1.3.1 型腔数量的确定 (4)1.3.2 型腔排列形式的确定 (4)1.4 确定模具结构形式 (5)1.5 确定成型工艺 (5)1.5.1 塑件材料的确定 (5)1.5.2 工艺特点 (5)1.6 确定注射机型号 (7)1.6.1 利用UG进行体积的计算 (7)1.6.2 锁模力的计算 (7)1.6.3 注射机的选择 (7)1.6.4 注射机有关参数的校核 (8)第二章浇注系统的设计 (9)2.1 主流道设计 (9)2.1.1 主流道尺寸 (9)2.1.2 主流道衬套形式 (9)2.2 分流道设计 (9)2.2.1 分流道的布置形式 (9)2.2.2 分流道长度 (10)2.2.3 分流道的形状、截面尺寸 (10)2.2.4 分流道的表面粗糙度 (11)2.3 浇口设计 (11)2.4 冷料穴和拉料杆设计 (11)第三章冷却及排气系统设计 (13)3.1 冷却系统设计 (13)3.2 排气系统设计 (13)第四章成型零件设计 (14)4.1 成型零件结构设计 (14)4.2 成型零件尺寸计算 (14)4.3 成型零件钢材的选用 (16)第五章模架的确定和标准件的选用 (17)5.1 模架的选择 (17)5.2 校核注射机 (17)结论 (17)致谢 (18)参考文献 (18)引言模具是汽车、电子、电器、航空、仪表、轻工、塑料、日用品等工业生产的重要工艺装备,模具工业是国民经济的基础工业。
没有模具,就没有高质量的产品。
用模具加工的零件,具有生产率高、质量好、节约材料、成本低等一系列优点。
因此已经成为现代工业生产的重要手段和工艺发展方向。
因此,模具技术,特别是制造精密、复杂、大型模具的技术,已成为衡量一个国家机械制造水平的重要标志之一。
模具在现代生产中,是生产各种工业产品的重要工艺装备,它以其特定的形状通过一定的方式使原材料成型。
打印机注塑件模具设计

打印机注塑件模具设计摘要:本文主要针对打印机注塑件的模具设计展开了探讨,系统分析了注塑件的工艺,对注塑件模具的设计和模具工作的行程作了详细的阐述,以期能为有关方面的需要提供有益的参考和借鉴。
关键词:注塑件;模具;设计好的模具设计工作对于打印机的注塑件来说有着重要的作用,因此,做好打印机注塑件的模具设计工作非常必要。
我们需要熟练注塑件的工艺,以做好模具设计工作。
基于此,本文就打印机注塑件的模具设计进行了探讨,相信对有关方面的需要能起到一定的帮助作用。
1 注塑件的工艺分析塑料注射成形是利用塑料的可挤压性与可模塑性,首先将粒状或粉状的塑料加入到注塑机的料斗,由螺杆带动塑料前行进入料筒,由料筒壁的加热器及螺杆的摩擦作用令塑料在料筒内加热至熔融状态,在螺杆的高压推动下,以一定的速度和压力经浇注系统进入闭合模具中,经过保压冷却凝固成形后开模,模具推出机构推出制件,从而获得具有一定形状和尺寸的塑料制件。
模具设计应根据塑件的使用要求及相应的技术指标,选择合理的工艺方案。
(1)注塑件的结构形状分析。
该塑件是打印机上一个部件,受到振动、摩擦等情况比较多,制件材料要求韧性好,表面粗糙度低。
制件结构简单,形状规则,大批量生产。
采用单分型面注塑模有利于降低模具复杂程度,有利于模具加工制造。
(2)注塑件的性能指标及成型特性分析。
工件材料为HIPS,是PS的改性材料,分子中含有5%~15%橡胶成份,韧性好、冲击强度高,成型加工性能好、着色力强。
HIPS制品不透明,吸水性低,可不需预先干燥。
主要性能指标:弯曲强度13.8~55.1MPa;拉伸强度13.8~41.4MPa;断裂伸长率为15%~75%;维卡软化点185°~220°F。
(3)注塑成型工艺参数分析。
根据经验数据和推荐值,初步确定成型工艺参数选择往复螺杆式注塑机,由公称注射量选定注射机。
打印机零件的注塑模采用单分型面注塑模,一模四腔。
产品材料HIPS,其密度为1.035~1.04g/cm3,收缩率为0.3~0.8,计算其平均密度设为1.04g/cm3,平均收缩率为0.5%。
模具注塑产品设计方案模板
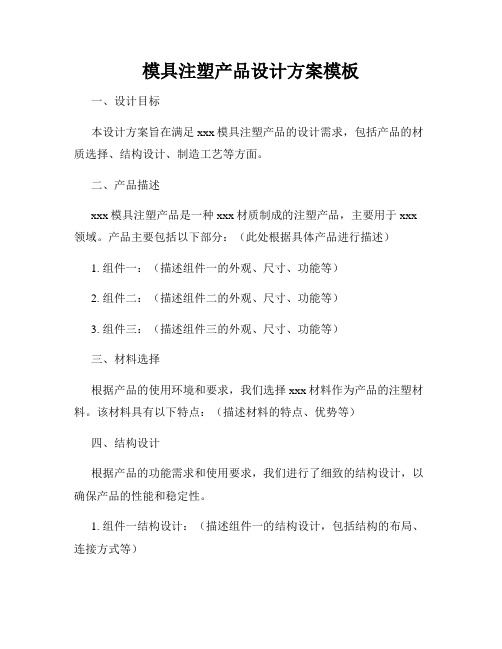
模具注塑产品设计方案模板一、设计目标本设计方案旨在满足xxx模具注塑产品的设计需求,包括产品的材质选择、结构设计、制造工艺等方面。
二、产品描述xxx模具注塑产品是一种xxx材质制成的注塑产品,主要用于xxx 领域。
产品主要包括以下部分:(此处根据具体产品进行描述)1. 组件一:(描述组件一的外观、尺寸、功能等)2. 组件二:(描述组件二的外观、尺寸、功能等)3. 组件三:(描述组件三的外观、尺寸、功能等)三、材料选择根据产品的使用环境和要求,我们选择xxx材料作为产品的注塑材料。
该材料具有以下特点:(描述材料的特点、优势等)四、结构设计根据产品的功能需求和使用要求,我们进行了细致的结构设计,以确保产品的性能和稳定性。
1. 组件一结构设计:(描述组件一的结构设计,包括结构的布局、连接方式等)2. 组件二结构设计:(描述组件二的结构设计,包括结构的布局、连接方式等)3. 组件三结构设计:(描述组件三的结构设计,包括结构的布局、连接方式等)五、制造工艺为实现设计方案,我们采用了以下制造工艺来生产xxx模具注塑产品。
1. 模具制造:选择优质的钢材,开展精密的数控加工,制造符合精度要求的模具。
2. 注塑成型:通过将注塑材料加热熔化后注入模具中,冷却后获取最终成型的产品。
3. 后处理:对成型产品进行去除模具余料、修整边缘、表面处理等工艺,使产品达到要求。
六、检测与质量控制为确保产品的质量,我们采用以下检测方法和质量控制措施:1. 外观检测:检查产品的表面光洁度、色彩、图案等外观要素。
2. 尺寸检测:使用合适的测量工具对产品的尺寸进行严格检测。
3. 功能性检测:对产品的功能进行评估,确保其满足使用要求。
七、产品应用与推广xxx模具注塑产品可广泛应用于xxx领域,如xxx等。
我们将通过合适的渠道进行产品的推广,并提供优质的售后服务。
八、总结本设计方案是基于对xxx模具注塑产品的需求和要求进行的综合设计。
通过合理的材料选择、结构设计和制造工艺,我们将为客户提供优质的产品和服务。
本科毕业设计论文--φ40×12电器盖注塑模具设计

摘要随着经济的发展和人们生活水平的提高,对一些小的物品就像一个小小的按钮都有独到的要求,不仅要方便使用而且对外观的要求也很高.所以对塑料模具的要求也很高也越来与越高。
随着现代工业发展的需要,模具是重要的工艺装备之一,它在工农业生产以及日常生活中得到了广泛的应用。
由于采用模具进行生产能提高生产效率、节约原材料、降低成本,并可保证一定的加工质量要求,所以在电子,汽车、电机、电器、飞机、仪表,家电和通讯等产品中大部分零部件都采用模具进行加工。
塑料模具设计则是模具的主要部分,塑料模具的设计与制造水平的普及提高,是塑料成型加工工业,发展必不可少的重要条件.模具生产技术水平的高低,已成为衡量一个国家产品制造水平高低的重要标志.此次,通过对端盖注塑模具的设计,可以使我对注塑模有更深刻的理解而且可以熟练掌握相关软件,同时也锻炼了我综合运用所学知识解决实际问题的能力。
.对于塑料模具来说,目前市场上的百分之九九的外壳类产品都采用塑料,因为它不用承受很大的负载,塑料又起到了绝缘的效果.塑料的颜色多变,能满足人们不同的喜好。
本次设计的是的电器盖注塑模具设计,分析可知该零件的外形比较小,因此采用浇注系统为侧浇口模式,一个模具两个型腔,单分型面注射成为本次设计的结构模式。
本次设计的具体操作如下:首先是对于本次所要设计的塑件进行一系列的分析。
其中包括了对塑件结构的尺寸分析和材料分析。
然后是是对本次设计的塑件设计一个合理的方案。
其中包括了分型面的确定,型腔数量的确定以及浇注系统和顶出系统的设计。
对于该模具的设计,先要选定一台符合本次设计要求的注塑机。
然后是设计该塑件的浇注系统。
接着是对成型零部件的结构设计和工作尺寸的计算。
以及对排气系统和冷却系统的优化。
最后是对于整个模具的装配的要求和过程,并且使用CAD软件绘制了本次设计的模具的装配图和各个零件图。
总结了设计说明书。
关键字:注塑模具;侧浇口;CAD。
AbstractWith the economic development and people's living standards improve, on a number of small items like a small button has unique requirements, should not only has the advantages of convenient use and appearance requirements are very high. So the requirement of plastic mold is also very high and and higher.With the development of modern industry, the mold is one of the important technological equipment, it has been widely used in industrial and agricultural production and daily life.Home appliances and communication products such as most of the parts of the mold processing. Plastic mold design is the mold of the main part, improve the popularity of the plastic mold design and manufacturing level, plastics processing industry, essential for the development of an important condition. Level of mold production technical level has become the measure of a national product manufacture level of an important symbol of. This time, by the end cover injection mold design can enable me to cast the mold to have more profound understanding and mastery of the relevant software, but also exercise the integrated use of my knowledge to solve practical problems.For plastic mould, at present market of 99 percent of shell products are made of plastic, because it doesn't have to bear great load, plastic and insulation. Plastic color changeable, meet people's different preferences.This design is the electrical cover injection mold design and analysis shows that the parts of the shape is relatively small, so the use of gating system for side gate pattern and a mold two cavity, a single type of injection into the design modes of the structure. The design of the specific operation are as follows: first, the design of the plastic parts to carry out aseries of analysis. The dimension analysis and material analysis of the structure of the plastic parts are included. Then is the design of the plastic parts of the design of a reasonable solution. It includes the determination of the parting surface, the determination of the number of cavities and the design of the gating system and the ejection system.For the design of the mold, we must first select a machine that meets the requirements of the design of the injection molding machine. Then the casting system of the plastic part is designed. Then the structure design of the forming parts and the calculation of the working dimensions are followed. Optimization of exhaust system and cooling system. Finally, the requirements and process for the entire mold assembly, and the use of CAD software to draw the design of the mold assembly drawing and parts drawing. The design specification is summarized.Keywords:injection mold side gate; CAD.目录第1章.绪论 (1)第2章塑料制件的分析 (2)2.1 成型塑料件的工艺性分析 (2)2.2 成型塑件的材料分析 (3)第3章注塑设备的选择 (4)3.1估算塑件体积质量 (4)3.2 注塑机的选择 (4)第4章成型零件设计和计算 (6)4.1凸模的结构设计 (6)4.2凹模的结构设计 (7)4.3 型芯型腔尺寸计算 (8)4.3.1型腔凹模尺寸的计算 (10)4.3.2型芯凸模尺寸的计算 (12)第5章浇注系统的设计 (14)5.1 分型面的选取 (14)5.2模具型腔排列方式 (16)5.3浇口套的选用 (17)5.4冷料井的设计 (19)5.5分流道的设计 (20)5.7浇口设计 (22)第6章合模导向机构的设计 (23)6.1导柱的设计 (23)6.2 导套的设计 (25)第7章脱模结构的设计 (26)7.1 脱模力的计算 (26)7.2推出结构的设计 (27)第8章侧向分型和抽芯机构的设计 (29)8.1抽拔距的计算 (29)8.2斜导柱的尺寸与安装形式 (29)8.3 锁紧楔形式 (31)8.4 斜导柱的受力分析及强度计算 (31)第9章排气系统和冷却系统的设计 (32)9.1排气系统 (32)9.2冷却系统的设计 (32)第10章绘制装配图 (34)第11章注射机的校核 (36)11.1 注射量的校核 (36)11.2 锁模力的校核 (36)11.3 模具高度校核 (37)11.4 模具开模行程校核 (37)结论 (38)参考文献 (39)致谢 (40)第1章.绪论在五十年前,中国的模具行业取得了长足的进步,大大提高了模具制造的水平。
小瓶盖塑料注塑模具设计说明书
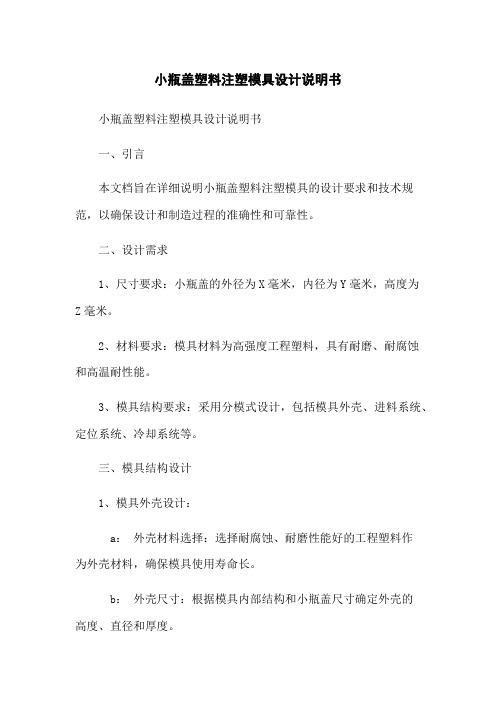
小瓶盖塑料注塑模具设计说明书小瓶盖塑料注塑模具设计说明书一、引言本文档旨在详细说明小瓶盖塑料注塑模具的设计要求和技术规范,以确保设计和制造过程的准确性和可靠性。
二、设计需求1、尺寸要求:小瓶盖的外径为X毫米,内径为Y毫米,高度为Z毫米。
2、材料要求:模具材料为高强度工程塑料,具有耐磨、耐腐蚀和高温耐性能。
3、模具结构要求:采用分模式设计,包括模具外壳、进料系统、定位系统、冷却系统等。
三、模具结构设计1、模具外壳设计:a:外壳材料选择:选择耐腐蚀、耐磨性能好的工程塑料作为外壳材料,确保模具使用寿命长。
b:外壳尺寸:根据模具内部结构和小瓶盖尺寸确定外壳的高度、直径和厚度。
c:模具外壳装配:确保外壳的装配牢固,能够承受注塑过程中的压力和冲击。
2、进料系统设计:a:进料口位置:进料口位于模具外壳上方,方便塑料材料的注入和冷却。
b:进料系统结构:进料系统包括进料管道、进料阀门和喷嘴等组成,确保塑料均匀流动。
3、定位系统设计:a:定位杆:在模具内部设置定位杆,以确保小瓶盖注塑时的位置准确性。
b:定位孔:在小瓶盖上开设定位孔,使得小瓶盖能够准确地套在定位杆上。
4、冷却系统设计:a:冷却通道:在模具内部设置冷却通道,以降低注塑过程中的温度,提高生产效率和产品质量。
b:冷却介质:选择高效的冷却介质,如冷水或冷气等,快速降低模具温度。
四、模具制造要求1、加工工艺:采用先进的数控加工设备和工艺,确保模具的加工精度和表面光洁度。
2、查漏测试:在模具制造过程中进行查漏测试,确保模具没有任何渗漏。
五、附录本文档涉及以下附件:1、小瓶盖的详细尺寸图纸。
2、模具的3D设计图纸。
六、法律名词及注释1、注塑模具:指用于塑料注塑成型的模具,可分为热流道模具和冷流道模具。
2、工程塑料:指具有高强度、耐磨、耐腐蚀和高温耐性能的塑料材料。
3、渗漏:指模具在注塑过程中出现塑料渗漏的现象,对产品质量产生负面影响。
塑料盖注射模设计说明书

1 塑料模具概论1.1 论文背景及意义随着市场竞争趋势日益加,使产品功能多元化增加,同时产品的生命周期不断缩短,塑料产品结构变得多样化和复杂化,客户对产品质量的要求也越来越高。
在一定程度上使模具设计和注射成型过程的趋于复杂,某些注射成型问题甚至是经验丰富的模具设计师和注射工艺师都难以把握和解决。
在注射模具的设计过程中,首先考虑的一般是模具结构本身的需要,在满足这个要求之后才考虑注射制品的需要。
例如,传统规的注射模设计通常是根据经验来确定浇注系统和冷却系统的形式和尺寸,而并非根据流动分析的方法来确定。
在最后的试模过程中通过反复的调整模具的浇注系统和冷却系统参数以求基本达到产品的质量要求。
这样势必将造成模具试模周期过长、试模成本过高,从而严重影响了企业的经济效益和竞争力。
因此,塑料熔体注射成型过程的设计和计算产品结构设计、模具结构以及注射成型工艺都具有非常重要的指导性意义。
1.2 课题国内外发展现状当今世界,模具生产技术水平的高低已经成为衡量一个国家制造水平高低的重要标志之一,因为模具的质量在很大程度上决定了产品的质量、效益以及新产品的开发能力。
塑料模具的发展是随着塑料工业的发展而发展起来的。
随着经济的发展人们对生活的质量要求越来越高,对设备和用品的外观、舒适度、轻量化以及价格的要求越来越高,这就使塑料制品有了更为广阔的市场前景。
塑料模具产业的发展进步,对塑料制品业的发展起到了关键性的作用。
塑料制品在家电、汽车、办公用品、IT 信息、工业电器等各个行业的发展非常迅速,使得塑料模具行业也快速发展。
1.2.1 主要研究成果塑料注射模具的发展在我国起步比较晚,但发展速度很快,特别是在近些年来,无论是在质量和技术上,还是在制造能力上都有很大的发展和进步。
主要成就有以下几个方面:⑴CAD/CAM/CAE技术在塑料模具的设计制造上应用越来越普遍,特别是在CAD/CAM 技术的应用方面,取得了非常大的成绩。
⑵电子信息工程技术的广泛应用提高了塑料模的设计和制造水平。
毕业设计(论文)-塑料端盖注塑模具设计
毕业设计(论文)任务书指导教师签字:教研室主任签字:学生姓名高雪慧专业班级模具设计与制造z070220班指导教师范敏课题类型工程设计题目塑料端盖注塑模具设计主要研究目标(或研究内容)1、应达到的目标:(1)完整设计一套能够生产塑件的塑料注射模具;(2)设计的模具结构合理,参数选择正确,基本符合实际生产需要;(3)绘图符合国家标准、结构表达完整,尺寸标注正确;(4)设计说明书内容完整、符合规定的格式要求。
2、主要技术要求:(1)塑件材料选用市场能买到的常用塑料(如工程塑料ABS或聚氯乙烯PVC等);(2)生产类型为大批量生产,年产量为30万件;课题要求、主要任务及数量(指图纸规格、张数,说明书页数、论文字数等)(1)分析塑料件的结构特征,绘出塑件零件图,确定塑件的质量和体积;(2)根据塑件的生产要求选定注射工艺参数,制定注射工艺规程;(3)选择能满足生产需要的注射机;(4)确定塑料注射模具的设计方案,绘出装配草图,确定每个零件的形状、尺寸、公差、材料、热处理方式和技术条件等;(5)绘制注射模具的装配图和全部零件的零件图,写出3万字左右的设计说明书.。
进度计划(1)1~3周,选择塑料件,查阅相关资料,学习塑料模具的设计方法。
(2)4~7周,根据任务书要求,对塑件进行分析,确定模具的设计方案,按步骤进行设计计算,确定工艺参数,画出模具的装配结构草图,并确定草图中各零件的结构、尺寸、材料、公差和技术要求。
(3)8~10周,书写设计说明书,用CAD画出模具装配图和所有零件的零件图,绘出主要零件的立体模型图,交指导教师审查。
(4)11~12周,按指导教师的要求对设计说明书和图的电子稿进行修改,修改后交主要参考文献(1)于保敏塑料成型工艺与模具设计 .北京:清华大学出版社2009 (2)王鹏驹塑料模具设计及制造 .北京:机械工业出版社,2005 (3)杨占尧塑料模具典型结构设计实例 .北京:华工工业出版社,2008 (4)冯爱新 .塑料模具工程师手册上海:科学技术出版社,1998指导教师签字:教研室主任签字:年月日毕业设计零件图端盖塑料模具设计摘要本课题主要是针对端盖的模具设计,通过对塑件进行工艺的分析和比较,最终设计出一副注塑模。
打印机外壳注塑模具设计
本科毕业设计(论文) 题目:打印机外壳注塑模具设计系别:机电信息系专业:机械设计制造及其自动化班级:学生:学号:指导教师:2013年05月打印机外壳注塑模具设计摘要本设计为打印机外壳注塑模的设计。
设计中采用一模一腔,浇口采用点胶口,分型面选在截面最大处,塑件成型后利用推杆将成型制品从动模上推出,回程时利用复位杆复位。
设计中需要对塑件的尺寸进行计算,确定尺寸精度,然后进行注射机的初步选取。
以及对注塑机的浇注系统、成型零件的结构、成型零件的尺寸、脱模推出机构、排气系统、温度调节系统进行了设计与计算。
并且对注射机参数进行校核,包括模具闭合厚度、模具安装尺寸、模具开模行程、注射机的锁模力等。
各个参数都满足要求后才能确定注射机的型号。
在设计过程中,为了更清楚的表达模具的内部结构,因此附有动模镶块、定模镶块、定模推板的二维零件图和模具三维爆炸图。
关键词:打印机外壳;分型面;浇口;工艺分析Ink jet printer cover injection mold designAbstractThis design is the design of injection mould for the cabinet. The design uses two mold cavity, type of the sprue is latent gate, the parting surface is chosen in the maximum section of the plastics. After plastics are molded,molding products are driven by putting from dynamic model,then using reset stem returned.In the design ,The need to calculate the size design, determine the size precision, the preliminary selection and the injection machine. And the injection molding machine of gating system, forming part of the structure, forming part of the size, mold release mechanism, exhaust system, temperature control system design and calculation. And to check the injection machine parameters, including the thickness of mold closing, mold installation size, mold opening stroke, the clamping force injection molding machine etc.. All the parameters meet the requirements to determine the type of injection machine.In the design process, in order to express more clearly the internal structure of the mold, so a moving die insert, fixed die insert, the fixed mould push plate 2D part drawing and 3D map explosion.Keywords: Cabinet;Parting;surface;Runner;Process analysis主要符号表T额定锁模力q模腔压力K安全系数H最小模具厚度minH最大模具maxδ塑件尺寸误差sS塑料的最大收缩率maxS塑料的最小收缩率minL塑件尺寸sS塑料的平均收缩率∆塑料的公差δ模具制造公差[]δ型腔许用变形量E型腔材料的弹性模量σ型腔材料的需用压力[]α脱模斜度f摩擦系数F脱模力φ推杆长度系数Q总脱模力σ应力σ屈服极限s目录1绪论 (1)1.1题目背景 (1)1.2题目国内外相关研究情况 (1)1.2.1国内研究的情况 (1)1.2.2国外研究情况 (2)1.3中国与国外先进技术的差距 (2)1.4塑料模具发展走势 (2)2 产品分析 (4)2.1塑件分析 (4)2.1.1结构分析 (4)2.1.2尺寸精度分析 (5)2.1.3 塑件厚度检测 (5)2.1.4表面质量分析 (5)2.2 塑件材料选择 (6)2.2.1物理性能 (6)2.2.2 ABS的主要性能指标 (6)2.2.3ABS成型塑件的主要缺陷及消除措施 (6)3拟定模具结构形式及注射机的初步选择 (7)3.1分型面位置的确定 (7)3.1.1模具的分型面 (7)3.1.2分型面的确定 (7)3.2塑件相关计算 (8)3.2.1塑件相关计算 (9)3.3 型腔数量的确定 (10)3.4初步选择注塑机 (11)4浇注系统的设计 (13)4.1浇注系统 (13)4.1.1浇注系统的作用 (13)4.1.2浇注系统布置 (13)4.2浇注系统设计 (13)4.2.1浇口套的设计 (13)4.2.2 浇注系统的设计 (16)4.2.3 分流道与浇口 (17)4.3浇口设计 (18)4.3.1浇口的类型 (18)4.3.2浇口的位置 (18)5 成型零件的工作尺寸计算 (20)5.1成型零件工作尺寸的计算 (20)6成型零件结构设计 (24)6.1 PRO/E中的模具模块设计 (24)6.1.1凹模结构设计 (25)6.1.2凸模结构设计 (25)7导向机构设计 (27)7.1导向机构 (27)7.1.1导柱 (27)7.1.2 导套 (28)7.1.3 导柱与导套的配用 (29)7.1.4 导柱布置 (30)7.2 定位装置 (30)7.2.1拉杆 (30)7.3尼龙开闭器装置 (30)8 脱模推出机构的设计 (32)8.1 在设计脱模推出机构是应遵循下列原则 (32)8.2 脱模力的计算 (32)8.3推出机构设计 (32)8.3.1推杆布置 (32)8.3.2推杆结构及固定 (33)8.3.3推杆强度交核 (33)8.4 拉料机构 (34)9 排气系统设计 (36)10 温度调节系统设计 (37)10.1对温度调节系统的要求 (37)10.2 冷却系统设计 (37)10.2.1 冷却回路的布置 (37)10.2.1 设计原则 (37)10.2.2冷却时间的确定 (38)10.3模具冷却系统的计算 (39)11注塑机的校核 (40)11.1最大注塑量的校核 (40)11.2锁模力的校核 (40)11.3 喷嘴尺寸校核 (40)11.4定位圈尺寸校核 (41)11.5模具外形尺寸校核 (41)11.6模具厚度校核 (41)11.7模具安装尺寸校核 (41)11.8开模行程的校核 (41)12 模具工作过程 (43)12.1 模具总体结构 (43)12.2开合模动作 (45)13模具可行性分析 (46)13.1本模具的特点 (46)13.2市场效益及经济效益分析 (46)结论 (47)致谢 (48)参考文献 (49)毕业设计(论文)知识产权声明 (50)毕业设计(论文)独创性声明 (51)附录 (52)1 绪论1绪论1.1题目背景近年来,我国塑料模具业发展相当快,目前,塑料模具在整个模具行业中约占30%左右,而在整个塑料模具市场以注塑模具需求量最大。
盖的注塑模具设计
盖的注塑模具设计注塑模具设计是一项非常关键和复杂的工作。
通过合理设计模具,可以提高产品的质量和生产效率,并降低生产成本。
本文将介绍注塑模具设计的一般步骤和注意事项。
一、注塑模具设计的一般步骤(一)确定产品需求首先要根据产品的要求确定模具设计的目标和要求。
包括产品的材料、尺寸、外观要求等。
这些信息将作为模具设计的基础。
(二)模具结构设计根据产品的形状和要求,确定模具的结构。
通常包括模具的什么类型(如单腔模、多腔模、自动剥料模等)、模具的分型方式(如顶出式、拉出式等)、模具的开合方式(如水平开合、垂直开合等)等。
(三)模具的尺寸和定位设计根据产品的尺寸和结构,确定模具的尺寸和定位。
包括模具的长度、宽度、高度等。
同时,还需要确定模具的定位方式,以确保产品在模具中的位置准确。
(四)模具的加工工艺设计根据模具的结构和尺寸,确定模具的加工工艺。
包括模具的开槽、铣削、钻孔等工艺。
同时,还要确定模具的材料,以确保模具的强度和耐磨性。
(五)模具的冷却系统设计注塑过程中,需要通过冷却系统来降低模具温度,以确保产品的质量。
因此,需要设计模具的冷却系统。
包括水路布局、水流量、水压等。
(六)其他考虑因素除了上述内容,还有一些其他的考虑因素。
比如模具的排气设计、模具的剥料设计、模具的注塑机尺寸等。
这些因素都需要考虑到,以确保模具的正常运行。
二、注塑模具设计的注意事项(一)模具的结构要合理,易于加工和维修。
模具的结构应尽量简单,以降低生产成本。
(二)模具的冷却系统设计要科学合理。
冷却系统的设计直接影响产品的质量和生产效率。
(三)模具的尺寸和定位要准确。
尺寸和定位的不准确会导致产品的尺寸偏差,甚至无法使用。
(四)模具的材料选择要恰当。
根据产品的要求和工作条件,选择合适的模具材料,以确保模具的使用寿命。
(五)模具的加工要精确。
尤其是模具的分型面、腔体等部分,需要精密加工,以确保产品的质量。
(六)模具的周边设备要配套齐全。
模具的周边设备包括注塑机、冷却设备、模具温控装置等,需要与模具配套使用。
端盖注射模模具设计
端盖注射模模具设计为了满足市场需求,我们需要设计一款端盖注射模具。
以下是模具设计的步骤和过程:一、产品分析该注射模具的主要产品是塑料端盖。
端盖的材质为聚丙烯(PP),常用于封装包装和容器,具有抗冲击、抗压和耐化学腐蚀等特性。
我们需要了解其规格和尺寸,以便进行模具设计。
二、模具结构分析1. 模具结构分为两部分:上模和下模。
上模包括注射喷嘴、挤出口、进料口、冷却系统、端盖定位装置等;下模包括模板、端盖定位销、定位杆、挤出筒等。
2. 模具采用四柱式结构,具有稳定性、刚性和精度。
三、模具设计步骤1. 确定模具型号和规格模具型号为SJ-01,规格为400×400×350mm。
2. 确定注射机的规格和参数注射机规格为400T,注射量为500g,注射压力为160MPa。
3. 设计上模和下模(1)上模设计a. 设计喷嘴和进料口喷嘴和进料口的位置应该在端盖的一侧,注射方向与端盖的尺寸方向垂直。
喷嘴选择直径为1mm的圆形棒材,该尺寸适合注射量500g的端盖。
进料口的位置应该在模具中心位置,方便塑料材料的流动。
b. 设计冷却系统使用水冷却系统,包括水流通道、水口、止回阀和水管。
水流通道应该设置在大型结构的表面,以方便冷却和缩短成型时间。
c. 设计端盖定位装置采用便于更换和调整的设计,可以根据端盖的不同尺寸和形状进行调整。
(2)下模设计a. 设计模板模板采用高强度合金材料加工,具有硬度高、抗压性能强、耐磨损的特点。
模板的内部应该加强水平连接结构,以保证模板的中心线与机床的中心线保持一致。
b. 设计端盖定位销和定位杆端盖定位销应该精度高且紧密连接,以确保端盖的定位精度。
定位杆应该设计成固定位置和可调式,可根据端盖的不同尺寸和形状进行调整。
c. 设计挤出筒挤出筒应该选用优质合金钢材制造,具有高耐蚀性、高耐磨性和高强度。
同样重要的是,挤出筒的尺寸和长度应该符合端盖的尺寸和需求。
4. 完成模具设计和制造通过CAD和CAM软件进行模具设计,完成模具的制造和加工。
- 1、下载文档前请自行甄别文档内容的完整性,平台不提供额外的编辑、内容补充、找答案等附加服务。
- 2、"仅部分预览"的文档,不可在线预览部分如存在完整性等问题,可反馈申请退款(可完整预览的文档不适用该条件!)。
- 3、如文档侵犯您的权益,请联系客服反馈,我们会尽快为您处理(人工客服工作时间:9:00-18:30)。
本科毕业设计(论文>题目:复印机小端盖注塑模具设计系^别:机电信息系专业:机械设计制造及其自动化班级:学生:学号:指导教师:2018年5月目录1 绪论11.1 题目的背景和意义11.2国内外模具工业的发展状况11.3 塑料模具发展走势............................................................................2. .1.4 课题研究的意义及主要研究内容22 复印机小端盖的工艺性分析42.1 塑件的材料与结构分析4 2.1.1塑件的体积及质量计算4 2.1.2塑件的结构与材料52.2塑件的尺寸精度及表面质量7 2.2.1塑件的尺寸精度7 2.2.2塑件的表面质量72.3工艺性分析73 注塑模具结构设计83.1分型面的确定83.2 浇口的确定103.3型腔数目的确定113.4浇注系统设计123.4.1主流道123.4.2分流道133.4.3 浇口的设计13 3.4.4浇口套的形式及固定方式143.5成型零部件设计14 3.5.1成型零部件结构设计15 3.5.2成型零件工作尺寸计算183.6导向零件的设计193.7 抽芯机构和顶出机构的设计213.7.1抽芯机构的设计213.7.2顶出机构的设计223.8 脱模结构的设计243.8.1 脱模力的计算244 冷却设计及排气系统264.1 冷却水道热传面积264.1.1塑料传给模具的热量264.1.2冷却水的体积流量264.1.3冷却水道热传面积274.2排气系统的设计275 注射机的选择及校核285.1 选择注射机285.2注射机的校核285.2.1 注射压力的校核295.2.2最大注射量的校核305.2.3锁模力的校核305.2.4喷嘴尺寸校核305.2.5 注射机固定模板定位孔与模具定位圈的关系315.2.6模具外形尺寸校核315.2.7 模具的安装紧固315.3 本章小结316 模具材料的选择327 模具装配图及制造工艺337.1 模具装配图337.2模具制造工艺357 模具可行性分析368.1 本模具的特点........................................................................... 3.. 68.2 市场效益及经济效益分析........................................................................... 3.. 69 结论37致谢38参考文献 (39)毕业设计<论文)知识产权声明. (40)毕业设计<论文)独创性声明. (41)附录42图纸和说明书联系QQ25766365382复印机小端盖的工艺性分析2.1塑件的材料与结构分析2.1.1塑件的体积及质量计算体积及质量的计算也利用PRO/ENGINEER的分析模块自动计算获得<塑件密度由《塑料模设计手册》表1—4查得:p =1.2g/cm),如图2.1所示:结果如下: 体积=3.9154560e+04 MM A 3曲面面积=3.3292018e+04 MMA2密度=1.2000000e+00 公吨 / MMA3质量= 4.6985471e+04 公吨故注塑件体积为:V=39.15cm 3质量为:M=39.15x1.2g=46.98g<注:此处的塑件体积及质量都不包括浇注系统在内)坐标丟3. 29SQ]le40q NT 2 EDaomav+aD / n 『s 693547] ^0-1 经*6 二面三=$眼庭一FTJ ■鱼味过电谄定至心 H 0 x 图2.1塑件三维图2.1.2塑件的结构与材料塑件的三维造型如图2.2,二维如图2.3所示图2.2塑件三维图图2.3塑件二维图零件尺寸如图2.2所示,该塑件名称为复印机小端盖,塑件形状类似为平板薄壳结构,盒盖长110mm,宽85mm,高26mm,壳盖壁厚为3mm,最薄壁厚为1mm。
结构对称。
要求具有一定的强度、刚度、耐热和耐磨损等性能。
ABS 合成塑料以其很好的韧性、密封性,很高的机械强度,耐化学腐蚀,加工适应性好,注射成型,挤出成型等所有的加工方法都可以,而且尺寸稳定性好,耐碱性,耐应力开裂性也好,根据以上特点以及经济因素,采用ABS塑料。
2.2塑件的尺寸精度及表面质量2.2.1塑件的尺寸精度a.尺寸精度的选择;塑件的尺寸精度是决定塑件制造质量的首要标准,然而,在满足塑件使用要求的前提下,设计时总是尽量将其尺寸精度放低一些,以便降低模具的加工难度和制造成本。
对塑件的精度要求,要具体分析,根据装配情况来确定尺寸公差,该塑件是一般办公用品,所以精度要求为一般精度即可,根据精度等级选用表,ABS的高精度为MT3级,一般精度为MT4级。
根据塑件尺寸公差表,在公称尺寸在65~80范围内,MT4A级的公差值为0.64mm,MT4B级的公差数值为0.84 mm。
b.尺寸精度的组成及影响因素;制品尺寸误差构成为:<2.1式中:一制件总的成型误差;――塑料收缩率波动所引起的误差;模具成型零件制造精度所引起的误差;――模具磨损后所引起的误差;――模具安装,配合间隙引起的误差。
影响塑料制品尺寸精度的因素比较复杂,归纳有以下三个方面。
模具一一模具各部分的制造精度是影响制件尺寸精度重要的因素;塑料材料一一主要是收缩率的影响,收缩率大的尺寸精度误差就大;成型工艺一一成型工艺条件的变化直接造成材料收缩,从而影响尺寸精度。
2.2.2塑件的表面质量该塑件是复印机小端盖,表面粗糙度为细橘皮状,除要求没有凹陷,无毛刺,内部无缩孔,没有特别得表面质量要求,故比较容易实现。
综以上分析可知,注射时在工艺参数控制较好的情况下,零件的成型质量很容易得到保证。
2.3工艺性分析为了满足制品表面光滑的要求与提高成型效率采用侧浇口。
浇口隐藏在塑件的内部。
结合塑件实际情况,采用从顶杆侧面进浇方式。
从塑料件侧面进料,因而塑件外表面不受损伤,不致因浇口痕迹而影响塑件的表面质量与美观效果。
塑件的工艺参数: 干燥条件:80-90 C 2小时成型收缩率:0.4-0.7% 。
模具温度:40-90C <模具温度将影响塑件光洁度,温度较低则导致光洁度较低)。
注射压力:56-176mpa。
注射速度:中高速度。
3注塑模具结构设计3.1分型面的确定分型面是决定模具结构形式的一个重要因素,它与模具的整体结构、浇注系统的设计、塑件的脱模和模具的制造工艺的有关,因此,分型面的选择是注射模设计中的一个关键。
根据分型面的选择原则:a.分型面应选在塑件外形最大轮廓处;b.在开模时尽量使塑件留在动模;c.分型面的选择应保证塑件的尺寸精度和表面质量;d.有利于排气和模具的加工方便;e.有助于避免侧抽芯或便于侧抽芯。
由以上因素决定,有三种分型面方案,如图 3.1万案图3.1方案的选择如图3.1中方案一分型面的选择使得在浇注过程中,动模和定模上都有侧挖,不利于散热,设计复杂,不利于简化模具设计,设计不合理。
方案二有侧挖,分型面较大,侧挖结构简单,有利于制品推出,简化模具结构,设计合理。
方案三分型面处,将主要结构全部放入动模中,有侧挖,同时也影响本身的美观。
设计不合理。
该塑件为端盖不太要求过于美观,无斑点和熔接痕,表面质量要求一般高。
在选择分型面时,塑件开模后会包在动模型芯上,模具结构也较为简单。
所以,选塑件大端底平面作为分型面较为合适,故选择分分型面方案二。
3.2浇口的确定浇口亦称进料口,是连接分流道与型腔的通道。
是浇注系统的关键部分,浇口的位置、形状及尺寸对塑件的性能和质量的影响最大。
常用的浇口形式有:1)直接浇口;2)侧浇口;3)扇形浇口;4)平缝浇口;5)环形浇口;6)轮辐浇口;7)爪形浇口;8)点浇口;9)潜伏浇口;10)护耳浇口。
本次设计复印机小端盖,该塑件属于外观件,端盖表面质量要求无斑点和熔接痕,进浇入潜在外面影响美观,所以要把进浇口隐藏在塑件的内部。
结合塑件实际情况,采用从顶杆侧面进浇方式,见下图32图3.2进浇方式3.3型腔数目的确定注射模的型腔数目,可以是一模一腔,也可以是一模多腔,在型腔数目的确定时主要考虑以下几个有关因素:a.塑件的尺寸精度;b.模具制造成本;c.注射成型的生产效益;d.模具制造难度。
考虑到该塑件是一般办公用品,查手册得塑件的经济精度推荐4级,塑件的尺寸中等,考虑其浇注方式为潜伏式测浇结构,为保证其主浇道浇注不发生偏移的情况至少采用一模2腔结构。
考虑其经济性能,降低模具制造成本低,所以本次设计采用一模2腔结构比较合适,装配也方便。
3.4浇注系统设计注射模的浇注系统是指模具中从注射机喷嘴开始到型腔入口为止的塑料熔体的流动通道,它由主流道,分流道,冷料穴和浇口组成。
它向型腔中的传料,传热,传压情况决定着塑件的内在和外表质量,它的布置和安排影响着成型的难易程度和模具设计及加工的复杂程度,所以浇注系统是模具设计中的主要内容之一。
3.4.1主流道主流道是连接注射机的喷嘴与分流道的一段通道,通常和注射机的喷嘴在同一轴线上,断面为圆形,有一定的锥度,目的是便于冷料的脱模,同时也改善料流的速度,因为要和注射机相配,所以根据选用的XS-ZY250型号注射机的相关尺寸得喷嘴前端孔径:d0=4.0mm;喷嘴前端球面半径:R0=16m;根据模具主流道与喷嘴的关系取主流道球面半径:R=16mm;取主流道小端直径:d=4.5mm为了便于将凝料从主流道中取出,将主流道设计成圆锥形,起斜度为一此处选用2°经换算得主流道大端直径为6.4mm如图3.3所示。
图3.3主浇道由于主流道要与高温的塑料熔体和喷嘴反复接触和碰撞,所以主流道部分常设计成可拆卸的主流道浇口套,以便选用优质的钢材单独加工和热处理。
3.4.2分流道分流道是主流道与浇口之间的通道,一般开设在分型面上,起分流和转向作用,分流道的长度取决于模具型腔的总体布置和浇口位置,分流道的设计应尽可能短,以减少压力损失,热量损失和流道凝料。
分流道如图3.4所示。
图3.4分流道由于分流道中与模具接触的外层塑料迅速冷却,只有中心部位的塑料熔体的流动状态较为理想,因此里面分流道的内表面粗糙度Ra并不要求很低,一般取0.4卩m左右既可,这样表面稍不光滑,有助于塑料熔体的外层冷却皮层固定,从而与中心部位的熔体之间产生一定的速度差,以保证熔体流动时具有适宜的剪切速率和剪切热。
3.4.3浇口的设计a.浇口类型及位置的确定该模具是小型塑件的型腔模具,同时从所提供塑件图样中可看出,在底部顶杆上的设置潜伏式侧浇口比较合适。
该模具采用侧浇潜伏式浇口,其有以下特性:(1>形状简单,去除浇口方便,便于加工,而且尺寸精度容易保证;(2>试模时如发现不当,容易及时修改;(3>能相对独立地控制填充速度及圭寸闭时间;(4>对于壳体形塑件,流动充填效果较佳。