热成形钢板凸焊工艺介绍及参数说明
凸焊资料整理

目录一.概述 (2)二.种类 (2)三.原理 (3)四.焊接质量的影响因素 (3)五.凸焊焊接过程 (5)六.焊接凸点的设计 (5)七.常用金属的焊接 (6)八.凸焊电极材料 (8)九.检验方法 (8)十.焊接前的工件清理 (8)十一.飞溅 (9)一.概述凸焊,是在一工件的贴合面上预先加工出一个或多个突起点,使其与另一工件表面接触并通电加热,然后压塌,使这些接触点形成焊的电阻焊方法,凸焊是点焊的一种变形,主要用于焊接低碳钢和低合金钢的冲压件,板件凸焊最适宜的厚度为0.5~4mm,小于0.25mm时家采用点焊。
随着汽车工业发展,高生产率的凸焊在汽车零部件制造中获得大量应用。
另外,凸焊在线材、管材等连接上也获得普遍应用。
二.种类根据凸焊接头的结构形式,将凸焊方法分类见表1,实例如图1所示。
表1 凸焊方法及特点凸焊类型接头结构形式应用单点凸焊多点凸焊凸点设计成球面形、圆锥形和方形,并预先压制在薄件或厚件上最广,单点凸焊可以在与点焊机上进行;多点凸焊也可在凸焊机上进行,最多一次焊20点环焊在一个工件上预先制出凸环或利用工件原有的型面、倒角构成的锐边,焊后形成一条环焊缝很广,密封性焊缝应在直流焊机上进行,最大¢80mm,非密封性焊缝亦可在交流焊机上进行;管壳、螺母、注液口等T形焊在杆形上预制出单个或多个球面形、圆锥形、弧面形及齿形等凸点,一次加压通电焊接点焊机或凸焊机进行;螺钉、管_板等T形接头滚凸焊在面板上预先制出多个圆凸点或长凸点,滚轮电极压紧工件,电流仅在有凸点的位置才通过,电极与工件连续转动专用滚凸焊机;汽车制动踏等线材交叉焊利用线材(包含管材)轮廓的凸起部分相互交叉接触较广,可在凸焊机或多点焊机上进行,网片焊接等三.原理凸焊是点焊的一种,所以凸焊的原理与点焊是相同的。
通过电极压力将工件夹在一起,电极两端通大电流。
由于工件间的电阻较大,在接触面形成热量熔化金属,形成焊核。
(如图1所示)四.焊接质量的影响因素由原理可知,焊核的好坏直接影响着焊接的质量,而产生热量的多少又影响着焊核的大小及熔融程度。
凸焊的工艺特点和工艺参数

凸焊的工艺特点和工艺参数1、凸焊的工艺特点凸焊是点焊的一种变形,通常是在两板件之一上冲出凸点,然后进行焊接,由于电流集中,克服了点焊时熔核偏移的缺点,因此凸焊时工件的厚度。
比可以超过6:1。
凸焊时,电极必须随着凸点的被压溃而迅速下降,否则会因失压而产生喷溅,所以应采用电极随动性好的凸焊机。
多点凸焊时,如果焊接条件不适当,会引起凸点移位现象,并导致接头强度降低。
实验证明,移位是由电流通过时的电磁力引起的。
影响凸点移位的电磁力F与电流I的平方和凸点的高度h成正比,与点距Sd成反比,凸点移动向外偏斜是次级回路电磁力附加作用的结果。
在实际焊接时,由于凸点高度不一致,上、下电极平行度差,一点固定另一点移动要比两点同时移动的情况多。
为了防止凸点移位,除在保证正常熔核的条件下,选用较大的电极压力,较小的焊接电流外,还应尽可能地提高加压系统的随动性。
提高随动性的方法主要是减小加压系统可动部分的质量;以及在导向部分采用滚动摩擦。
多点凸焊时,为克服各凸点间的压力不均衡,可以采用附加预热脉冲或采用可转动电极的办法,特别适用于在同一个板件上焊接两个距离较大的零件,在上电极与上座板之间装有由多层铜箔制成的铜分路,目的是防止枢轴过热和两侧凸点电流不均衡。
2、凸焊的工艺参数凸焊的主要工艺参数是电极压力、焊接时间和焊接电流。
(1)电极压力凸焊的电极压力取决于被焊金属的性能、凸点的尺寸和一次焊成的凸点数量等。
电极压力应足以在凸点达到焊接温度时将其完全压溃,并使两工件紧密贴合。
电极压力过大会过早地压溃凸点,失去凸焊的作用,同时因电流密度减小而降低接头强度,压力过小又会引起严重喷溅。
(2)焊接时间对于给定的工件材料和厚度,焊接时间由焊接电流和凸点刚度决定。
在凸焊低碳钢和低合金钢时,与电极压力和焊接电流相比,焊接时间是次要的,在确定合适的电极压力和焊接电流后,再调节焊接时间,以获得满意的焊点。
如果想缩短焊接时间,就要相应增大焊接电流,但过分增大焊接电流可能引起金属过热和喷溅,通常凸焊的焊接时间比点焊长,而电流比点焊小。
热成形钢板凸焊工艺介绍及参数说明
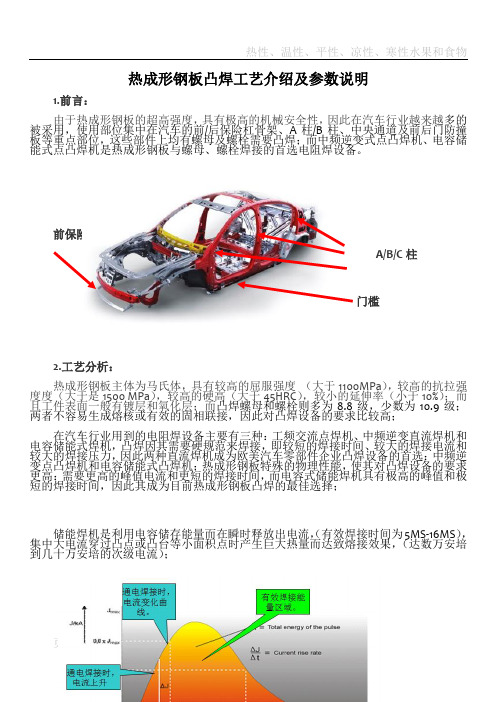
热成形钢板凸焊工艺介绍及参数说明1.前言:由于热成形钢板的超高强度,具有极高的机械安全性,因此在汽车行业越来越多的被采用,使用部位集中在汽车的前/后保险杠骨架、A柱/B柱、中央通道及前后门防撞板等重点部位,这些部件上均有螺母及螺栓需要凸焊;而中频逆变式点凸焊机、电容储能式点凸焊机是热成形钢板与螺母、螺栓焊接的首选电阻焊设备。
前保险杠A/B/C柱门槛2.工艺分析:热成形钢板主体为马氏体,具有较高的屈服强度(大于1100MPa),较高的抗拉强度度(大于是1500 MPa),较高的硬高(大于45HRC),较小的延伸率(小于10%);而且工件表面一般有镀层和氧化层;而凸焊螺母和螺栓则多为8.8级,少数为10.9级;两者不容易生成熔核或有效的固相联接,因此对凸焊设备的要求比较高;在汽车行业用到的电阻焊设备主要有三种:工频交流点焊机、中频逆变直流焊机和电容储能式焊机,凸焊因其需要硬规范来焊接,即较短的焊接时间、较大的焊接电流和较大的焊接压力,因此两种直流焊机成为欧美汽车零部件企业凸焊设备的首选:中频逆变点凸焊机和电容储能式凸焊机;热成形钢板特殊的物理性能,使其对凸焊设备的要求更高:需要更高的峰值电流和更短的焊接时间,而电容式储能焊机具有极高的峰值和极短的焊接时间,因此其成为目前热成形钢板凸焊的最佳选择;储能焊机是利用电容储存能量而在瞬时释放出电流,(有效焊接时间为5MS-16MS),集中大电流穿过凸点或凸台等小面积点时产生巨大热量而达致熔接效果,(达数万安培到几十万安培的次级电流);电容式储能焊机放电波形图3.案例分析:例1:苏州安嘉为某车型A柱螺母凸焊,板材为BTR165H热成形钢,厚度1.8MM;螺母为M10凸焊法兰螺母,三段月牙凸台;焊接要求:扭矩130N.M,推脱力8KN,螺纹无损伤,外观无明显损伤;凸焊螺母示意图汽车A柱示意图3.1焊机:机型为DR-30000J,采用山形电极垂直加压;电容式储能名称凸焊机型号DR-30000J充电电100V-800V压加压方气动加压式最大短160000A路电流最大焊29000 N接压力电极材铬锆铜3.2焊接规范调整:3.2.1在常规电阻焊工艺参数调整时,三个基本要素:焊接时间、焊接电流、焊接压力缺一不可,而在电容式储能焊机则无焊接时间调整这一项,焊接电流也是通过充电电压反映出来的,因此储能焊机规范调整主要是在焊接压力和充电电压之间匹配,特殊情况下会再加一项回火电压用于细化晶粒;3.2.2本案热成形钢螺母凸焊工艺调整时需要克服的难点:1.焊接压力的设定,由于热成形钢板的强度较高,熔接时需要更大的压力,但凸焊螺母的强度较低,较大的压力会导致凸点过早的压溃,因此焊接压力最好采用马鞍形压力曲线,实用情况是阶梯状的二段压力更为普遍些,这样能保证凸点不过早压溃变形,又能在熔核生长后期不会产生太多的飞溅;2.充电电压的设定,过高的充电电压在焊接时产生过大的热量,螺母金属表现为挤出、飞溅,会造成两种情况,一是飞溅导致熔合联接面积减少(过烧),螺母推脱力下降,二是螺纹塞规无法通过;较低的充电电压则会导致熔接深度不够,出现螺母推脱力不达标和虚焊;3.2.3工艺规范调整方法,两个焊接要素(充电电压和焊接压力)调整时需以其中一个为基础对另一数值做出调整匹配,不可同时调做出两项调整;此处应考虑到经验的运用,有类似的螺母凸焊的参数可以做为参考,能有效减少调整的次数,只是热成形板材的焊接需要更大的电流和压力,可以从同规格在普通材料上的测试数据做为起点开始调整,经过试焊及试验室验证找出最佳的数值;需要注意的时,在批量生产时应在试焊数据基础上加大3-5%,以满足产品其它原因造成的波动下限;3.3焊接参数确认:3.4工件推脱力及破坏测试:测试设备扭力钣手、万能实验机、螺纹塞规测试结果扭力﹥180 N.M;推脱力﹥12KN,螺纹无异常,外观无损伤例2:某车型B柱螺栓凸焊,板材为BTR165H热成形钢,厚度2.0MM;螺栓为M10凸焊螺栓,三凸点;焊接要求:推脱力8KN,螺纹无损伤,外观无损伤;3.5焊接参数确认:3.6工件推脱力及破坏测试:4.电极部分工艺补充:4.1在热成形钢版凸焊时由于焊接压力巨大、峰值电流非常高,因此焊接时对电极材料的要求很高,需要较高的软化温度、较高的导电率和较高的硬度,而弥散铜(氧化铝铜)具有这几种优势,(软化温度达950°),成为目前热成形钢板凸焊最合适的电极材料;4.2定位销常用用的材质有胶木、陶瓷、KCF等,而近年欧美车企有用到氮化硅做为热成形钢板凸焊的定位销,因其使用寿命更长(20万次)、绝缘效果好、硬度高等特点,使其成为凸焊定位销材质的新宠,但因其价格昂贵,目前尚无普遍使用,但这是未来定位销的方向。
凸焊基础知识

进行电极间回火,并应采用比低碳钢高的电极压力。 不锈钢凸焊没有困难,但较易产生熔核移位现象。应注意选用合理的焊接工艺参数,并避免采用 过小的点距。 铝合金强度低,则一通电凸点即被压馈。起不到集中电流的作用,因此很少采
起各点电流的不平衡,使接头强度不稳定。因此凸点高度误差应不超过 ±0.12mm。如采用预热电流,则误差可以增大。
凸点也可以做成长形的(近似椭圆形),以增加熔核尺寸,提高焊点强度,此时凸点与平板将为 线接触。 凸焊时,除利用上述几种形式的凸点形成接头外,根据凸焊工件种类不同还有多种接头形式。 用于凸焊的螺栓和螺帽上的凸点和凸环多是在零件锻压时一次成形。
凸焊的每一焊点所需电流比点焊同样一个焊点时小。但在凸点完全压溃之前电流必须能使凸 点溶化,推荐的电流应该是在采用合适的电极压力下不至于挤出过多金属的最大电流。对于一定 凸点尺寸,挤出的金属量随电流的增加而增加。采用递增的调幅电流可以减小挤出金属。和点焊 一样,被焊金属的性能和厚度仍然是选择焊接电流的主要依据。 多点凸焊时,总的焊接电流大约为每个凸点所需电流乘以凸点数。但考虑到凸点的公差、工件形 状。以及焊机次级回路的阻抗等因素,可能需要做一些调整。 凸焊时还应做到被焊两板间的热平衡,否则,在平板未达到焊接温度以前便已溶化,因此焊接同 种金属时,应将凸点冲在较厚的工件上,焊接异种金属时,应将凸点冲在电导率较高的工件上。 但当在厚板上冲出凸点有困难时,也可在薄板上冲凸点。 电极材料也影响两工件上的热平衡,在焊接厚度小于 0.5mm 的薄板时,为了减少平板一侧的散 热,常用钨-铜烧结材料或钨做电极的嵌块。
简介 板件凸焊最适宜的厚度为 0.5-4mm。焊接更薄的板件时,凸点设计要求严格,需要随动性
凸焊的工艺技术要求

凸焊工艺规范1 范围本规范规定了公司常用标准件凸焊工艺技术要求。
本规范适用于公司规划和设计部门对凸焊工艺的审查。
2 规范性引用文件无3术语3.1 凸焊凸焊是在焊接件的接合面上预先加工出一个或多个凸点,使其与另一焊接件表面相接触,加压并通电加热,凸点压溃后,使这些接触点形成焊点的电阻焊方法1)。
凸焊的位置精度取决于定位销与被焊接对象之间的配合精度,奇瑞公司的凸焊理论定位偏差最大为:(螺母)0.2mm(螺栓)0.25mm。
——————————《焊接工程师手册》 陈祝年 机械工业出版社 2002.1 第四章 凸焊工艺3.2凸焊设备81.上电极臂 4.下电极夹持器 7.定位销2)2.下电极臂 5.上电极8.凸焊标准件 3.上电极夹持器 6.下电极 9.钣金件图1 螺栓凸焊螺母凸焊图3图2 图4 4内容 4.1 螺母凸焊4.1.1 凸焊电极需要的空间螺母凸焊面必须为平面。
图1螺母凸焊下电极直径大小有Φ32、Φ35、Φ38、Φ42,常用为Φ32;上电极直径有Φ16、Φ20、Φ27,M5常用为Φ16,M6、M8常用为Φ20。
所以普通螺母的下电极至少要预留Φ32的圆平面。
保险带安装螺母(如图2)上电极与下电极直径相同,有Φ38、Φ42两种。
所以对于安全带螺母上下电极需要至少预留Φ38的圆平面。
4.1.2 凸焊定位底孔为降低凸焊电极制造成本,凸焊螺母底孔统一定为(M+1)mm,其中M为焊接螺母的公称直径(螺纹大径)。
英制螺母螺纹大径加1后取整。
如:7/16螺母(QR366716),螺纹大径约Φ11.1125mm,其螺母底孔直径为Φ12mm。
4.2 螺栓凸焊螺栓凸焊有两种形式,一种为承面凸焊,钣件对应位置开孔(如图1,3);另一种为端面凸焊,钣件位置无孔(如图4),目前奇瑞公司基本为承面凸焊。
4.2.1 凸焊电极需要的空间螺栓凸焊面必须为平面。
图3 螺栓凸焊下电极直径大小有Φ25、Φ32,上电极大小有Φ16、Φ20;M5、M6下电极常用深度为30mm,M8下电极常用深度为38mm。
热板焊接工艺参数
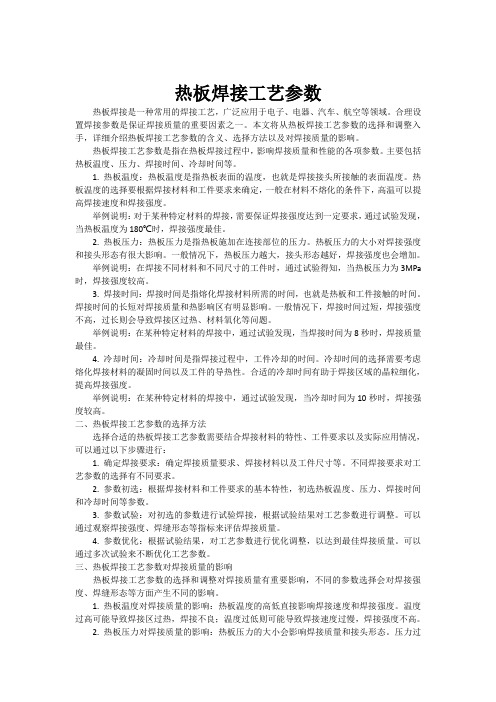
热板焊接工艺参数热板焊接是一种常用的焊接工艺,广泛应用于电子、电器、汽车、航空等领域。
合理设置焊接参数是保证焊接质量的重要因素之一。
本文将从热板焊接工艺参数的选择和调整入手,详细介绍热板焊接工艺参数的含义、选择方法以及对焊接质量的影响。
热板焊接工艺参数是指在热板焊接过程中,影响焊接质量和性能的各项参数。
主要包括热板温度、压力、焊接时间、冷却时间等。
1. 热板温度:热板温度是指热板表面的温度,也就是焊接接头所接触的表面温度。
热板温度的选择要根据焊接材料和工件要求来确定,一般在材料不熔化的条件下,高温可以提高焊接速度和焊接强度。
举例说明:对于某种特定材料的焊接,需要保证焊接强度达到一定要求,通过试验发现,当热板温度为180℃时,焊接强度最佳。
2. 热板压力:热板压力是指热板施加在连接部位的压力。
热板压力的大小对焊接强度和接头形态有很大影响。
一般情况下,热板压力越大,接头形态越好,焊接强度也会增加。
举例说明:在焊接不同材料和不同尺寸的工件时,通过试验得知,当热板压力为3MPa 时,焊接强度较高。
3. 焊接时间:焊接时间是指熔化焊接材料所需的时间,也就是热板和工件接触的时间。
焊接时间的长短对焊接质量和热影响区有明显影响。
一般情况下,焊接时间过短,焊接强度不高,过长则会导致焊接区过热、材料氧化等问题。
举例说明:在某种特定材料的焊接中,通过试验发现,当焊接时间为8秒时,焊接质量最佳。
4. 冷却时间:冷却时间是指焊接过程中,工件冷却的时间。
冷却时间的选择需要考虑熔化焊接材料的凝固时间以及工件的导热性。
合适的冷却时间有助于焊接区域的晶粒细化,提高焊接强度。
举例说明:在某种特定材料的焊接中,通过试验发现,当冷却时间为10秒时,焊接强度较高。
二、热板焊接工艺参数的选择方法选择合适的热板焊接工艺参数需要结合焊接材料的特性、工件要求以及实际应用情况,可以通过以下步骤进行:1. 确定焊接要求:确定焊接质量要求、焊接材料以及工件尺寸等。
22MnB5热成形钢点焊接头组织演变与性能分析
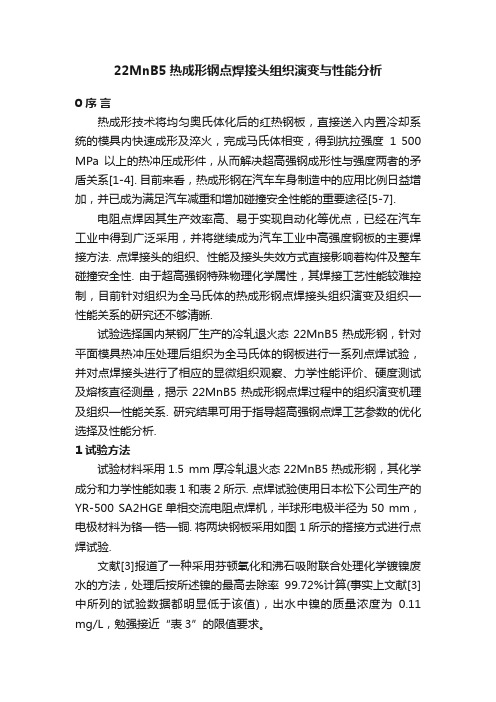
22MnB5热成形钢点焊接头组织演变与性能分析0 序言热成形技术将均匀奥氏体化后的红热钢板,直接送入内置冷却系统的模具内快速成形及淬火,完成马氏体相变,得到抗拉强度1 500 MPa以上的热冲压成形件,从而解决超高强钢成形性与强度两者的矛盾关系[1-4]. 目前来看,热成形钢在汽车车身制造中的应用比例日益增加,并已成为满足汽车减重和增加碰撞安全性能的重要途径[5-7].电阻点焊因其生产效率高、易于实现自动化等优点,已经在汽车工业中得到广泛采用,并将继续成为汽车工业中高强度钢板的主要焊接方法. 点焊接头的组织、性能及接头失效方式直接影响着构件及整车碰撞安全性. 由于超高强钢特殊物理化学属性,其焊接工艺性能较难控制,目前针对组织为全马氏体的热成形钢点焊接头组织演变及组织—性能关系的研究还不够清晰.试验选择国内某钢厂生产的冷轧退火态22MnB5热成形钢,针对平面模具热冲压处理后组织为全马氏体的钢板进行一系列点焊试验,并对点焊接头进行了相应的显微组织观察、力学性能评价、硬度测试及熔核直径测量,揭示22MnB5热成形钢点焊过程中的组织演变机理及组织—性能关系. 研究结果可用于指导超高强钢点焊工艺参数的优化选择及性能分析.1 试验方法试验材料采用1.5 mm厚冷轧退火态22MnB5热成形钢,其化学成分和力学性能如表1和表2所示. 点焊试验使用日本松下公司生产的YR-500 SA2HGE单相交流电阻点焊机,半球形电极半径为50 mm,电极材料为铬—锆—铜. 将两块钢板采用如图1所示的搭接方式进行点焊试验.文献[3]报道了一种采用芬顿氧化和沸石吸附联合处理化学镀镍废水的方法,处理后按所述镍的最高去除率99.72%计算(事实上文献[3]中所列的试验数据都明显低于该值),出水中镍的质量浓度为0.11 mg/L,勉强接近“表3”的限值要求。
同时,为了体现桩-土界面土体位移的大小及分布情况,可对位移矢量图加以处理得到土体位移云图.图5为桩-土界面水平位移云图和竖向位移云图,由图可以看出,土体位移呈现局部化特征,分布并无明显规律.对比两个方向位移,可以发现水平位移较竖向位移小1~2个数量级,说明桩-土界面土体以竖向位移为主,因此本试验主要考虑桩-土界面土体的竖向位移.为探究沉桩速度和沉桩深度对桩-土界面土体变形的影响,设计了以下两组试验:桩端在同一深度处,不同压桩速度对土体位移的影响;相同压桩速度下,桩端位于不同深度时压桩对土体位移的影响.表 1 22MnB5热成形钢板化学成分(质量分数,%)Table 1 Chemical compositions of 22MnB5 hot stamped steelCSiMn CrMoBTi 0.230.170.950.240.210.001 90.02表 2 22MnB5热成形钢板力学性能Table 2 Mechanical properties of 22MnB5 hot stamped steel断后伸长率A(%)热成形前铁素体+ 珠光体43051031.3热成形后马氏体1 1001 560 7.5状态组织屈服强度ReL/MPa抗拉强度Rm/MPa图 1 点焊试验中的试样尺寸 (mm)Fig. 1 Sample dimensions of spot welding test点焊试验中采用的焊接工艺参数如表3所示.依次调整焊接电流I、焊接时间t及电极压力F,分析22MnB5热成形钢点焊获得的熔核直径、拉剪载荷及接头失效形式,确定合理的焊接工艺窗口范围. 焊点力学性能评价在电子式万能材料试验机上进行,拉伸速度为2 mm/min,焊点失效破坏过程中所承受载荷的最大值即为焊点的拉剪力. 使用线切割机将焊点沿中心切开制备金相试样,经研磨、抛光及4%的硝酸酒精溶液腐蚀后,采用Leica DMIRM光学显微镜及JXA-8530F场发射电子探针分析仪观察点焊接头的宏观及微观组织. 利用维氏硬度计测试点焊接头的显微硬度,所用测试载荷为2.94 N,加载时间为 10 s,测试点间距为 0.2 mm.表 3 点焊试验中的焊接工艺参数Table 3 Welding parameters of spot welding test焊接电流I/kA 焊接时间t/ms电极压力F/kN 4.5 ~ 12.04007.0 8.0 ~ 10.0300 ~ 5008.0 9.04003.5 ~ 11.52 试验结果与分析2.1 焊接工艺参数对点焊性能的影响焊接工艺参数对22MnB5热成形钢点焊接头拉剪力及熔核直径的影响如图2所示. 由图2a可以看出,随着焊接电流的增加,焊点失效时承受的拉剪力及熔核直径均呈现先增加后缓慢降低的变化趋势. 当I 较小时,焊点处金属熔化量少,熔核直径小,熔核强度不足,从而发生“界面撕裂”失效.当 I为7.5 kA时,熔核直径D达到7.1 mm,接头失效形式由“界面撕裂“转变为”熔核拔出”. 通常来讲,“熔核拔出”是焊点最理想的失效形式,表明焊点具有很强的承载能力. 当I增加至10.5 kA时,出现焊接飞溅,减少了焊点处的金属熔化量,从而减少了熔核直径,强度降低,导致拉剪力降低. 可以得出,22MnB5热成形钢的理想焊接电流I为7.5 ~10.0 kA. 焊点拉剪力与熔核直径的对应关系表明,焊点可承载的拉剪力主要取决于熔核尺寸大小,大尺寸熔核具有更大的承载面积及更高的熔核强度,因此具有更高的承载能力.图 2 焊接工艺对焊点拉剪力及熔核直径的影响Fig. 2 Effects of welding parameters on nugget diameter andpeak load of spot weld in tensileshear test根据焦耳定律,点焊热输入量 Q = I2Rt,其中I为焊接电流,R为接触电阻,t为焊接时间. 焊接电流和焊接时间作为影响焊接热输入的主要因素,直接影响着点焊接头熔核直径及拉剪力. 由图2b可以看出,在合理的工艺窗口内,采用小电流长时间或大电流短时间的焊接工艺可得到相近的熔核直径及拉剪力,且所有焊点均表现出“熔核拔出”的失效形式.电极压力影响着接触电阻,从而也是影响焊接热输入的重要因素. 如图2c所示,随着电极压力的增加,拉剪力及熔核直径均先增加后略降低. 在F为5.5 kN时,熔核直径D达到7.6 mm,接头失效形式由“界面撕裂”失效转变为“熔核拔出”失效. 然而F低于6.5 kN时,出现焊接飞溅. 由此得出,22MnB5热成形钢的理想电极压力F 为6.5 ~10.0 kN.虽然图2c表现出与图2a相似的变化趋势,但当电极压力增加至一定值时,两块钢板搭接处的接触面积达到较为稳定的状态,随后焊点拉剪力及熔核直径受电极压力的影响较小,表明电极压力对焊点性能的影响程度弱于焊接电流.6个月复查时去片UCVA≤0.8组、>0.8组眼轴长度分别为(25.35±0.77)mm和(25.07±0.77)mm,增长量分别为0.28~0.50(0.07±0.15)mm和-0.27~0.44(0.11±0.15)mm,通过协方差分析,2组眼轴增长差异无统计学意义(F=0.18,P=0.67),主要与基础眼轴长度相关(F=5.08,P=0.03),并不受分组影响(F=0.16,P=0.69)。
热板焊接工艺参数
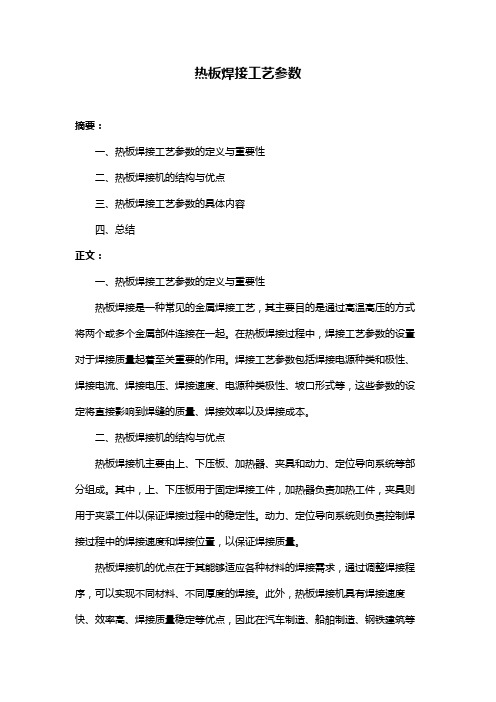
热板焊接工艺参数摘要:一、热板焊接工艺参数的定义与重要性二、热板焊接机的结构与优点三、热板焊接工艺参数的具体内容四、总结正文:一、热板焊接工艺参数的定义与重要性热板焊接是一种常见的金属焊接工艺,其主要目的是通过高温高压的方式将两个或多个金属部件连接在一起。
在热板焊接过程中,焊接工艺参数的设置对于焊接质量起着至关重要的作用。
焊接工艺参数包括焊接电源种类和极性、焊接电流、焊接电压、焊接速度、电源种类极性、坡口形式等,这些参数的设定将直接影响到焊缝的质量、焊接效率以及焊接成本。
二、热板焊接机的结构与优点热板焊接机主要由上、下压板、加热器、夹具和动力、定位导向系统等部分组成。
其中,上、下压板用于固定焊接工件,加热器负责加热工件,夹具则用于夹紧工件以保证焊接过程中的稳定性。
动力、定位导向系统则负责控制焊接过程中的焊接速度和焊接位置,以保证焊接质量。
热板焊接机的优点在于其能够适应各种材料的焊接需求,通过调整焊接程序,可以实现不同材料、不同厚度的焊接。
此外,热板焊接机具有焊接速度快、效率高、焊接质量稳定等优点,因此在汽车制造、船舶制造、钢铁建筑等行业中得到广泛应用。
三、热板焊接工艺参数的具体内容热板焊接工艺参数主要包括以下几个方面:1.焊接电源种类和极性:焊接电源种类有交流和直流两种,极性选择则分为正接和反接。
不同的极性选择对于焊接过程的稳定性和焊接质量有很大影响,需要根据具体情况进行选择。
2.焊接电流:焊接电流是焊接过程中的关键参数之一,其大小直接影响到焊缝的深度和宽度。
通常情况下,焊接电流越大,焊缝的深度和宽度也越大,但过大的电流可能导致焊缝过宽、焊缝成形不良等问题。
3.焊接电压:焊接电压是焊接过程中的另一个重要参数,其大小直接影响到电弧的稳定性和焊接质量。
通常情况下,焊接电压越高,电弧的稳定性越好,但过高的电压可能导致电弧过长、飞溅严重等问题。
4.焊接速度:焊接速度是指焊接过程中工件移动的速度,其大小直接影响到焊接效率和焊接质量。
- 1、下载文档前请自行甄别文档内容的完整性,平台不提供额外的编辑、内容补充、找答案等附加服务。
- 2、"仅部分预览"的文档,不可在线预览部分如存在完整性等问题,可反馈申请退款(可完整预览的文档不适用该条件!)。
- 3、如文档侵犯您的权益,请联系客服反馈,我们会尽快为您处理(人工客服工作时间:9:00-18:30)。
热成形钢板凸焊工艺介绍及参数说明
1.前言:
由于热成形钢板的超高强度,具有极高的机械安全性,因此在汽车行业越来越多的被采用,使用部位集中在汽车的前/后保险杠骨架、A柱/B 柱、中央通道及前后门防撞板等重点部位,这些部件上均有螺母及螺栓需要凸焊;而中频逆变式点凸焊机、电容储能式点凸焊机是热成形钢板与螺母、螺栓焊接的首选电阻焊设备。
前保险杠
A/B/C柱
门槛
2.工艺分析:
热成形钢板主体为马氏体,具有较高的屈服强度(大于1100MPa),较高的抗拉强度度(大于是1500 MPa),较高的硬高(大于45HRC),较小的延伸率(小于10%);而且工件表面一般有镀层和氧化层;而凸焊螺母和螺栓则多为8.8级,少数为10.9级;两者不容易生成熔核或有效的固相联接,因此对凸焊设备的要求比较高;
在汽车行业用到的电阻焊设备主要有三种:工频交流点焊机、中频逆变直流焊机和电容储能式焊机,凸焊因其需要硬规范来焊接,即较短的焊接时间、较大的焊接电流和较大的焊接压力,因此两种直流焊机成为欧美汽车零部件企业凸焊设备的首选:中频逆变点凸焊机和电容储能式凸焊机;热成形钢板特殊的物理性能,使其对凸焊设备的要求更高:需要更高的峰值电流和更短的焊接时间,而电容式储能焊机具有极高的峰值和极短的焊接时间,因此其成为目前热成形钢板凸焊的最佳选择;
储能焊机是利用电容储存能量而在瞬时释放出电流,(有效焊接时间为
5MS-16MS),集中大电流穿过凸点或凸台等小面积点时产生巨大热量而达致熔接效果,(达数万安培到几十万安培的次级电流);
电容式储能焊机放电波形图
3.案例分析:
例1:苏州安嘉为某车型A柱螺母凸焊,板材为BTR165H热成形钢,厚度1.8MM;螺母为M10凸焊法兰螺母,三段月牙凸台;焊接要求:扭矩130N.M,推脱力8KN,螺纹无损伤,外观无明显损伤;
凸焊螺母示意图
汽车A柱示意图
3.1焊机:机型为DR-30000J,采用山形电极垂直加压;
3.2焊接规范调整:
3.2.1在常规电阻焊工艺参数调整时,三个基本要素:焊接时间、焊接电流、焊接压力缺一不可,而在电容式储能焊机则无焊接时间调整这一项,焊接电流也是通过充电电压反映出来的,因此储能焊机规范调整主要是在焊接压力和充电电压之间匹配,特殊情况下会再加一项回火电压用于细化晶粒;
3.2.2本案热成形钢螺母凸焊工艺调整时需要克服的难点:1.焊接压力的设定,由于热成形钢板的强度较高,熔接时需要更大的压力,但凸焊螺母的强度较低,较大的压力会导致凸点过早的压溃,因此焊接压力最好采用马鞍形压力曲线,实用情况是阶梯状的二段压力更为普遍些,这样能保证凸点不过早压溃变形,又能在熔核生长后期不会产生太多的飞溅;2.充电电压的设定,过高的充电电压在焊接时产生过大的热量,螺母金属表现为挤出、飞溅,会造成两种情况,一是飞溅导致熔合联接面积减少(过烧),螺母推脱力下降,二是螺纹塞规无法通过;较低的充电电压则会导致熔接深度不够,出现螺母推脱力不达标和虚焊;
3.2.3工艺规范调整方法,两个焊接要素(充电电压和焊接压力)调整时需以其中一个为基础对另一数值做出调整匹配,不可同时调做出两项调整;此处应考虑到经验的运用,有类似的螺母凸焊的参数可以做为参考,能有效减少调整的次数,只是热成形板材的焊接需要更大的电流
和压力,可以从同规格在普通材料上的测试数据做为起点开始调整,经过试焊及试验室验证找出最佳的数值;需要注意的时,在批量生产时应在试焊数据基础上加大3-5%,以满足产品其它原因造成的波动下限;
3.3焊接参数确认:
充电电压设定焊接气压设定焊接电流监测预压压力监测焊接压力监测焊接时间监测430V 0.3Mpa 54KA 9.6KN 13KN 9MS 3.4工件推脱力及破坏测试:
测试设备扭力钣手、万能实验机、螺纹塞规
测试结果扭力﹥180 N.M;推脱力﹥12KN,螺纹无异常,外观无损伤
例2:某车型B柱螺栓凸焊,板材为BTR165H热成形钢,厚度2.0MM;螺栓为M10凸焊螺栓,三凸点;焊接要求:推脱力8KN,螺纹无损伤,外观无损伤;
3.5焊接参数确认:
4.1在热成形钢版凸焊时由于焊接压力巨大、峰值电流非常高,因此焊接时对电极材料的要求很高,需要较高的软化温度、较高的导电率和较高的硬度,而弥散铜(氧化铝铜)具有这几种优势,(软化温度达950°),成为目前热成形钢板凸焊最合适的电极材料;
4.2定位销常用用的材质有胶木、陶瓷、KCF等,而近年欧美车企有用到氮化硅做为热成形钢板凸焊的定位销,因其使用寿命更长(20万次)、绝缘效果好、硬度高等特点,使其成为凸焊定位销材质的新宠,但因其价格昂贵,目前尚无普遍使用,但这是未来定位销的方向。
4.3热成形钢板凸焊时由于其物理特性和采用硬规范焊接,金属挤出的机率比较高,采用下电极吹气的方法能有效改善,在焊接时用较大的气压对焊接区域吹气,可以使挤出金属迅速氧化、燃烧,大幅减少挤出金属的粘附,保证螺纹的合格。
5.结束语
苏州安嘉通过对热成形钢板凸焊件的测试,在使用电容式储能焊机和合理工艺情况下,焊接后均能达到技术要求,甚至远高于技术要求,是理想的凸焊设备,也使得热成形钢板的凸焊变得不那么困难;近年由于逆变技术的突飞猛进,中频逆变直流焊机的输出电流也不断提升,控制电流的爬升速率也越来越也高效,能模拟出电容式储能焊机的输出波形,使得中频逆变直流焊机凸焊热成形钢板上螺母和螺栓成为可能,也让热成形钢板的凸焊多了一个选择。
苏州安嘉自动化设备有限公司。